正交车铣加工切削力仿真分析
机械切削力的数学建模与仿真分析
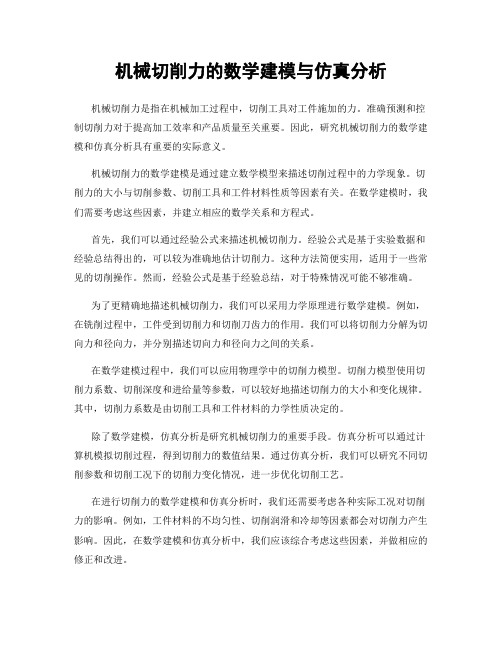
机械切削力的数学建模与仿真分析机械切削力是指在机械加工过程中,切削工具对工件施加的力。
准确预测和控制切削力对于提高加工效率和产品质量至关重要。
因此,研究机械切削力的数学建模和仿真分析具有重要的实际意义。
机械切削力的数学建模是通过建立数学模型来描述切削过程中的力学现象。
切削力的大小与切削参数、切削工具和工件材料性质等因素有关。
在数学建模时,我们需要考虑这些因素,并建立相应的数学关系和方程式。
首先,我们可以通过经验公式来描述机械切削力。
经验公式是基于实验数据和经验总结得出的,可以较为准确地估计切削力。
这种方法简便实用,适用于一些常见的切削操作。
然而,经验公式是基于经验总结,对于特殊情况可能不够准确。
为了更精确地描述机械切削力,我们可以采用力学原理进行数学建模。
例如,在铣削过程中,工件受到切削力和切削刀齿力的作用。
我们可以将切削力分解为切向力和径向力,并分别描述切向力和径向力之间的关系。
在数学建模过程中,我们可以应用物理学中的切削力模型。
切削力模型使用切削力系数、切削深度和进给量等参数,可以较好地描述切削力的大小和变化规律。
其中,切削力系数是由切削工具和工件材料的力学性质决定的。
除了数学建模,仿真分析是研究机械切削力的重要手段。
仿真分析可以通过计算机模拟切削过程,得到切削力的数值结果。
通过仿真分析,我们可以研究不同切削参数和切削工况下的切削力变化情况,进一步优化切削工艺。
在进行切削力的数学建模和仿真分析时,我们还需要考虑各种实际工况对切削力的影响。
例如,工件材料的不均匀性、切削润滑和冷却等因素都会对切削力产生影响。
因此,在数学建模和仿真分析中,我们应该综合考虑这些因素,并做相应的修正和改进。
总之,机械切削力的数学建模和仿真分析对于工业生产具有重要的意义。
通过建立准确的数学模型,我们可以预测和控制切削力,提高切削效率和产品质量。
未来,随着数学建模和仿真技术的不断发展,我们可以实现更精确、更可靠的切削力分析,推动机械加工技术的进一步发展。
切削仿真研究报告总结
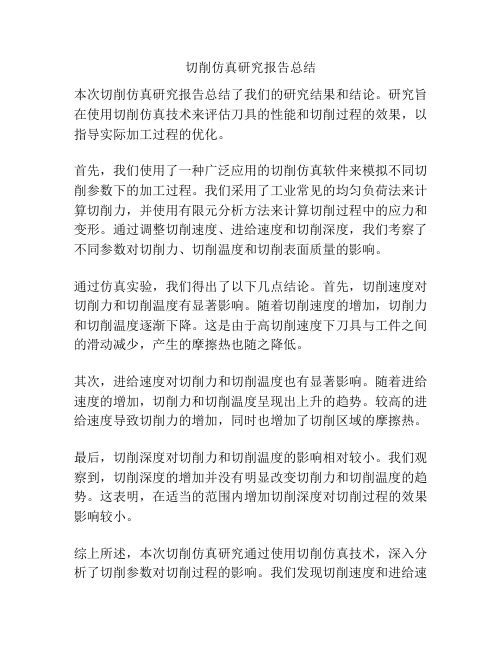
切削仿真研究报告总结
本次切削仿真研究报告总结了我们的研究结果和结论。
研究旨在使用切削仿真技术来评估刀具的性能和切削过程的效果,以指导实际加工过程的优化。
首先,我们使用了一种广泛应用的切削仿真软件来模拟不同切削参数下的加工过程。
我们采用了工业常见的均匀负荷法来计算切削力,并使用有限元分析方法来计算切削过程中的应力和变形。
通过调整切削速度、进给速度和切削深度,我们考察了不同参数对切削力、切削温度和切削表面质量的影响。
通过仿真实验,我们得出了以下几点结论。
首先,切削速度对切削力和切削温度有显著影响。
随着切削速度的增加,切削力和切削温度逐渐下降。
这是由于高切削速度下刀具与工件之间的滑动减少,产生的摩擦热也随之降低。
其次,进给速度对切削力和切削温度也有显著影响。
随着进给速度的增加,切削力和切削温度呈现出上升的趋势。
较高的进给速度导致切削力的增加,同时也增加了切削区域的摩擦热。
最后,切削深度对切削力和切削温度的影响相对较小。
我们观察到,切削深度的增加并没有明显改变切削力和切削温度的趋势。
这表明,在适当的范围内增加切削深度对切削过程的效果影响较小。
综上所述,本次切削仿真研究通过使用切削仿真技术,深入分析了切削参数对切削过程的影响。
我们发现切削速度和进给速
度对切削力和切削温度具有显著影响,而切削深度的影响相对较小。
这些结论为优化切削参数提供了指导,能够帮助提高切削效率和加工质量。
在实际应用中,我们可以根据具体工件材料和切削条件,通过合理调整切削参数来优化加工过程,并达到更好的加工效果。
二维正交铣削加工有限元仿真分析

nt lm e ta ay i s fwa eABAQUS,h a e ieee n n l ss ot r t ep p r
smul t s a a l z s he r n o he t e s i a e nd na y e t t e ds f t s r s , s r i a li g f r e o he wo k e e i he 2 t an nd miln o c ft r pic n t D miln o e s li g pr c s .The c nt a t t he c nc r d e — o r s o t o e ne x itng c t i h o y S O St r ndsa et u . s i u tng t e r H W he t e r r e Ke r : WO — di e i na iln FEAS; y wo ds t m nso lm li g; ma e i lf iu e; te sa t a n t ra al r s r s nd s r i
