防砂方法

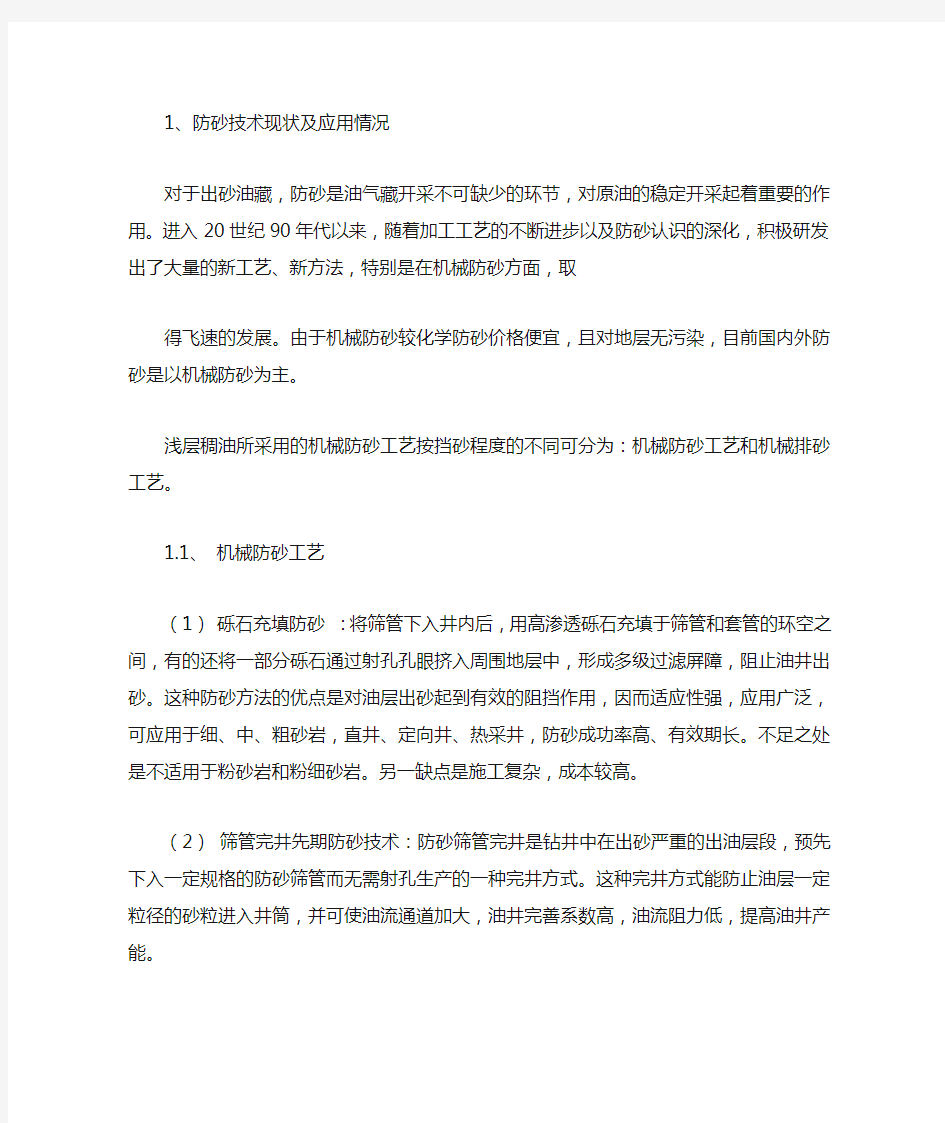
防砂方法
一、项目简介
防砂管结构:精密复合防砂筛管具有防砂效果好,结构简单、使用时效长、渗流面积大、出油率高、作业方便等特点。该产品从内到外由中心管、防砂过滤套、不锈钢外保护套等组成。中心管采用API标准套管或油管,防砂过滤套可分别用金属丝编织方孔网、金属丝编织密纹网,也可根据实际技术要求为用户设计过滤面积大,可自洁、不宜堵塞的滤材结构。产品可用于各类油、气、水井的防砂,以达到保护井下及地面设备的目的,提高出油率延长油井的使用寿命。
性能特点:这种筛管具有极佳的整体强度和抗变形能力。空隙度最高可达90%,抗堵塞能力强,渗透率高、耐高温、抗腐蚀、防砂范围广,适用于各种不同油层。有效的控制砂的粒径,过滤效率达99.5%.。使用性能可靠,是机械防砂领域中的高新技术之一。
二、以准噶尔盆地出砂分布情况为例予以简要说明
浅层稠油藏处于准噶尔盆地西北缘油气富集区,属砂岩油藏,由于地层本身结构疏松,加上采取的注高温高压蒸汽的强采方式,致使在油田开发的同时就伴随着不同程度的出砂,随着开发的延续,出砂井日益增多,出砂情况也更趋复杂、加剧。油井出砂致使油井生产周期缩短,油井产量大减,甚至造成油井停产、报废,严重制约了油井潜能的充分发挥,同时也使开采设备、地面工艺情况迅速恶化,严重影响了油田的高效稳产。
三、机械防砂工艺应用现状
1、防砂技术现状及应用情况
对于出砂油藏,防砂是油气藏开采不可缺少的环节,对原油的稳定开采起着重要的作用。进入20世纪90年代以来,随着加工工艺的不断进步以及防砂认识的深化,积极研发出了大量的新工艺、新方法,特别是在机械防砂方面,取
得飞速的发展。由于机械防砂较化学防砂价格便宜,且对地层无污染,目前国内外防砂是以机械防砂为主。
浅层稠油所采用的机械防砂工艺按挡砂程度的不同可分为:机械防砂工艺和机械排砂工艺。
1.1、机械防砂工艺
(1)砾石充填防砂:将筛管下入井内后,用高渗透砾石充填于筛管和套管的环空之间,有的还将一部分砾石通过射孔孔眼挤入周围地层中,形成多级过滤屏障,阻止油井出砂。这种防砂方法的优点是对油层出砂起到有效的阻挡作用,因而适应性强,应用广泛,可应用于细、中、粗砂岩,直井、定向井、热采井,防砂成功率高、有效期长。不足之处是不适用于粉砂岩和粉细砂岩。另一缺点是施工复杂,成本较高。
(2)筛管完井先期防砂技术:防砂筛管完井是钻井中在出砂严重的出油层段,预先下入一定规格的防砂筛管而无需射孔生产的一种完井方式。这种完井方式能防止油层一定粒径的砂粒进入井筒,并可使油流通道加大,油井完善系数高,油流阻力低,提高油井产能。
1.2、机械排砂工艺—泵挂滤砂管柱防砂
在泵下下入滤砂管柱,例如下入带有割缝衬管、各种地面预制成型的滤砂器管柱等。这种方法优点是施工简单、成本低;缺点是不能对地层出砂进行控制,不能防止一定粒径的砂粒进入井筒,并且滤砂管柱容易堵塞,有效期短。只适用于中、粗砂岩地层(d50>0.1mm),不适用于出砂、汽窜严重,经常砂埋的出砂井。
2.1砾石充填防砂——管内绕丝筛管防砂技术
绕丝筛管的制造方法是在均匀分布于圆周的筛竿上或开孔的金属衬管上,缠绕某种截面的钢丝并焊牢,留出一定的缝隙作为筛孔。管内绕丝筛管防砂工艺主要针对粒径中值在0.26mm以上的出砂井,89—94年普遍采用,防砂有效率88%,该工艺的实施解决了当时特稠油区块的防砂问题。但由于成本高、现场施工复杂,并且当时的加工工艺较为落后,缝隙精度差。因此在1989-1994年经历了大量使用后目前已遭淘汰。
2.2 、筛管完井先期防砂技术
精密微孔复合防砂筛管:从内到外由基管、复合防砂过滤套、不锈钢外保护套等组成。基管采用API标准套管或油管,防砂过滤套为不锈钢精密微孔复合过滤材料,采用全焊接结构。复合防砂过滤套具有高渗透性、高强度、抗高变形能力、高可靠性、抗腐蚀性好的特点,是机械防砂的一种新技术。
精密冲缝筛管:由基管、不锈钢过滤套和支撑环组成。基管采用符合API标准的
套管或油管钻孔而成,冲缝过滤套采用优质不锈钢材料,经数控精密冲孔工艺形成高密度的空间条缝,冲缝过滤套通过支撑环与基管焊接为一体。工作时地层砂被阻挡在冲缝过滤套外,地层流体经过冲缝间隙进入筛管内达到防砂目的。
筛管完井先期防砂技术优点是利用筛管完井有效地避免射孔完井对地层的伤害,极大地保护油层的渗透能力和过流能力。并且在生产中筛管外壁可逐步形成过流砂桥,可阻止较小粒径的砂子进入井筒。它的另一优势是可利用生产中常规措施注汽或拌热对筛管外壁堆积或裹胁的泥砂进行反向冲洗,避免了泵挂滤砂管存在的防砂缝隙容易被泥砂堵塞而无法解堵只能拔出的难题。
2005年在出砂严重的新井采用精密微孔管和精密冲缝管先期防砂完井管柱,达到了较好的防砂和增油效果。
2.3、泵挂滤砂管柱防砂
2.3.1泵挂绕丝管防砂技术
1991年以来因出砂而造成卡泵停抽生产井,进行了泵挂绕丝管防砂,因效果不明显,有效期短而没有大面积被油田推广应用。
2.3.2金属纤维管
金属纤维管挡砂过程是:当携砂流体通过护管流经金属纤维体进入中心管时,油砂被挡在金属纤维体之外,从而达到防砂目的。因为金属纤维有很高的弹性,不同的生产压力会形成不同的孔喉通道,不同粒径的地层砂会通过相应的孔喉通道进入井筒。该工艺具有渗透性高、抗压强度高、耐高温、流通面大、施工工艺简单、作业周期短等特点,适用于泥质含量低于20%、粒度中值大于0.1mm的疏松砂岩油藏。
