上流式厌氧污泥床反应器(UASB)
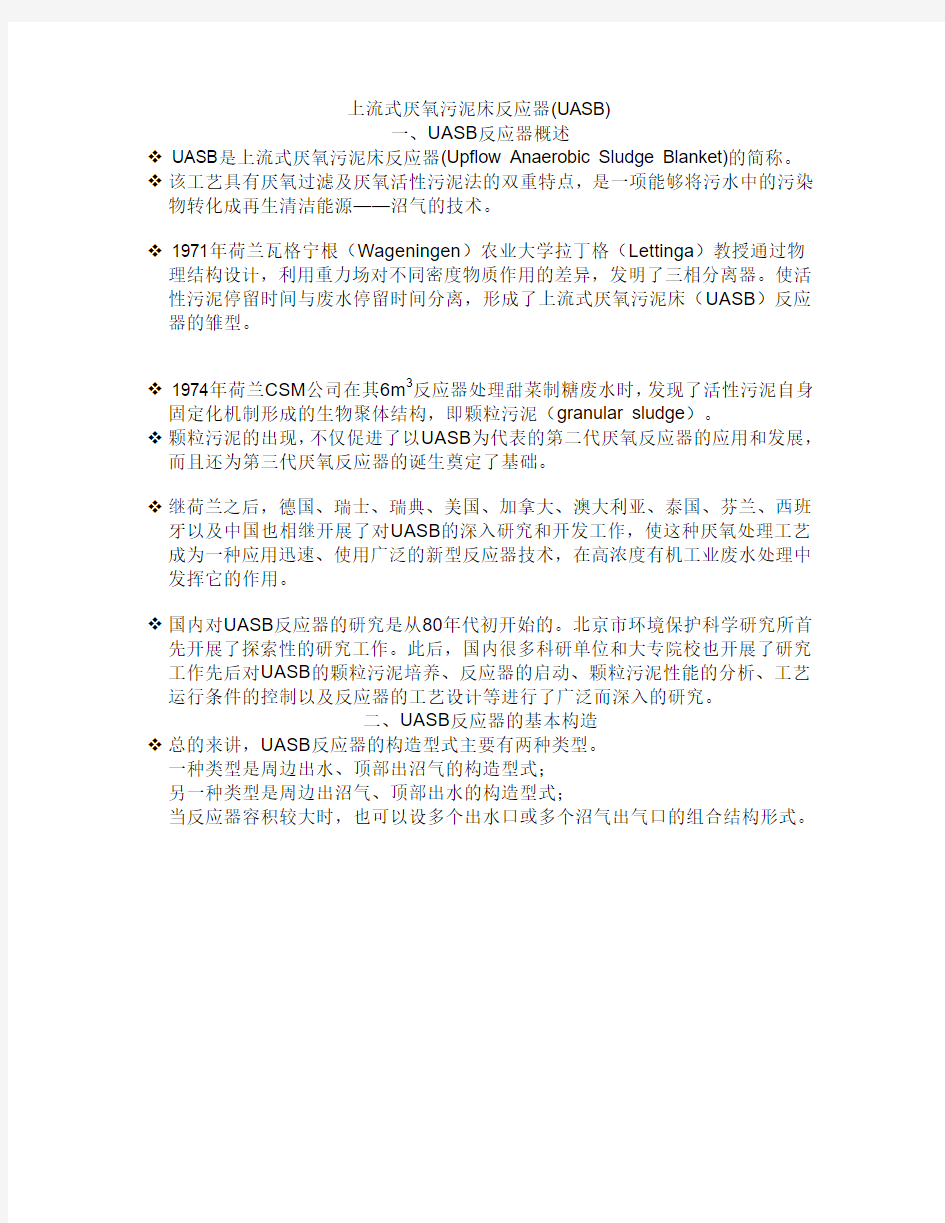
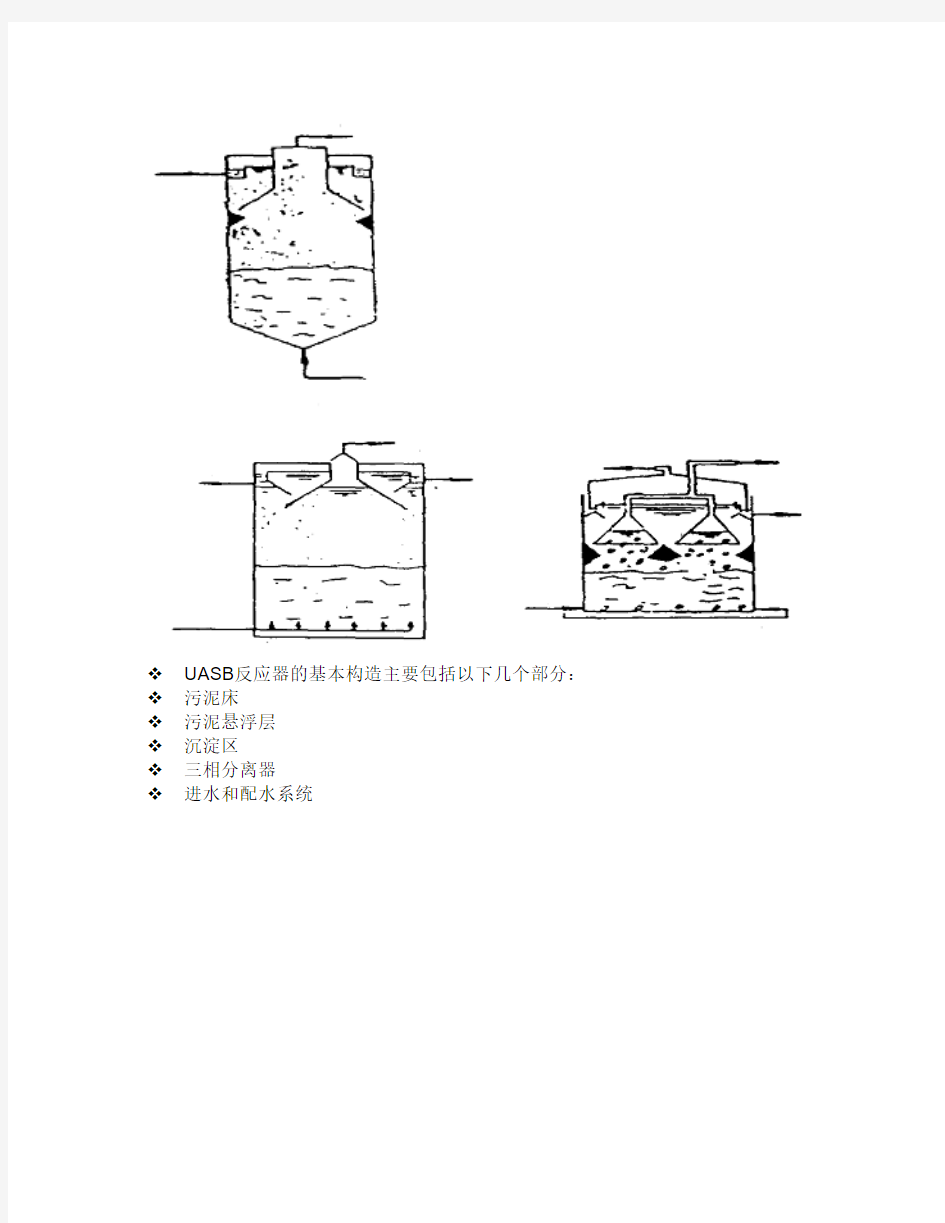
上流式厌氧污泥床反应器(UASB)
一、UASB反应器概述
UASB是上流式厌氧污泥床反应器(Upflow Anaerobic Sludge Blanket)的简称。 该工艺具有厌氧过滤及厌氧活性污泥法的双重特点,是一项能够将污水中的污染物转化成再生清洁能源——沼气的技术。
1971年荷兰瓦格宁根(Wageningen)农业大学拉丁格(Lettinga)教授通过物理结构设计,利用重力场对不同密度物质作用的差异,发明了三相分离器。使活性污泥停留时间与废水停留时间分离,形成了上流式厌氧污泥床(UASB)反应器的雏型。
1974年荷兰CSM公司在其6m3反应器处理甜菜制糖废水时,发现了活性污泥自身固定化机制形成的生物聚体结构,即颗粒污泥(granular sludge)。
颗粒污泥的出现,不仅促进了以UASB为代表的第二代厌氧反应器的应用和发展,而且还为第三代厌氧反应器的诞生奠定了基础。
继荷兰之后,德国、瑞士、瑞典、美国、加拿大、澳大利亚、泰国、芬兰、西班牙以及中国也相继开展了对UASB的深入研究和开发工作,使这种厌氧处理工艺成为一种应用迅速、使用广泛的新型反应器技术,在高浓度有机工业废水处理中发挥它的作用。
国内对UASB反应器的研究是从80年代初开始的。北京市环境保护科学研究所首先开展了探索性的研究工作。此后,国内很多科研单位和大专院校也开展了研究工作先后对UASB的颗粒污泥培养、反应器的启动、颗粒污泥性能的分析、工艺运行条件的控制以及反应器的工艺设计等进行了广泛而深入的研究。
二、UASB反应器的基本构造
总的来讲,UASB反应器的构造型式主要有两种类型。
一种类型是周边出水、顶部出沼气的构造型式;
另一种类型是周边出沼气、顶部出水的构造型式;
当反应器容积较大时,也可以设多个出水口或多个沼气出气口的组合结构形式。
UASB反应器的基本构造主要包括以下几个部分: 污泥床
污泥悬浮层
沉淀区
三相分离器
进水和配水系统
1、污泥床
污泥床位于整个UASB反应器的底部。
污泥床内具有很高的污泥生物量,其污泥浓度(MLSS)一般为40000~80000mg/L 污泥床中污泥由高度发展的颗粒污泥组成,其中活性生物量(或细菌)占70%~80%
以上的,正常运行的UASB中颗粒污泥的粒径一般在0.5~5mm之间,具有优良的沉降性能,
沉降速度一般为1.2~1.4cm/s,
典型的污泥容积指数(SVI)为10~20ml/g。
颗粒污泥中的生物相组成比较复杂,主要是杆菌、球菌和丝状菌等。
污泥床的容积一般占整个UASB反应器容积的30%左右,但它对UASB反应器的整体处理效率起着极为重要的作用,它对反应器中有机物的降解量一般可占到整个反应器全部降解量的70%~90%。
污泥床对有机物如此有效的降解作用,使得在污泥床内产生大量的沼气,微小的沼气气泡经过不断的积累、合并而逐渐形成较大的气泡,并通过其上升的作用而将整个污泥床层得到良好的混合。
2、污泥悬浮层
污泥悬浮层位于污泥床的上部,占据整个UASB反应器容积的70%左右。
其中的污泥浓度要低于污泥床,通常为15000~30000mg/L
污泥悬浮层由高度絮凝的污泥组成,一般为非颗粒状污泥,其沉速要明显小于颗粒污泥的沉速,SVI一般在30~40ml/g之间,靠来自污泥床中上升的气泡使此层污泥得到良好的混合。
污泥悬浮层中絮凝污泥的浓度呈自下而上逐渐减小的分布状态。这一层污泥担负着整个UASB反应器有机物降解量的10%~30%。
3、沉淀区
沉淀区位于UASB反应器的顶部。
其作用是使得由于水流的夹带作用而随上升水流进入出水区的固体颗粒(主要是
污泥悬浮层中的絮凝性污泥)在沉淀区沉降下来,并沿沉淀区底部的斜壁滑下而重新回到反应区内(包括污泥床和污泥悬浮层),以保证反应器中污泥不致流失而同时保证污泥床中污泥的浓度。
可以通过合理调整沉淀区的水位高度来保证整个反应器的集气室的有效空间高度而防止集气空间的破坏。
4、三相分离器
三相分离器是UASB反应器中最有特点和最重要的装置,一般设置在沉淀区的下部,但也可将其设置在反应器的顶部,具体视所用的反应器的型式而定。
三相分离器由气体收集器和折流挡板组成。有时,也可将沉淀装置看做三相分离器的一个组成。
其主要作用是将气体(反应过程中产生的沼气)、固体(反应器中的污泥)和液体(被处理的废水)等三项加以分离。将沼气引入集气室,将处理出水引入出水区,将固体颗粒导入反应区。相当于传统污水处理工艺中的二次沉淀池,并同时具有污泥回流的功能。
5、进水和配水系统
UASB反应器的进水系统兼有配水和水力搅拌的功能。
目前生产性UASB反应器装置所采用的进水方式:
间隙式进水、
脉冲式进水、
连续均匀进水
连续进水与间隙回流相结合的进水方式
UASB反应器中一般情况下多采用连续进水的运行方式,必要时也可采用脉冲式进水和连续进水与间隙回流相结合的进水方式。采用后两种进水方式的目的是使反应器内的絮凝、颗粒污泥经常性地处于均匀混合和颗粒松散状态,多在反应器的启动初期或反应器中出现沟流时使用。当反应器运行正常后,一般不必进行回流,而进行连续进水。
三、UASB反应器的反应机理
UASB反应器中的厌氧反应过程与其它厌氧生物处理工艺一样,包括了极为复杂的生物反应过程。虽然迄今为止仍未完全了解反应过程中的复杂机理(对于诸如纤维素等非溶解性的复杂有机物而言更是如此),但目前业已提出了比较全面的厌氧反应过程的有关基本过程。
厌氧反应过程与好氧处理过程不同,它有多种不同的微生物参与了底物的转化过程,经过复杂的反应将底物转化为最终产物。
在反应过程中,经过水解、发酵、产酸和产气步骤,复杂的底物被厌氧微生物转化为多种多样的中间产物,如糖类、有机酸、醇、醛和氢等,并最终转化为沼气。 在厌氧消化过程中参与反应的厌氧微生物主要有以下几种:
水解—发酵(酸化)细菌:将复杂的聚合底物水解成各种有机酸、乙醇、糖类、氢和二氧化碳。
乙酸化细菌:将第一步水解发酵的产物(有机酸和糖类等)转化为氢、乙酸和二氧化碳。
产甲烷菌:将简单的底物,如乙酸、甲醇和二氧化碳,与氢转化为甲烷。
非溶解性有机聚合物(蛋白质、脂类和碳水化合物等)的厌氧分解还可以更细致地划分为六个明显的步骤:
聚合物(蛋白质、脂类或碳水化合物)水解;
氨基酸和糖发酵成氢、乙酸盐、短链脂肪酸和乙醇;
长链脂肪酸和乙醇的无氧氧化;
中间产物如挥发酸(乙酸除外)的无氧氧化;
嗜乙酸微生物将乙酸转化为甲烷;
嗜氢微生物将氢转化为甲烷(二氧化碳还原)。
四、UASB反应器的工作原理
需要处理的废水以一定的流速自反应器的底部进入反应器,水流在反应器中呈推流形式上升,废水流速一般为0.5~1.5m/h,多宜在0.6~0.9m/h之间。
进水首先流入反应器底部的污泥床,随后流入污泥悬浮层,与反应区中的污泥充分混合接触,污泥中的微生物对厌氧分解水中的有机物,把它转化为沼气。
厌氧分解过程中产生的沼气在上升过程中将污泥颗粒托起,由于大量气泡的产生,即使在较低的有机和水力负荷条件下也能看到污泥床明显的膨胀。
沼气以微小气泡的形式不断放出,微小气泡在上升过程中相互结合而逐渐形成较大的气泡,将污泥颗粒向反应器的上部携带,最后由于气泡的破裂,绝大部分污泥颗粒又返回到污泥区,对污泥起到搅拌的作用。
随着反应器产气量的不断增加,由气泡上升所产生的搅拌作用变得日趋激烈,从而降低了污泥中夹带气泡的阻力,气体便从污泥床内突发性地逸出,引起污泥床表面呈沸腾和流化状态。反应器中沉淀性较差的絮体状污泥则在气体的搅拌作用下,在反应器上部形成污泥悬浮层。沉淀性能良好的颗粒状污泥则处于反应器的下部形成高浓度的污泥床。
随着水流的上升流动,气、水、泥三相混合液上升至三相分离器中。
沼气碰到分离器下部的反射板后折向集气室,被有效地分离收集,并通过沼气管道排出。
污泥和水进入反应器上部的沉淀区,污水中的污泥发生絮凝,颗粒逐渐增大,在重力的作用下沉降,发生泥水分离。回落至斜壁上的污泥沿斜壁滑回反应器的反应区。处理过的水从沉淀区溢流堰溢出,排出反应器。
由于三相分离器的作用,使得反应器混合液中的污泥有一个良好的沉淀、分离和再絮凝的环境,有利于提高污泥的沉降性能。在一定的水力负荷条件下,绝大部分污泥能在反应器中保持很长的停留时间,使反应器中具有足够的污泥量。
五、UASB反应器的特点
UASB反应器的优点:
反应器内污泥浓度高。
一般平均污泥浓度为30~40g/L,污泥床为40~80g/L,污泥悬浮层为15~30g/L。 反应器中的污泥颗粒化。
