高韧性球墨铸铁生产工艺及应用_王永振
固溶强化球墨铸铁生产工艺

固溶强化球墨铸铁生产工艺固溶强化是一种常用的球墨铸铁生产工艺,通过对球墨铸铁进行固溶处理,可以显著提高其力学性能和耐磨性能。
本文将详细介绍固溶强化球墨铸铁的生产工艺及其优点。
一、固溶强化球墨铸铁的生产工艺1. 原料准备:选择高品质的生铁和合适的合金元素作为原料,确保球墨铸铁的化学成分符合要求。
2. 熔炼:将生铁和合金元素放入高炉或电炉中进行熔炼,控制好熔炼温度和时间,使合金元素充分溶解于铁液中。
3. 铸造:将熔炼好的铁液倒入球墨铸铁模具中,通过冷却凝固形成球墨铸铁件。
4. 固溶处理:将球墨铸铁件放入固溶炉中,加热至一定温度进行固溶处理。
固溶温度一般为球墨铸铁材料的临界温度,不同的合金元素有不同的固溶温度。
5. 淬火处理:固溶处理后的球墨铸铁件需要进行淬火处理,以获得良好的力学性能。
淬火温度和时间需要根据具体材料和要求来确定。
6. 机械加工:经过固溶强化处理的球墨铸铁件可以进行机械加工,如铣削、车削、磨削等,以达到所需的形状和尺寸。
二、固溶强化球墨铸铁的优点1. 提高强度和硬度:固溶处理可以使球墨铸铁中的合金元素均匀溶解,形成固溶体,从而提高材料的强度和硬度。
2. 提高耐磨性:固溶强化处理可以使球墨铸铁中形成更细小、更均匀的碳化物,从而提高材料的耐磨性和抗磨损能力。
3. 改善抗拉强度和韧性:固溶强化可以改善球墨铸铁的抗拉强度和韧性,使其在受力时更加稳定和可靠。
4. 提高抗疲劳性能:经过固溶强化处理的球墨铸铁具有较好的抗疲劳性能,能够在长期受到循环载荷时不易发生断裂和损伤。
5. 优化加工性能:固溶处理可以消除球墨铸铁中的残余应力,减少加工变形和裂纹的产生,提高材料的加工性能。
固溶强化是一种能够显著提高球墨铸铁性能的生产工艺。
通过固溶处理和淬火处理,可以使球墨铸铁具有更好的强度、硬度、耐磨性和韧性,适用于各种机械零部件和工程结构的制造。
球墨铸铁生产工艺控制

球墨铸铁生产工艺控制球墨铸铁是一种使用球墨铸铁母合金进行球化处理后浇铸而成的铸铁材料。
球墨铸铁具有良好的机械性能、高强度和耐磨性能,被广泛应用于汽车、机械、建筑和航空等领域。
在球墨铸铁生产工艺中,控制各个环节的参数和条件对于保证产品质量至关重要。
本文将重点探讨球墨铸铁生产工艺的控制。
首先,球墨铸铁生产工艺的控制从材料选择开始。
球墨铸铁的母合金应具有合适的成分和适宜的球化剂含量。
合金成分的选择应根据所需的性能要求和使用环境进行调整。
球化剂含量的控制则直接影响到球化效果。
过高或过低的球化剂含量都会导致球墨铸铁的性能下降。
因此,在材料选择阶段就需要有明确的控制要求。
其次,在球墨铸铁的熔炼过程中需要控制炉温和熔化时间等参数。
炉温过高会造成糊花的生成,破坏球化效果;炉温过低则会导致球墨形态不完整。
熔化时间过长会导致合金因在高温下持续存在而发生发热和烧损现象,降低了合金的性能。
因此,在熔炼过程中需要精确控制炉温和熔化时间,以达到优化的球化效果和合金质量。
再次,铸造工艺对球墨铸铁的性能和质量也有重要影响。
铸造温度和冷却速度是需要控制的关键参数。
铸造温度低于需求范围会导致铸件凝固不完全,造成缩松和孔洞等缺陷;铸造温度过高则会加剧合金的河流现象,使得铸件组织松散。
冷却速度过大或过小也会对铸件的显微组织和性能产生负面影响。
因此,在铸造过程中需要通过调整冷却剂和冷却方式来控制铸造温度和冷却速度,以达到理想的铸件质量。