金属纤维管按设计及制造工艺的不同可分为两种:金属绵蠕动滤砂管和金属纤维薄膜防砂管柱。
金属绵蠕动滤砂管:采用具有一定弹性且不粘结的耐腐蚀金属纤维制成独立滤砂室,分别固定安装在单层的基管管壁中。该工艺主要针对粒径中值在0.1mm以上的出砂井,由于试验井次少,效果有待进一步确定。
金属纤维薄膜防砂管柱:采用设计独特的新型过滤材料,利用线性结构过滤挡砂,过滤层可以根据砂粒粒径大小要求调整。在结构设计上克服了其他筛管的一些缺陷,具有防砂质量稳定可靠、效果好、渗透率大、抗堵塞能力
强等特点。
2.3.3陶瓷滤砂管——防砂器技术将高分子材料
第二章 防砂方法原理
第二章防砂方法原理 2.1 防砂方法分类 根据防砂原理及工艺特点,目前主要防砂方法大致可分为机械防砂、化学防砂、复合防砂和其它防砂方法几类。 (1)机械防砂方法 机械防砂方法可以分为两类,第一类是仅下入机械管柱的防砂方法,如绕丝筛管、割缝衬管、各种滤砂管等。这种方法简单易行,施工成本低。缺点是防砂管柱容易被地层砂堵塞,只能阻止地层砂产出到地面而不能阻止地层砂进入井筒,有效期短,只适用于油砂中值大于0.1mm的中、粗砂岩地层。 第二类机械防砂方法为管柱砾石充填,即在井筒内下入绕丝筛管或割缝衬管等机械管柱后,再用砾石或其它类似材料充填在机械管柱与套管的环形空间内,并挤入井筒周围地层,形成多级滤砂屏障,达到挡砂目的。这类方法设计及施工复杂,成本较高;但挡砂效果好,有效期长,成功率高,适用性广,可用于细、中、粗砂岩地层,垂直井,定向井,热采井等复杂条件。砾石充填防砂的缺点主要是施工复杂,一次性投入高;若砾石尺寸选择不当,地层砂侵入砾石层后会增加油流入井的阻力,影响防砂后的油井产能。研究结果表明,砾石充填井筒附过主要压降损失在填有砾石的射孔炮眼内。因施工过程较长,必须注意减少作业过程中对油层的作害。 (2)化学防砂 化学防砂是向地层中挤入一定数量的化学剂或化学剂与砂浆的混合物,达到充填、固结地层、提高地层强度的目的。化学防砂主要分为人工胶结地层和人工井壁两种方法。人工胶结地层是向地层注入树脂或其它化学固砂剂,直接将地层砂固结;人工井壁是将树脂砂浆液、预涂层砾石、水带干灰砂、水泥砂浆、乳化水泥等挤入井筒周围地层中,固结后形成具有一定强度和渗透性的人工井壁。 化学防砂方法适用于薄层短井段,对粉细砂岩地层的防砂效果好,施工后井筒内不留下任何机械装置,便于后期处理。缺点是有机化学剂材料成本高,对油藏温度的适应性较差,易老化,有效期短,固结后地层渗透率明显下降,产能损失大。 (3)焦化防砂
消失模铸造缺陷及解决措施
铸造缺陷及解决措施: 1、砂眼(或白灰):是铸件的致命缺陷,重则报废。要做到:①、 浇口杯、直浇道、横浇道、内浇道与铸件封闭结合严密。如不严密,在负压的作用下就会吸入砂子,所以装箱者一定要精心操作,把好各关口。任何一个薄弱环节或疏忽都会造成此类缺陷。②浇注系统多刷一遍涂料以增强其强度。③涂料的强度、透气性、刚度、耐火度、暴热抗烈性也很重要,因为在运输、装填砂、震动时都会出现破坏、变形、开裂、脱落。④震实时,开始幅度要小,待填满砂时再振幅大些。⑤浇口杯无浮砂、尘土等杂物。⑥浇注时,浇包嘴尽量靠近浇口杯,以免压力头过大。⑦负压过大,使金属液流经开裂、裂纹处时,吸入干砂和杂物可能性加大,粘砂严重。⑧过快的充型速度使冲刷力加大。 2、气孔:①浇注温度低,充型前沿金属液不能使泡沫充分分解汽 化,未分解的残留物质来不及浮集到上面及冒口中,汽化分解生成的气体及残留物不能及时排出铸型而凝固在铸件中,另外,摸样分解不充分,液相残留物会堵塞涂料层,使热解气体排出受阻,腔内形成反压力,充型流动性下降,凝固快。②涂料透气性差或负压不足,砂子透气性差,不能及时排除型腔内的气体及残留物,在充型压力下形成气孔。③浇注速度慢,浇口杯未充满,暴露直浇道卷入空气,吸入杂质,形成携裹气孔和渣孔。④浇杯容量小,金属液形成涡流,侵入空气生成气孔。⑤浇口杯及浇注系统之间的连接处密封不好,尤其是直浇道和浇口杯。在负压作用下很容
易形成夹砂及气孔。⑥型砂粒度太细,粉尘含量高,透气性差,负压管道内部堵塞,造成负压度失真,使型腔周围的负压值远低于指示负压,汽化物不能及时排出涂料层而形成气孔或皱皮。⑦合理的浇注工艺和负压度。消失模浇注工艺是以充满封闭直浇道为原则,不能忽快忽慢、紊流、断流,更不允许暴露直浇道。浇注速度,尤其是在行车提升停顿瞬间力求平衡,不断流。进入尾期慢慢收包,使渣、气、及汽化残留物有充分时间浮集到浇冒口中。负压度过大,加剧金属液渗透粘砂,并造成附壁效应,不利于液相泡沫被涂层吸附,生成很多气孔。适宜的负压是排气的保证,也是防止粘砂的措施。⑧模样粘合应选用专用的热熔胶或冷胶,在保证粘牢的情况下,用量越少越好。尽量避免使用汽化缓慢的乳胶。 2012-1-13于万钢机械有限公司 卢山河
呋喃树脂砂铸件常见缺陷及预防措施
一、气孔与针孔 1.产生原因 1.1树脂添加量过多,树脂中氮含量过高。 1.2醇基涂料的溶剂中有变质酒精、含水分较多或涂料的浓度太低,点火后干燥不彻底。 1.3水基涂料干燥不充分。 1.4造型互艺方案不良。其中影响较大的因素有:浇注速度过慢;通气方案不良;浇注系统尺寸合比例不当;压头太低。 1.5回收再生砂的灼减量过高。 1.6造型(芯)后尚未充分固化就过早合箱浇注,造成发起量过大。 1.7造型操作不当。如芯铁外露,芯头钻铁等。 2.气孔类缺陷的预防措施针对以上各条产生原因,采取以下相应对策: 2.1降低树脂添加量: 2.11 2.12 2.13 2.14 选择含N 量较低的树脂,选用粒型圆整、粒度适中、含微粉量低、耗 酸量低的原砂;添加偶联剂; 选用强度性能好的树脂及适当的固化剂等,尽可能将树脂添加量将至砂重的1.2%以下。 2.2涂料 2.2.1重视涂料
