通风机铆焊件技术条件(精)

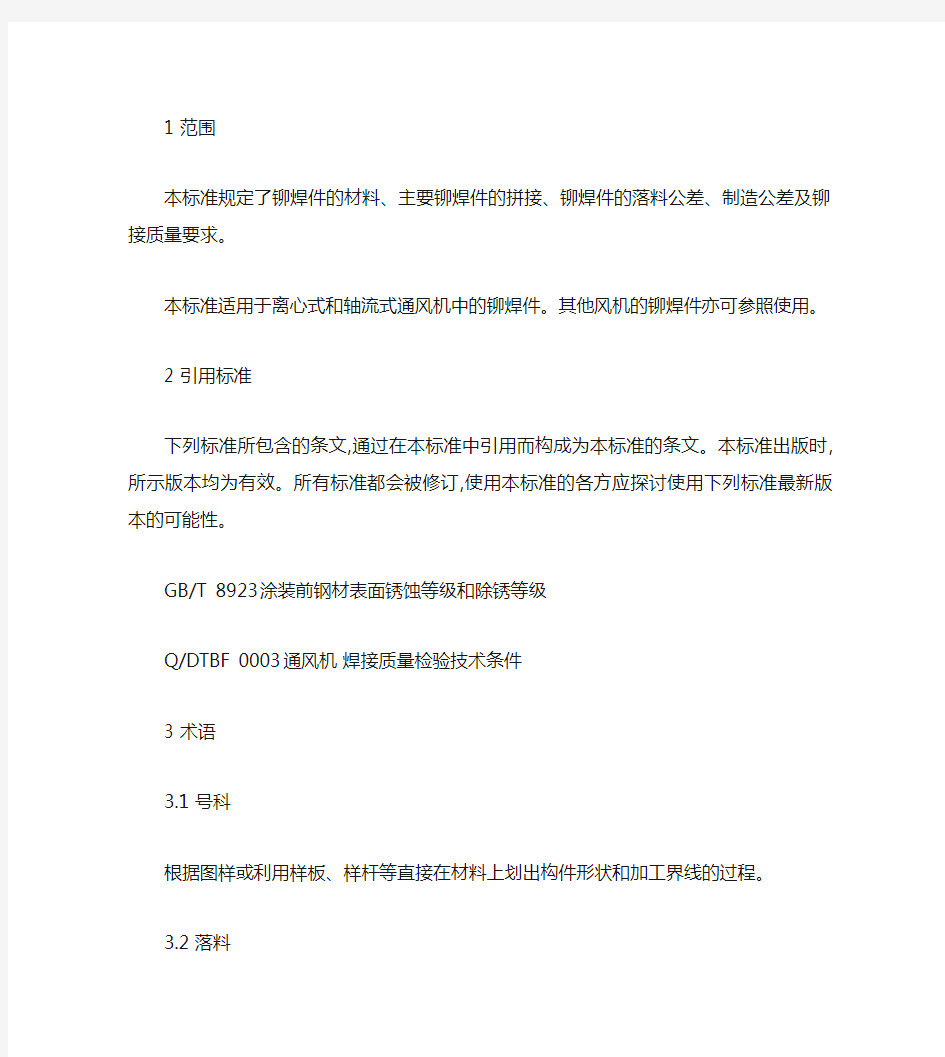
前言
为了适应公司长期发展的需要,加强企业标准化建设,方便设计检验,制定本标准。本标准由南通大通宝富风机有限公司技术中心提出并归口
本标准起草单位:南通大通宝富风机有限公司技术中心
本标准主要起草人:顾晓卫
II
通风机铆焊件技术条件
1 范围
本标准规定了铆焊件的材料、主要铆焊件的拼接、铆焊件的落料公差、制造公差及铆接质量要求。
本标准适用于离心式和轴流式通风机中的铆焊件。其他风机的铆焊件亦可参照使用。
2 引用标准
下列标准所包含的条文,通过在本标准中引用而构成为本标准的条文。本标准出版时,所示版本均为有效。所有标准都会被修订,使用本标准的各方应探讨使用下列标准最新版本的可能性。
GB/T 8923 涂装前钢材表面锈蚀等级和除锈等级
Q/DTBF 0003 通风机焊接质量检验技术条件
3 术语
3.1 号科
根据图样或利用样板、样杆等直接在材料上划出构件形状和加工界线的过程。
3.2 落料
通过气割、剪切、锯料、冲切等工序,使材料分离成所需零件的工艺方法。
3.3 样冲眼
在毛坯或工件划线后,用样冲在中心线或辅助线上打出冲点的方法称为打样冲印,其冲点称为样冲眼。
4 铆焊件的材料
4.1 通风机铆焊件所用材料应符合有关材料标准的规定,转动件须具有合格证明或检验报告。 4.2 严禁使用有夹层、重皮等缺陷的材料。
4.3 非转动件材料的外表面允许有深度不超过0.5mm的划痕,并在涂漆前予以腻平;铝材的局部划痕深度不得大于0.3mm,不锈钢及其他有色金属材料的划痕深度不得大于0.1mm.
4.4 转动件代用材料的力学性能应不低于被代用材料的力学性能。
4.5 焊接件所选用的焊条应按图样的材质选取,其力学性能不得低于母材的性能。
1
4.6 按GB/T 8923 的规定,对锈蚀等级为B 级以下的材料,不得用在转动件上,也不得用在其余零部件的外表面上。
5 主要铆焊件的拼接
5. 1 离心通风机
5.1.1 叶轮的轮盘与轮盖允许拼接块数不得超过表1的规定。除平轮盘外,其余轮盖一般为径向拼接。拼接焊缝的位置与叶片焊缝的位置交叉。
表1 轮盘与轮盖允许拼接的块数叶轮直径平轮盖锥面轮盖单圆弧轮盖双圆弧轮盖双锥面轮盖轮盘 280-400
————≤2 — >400-1000
≤2 ≤2 ≤2 ≤2 ≤2 >1000-1600
≤2 ≤3 ≤3 ≤3 ≤4 ≤3 >1600-2800
≤3 ≤4 ≤4 ≤4 ≤6 ≤3 >2800-3150
≤4 ≤5 ≤6 ≤6 ≤8 ≤3 >3150
≤5 ≤6 ≤8 ≤8 ≤10 ≤4
注:
1、叶轮直径系指叶片出口直径。
2、“—”表示不允许拼接。
图1 轮盘的焊接位置
图2 轮盖拼接及焊接位置
5.1.2 机号大于或等于№4 的a、b 型进风口允许在环面和锥面的切点附近接一道环形接缝;c 型进风口允许在切点附近接一道椭圆形接缝;e 型进风口的筒板允许有轴向接缝;各型进风口的接缝位置见图3,等分拼接块数按表
2 的规定
图
3 各型进风口的接缝位置
图3 各型进风口的接缝位置(续
表2 进风口等分拼接块数类型
a b c d e f 环面锥面环面锥面槽形圈上环面下环面锥面槽形圈整体圆筒法兰锥面法兰
部位
机号No
块数≤4
——————— >4-8
≤2 ≤2 ≤2 ≤2 ≤2≤2 ≤2>8-12.5
≤3 >12.5-16
≤3 ≤4 ≤3 ≤4 ≤2———≤2≤3≤4 ≤2 ≤3≤2>16-18
>18-20
≤4 ≤5 ≤4 ≤5 ≤3≤4≤4≤5≤3≤5 ≤3 ≤4≤3>20-22.4
>22.4-25
≤5 ≤6 ≤5 ≤6 ≤5≤5≤6≤4≤6 ≤5>25-28
≤6 ≤7 ≤6 ≤7 ≤4≤6≤6≤7≤4≤5≤7 ≤4 ≤6≤4>28 ≤7 ≤8 ≤7 ≤8 ≤5≤7≤7≤8≤5≤6≤8 ≤5 ≤8≤5
5.1.3 调节门
调节门的筒板和法兰圈允许拼接块数按表 3 的规定,且法兰圈接缝应躲开圆周的等分孔,矩形调节门窄端法兰不允许拼接,长端允许≤2 块拼接,接缝须避开孔径并焊后修磨平。
表 3 调节门的筒板和法兰圈允许拼接块数
机号 No 筒板块数法兰圈块数
筒板≤8
≤2 >8-12.5 ≤3
≥ 1/3周长
>12.5-16 ≤2 >16-18 >18-20 ≤4
≤3
≥ 1/4周长
>20-22.4 >22.4-25 ≤5
≥ 1/5周长
>25-28 ≤4
>28
≤6
≤5
≥ 1/6周长 5.1.4 机壳
5.1.4.1 机壳侧板的接缝一 5.2.4般应与出风口边平行或垂直,最小拼接块数的宽度不得窄于( 0mm。
5.2.14 机号小于或等于№16 时,蜗壳板的接缝位置按图 4;机号大于№16 时,接缝位置可从图 4、图 5中任选,当选用图 5 时,其允许拼接块数不得超过 2n–1。
注 n 为表 4 中蜗壳板的块数(不包括带有扩压段的扩压部分。
5.2.15 机壳的侧板、蜗壳板、法兰侧以及出口角钢的拼接块数按表 4执行。
图 4 蜗壳板的拼接形式
图 5 蜗壳板的拼接形式(续表 4 机壳主要件的拼接块数机号 No 侧板蜗壳板法兰圈
角钢圈
2.8-4 —
>4-6.3 ≤ 2
>6.3-9 ≤ 3
≤ 3≤ 2
>9-12.5 ≤ 4 >12.5-16 ≤ 5 ≤ 4≤ 3
≤ 2
>16-20 ≤ 6≤ 5≤ 4
>20-25 ≤ 7≤ 6≤ 5
≤ 3
>25-28 ≤ 8≤ 7≤ 6
>28 ≤ 9≤ 8≤ 7
≤ 4
注
1 侧板块数包括图样中给定块数
2 角钢圈和法兰圈为等分拼接
5. 2 轴流通风机
5.2.1 高度大于100mm的圆筒与环面相切而成的集流器,允许于切点处有环焊缝(见图6;周向允许等分拼接块数按表5 的规定。
图 6 集流器的拼接
5.2.2 高度大于 100mm 的圆筒与椭球面(图 7或球面(图 8相切而成的整流体,允许于切点处有环焊缝;整流体球面拼接允许在球冠处拼一道环焊缝,球冠的拼接直径为 100~300mm。周向允许等分拼接块数按表
5 的规定。
图7 整流体的拼接图 8 整流体的拼接(续
表5 集流器和整流体等分拼接块数
集流器
整流体
类别
环面
筒面
球面
筒面
机号块数
> 9-12.5 ≤6 ≤2 ≤6 ≤2 >12.5-16 ≤8 ≤8 > 16-20 ≤10 ≤4
≤10 ≤4
> 20-25 > 25-28 ≤12
≤12
> 28
≤14 ≤6
≤14
≤6 5.2.3 轮毂
5.2.3.1 直径大于1000mm的毂盘,允许两块或三块拼接,具体拼接位置按图9 或图10。
5.2.3.2 圆筒毂壳(图9和球面毂壳(图10的周长,允许拼接块数按表6,且接缝躲开圆周上的等分孔。球面拼接(>600-1000mm应≤3 为宜。
图 9 圆筒毂壳的拼接图 10 球面轮毂的拼接
表 6 毂壳周长允许拼接块数
毂壳外径球面毂壳圆筒毂壳接块最短长度
> 600~1000≤ 3
>1000≤ 4
≤ 2≥ 1/4周长
5.3 拼接件的焊接质量应符合JB/T 10213 的规定。
6 样板的制造公差与有关号料的要求
6.1 样板的制造公差
6.1.1 号料样板制造的极限偏差应不超过表7中A级偏差数值的1/2。表7 线性尺寸的极限偏差
单位为毫米(mm 尺寸范围
级
别 2~30
