浅析石灰石分解特性与石灰窑结瘤的关系
影响石灰窑煅烧的主要因素

影响石灰窑煅烧的主要因素1.1 石灰石质量的影响1.1.1 杂质的影响在石灰石矿石的化学成分中,除含CaCO3有效成分之外,还含多种有害杂质。
杂质来源主要有以下三种途径:(1)矿石自身含有的杂质,如:SiO2、Al2O3、Fe2O3、K2O、Na2O、P、S等。
(2)矿石在开采过程中,矿体围岩或夹层混入的杂质等。
(3)矿石在开采、运输、装卸过程中,粘附在矿石表面的泥土、沙粒等杂质。
无论杂质来自何方,都会对石灰窑产生很大的危害。
如杂质中的SiO2、Al2O3、Fe2O3在较低温度(900℃)下就开始和烧成石灰中的CaO发生反应,在煅烧区易形成液相,生成低熔点带粘性的含钙化合物,如硅灰石(CaO·SiO2),硅酸二钙(2CaO·SiO3),铁酸钙(CaO·Fe2O3和2CaO·Fe2O3)等,随着温度升高反应加剧。
这些低熔点化合物生成后,导致石灰颗粒间相互粘结,堵塞颗粒表面的细孔,不仅降低石灰活性,还会堵塞CO2分解逸出的通路,使石灰石分解不完全,烧成的石灰带“芯,石灰形成生烧,致使石灰的活性降低,影响其质量。
当杂质含量过高时,会与石灰中CaO反应后结团形成窑瘤,从而导致炉况失常。
当SiO2、Al2O3和Fe2O3或Na2O、K2O的总量分别为4~5%或0.1~0.2%以上时,易对炉况造成危害。
1.1.2 石灰石的结晶组织石灰石的晶形结构对煅烧速度、出灰质量也有较大的影响。
如嫩石、石纹较细的石灰石,石灰石中的方解石(CaCO3)结晶粒度小、晶粒间有间隙,在低温下煅烧体积膨胀而不易碎裂,在高温时CO2容易分离逸出,这种石灰石更易燃烧,产生的石灰颗粒细、活性好;边坡石、石纹粗糙的石灰石与此相反。
当温度在500~600℃,尚未达到CaCO3分解点时,因石灰石中的方解石结晶粒度粗大,结构致密,受热后因体积膨胀而易碎裂,易成碎块、细末,将阻塞窑内风路,恶化煅烧条件,分解时CO2逸出阻力大,分解速度慢,不宜使用。
石灰窑常见问题和故障处理
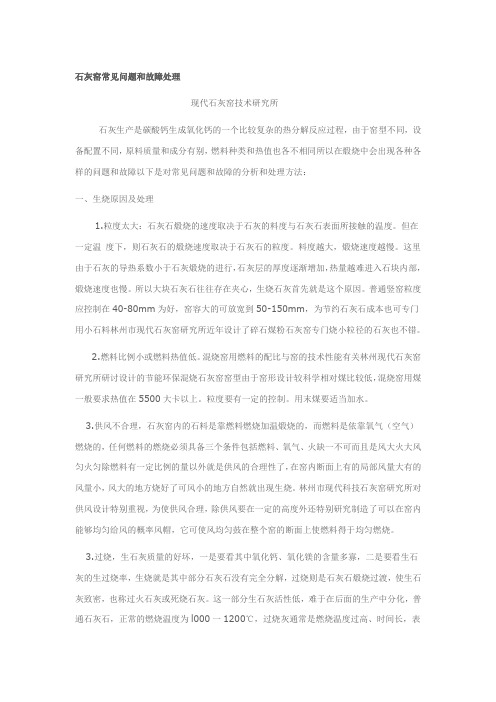
石灰窑常见问题和故障处理现代石灰窑技术研究所石灰生产是碳酸钙生成氧化钙的一个比较复杂的热分解反应过程,由于窑型不同,设备配置不同,原料质量和成分有别,燃料种类和热值也各不相同所以在煅烧中会出现各种各样的问题和故障以下是对常见问题和故障的分析和处理方法:一、生烧原因及处理1.粒度太大:石灰石煅烧的速度取决于石灰的料度与石灰石表面所接触的温度。
但在一定温度下,则石灰石的煅烧速度取决于石灰石的粒度。
料度越大,煅烧速度越慢。
这里由于石灰的导热系数小于石灰煅烧的进行,石灰层的厚度逐渐增加,热量越难进入石块内部,煅烧速度也慢。
所以大块石灰石往往存在夹心,生烧石灰首先就是这个原因。
普通竖窑粒度应控制在40-80mm为好,窑容大的可放宽到50-150mm,为节约石灰石成本也可专门用小石料林州市现代石灰窑研究所近年设计了碎石煤粉石灰窑专门烧小粒径的石灰也不错。
2.燃料比例小或燃料热值低。
混烧窑用燃料的配比与窑的技术性能有关林州现代石灰窑研究所研讨设计的节能环保混烧石灰窑窑型由于窑形设计较科学相对煤比较低,混烧窑用煤一般要求热值在5500大卡以上。
粒度要有一定的控制。
用末煤要适当加水。
