南京工程学院质量管理第14讲质量检验
施工方案中质量检验部分讲座

增速器
• A、齿轮轴心线的平行度公差X为 0.11㎜,Y为0.019㎜。 B、主动轴齿轮与从动齿轮轴中心 距250㎜,偏差为±0.03㎜。 C、齿面接触斑迹按齿轮宽不小于 90%,按齿高不小于70%(跑合后) ,齿侧间隙为0.12-0.24㎜。
齿轮轴心线公差示意图
示意图 • 4、确定停监点和必监点
二、编制质检计划的通病
• 1、没有质保组织机构或在组织机构中没有项目质量负责人。 • 2、有些单位在编写时采用的规范或标准为过时的。 • 3、质检计划或质量检验标准过于简单,没有具体的规定
或标准值,在实际检修过程中没有可操作性或可操作性差, 在这一点上应当特别注意。 • 4、停监点和必监点应确定准确。停监点和必监点的代号 应准确运用,不能混淆。W---必监点、H---停监点 • 5、施工方案使用过期的版本. • 6、单位领导的签字用盖章代替。 • 7、在施工方案的编写过程中,利用原来的稿件可以,但 一定要把那些过时的东西剔出去,过时的语言拿掉。
鼓风机轴瓦示意图
增速器轴瓦间隙示意图
密封
• 轴封、气封齿片应完 整无歪斜。
• 鼓风机轴封、隔板气 封、叶轮气封、增速 器和电机的油封间隙 应符合表中规定。
部位 油封 隔板 叶轮 油封 气封 气封
规程
∮170- ∮200 -∮180
∮549 - ∮120 -∮555 -∮135
标准 0.20- 0.30- 0.35- 0.15-
量具 专检 量具 专检
质检员 检修记录 质量标准 质检员 检修记录 质量标准
5、质量保证措施
• 为更好的保证本方案质量计划的全面落实,确保 D750-24煤气鼓风机检修的质量,我们将对检修 质量计划进行全面的贯彻和落实,在组织检修人 员进行技术交底的情况下,全面系统的学习施工 方案,有针对性的进行讲解,使全体参加检修人 员都能熟练掌握检修质量标准,检修的质量检测 方法和步骤,工具的使用及标准值的确定。最终 达到质量目标明确,检修方法得当,科学文明检 修,优质高效的目的,实现设备长周期运行。
《软件工程》课件第14章 软件质量的评价和保证

第14章 软件质量的评价和保证
14.2.2 ISO的软件质量评价模型 按照ISO/TC97/SC7/WG3/1985-1-30/N382,软件质
量度量模型由3层组成,如图14.3所示。 高层是软件质量需求评价准则(SQRC)。 中层是软件质量设计评价准则(SQDC)。 低层是软件质量度量评价准则(SQMC)。
第14章 软件质量的评价和保证 2) 面向软件产品修正 面向软件产品修正的定义如下: (1) 可维护性:指找到并改正程序中的一个错误所需代价 的程度。 (2) 可测试性:指测试软件以确保其能够执行预定功能所 需工作量的程度。 (3) 适应性:指修改或改进一个已投入运行的软件所需工 作量的程度。 3) 面向软件产品转移 面向软件产品转移的定义如下: (1) 可移植性:指将一个软件系统从一个计算机系统或环 境移植到另一个计算机系统或环境中运行时所需的工作量。
第14章 软件质量的评价和保证
(2) 可重用性:指一个软件(或软件的部件)能再 次用于其他相关应用的程度。
(3) 可互操作性:指将一个系统耦合到另一个系 统所需的工作量。
通常,对以上各个质量特性直接进行度量是很困 难的,在有些情况下甚至是不可能的。因此,McCall 定义了一些评价准则,这些准则可对反映质量特性的 软件属性分级,并以此来估计软件质量特性的值。软 件属性一般分级范围从0(最低)~10(最高)。主要评价 准则定义如下:
第14章 软件质量的评价和保证