的溶剂质量;酒精快干涂料的酒精浓度一般不小于95%。2.2.2涂刷前对涂料充分搅拌,浓度应大于30“ B;e 2.2.3涂刷料后即时点火干燥。 224使用水基涂料后应在小于180C温度下烘烤1小时?2小时以上,务必使涂料充分干燥。 2.3制定互艺方案时要注意提高浇注速度,合理有效的设计通气;掌握快速、封闭、底注、不紊流的设计原则。 2.4回用砂灼减量控制在 3.0%?3.5%以下。主要措施有尽量降低砂铁比,选择优良的再生设备,注意再生砂的管理。 2.5型芯最好隔天使用,铸型也应在造型4小时?6小时以后再上涂料及合箱浇注。 2.6 严格控制造型(芯)、配模的操作过程。芯骨不要外漏,芯头要有防止钻铁措施,以免呛火造成气孔缺陷。 以上主要讨论了因呋喃铸型本身而造成的侵入型气孔缺陷,实际生产中因铁水温度及溶炼质量等因素引起的气孔比例也不小,要注意具体分析、对症下药。 二、机械粘砂与脉纹 1.产生原因 1.1型砂骨料粒度分布不当及造型(芯)时紧实度太低。 1.2涂料耐火度低、涂层厚度不够。 1.3新砂用量较大时易产生渗铁与脉纹,尤其当新砂的SiO 2 含量很高时。 1.4造型操作不当引起的型砂强度过低、表面稳定性差,促使粘砂脉纹的发生。 如使用超过了可使时间的型砂,连续式混砂机的头砂尾砂充当面砂,修模型砂(芯)表面时引起的表面稳定性降低、砂温过高等。 2.预防措施
国内外防砂技术现状与发展趋势
本科生毕业设计(论文) 论文题目:油井防砂工艺技术研究 学生姓名:××× 学号: 系别:石油工程系 专业年级: 指导教师:
目录 第一章绪论 .................... 错误!未定义书签。 1. 研究的目的和意义....................................................................................... 错误!未定义书签。 2. 国内外研究现状........................................................................................... 错误!未定义书签。 3. 研究的目标、技术路线及所完成的工作................................................... 错误!未定义书签。 3.1 研究的目标......................................................................................... 错误!未定义书签。 3.2 技术路线............................................................................................. 错误!未定义书签。 3.3 本文所完成的工作............................................................................. 错误!未定义书签。第二章出砂原因和出砂机理 ...... 错误!未定义书签。 1. 出砂因素....................................................................................................... 错误!未定义书签。 1.1 地质因素............................................................................................. 错误!未定义书签。 1.2 开采因素............................................................................................. 错误!未定义书签。 1.3 完井因素............................................................................................. 错误!未定义书签。 2. 油层出砂机理............................................................................................... 错误!未定义书签。 2.1 剪切破坏机理..................................................................................... 错误!未定义书签。 2.2 拉伸破坏机理..................................................................................... 错误!未定义书签。 