3.供风不合理,石灰窑内的石料是靠燃料燃烧加温煅烧的,而燃料是依靠氧气(空气)燃烧的,任何燃料的燃烧必须具备三个条件包括燃料、氧气、火缺一不可而且是风大火大风匀火匀除燃料有一定比例的量以外就是供风的合理性了,在窑内断面上有的局部风量大有的风量小,风大的地方烧好了可风小的地方自然就出现生烧。
林州市现代科技石灰窑研究所对供风设计特别重视,为使供风合理,除供风要在一定的高度外还特别研究制造了可以在窑内能够均匀给风的概率风帽,它可使风均匀鼓在整个窑的断面上使燃料得于均匀燃烧。
3.过烧,生石灰质量的好坏,一是要看其中氧化钙、氧化镁的含量多寡,二是要看生石灰的生过烧率,生烧就是其中部分石灰石没有完全分解,过烧则是石灰石煅烧过渡,使生石灰致密,也称过火石灰或死烧石灰。
窑结大球原因分析
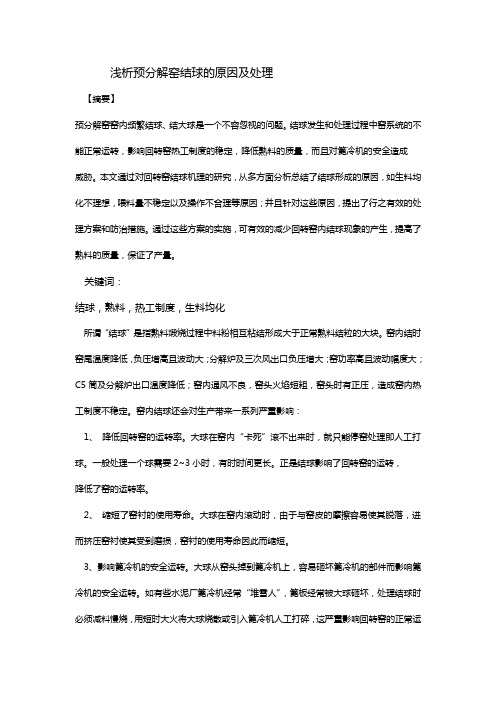
浅析预分解窑结球的原因及处理【摘要】预分解窑窑内频繁结球、结大球是一个不容忽视的问题。
结球发生和处理过程中窑系统的不能正常运转,影响回转窑热工制度的稳定,降低熟料的质量,而且对篦冷机的安全造成威胁。
本文通过对回转窑结球机理的研究,从多方面分析总结了结球形成的原因,如生料均化不理想,喂料量不稳定以及操作不合理等原因;并且针对这些原因,提出了行之有效的处理方案和防治措施。
通过这些方案的实施,可有效的减少回转窑内结球现象的产生,提高了熟料的质量,保证了产量。
关键词:结球,熟料,热工制度,生料均化所谓“结球”是指熟料煅烧过程中料粉相互粘结形成大于正常熟料结粒的大块。
窑内结时窑尾温度降低,负压增高且波动大;分解炉及三次风出口负压增大;窑功率高且波动幅度大;C5筒及分解炉出口温度降低;窑内通风不良,窑头火焰短粗,窑头时有正压,造成窑内热工制度不稳定。
窑内结球还会对生产带来一系列严重影响:1、降低回转窑的运转率。
大球在窑内“卡死”滚不出来时,就只能停窑处理即人工打球。
一般处理一个球需要2~3小时,有时时间更长。
正是结球影响了回转窑的运转,降低了窑的运转率。
2、缩短了窑衬的使用寿命。
大球在窑内滚动时,由于与窑皮的摩擦容易使其脱落,进而挤压窑衬使其受到磨损,窑衬的使用寿命因此而缩短。
3、影响篦冷机的安全运转。
大球从窑头掉到篦冷机上,容易砸坏篦冷机的部件而影响篦冷机的安全运转。
如有些水泥厂篦冷机经常“堆雪人”,篦板经常被大球砸坏,处理结球时必须减料慢烧,用短时大火将大球烧散或引入篦冷机人工打碎,这严重影响回转窑的正常运转,影响回转窑的热工制度的稳定,降低了熟料的质量。
因此,研究结球极其重要,绝不容忽视。
一、结球的机理简析近年来,很多人对回转窑结球的机理进行了探讨,研究报道中都有对结蛋料和正常料化学成分的对比,并探讨结蛋形成的机理。
有水泥专业技术人员曾经从预分解窑生料圈后面(过渡带)发现许多直径达1m的大球,并从中取出10个大球,从中间锯开,发现这些球中间都有一个褐色、细粒、白垩状的内核及灰褐色多孔状的外壳。
窑内结圈、结球的原因及处理措施

窑内结圈、结球的原因及处理措施中控室侯素克结圈是指窑内在正常生产中因物料过度黏结,在窑内特定的区域形成一道阻碍物料运动的环形、坚硬的圈。
这种现象在回转窑内是一种不正常的窑况,他破坏正常的热工制度,影响窑内通风,造成来料波动很大,直接影响回转窑的产量、质量、消耗和长期安全运转。
尤其频繁结圈的回转窑,不仅破坏了窑内正常热工制度,而且损害操作人员的身体健康,给生产造成经济损失。