>30 -120 >120
-400
>400
-1000
>1000
-2000
>2000
-4000
>4000
-8000
>8000
-12000
>12000
-16000
>16000
-20000
>20000
A ±1 ±1 ±1 ±2 ±3 ±4 ±5 ±6 ±7 ±8 ±9
B ±1 ±2 ±2 ±3 ±4 ±6 ±8 ±10 ±12 ±14 ±16
C ±1 ±3 ±4 ±6 ±8 ±11 ±14 ±18 ±21 ±24 ±27
D ±1 ±4 ±7 ±9 ±12 ±16 ±21 ±27 ±32 ±36 ±40 6.1.2 号料样板的垂线或垂直边的垂直度公差应不超过表8 中
E 级公差数值的1/2。
表8 铆焊件的形位公差
单位为毫米(mm 尺寸范围
级
别
>30 -120 >120
-400
>400
-1000
>1000
-2000
>2000
-4000
>4000
-8000
>8000
-12000
>12000
-16000
>16000
-20000
>20000
E 0.5 1.0 1.5 2.0 3.0 4.0 5.0 6.0 7.0 8.0
F 1 1.5 3.0 4.5 6.0 8.0 10.0 12.0 14.0 16.0
G 1.5 3.0 5.5 9.0 11.0 16.0 20.0 22.0 25.0 25.0
H 2 5.0 9.0 14.0 18.0 26.0 32.0 36.0 40.0 40.0 6.1.3 确定各连接孔中心的号料样板其位置度公差不得大于φ0.5mm。
6.2 检查用量形样板
6.2.1 检查用量形样板制造的极限偏差不得超过表7中A级偏差数值的1/4。
6.2.2 检查用量形样板中垂线或垂直边的垂直度公差不得超过表8中E级公差数值的1/3。
6.3 号料线的公差
6.3.1 号料线的极限偏差不得超过表7 中A级偏差数值的2/3。
6.3.2 检查用量形样板中垂线或垂直边的垂直度公差不得超过表8中E级公差数值的1/3。
6.3.3 号料时连接孔中心的“样冲眼”其位置度公差不得大于φ0.6mm。
6.4 铆焊件材料的纤维方向
6.4.1 折弯件的折弯线应垂直于板材的纤维或与纤维的倾角α在35°~145°之间(见图11。
图 11 折弯件材料的纤维方向
6.4.2 延伸件(如圆弧形进风口、轮盖等的展开料为圆形或大于半圆的扇形,不必考虑材料的纤维方向;对小于半圆的扇形,其扇形弦线与板材纤维的交角α应在下式范围内(见图12:
90°–β≤α≤90°+β
式中:
β
—弦线与边线的夹角。
图 12 延伸件材料的纤维方向
7 铆焊件的落料公差
7.1 非配合件剪切的极限偏差
7.1.1 剪切件的极限偏差不得超过表7中A级偏差的数值。
7.1.2 剪切件直角边的垂直度公差不得超过表8中F级公差的数值。
7.2 非配合件的气割公差
7.2.1 气割件尺寸的极限偏差不得超过表7中B级偏差的数值。
7.2.2 气割件直角边的垂直度公差按表8中F级公差数值的1.2 倍。
7.2.3 凡不进行“机械加工”的气割件,外缘应圆滑过渡,在≤500mm 范围内,缺陷所造成凸、凹处应不多于一处,500~1000mm 范围内凸、凹处应不多于两处。
7.3 未注公差间隙配合件的落料公差
7.3.1 间隙配合的轴类件,其落料的下偏差按表7中A级的下偏差,上偏差为零。
7.3.2 间隙配合的孔类件,其落料的上偏差按表7中B级的上偏差,下偏差为零。
7.3.3 机壳中蜗板宽度的落料上偏差取表7中A级的上偏差之半;下偏差取表7中A级下偏差的数值。 7.3.4 通风机叶片尺寸的极限偏差不得超过表7中A级偏差的数值。
7.3.5 圆筒的周长落料公差应等于圆筒的配合公差与圆周率π的乘积值的0.8倍。
7.3.6 配合件直角边的垂直度公差按表8中E级的规定。
8 铆焊件的制造公差
8.1 未注公差的铆焊件的制造公差
8.1.1 不经弯曲成型的非配合件,其制造极限偏差同7.1与7.2的规定。
8.1.2 经弯曲成型的非配合件,成型后的极限偏差按表7的B 级。
8.1.3 不经弯曲成型的配合件,其制造极限偏差同7.3.1与7.3.2的规定。
8.1.4 与圆筒外径配合的孔类件,其孔径的上偏差按表7中B级的上偏差,下偏差为零;圆筒外径的下偏差按表7中A级的下偏差,上偏差为零。
8.1.5 与圆筒内径配合的轴类件,其外径的下偏差按表7中A级的下偏差,上偏差为零;圆筒内径的上偏差按表7中B级的上偏差,下偏差为零。
8.1.6 离心通风机进风口喉径的极限偏差不得超过尺寸的±0.6%。
8.1.7 组合件非配合尺寸的极限偏差按表7中的C级。
8.1.8 组合件非配合边缘的垂直度公差按表8中的G级。
8.1.9 组合件配合边缘的垂直度公差按表8中的E级。
8.1.10 组合件法兰面的平面度公差按表8中的F级。
8.1.11 离心通风机机壳前后通孔的同心度公差不超过表8中的E级。
8.2 离心通风机铆焊件的形位公差
8.2.1 叶片型线的线轮廓度公差按表8 中的F 级,基本尺寸为叶片弧长。
8.2.2 弧形轮盖的线轮廓度公差按表8 中的F 级,基本尺寸为叶轮直径。
8.2.3 进风口弧面部分的型线的线轮廓度公差按表8 中的F 级,基本尺寸为进风口喉径。
8.2.4 单件侧板的平面度公差按表8 中的F 级;组装成机壳后侧板的平面度公差按表8 中的G级。 8.2.5 叶片进出口安装角的极限偏差为±1°。
8.2.6 叶片出口边对轮盘的垂直度公差应小于或等于叶片出口宽度的1/100。
8.2.7 任意三个相邻叶片于出口端的两个节距(弦长之差 K 值不得超过表9 的规定。
表 9 叶片节距差值 K
单位为毫米(mm 机号№ ≤ 10>10~20>20~25> 25
K 0.45№ 0.43№ 0.42№ 0.41№
注:№为对应的机号数。
8.2.8 拼接前的叶轮轮盘的平面度公差按表8中的E级;组装成叶轮后轮盘的平面度公差按表8中的 G 级。
8.2.9 叶轮轮盖内径的圆跳动公差应小于或等于叶轮与进风口最小单侧间隙值的一半, 叶轮端面的圆跳动公差按表10 的规定。
表 10 叶轮端面圆跳动公差
单位为毫米(mm 叶轮直径
项目
200-400 > 400-1000 >1000-1600 >1600~2500 >2500~3150 >3150~5000轮盘端面圆跳动 2.0 3.0 4.0 5.0 5.5 6.5 轮盖端面圆跳动 2.5 3.5 5.0 5.5 6.5 7.5 8.3 轴流通风机铆焊件的形位公差
8.3.1 叶片型线的线轮廓度公差不应超过所测叶片截面弦长的1/150,对于碳钢叶片表面划痕深度不得大于0.5mm, 铝材叶片划痕深度不得大于0.3mm, 不锈钢及其他有色金属材料的叶片划痕深度不得大于0.1mm。
8.3.2 叶片扭曲角的偏差不得超过±1°。
8.3.3 任意三个相邻叶片于外圆处两个相应端点节距(弦长之差 K' 值不应超过表11 的规定。
表 11 叶片节距差值K'
单位为毫米(mm 叶轮直径
叶片数
≤ 630 >630-800 >
800-1250
>
1250-2000
>
2000-3150
>
3150-5000
>
5000-8000
>8000