2.3 微粒运移............................................................................................. 错误!未定义书签。第三章稠油井防砂及配套工艺技术研究错误!未定义书 签。 1. 孤岛油田稠油热采区块开发概况............................................................... 错误!未定义书签。 2. 稠油热采一次防砂工艺的研究................................................................... 错误!未定义书签。 2.1 稠油热采一次防砂工艺防砂机理..................................................... 错误!未定义书签。 2.2 割缝管防砂工艺的研究..................................................................... 错误!未定义书签。 3. 配套工艺技术研究....................................................................................... 错误!未定义书签。 3.1 高温防砂剂强度及耐温性能的研究................................................. 错误!未定义书签。 3.2 射孔工艺............................................................................................. 错误!未定义书签。 3.3 深部处理油层技术............................................................................. 错误!未定义书签。 4. 现场应用效果分析....................................................................................... 错误!未定义书签。 5. 小结............................................................................................................... 错误!未定义书签。第四章结论及建议 .............. 错误!未定义书签。 1. 结论............................................................................................................... 错误!未定义书签。 2. 建议............................................................................................................... 错误!未定义书签。致谢 ............................ 错误!未定义书签。 参考文献 ........................ 错误!未定义书签。
呋喃树脂砂铸钢件的粘砂机理及预防措施研究
呋喃树脂砂铸钢件的粘砂机理及预防措施研究 文章主要研究了应用呋喃树脂砂生产大型、特大型、特殊结构铸钢件粘砂的形成机理,分析了造成粘砂的主要因素,并总结出多种防粘砂的措施及方法,通过以上措施的实施来消除和减少铸件的粘砂缺陷,以提高铸件表面质量。 标签:呋喃树脂砂;大型铸钢件;粘砂 壁厚较大的大型铸钢件和结构复杂的铸件部位极易产生表面粘砂缺陷,在铸件的表面形成一层钢水和型砂的混合物粘砂层,不仅给后序的清理和加工带来极大困难,而且对于一些特殊材质的产品在处理表面粘砂的过程中还极易产生次生裂纹缺陷,从而造成极大地经济损失。文章着重分析了大型铸钢件的粘砂机理,并且总结了近几年来采取的一些有效措施,希望对其他兄弟制造单位起到一些借鉴的作用。 1 粘砂的形成原因 1.1 机械粘砂 金属液体渗入砂型表面孔隙中凝固后将砂粒机械地钩连在铸件表面上。渗入的液态金属越多、越深机械粘砂越严重,其中两种力对比和变化,决定了铸件机械粘砂倾向,必定有一种力促使液态金属渗入砂型孔隙,一种力阻止渗入,如果金属液对铸型材料不润湿,发生渗透所需压力P应为: P=2δcosθ/r 式中,δ-金属表面张力;θ-液体金属与铸型材料间的润湿角;r-砂粒孔隙半径。 1.2 化学粘砂 铸件的化学粘砂是金属液体表面被氧化,生成氧化铁等金属氧化物,再和型砂中的SiO2进行化学反应,生成低熔点的铁硅酸盐渣液,凝固后与砂粒一起牢固地粘附在铸件表面上的结果。钢液表面极易氧化形成氧化层,主要是FeO,熔点为1370℃,能润湿石英砂,易于渗入砂型,并和二氧化硅反应生成低熔点物质硅酸亚铁,其熔点为1205℃,砂型中若含有碱性物质,则会加剧铸件的化学粘砂,是因为形成了易熔的硅酸盐,由Na2O-FeO-SiO2系统的状态图可知其中熔点最低的可低于500℃。低熔点物生成后,由于流动性好又能润湿型壁故易于渗入砂型孔隙内,扩大氧化铁和型砂的作用面积,加剧化学粘砂,化学反应的结果又扩大了砂粒间孔隙更有利于低熔点物质向砂型深处渗入,从而将金属和砂型联成一体。 2 预防粘砂的主要措施