动 对模 拟过程 的影 响 , 且 因刀 具 锋利 而 忽 略 了后 并
0 引 言
自2 O世纪 9 O年 代 以来 , 国外 数 控铣 削 加 工 呈
刀 面对 已加工 表 面的影 响 。第 3 假设保 证 了切削 个
模 拟过程 的稳 定性 。 正 交 切 削 加 工有 限 元 模 拟模 型 如 图 1 示 , 所 在
合有 限元 分析软 件 A AQUS中材料 的 失效 与 切屑 B 分 离准则 , 拟 了二 维铣 削加 工过程 中工件 的 应 力、 模
应 变和铣 削 力的 变化 趋 势 , 与相 关切 削加 工 理 论对 比 分析 , 明其 变化 趋势是 正确 的 。 说
正交车铣三维切屑理论建模研究

正交车铣三维切屑理论建模研究朱立达;李虎;杨建宇;王宛山【摘要】Aiming at the problems of varying chip thickness and depth due to the complex motion in orthogonal turn-milling, the mathematical models of centric and eccentric chip formation were proposed based on the orthogonal turn-milling theory, respectively Consequently, the mathematical expressions of chip depth and thickness for both the circumference edge and the face edge were obtained. The theoretical model of orthogonat turn-milling chip was validated by comparing the geometric chip formation with the experimental one under the same cutting condition. The chip model may provide a theoretical foundation and reference for the research on orthogonal turn-milling mechanisms.%针对正交车铣复杂运动所产生变深度、变厚度的切屑问题,基于正交车铣切削理论建立有效的无偏心切屑和偏心切屑的数学模型,从而分别获得圆周刃、端面刃的切屑厚度和深度的数学表达式.在相同切削参数条件下,通过理论建模方法和实验测试方法分别获得三维切屑几何形状,对比分析可知,正交车铣三维切屑理论建模是正确的.因此该切屑的理论模型为正交车铣加工机理的研究提供理论基础和参考依据.【期刊名称】《东北大学学报(自然科学版)》【年(卷),期】2012(033)001【总页数】5页(P111-115)【关键词】正交车铣;三维切屑;偏心距;建模;圆周刃;端面刃【作者】朱立达;李虎;杨建宇;王宛山【作者单位】东北大学机械工程与自动化学院,辽宁沈阳110819;东北大学机械工程与自动化学院,辽宁沈阳110819;东北大学机械工程与自动化学院,辽宁沈阳110819;东北大学机械工程与自动化学院,辽宁沈阳110819【正文语种】中文【中图分类】TG5正交车铣是利用铣刀和工件同时旋转的合成运动来实现切削加工,使加工精度、加工效率等多方面达到实用要求的一种先进切削加工方法[1].其中正交车铣切屑的形状和大小,对加工中的切削力、颤振、切削温度等都有重要的影响,从而影响到工件的表面质量、刀具的使用寿命和加工效率,因此深入研究正交车铣切屑形状是非常有意义的[2-3].目前国内外一些专家和学者已对车铣切屑进行了研究,其中沈阳理工大学姜增辉等[4-5]研究比较早,也比较深入,为车铣加工研究奠定了坚实基础,但其切屑建模侧重于无偏心切屑且建模方法过于复杂;孙建业等[6]、金成哲等[7]通过实验方法对切屑形成机理进行研究,但没有进行切屑理论建模与分析;克罗地亚的Skoric 等[8]利用车铣技术对旋转工件表面加工的可行性进行了研究,提到了切屑的大致形状.Choudhury等[9]和Pogacink等[10]利用实验方法研究车铣偏心加工对表面质量的影响.本文首先基于正交切削理论采用数学方法分别建立无偏心和偏心的切屑理论模型,然后通过实验验证理论模型的正确性.1 正交车铣切屑建模铣刀轴和工件轴的相对位置称为偏心距.切屑建模主要包括圆周刃切屑厚度建模、圆周刃切屑深度建模[4]、端面刃切屑厚度建模和端面刃切屑深度建模.1.1 无偏心切屑建模轴向进给量 f a为已知切削参数,切削宽度w,如图1所示.