>103.0 4.0 6.0 8.0 10.0 12.0 20.0 30.0 ≤ 104.8 6.4 9.6 13.0 16.0 22.0 30.0 40.0 8.3.4 导叶、集流器、整流体的弧面型线与量形样板的间隙不得大于所测弧长的1/100。
8.3.5 叶轮的跳动公差不得超过表12 的规定
表 12 轴流通风机叶轮的跳动公差
单位为毫米(mm 叶轮直径
项目
≤ 630 >630~800 >800~1250 >1250~2000 >2000~3150 >3150~5000 轮毂径向与端面圆跳动 1.0 1.5 2.0 3.0 4.0 5.0 叶轮外径径向圆跳动 1.0 1.5 2.0 3.0 3.5 4.0 叶轮外径端面圆跳动 2.0 3.0 4.0 5.0 6.0 10.0 8.3.6 导叶于风筒中的安装角偏差不得大于±1°。
8.3.7 机壳尺寸的极限偏差和形位公差不应超过表13 的规定
表 13 轴流通风机叶轮的跳动公差
单位为毫米(mm 叶轮直径
项目≤ 630 ≤ 630
-800
>800
-1250
>1250
-2000
> 2000
-3150
>3150
-5000
铆焊件加工技术操作规程
铆焊件加工技术操作规程(B标准) 1、主题人容和应用范围 本标准规定了铆焊件加工的操作规程 本标准适用于本厂铆焊件的加工 2、引用标准 YB/JQ 101.10 钢铁企业机修制造通用技术条件焊接结构件 GB152 钉孔直径 3、加工前准备 加工前应熟悉图纸和工艺要求,并准备好所用的设备、工具、样板及量具等。 4、工件加工 4.1剪切 4.1.1剪切前应核对剪切件的材质,并检查其是否符合剪切机的前切要求。 4.1.2清理现场,检查设备的工作情况,并开车试转,确信良好后方可工作。 4.1.3根据来料选择剪切顺序,调整好合适的剪刃间隙。 4.1.4剪切时要分清各种号料线,并按剪切线的冲印剪切,上剪刃口与剪切线对正。相对剪切线的允许剪切偏差见表1。 4.1.5多人共同操作,必须密切配合,听从一人指挥。 4.2孔的加工 4.2.1孔的加工方法根据工艺要求或加工条件选择,并分清所加工孔在下道工序的用途。 4.2.2钻床加工孔按钻孔的操作规程。电钻钻孔时,操作人员应互相配合,手应端平,工作需夹紧,钻头垂直于工作表面。 4.2.3铆钉孔的加工按铆接要求确定孔与钉直径关系。 4.2.3.1热铆时钉孔直径应比钉杆直径略大。钉孔的直径标准见表2。
4.2.3.2冷铆的钉孔与钉杆直径接近。钻头直径应比铆钉直径大0.5—1mm。 4.2.3.3多层板紧固铆接,钻孔直径按标准孔减小1—2 mm,以备弯曲成形后绞孔修正。 4.2.4筒形件在弯曲前钻孔,孔径比标准孔小1—2mm,以备弯曲成形后绞孔修正。 4.2.5绞孔时必须选好绞削用量和冷却液,且工件要夹正,夹紧力适当,手绞时两手两力要均匀,防止缺陷。 4.2.6攻丝时工件装夹要正确,为提高精度可经常加润滑液。 4.2.7对于装配孔的加工按工艺要求。 4.2.7对于装配孔的加工按工艺要求。 4.3焊接坡口加工 4.3.1根据工艺文件详细了解坡口的形式,加工要求。 4.3.2坡口的加工方法按工艺要求,或根据坡口精度要求,加工条件选定。 4.3.2.1风铲加工,风铲头切削角度以50o左右为宜,铲头要适当润滑。 4.3.2.2刨边机加工,须先检查设备运行情况,并给规定部位加润滑油。凡创边工作需预留2—4mm的余量。4.3.2.3气割坡口执行有关气割的操作规程。 4.3.2.4碳弧气刨加工坡口应尽可能顺风向,刨削结束应先断弧,过几秒钟后关闭气阀。 4.4矫正 4.4.1矫正前准备 4.4.1.1检查要矫正的工件,对照图纸详细了解工件变形的程度、变形类型,并分析变形的原因,同时考虑好矫正的方法。 4.4.1.2清除工件上的毛剌、氧化皮、飞溅等,并检查是否有裂纹。 4.4.1.3手工矫正应准备好平台,必要的工具、量具及简单机具。用锤必须检查锤把与锤头是否牢固。 4.4.1.4利用机器矫正,应先调试好机器使之正常工作。 4.4.1.5采用火焰矫正,应准备好加热源。 4.4.2矫正操作 4.4.2.1薄板和小规格的型钢结构可用手工矫正法,厚板和大规格的型钢要结合机械矫正法和火焰矫正法。4.4.2.2矫正要根据材料的规格、变形类型、变形程度确定,具有复杂变形的工件,要注意矫正顺序。一般先矫复杂变形,后矫简单变形。 4.4.2.3手工矫正工件时,锤痕深度不得超过0.5mm。对重要件大锤不能直接击在钢板上,应在工件上垫平锤后锤击。4.4.2.4几个人同时用大锤矫正一块板料,必须听从主锤的指挥,不许抢锤、弃锤。 4.4.2.5滚析机矫正析材,先要视变形情况调整轴辊间隙,且板材必须与辊子同步移动,不允许打滑。 4.4.2.6压力机矫正工件要考虑回弹情况,矫正时要反复试验,视矫正效果调整施加压力的大小。 4.4.2.7型钢应尽量用丝杆顶压的方法矫正。 4.4.2.8火焰矫正要注意材质,防止淬裂。一般加热温度为700—800oC,在200—500 oC蓝脆区禁止打击。4.4.2.9火焰矫正要选择正确的加热位置和加热方式。 a、若第一次加热矫正未能成功,可进行第二加热,但加热位置应与前次错开,加热点不复重复。 b、点状加热时点的大小根据板厚确,点与点之间的距离一般为50—100mm。 c、线状加热的宽度一般为钢板厚度的0.5—2倍左右。此法常用于变形圈大的结构。 d、三角加热用于刚性较大的构件弯曲变形矫正。 4.4.2.10水火矫正,用于8mm以下的钢板矫正,水与火的距离随钢材厚度的增大而增加,一般不超过30 mm。对40 m m厚以上的工件火焰矫正不能用水冷却。 4.4.2.11矫正时必须随时检查矫正效果。 4.4.3工件矫正后经检查达到要求的工件,应妥善放置,不准随意扔掷。
变速箱通用技术条件
费城搅拌器变速箱通用技术条件 JT 第105册共19页 河南中光学集团有限公司 2003年5月
费城搅拌器变速箱通用技术条件 1范围 1.1主题内容 本技术条件规定了费城搅拌器变速箱(以下简称变速箱)的技术要求、试验方法、检验规则及标志、包装、运输、贮存。 1.2适用范围 本技术条件适用于变速箱系列产品及其零、部件。 2引用标准 GB/T1031-1995 《表面粗糙度参数及其数值》 GB/T131-1993 《机械制图表面粗糙度符号、代号及其注法》 GB/T1182-1996 《形状和位置公差通则、定义、符号和图样表示法》 GB/T1184-1996 《形状和位置公差未注公差值》 GB10095-1988 《渐开线圆柱齿轮精度制与侧隙》 JB/T5000.12-1988 《重型机械通用技术条件涂装》 GB/T13384-1992 《机电产品包装通用技术要求》 GB191-1990 《包装储运图示标志》 GB/T2828-1987《逐批检查计数抽样程序及抽样表》 3 技术要求 3.1总则 变速箱及其零部件应按经规定程序审批的产品图样及技术文件制造与验收,并符合本技术条件的规定。 3.2图纸转化中的一般要求 3.2.1对于图纸中的表面粗糙度,应在不降低原设计要求的基础上符合下述标准要求: GB/T1031-1995 《表面粗糙度参数及其数值》 GB/T131-1993 《机械制图表面粗糙度符号、代号及其注法》 3.2.2图纸中尺寸、尺寸公差及形位公差的转化要求: a)尺寸及各项公差的转化,原则上保持原有精度,只将其数值大小由英制转化为公制即可。 b)形位公差的转化,应符合GB/T1182-1996《形状和位置公差通则、定义、符号和图样 表示法》及GB/T1184-1996《形状和位置公差未注公差值》的要求。 3.2.3齿轮精度在对等原则下,转化为符合GB10095-1988《渐开线圆柱齿轮精度制与侧隙》