此外,球墨铸铁的热处理过程也需要进行精确控制。
球化处理、淬火和回火等工艺参数的控制都会直接影响到球墨铸铁的硬度、强度和韧性等性能。
通过控制加热温度、保温时间和冷却速度等参数,可以使球墨铸铁获得最佳的组织结构和性能。
综上所述,球墨铸铁生产工艺控制涉及到整个生产过程中的多个环节和参数。
只有精确控制每个环节和参数,才能确保球墨铸铁的优良性能和高质量。
因此,科学、严谨的生产工艺控制是球墨铸铁生产过程中必不可少的重要环节。
高强度高韧性球墨铸铁的u000b质量评估和生产工艺控制

FIAT 45-33-15 60-38-10 65-48-05 90-52-05
美国标准 60-40-18 65-45-12 80-55-06 100-70-03 120-90-02
*1PSi=0.70 kg/mm2
6
4.球铁的生产现状和发展方向
1)目前球铁发展的方向主要着重于推广现有 牌号和提高铸件的全面质量,实现优质生 产。如材质、工艺、内在质量、表面质量 等。
47
例如: QT900-5 应用:Ni 0.25~0.35% Cu 0.5~0.6%; 铸态QT700-2 Cu 0.30~0.50% Sn 0.03%
48
4.微量元素的作用
主要是指一些干扰球化或其他有 害作用的微量元素,如Ti、Sn、Al、 Cr、Sb、Bi、Pb等。
49
说明:
(1)干扰元素在大于某一定量时才发生有害作用; (其界限量见下表) 反球化干扰元素界限量
C
Si Mn P
S
Mg′
RE′
3.4~3.9 2.0~3.0 0.1~0.7 <0.08 <0.02 0.03~0.05 0.02~0.04
35
1.基本元素的作用
1)C和Si:
一般选择在近共晶成分(由于球化元素Mg
的作用,共晶点右移到4.6~4.7%)。
优点(1)流动性好;(2)形成集中缩孔倾向
大;(3)致密度高。
(1)与S作用:MnS+FeS+2Mg→Fe+Mn+2MgS (S由0.05~0.08↘~0.02)
消 M 耗 脱 Sg 0 .7 ( S 6 原 S 终 ) M S ( g 原 3 2 子 2 40 .7量 6
(2)与O作用(烧损):生成MgO 占15~30%。 (3)脱氧去气:Mg去气<0.01%
风电球墨铸铁行星架铸造工艺研究

风电球墨铸铁行星架铸造工艺研究一、引言风电球墨铸铁行星架是风力发电机组的重要组成部分,其质量和性能对于整个风力发电系统的运行稳定性和经济效益具有重要影响。
因此,研究其铸造工艺具有重要的意义。
二、球墨铸铁行星架的概述球墨铸铁行星架是指采用球墨铸铁材料制造的风力发电机组主轴支撑结构,其主要功能是承受转子和风轮负荷,并传递到塔筒上。
该部件通常由两个半轮组成,通过螺栓连接在一起。
三、球墨铸铁材料的特点球墨铸铁材料具有高强度、高韧性、耐疲劳、耐腐蚀等优点,适用于制造大型机械零件。
同时,球墨铸铁材料也存在着一些缺陷,如气孔、夹渣等。
四、球墨铸铁行星架的设计球墨铸铁行星架的设计需要考虑多种因素,包括载荷条件、结构尺寸、材料选择等。
其中,载荷条件是设计的核心,需要考虑风轮的质量、旋转速度、风向变化等因素。
五、球墨铸铁行星架的铸造工艺球墨铸铁行星架的铸造工艺是影响其质量和性能的关键因素。
常用的球墨铸铁行星架铸造工艺包括砂型铸造、气体硬化模型(HWS)铸造、失重法(投资法)铸造等。