引起回转窑结圈的因素很多,它与原料性质、生料成分、燃料的灰分和细度、窑型、窑内还原气氛及热工制度等有关。
1 结圈的形成回转窑内形成结圈的因素很多,但液相的产生和固化是结圈的主要形成过程。
而衬料温度、物料温度、煤灰和生料组成又是决定液相的生成和固化的主要因素。
在正常情况下,窑皮保持在200mm左右的厚度,该温度条件及区域内若熔化和固化的过程达到平衡,窑皮就不会增厚。
当熔化的少固化的多,其厚度增长到一定程度,即形成圈。
当衬料与物料的温差大时,在足够液相的条件下,圈体越结越厚。
1.1前结圈的形成前圈结在烧成带和冷却带交界处,由于风煤配合不好,或者煤粉粒度过粗,煤灰和水分大,影响煤粉燃烧,使黑火头长,烧成带像窑尾方向移动,熔融的物料凝结在窑口处使“窑皮”增厚,发展成前圈,或者由于煤粉落在熟料上,在熟料中形成还原性燃烧,铁还原成亚铁,形成熔点低的矿物或者由于煤灰分中氧化铝含量高而使熟料液相量增加,黏度增大,当遇到入窑二次风温降温、冷却,就会逐渐凝结在窑口处形成圈。
前圈形成的主要原因是煤粉的质量,熟料中溶剂矿物含量过高或氧化铝含量过高,燃烧器在窑口断面的位置不合理,影响煤粉燃烧,使结圈速度加快,前温急烧,导致温差相差大,造成液相冷却凝固形成前圈,1.2熟料圈的形成原因熟料圈(又称后圈),是结在窑内烧成带与放热反应带之间的圈,也是回转窑内危害最大的结圈。
造成熟料圈的原因很多,主要有生料化学成分,熟料圈行成往往在物料刚出现液相的地方,物料在1200~1300度范围内为防止结圈,配料时应考虑液相不易过多,液相黏度不易过大;原燃材料中的有害成分,原燃材料中的有害成分过多,降低物料的熔点,结圈的可能性就增大,正常情况下,此类结圈大多发生在放热反应带以后的地方;煤的影响,煤灰中氧化铝的含量较高,当煤灰掺入物料中时,使物料液相量增加往往易结圈;操作和热工制度的影响,头煤加入量较多,产生还原气氛,形成低熔点矿物,使液相提前出现,容易结圈,二三次风配合不当,火焰过长,液相提前出现,特别是在分解率高的情况下,结圈的可能性更大。
石灰竖窑窑内结瘤及处理办法

石灰竖窑窑内结瘤及处理办法石灰回转窑结瘤石灰石生成石灰是一个简单的化学反应,热量输入过多造成温度过高或反应时间过长,就会出现过烧。
石灰相互粘连在一起,或与周围正常状态下的物料粘连起来,或粘附在窑壁上,形成结瘤。
一、轻微过烧粘连当窑温过高、频繁或大幅调产后会出现局部温度过高造成粘连,但采用敲打等方式很易破碎。
在窑底卸灰过程中观测到有个別烧融、粘连的情况。
降低产品活性度,影响窑体通透性,是结瘤的诱因。
解决办法:立即降低温度,检査设备,手工或自动卸料加速粘连物卸出,恢复窑体通透性,避免更严重的结瘤发生。
二、大面积结瘤轻微粘连如若未能及时发现,很快就会发展成大面积粘连结瘤,卡在窑底不能卸料,并在卸料区产生高温,损坏卸料平台和液压缸。
卸料平台温度急剧上升,窑顶料面出现倾斜,卸料平台动作次数明显增多。
损坏卸料平台、风帽和液压设备,严重影响石灰质量和产量,处理费时费力,短则10h以上,长则需要10~15日。
解决办法:1、立即降产降温避免结瘤。
2、打开卸料平台入孔,观测结瘤是否已经移动到卸料平台,如果没有就手动卸料,避免损坏卸料平台,加快结瘤的移动以避免粘结更大。
3、在结瘤凹陷处凿出小洞,用铁管引压缩空气直吹洞中,加速结瘤局部冷却。
产生的应力将结瘤分裂开,将较大的结瘤分裂成小块,顺利掏出。