焊接件通用技术条件
1.主题内容与适用范围 本标准规定了本公司产品焊接件的技术要求,试验方法和检验规则。 本标准适用于本公司生产的造纸机械、矿山机械、环保设备及其它产品焊接件的制造和检验。若本标准规定与图纸要求相矛盾时,应以图纸要求为准。 本标准适用于碳素结构钢、低合金结构钢和不锈钢材料,采用手工电弧焊、CO2气体保护焊及氩弧焊方法制造的焊接件。 2.技术要求 材料 用于制造焊接结构件的原材料(板材、型材等)的牌号、规格、尺寸应符合图样或技术文件的要求,若不符时,应按公司内材料代用制度办理材料代用。 用于焊接件的材料(钢板、型钢、铸钢、焊条、焊丝等)购进时,应有质量证明书,并按材料标准规定检验合格后,方准入库使用。 对无牌号、无质证书的原材料和焊材,必须进行检验和鉴定。其成份和性能符合要求时方准使用。 钢板的初步矫正 各种钢材在划线前,不能有较大的变形,其形状公差不得超出下列规定: a.钢板的平面度不应超过表1规定 b.型材的直线度和垂直度公差不超过表2的规定
c.歪扭不超过表2的规定,当超过规定,本公司无法矫正时,经检验部门同意,可用于 次要结构。 钢材的矫正。可用机械矫正和火焰矫正,或在平台上锤击。矫正后的钢材,不得有明显的伤痕,其伤痕深度,钢板一般≤0.5mm,型钢≤1mm。 不锈钢材料不准用铁锤直接锤击(可垫一铜块锤击或用木锤锤击) 号料划线前的准备 划线或样板的制作,需考虑结构在焊接时所产生的收缩量,收缩量的大小,按工艺要求规定。如工艺文件没有规定时,一般箱型或工字型结构或类似箱型划工字型结构,纵向焊缝收缩量⊿L按下式计算 ⊿L=1/1000L=0.5n (L:焊件纵向焊缝总长mm;n:筋、隔板数量) 横向焊缝的收缩量⊿B按下式计算 ⊿B=1/1000B (B:焊件横向焊缝总长mm) 焊接结构件的装配间隙,在制作样板时应予以考虑。其间隙在图纸和工艺文件没有要求时,一般为1-2mm。 样板的外围尺寸偏差,应在-0.5~-1.0范围内。 样板需经检验员验收合格后方可使用。 号料 对单件小批生产的产品,可直接在钢材上按图进行划线,但必须根据工艺规定留出焊接收缩量。工艺无规定时,按2.3.1条规定生产。 划线时,应留出机械加工余量,余量多少由工艺文件规定。 下料 钢材可采用机械剪切、气割。等离子切割。零件切割后的尺寸偏差应符合下列规定:机械切割的板材(剪板)零件尺寸的极限偏差按表3规定:等离子切割的板材,型材零件尺寸的极限偏差按表4规定
焊接件通常技术要求
焊接件通用技术要求 一、主题内容与适用范围 本标准规定了本公司产品焊接件的技术要求,试验方法和检验规则。本标准适用于本公司生产的各机型农机及其它焊接件的制造和检验。若本标准规定与图纸要求相矛盾时,应以图纸要求为准。本标准适用于手工电弧焊、CO2气体保护焊等焊接方法制造的焊接件。 二、技术要求 1、材料 用于制造组焊件的原材料(钢板、型钢和钢管等)、焊接材料(焊条、焊丝、焊剂、保护气体等) 进厂时,须经检验部门根据制造厂的合格证明书验收后,才准入库。对无牌号、无质证书的原材料和焊材,必须进行检验和鉴定。其成份和性能符合要求时方准使用。 1.1焊接材料: 1)焊条、焊丝应存放于干燥、通风良好的库房内,各类焊条必须分类、分牌号堆放,避免混乱。搬运过程轻拿轻放,不要损伤药皮。焊条码放不可过高 2)仓库内,保持室温在0°C以上,相对湿度小于60%。 3)各类存储时,必须离地面高300mm,离墙壁300mm以上存放,以免受潮。 4)一般焊条一次出库量不能超过两天的用量,已经出库的焊条,必须要保管 好。焊条使用前应按其说明书要求进行烘焙,重复烘焙不得超过两次。 1.2原材料 1.2.1各种钢材在划线前,不能有较大的变形,其形状公差不得超出下列规定:1)钢板的平面度不应超过表1规定 表1 钢板平面度公差值f
2)型材的直线度和垂直度公差不超过表2的规定 表2 3)歪扭不超过表2的规定,当超过规定,本公司无法矫正时,经检验部门同意,可用于次要结构。 1.2.2下料: 1.2.2.1尺寸偏差:钢材可采用机械剪切、气割、等离子切割、火焰切割、激光切割等下料方法,零件切割后的尺寸偏差应符合下列规定: 剪板机下料零件尺寸的极限偏差按表3规定:气割、等离子切割、火焰切割的零件尺寸的极限偏差按表4规定
摩托车涂装通用技术条件
摩托车涂装通用技术条件 1适用范围 本技术条件规定了公司各种摩托车部件零部件的涂装技术要求及试验方法,它适用所有本公司摩托车的涂漆零部件。 2引用标准 下列文件中的条款通过本标准的引用而成为本标准的条款。凡是注日期的引用文件,其随后所有的修改单(不包括勘误的内容)或修订版均不适用于本标准,然而,鼓励根据本标准达成协议的各方单位沟通是否可使用这些文件的最新版本。凡是不注日期的引用文件,其最新版本适用于本标准。 GB/T1720 漆膜附着力测定法 GB/T1727 漆膜一般制备法 GB/T1732 漆膜耐冲击测定法 GB/T1733 漆膜耐水性测定法 GB/T1734 漆膜耐汽油性测定法 GB/T1740 漆膜耐湿热测定法 GB/T1743 漆膜光泽测定法 GB/T1763 漆膜耐化学试剂性测定法 GB/T1764 漆膜厚度测定法 GB/T1765 测定耐湿热、耐盐雾、耐候性(人工加速)的漆膜制备法 GB/T1766 色漆和清漆涂层老化的评级方法 GB/T1769 漆膜磨光测定法 GB/T1865 色漆和清漆人工气候老化和人工辐射暴露(滤过的氙弧弧辐射) GB/T3181 漆膜颜色标准 GB/T3186 涂装产品的取样 GB/T6514 涂装作业安全规程涂装工艺通风净化 GB/T6739 漆膜硬度铅笔测定法 GB/T6807 钢铁工件涂装前磷化处理技术条件 GB8264 涂装技术术语 GB/T9276 涂层自然气候暴露试验方法 GB/T9969.1 工业产品使用说明书总则 GB/T11186.3 漆膜颜色的测量方法第三部分色差计算 GB/T12334 金属和其他非有机覆盖层关于厚度测量的定义和一般规则 JB/T7504 静电喷涂装备技术条件 JB/T6978 涂装前表面准备——酸洗 QC/T29117.3-93 摩托车和轻便摩托车产品质量检验评定:整车外观质量评定方法3定义 本标准采用下列定义,涂装技术其它术语引用GB 8264。 3.1 油漆涂层缺陷用语 3.1.1 起泡 涂层表面呈现鼓包现象。 3.1.2针孔 漆膜表面呈现针孔状小孔或毛孔的现象。 3.1.3起皱 漆膜表面呈现凹凸不平且无规则线状褶皱的现象。 3.1.4桔皮 漆膜表面呈现桔皮状纹路的现象。
金属件涂装通用技术条件讲解