颗粒污泥具有生物固体沉降性能好、生物浓度高、固液分离好的特点,使反应器对不利条件的抗性增强,是UASB反应器的一个重要特征。
反应器的有机负荷高。
COD容积负荷在小试验和中型试验中可高达20~40kg COD/(m3·d),在大型生产装置中可达到6~8kg COD/(m3·d)。
工艺简单,投资和运行费用低。
反应器内设三相分离器,被沉淀区分离的污泥能自动回流到反应区,因而无污泥回流设备。
反应器无混合搅拌设备。
投产运行后,利用进水和本身产生的沼气进行搅动,实现基质与污泥的充分接触。
反应器中不使用填料。
提高了容积利用率,节省造价及避免堵塞问题。而填料在其它构型中为生物有效停留提供稳定环境,是必须的。
UASB反应器的局限:
大型装置内易发生短流现象,影响处理能力,对配水系统的性能要求较高。
反应器进水SS不宜超过200mg/L,以避免对污泥颗粒化不利或减少反应区的有效容积,甚至引起堵塞。
反应器在没有颗粒污泥接种的情况下,启动时间长。
反应器对进水水质和负荷的突然变化比较敏感,耐冲击力较差。
反应器中所要求的水温较高,最好在35℃左右。
六、UASB反应器的控制要点
在UASB反应器的运行中,其控制要点及常见问题主要有以下四个方面:
反应器的启动和颗粒污泥培养
反应器污泥流失及解决方法
反应器中的酸碱平衡及pH值的控制
反应器中硫酸盐、硫化氢的控制技术
1、反应器的启动和颗粒污泥培养
对于一个新建的UASB反应器来说,启动过程主要是用未经驯化的絮状污泥对其进行接种,并经过一定时间的启动调试运行,使反应器达到设计负荷并实现有机物的去除效果,通常这一过程会伴随着污泥颗粒化的实现,因此也称为污泥的颗粒化。
由于厌氧微生物,特别是甲烷菌增殖很慢,厌氧反应器的启动需要很长时间。
但是,一旦启动完成,在停止运行后的再次启动可以迅速完成。
当没有现成的厌氧污泥或颗粒污泥时,采用最多的是城市污水处理厂的消化污泥。除消化污泥之外,可用作接种的物料很多,例如牛粪和各类粪肥、下水道污泥等。一些污水沟的污泥和沉淀物或富微生物的河泥也可以被用于接种,甚至好氧活性污泥也可以做为接种污泥。污泥的接种浓度以6~8kgVSS/m3 (按反应器总有效容积计算)为宜,至少不少于5kgVSS/m3,接种污泥的填充量应不超过反应器容积的60%。
当接种污泥不是颗粒污泥时,为了培养颗粒污泥或沉降性能好的活性污泥,都存在着一个将絮状污泥和分散的细小污泥从反应器内“洗出”的过程,这是UASB反应器实现颗粒化的先决条件之一。
这一过程是一个微生物逐步筛选和进化的过程,控制的关键因素之一是反应器内的水力停留时间或上升流速。经验表明,升流速度在0.4~1.0m/s之间较合适,如果有必要可以采用出水回流方式以适当提高反应器内的升流速度。
一般来说,在颗粒污泥培养期内随水被冲出反应器的污泥是没有必要回流到反应器中去的。
从负荷角度考虑UASB的初次启动和颗粒化过程,可分为三个阶段:
Ⅰ启动的初始阶段,这一阶段是低负荷阶段(<2kgCOD/(m3·d))
Ⅰ当反应器负荷上升至2~5kgCOD/(m3·d)的启动阶段。在这阶段污泥的洗出量增大,其中大多为细小的絮状污泥。实际上这一阶段在对较重的污泥颗粒和分散的、絮状的污泥进行选择,使这一阶段的末期留下的污泥中开始产生颗粒状污泥。
这一阶段是反应器负荷超过5kgCOD/(m3·d) 在此时,絮状污泥变得迅速减少,而颗粒污泥加速形成直到反应器内不再有絮状污泥存在。
5kgCOD/(m3·d)左右是反应器中以颗粒污泥或絮状污泥为主的一个重要分界。
当反应器负荷大于5kgCOD/(m3·d),由于颗粒污泥的不断形成,反应器的大部分被颗粒污泥充满时,其最大负荷可以超过20kgCOD/(m3·d)。
在UASB反应器启动过程中会出现两种污泥流失:
一种是污泥本身性质不好,在低负荷运行时也会发生流失,这主要是由于污泥本身性质所引起的流失;
另一种则是在水力负荷、容积负荷太高的情况下而引起的污泥流失,这种污泥流失称之为膨胀跑泥。
沉淀性能较差的污泥流失与膨胀跑泥在污泥的性质上存在着差别。经测定后可以发现,污泥流失的VSS/SS值要比留在反应器中污泥的VSS/SS值略大,即其无机成分的含量要小一些,容易从反应器中流失,沉降性能差。而膨胀跑泥的VSS/SS 值与留在反应器内污泥的VSS/SS值基本相同,在一定程度上说明膨胀跑泥的性质与同期留在反应器内污泥的性质是相同的,这些污泥是由于水力负荷或污泥负荷过高而被冲出反应器的。
区分两种跑泥方式后,可以更好的探讨解决此问题的方式。
对于因沉淀性能较差的污泥流失,因为其性能差,是应该让它们流失或主动排放的,而不应该回流。这些污泥即使回流到反应器中,也会再次上浮,结果仍然会流失。而且这些污泥还会与颗粒污泥竞争基质,不利于颗粒化的进程。
而对于膨胀跑泥,因为其性质基本上与反应器内的污泥完全一样,放弃这些污泥是很可惜的。厌氧微生物特别是产甲烷菌生长非常缓慢,单纯依靠自身生长重新获得这些污泥需要一定的时间。同时污泥的颗粒化归根到底还是要使得某些细菌在细小的、絮状污泥中的某些“核心”上附着生长并逐渐形成初始的颗粒污泥,因此若放弃这些污泥,也就放弃了一次污泥颗粒化的机会,因此,对于膨胀跑泥应该加以回流或加以避免。
2、反应器污泥流失及解决方法
UASB反应器启动阶段结束后,在运行过程中仍然会发生污泥流失。
虽然三相分离器在混合液进入沉淀区前已把气体分离,但由于沉淀区内的污泥仍具有较高的产甲烷活性,继续在沉淀区内产气;或者由于冲击负荷及水质突然变化,可能使反应区内污泥膨胀,结果沉淀区固液分离不佳,发生污泥流失而影响了水质和污泥床中污泥浓度。
为了减少出水所带的悬浮物进入水体,外部另设一沉淀池,沉淀下来的污泥回流到污泥床内。
外部设置沉淀池的好处是:
污泥回流可加速污泥积累,缩短启动周期;
去除悬浮物,改善出水水质;
当偶尔发生大量漂泥时,提高了可见性,能够及时回收污泥保持工艺的稳定性; 回流污泥可进一步分解,减少剩余污泥量。
3、反应器中的酸碱平衡及pH值控制
pH值是影响厌氧消化过程的重要因素,许多研究结果和实际运行经验表明,厌氧消化需要一个相对稳定的pH值范围,对于以产甲烷为主要目的的厌氧过程来说,为6.5~7.5.如果生长环境的pH过高(>8.0)或过低(<6.0),产甲烷菌的生长代谢和繁殖就会受到抑制,并进而对整个厌氧消化过程产生严重的不利影响。
因为在厌氧体系中,其它非产甲烷菌如发酵细菌等对pH值的变化不如产甲烷菌敏感,在pH值发生较大变化时,这些细菌受到的影响较小,它们能继续将进水中的有机物转化为脂肪酸等,导致反应器内有机酸的积累、酸碱平衡失调,使产甲烷菌的活性受到更大的抑制,最终导致反应器运行失败。因此,在厌氧生物处理过程中,应特别注意反应期内pH值的控制,一般应维持在产甲烷菌的最适范围内,即6.5~7.5。
厌氧消化体系中的pH值是体系中CO2、H2S在气、液两相间的溶解平衡、液相内的酸碱平衡及固、液相间离子溶解平衡等综合作用的结果,而这些又与反应器内发生的生化反应直接有关。因此,分析和研究厌氧消化过程中酸碱平衡的实质和pH值的控制技术,对于选择和设计废水生物处理工艺、调试和运行厌氧生物处理装置等都有重要的指导意义。
(2)消化过程中的生化反应及对酸碱平衡的影响
厌氧体系中的酸碱平衡
根据对厌氧消化体系中成分的分析,可知影响酸碱平衡的主要成分有脂肪酸、氨氮、H2S、CO2等,这些物质在厌氧体系中存在着溶解平衡、电离平衡等反应平衡。
脂肪酸的电离平衡
在厌氧体系中,脂肪酸主要包括乙酸、丙酸、丁酸等,三者的电离常数相差不大,当都采用摩尔浓度表示时,其对体系的酸碱平衡的影响也相差不大,将厌氧体系中所有脂肪酸都换算成等摩尔的乙酸,统一用乙酸的电离平衡来计算,如下式:
氨氮的电离平衡
在厌氧体系中氨氮的电离平衡可表示如下:
CO2的溶解及H2CO3的电离平衡
CO2在气、液相间的溶解平衡可表示为:
根据气体溶解平衡的亨利定律,有:
式中:H CO2——亨利常数(mol/L·atm)
P CO2——CO2的平衡分压(atm)
CO2的溶解及H2CO3的电离平衡
CO2在水中还会发生强烈的水合反应,其平衡反应式为:
CO2的溶解及H2CO3的电离平衡
反应生成的H2CO3又会发生电离平衡,反应式为:
CO2的溶解及H2CO3的电离平衡
与H2CO3较困难,根据复合酸度常数的概念,因为在进行化学分析时区别CO2(
液)
令:
CO2的溶解及H2CO3的电离平衡
根据复合碳酸的电离平衡,有:
H2S的电离平衡
与CO2一样,首先存在着气、液相间的溶解平衡:
根据亨利定律有:
H2S的电离平衡
厌氧体系中的致碱物质
通过以上分析可知,厌氧体系中与酸碱平衡有关的共轭酸碱对主要有:
等。随着厌氧体系pH值的不同,这些共轭酸碱对在各种形态之间的分布也会发生变化。