在铣刀上建立旋转坐标系,它的Y′轴与工件上的进给螺旋线方向一致,铣刀在旋转坐标系内的转角φ′与在原坐标系内的转角φ有如下关系:铣刀中心从 O 1位置运动到 O2,每齿进给量为fz,此时工件转角为图1 正交车铣的理论切削几何模型(无偏心)Fig.1 Theoretical chip geometry with orthogonal turn-milling(centric position)式中:n1为铣刀转速;n2为工件转速;z为铣刀齿数.1)圆周刃的切屑厚度.切屑厚度的度量方向应始终与铣刀的切削速度方向垂直,铣刀圆周刃的切入角φ′pst和切出角φ′pex表达式为圆周刃切屑厚度模型如下:这里φm是h p1(φ)=h p2(φ)=h p,max(切屑厚度最大值)在时铣刀圆周刃的转角.2)端面刃的切屑深度.铣刀端面刃与工件在X-Z平面内的啮合区情况,还要参考端面刃与工件在X-Y平面内的啮合区,因此端面刃的切屑深度与圆周刃的切屑厚度密切相关,并在同一个平面上进行分析.端面切入角:端面切出角:端面刃的切屑深度可以表示为在PD′段:在PP′段:3)端面刃的切屑厚度.铣刀端面刃上任一点到铣刀旋转中心的距离r′(x(r′,φ)=r′◦cosφ),铣刀旋转一周,铣刀上任一齿端面刃切屑厚度的表达式:1.2 偏心切屑建模1)圆周刃的切屑厚度.由于切屑厚度的度量方向应始终与铣刀的切削速度方向垂直,因此,铣削厚度是由图2中通过螺旋线方向旋转变换得到的.在原坐标系中,铣刀切入角φpst和切出角φpex表达式为对于偏心正交车铣,圆周刃的切屑厚度计算公式如下:图2 正交车铣的理论切屑几何模型(偏心)Fig.2 Theoretical chip geometry with orthogonal turn-milling(eccentric position)2)端面刃的切屑深度.端面切入角为端面切出角在X轴方向上AD=f w/2,端面刃切屑深度可以表示为3)端面刃的切屑厚度.铣刀上任一齿端面刃切屑厚度的表达式:式中 x=-e-r′(φ)cosφ,因此端面刃切屑厚度表示为通过上面推导的数学表达式可分析车铣切削参数和偏心距等对圆周刃的切屑厚度和深度、端面刃的切屑厚度和深度的影响规律.2 实验验证三维切屑几何形状正交车铣加工在MORI SEIKI NT-3150车铣加工中心上,其中刀柄型号:SANDVIK C5-391 HMD-25-070;刀具型号:SANDVIK R390-020A25-11L.工件材料为铝 6061-T6(美标),直径为 40 mm.铣削方式:顺铣;冷却方式:干切削.切削参数如下:铣削主轴转速为1000 r/min;车削主轴转速为40 r/min;切削深度为2 mm;偏心距为6mm;轴向进给速度为1mm/s.通过建模与实验可以获得切屑的三维几何形状,如图3所示.图3 正交车铣三维切屑几何形状与实验形状对比Fig.3 Comparisons of 3D chip geometry and experimental ones of orthogonal turn-milling(a)—无偏心切屑三维几何形状;(b)—偏心切屑三维几何形状;(c)—无偏心切屑实验形状;(d)—偏心切屑实验形状(e=6mm).从图3可以看出,所获得的切屑厚度和深度总是变化的,即变厚度、变深度切屑.与车削切屑和铣削切屑不同,无论无偏心还是偏心的正交车铣切屑都由相互垂直且相联的两部分组成,理论建模与实验获得切屑形状上是一致的.从理论建模获得三维切屑几何形状与实验对比可知,切屑在工件分离过程中发生很大变形,尤其高速切削加工,但从整体形状上分析,正交车铣切屑建模是正确的、可行的.3 结论1)基于正交车铣加工原理对无偏心切屑和偏心切屑建模,分别获得圆周刃切屑厚度和深度、端面刃切屑厚度和深度的数学表达式以及与切削参数之间的变化规律,解决变切深、变厚度的切屑问题,为切削力和颤振等研究提供理论基础和参考依据. 2)不论偏心距多大,圆周刃和端面刃不是同时切入工件,而是同时切出工件,但圆周刃在整个切削过程中起到主导作用.通过建模与实验获得的三维切屑几何形状对比分析可知,切屑建模方法是可行的、正确的.在实验条件允许的情况下,通过切削力测量分析切屑形状,对理论模型的验证更有说服力.参考文献:[1]Savas V,Ozay C.Analysis of the surface roughness of tangential turn-milling for machining with end milling cutter[J].Jour nal of Materials Processing Technology,2007,186:279-283.[2]Nikhil D,Prakash K,Satish K.Automated process planning method to machine a B-spline free-form feature on a mill-turn center[J].Computers&Industr ial Engineer ing,2009,56(1):198-207.