金属零部件涂装通用技术条件 1范围 本标准规定了金属零部件上的涂装的种类和等级、要求、试验方法、检验规则、包装、运输及贮存。 本标准适用于在不同金属底材零件(以下简称“零件”)表面上进行的、主要以装饰及防 腐蚀为目的的一般装饰用涂装(以下简称“涂装”)。 本标准适用如下涂装: a)以酸洗磷化处理的金属; b)真空镀膜的涂装; c)以指向性反射或萤光性为目的的涂装; d)电绝缘性为目的涂装。 2规范性引用文件 下列文件中的条款通过本标准的引用而成为本标准的条款。凡是注日期的引用文件,其随后所有的修改单(不包括勘误的内容)或修订版均不适用于本标准,然而,鼓励根据本标准达成协议的各方研究是否可使用这些文件的最新版本。凡是不注日期的引用文件,其最新版本适用于本标准。 GB/T 1731-1993 GB/T 1732-1993 GB/T 1733-1993 GB/T 1734-1993 GB/T 1735-1979 GB/T 1743-1979 GB/T 1763-1979 GB/T 1764-1979 GB/T 1766-1995 GB/T 1771-1991 GB/T 1865-1989 GB/T 2828-1987 GB/T 6739-1996 GB/T 6807-2001 GB/T 9276-1996 GB/T 9286-1988 GB/T 9754-1988 GB/T 9761-1988 GB/T 13452.2-1992色漆和清漆漆膜厚度的测定漆膜柔韧性测定法漆膜耐冲击性测定法漆膜耐水性测定法漆膜耐汽油性测定法漆膜耐热性测定法漆膜光泽测定法漆膜耐化学试剂性测定法漆膜厚度测定法色漆和清漆涂层老化评级方法色漆和清漆耐中性盐雾性能的测定漆膜老化(人工加速)测定法逐批检查计数抽样程序及抽样表(适用于连续批次的检查)漆膜硬度铅笔测定法 钢铁工件涂装前磷化处理技术条件漆层自然气候曝露试验方法色漆和清漆色漆和清漆色漆和清漆 漆膜的划格试验 60度镜面光泽的测定 色漆的目视比色
铆焊件技术协议
铆焊件技术协议 1 总则 1.1 用于焊接、铆接件母材的牌号,应符合国家标准。 1.2 焊接、铆接件的制造应符合图样,工艺文件和本标准的规定。 1.3 焊接件所用焊条按母材强度条件选择。 1.3.1 常用焊条应按图样规定牌号,符合GB980—76《焊条分类及型号编制方法》的规定。1.3.2 焊接低碳钢、低合金钢的焊条应按图样规定牌号,符合GB981—76《低碳钢及低合金高强度钢焊条》的规定。 1.3.3 焊接钼和铬钼钢的焊条应按图样规定牌号,符合GB982—76《钼和铬钼耐热钢焊条》的规定。 1.3.4 焊接不锈钢的焊条应按图样规定牌号,符合GB983—76《不锈钢焊条》的规定。1.3.5 堆焊焊条应符合GB984—76《堆焊焊条》的规定。 1.3.6 焊接结构件的焊条,在图样中未对焊条规定时,可用T422焊条焊接。 1.4 焊接中所用的焊丝应符合GB1300—77《焊接用钢丝》的规定。 1.5 在下雨、雪及大雾的情况下,不得进行露天焊接。气体保护焊只能在室内进行。 1.6 焊接处应预先清除氧化皮、油、油漆等表面污物。 1.7 结构件选用新钢种时,应对材料进行必要的可焊性试验,证明符合质量要求后,方可投入生产。 1.8 焊接后,溶渣、溅粒等均应清除干净。 1.9 焊接尺寸应符合图样规定,焊接表面应呈现均匀平滑的鳞状波纹,并在焊缝的全长上保持一致。 1.10 图样中的焊缝代号必须符合GB324—80《焊缝代号》的规定。 1.11 接触食品焊接、铆接件所选用的焊条、铆钉,应符合“食品卫生法”的规定。 1.12 凡接触食品的焊接、铆接件,应平滑,无毛刺,不允许食品接触而残存,造成污染食品。1.13 焊接和铆接件由制造单位技术检验部门按图样及工艺进行检验。 1.14 各类焊接、铆接件应按不同的材料配备工艺设备和选用加工方法。
涂装通用技术条件
机械制造作业指导书 HZ\WI7.5-20-2002 涂装过程控制规定 文件提出部门: 编写: 审核: 批准: 2002年9 月 2 日发布 2002年9 月 2 日实施
⒈主题内容与适用范围 本指导书规定了机械产品涂装的通用技术要求与检验规则。 本指导书适用于机械产品的防护和装饰性涂装。 ⒉术语 ⒉1底漆 直接涂于物体表面打底,是基层用漆。其防锈能力强,附着力强,对金属起防锈作用。 ⒉2腻子 用于预先涂有底漆的表面,填平凹坑、缝隙、碰伤及划伤等缺陷;腻子应具备良好的结合力和打磨性能,经打磨后呈平整光滑的表面。 ⒉3面漆 用于底漆和腻子之后,保护底漆和腻子,对金属起防蚀作用。面漆应具有良好的耐候性、化学稳定性及物理机械性能。涂膜光亮,色彩绚丽,使产品外形光滑、整洁、美观。 ⒉4稀释剂 用于稀释涂料,是涂料的辅助材料之一。 ⒊涂料要求 ⒊1涂装所用的底漆、腻子、二道底漆、面漆、稀释剂,应具有良好的配套性。必须配套使用,具体品种按表1规定选用,图样或技术文件有特殊要求时按其要求选用。 ⒊2涂料的质量必须符合化工部标准或有关标准的规定。 表1 ⒋涂层部位与涂层颜色 ⒋1产品机身外部表面的涂料颜色一般按图纸要求执行,也允许按用户要求
确定。 ⒋2机身上可以根据具体情况采用不同的装饰性线条或颜色。 ⒋3齿轮箱体和箱盖、轴承盖、油箱的未加工内壁,以及经常浸在油中的零件未加工表面,应涂耐油涂料。 ⒋4装配后不易或不能涂装的部件或表面应在装配前涂装。 ⒋5需要引起注意部位的涂装,应涂鲜艳色彩的涂料。裸露的转动零件如飞轮、皮带轮、齿轮等轮辐及转动罩壳,应涂红色涂料。 ⒋6产品上各种特殊标志,如厂名、商标、指示符号、警戒标志等,应涂与该标志所在部位的颜色有明显区别、协调而醒目的颜色。 ⒋7已涂装的外购件和外协件,如涂膜未被破坏且装配后不影响整机美观时,可不再涂装。否则必须用与原色相同的涂料补涂。 ⒌涂装施工 涂装施工时,必须严格遵守各种涂料对温度、湿度、重涂间隔时间、调配方法、注意事项等各种规定。 ⒌1施工条件的要求 ⒌⒈1涂装施工应在清洁、干燥、空气流通、光线充足的地方进行,环境温度应保持在10~35℃。相对温度不大于75%。 ⒌⒈2涂装用具必须清洁。喷涂用的压缩空气应保持清洁干燥。 ⒌2涂面清洁的要求 ⒌⒉1经喷丸(砂)处理的零件表面,应呈金属本色,不得有残存氧化皮、型砂、锈迹等。经预处理喷底漆的型材组焊后,焊缝处必须手工除锈补漆。⒌⒉2经酸洗、磷化处理的零件,其表面应无氧化皮、锈迹、油污、酸碱液等。磷化膜应结晶致密、连续、均匀,不允许有绿斑、严重挂灰、结晶疏松等缺陷。 ⒌⒉3经手工打磨的零件表面,不应残存浮锈、氧化皮、型砂、焊渣、油污等。 ⒌3涂装的要求 ⒌⒊1涂底漆 ⒌⒊⒈1涂面清理完后,应在4小时内涂一道底漆。 ⒌⒊⒈2除下列情况不涂底漆之外,其他金属零件均应涂底漆。 a.零件加工表面; b.标准件;
铆焊工序验收标准
铆焊件几何尺寸及外观质量验收标准 1、一般规定:本规定适用于我公司所有铆焊接构件的验收,若图纸或者相应技术文件有要求的按图纸或者技术文件的规定执行 2、加工余量 (Ⅰ)卷制的筒形件加工余量应不大于下表(mm) (Ⅱ)手动气割类板材边沿或圆盘类件加工余量(mm) 数控及仿型气割板材直径余量2-4 mm,高度余量3-5 mm。
(Ⅲ)结构件平面加工余量应不大于下表(mm) 3、尺寸偏差 (1)成型前应在平板机或压力机上对钢材进行初步矫正,矫正后钢材表面不得有裂纹及明显痕迹。 (2)对于焊后加工的零件,应本着宁大勿小的原则保留加工余量,并在此基础上尽可能接近标准要求,节约材料。 (3)成型焊接前应考虑到工件在焊接过程中的变形,预先进行反变形处理措施。当工件有焊接变形时,应进行整形处理。完成后其几何偏差为(图纸未明确要求的)(mm)。 4下料外观质量要求下料后必须铲除边棱上的堆积物,毛刺及凸起部分气割口端面应光滑干净,表面毛刺、熔渣均应铲除。 5、焊接及焊缝外观质量要求