如果是更大或多个结瘤,可将多个入孔打开,同时进行此操作。
4、如采结瘤块非常坚固,需要用风镐等工具,配合降温措施,将结瘤块打碎成小的结瘤块,从卸料平台掏出。
5、如果结瘤块过大,不能随着物料下降,则需停产,降至常温,进入窑内进行破碎。
三、粘在窑壁上这是较严重的结瘤,一般出现在煅烧带,往往伴随着大面积结瘤而产生,是不好处理的,属于严重的生产事故。
早期会出现窑顶料面倾斜,卸料不均衡,石灰生烧或过烧,质量严重分化,出现偏窑现象。
在窑壁外侧可测出高温点,严重时将外壁油漆烧毁,卸料平台处可见到红灰。
严重影响窑体寿命,处理不当会导致窑内耐材报废。
石灰竖窑结瘤原因分析和预防措施

第3 8 卷 第1 期
2 0 I 3年 2月
耐 火 与 石 灰
・ 1 5・
石灰 竖 窑 结瘤 原 因分 析 和 预 防措 施
刘 俊 海 张 宝吉 ( 焦作 神华 重 型机械 制造 有 限公 司 ,焦作 4 5 4 1 0 0 )
摘 要 :结合生产实践 , 对石 灰竖 窑 的结瘤 原因进 行 了分析 , 介 绍 了结瘤 的 防范措 施 、 结 瘤的 判断 方 法及 处理
C a C O 含量不同, 最好 的石 灰 石 C a C O 含 量 达 9 8 %
以上 , 一 般 要 求 如 下 :C a C O 3>9 0 % ;S i O <3 %;
Mg C O 3 < 6 %; ( A 1 2 O 3 +F e 2 O 3 ) <1 . 5 %。
等有关 单 位投产 , 在 使用 的几 年 时间里 , 由于使 用单
L i u J u n h a i Z h a n g B a o j i ( J i a o z u o S h e n h u a He a v y Ma c h i n e B u i l d i n g C o . , L t d . ,J i a o z u o 4 5 4 1 0 0 , C h i n a )
整, 并 采 取 了 相应 的 预 防措 施 , 使 结 瘤 现 象 逐 步 缓 解, 直 至完全 得 到控制 。
石灰煅烧机理

石灰煅烧机理石灰煅烧是指将石灰石(CaCO3)在高温下分解成氧化钙(CaO)和二氧化碳(CO2)的过程。
这个过程不仅在工业生产中广泛应用,也在冶金、建筑、环保等领域发挥着重要作用。
本文将详细介绍石灰煅烧的机理。
石灰煅烧的机理可以通过两个主要反应来解释:石灰石的分解反应和氧化反应。
首先是石灰石的热分解反应,化学方程式为CaCO3(s) → CaO(s) + CO2(g)。
这个反应在900~1000℃之间进行,需要输入大量的热量。
石灰石分解的主要原因是在高温下,CaCO3的分解活化能降低,使得分子内的化学键能够被破坏。
具体来说,随着温度的升高,CaCO3的晶格结构发生变化,相邻Ca和CO3离子之间的距离增加,石灰石颗粒内部的压力增大,导致材料发生脆性断裂。
分子内的键被破坏后,CaO和CO2分开,形成氧化钙和二氧化碳。
其次是氧化反应,化学方程式为CaO(s) + 1/2 O2(g) → CaO(s)。
在空气中,氧化钙会与氧气发生反应,生成CaO。
这个反应是一个氧化还原反应,氧化钙失去电子生成Ca2+离子,氧气获得电子生成O2-离子。
由于氧化反应伴随着释放热量,所以这个反应是放热反应。
通过这个反应,氧化钙可以得到更加稳定的化学结构,使得石灰石的煅烧产物更加纯净。