防砂处理
一、防砂工艺 1. 出砂的原因 1.1 出砂的地质条件(内因) a. 地层地质年代新(第三系、第四系); b. 埋藏浅(一般小于1500m),压实作用差; c. 地层胶结强度低(可由室内岩芯实验确定); d. 机杂及胶结物含量低; e. 以泥质胶结为主的敏感性(水敏和速敏)储层,遇水后易发生膨胀和运移; f. 高孔(25.0%~30.0%)和高渗(数百到数千 md); g. 往往是稠油油藏,流动阻力大; h. 断块油藏——断层发育,构造应力大; 1.2 出砂的开发因素(外因) a. 地层压力降低,出砂; b. 完井方式与参数; c. 生产压差:避免压力激动和过大压差; d. 油井含水:含水上升,出砂加剧; e. 地层损害:渗透率降低,出砂; f. 钻井/作业:液体漏失、地层损害。
2. Palogue油田的出砂预测 2.1 组合模量法 储层岩石强度是决定油气井是否出砂的主要因素,它与其弹性参数如剪切模量、体积模量有良好的相关性。美国莫尔比石油公司提出的组合模量法能很好的预测油藏是否出砂。组合模量法在墨西哥湾和北海已广泛应用,当Ec大于3×106psi时油气井不出砂。 E c =(9.94×108ρ r )/△t2 c 式中: E c ----岩石组合模量(岩石密度、声波时差函数),×1.4503×106psi ρ r ----岩石密度,g/cm3 t----岩石纵波时差,μs/m 胜利油田通过现场应用,最终得到出砂界限值: E c >3×106psi,在正常生产中油气井不出砂; 2.03×106psi 常见铸件缺陷及其预防措施 常见铸件缺陷及其预防措施(序+缺陷名称+缺陷特征+预防措施) 1 气孔在铸件内部、表面或近于表面处,有大小不等的光滑孔眼,形状有圆的、长的及不规则的,有单个的,也有聚集成片的。颜色有白色的或带一层暗色,有时覆有一层氧化皮。降低熔炼时流言蜚语金属的吸气量。减少砂型在浇注过程中的发气量,改进铸件结构,提高砂型和型芯的透气性,使型内气体能顺利排出。 2 缩孔在铸件厚断面内部、两交界面的内部及厚断面和薄断面交接处的内部或表面,形状不规则,孔内粗糙不平,晶粒粗大。壁厚小且均匀的铸件要采用同时凝固,壁厚大且不均匀的铸件采用由薄向厚的顺序凝固,合理放置冒口的冷铁。 3 缩松在铸件内部微小而不连贯的缩孔,聚集在一处或多处,晶粒粗大,各晶粒间存在很小的孔眼,水压试验时渗水。壁间连接处尽量减小热节,尽量降低 浇注温度和浇注速度。 4 渣气孔在铸件内部或表面形状不规则的孔眼。孔眼不光滑,里面全部或部分充塞着熔渣。提高铁液温度。降低熔渣粘性。提高浇注系统的挡渣能力。增大 铸件内圆角。 5 砂眼在铸件内部或表面有充塞着型砂的孔眼。严格控制型砂性能和造型操 作,合型前注意打扫型腔。 6 热裂在铸件上有穿透或不穿透的裂纹(注要是弯曲形的),开裂处金属表皮氧化。严格控制铁液中的 S、P含量。铸件壁厚尽量均匀。提高型砂和型芯的退让性。浇冒口不应阻碍铸件收缩。避免壁厚的突然改变。开型不能过早。不能 激冷铸件。 7 冷裂在铸件上有穿透或不穿透的裂纹(主要是直的),开裂处金属表皮氧化。 8 粘砂在铸件表面上,全部或部分覆盖着一层金属(或金属氧化物)与砂(或涂料)的混(化)合物或一层烧结构的型砂,致使铸件表面粗糙。减少砂粒间隙。适当降低金属的浇注温度。提高型砂、芯砂的耐火度。 9 夹砂在铸件表面上,有一层金属瘤状物或片状物,在金属瘤片和铸件之间夹有一层型砂。严格控制型砂、芯砂性能。改善浇注系统,使金属液流动平稳。 大平面铸件要倾斜浇注。 10 冷隔在铸件上有一种未完全融合的缝隙或洼坑,其交界边缘是圆滑的。提 高浇注温度和浇注速度。改善浇注系统。浇注时不断流。 11 浇不到由于金属液未完全充满型腔而产生的铸件缺肉。提高浇注温度和浇 注速度。不要断流和防止跑火。 夹砂、鼠尾、沟槽 形成原因:1)金属流股的热量在被烘烤的砂型表层形成低强度高湿度水份 熔模铸件常见缺陷分析及处理 ——表面缺陷类之一 化学粘砂与机械粘砂 潘玉洪 摘要:机械粘砂和化学粘砂是熔模铸件常见的铸造缺陷之一,它是指在铸件的表面上牢固地粘结着一层金属与型壳材料结合物。本文重点阐述熔模铸件化学粘砂和机械粘砂的外部特征,产生的部位、机理以及主要原因,同时提出了从熔模铸造的选材、制壳工艺、焙烧工艺、熔炼工艺等方面采取实用、有效的对策,从而提高熔模铸件的合格率。 关键词:熔模铸件;粘砂缺陷;分析与处理 1.引言 在熔模铸造生产中,当灼热的金属液浇入型壳中,金属液与型腔表面就发生极为复杂的、物理的和化学的相互作用,往往导致铸件产生各种类型的铸造缺陷,机械粘砂和化学粘砂就是其中之一。 如果铸件局部产生粘砂,还不至于使铸件报废;但它影响了铸件的外观,增加了清理铸件的工时和劳动量;尤其对于需要机械加工的铸件,粘砂会给切削加工带来很多的麻烦,提高了生产成本,甚至影响正常的生产进度和交货期。所以,熔模铸造工作者必须在生产中尽量减少,甚至消除铸件的机械粘砂和化学粘砂缺陷。 目前,国内外一些资料把粘砂分为两种、三种或四种,作者认为分为化学粘砂和机械粘砂两种比较合适。 2.化学粘砂 2.1概述 2.1.1特征 金属液在高温下与型腔表面发生相互作用,冷凝后在铸件的表面上牢固地粘结一层难以清除的金属液与型壳材料之间化学反应生成粘砂。