(1)焊接前应将坡口表面及内外侧20mm范围内的油锈、污物及水、汽清除干净。 (2)焊接时的临时焊点,应是正式焊缝的一部分,故其高度和宽度应该是小于正式焊缝的尺寸,点焊缝有裂纹时应铲除重焊。重要的焊接件应在可能的条件下,在背面点焊。 (3)多层焊接时,在焊接每层焊缝以前,应对前一层焊缝进行检查,清除夹渣、气孔及裂纹。 (4)不同厚度的焊接件组装时,当薄件厚度小于10mm,厚度差大于薄件厚度的30﹪或超过5mm时,应进行对接坡口处理,以增加焊接强度。 (5)焊缝不允许有烧穿及裂纹现象,焊缝总体上应宽度均匀,鲜状波纹高低一致,不允许焊缝间断及未焊现象存在。 (6)焊缝宽度不均匀程度应该控制在1mm-2mm,焊缝高度<6 mm时,偏差不超过-0.5-1.0 mm,当焊缝高度≤14 mm时,偏差不超过-1.0—1.5 mm,当焊缝高度>14 mm时,偏差不超过-1--2 mm。 (7)焊接完成应将焊缝上的渣皮及飞溅物清除干净,保证工件的外观整洁美观。 (8)对于要求进行无损探伤的焊缝,其不合格部位必须进行返修处理,然后再按原方法进行检查。 6、构件的防锈防护所有构件转出车间之前必须涂防锈底漆,涂漆应均匀无流痕。
焊接件通用技术条件(2019)
焊接件通用技术条件 1 范围 本标准适用于公司所有产品中采用手工电弧焊、钨极氩弧焊、富氩气体保护焊及自动焊焊接的零部件。 本标准适用于产品图样或技术文件中无特殊要求的焊接件。 2 引用标准 下列文件中的条款通过本标准的引用而成为本标准的条款。凡是注日期的引用文件,其随后所有的修改单(不包括勘误的内容)或修订版均不适用于本标准,然而,鼓励根据本标准达成协议的各方研究是否可使用这些文件的最新版本。凡是不注日期的引用文件,其最新版本适用于本标准。 GB/T 985 气焊、手工电弧焊及气体保护焊焊缝坡口的基本形式和尺寸 GB/T 986 埋弧焊焊缝坡口的基本形式和尺寸 GB/T 2649 焊接接头机械性能试验取样方法 GB/T 2650 焊接接头冲击试验方法 GB/T 2651 焊接接头拉伸试验方法 GB/T 2652 焊缝及熔敷金属拉伸试验方法 GB/T 2653 焊接接头弯曲及压扁实验方法 GB/T 3323 钢熔化焊对接接头射线照相和质量分等 GB/T 5117 碳钢焊条 GB/T 5118 低合金钢焊条 GB/T 8110 气体保护焊丝用碳钢、低合金钢焊丝 JG/T 5082.1 建筑机械与设备焊接件通用技术条件 3 一般要求 3.1焊接结构件的制造应符合设计、工艺文件和本标准的规定。 3.2焊接生产过程对环境温度的规定: 3.2.1零件和成品矫正时,不应低于下列温度: 3.2.1.1低碳钢材质:-20℃; 3.2.1.2低合金结构钢材质:-15℃。 3.2.2一般焊接件允许施焊温度应符合表1的规定。 3.2.3焊接件在低温条件下(如表1所列)焊接时,钢材表面应进行预热,必须保证预热 区宽度大于被焊板材厚度的4倍,且每侧预热宽度不得小于100mm,必须保证加热到100~ 200℃后才能施焊。如果用火焰预热时,焰芯距板面距离应大于50mm。 3.2.4在常温条件下,对刚性大、可焊性差的焊接件,也应焊前预热(预热温度在100~ 200℃范围内),焊后需进行保温或回火消除焊接应力。
焊接件制作规范
焊接件制作质量标准 1、范围 本标准适用于抛丸清理产品所有焊接件外观的质量要求。 2、规范性引用文件 下列文件中的条款通过本标准的引用而成为本标准的条款。 JB/T7949-1999 钢结构焊缝外形尺寸 JB/T5943-1991 工程机械焊接件通用技术条件 GB/T5117-1995 碳钢焊条 HB/Z5134-1979 结构钢和不锈钢熔焊工艺 3、质量标准 3.1焊件的质量要求 3.1.1所用组焊料必须符合图纸规定的规格、型号。下料尺寸必须符合图纸要求。若发现下料尺寸与组焊件尺寸不符时,应及时通知车间负责人或检验部门,由车间负责人或检验部门及时与设计部门进行联系处理。 3.1.2组焊成型 组焊前组焊料必须按图纸要求进行整形,各面必须达到平整,并去除组焊料的飞边、毛刺,表面氧化皮及加工后的毛刺,气割件要加工或打磨掉锯齿纹,保证表面光滑,棱角及直角要打磨,保证达到圆滑过渡。需打坡口焊接的组件,必须按图纸要求尺寸打坡口。组焊时,应根据组焊件所用材料选择合适的焊条焊料,根据组焊件的壁厚及材料及时调整焊机,选择合适的的焊接电流强度。 3.1.2焊缝的表观要求 3.1.3..1焊接件焊缝外观应均匀、平滑、波纹度小于0.5mm。焊道与焊道、焊道
与基本金属之间应平滑过渡,不得有气孔、裂纹、弧坑和夹渣等缺陷。 3.1.3.2角焊缝焊角高度应达到图纸要求,且两侧要均匀、美观,无内部缺陷,无缺焊、漏焊、缺焊肉等缺陷。 3.1.3.3焊接完工必须全部清除焊渣与内外飞溅物,并对焊道进行修磨。外观焊道原则上达到不扎手、不粘连棉纱为准。 3.1.4焊缝的外形尺寸控制 3.1. 4.1焊缝最大宽度Cmax与最小宽度Cmin的差值,在任意50mm焊缝长度范围内不得大于1mm,整个焊缝长度范围内不得大于2mm。 3.1. 4.2焊缝边缘直线度f:在任意300mm连续焊缝内,焊缝边缘沿焊缝轴向的直线度f如图1所示其值控制在<1mm内。 3.1. 4.3焊缝余高h应控制在0~1mm范围内。焊缝表面凹凸,在焊缝任意25mm长度范围内,焊缝余高hmax、hmin的差值(及波度)不得大于0.8mm,见图2. 3.1. 4.4角焊的焊角尺寸k值应严格按图样执行,其k值的偏差应符合表1的规定。 3.1. 4.5焊缝咬边尺寸△δ的值小于0.05δ但不得大于0.5mm,累计长度不得超
各种防腐涂料的国家相关标准
各种防腐涂料的国家相关标准混凝土防腐涂料 1.海港工程混凝土结构防腐蚀技术规 范 JTJ275-2000 2.混凝土桥梁结构表面涂层防腐技术条件JT/T695-2007 3.火力发电厂烟囱(烟道)内衬防腐材料DL/T901-2004 4.烟囱混凝土耐酸耐腐蚀涂料DL/T693-1999 5.水电水利工程金属结构设备防腐蚀技术规 范 DL/L5358-2006 钢结构防腐 1.建筑用钢结构防腐涂料JG/T224-2007 2.交通钢构件聚苯胺防腐涂料JT/T657-2006 3.钢结构桥梁漆HG/T3656-1999 4.铁路钢桥保护涂装TB/T1527-2004 5.富锌底漆HG/T3668-2009 6.喷涂聚脲防护材料HG/T3831-2006 7.交通钢结构聚苯胺防腐涂料JT/T695-2006 8.喷涂聚脲规范JGJ210—2010石油防腐 1.钢质石油储罐防腐工程技术规程GB50393-2008 2.钢制储罐液体环氧涂料内防腐层技术标准SY/T0319-1998 3.钢制管道液体环氧涂料内防腐层技术标准SY/T0457-2000 4.管道无溶剂聚氨酯涂料内外防腐层技术规 范 SY/T4106-2005 船用漆 1.船底防锈通用技术条件GB13351-1992 2.船用防锈漆通用技术条件GB6748-1986 3.船壳漆GB/T6745-2008 4.船用油舱漆GB/T6746-2008 5.船用车间底漆GB/T6747-2008 6.船用防锈漆GB/T6748-2008 7.船舶压载舱漆GB/T6823-2008 8.货舱漆GB/T9262-2008 铁路客运 1.客运专线铁路CRTSI型板式无砟轨道水泥乳化沥青砂浆暂行技术条件
焊接基础通用标准