在石灰煅烧的过程中,还有一些次要反应参与其中。
一方面,石灰石的分解反应是一个端头反应,需要从石灰石颗粒的表面开始进行。
因此,石灰石的分解速率也受到颗粒表面的条件和外界环境的影响。
另一方面,由于煅烧温度较高,石灰石颗粒中的杂质(如镁、铁、铝等)有可能发生固相反应或溶解反应。
这些反应可以改变石灰石的煅烧产物的性质,使得产物的纯度和质量发生变化。
石灰石的煅烧过程涉及到多个物理和化学因素的相互作用。
首先是温度的影响。
石灰石分解反应的速率随着温度的升高而增加,但反应速率也会受到温度过高时颗粒烧结的影响。
其次是氧气的影响。
较高的氧浓度可以提高氧化反应的速率,但过高的氧浓度会加剧石灰石颗粒的烧结现象。
石灰炉结瘤

石灰炉结瘤,是石灰煅烧工艺中危害最大、处理起来却又十分棘手的问题。
石灰炉结瘤除了造成炉内通风不畅,还会因炉壁瘤脱落而破坏内衬。
因此,结瘤对石灰炉优化指标、延长使用寿命、节约运行成本等,均会产生很大的负面影响。
由于矿石成因、运输成本等多种原因,中铝河南分公司6台石灰炉所用的石灰石,普遍存在粒度偏大且不均匀、杂质含量高等突出问题,从而造成结瘤现象更加严重。
实际生产中就曾出现过石灰炉冷却带与预热带交界处结瘤厚达1米多的现象,并因此造成炉内通风不畅、石灰生烧,对氧化铝生产造成了十分不利的影响。
一、石灰炉结瘤的机理石灰炉结瘤的原因,主要是进入石灰炉内的杂质发生了次生反应。
实际生产中我们发现,杂质含量多的物料,即使在正常的温度下煅烧,也容易出现结瘤现象。
而杂质含量低的物料,即使煅烧温度较高、过烧量大,也不容易发生结瘤现象。
可见,结瘤的程度与石灰炉内的杂质含量有直接的关系。
入炉杂质的主要来源是石灰石中夹带的杂质和焦炭中的灰分。
通过对炉内杂质进行化验分析,我们确认杂质的主要成分为SiO2、Fe2O3、Al2O3、Na2O和K2O等。
这些杂质与石灰石(主要成分为CaCO3)煅烧后形成的CaO在炉内不同温度下发生化学反应后所形成的固态物质即为瘤子,其中尤以Fe2O3、Al2O3和SiO2的影响最为严重。
炉内杂质与CaO之间的化学反应主要有以下几种:CaO+Al2O3=CaO·Al2O33CaO+Al2O3=3CaO·Al2O3CaO+SiO2=CaO·SiO2CaO+Fe2O3=CaO·Fe2O32CaO+Fe2O3=2CaO·Fe2O34CaO+4Fe2O3+4Al2O3=4CaO·Fe2O3·Al2O3其中Al2O3与CaO的反应温度为500~900℃,到1000℃时反应进行得十分迅速,主要生成物有CaO·Al2O3和3CaO·Al2O3;Fe2O3与CaO的反应温度为800~900℃,主要产物有CaO·Fe2O3。
- 1、下载文档前请自行甄别文档内容的完整性,平台不提供额外的编辑、内容补充、找答案等附加服务。
- 2、"仅部分预览"的文档,不可在线预览部分如存在完整性等问题,可反馈申请退款(可完整预览的文档不适用该条件!)。
- 3、如文档侵犯您的权益,请联系客服反馈,我们会尽快为您处理(人工客服工作时间:9:00-18:30)。
16纯碱工业浅析石灰石分解特性与石灰窑结瘤的关系魏浩源,宋信信,曾建刚(江西晶昊盐化有限公司,江西宜春331200)摘要:针对石灰窑烧制时容易结瘤的特点,从石灰石的分解特性入手,结合相关文献资料,总结了石灰窑煅烧时窑体可能发生的化学反应及物理变化,旨在说明窑体结瘤的大致过程,为同行从业人员提供相关的理论参考。