1. 砂型铸造砂型铸造是球墨铸铁行星架最常用的一种生产工艺。
该工艺具有成本低、适用范围广等优点,但存在着砂芯制作难度大、表面粗糙度高等缺点。
2. HWS 铸造HWS 铸造是一种新兴的球墨铸铁行星架生产工艺,其主要特点是采用气体硬化模型代替传统砂模。
该工艺具有制品尺寸精度高、表面质量好等优点,但成本较高。
3. 失重法(投资法)铸造失重法(投资法)铸造也是一种常用的球墨铸铁行星架生产工艺。
该工艺具有制品表面光洁度高、尺寸精度高等优点,但成本较高。
六、球墨铸铁行星架的质量控制球墨铸铁行星架的质量控制是保证其性能和寿命的重要环节。
常用的质量控制方法包括化学成分分析、金相组织检测、硬度测试、超声波探伤等。
七、结论风电球墨铸铁行星架作为风力发电机组的重要组成部分,其质量和性能对于整个风力发电系统的运行稳定性和经济效益具有重要影响。
因此,研究其铸造工艺及质量控制方法具有重要意义。
球墨铸铁性能及生产工艺
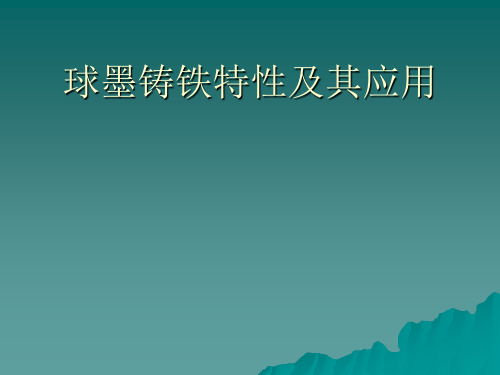
二、合金元素 球墨铸铁的合金元素主要有钼、铜、 镍、铬、锑、钒、铋等金属。 这些元素的主要是起提高铸铁的强度, 稳定基体组织的作用。
球墨铸铁的凝固特点
1、球墨铸铁有较宽的共晶温度范围 2、球墨铸铁的糊状凝固特性 3、球墨铸铁具有较大的共晶膨胀
球墨铸铁的典型缺陷
1、球化不良和球化退化 特征:断口银灰色,分布芝麻状黑斑点。 金相组织分布大量厚片石墨。 原因:原铁液含硫高,过量反球化元素。 建议选用低硫焦炭,脱硫处理,必要时增 加球化剂稀土量,控制冲天炉鼓风强度和 料位。
讨 论
薄壁铸态球墨铸铁
在欧美发达国家的阀门铸造 工艺中,日趋使用薄壁铸件, 可以节约资源。 薄壁铸态球墨铸铁件是壁厚 仅为几毫米的铸件。由于薄壁, 共晶凝固时冷却速度极快,所 以抑制白口组织的出现成为首 要问题。
白口临界球数(个/平方毫米)
700 600 500 400 300 200 100 0 0 1 2 5 10 15 20 25 冷却速度R(摄氏度/秒) 冷却速度与临 界球数的关系
1、石墨:未溶石墨、添加晶体石墨、非平 衡石墨 2、岩状结构碳化物基底 3、氧化物 4、硫化物/氧化物 5、铋及铋的化合物
球墨铸铁的孕育
球墨铸铁孕育的重要性 灰铸铁、球墨铸铁孕育的异同点 孕育衰退现象 提高孕育效果的措施 a.选择强效孕育剂 b.必要的S的含量 c.改善处理方法 d.提高铸件冷却速度
球状石墨的生长
球状石墨的生长条件 a、极低的硫、氧含量 b、限制反球化元素 c、保证必要的冷却速度 d、添加的球化元素 第一组:镁、钇、铈、钙、镧、镤、钐、 镝、镱、钬、铒 第二组:钡、锂、铯、铷、锶、钍、钾、钠 第三组:铝、锌、镉、锡 最佳含量 W(Mg):(0.04-0.08)% W(Ce): (0.07-0.12)% W(Y) : (0.15-0.2)%
球墨铸铁材质报告单
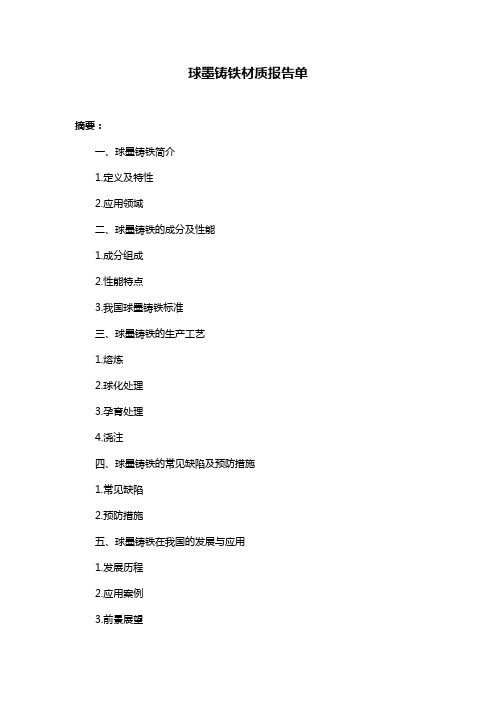
球墨铸铁材质报告单摘要:一、球墨铸铁简介1.定义及特性2.应用领域二、球墨铸铁的成分及性能1.成分组成2.性能特点3.我国球墨铸铁标准三、球墨铸铁的生产工艺1.熔炼2.球化处理3.孕育处理4.浇注四、球墨铸铁的常见缺陷及预防措施1.常见缺陷2.预防措施五、球墨铸铁在我国的发展与应用1.发展历程2.应用案例3.前景展望正文:球墨铸铁材质报告单一、球墨铸铁简介球墨铸铁是一种高强度、高韧性的铸铁材料,其特点是铁素体基体中分布着球状石墨。