如图1: 图1 化学粘砂 左A-化学粘砂右-正常 2.1.2 部位 常常产生在大型铸件、铸件的厚大部位,铸件浇注部位的下端,靠近内浇口或冒口等部位。 2.1.3 机理 按照化学粘砂产生的主要原因,把化学粘砂的形成过程分为三种情况,如图2: 图2 化学粘砂形成过程的示意图 A型:a—金属液浇入型腔中; b—金属液被型砂中的空气或水分氧化,生成低熔点的、与石英砂浸润能力很强的氧化铁: 2Fe +O2=2FeO (液、固)(气)(液、固) c—氧化铁与石英砂(粉)作用: 2FeO+SiO2=2FeO ·SiO2 生成液态的铁硅酸盐(也称铁橄榄石),因为其熔点低(为1205℃)、流动性好、 国内外防砂技术现状与发展趋势 概述 疏松砂岩油藏分布范围广、储量大,这类油藏开采中的主要矛盾之一是油井出砂。因此,油井防砂工艺技术的研究和发展对疏松砂岩油藏的顺利开发至关重要。目前国外在油气井防砂方面主要以机械防砂为主,约占防砂作业的90%,随着油田的进一步开发,现在又相继研究开发各类型的滤砂管、可膨胀性割缝筛管和压裂防砂、过油管防砂等防砂工艺技术。化学防砂六十年代在美国墨西哥湾地区曾占据防砂作业的主导地位,但由于机械防砂的完善和发展,其主导地位逐渐被取代。进入九十年代后,性能较好的固砂剂不断出现,化学防砂的前景又趋看好。 国内防砂工艺技术的发展已有数十年的历史,辽河油田、胜利油田、大港油田在油气井防砂方面也作了大量的工作,丰富和提高了国内防砂工艺技术水平。目前已形成机械防砂工艺、化学防砂工艺和复合防砂工艺三大体系的油气水井防砂工艺技术。其中辽河油田防砂中心,研制开发了复合射孔防砂技术,为国际领先水平。随着辽河油田稠油开发比重的增加,辽河油田的出砂情况变得越来越复杂,防砂治理工作难度也越来越大,辽河油田结合油井出砂特点,开展了防砂基础理论及试验研究,主要包括:出砂机理分析、防砂数据库和出砂预测软件的建立、防砂机具性能评价研究。先后研制开发了机械、化学、复合型防砂工艺技术近20项,主要有TBS筛管防砂技术、MC-Ⅰ组合式筛管防砂技术、塑料筛管防砂技术、激光割缝筛管高压砾石充填深部防砂技术、压裂防砂技术、复合射孔防砂技术、焦碳人工井壁防砂技术、泡沫树脂液防砂技术、乳液树脂固砂技术、桃壳人工井壁防砂技术、高温固砂技术、携砂采液技术、低压井冲砂技术。 一、机械防砂 目前机械防砂主要化分两类:一类是下入防砂管柱挡砂,如割缝衬管、绕丝筛管、胶结成型的滤砂管、双层或多层筛管等。这类防砂方法简单易行,但效果差,寿命短。原因是防砂管柱的缝隙或孔隙易被进入井筒的细地层砂所堵塞。另一类是下入防砂管柱后再进行充填,充填材料多种多样。最常用的是砾石,还可用果壳、果核、塑料颗粒、玻璃球或陶粒等。这种防砂方法能有效地把地层砂限制在地层内,并能使地层保持稳定的力学结构,防砂效果好,寿命长。 相对来说,机械防砂对地层的适应能力强,无论产层厚薄、渗透率高低,夹层多少都能有效的实施;在老油井作业中,还可起到恢复地层应力的作用,从而延长生产周期,使出砂井能得到充分的利用。加上机械防砂成功率高,相对成本较低等优点,目前应用十分广泛。 1国外机械防砂技术 国外油气井防砂工艺技术研究起步较早,最初采用限产的方法来控制油气井出砂,1932年开始采用砾石充填方法。目前国外在油气井防砂方面主要以机械防砂为主,其中绕丝筛管砾石充填经过不断的完善和发展,到八十年代已发展成为一项较成熟的技术。如美国的贝克—休斯公司、道威尔—斯伦贝谢公司、哈里巴顿公司、沙龙公司、雪弗龙公司等都拥有自己专门的防砂器材、施工设备和施工工艺,从砾石充填工具、封隔器、滤砂管、泵送设备到施工液体、化学药剂、技术咨询、现场服务等形式一条龙服务。随着油田的进一步开发,为满足各种类型的油气井防砂需求,现在国外又相继研究开发出各种类型的滤砂管和多种防砂工艺技术。 粘砂问题分析 诸位好! 咱们区铸铁分厂目前生产产品,产品内腔时常出现粘砂、肌瘤和铸砂,有时还伴随着颗粒和尖角毛刺,产品在清理工段形成瓶颈,同时给检验带来很大难度,咱们分厂清理工段使用各种形式的清理工具,逐件用手摸后确定部位再清理清除(有时操作者手指都要磨破),到检验工段,检验员使用手电筒查看内腔,发现不合格唯一处理方式为返工返修(由于咱们执行的是零缺陷,生锈、铸砂的产品要重新喷砂,产品有的经过数次喷砂字迹都没了内腔还未处理彻底)。咱们的产品流入客户端也发生了多次投诉,怎样解决问题,从根本上消除隐患。首先咱们要了解粘砂。 粘砂分为机械粘砂又称为金属液渗透粘砂和化学粘砂两种形式的粘砂定义和特征为: 机械粘砂又称为金属液渗透粘砂,是由液态金属或金属氧化物通过毛细管渗透或气相渗透方式钻入型腔表面砂粒间隙,在铸件表面形成的金属和砂粒机械混合的粘附层。清铲粘砂层时可见金属光泽。机械粘砂表面呈海绵状,牢固地粘附在铸件表面,多发生在砂型和砂芯表面受热作用强烈及砂型紧实度低的部位,如浇冒口附近,铸件厚大截面、内角和凹槽处。 鉴别方法 肉眼外观检查。机械粘砂可发生在各种砂型中,表面呈海绵状,可用喷、抛丸法清理,有时也要进行打磨。树脂砂型粘砂通常为机械粘砂。 形成原因 1.型砂和芯砂粒度太粗 2.砂型和砂芯的紧实度低或不均匀 3.型、芯的涂料质量差,涂层厚度不均匀,涂料剥落 4.浇注温度和浇注高度太高,金属液动压力大 5.上箱或浇口杯高度太高,金属液静压力大 6.型砂和芯砂中含粘土、粘结剂或易熔性附加物过多,耐火度低,导热性差 7.