(3)pH值的控制技术
为了保证厌氧反应器中的pH值稳定在适宜的范围内,就必须采取一定的措施对反应器的运行状况进行调节和控制。在实际运行中,主要通过以下几种方法来调节和控制厌氧反应器内的pH值:
投加致碱或致酸物质
出水回流
出水吹脱CO2后回流
投加致碱或致酸物质
在进水中或直接在反应器中加入致碱或致酸物质,是最直接的调控厌氧反应器内pH值的方法。实际运行中所使用的致碱物质主要有Na2CO3、NaHCO3、NaOH 和Ca(OH) 2等。用这种方法要消耗化学药品,从而增加了运行费用。而且,现
场操作人员应在废水中加入多少致碱物质不好掌握。
一般情况下,在废水pH>8.0时,则应加酸调节
出水回流
一般情况下,厌氧反应器的出水碱度会高于进水碱度,所以可采用出水回流的方法来控制反应器内pH值,同时出水回流还可起到稀释作用。有研究表明,采用该法来控制反应期内pH值,回流比一般应控制在5~20之间。
出水吹脱CO2后回流
出水中的CO2是主要的致酸物质,把出水中的CO2经吹脱去除后再回流,是一种更好的调控厌氧反应器中pH值的方法。
但在采用该法时,由于一般均采用空气进行吹脱,所以回流中会含有一定的溶解氧。溶解氧的带入会对反应器的运行产生一定的不利影响。
4、反应器中硫酸盐、硫化氢的控制技术
(1)硫酸盐还原作用
(2)硫酸盐还原菌
硫酸盐还原菌通常是指一类通过异化还原作用进行硫酸盐还原的细菌。
硫酸盐还原菌形态、营养多样化,利用硫酸盐作为有机物分解过程的最终电子受体。
硫酸盐还原菌都是严格厌氧菌,生长速率相对较缓慢,但具有较强的生存能力,而且分布广泛,只要条件许可就会马上活跃起来。
影响硫酸盐还原菌生长的主要因素
温度
与产甲烷菌类似,硫酸盐还原菌也在两个温度段表现出较强活性。其多数是中温型,最佳生长温度为30~37℃,少数是高温型,最佳生长温度为40~70℃。
pH值
其生长的最适pH值为7.1~7.6,但大多数均可在4.5~9.5的范围内生长。
氧化还原电位
硫酸盐还原菌是严格的厌氧细菌,其生长环境的氧化还原电位在-100mV以下,而产甲烷菌所要求的氧化还原电位为-300mV以下。
营养要求
硫酸盐还原菌是异养菌,其生长除了需要有机物外,还需要有硫酸盐、亚硫酸盐、硫代硫酸盐等含有氧化态硫的化合物作为电子受体。
生长刺激物
其生长一般都需要维生素等生长刺激物。
生长抑制剂
许多物质对硫酸盐还原菌具有抑制作用,如一定浓度的Na2AsO4、K2CrO4、
PbCl2、Na2MoO4等,而这些物质对产甲烷菌则有不同程度的激活作用。
另外,超声波、紫外线等在一定条件下对硫酸盐还原菌也能起抑制或灭活作用。
(3)硫酸盐还原作用对厌氧消化的影响
硫是微生物生长所必需的营养元素之一,少量的硫酸盐(或其它含硫化合物)会有益于厌氧消化过程,甚至在某些情况下还需要补充一定量的含硫物质作为微生物生长的硫源。
当厌氧系统中含有适量的硫酸盐时,硫酸盐还原菌能够有效地利用氢来还原硫酸盐,从而加快产氢产乙酸反应的速度,提高种间氢的转移速度,有助于厌氧消化过程的进行。
但是当废水中含有高浓度的硫酸盐时,则会对厌氧消化产生不利影响。
基质竞争性抑制作用
硫酸盐还原菌生长的pH值、温度、氧化还原电位等环境条件及其可利用基质的范围都比产甲烷菌要广,所以其更容易生长。
硫酸盐还原菌和产甲烷菌都能利用乙酸和氢等作为生长基质,在反应器内必然会发生基质竞争,并由此产生对甲烷菌的抑制作用,影响厌氧消化的进行。
硫化氢对产甲烷菌的毒害作用
硫化物是硫酸盐还原作用的最终产物,不仅会增加沼气中H2S的含量,增加出水的COD值,更重要的是还会对厌氧细菌(特别是产甲烷菌)产生抑制作用,而对整个厌氧消化过程产生不利影响,严重时可能导致整个厌氧反应器无法正常运行。
(4)硫酸盐及硫化氢的控制技术
可分为物理化学法和生物法两大类
物理化学法
包括气体吹脱、化学沉淀和抑制等。
采用吹脱法处理实际上是把液相中的硫化氢转移到气相中去,并没有消除硫化氢对环境的污染。
化学沉淀法和抑制法需要外加沉淀剂和抑制剂,能耗、化学药品及后处理费用较高。
气体吹脱法
由于pH值较低时,溶液中溶解性的硫化物大部分以H2S的形式存在。利用这一性质,在单项厌氧处理系统中安装循环气体吹脱装置,将硫化物吹脱,减轻对产甲烷过程的抑制作用,改善反应器的运行性能。
化学沉淀法
投加金属盐与溶解性硫化物反应生成金属硫化物沉淀,从而降低反应器中的硫化物浓度。用来沉淀硫离子最常见的金属盐是铁盐。但此法缺点也很明显,加入金属盐使运行费用增加,沉淀物在反应器中的沉积使污泥的VSS/TSS值降低,污泥产量增加。
化学抑制法
钼酸盐对硫酸盐还原菌具有较强的抑制作用,对产甲烷菌反而有激活作用,但对其机理尚不十分清楚。
虽然钼酸盐对硫酸盐还原菌有很好的专一性抑制作用,但是这种方法也有其弊端。一方面对废水中的硫酸盐未加以控制,排入水体后仍会引起一系列的环境问题;另一方面,钼酸盐价格昂贵,运行费用高。
生物法
厌氧消化过程可概括地分为产酸和产甲烷两个阶段,由此发展起来的两相厌氧工艺是根据参与产酸和产甲烷发酵的微生物类群不同,设立两个独立的反应器,通过控制运行条件,保证两大类群细菌在各自的反应器中获得最佳的生长条件,使整个系统达到较高的处理能力和运行稳定性。
在此工艺的启发下,研究者试图将硫酸盐还原作用控制在产酸阶段完成,然后设法将产酸反应器出水中的硫化物去除,最后令其进入产甲烷反应器进行反应。
将硫酸盐还原作用控制在产酸阶段完成具有如下优点:
发酵性细菌比产甲烷菌能忍耐较高的硫化物浓度,所以产酸作用可以与硫酸盐还原作用同时进行,不会影响产酸过程;
产酸相反应器处于弱酸状态,生成的硫化物主要以H2S形式存在,有利于硫化物的进一步去除;
硫酸盐还原菌本身就是一种产酸菌,它可以利用普通产酸菌的某些中间产物(如乳酸、丙酮酸、丙酸等),将其进一步降解为乙酸,故将硫酸盐还原作用与产酸作用控制在一个反应器中进行,在一定程度上有利于提高产酸相的酸化率,使产酸类型向乙酸发展,有利于后续的产甲烷反应,提高产气率;
硫酸盐还原作用与产甲烷作用分别在两个反应器内进行,避免了硫酸盐还原菌和产甲烷菌之间的基质竞争;
硫化物设法去除后,可不与产甲烷菌直接接触,不会对产甲烷菌产生毒害作用; 大部分的硫酸盐已在产酸相中被去除,形成的沼气中H2S含量较少,回收利用方便。
七、不同UASB系统的对比分析
从世界上采用UASB反应器处理啤酒废水业绩的统计数据来看:采用颗粒污泥,处理负荷可以达到10~15kgCOD/(m3·d)以上;
采用絮状污泥,处理负荷在5kgCOD/(m3·d),但是COD去除率可以达到
90%~95%。
这说明同样是厌氧技术,但选取的设计参数可以有很大不同。
EGSB反应器
实际上是改进的UASB反应器,运行中维持高的上升流速(6~12m/h),使颗粒污泥处于悬浮状态,保证进水与污泥颗粒的充分接触。
EGSB概念特别适于低温和浓度相对低的啤酒废水。在低温条件下采用低负荷时,
沼气产率低、混合强度低。EGSB反应器依靠进水动能和污泥床膨胀高度保证了进水与污泥的充分接触,可获得比传统UASB反应器好的运行结果。
三种UASB系统设计负荷和预计去除率
经对比可发现,三种UASB系统各有优点,在设计中应该根据所处理废水的水量、水质,所要达到的处理标准,以及建设运行的预算进行合理选择。
八、UASB反应器的监控
系统需要的检控与系统所采用的负荷和设计上的安全系数有关。
有时为了减少反应器体积,负荷定得很高;或工艺在短时间的超负荷可能变得不平衡,在这些情况下,监控变的非常关键。
低负荷系统所需的监控要少得多,对于一个中等负荷的工艺每周监测一次就足够了。
监控甲烷产生量、pH范围和挥发性脂肪酸(VFA),可揭示系统运转的状态。
前两者可以反映生物的状况,但是不能鉴别功能不佳的原因,也不能预测系统的状况。类似的,VFA浓度可以被监测,但仅仅提供了工艺开始偏离正常的信号。
监控可以减少运行费用。
例如,通过在低pH值运行反应器(注意进水pH与反应器pH无关)来减少碱度的需要,可以大量节省补充碱度所需的费用。
九、UASB反应器在啤酒工业废水
处理中的应用
概述
啤酒废水
厌氧—好氧联合处理技术
不同处理系统的技术经济分析
1、概述
目前,国内外啤酒废水处理技术已有了迅速的发展,有采用接触氧化法、气动式生物转盘、生物滤池、深井曝气、两级活性污泥法、厌氧消化等工艺。
在国外,传统活性污泥法、升流式流化床等工艺已广泛地应用于啤酒废水处理。
特别是啤酒废水的UASB法处理技术,可以大幅度地降低处理设施的建设费用和运行费用,具有很大的经济性。
朝日啤酒公司已建成的东京、大阪等六处处理设施的运行效果证明,同传统活性污泥相比,厌氧—好氧工艺可以使处理能力增加1~2倍;回收的沼气经锅炉燃烧后,所产蒸气供维持啤酒发酵温度利用,可降低能源消耗。