由于其优异的性能,球墨铸铁广泛应用于各个领域,如汽车、火车、船舶、建筑等。
二、球墨铸铁的成分及性能球墨铸铁的主要成分是铁、碳、硅、锰、磷、硫等元素。
其中,碳含量在2.5%~4.0%,硅含量在1.0%~3.0%,锰含量在0.5%~1.5%。
这些成分使其具有较高的强度、韧性、耐磨性、抗腐蚀性等性能。
我国已制定了一系列球墨铸铁标准,以规范其生产与应用。
三、球墨铸铁的生产工艺球墨铸铁的生产工艺主要包括熔炼、球化处理、孕育处理和浇注。
首先,将铁合金、废钢等原料进行熔炼,然后进行球化处理,使石墨呈球状。
接着进行孕育处理,以改善石墨球的形成和分布。
最后进行浇注,将熔融的铁液倒入模具中,形成铸件。
四、球墨铸铁的常见缺陷及预防措施球墨铸铁的常见缺陷有石墨漂浮、缩孔、裂纹等。
为预防这些缺陷,需严格控制熔炼质量、球化处理效果、孕育处理参数以及浇注工艺。
此外,合理设计模具和冷却系统,以及采用合适的熔炼材料和铸造工艺,也有助于减少缺陷。
五、球墨铸铁在我国的发展与应用我国自20世纪50年代开始研究球墨铸铁,经过几十年的发展,已取得了显著成果。
目前,我国已成为世界上最大的球墨铸铁生产国和消费国。
球墨铸铁在我国广泛应用于汽车、火车、船舶、建筑、石油化工等领域,为我国的经济建设做出了巨大贡献。
铸态球墨铸铁生产技术.docx

铸态球墨铸铁生产技术陈永成仲天创展球铁有限公司 佛山顺德 528313 )球墨铸铁是一种广泛应用于各工业部门的重要结构材料, 它的出现使铸铁材 料的性能发生了质的飞跃,因此在国内外发展都很快,许多方面已取代了锻钢、 铸钢及可锻铸铁的应用,成为产量仅次于灰铸铁的铸造合金材料。
以往球铁均需 通过各种不同的热处理手段方能达到相应的牌号要求,从而耗费能源、污染环境、 增加成本、延长生产周期、加重工人劳动强度,因此生产铸态球铁便成为近年来 国内外球铁生产方面的一个重要发展方向。
据数据统计,我国用于灰铸铁件热时 效的能耗每吨铸件为40〜100kg 标准煤,而用于球墨铸铁件退火、正火的能耗每 吨铸件为100〜180kg 标准煤。
我国球墨铸铁件中高韧性铁素体球铁和高强度珠 光体球铁占有很大的比重,通常是采用退火、正火处理。
采用铸态球墨铸铁生产 技术省去了退火、正火处理工序,节约能源,避免了因高温处理而带来的铸件变 形、氧化等缺陷。
所以,推广应用铸态球墨铸铁生产技术,对于铸造行业的节能 降耗减少排放,以及提高经济效益都具有非常重要的意义。
一、铸态球铁生产的基本条件广义上的铸态球铁应包括 GB/T 1348-2009《球墨铸铁件》中的所有材质牌号,但是由于QT800-2和QT900-2在铸态条件下极难稳定地生产,所以一般不 考虑在内。
近年来随着对优质球铁件的需求量越来越大, 对其质量要求也越来越图1•燃煤退火炉 图2•正火球铁件出炉空冷高,甚至达到了苛刻的程度。
除了抗拉强度和伸长率之外,室温或低温冲击功、屈服强度、硬度、球化率、石墨大小、基体组织一直到化学成分对重要球铁件或某些客户来说,也成为了质量验收指标。
除了浇注单铸试块,附铸试块外,还有要求铸件指定位置的本体试块,最近发展到在铸件里取样的掏料试样。
球铁铸造厂要生产铸态球墨铸铁,必须经得起客户指定的力学性能、金相组织等综合性能检验的考验,必须能够稳定地生产,铸态合格率要达到90%以上,否则不能认为是成功。