(5) 发挥每个开发者的能力。软件生产是人的智 能生产活动,它依赖于开发组织团队的能力。开发者 必须有学习各专业业务知识、生产技术和管理技术的 能动性。管理者或产品服务者要制定技术培训计划、 技术水平标准,以及适用于将来需要的中长期技术培 训计划。
质量检验培训教材PPT课件
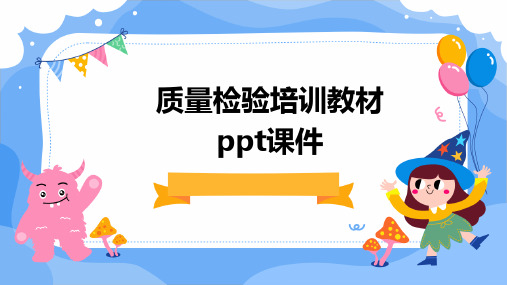
通过品尝产品味道,判 断是否符合口感要求。
触觉检验
通过触摸产品表面,判 断其质地、硬度、温度
等特性。
理化检验方法
物理检验
运用物理原理和技术对产 品进行检验,如测量尺寸、 重量、密度等。
化学分析
通过化学反应和仪器分析, 检测产品中的化学成分和 含量。
仪器分析
使用专业仪器对产品进行 高精度、高灵敏度的检测 和分析。
02
03
随机抽样
确保每个样本被抽取的概 率相等,消除主观偏见。
系统抽样
按照一定间隔从总体中抽 取样本,适用于大规模生 产线上。
分层抽样
将总体划分为若干层,从 每层中随机抽取样本,以 提高检验精度。
感官检验方法
视觉检验
嗅觉检验
味觉检验
通过肉眼观察产品外观、 颜色、形状等特征,判断
是否符合标准。
通过鼻子闻产品气味, 判断是否有异味或变质。
质量检验流程
检验准备
熟悉产品图纸、工艺文件、检 验指导书等技术资料,准备检 验所需的量具、检具和仪器。
进货检验
对采购的原材料、外购件、外 协件进行检验,确保符合采购 合同和技术要求。
过程检验
在生产过程中,对半成品、成 品进行检验,确保符合工艺要 求和产品质量标准。
最终检验
在产品生产完成后,进行全面 的最终检验,确保产品符合出
案例三:某制药厂质量检验案例分析
检验项目
药品成分、微生物限度、杂质含量
检验方法
高效液相色谱法、薄层色谱法、紫外分光 光度法
问题发现
药品溶出度不合格、微生强生产 环境管理
06
质量检验培训总结与展望
培训内容总结
01
质量检验基本概念和原理
2024版质量检验人员培训讲义课件
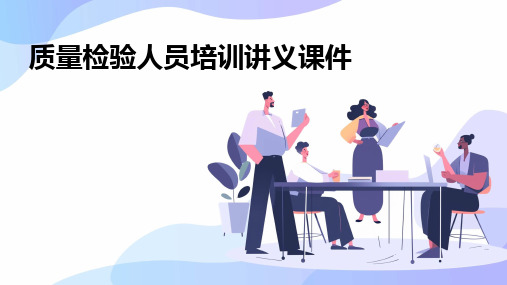
理化检验的常用方法与设备
物理检验方法
包括感官检验、密度测定、熔点测定、 折射率测定等。常用设备有天平、密 度计、熔点仪、折射仪等。
化学检验方法
包括酸碱滴定法、氧化还原滴定法、沉 淀滴定法、络合滴定法等。常用设备有 滴定管、容量瓶、移液管、分光光度计 等。
理化检验的操作规范与注意事项
操作规范 检验前应对仪器进行校准,确保测量结果的准确性。
质量检验的案例分析与经验分享
案例一
某企业因未对原料进行严格的质量检验,导致一批不合格原料进入生产环节,最终造成大量产品不合格,给企业带来巨大 损失。
案例二
某企业在生产过程中加强了过程检验和成品检验,及时发现并处理了质量问题,确保了产品质量的稳定性和一致性,赢得 了客户的信任和好评。
经验分享 质量检验人员需要具备高度的责任心和专业技能,时刻保持警惕,对每一个环节都要进行严格把关。同 时,要加强与生产部门和其他相关部门的沟通和协作,共同维护产品质量的稳定性和可靠性。
质量检验人员培训讲义课件
目录
• 质量检验概述 • 质量检验基础知识 • 抽样检验技术 • 感官检验技术 • 理化检验技术 • 质量检验实践与应用 • 质量检验人员的自我提升与发展
01
质量检验概述
质量检验的定义与目的
定义
质量检验是指对产品或服务的一个或多个质量特性进行观察、测量、试验,并 将结果和规定的质量要求进行比较,以确定每项质量特性合格情况的技术性检 查活动。
06
质量检验实践与应用
质量检验在生产过程中的应用
01
02
03
原料检验