2、啤酒废水
(1)啤酒废水的主要来源
麦芽生产过程的洗麦水、浸麦水、发芽降温喷雾水、麦糟水、凝固物洗涤水;
糖化过程的糖化废水、过滤洗涤水;
发酵过程的发酵罐洗涤水、过滤洗涤水;
灌装过程洗瓶废水、灭菌废水、破瓶啤酒、冷却水和成品车间洗涤水;
生活污水主要来自办公楼、食堂、宿舍和浴室。
(2)啤酒生产废水特点
啤酒厂生产啤酒过程用水量很大,特别是酿造、灌装工艺过程,由于大量使用新鲜水,相应产生大量废水。
由于啤酒的生产工序较多,不同啤酒厂生产过程中吨酒耗水量和水质相差较大。
啤酒工业废水按其有机物含量可以分为以下几类
冷却水:冷冻机、麦汁和发酵冷却水等,这类废水基本上未受污染。
清洗废水:大麦浸渍废水、发芽降温喷雾水、清洗生产装置废水、漂洗酵母水、洗瓶机初期洗涤水、酒罐消毒废液、巴斯德灭菌喷淋水和地面冲洗水等,这类废水受到不同程度的有机污染。
UASB厌氧反应器操作说明书
UASB厌氧反应器操作说明书 一 UASB厌氧反应器的原理: 在UASB厌氧反应器内,厌氧细菌对有机物进行三个步骤的降解:(1)水解、酸化阶段;(2)产氢产乙酸阶段;(3)产甲烷阶段,使污染物质得到去除,并产生沼气和厌氧污泥。 通过UASB内部的三相分离器的作用,实现水、污泥、沼气的分离,污泥回流至UASB底部,沼气经收集后进行沼气利用系统,清水至后续处理。 UASB厌氧反应器的操作说明 1开车: 认真执行交接班制度,提前5分钟上岗,了解上一班的情况(如UASB进水水温、水量、COD、PH值、NH3-N、SO42-,以及UASB出水水温、COD、PH 值、VFA等,并要上厌氧反应器巡视出水有无异常现象)掌握本班的生产要求,做好班前检查工作,熟悉厌氧塔进水泵的运行情况。 在预处理中废水达到工艺控制参数后,既可开启厌氧泵往UASB进水。 2操作过程: 1)在预处理的废水满足厌氧处理所需的进水条件后,启动厌氧泵向UASB反应器进水。启动厌氧泵之前检查需检查泵是否正常,开启泵后,检查流量计显示,判断废水是否正常输出。调节泵的出口阀门,将各厌氧反应器的流量调节到规定范围;起用泵前一定要详细检查该泵的运转纪录,确认该泵无异常后方可启用。2)密切注意厌氧反应器上部出水情况,要注意跑泥现象,防止出水带泥过多,一般小于20%,定期清理溢流堰口的堵塞物,但需注意防止跌落溺水。 3)密切关注厌氧反应器出水的COD、PH值、VFA、温度等指标,防止反应器
工艺指标变化过大; 4)经常巡视厌氧反应器顶部水面的情况,防止大量气体溢出; 5)经常观察水封中的水位,将水封水位控制在一定高度; 6)根据需要,每班进行取样送检,并根据化验结果判断厌氧反应器的运行状况。3停止: 1)当预处理没有足够的废水或预处理水质达不到工艺控制控制要求时,反应器停止进水,待预处理正常后,再恢复进水;但在停水时要密切注意反应器内的温度变化,如温度下降多(超过5℃),再次进水时就先需将反应器的温度升至原正常运行时的温度,防止因温度变化的原因使反应器运行出现问题; 2)当反应器出水带泥过多(SV≥20%要密切关注)或出水水质变差时,减少反应器的进水量或改为间歇进水,防止反应器的深度恶化; 3)当UASB出水VFA大于8或UASB的COD去除率小于50%,适当减少反应器的进水量或改为间歇进水,甚至停止进水,防止反应器的深度恶化。 4、设备使用和维修说明: 1)定期对UASB反应器的拦杆、平台、水封、机泵等设备进行清洗、油漆等保养;清理时要注意正在运转的设备内部不能清理; 2)经常对UASB出水堰进行清理,防止水堰的堵塞;对于清理溢流堰口的时,应在溢流堰口上铺上木板、搭上平台,防止溺水; 1)厌氧进水泵在运行时,需经常检查,并注意水泵的压力变化,以及出口流量变化,防止泵烧坏或泵空转等现象出现; 2)经常检查流量计计数的变化,防止进水量的波动;
厌氧反应器的运行控制
1、污泥的培养、类型和主要性能 UASB反应器是目前各种厌氧处理工艺所能达到的处理负荷较高的高浓度有机废水处理装置,这是因为反应器内以甲烷菌为主体的厌氧微生物形成了粒径为1~5mm的颗粒污泥。不同的水质与环境条件会有不同的颗粒污泥的形成过程,颗粒污泥的类型和性质也会不同。 2、进水基质的类型及营养比的控制 为满足厌氧微生物的营养要求,运行过程中需保证一定比例的营养物数量,一般应控制C:N:P在(200~300)∶5∶1为宜。在反应器启动时,稍加一些氮、磷、微量元素等有利于微生物的生长繁殖。 3、进水中悬浮固体浓度的控制 对进水中悬浮固体(SS)浓度的严格控制要求是UASB反应器处理工艺与其他厌氧处理工艺的明显不同之处。对低浓度废水而言,其废水中的SS、COD的典型值为0.5,对于高浓度有机废水而言一般应将SS、COD的比值控制在0.5以下。
4、有毒有害物质的控制 ①氨氮(NH3-N)浓度的控制:氨氮浓度的高低对厌氧微生物产生2种不同影响。当其浓度在5~200mgL时,对反应器中的厌氧微生物有刺激作用;浓度在1500~3000mgL时,将对微生物产生明显的抑制作用。一般宜将氨氮浓度控制在100mg/L以下。 ②硫酸盐(SO42-)浓度的控制:UASB反应器中的硫酸盐离子浓度不应大于5000mgL,在运行过程中UASB的COD、SO42-比值应大于10。 ③其他有毒物质:导致UASB反应器处理工艺失败的原因,除上述几种以外,其他有毒物质的存在也必须加以十分注意。这些物质主要是:重金属、碱土金属、三氯甲烷、氰化物、酚类、硝酸盐和氯气等。 5、碱度和挥发酸浓度的控制 ①碱度(HCO3-):操作合理的反应器中的碱度一般应控制在2000~4000mgL之间,正常范围为1000~5000mgL。 ②VFA:在UASB反应器中挥发酸的安全浓度控制在500mgL(以HAC计)以内,当VFA的浓度小于200mgL时,一般是最好的。 6、沼气产量及其组分 当反应器运行稳定时,沼气中的CH4含量和CO2的含量也是基本稳定的。其中甲烷的含量一般为65%~75%,二氧化碳的含量为20%~30%。沼气中的氢(H2)含量一般测不出,如其含量较多,则说明反应器的运行不正常。当沼气中含有大量硫化氢气体时,反应器将受到严重的抑制而使甲烷和二氧化碳的含量大大降低。厌氧反应过程中的沼气产量及其组分的变化直接反映了处理工艺的运行状态。
IC厌氧反应器运行注意事项
IC厌氧反应器运行注意事项 IC反应器,即内循环厌氧反应器,相似由2层UASB反应器串联而成。其由上下两个反应室组成。与UASB反应器相比,在获取相同处理速率的条件下,IC反应器具有更高的进水容积负荷和污泥负荷率,IC反应器的平均升流速度可达到处理同类废水UASB反应器的20倍左右。以下是简易示意图。 IC反应器的构造及其工作原理决定了其在控制厌氧处理影响因素方面比其它反应器更具有优势。 (1). 容积负荷高:IC反应器内污泥浓度高,微生物量大,且存在内循环,传质效果好,进水有机负荷可超过普通厌氧反应器的3倍以上。 (2). 节省投资和占地面积:IC反应器容积负荷率高出普通UASB反应器3倍左右,其体积相当于普通反应器的1/4—1/3左右,大大降低了反应器的基建投资;而且IC反应器高径比很大(一般为4~8),所以占地面积少。 (3). 抗冲击负荷能力强:处理低浓度废水(COD=2000~3000mg/L)时,反应器内循环流量可达进水量的2~3倍;处理高浓度废水(COD=10000~15000mg/L)时,内循环流量可达进水量的10~20倍。大量的循环水和进水充分混合,使原水中的有害物质得到充分稀释,大大降低了毒物对厌氧消化过程的影响。 IC反应器在运行过程中的日常注意事项 由于该污水站厌氧工艺处理设备主要是IC厌氧反应器,其主要的控制参数有以下内1、污泥菌种的成分 污泥菌种的成分:厌氧污泥中具有处理污染物能力的就是细菌等有机物质,菌群的组成及菌种的成分决定了其颗粒强度、产甲烷活性及对污水的适应能力。一般来说,污泥中有机物的成分占70%左右,污泥外部菌种主要为丝菌,污泥内部主要为杆菌、球菌等。
高浓度有机废水厌氧处理反应器类型总结
高浓度有机废水厌氧处理反应器总结 1厌氧生物滤池(AF) 厌氧生物滤池是一种内部装填有微生物载体(即滤料)的厌氧生物反应器。厌氧微生物部分附着生长在滤料上,形成厌氧生物膜,部分在滤料空隙间悬浮生长。污水流经挂有生物膜的滤料时,水中的有机物扩散到生物膜表面,并被生物膜中的微生物降解转化为沼气,净化后的水通过排水设备排至池外,所产生的沼气被收集利用。厌氧生物滤池值所以能够成为高速反应器,是在于它采用了生物固定化技术,是污泥在反应器内停留时间(SRT)极大的延长。 1.1构造 (1)升流式厌氧生物滤池 升流式厌氧生物滤池的污水有底部进入,向上流动通过滤层,处理水从滤池顶部的旁侧流出,沼气则通过设于滤池顶部的收集管排出滤池; (2)降流式厌氧滤池 降流式厌氧滤池中,布水系统设于池顶,污水由顶部均匀向下直流到底部,生物反应产生的气体的流动可起一定的搅拌作用,因而无需复杂的配水系统,微生物附着在定向排列的滤料上,起降解有机物的作用。 1.2反应器特点 (1)是一种内部填充有微生物载体的厌氧生物反应器。厌氧微生物部分附着生长在填料上,形成厌氧生物膜,部分在填料空隙间处于