标准号标准名称焊接基础通用标准GB/T3375--94 焊接术语GB324--88 焊缝符号表示法GB5185--85 金属焊接及钎焊方法在图样上的表示代号GB12212--90 技术制图焊缝符号的尺寸、比例及简化表示法GB4656--84 技术制图金属结构件表示法GB985--88 气焊、手工电弧焊及气体保护焊焊缝坡口的基本形式和尺寸GB986--88 埋弧焊焊缝坡口的基本形式与尺寸GB/T12467.1—1998 焊接质量要求金属材料的熔化焊第1部分:选择及使用指南GB/Tl2468.2--1998 焊接质量保证金属材料的熔化焊第2部分:完整质量要求GB/Tl2468.3--1998 焊接质量保证金属材料的熔化焊第3部分:一般质量要求GB/Tl2468.4--1998 焊接质量保证金属材料的熔化焊第4部分:基本质量要求GB/T12469--90 焊接质量保证钢熔化焊接头的要求和缺陷分级GBl0854--90 钢结构焊缝外形尺寸GB/T16672—1996 焊缝----工作位置----倾角和转角的定义焊接材料标准焊条GB/T5117--1995 碳钢焊条GB/T5118--1995 低合金钢焊条GB/T983—1995 不锈钢焊条GB984--85 堆焊焊条GB/T3670--1995 铜及铜合金焊条GB3669--83 铝及铝合金焊条GBl0044--88 铸铁焊条及焊丝GB/T13814—92 镍及镍合金焊条GB895--86 船用395焊条技术条件JB/T6964—93 特细碳钢焊条JB/T8423—96 电焊条焊接工艺性能评定方法GB3429--82 碳素焊条钢盘条JB/DQ7388--88 堆焊焊条产品质量分等JB/DQ7389--88 铸铁焊条产品质量分等JB/DQ7390--88 碳钢、低合金钢、不锈钢焊条产品质量分等JB/T3223--96 焊接材料质量管理规程焊丝GB/T14957—94 熔化焊用钢丝GB/T14958--94 气体保护焊用钢丝GB/T8110--95 气体保护电弧焊用碳钢、低合金钢焊丝GBl0045--88 碳钢药芯焊丝GB9460--83 铜及铜合金焊丝GBl0858--89 铝及铝合金焊丝GB4242--84 焊接用不锈钢丝GB/T15620--1995 镍及镍合金焊丝JB/DQ7387--88 铜及铜合金焊丝产品质量分等焊剂GB5293--85 碳素钢埋弧焊用焊剂GBl2470--90 低合金钢埋弧焊焊剂钎料、钎剂GB/T6208--1995 钎料型号表示方法GBl0859---89 镍基钎料GBl0046--88 银基钎料GB/T6418--93 铜基钎料GB/T13815--92 铝基钎料GB/T13679--92 锰基钎料JB/T6045--92 硬钎焊用钎剂GB4906--85 电子器件用金、银及其合金钎焊料GB3131--88 锡铅焊料GB8012--87 铸造锡铅焊料焊接用气体GB6052--85 工业液体二氧化碳GB4842--84 氩气GB4844--84 氮气GB7445--87 氢气GB3863--83 工业用气态氧GB3864--83 工业用气态氮GB6819--86 溶解乙炔GBlll74--89 液化石油气GBl0624--89 高纯氩GBl0665--89 电石其它GB12174--90 碳弧气刨用碳棒焊接质量试验及检验标准钢材试验GBl954--80 镍铬奥氏体不锈钢铁素体含量测定方法GB6803--86 铁素体钢的无塑性转变温度落锤试验方法G132971--82 碳素钢和低合金钢断口试验方法焊接性试验GB4675.1--84 焊接性试验斜Y型坡口焊接裂纹试验方法GB4675.2—84 焊接性试验搭接接头(CTS)焊接裂纹试验方法GB4675.3--84 焊接性试验T型接头焊接裂纹试验方法GB4675.4--84 焊接性试验压板对接(FISCO)焊接裂纹试验方法GB4675.5—84 焊接热影响区最高硬度试验方法GB9447--88 焊接接头疲劳裂纹扩展速率试验方法GB/T13817--92 对接接头刚性拘束焊接裂纹试验方法GB2358--80 裂纹张开位移(COD)试验方法GB7032--86 T型角焊接头弯曲试验方法GB9446--88 焊接用插销冷裂纹试验方法GB4909.12—85 裸电线试验方法镀层可焊性试验焊球法GB2424.17--82 电工电子产品基本环境试验规程锡焊导则GB4074.26—83 漆包线试验方法焊锡试验JB/ZQ3690 钢板可焊性试验方法SJl798--81 印制板可焊性测试方法力学性能试验GB2649--89 焊接接头机械性能试验取样方法GB2650--89 焊接接头冲击试验方法GB2651—89 焊接接头拉伸试验方法GB2652—89 焊缝及熔敷金属拉伸试验方法GB2653--89 焊接接头弯曲及压扁试验方法GB2654--89 焊接接头
通风机铆焊件技术条件(精)
前言 为了适应公司长期发展的需要,加强企业标准化建设,方便设计检验,制定本标准。本标准由南通大通宝富风机有限公司技术中心提出并归口 本标准起草单位:南通大通宝富风机有限公司技术中心 本标准主要起草人:顾晓卫 II 通风机铆焊件技术条件 1 范围 本标准规定了铆焊件的材料、主要铆焊件的拼接、铆焊件的落料公差、制造公差及铆接质量要求。
本标准适用于离心式和轴流式通风机中的铆焊件。其他风机的铆焊件亦可参照使用。 2 引用标准 下列标准所包含的条文,通过在本标准中引用而构成为本标准的条文。本标准出版时,所示版本均为有效。所有标准都会被修订,使用本标准的各方应探讨使用下列标准最新版本的可能性。 GB/T 8923 涂装前钢材表面锈蚀等级和除锈等级 Q/DTBF 0003 通风机焊接质量检验技术条件 3 术语 3.1 号科 根据图样或利用样板、样杆等直接在材料上划出构件形状和加工界线的过程。 3.2 落料 通过气割、剪切、锯料、冲切等工序,使材料分离成所需零件的工艺方法。 3.3 样冲眼 在毛坯或工件划线后,用样冲在中心线或辅助线上打出冲点的方法称为打样冲印,其冲点称为样冲眼。 4 铆焊件的材料 4.1 通风机铆焊件所用材料应符合有关材料标准的规定,转动件须具有合格证明或检验报告。 4.2 严禁使用有夹层、重皮等缺陷的材料。
4.3 非转动件材料的外表面允许有深度不超过0.5mm的划痕,并在涂漆前予以腻平;铝材的局部划痕深度不得大于0.3mm,不锈钢及其他有色金属材料的划痕深度不得大于0.1mm. 4.4 转动件代用材料的力学性能应不低于被代用材料的力学性能。 4.5 焊接件所选用的焊条应按图样的材质选取,其力学性能不得低于母材的性能。 1 4.6 按GB/T 8923 的规定,对锈蚀等级为B 级以下的材料,不得用在转动件上,也不得用在其余零部件的外表面上。 5 主要铆焊件的拼接 5. 1 离心通风机 5.1.1 叶轮的轮盘与轮盖允许拼接块数不得超过表1的规定。除平轮盘外,其余轮盖一般为径向拼接。拼接焊缝的位置与叶片焊缝的位置交叉。 表1 轮盘与轮盖允许拼接的块数叶轮直径平轮盖锥面轮盖单圆弧轮盖双圆弧轮盖双锥面轮盖轮盘 280-400 ————≤2 — >400-1000 ≤2 ≤2 ≤2 ≤2 ≤2 >1000-1600 ≤2 ≤3 ≤3 ≤3 ≤4 ≤3 >1600-2800 ≤3 ≤4 ≤4 ≤4 ≤6 ≤3 >2800-3150 ≤4 ≤5 ≤6 ≤6 ≤8 ≤3 >3150 ≤5 ≤6 ≤8 ≤8 ≤10 ≤4