对进厂原料进行质量检验, 确保原料符合生产要求, 防止不合格原料进入生产 环节。
过程检验
质量检验人员培训讲义课件

质量检验人员培训讲义课件一、教学内容本次培训讲义课件主要针对质量检验人员进行,内容涵盖质量检验的基本概念、质量管理的原则、质量检验的程序与方法、常用检测设备及工具的使用、质量问题的分析与处理等方面。
1. 质量检验的基本概念:介绍质量检验的定义、作用、分类和基本要求。
2. 质量管理的原则:阐述质量管理的基本原则,包括客户导向、过程方法、系统管理、持续改进等。
3. 质量检验的程序与方法:详细讲解质量检验的流程,包括检验计划的制定、检验标准的设定、检验技术的选择、检验结果的判定等。
4. 常用检测设备及工具的使用:介绍常见的检测设备及工具,如万用表、显微镜、硬度计等,并演示其正确使用方法。
5. 质量问题的分析与处理:讲解质量问题的分类、原因及影响,并提供解决问题的方法和技巧。
二、教学目标1. 使学员掌握质量检验的基本概念和质量管理的原则。
2. 熟悉质量检验的程序与方法,并能正确使用常用的检测设备及工具。
3. 学会分析质量问题,并能采取有效的措施进行处理。
三、教学难点与重点1. 教学难点:质量检验的程序与方法,常用检测设备及工具的使用,质量问题的分析与处理。
2. 教学重点:质量管理的原则,质量检验的基本概念,质量问题的处理方法。
四、教具与学具准备1. 教具:投影仪、电脑、白板、黑板、粉笔等。
2. 学具:培训讲义、笔记本、笔、计算器等。
五、教学过程1. 引入:通过实际案例,引入质量检验的重要性和必要性。
2. 讲解:详细讲解质量检验的基本概念、质量管理的原则、质量检验的程序与方法、常用检测设备及工具的使用、质量问题的分析与处理。
3. 演示:现场演示常用检测设备及工具的使用方法。
4. 练习:随堂练习,让学员动手操作,巩固所学知识。
5. 讨论:分组讨论质量问题的分析与处理方法,分享实际工作经验。
六、板书设计1. 质量检验的基本概念。
2. 质量管理的原则。
3. 质量检验的程序与方法。
4. 常用检测设备及工具的使用。
质量检验培训课件(ppt)
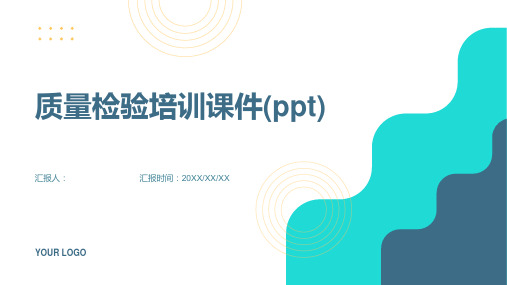
性能检测:按照产品标准或技术要求,对产品的性能进行检测,如开 关、按键、显示、音响等是否正常工作,是否符合客户要求。
检验记录:对每个产品进行详细的检验记录,包括外观、尺寸、性 能检测的数据和结果,以及质量等级的评定。
成品检验的记录和报告
质量检验培训课件(ppt)
汇报人:
汇报时间:0XX/XX/XX
YOUR LOGO
目录
CONTENTS
1 质量检验概述 2 质量检验计划 3 进货检验 4 过程检验 5 成品检验 6 质量检验数据分析和改进
质量检验概述
质量检验的定义和重要性
质量检验的定义
质量检验的重要 性
质量检验的目的 和意义
不合格品的处理和纠正措施
不合格品的标识和记录 原因分析:找出不合格品产生的原因 采取纠正措施:针对原因采取有效的措施 验证纠正措施的有效性
质量改进的策划和实施
确定改进目标:明确改进的方向和重点,制定合理的计划 数据分析:收集、整理、分析数据,找出问题的根源和影响 制定改进措施:根据数据分析结果,制定切实可行的改进措施 实施改进计划:落实改进措施,确保计划的顺利实施 监控和评估:对改进计划实施过程进行监控和评估,确保达到预期效果
检验员需对每批次产品进行外观、尺寸、性能检测,并记录检测数据。 成品检验报告需包含产品名称、规格、批次号、检验日期、检验依据等信息。 检验员需对不合格产品进行标识、隔离,并通知相关人员处理。 成品检验记录和报告需存档备查。