悬浮状态。废水流过被淹没的填料,污染物被去除并产生沼气; (2)AF能承受较高的有机物体积负荷[生产性使用装置的最大有机负荷通常在10~16kgCOD/(m3·d)之间]; (3)AF具有良好的运行稳定性,较能承受水质或水量的冲击负荷。 (4)出水可不回流,但如果出水回流,可降低进水浓度,减小堵塞的可能性,使填料中生物量趋向于均匀分布; (5)反应器内污泥产率低,运行启动快。 (6)AF具有生物浓度高、微生物停留时间长、耐冲击负荷;停止运行后,再启动容易;无需污泥回流.运行管理简便等优点。 1.3 存在的问题 ①反应器放大设计的相似理论问题;②加强反应器颗粒化规律及生物膜附着过程机理的研究,以缩短启动时间;③加强填料技术的研究,以开发性能更好、价格低廉的新型填料;④从生态学角度深入研究AF中微生物的组成及其相互关系,以明了AF性能的本质因素等。 2 厌氧流化床反应器(AFB) 厌氧流化床( Anaerobic Fluidized-bed,AFB)反应器用于高浓度有机废水处理的优越性已为众多研究者证实。 这种反应器的典型结构是圆柱形, 其中充填有载体粒子。载体粒径一般为0.3-3.0mm。构成生物膜的厌氧微生物附着在其上生长而形成生物粒子。污水作为流化介质流经床层使生物粒子克服重力和液体
UASB基础知识
一、概述 UASB是升流式厌氧污泥床反应器废水厌氧生物处理技术的简称。 1971年荷兰瓦格宁根(Wageningen)农业大学拉丁格(Lettinga)教授通过物理结构设计,利用重力场对不同密度物质作用的差异,发明了三相分离器。使活性污泥停留时间与废水停留时间分离,形成了上流式厌氧污泥床(UASB)反应器的雏型。 1974年荷兰CSM公司在其6m3反应器处理甜菜制糖废水时,发现了活性污泥自身固定化机制形成的生物聚体结构,即颗粒污泥(granular sludge)。颗粒污泥的出现,不仅促进了以UASB为代表的第二代厌氧反应器的应用和发展,而且还为第三代厌氧反应器的诞生奠定了基础。 继荷兰之后,德国,瑞士,美国以及我国也相继开展了对UASB的深入研究和技术开发工作,并将其作为一种新型厌氧处理工艺在高浓度有机废水处理中快速的推广应用。目前全世界已有1000余座UASB反应器在实际生产中使用。 二、反应器的基本构造与原理 UASB反应器是集有机物去除及泥(生物体)、水(废水)和气(沼气)三相分离于一体的集成化废水处理工艺,其工艺的突出特征是反应器中可培养形成沉降性能良好的颗粒污泥、形成污泥浓度极高的污泥床,使其具有容积负荷高,污泥截留效果好,反应器结构紧凑等一系列优良的运行特征。 1、UASB反应器的构造 图1是UASB反应器的示意图。UASB反应器的主体部分主要分为两个区域,即反应区和三相分离区。其中反应区为UASB 反应器的工作主体。 反应器的基本构造主要由污泥床、污泥悬浮层、沉淀区、三相分离器及进出水系统等各功能部分组成。 2、UASB工作原理 (1)反应过程
UASB由污泥反应区、气液固三相分离器(包括沉淀区)和气室三部分组成。在底部反应区内存留大量厌氧污泥,具有良好的沉淀性能和凝聚性能的污泥在下部形成污泥层。要处理的污水从厌氧污泥床底部流入与污泥层中污泥进行混合接触,污泥中的微生物分解污水中的有机物,把它转化为沼气。沼气以微小气泡形式不断放出,微小气泡在上升过程中,不断合并,逐渐形成较大的气泡。 在污泥床上部由于沼气的搅动形成一个污泥浓度较稀薄的污泥和水一起上升进入三相分离器,沼气碰到分离器下部的反射板时,折向反射板的四周,然后穿过水层进入气室;集中在气室的沼气,用导管导出,固液混合液经过反射进入三相分离器的沉淀区,污水中的污泥发生絮凝,颗粒逐渐增大,并在重力作用下沉降。沉淀至斜壁上的污泥沿着斜壁滑回厌氧反应区内,使反应区内积累大量的污泥,与污泥分离后的处理出水从沉淀区溢流堰上部溢出,然后排出污泥床。 3、工艺特点 UASB 反应器运行的3 个重要的前提是: ①反应器内形成沉降性能良好的颗粒污泥或絮状污泥; ②出产气和进水的均匀分布所形成的良好的搅拌作用; ③设计合理的三相分离器,能使沉淀性能良好的污泥保留在反应器内。 (1)污泥颗粒化 UASB 反应器利用微生物细胞固定化技术-污泥颗粒化实现了水力停留时间和污泥停留时间的分离,从而延长了污泥泥龄,保持了高浓度的污泥。颗粒厌氧污泥具有良好的沉降性能和高比产甲烷活性,且相对密度比人工载体小,靠产生的气体来实现污泥与基质的充分接触,节省了搅拌和回流污泥的设备和能耗;也无需附设沉淀分离装置。同时反应器内不需投加填料和载体,提高了容积利用率。 (2)良好的自然搅拌作用 在UASB反应器中,由产气和进水形成的上升液流和上窜气泡对反应区内的污泥颗粒产生重要的分级作用。这种作用不仅影响污泥颗粒化进程,同
污水处理系统操作规程
污水处理系统操作规程 一、污水处理运行安全操作要求 1.正确穿戴好个人劳动防护用品。 2.仔细阅读上班次的运行记录、化验记录,确认设备运行参数是否发生了变化,掌握系统存在的问题。 3.维护好值班室、加药间、现场的环境卫生。 4.检查系统管路阀门是否在运行位置。 5.检查各运转设备是否有异响,是否有“跑、冒、滴、漏”现象。 6.根据系统运行情况、水质情况及时调整加药量和控制参数。 7.检查叠螺机运行是否正常,药剂与污泥的比例是否恰到好处。 8.检查加药罐内药剂是否充足。 9.检查水池表面泡沫、浮泥情况。 10.检查各水池是否有杂物,整理并打扫干净。 11.检查各设备是否正常运转,若发现设备故障立即切换至备用设备并安排检修。 12.检查各水泵流量是否正常,若发现异常立即进行排查恢复。 二、污水处理工艺流程图
工艺流程说明: 工艺流程说明:生产废水进入均质调节池,均匀水质水量,调节PH 值后,通过泵提进入水解酸化池,在水解酸化池中部分大分子有机物被水解成小分子有机物,有效加快厌氧反应进程,提高有机物去除率;酸化后的废水进入ACS 厌氧反应器,去除大部分COD ,出水沉淀后进入AmOn 池,通过调节回流比去除绝大部分COD 和总氮;最后通过二沉池去除SS 后,达标外排,进入清水池后达标排放。厌氧、兼氧和沉淀池剩余污泥进入污泥浓缩池,通过污泥脱水机脱水后外运处理,污泥浓缩池上清液和污泥脱水机压滤液进入均质调节池,继续处理。 三、加药装置的控制 (1)碱液的配制和投加 ①先将清水放入碱药剂箱2/3处,打开气搅装置,同时将所需片碱慢慢地、均匀地加入箱内,一边搅拌继续加水,至药箱3/4处后停止加水,继续搅拌使NaOH 完全溶解,NaOH 不能即配即用,必须充分溶解后才能使用;碱液的浓度根据污水调节pH 所需的浓度为准。 ②打开NaOH 溶液加药球阀,启动NaOH 溶液加药泵,进行药剂投加,药剂投加量由现场反 生产废水均质调节池 ACS厌氧池 中间沉淀池一级A池 一级O池 二级A池 二级O池 达标排放泵提 加压空气 硝化水回流硝化水回流 污泥回流沼气处理系统流失污泥回流污泥浓缩池上清液自流至均质调节池叠螺式污泥脱水机压滤液自流至均质调节池提升池 泵提 清水池
详细介绍IC厌氧反应器工作过程
详细介绍IC厌氧反应器工作过程 厌氧塔又叫厌氧设备厌氧反应器等别名,主要有三部分组成分别由污泥反应区、气液固三相分离器和气室,设备内仓留有大量厌氧污泥,具有良好的沉淀性能和凝聚性能的污泥在下部形成活性污泥层。 厌氧塔反应器设备的运行流程: 污水从厌氧设备底部流入污泥中层进行混合反应,中层部分的厌氧生物分解污水中的COD等有机物并转化成气体。产生的气泡不断合并成大气泡,在厌氧塔中上部由于气体的上升产生搅动使较稀薄的污泥和水一起上升进入厌氧设备三相分离器,气体碰到分离器下部的挡板时转向挡板的四周过水层进入气室,集中在气室中的气体通过管道排出,固液混合液经过反射进入三相分离器的沉淀区,污水中的污泥发生絮凝,颗粒逐渐增大,并在重力作用下沉降。沉淀至斜壁上的污泥沼着斜壁滑回厌氧反应区内,与污泥分离后的上清液通过溢流堰上部溢出流入污水处理工艺中的下一道好氧工序。 IC厌氧反应器工作原理: 废水好氧生物处理方法的实质是利用电能的消耗来达到改善废水水质的一种技术措施,因此能、低能耗的厌氧废水处理技术在近代废水处理技术中得到了广泛的应用,厌氧生物处理法有了较大的发展。厌氧消化工艺由普通厌氧消化法演变发展为厌氧接触法(厌氧活性污泥法)、生物滤池法、上流式厌氧污泥床反应器(UASB)、厌氧流化床、复合厌氧法等,其中普通消化池法、厌氧接触法等为*代厌氧反应器,生物滤池法、UASB、厌氧流化床等为第二代厌氧反应器,随着厌氧技