2007重型机械通用技术条件
重型机械通用技术条件 1 概况 2007年版《重型机械标准》(以下简称新《重标》)第一卷第3部分“通用技术条件”,共编入标准二十六项。其中包括:生产设备安全卫生设计标准一项,重型机械通用技术条件JB/T5000.1~15-2007及JB/ZQ4722-2006十六项,液压、气动系统通用技术条件三项,以及运输包装方面的标准六项。与1998年版《重型机械标准》(以下简称原《重标》)第一卷第三部分“通用技术条件”的项目相比,删除了一项标准,增加了五项标准,该套标准包含从原材料、外购件、铸件、焊件、锻件、切削加工件、配管、涂装、装配到产品包装全生产过程中各主要工序通用的,也是必须执行的技术规范。是新《重标》的重点部分。新、旧《重标》通用技术条件标准项目对照。见表1。 JB/ZQ 4722-2006 重型机械通用技术条件锻钢件补焊、JB/T 10607-2006 液压系统工作介质使用规范、GB/T 18923-2002 运输包装件质量界限、道路车辆外廓尺寸、GB 1589-2004轴荷及质量限值五项标准。取消了GB/T 1834- 80通用集装箱最小内部尺寸,GB/T 1413- 1998 系列1集装箱分类、尺寸和额定质量中已包含GB/T 1834- 80通用集装箱最小内部尺寸的内容,GB/T 1413-1998将二项标准合并为一项标准。下面重点介绍JB/T5000.1~15新、旧标准的主要差异。 2 JB/T 5000.1 《重型机械通用技术条件产品检验》 2.1 产品检验的一般要求
2.1.1 增加了2.1条对半成品(原材料)的定义。 2.1.2 新《重标》根据使用要求,增加了2.1.3条对半成品的检验要求。 2.1.3 增加了2.3 C)条对外协配套件的选用要求。 2.1.4 新《重标》中的表2将焊缝缺陷等级、焊接件尺寸偏差及形位公差等级的图样标注由原来的4个等级改为3个等级,取消了原《重标》焊缝质量评定级别DS、DK级、焊缝缺陷等级Ⅳ级及尺寸与角度偏差等级D级和形位公差等级H级。 2.1.5 修改了铸件尺寸公差图样标注的毛坯基本尺寸范围及尺寸公差等级,新、旧标准对比见表2。 2500mm和有色金属铸件毛坯基本尺寸≥10~250mm的尺寸分段,增加了铸铁件尺寸公差等级CT11和有色金属铸件尺寸公差等级CT9并规定在图样上不标注。取消了铸钢件毛坯基本尺寸≤16mm的尺寸分段及尺寸公差等级CT12。 2.1.6 修改了涂装除绣等级与腐蚀类别及在图样上标注的规定,新、旧标准差异见表3。 a)新《重标》增加了除绣等级及其在图样上标注的规定; b)根据ISO12944将涂装类别改为腐蚀类别。 c)除绣等级、腐蚀类别、涂层厚度及面漆颜色均按JB/T 5000.12-2007的规定。 2.1.7 增加了2.13条对生产厂家的产品制造质量要求及2.14条对特殊装置的检验要求。 2.2 检验记录 2.2.1 产品质量检验记录种类的C)条增加了粘结剂的检验记录。 2.2.2 原《重标》的5.3条规定“产品质量检验记录由制造厂质量检验部门填报与汇总并建立产品质量档案”,新《重标》在原基础上增加了“如合同约定由第三方对产品质量进行监理,监理方可以见证制造厂的检验过程和检验结果。” 3 JB/T 5000.2 《重型机械通用技术条件火焰切割件》 3.1 适用范围 修改了火焰切割件的适应范围,由原“本标准适用于重型机械产品中碳钢、低合金钢、钛及钛合金板材的火焰切割件”改为“本标准适用于厚度为6~300mm的低碳钢、中碳钢及普通低合金钢的火焰切割件”增加了厚度为6~300mm的低碳钢及取消了钛及钛合金板材的适用范围。 3.2 术语和定义 3.2.1 增加了1.1条火焰切割件、1.7条表面缺陷、1.8条上缘熔化及1.9条挂渣的定义。 3.2.2 修改了垂直度和倾斜度公差及表面粗糙度的定义 a) 垂直度公差原定义是“指在理论正确角度条件(与工件基准面成90°),通过切割面轮廓最高点和最低点的两条平行直线间的距离。垂直度公差用u表示”(见原标准的图1),现定义为“在本部分
焊接通用技术条件
焊接通用技术条件 SDZ018-85 本标准适用于水利电力系统一般机械及钢结构产品的手工电弧焊和埋弧自动焊。凡产品图样或技术文件中无特殊要求时,均应符合本标准的规定。 1 一般技术要求 1.1 焊接工作应配备专职的焊接技术人员、焊接检查和检验人员。 1.2 焊工应经专门的技术训练,从事Ⅰ、Ⅱ类焊缝焊接的工人,需按SDZ009-84《手工电弧焊及埋弧自动焊焊工考试规则》或其他有关焊工考试规则进行考试,并取得第三方公证单位认可的焊工合格证。 1.3 焊接原材料和焊接材料的型号、规格和订货要求应符合图样和技术文件规定,材料的代用应执行代用制度。材料进厂时,应按材料标准的规定检查验收,必要时可进行抽检复验。对无牌号、规格、无质量保证书的原材料和焊接材料,只有经过检验和鉴定,确定其规格、型号、质量状态后,方可使用。 1.3.1 焊接材料的选用,应根据母材的化学成份、机械性能、焊接接头的抗裂性、焊前预热、焊后热处理及使用条件等因素综合考虑。参照表1选用。 表1 焊接材料的选用及预热、焊后热处理规范
注:回火加热速度不大于200℃/小时,保温时间一般为0.04时/毫米,最低不少于两小时,以2.5~
3℃/分钟的速度缓冷至300℃后空冷。 1.3.1.1 同种钢材之间的焊接,焊接材料的选用,一般应符合下列要求: a.焊接接头的机械性能应与母材相当; b.工艺性能良好; c.低碳钢及低合金钢焊接的焊条应符合GB981-76《低碳钢及低合金高强度钢焊条》的要求。 1.3.1.2 异种钢之间的焊接,焊接材料的选用应符合下列要求: a.两侧均非奥氏体不锈钢时,可根据合金元素含量较低(或强度等级较低)的一侧钢材选用。 b.其中一侧是奥氏体不锈钢时,可选用含镍、铬量比不锈钢更高的焊条(焊丝)。 1.4 焊前准备。 1.4.1 焊接前必须根据材料的可焊性、结构特点、设计要求、设备能力、使用条件及施工环境等因素编制合理的焊接工艺。 1.4.2 首次使用的钢种以及改变焊接材料类型、焊接方法和焊接工艺,必须在施工前进行焊接工艺试验。并按有关标准进行工艺评定。 1.4. 2.1 工艺试验所取得的焊接位置,应包括现场作业中所有的焊接位置。当现场实际焊接作业中,存在明显的妨碍焊接过程的障碍时,应在试验中考虑设置模拟障碍。 1.4. 2.2 工艺试验所使用的母材及焊接材料,应与工程上使用的相同。 1.4. 2.3 工艺试验结果评定内容,除无损探伤、拉伸及冷弯试验外,还应根据材料性质提出有关力学性能试验、金相试验、抗裂试验和化学试验等。 1.4. 2.4 在焊工考试和工程施焊前,必须具有合格的试验评定结果,该结果应由技术负责人验证。 1.4.3 焊接材料的使用。 1.4.3.1 焊条应根据说明规定进行烘干,烘干的焊条应在100~150℃保温,随用随取。烘干的焊条位置于空气中超过四小时,重新烘干,重新烘干次数不超过两次。 1.4.3.2 焊丝表面不得有油污、水、铁锈等,不得有小角度弯曲。 1.4.3.3 焊剂颗粒度应符合说明书要求,焊剂使用前应烘干,烘干温度和保温时间,按说明书要求进行,烘干的焊剂要随用随取。 1.4.4 钢结构焊缝分类参照表2。