关键词:石灰石;煅烧;结瘤;石灰窑;机理中图分类号:TQ132.32 文献标识码:C文章编号=1005-8370(2019)01 -16-03石灰作为重要的工业原料,常见于纯碱、钢铁、电石等工业,这些产业的高速发展推动了石灰石煅 烧技术的全面发展[1]。
但是,无论各行业使用哪种 类型的窑体,烧制石灰石时都无法避免结瘤现象。
结瘤不仅影响正常的生产制造,而且会对窑体产生 不可逆的损伤。
结瘤是指石灰石在高温煅烧时,窑 体出现块状石灰粘结料(俗称“瘤子”)的现象[2],是 窑体物料经历一系列复杂的化学反应和物理变化的 过程,主要包括固相化学反应、液相生成和冷却结块 三个过程。
在纯碱生产中,结瘤不仅会使出灰螺锥 无法正常下灰,导致石灰产量大幅度减少,而且会降 低窑体中C02的含量,影响下游碳化塔的正常工 作,严重的将导致停产。
因此,为了使同行业人员对 结瘤现象有一个较为清晰的认识,本文着重阐述了 窑体物料在结瘤时可能发生的物理和化学变化,以此期望同行操作人员能在煅烧石灰石时尽量规避瘤 子的生成,保证石灰窑的连续化生产。
1石灰石原料的成分石灰石是氨碱法中最重要的原料之一,在我国 的蕴藏极为丰富。
相比于其它制碱原料而言,石灰 石为天然资源,成分含量相对复杂,主要为CaC03,其余为杂质。
各地石灰石中CaC03及其杂质含量 各有差异,但基本上包括MgC03、Fe203、Si02和A1203等氧化物。
一般纯碱生产中石灰石原料的规 格成分如下:CaC0390% 〜99%,Si023%,Mg-C033 %,Fe203十Al2031.5 %。
高温煅烧时,过多的 杂质在分解时不仅浪费能源,且产生的副产物不能 参与氨的回收。
更为严重的是这些杂质是石灰窑结 瘤的“首恶元凶”。
2石灰窑中瘤子的形成2.1 CaC03的分解煅烧CaC03时,发生分解反应:CaC03(s)—CaO(s) +C02(g)某温度时CaC03分解的平衡常数K表示为:C c a O X C c〇2式中CaC03和CaO为固体,浓度为常数,即CaC03在某温度时的分解平衡常数与生成物C02浓度呈正相关,亦可用C02分压表示。
CaC03分解 温度与C02分压关系如图1所示[3]。
图1 CaC03分解温度与C(〕2分压曲线图一般而言,CaC03分解由五个步骤组成,包括 两步热传递、CaC03正式受热分解和C02的逐层逸 出W。
其分解过程符合固态化合物分解反应特性,即最初反应分布在某些区域,随后这些分解产物逐 渐增多并聚集成一个个新物相的核,即分解晶核,然 后周围分子围绕晶核继续发生界面反应,直至Ca-C03全部分解[5]。
由图1可知,CaC03的分解温度 始于600 °C左右,900 °C以后,分解速率显著增加,如若继续升温,分解速度呈现倍数增长。
需要指出 的是,虽然高温有利于CaC03的分解,但是煅烧温 度不能无限制上升,因为纯CaC03在常压下的熔点 为1 340 °C。
如若局部超过此温度,则CaC03的物 理状态开始发生变化,由固相转变为液相,此时Ca-c o3的分解不再满足固态化合物分解反应特性,且 液态CaC03很可能会粘结在固态CaC03和CaO的表面,形成瘤块。
2.2 Si02、Fe203与瘤块的形成石灰石中Si02杂质能与CaO反应,生成CaO •Si02、2Ca0 .Si02、3Ca0 •Si02 等硅酸钙系列化 合物。