型、芯砂中含回用砂太多,回用砂中细碎砂粒、粉尘、死烧粘土、铁包砂太多,型砂烧结温度低 8.铸件开箱落砂太晚,形成固态热粘砂,尤其是厚大铸件和高熔点合金铸件 9.金属液流动性好、表面张力低。例如,铜合金中磷、铅含量过高,铸钢中磷、硅、锰含量过高 10.树脂砂型、芯表面未刷涂料或涂料质量差,涂层厚薄不均,浇注时砂粒间树脂膜气化,形成毛细通道,在金属液静压力、蒸气压和表面张力作用下,金属液或金属蒸气渗入毛细通道,形成机械粘砂 11.金属液中的氧化物和低熔点化合物与型砂发生造渣反应,生成硅酸亚铁、铁橄榄石等低熔点化合物,降低金属液表面张力并提高其流动性,使低熔点化合物和金属液通过毛细管作用机制,渗入砂粒间隙,并在渗透过程中,不断消蚀砂粒,使砂粒间隙扩大,导致机械粘砂 12.浇注系统和冒口设臵不当,造成铸型和铸件局部过热。 防止方法 1.使用耐火度高的细粒原砂 2.采用再生砂时,去除过细的砂粒、死烧粘土、灰分、金属氧化物、废金属、铁包砂及其他有害杂质,提高再生砂质量。定期补充适量新砂 3.水是强烈氧化剂,应严格控制湿型砂水分,加入适量煤粉、沥青、碳氢化合物等含碳材料,在砂型中 防砂方法分类及选择 1)防砂分类方法 按防砂机理及工艺条件,防砂方法大致分为机械防砂、化学防砂、拱砂防 砂以及其他方法。 (1)机械防砂:又可细分为两类。 ①第一类:仅下入防砂用的滤砂管柱,如割缝衬管、绕丝筛管,各类地面 预制成型的滤砂器(如双层预充填筛管、树脂砂粒滤砂管、金属棉纤维滤砂管、多孔陶瓷滤砂管等)。这种方法简单易行,施工成本低,缺点是滤砂器易堵塞, >0.1mm)。不能阻止地层砂进入井筒,有效期短,只宜用于中、粗砂岩地层(d 50 ②第二类:在下入绕丝筛管(或其他滤管)后,再用高渗透砾石充填筛管和井壁之间的油井环空,并部分挤入井筒周围地层,形成多级过滤屏障,阻止地 层砂运移。 (2)化学防砂:通过向套管外地层挤入一定数量的化学剂或化学剂与砂浆的 混合物,达到充填、胶固地层的目的,提高地层强度,减少出砂。按工艺性可 分为两种: ①胶固地层:挤入树脂或其他化学固砂剂,直接将地层砂固结; ②人工井壁:用树脂砂浆液、预涂层砾石、水带干灰砂、水泥砂浆、乳化 水泥等挤入井眼周围地层中,固结后建立一个可渗透的人工井壁,阻止地层出砂。 化学防砂一般适用于薄层短井段,若井段太长,视情况采取措施分段施工。此法对粉细砂岩的防砂效果由于机械防砂,优点是井筒内部不留下任何机械装置,便于后期处理;缺点是成本太高,树脂等化学材料易老化寿命短,固结后 底层渗透率下降明显,产能损失大,固现场目前应用程度远低于绕丝筛管砾石 充填类的机械防砂。 (3)拱砂防砂:这是一种油(气)井射孔完成后,不在下入任何机械装置或挤入化学剂的防砂方法。它防砂的实质是要靠一种机械作用力强迫压实出砂 的裸眼井壁,以提高井眼周围的地层应力水平达到甚至超过地层未钻开前的原 始应力。这样可以减少出砂的可能性,油井投产时,地层砂流入射孔处,可自 然堆积,形成具有一定承载能力的砂拱,类似于桥梁的桥拱,可以进一步阻止 底层出砂。此方法优点在于井筒内无任何机械装置,容易进行补救性作业,此外,底层渗透率未受显著伤害,故油井防砂后,产能损失小。缺点是砂拱稳定 性差,防砂效果不易保证,一般只用于出砂不严重的中、粗砂岩和中、底产井;不适用于粉细砂岩、流沙层和高产井。 2)防砂方法的选择 (1)选择原则: 大型铸钢件粘砂的研究 [摘要]本文分析了铸钢件粘砂的原因和机理,结合现场的实际情况,提出了切实可行的工艺措施,最终大幅度地减少了铸件粘砂,提高了铸件的质量,对防止铸件粘砂具有实际的意义。 【关键词】铸钢件;粘砂;工艺措施 一、前言 铸件粘砂已经成为铸造行业的普遍现象,由于各厂家工艺方法的不同,粘砂现象有轻有重,我厂粘砂问题比较严重。粘砂问题所产生的一系列质量问题已经严重的影响到我厂的铸件出厂进度,长久下去不仅会影响到客户对我厂的信赖程度,同时我们也浪费人力和物力,严重加大了成本。出于对这样的现状,有必要对型砂粘砂过程进行透彻的研究。不仅要从粘砂本质机理方面进行研究,同时更重要的是要根据现场的实际生产状况和铸件特点与理论进行有机的结合。 二、粘砂现象 机械粘砂是指金属液渗入砂型或砂芯砂粒间隙中,与砂烧结并粘附在铸件表面,金属液有时会渗透到砂芯的整个截面,致使内腔阻塞,这种粘砂往往是不可能清除的,铸件不得不报废;化学粘砂是指金属液化学反应生成的金属氧化物与造型材料作用形成的粘着力很强的硅酸铁浮渣,它多产生在铸件内浇口或厚壁处,尤其当砂型或砂芯较薄而铸件较厚时易产生。 我厂以生产大型铸钢件为主,尤其是搬入新厂区以来,随着产能的提升,铸件越来越大型化,加上型砂由原来的石灰石砂变成酯硬化水玻璃砂,随之而来的铸件粘砂问题日益突出。粘砂总体表现为铸件的里腔处,冒口根部,圆角处,厚大的热节处,还有一些铸件的外皮处。粘砂的案例为半齿轮和整齿轮铸件冒口下的轮辋处和双辅板轮中层砂芯处粘砂,下架体外皮筋的圆角处粘砂,中空轴的R 区和里腔粘砂,锻锤机身的大冒口根部粘砂。这些铸件有很大一部分是我厂的传统产品,严重的粘砂影响了供货周期和产品外观质量,更严重的是清理粘砂过程中容易铸件容易产生裂纹报废,可以说粘砂问题已严重地影响到企业的生存和发展。 三、粘砂原因 1、足够的压力使金属液渗入砂粒之间 (1)较高的金属液静压力头。即由铸件浇注高度和浇注系统形成的压力。如该压力超过砂粒间隙之间毛细现象形成的抵抗压力。