术的发展,由UASB衍生的EGSB和IC(内循环)厌氧反应器为第三代厌氧反应器。EGSB相当于把UASB反应器的厌氧颗粒污泥处于流化状态,而IC反应器则是把两个UASB反应器上下叠加,利用污泥床产生的沼气作为动力来实现反应器内混合液的循环。 IC厌氧反应器工作过程: 通过以下的对IC厌氧反应器的描述,您可以很清楚的了解到其所具有的优点的基本原理。 一般可以理解为IC是由上、下两个UASB组成两个反应室,下反应室负荷高,上反应室负荷低,在反应器内部,对应分为三个反应区。 高负荷区 利用特殊的多旋流式防堵塞的布水系统,高浓度的有机废水均匀进入反应器底部,完成与反应器内污泥的充分混合,由于内循环作用、高的水力负荷和产气的搅动,导致反应器底部的污泥膨胀状态良好,使废水与污泥能够充分接触,如此良好的传质作用和较高的污泥活性才保证了IC反应器具有较高的有机负荷。 低负荷区 低负荷区也是精处理区,在这个反应区内水力负荷和污泥负荷较低,产气量少,产气搅动作用小,因此可以有效的对废水中的有机物进行再处理。 沉降区 IC反应器顶部为污泥沉降区,有机物已基本去除的废水中的少量悬浮物在本区内进一步进行沉降,保证IC出水水质达到规定要求。
UASB升流式厌氧反应器
UASB升流式厌氧反应器 在污水厌氧处理上,UASB是常用的一种厌氧反应器,与好氧相比其主要的优势在于它的运行费用低,污泥产量低(只有15%转化成剩余污泥),且性能稳定,可回收能源。 污水经进水总管和配管进入反应器后上流经过颗粒污泥床,在这里,污水中的有机物被降解转化成甲烷和二氧化碳。在反应器下部产生的沼气携带污泥上升至三相分离器,沼气、污泥和处理后的水在三相分离器中被分离出来,污泥回沉于厌氧污泥床,处理后的水经出水堰排出,收集的沼气被引至厌氧反应器上的气水分离器内,经水封罐后可直接送至燃烧火炬或锅炉。 UASB升流式厌氧反应器在运行过程中要严格控制pH值在6.5-7.5(最好在6.8-7.2)的范围内,温度应控制在32-38℃,一般掌握在35℃左右。 UASB升流式厌氧反应器的容积负荷为10-20kgCOD/m3.d。COD去除率可达80-90%,去除1 kgCOD可产生0.4 m3甲烷气体。 UASB厌氧反应器也可为钢筋混凝土结构,可根据用户提供的现场情况进行设计和施工。 生物接触氧化池 生物接触氧化技术在有机污水处理中应用很广。它由池体、填料、布水、导流和曝气装置组成。在构筑物中安装一些比表面积很大的材料作为载体(填料),微生物附着其上形成生物膜,水中有机污染物、溶解氧在与生物膜接触的过程中,将有机污染物氧化分解,使污水得到净化。生物接触氧化法的特点是处理效果稳定、管理简便、耐冲击负荷、便于与其他处理技术组合使用。 生物接触氧化法中微生物所需的氧气是通过鼓风曝气供给。生物膜生长至一定厚度后,近填料壁的微生物将由于缺氧而进行厌氧代谢,产生的气体及曝气形成的冲刷作用会造成生物膜的脱落,并促进新生物膜生长,形成生物膜的新陈代谢。脱落生物膜将随水流出池外。 生物接触氧化法一般为多池结构,在每个生物接触氧化池中水流属完全混合型,但多池串联,水流又为推流型,每个池中的生物菌种类及数量是不一样的,各个池中生长着与污水相适宜的生物菌,这样可保证污水中有机物的有效降解。生物接触氧化池内设有填料,部分微生物以生物膜的形式固着生长于填料表面,部分则是絮状悬浮生长于水中。因此它兼有活性污泥法与生物滤池二者的特点。 生物接触氧化法与活性污泥法相比具有下列特点: ⑴由于填料比表面积大,池内充氧条件良好,生物接触氧化池内单位容积的生物固体量(10-20g/l)都高于活性污泥法曝气池(1.5-3.0g/l)及生物滤池(0.7-7.0g/l),生物接触氧化池具有比较高的容积负荷 3-6kgCOD/m3.d ,COD去除率可达90%左右。
渗滤液工艺操作规程
渗滤液工艺操作规程
————————————————————————————————作者:————————————————————————————————日期: ?
工艺操作规程 (2006第一版) 深圳市慧源环境技术有限公司编制
目录 一、工艺流程说明 (附工艺流程图) 二、操作规程 1.进水的操作规程 2.生化池操作规程 3.超滤系统操作规程 4.纳滤系统操作规程 5.实验室操作规程 附件一盐酸使用安全知识 附件二烧碱使用安全知识
一、 工艺流程说明 工艺流程(详见工艺流程图)可分为以下四个子系统: ● U ASB 厌氧反应器 ● 膜生化反应器(反硝化池、硝化罐、超滤装置) ● 纳滤装置 ● 污泥处理系统 膜 上 生 污 清 化 泥 液 反 回 应 流 剩余污泥 器 纳滤浓液 浓缩污泥 达标排放 工 艺 流 程 图 硝化池 超滤系统 污泥 浓缩 池 渗滤液调节池 反硝化池 回喷垃圾坑或回填埋场 厌氧反应池 纳滤系统
1.厌氧反应器 垃圾渗滤液经过收集进入调节池,用水泵抽送到厌氧反应器。为保护后续的超滤膜,厌氧反应器进水前加了排污过滤器,以祛除进水中的小颗粒物、绳子、头发等。为了使厌氧反应器在气温较低的时候维持一定的反应温度,在厌氧进水前、过滤器后增加一套换热装置,用于加热进到厌氧池的污水,使反应器水温达到30。C~35。C。 注:厌氧反应器在某些工程中没有设置。 2.膜生化反应器系统 膜生化反应器系统由生化池和超滤两部分组成。 生化池由反硝化池和硝化池组成,污水中含有碳、氮和磷等元素的有机物经过生物降解得到有效祛除。 反硝化池内安装有混合搅拌装置(液下搅拌机)。泥水混合物由反硝化池溢流至硝化池。 硝化池内采用自吸式射流曝气装置提供氧气。 在硝化池中,通过高活性的好氧微生物作用,降解大部分有机物,并使氨氮氧化为硝酸盐和亚硝酸盐。 硝化池内的泥水混合物通过超滤进水泵进入超滤系统(UF)。超滤过程如下:在压力作用下,料液中含有的溶剂及各种小的溶质从高压料侧透过超滤膜到达低压侧,从而得到清液,清液排放或进入下一级处理系统;而尺寸比膜孔大的溶质分子被膜截留成为浓缩液,浓液大部分回流到反硝化池,少部分作为剩余污泥通过排泥管排到污泥浓缩池。 回流到反硝化池的超滤浓液和系统进水混合,在缺氧环境中硝酸盐和亚硝酸盐还原成氮气排出,达到脱氮的目的。 3.纳滤和纳滤浓液的处理系统 为达到严格的排放标准,在UF后加上纳滤系统(NF),NF的作用是截留那些不可生化的大分子有机物COD,纳滤的清液可以达到很低的COD 浓度水平。 产生的纳滤浓缩液经过流量计计量后与絮凝剂在管道混合器中混凝再到污泥处置系统。 4.污泥处理与处置系统 每天产生的剩余污泥和絮凝后的纳滤浓液进入污泥浓缩池沉淀浓缩,清液溢流到调节池,浓缩污泥从池的底部抽到槽车回灌垃圾坑或填埋场。
厌氧反应器设备参数
IC厌氧系统技术要求 一、工艺要求 1.1预处理段及IC厌氧反应器进水水质 罐体直径:10.0m 罐体高度:15.0m 单体容积:1175m3 气体压力: 1000毫米汞柱
反应器内件:三相分离器模块 模块支撑系统 进水布水系统(含分水包) 内部管道系统 管道与人孔 径DN250,保温厚度50㎜,保温材质为玻璃丝 棉,满足相关规范要求。 3.排除内容: 土建基础:钢筋混凝土、表面敷设沥青砂垫层 2.2 反应器壳体材料要求:
?底板: Q235 *12mm ?1-2层板: Q235 *12mm ?3-6层板: Q235 *10mm ?7-10层板: Q235 *8mm ?出水堰:碳钢防腐材质4mm ?母体所属管道及阀门 2)布水系统 布水系统包括: ?布水管
?导流罩/布水罩(δ=4mm) ?支撑 3)三相分离器模块 ?IC三相分离系统由上部和下部三相分离器模块组成,模块由优质聚丙烯(PP)材料制成,三相分离器模块使用插接模式,保证整体牢固、 使用寿命。三角板采用折弯而成。 ?碳钢防腐材质的布水支管 6)气液分离器 位于IC反应器的顶部,它包括: 数量: 4个 ?碳钢防腐材质圆柱形罐体(δ=5mm)
?采用刮刀式视镜(每个气液分离器不得低于两个); 7)顶部平台 ?材质为碳钢防腐材质。 ?主要作为罐顶气液分离器的支撑平台,方便气液分离器的巡检观察; ?罐顶平台踏步为碳钢防腐花纹钢板。 所有机械除锈为St2.0级标准。 3) 调试培训工作 乙方负责设备的调试工作,以及调试所用颗粒污泥等材料物品,直至设备运 行正常。 乙方负责培训甲方操作人员,保证操作人员能独立操作,并能处理运行日常
厌氧反应器的发展历程与应用现状.