Fe203与CaO反应,生成铁酸钙,方程式可 表示为:Si02+XCa0^XCa0 •Si02Fe203+XCa0^XCa0 •Fe203Ca0、Fe203与Si02属于离子型晶格构造化合 物,具有较高的熔沸点,常规煅烧温度下基本不熔 化。
但是,它们之间彼此紧密相连,质点一旦获得能 量,就很容易脱离束缚,进人其它晶体晶格内,发生 固相化学反应M;生成的硅酸钙和铁酸钙复合物属 于低熔点化合物,在较低温度下即可转变为液相,此 液相复合物中游离的CaO又不断地与低熔点化合 物反应生成熔点更低的共熔复合物;在冷却结晶过 程中,其它熔点较高的其它物质,成为液相结晶的晶 核,伴随着晶核长大的过程就是瘤块初生的过程[7]。
初始,CaO与Fe203在760 °C左右即可有轻微 的吸热现象,生成2CaO • ?6203;随着煅烧温度不 断地升高,2CaO •Fe203继续参加反应,最终生成 CaO •Fe203。
Si02惰性较高,在900 °C时才开始 与CaO反应,其生成物2CaO • &02具有较高的熔 点,大多数直接转变为瘤块。
虽然在液相中2CaO •Si02的存量较少,但是它在降温过程中容易发生 晶型转变影响瘤块的强度。
如若考虑CaO—Fe203一Si02三元复合体系,Si02除了与CaO发生反应,在1 000 °C时也会和CaO •Fe203相互作用,生成 复合铁酸钙[8]。
从机理上说:铁酸钙系列化合物是 瘤子生长结块的基础液相,其它杂质化合物几乎围 绕铁酸钙不断反应并生成新的低熔点化合物。
2.3 Mg0、AI203对瘤块生成的影响石灰石中MgC03杂质在540 °C时即可发生分 解反应,化学方程式为:MgC03—Mg0+C02MgO在685 °C与Si02的固相化学反应:2MgO十Si02—2MgO •Si02600 °C时与Fe203开始作用:Mg0+Fe203—MgO .Fe203MgO属于高熔点化合物,在煅烧中会形成高熔 点的钙镁橄榄石,多数游离的MgO结晶为方镁石,直接成为瘤块的一部分。
其余MgO在结瘤过程中 主要起两个作用[9],一是M gO能够固溶进2CaO •Si02当中,维持2CaO •Si02的形态,促进硅酸盐的 生成;二是M gO不仅能减少铁酸钙化合物的生成 而且能有效降低液相量的数量。
结瘤过程是部分低 熔点化合物熔化后,流动至未熔化物料处并粘结成 一体,并不是一次性熔化后再凝固。
所以液相量的 减少,会使瘤块的体积和强度受到影响。
高熔点的 钙镁橄榄石,增加了体系内液相熔化温度,降低了瘤 块的强度。
相比于Ca0,Al203更容易与Fe203结合,它是 复合铁酸钙形成的结构基础。
在多元铁酸钙体系 中,Fe203与CaO反应生成二元铁酸钙,随着温度 的升高,三元铁酸钙出现,A1203在900 °C便能固溶 进铁二元酸钙中形成CaO •A1203• 2Fe203化合 物[1°]。
此后在900 °C时S02又开始与CaO •A1203 • 2Fe203发生固溶而形成复合铁酸钙。
江西晶昊盐化有限纯碱分公司自2018年7月19日点窑至今,未见结大瘤、团瘤、圈瘤的现象,窑气浓度平均>41%,窑况非常稳定;现场设备、生产、环境管理井然有序、石灰工序的生产运行未对下道 工序造成影响。