质量检验数据分析和改进
质量数据的收集和分析
明确收集哪些数据 确定收集数据的来源 选择合适的数据处理方法 数据分析工具的应用
质量检验基础知识讲义(ppt 33页)

1、抽样检验的定义:
抽样检验是按数理统计的方法,从 一批待检产品中随机抽取一定 数量的样本,并对样本进行全数 检验,再根据样本的检验结果来 判定整批产品的质量状况并做 出接收或拒收的结论。
总体
随机 抽样
全检
抽检方案( n , c)
样本
统计不合格品数d 比较判断
d >c 不合格批
拒收
d≤c 合格批
L(P)
n=100
c=4 c=3 c=1 c=2 c=0
P
8.抽样方案的确定
求解联立方程组:
= 1L(P0) = L(P1)
有很多组解。实际选择抽样方案时, 可根据标准。
二、抽样检验标准及其应用
GB2828 抽样表的使用
1.规定单位产品的质量特性 2.不合格的分类 3.合格质量水平的确定(AQL) 4.检验水平的规定 5.检验批的形成 6.检验严格度的确定
7.抽样方案的风险
(4)OC曲线的影响因素
① (n,c)一定,N对OC曲线的影响。
L(P)
A(1000,20,0)
B(100,20,0)
C(50,20,0)
甚微,可忽略
P(%)
②(N,c)一定,而n不同时的OC曲线 L(P) c=2 n=50 n=100 n=200 P(%)
③ n,N一定,而C不同时的曲线
三.过程检验
• 首件检验(首件三检制) • 巡回检验 • 末件检验 • 完工零件检验
第三节 抽样检验
• 一.抽样检验的基本概念 • 二.抽样检验标准及其应用
一.抽样检验的基本概念
• 1.抽样检验的定义 • 2.批质量 • 3.抽样方案及其分类 • 4.随机抽样法 • 5.接收概率 • 6.抽样特性曲线 • 7.抽样方案的风险 • 8.抽样方案的确定
质量检验培训PPT课件
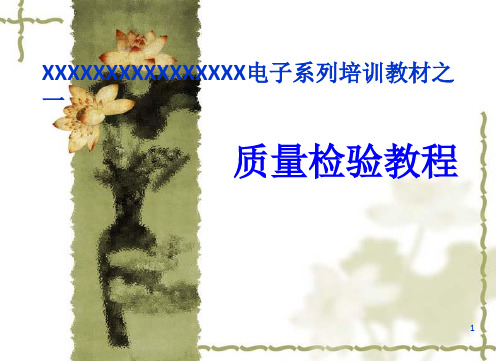
囊取物伤、涡流探伤等; ❖ 金属显微组织检验:利用金相显微镜进行检验。 ❖ 几何量测量:尺寸精度及形状与位置公差的测量。
10
什么是抽样检验?
抽样检验是指:按照预先确定的抽样方案,在整 批检验对象中随机抽取一定数量的样品进行 的检查,以及根据抽验结果对整批检验对象 的质量所做的判断。
❖ ②检查批:(简称批)。为实现抽样检查汇集起来的单 位产品。其可以投产批,销 售批、运输批。每个检查批 应由同型号、同等级、同种类。且生产条件和生产时间 基本相同的单位产品组成。
❖ ③批量:检查批所包含的单位产品数。记为N。 ❖ ④样本单位:从检查批中抽取并用于检验的单位产品。 ❖ ⑤样本:样本单位的全体。 ❖ ⑥样本大小:样本中包含的样本单位数。记为n。 ❖ 在具体实施抽样检查时,先根据提交检查批的批量与检
❖ 2.4顾客:是指接受产品的组织或个人。如消费者、 委托者等,组织可以是组织内部的或外部的。
❖ 2.5体系:是指相互关联或相互作用的一组要素。
28
❖ 2.6根据对顾客满意的影响程度不同,应对质量特 性进行分类管理。常用的质量特性分类方法是将 质量特性划分为键、重要和次要三类,分别是:
❖ 2.6.1关键质量特性:是指若超过规定的特性值要 求,会直接影响产品安全性或产品整机功能丧失 的质量特性。
❖ 1.2关于”要求”:要求指”明示的、通常隐含的或 必须履行的需求或期望” 。
❖ 2、与质量相关的概念:
❖ 2.1组织:是指”职责、权限和相互关系得到安排
的一组人员及设施”。
27
❖ 2.2过程:是指“一组将输入转化为输出的相互关联 或相互作用的活动”。过程由输入、实施活动和输 出三个环节组成。