厌氧反应器的发展历程与应用现状 迟文涛1, 赵雪娜2, 江翰3, 李伟涛3, 王凯军1 (1. 北京市环境保护科学研究院, 北京100037;2. 天津城建学院, 天津300384;3. 北京科技大学, 北京100083 摘要:污水厌氧反应器因其能耗少, 运行费用低等优点在全世界范围内得到了广泛的应用。对厌氧反应器的发展历程进行了系统的论述, 重点介绍了第三代厌氧反应器的特点并展望了厌氧反应器的发展前景。关键词:厌氧; EGSB 反应器; IC 反应器; 厌氧流化床; 新型反应器 中图分类号:X505文献标识码:B文章编号:1008-2271(2004 01-0031-03水环境污染和水资源短缺是全球正面临的两大问题。目前, 我国每年污水排放总量为395亿m 3, 根据预测, 到2050年, 我国污水排放总量将高达1200亿m 3[1]。 研制高效低耗并具有多种附加功能的厌氧污水处理工艺已经成为亟待解决的重大课题。1100多年的历史。1860年法国工程师Mouras 就采用厌氧方法处理废 水中经沉淀的固体物质。1896年英国出现了第一座用于处理生活污水的厌氧消化池, 所产生的沼气用于照明 [2] 。1904年德国的Imhoff 将其发展成为 Imhoff 双层沉淀池(即腐化池 , 这一工艺至今仍然 在有效地利用[3] 。在1910年至1950年, 高效的、可
加温和搅拌的消化池得到了发展, 其比腐化池有明显的优势。Schroepfer 在20世纪50年代开发了厌氧接触反应器。这种反应器是在出水沉淀池中增设了污泥回流装置, 增大了厌氧反应器中的污泥浓度, 处理负荷和效率显著提高。上述反应器被称为第一代厌氧反应器。 由于厌氧微生物生长缓慢, 世代时间长, 而厌氧 收稿日期:2003-12-11 作者简介:迟文涛,1977年生, 男, 吉林扶余人, 在读研究生。 消化池无法将水力停留时间和污泥停留时间分离, 由此造成水力停留时间必须较长, 一般来讲第一代厌氧反应器处理废水的停留时间至少需要20~30天[4]。 2:。(2 反应 。 依据这一原则,20世纪60年代末,Mccarty 和Y oung 推出了第一个基于微生物固定化原理的高速 厌氧反应器———厌氧滤池。它的成功之处在于在反应器中加入固体填料(如沙砾等 , 微生物由于附着生长在填料的表面, 免于水力冲刷而得到保留, 巧妙地将平均水力停留时间与生物固体停留时间相分离, 其固体停留时间可以长达上百天, 这就使得厌氧处理高浓度污水的停留时间从过去的几天或几十天缩短到几小时或几天。 在相同的温度下, 厌氧滤池的负荷高出厌氧接触工艺2~3倍, 同时有很高的COD 去除率, 而且反应器内易于培养出适应有毒物质的厌氧污泥。1972年, 厌氧滤池首次较大规模地应用于小麦淀粉废水处理。 1974年, 荷兰Wagningen 农业大学的Lettinga
UASB升流式厌氧污泥床
UASB 一、引言 厌氧生物处理作为利用厌氧性微生物的代谢特性,在毋需提供外源能量的条件下,以被还原有机物作为受氢体,同时产生有能源价值的甲烷气体。厌氧生物处理法不仅适用于高浓度有机废水,进水BOD最高浓度可达数万mg/l,也可适用于低浓度有机废水,如城市污水等。 厌氧生物处理过程能耗低;有机容积负荷高,一般为5-10kgCOD/m3.d,最高的可达30-50kgCOD/m3.d;剩余污泥量少;厌氧菌对营养需求低、耐毒性强、可降解的有机物分子量高;耐冲击负荷能力强;产出的沼气是一种清洁能源。 在全社会提倡循环经济,关注工业废弃物实施资源化再生利用的今天,厌氧生物处理显然是能够使污水资源化的优选工艺。近年来,污水厌氧处理工艺发展十分迅速,各种新工艺、新方法不断出现,包括有厌氧接触法、升流式厌氧污泥床、档板式厌氧法、厌氧生物滤池、厌氧膨胀床和流化床,以及第三代厌氧工艺EGSB和IC厌氧反应器,发展十分迅速。 而升流式厌氧污泥床UASB( Up-flow Anaerobic Sludge Bed,注:以下简称UASB)工艺由于具有厌氧过滤及厌氧活性污泥法的双重特点,作为能够将污水中的污染物转化成再生清洁能源——沼气的一项技术。对于不同含固量污水的适应性也强,且其结构、运行操作维护管理相对简单,造价也相对较低,技术已经成熟,正日益受到污水处理业界的重视,得到广泛的欢迎和应用。 本文试图就UASB的运行机理和工艺特征以及UASB的设计启动等方面作一简要阐述。 二、UASB的由来 1971年荷兰瓦格宁根(Wageningen)农业大学拉丁格(Lettinga)教授通过物理结构设计,利用重力场对不同密度物质作用的差异,发明了三相分离器。使活性污泥停留时间与废水停留时间分离,形成了上流式厌氧污泥床(UASB)反应器的雏型。1974年荷兰CSM公司在其6m3反应器处理甜菜制糖废水时,发现了活性污泥自身固定化机制形成的生物聚体结构,即颗粒污泥(granular sludge)。颗粒污泥的出现,不仅促进了以UASB为代表的第二代厌氧反应器的应用和发展,而且还为第三代厌氧反应器的诞生奠定了基础。 三、UASB工作原理 UASB由污泥反应区、气液固三相分离器(包括沉淀区)和气室三部分组成。在底部反应区内存留大量厌氧污泥,具有良好的沉淀性能和凝聚性能的污泥在下部形成污泥层。要处理的污水从厌氧污泥床底部流入与污泥层中污泥进行混合接触,污泥中的微生物分解污水中的有机物,把它转化为沼气。沼气以微小气泡形式不断放出,微小气泡在上升过程中,不断合并,逐渐形成较大的气泡,在污泥床上部由于沼气的搅动形成一个污泥浓度较稀薄的污泥和水一起上升进入三相分离器,沼气碰到分离器下部的反射板时,折向反射板的四周,然后穿过水层进入气室,集中在气室沼气,用导管导出,固液混合液经过反射进入三相分离器的沉淀区,污水中的污泥发生絮凝,颗粒逐渐增大,并在重力作用下沉降。沉淀至斜壁上的污泥沼着斜壁滑回厌氧反应区内,使反应区内积累大量的污泥,与污泥分离后的处理出水从沉淀区溢流堰上部溢出,然后排出污泥床。 基本出要求有: (1)为污泥絮凝提供有利的物理、化学和力学条件,使厌氧污泥获得并保持良好的沉淀性能;
升流式固体厌氧反应器
升流式固体厌氧反应器(USR),是一种结构简单、适用于高悬浮固体有机物原料的反应器。原料从底部进入消化器内,与消化器里的活性污泥接触,使原料得到快速消化。未消化的有机物固体颗粒和沼气发酵微生物靠自然沉降滞留于消化器内,上清液从消化器上部溢出,这样可以得到比水力滞留期高得多的固体滞留期(SRT)和微生物滞留期(MRT),从而提高了固体有机物的分解率和消化器的效率。在当前畜禽养殖行业粪污资源化利用方面,有较多的应用。许多大中型沼气工程,均采用该工艺。 经过USR处理后产生的沼液属于高浓度有机废水。该废水具有有机物浓度高、可生化性好、易降解的特点,不能达到排放标准,因此除用于花卉蔬菜等的肥料外,剩余沼液须回流至集水池,经过好氧处理后达标回用或排放。针对该沼液含氨氮较高的特点,通过预处理可将溶于水的挥发性氨氮部分去除。沼液中的有机物则通过生物法进行处理。即利用水中微生物的新陈代谢作用,将有机污染物降解,达到净化水质、消除污染的目的 前处理 7.1前处理工艺类型 7.1.1 “能源生态型”沼气工程 污水通过管道自流入调节池,在调节池前设有格栅,以清除较大的杂物,人工清出的粪便运至调节池,与污水充分地混合,然后流入到计量池,计量池的容积根据厌氧消化器的要求确定。当以鸡粪为原料时,应在调节池后设沉砂池。粪便的加入点与厌氧消化器类型有关,一般在调节池加入,带有搅拌装置的塞流式反应器也可直接加入到厌氧消化器。 7.1.2 “能源环保型”沼气工程 污水通过管道自流入调节池,在调节池前设有格栅,以清除较大的杂物,调节池的污水用泵抽入到固液分离机,分离的粪渣用作有机肥原料,分离出的污水流入沉淀池,沉淀的污泥进入污泥处理设施,上清液自流入集水池。 7.2前处理的一般规定 7.2.1 “能源生态型”沼气工程前处理的一般规定
沼气安全操作规程及注意事项
沼气安全操作规程及注意事项 ●沼气进锅炉操作规 ★点火前准备 A.检查锅炉引起风机,燃烧器等正常完好,确保无误后告知厌氧处理站开放沼气供应。 B.锅炉燃烧使用沼气前,先关停引风机,鼓风机,再用点火把点燃(明火)正常后方能打开沼气阀送气,沼气燃烧正常后,方能启动引风机,鼓风机。 C.锅炉燃烧正常后,关闭阻火器,排空阀。 D.锅炉停止使用沼气时,必须先打开阻火器排空阀,然后再关闭锅炉进气阀,并通知厌氧操作人员打开厌氧罐排空阀。 ●沼气安全操作流程 开气顺序:打开锅炉膛进所阀→关闭2#阻火器排空阀→关闭1#阻火器排空阀→关闭厌氧罐排空阀。 关停顺序:打开厌氧罐排空阀→打开1#阻火器排空阀→打开2#阻火器排空阀→关闭锅炉膛进气阀。 特别提示:司炉工上班前要阅读沼气安全操作规程,掌握操作技术,确保环保设施的安全运行。 厂安全生产管理领导小组。 污水治理设施应急预案