这总体上得益于车间和班组严格统 一的石灰石煅烧机理和理念,严控各个操作参数和 指标做到始终如一'。
现附上1*窑体的部分数据,供同行参考。
3石灰窑操作数据一•一煅烧区 一▲一冷却IK121416 18 20日期(9月)图2 1#窑体内三区温度变化曲线4结语高温条件及成分的复杂性,决定了石灰石在分解时窑体内部物料变化的复杂性。
基于石灰窑结瘤 机理可知,石灰石中杂质的含量决定了瘤块的生成 情况。
因此,为了减少瘤子的产生,维持石灰窑连续 化周期性生产,需对石灰石原料的进场质量进行严 格把关,坚决杜绝不合格的石灰石进窑;在操作上,需控制好煅烧温度,CaC 03含量高的石灰石,可适 当提高煅烧温度;对于CaC 03含量较低的石灰石, 可将煅烧区的温度控制在1 1〇〇 °C 左右。
[J ].工程建设与设计,2014(2)[2] 顾德平.如何预防石灰窑结瘤[J ].纯碱工业,1988 (3)[3] 大连化工研究设计院.纯碱工学(第2版)[M ].北京:化学工业出版社,2004[4] 冯云,陈延信.碳酸钙的分解动力学研究进展[J ].硅酸盐通报,2006 (3)[5] 范浩杰,章明川,吴国新.碳酸钙热分解的机理研究[J ].动力工程,1998 (5)[6] 郭贺.M gO 对烧结矿强度以及还原熔滴性能影响的机理研究[D ].东北大学,2016[7] 丁祥.Fe2()3—CaO —Si ()2系铁酸钙(SFC )生成机理研究[D ].北京科技大学,2015[8] 庞建明,汪志全.Si 02对烧结矿矿相组成的影响[_!].安徽工业大学学报(自然科学版),2005 (4)[9] 邓涛,赵凯,胡长庆,王建超.M gO 对铁矿粉烧结液相生成的影响[J ].矿冶工程,2015 (1)[10] 崔利民.MgO /A 1203比对铁矿粉烧结液相生成的影响[D ].华北理工大学,2016收稿日期:2018_11_15作者简介:魏浩源(1965—),大学,工程师,现为江西晶昊盐化有限公 司石灰车间主任。
安全环保提升专项行动全面铺开近日,中国氯碱工业协会、中国纯碱工业协会、中国氮肥工业协会、中国电石工业协会、煤化工专业委员 会、石油和天然气专业委员会等先后发出通知,在氯碱、纯碱、氮肥、电石、煤化工、炼油等行业组织开展安全 环保提升专项行动,提升各行业安全环保水平。
根据各行业协会和专委会公布的工作方案,纯碱协会要求,纯碱企业要在2019年1月底前,对生产过程 中的主要危险危害因素检查。
纯碱协会将于1月中旬至月底前,据各企业自查情况、整改方案和整改计划、 自查报告,协会安全环保提升专项行动领导小组组织人员对部分企业进行抽查,进行总结并形成总结报告。
18纯碱工业1#窑体石灰石粒度:60〜120 mm ;焦炭粒度: 区及其相关区域温度的平均数值,记录时间为201820〜60 mm 。
年9月11日至9月20日。
以下是1#窑的石层高度、顶温、灰温、窑体煅烧表1 1#窑连续十天的工艺参数日期9-119-129-139-149-159-169-179-189-199-20石层高度,m 44 4. 14. 143. 93. 93. 94. 14. 1顶温,°c 108121135167154152116103131142灰温,°c656058696355706266591 200 - ___________^ 参考文献……… ----[1]李京旺,牛海涛.石灰窑结构及性能的优化设计措施I400-p rs。