即P毛=2σCOSθ/r,式中P毛为毛细压力;σ为金属液表面张力;θ为金属液毛细管的润湿角;r为毛细管半径。就会形成机械粘砂。静压力头超过500mm,铸造用砂又较粗,多数会产生机械粘砂。上式也说明r越大,即砂粒粒度越粗,P毛越小,即较易产生机械粘砂; (2)金属液在铸型内流动形成的动压力; (3)铸型“爆”或“呛”。即铸型浇注时释放的可燃气体与空气混合并被炽热金属液点燃所形成的动压力。 2、机械粘砂一经开始,即便压力减小,金属液渗透还会继续进行,直到渗透金属液前沿凝固。即金属液温度低于固相线温度,渗透方可停止。 3、化学粘砂最通常的原因是砂型和制芯用原材料耐火度、烧结点低;石英砂不纯;没有使用涂料或使用不当;浇注温度过高;浇注不当致使渣子进入铸型 化学防砂方法与原理及其适用性 一概述 化学防砂是向地层挤入一定量的化学剂充填于地层孔隙中以达到充填和固结地层提高地层强度的目的。 方法一般分为人工胶结地层和人造井壁两种防砂方法,还有一些其他的固砂方法。 原理前者是向地层注入各类树脂或各种化学固砂剂直接将地层固结它对疏松油层出砂特别适用。后者是把具有特殊性能的水泥、树脂、预涂层砾石、水带干灰砂或化学剂挤入井筒周围地层中这些物质凝固后形成一层既坚固又有一定渗透性和强度的人工井壁达到防止油层出砂的目的人工井壁法对由于出砂造成套管外油层部位坍塌所造成的亏空井防砂比较适宜。 适用性它适用于渗透率相对均匀的薄层段地层防砂而层内差异大的厚层化学防砂施工由于注入剂锥进不均和重力作用易造成固结不均影响防砂效果。化学防砂还可适用于合采井上部地层防砂。化学防砂优点是施工后井内无遗留物并可用于异常高压井层的防砂缺点是对地层渗透率有一定伤害特别是重复施工时。另外注入剂存在老化现象使其有效期有限成功率不如机械防砂化学防砂不适用于裸眼井防砂。 我国疏松砂岩油藏分布范围广、储量大油气井出砂是这类油藏开采的主要矛盾。出砂往往会导致砂埋油层或井筒砂堵或油气井停产作业、使地面或井下的设备严重磨蚀、砂卡及频繁的冲砂检泵、地面清 罐等维修使工作量巨增既提高了原油生产成本又增加了油田管理难度。防砂是开发易出砂油气藏必不可少的工艺措施之一对原油稳定生产及提高开发效益起着重要作用。 二方法 1.人工胶结法 人工胶结防砂法是指从地面向油层挤入液体胶结剂及增孔剂,然后使胶结剂固化,在油层层面附近形成具有一定胶结强度和渗透性的胶结砂层,达到防砂的目的。目前已使用的方法主要有酚醛树脂溶液、酚醛溶液地下合成、脲醛树脂等方法。 1.1 酚醛树脂胶结砂层 酚醛树脂胶结砂层是以苯酚和甲醛为主料,以碱性物质为催化剂,按比例混合,经加热熬制成的树脂,将其溶液挤入砂岩油层,以柴油增孔,再挤入盐酸作固化剂,在油层温度下反应固化,将疏松砂岩胶结以防止油水井出砂。该方法适用于早期出砂的油水井防砂,施工工艺简单,但成本较高,施工作业时间长。 1.2 酚醛溶液地下合成防砂 酚醛溶液地下合成防砂是将加有催化剂的苯酚与甲醛,按比例配料搅拌均匀,并以柴油为增孔剂配成树脂溶液,酚醛溶液挤入出砂层后,在油层温度下逐渐形成树脂并附着于砂粒表面,固化后将油层砂胶结牢固,而柴油不参加反应为连续相充满孔隙,使胶结后的砂岩保持良好的渗透性,从而起到提高砂岩的胶结强度,防止油气层出砂的方法。该方法为油井先期和早期的防砂方法,适用于温度高于60℃,粘土含量较低的中细砂岩油层。平均有效期二年以上,施工较为简单, 防砂方法 一、项目简介 防砂管结构:精密复合防砂筛管具有防砂效果好,结构简单、使用时效长、渗流面积大、出油率高、作业方便等特点。该产品从内到外由中心管、防砂过滤套、不锈钢外保护套等组成。中心管采用API标准套管或油管,防砂过滤套可分别用金属丝编织方孔网、金属丝编织密纹网,也可根据实际技术要求为用户设计过滤面积大,可自洁、不宜堵塞的滤材结构。产品可用于各类油、气、水井的防砂,以达到保护井下及地面设备的目的,提高出油率延长油井的使用寿命。 性能特点:这种筛管具有极佳的整体强度和抗变形能力。空隙度最高可达90%,抗堵塞能力强,渗透率高、耐高温、抗腐蚀、防砂范围广,适用于各种不同油层。有效的控制砂的粒径,过滤效率达99.5%.。使用性能可靠,是机械防砂领域中的高新技术之一。 二、以准噶尔盆地出砂分布情况为例予以简要说明 浅层稠油藏处于准噶尔盆地西北缘油气富集区,属砂岩油藏,由于地层本身结构疏松,加上采取的注高温高压蒸汽的强采方式,致使在油田开发的同时就伴随着不同程度的出砂,随着开发的延续,出砂井日益增多,出砂情况也更趋复杂、加剧。油井出砂致使油井生产周期缩短,油井产量大减,甚至造成油井停产、报废,严重制约了油井潜能的充分发挥,同时也使开采设备、地面工艺情况迅速恶化,严重影响了油田的高效稳产。 三、机械防砂工艺应用现状 1、防砂技术现状及应用情况 对于出砂油藏,防砂是油气藏开采不可缺少的环节,对原油的稳定开采起着重要的作用。进入20世纪90年代以来,随着加工工艺的不断进步以及防砂认识的深化,积极研发出了大量的新工艺、新方法,特别是在机械防砂方面,取 得飞速的发展。由于机械防砂较化学防砂价格便宜,且对地层无污染,目前国内外防砂是以机械防砂为主。 浅层稠油所采用的机械防砂工艺按挡砂程度的不同可分为:机械防砂工艺和机械排砂工艺。 1.1、机械防砂工艺常见铸件缺陷及其预防措施
熔模铸件缺陷分析--粘砂
国内外防砂技术
粘砂和砂眼
防砂方法分类及选择
大型铸钢件粘砂的研究
化学防砂的方法与原理及其适用性
防砂方法