污水处理站污水超标排放应急措施 1.立即通知处生产计划科减少送水量,同时对进入工艺的污水进行 减量处理。 2.厂生产技术人员立即对进厂水质、工艺运行参数、出水水质数据 进行分析,根据超标数据对相关的工艺进行及时调整。如BOD、COD超标,则调整进水量、风量、回流量等。如SS超标,则及时排泥,增加污泥处理量等。以最短时间使工艺运行、出水水质达到正常排放标准。 污水处理站台风应急措施 1.及时通知各部门做好防台风的准备,将各岗位门窗关紧对变电所 架空进户线进行不间断地巡视检查,发现情况立即进行紧急处置。 2.尽量减少操作人员在构筑物上巡视或操作次数,待风力减小后再 外出巡视操作。 3.厂抢险队员、车辆做到随叫随到,严阵以待,以处置突发事件的 发生。 污水处理厂暴雨应急措施 1.根据天气预报,预先对各设备进行检查,确保完好。对厂内雨 水管道进行疏通,确保畅通。 2.增加水泵,降低集水井水位,直到所有水泵满负荷运行。对易 进水的电缆沟安装潜水泵。 3.将各岗位门窗关紧,防止雨水流进操作间影响机器设备的正常 运行。
厌氧处理操作
厌氧处理操作 UASB厌氧处理系统包括:东配水池、西配水池、凉水塔、竖流沉降罐、换热间、UASB厌氧罐、一沉池、沼气间 一、主要任务 1.1 对各排水车间、生活污水所排原水取样送化验室监测各项指标; 1.2 竖流沉降罐溢流堰板的调节,重力曲筛筛上杂物的清理,竖流沉降罐内污泥清理、外运; 1.3 调节配水池原水水质及预酸化池水质,调节进水COD、温度及pH值,使其符合厌氧进水要求; 1.4 操作污水提升泵,控制UASB(升流式厌氧污泥床)及IC(内循环厌氧反应器)进水流量; 1.5 UASB厌氧反应器和一沉池溢流堰板的调节,保证出水均匀; 1.6 监测厌氧出水情况,取样化验出水的各项指标; 1.7 控制沼气水封罐水位,负责沼气缓冲罐积水
排放、水封罐定期更换水操作; 1.8 一沉池污泥的清理和外运; 1.9 监测IC反应器出水情况及产气情况,调整进水流量; 1.10 厌氧各种加药量的控制及加药系统的日常维护; 1.11 及时清理涤气塔间积液。 二、工艺参数 原水: COD≤4500mg/L; pH值:3.5~9.0,最佳范围:6.8~7.2 ; 硫酸盐≤500mg/L,COD/硫酸盐浓度≥5,最佳范围:COD/硫酸盐浓度:≥10; 温度:30~40℃;最佳温度:35~38℃;
氨氮≤500 mg/L; 上升流速:0.5~1.5m/h 三、质量标准 厌氧出水: COD≤1500 mg/L,最佳COD≤400 mg/L;(与进水COD高低而定,保证去除率在70%以上即可) VFA:≤1000mg/L,最佳≤400 mg/L; pH值6.0~8.0,最适pH值6.8~7.2; 四、操作标准 4.1东配水池 控制流量,合理配水控制各车间来水水量,根据各车间来水水质情况,混合调配;pH值不足时加纯碱或液碱;温度不足时向配水池通入蒸汽;温度高时把高温水引致凉水塔降温;定时加营养物质氯化钙和微量元素;控制配水池液位不要过低 导致污水泵进气抽空,同时不能太高导致池子冒水; 4.2 西配水池
IC厌氧反应器调试
IC厌氧反应器调试总结 此次调试的污水处理工艺采用厌氧—好氧组合方式处理来去除污水中COD、SS以及N、P等富营养化物质,经过半年的调试运行,工艺已经日趋成熟,出水质量均符合国家排放标准。工艺的稳定运行离不开重要参数的严格控制, 下面就IC厌氧工艺阶段的主要控制参数进行简要分析说明 厌氧工艺处理设备主要是IC厌氧反应器,其主要的控制参数有以下内容: PH值:反应器进水PH值要求控制在6.5~8.0之间,过低或过高的PH值都会对工艺造成巨大的影响,其影响主要体现在对厌氧菌(主要是产甲烷菌)的方面,包括:①影响菌体及酶系统的生理功能和活性②影响环境的氧化还原电位③影响基质的活性。产甲烷菌的这些性质功能遭到破坏后,处理COD的活性就会大大的降低。 温度:反应器进水温度要求控制在35.5~37.5之间,因为产甲烷菌大多数都属于中温菌,在这个范围内,其处理效率是很高的。温度高于40℃时,处理效率会急剧下降;最好也不要低于35℃,温度过低,处理效率也会下降很多。 预酸化度:废水进入厌氧反应器之前要保持足够的预酸化度,一般在30%~50%之间,最好是在40%左右。预酸化度高的情况下,VFA高,进水PH值会降低,为调解PH值,会增高污水处理的运行费用,同时还会影响污泥的颗粒化。 有毒物质:对厌氧颗粒污泥有抑制性作用的有毒物质主要是H2S和亚硫酸盐。H2S的允许浓度为小于150㎎/L,否则可能会使大部分产甲烷菌降低50%的活性;亚硫酸盐的允许浓度是小于150ppm,否则将会导致一半的产甲烷菌失去活性,所以一定要严格控制这两样有毒物质的含量,对其进行定期的检测。 容积负荷率:厌氧反应器具有很高的容积负荷率,操作手册上为16~24㎏COD /m3/d,而一些学者认为其容积负荷率还可以更高可达30~40㎏COD /m3/d,但是这个数值的短期内变化幅度最好不要过大,就是说要让厌氧菌有一定的适应时间,逐步增加或降低负荷。如果条件可以,尽量使其负荷率在一个范围之间,趋于稳定的状态。 上升流速:IC反应器的上升流速一般在4~10m/h, 当污水的进水COD值浓度较低时,需要提高流量来增加COD的负荷率,较高的上升流速会有助于颗粒污泥与有机物之间的传质过程,避免了混合不均匀对设备的影响。 污泥菌种的成分:厌氧污泥中具有处理污染物能力的就是细菌等有机物质,菌群的组成及菌种的成分决定了其颗粒强度、产甲烷活性及对污水的适应能力。一般来说,污泥中有机物的成分占70%左右,污泥外部菌种主要为丝菌,污泥内部主要为杆菌、球菌等。 除了以上这些因素外,IC反应器的运行控制条件还有很多,如进水COD浓度,污泥颗粒化程度等等,工艺正常运行,每个工艺条件都是不可缺少的,因为各个条件之间是环环相扣的的关系,一个参数出了问题,所有的问题就都会显现出来。为了避免问题的出现,就应该及时监测、化验、分析,发现异常现象,立即采取措施进行处理,防止更多问题的出现。 污水经过厌氧反应器处理后,会进入好氧段进行氧化处理。好氧段分为两个部分,即兼氧池和曝气池,兼氧池作为厌氧段与好氧段过度过成,主要用于处理N、P等富营养化物质,根
试论污水处理厂高速厌氧污泥床反应器(HSASB)工艺
试论污水处理厂高速厌氧污泥床反应器(HSASB)工艺 摘要:本文论述某造纸厂为保证污水达标排放,在原污水处理厂加设厌氧处理 单元,采用高速厌氧污泥床反应器(HSASB)的改造方案优势性。 关键词:污水处理;厌氧处理;高速厌氧污泥床反应器(HSASB) 1、项目概况 本项目废水处理采用集水池—斜筛—平流式沉淀池—幅流式沉淀池—浅层气浮—好氧曝气—幅流式二沉池处理系统工艺,其中平流式沉淀池出水大量循环回 用于废纸碎解,气浮出水回用造纸及制浆清洗系统,剩余约500m3/d经生化处理 到COD低于400mg/l后排入市政管网进行集中处理。 目前污水处理站污水处理工艺随着废水的逐渐循环回用,污染物浓度因不断 积累而增高,造成出水浓度高,外排水质不能达到市政管网水质要求,随着造纸 行业环保要求的日益严格及企业清洁生产的实施,为此,需要对现有废水处理站 进行改造,以满足外排水质要求。 厌氧技术在降解高浓废水的同时,能将其中的有机物转化为沼气作为新的能 源加以利用。厌氧处理技术作为目前最经济的高浓有机废水处理技术,已经成为 处理高浓度造纸行业废水的重要手段。 根据目前污水处理情况及场地狭小的现状,提出在好氧处理前新增厌氧处理 单元,以保证污水处理的效果,满足出水的达标排放。 2、厌氧处理工艺介绍 厌氧生物处理技术迄今已有100多年的历史,厌氧反应器的发展也经过了四 代的更新,发展到目前的第四代高速厌氧反应器技术。 第一代厌氧技术——普通消化池。普通消化池的特点厌氧消化反应与固液分离在同一个池内实现,结构简单,但缺乏补充厌氧活性污泥的特殊装置,消化器 难以保持大量的微生物细胞,对于无搅拌的消化器,还存在料液的分层现象严重,微生物不能与料液均匀接触,温度不均匀,消化效率低的缺点,增设搅拌装置又 带来高能耗的问题。 第二代厌氧技术——厌氧接触法。在消化池后设沉淀池,将沉淀污泥回流至消化池,形成厌氧接触法。该系统使污泥不流失、出水水质稳定。但厌氧接触法 存在增设污泥沉淀、污泥回流和脱气设备、混合液在沉淀池中难以沉降等缺点。 第三代厌氧技术——UASB 反应器。又称上流式厌氧污泥床反应器,是在20 世纪70年代开发的一种新型高效厌氧反应器,反应器由反应区、沉淀区和气室 三部分组成,顶部设有三相分离器。UASB具有反应器内污泥浓度高、有机负荷高、水力停留时间短、不需设搅拌器、无堵塞现象等优点。 第四代厌氧技术——高速厌氧污泥床反应器(HSASB)。高速氧污泥床反应 器(HSASB)是在第三代厌氧反应器(UASB)的基础上,把多级处理技术、流化 床技术、污泥颗粒化技术、内外循环等技术集合在同一个厌氧反应器内,在高速 厌氧污泥床反应器(HSASB)中,厌氧颗粒污泥(微生物)将废水中的COD厌氧 降解转化为沼气。高速厌氧污泥床反应器(HSASB)为内循环反应器,内循环是 基于气体提升原理,而由“上升管”和“下降管”中所含气体量的不同而产生的可达 到自行调节。产生的气体被两个称之为三相分离器的装置从所处理的废水中分离 出来,引出反应器。高速厌氧污泥床反应器(HSASB)含有上下两个UASB(上流