[3]Savas V,Ozay C.The optimization of the surface roughness in the process of tangential turn-milling using genetic algorithm[J].International Journal of Advanced Manufacture Technology,2008,37:335-340.[4]姜增辉,贾春德.无偏心正交车铣理论切削力[J].机械工程学报,2006(9):23-27.(Jiang Zeng-hui,Jia Chun-de.Theoretical cutting force of non-eccentricity orthogonal turn-milling[J].Chinese Jour nal of Mechanical Engineering,2006(9):23-27.)[5]姜增辉,贾春德.正交车铣切屑仿真的研究[J].兵工学报,2002(11):525-528.(Jiang Zeng-hui,Jia Chun-de.A study on the emulation of orthogonal turn-milling chips[J].Acta Ar mamentarii,2002(11):525-528.)[6]孙建业,马骏.车铣复合加工的切屑形态分析[J].制造技术与机床,2009(12):72-74.(Sun Jian-ye,Ma Jun.Analysis of chip shape in turn-millingmachining[J].Manufacturing Technology&Machine Tool,2009(12):72-74.) [7]金成哲,贾春德.正交车铣高强度钢切屑形成机理的研究[J].哈尔滨工业大学学报,2006,38(9):1610-1612.(Jin Cheng-zhe,Jia Chun-de.Research on mechanism of chip formationin orthogonal turn-milling high strengthsteel[J].Journal of Harbin Institute of Technology,2006,38(9):1610-1612.) [8]Skoric S,Udiljak T,Ciglar D.Study of the suitability of the machining of rotating surfaces[J].Transactions of Famena,2008,32(2):69-83.[9]Choudhury SK,Bajpai JB.Investigation in orthogonal turnmilling towards better surface finish[J].Jour nal of Mater ials ProcessingTechnology,2005,170(3):487-493.[10]Pogacink M,Kopac J.Dynamic stabilization of the turnmilling process by parameter optimization[J].Journal of Engineering Manufacture,2000,214(2):127-135.。
正交切削加工过程仿真

Z N ia ,Q u qu , HA G G oh n HE G Xj n i IZ o i Z N uzo g
( .S h o o Me h n a E g 1 c ol f c a i l n .& A t ai , otes r nv ,S e y g 10 1 ,C ia c u m t n N r at n U i. h n a 10 4 h ; o o h e n n
选择 及 实际的切 削加 工提供指 导.
关键词 : 交切 削 ; 限元 ; 削应 力 ; E O M 正 有 切 DFR
中图分类 号 : H13 2 T 15 T 2.; B 1; 9 . 19 文 献标 志码 : A
S m u a i n o r c s l o t o o a u tn  ̄ i l t n o o e s O。 r ’ g n lc ti g n0 ‘ n lt
维普资讯
第1 6卷 第 4期
20 0 7年 1 2月
计 算 机 辅 助 工 程
C0M PUTER DED A .
De . 2 0 c 07
文章 编 号 :0 6—0 7 (0 7 0 -0 00 10 8 1 20 )40 4 -3
第300步漏度口羹誓图5切削力随刀具行程的变化曲线253切削加工的应力仿真实际切削加工过程中由于切削层金属在挤压条件下实现切削层与工件的分离会形成很强的塑性变形应力场和温度场工件表层的受热受挤压部分图4切削过程中工件及切削的温度分布云图从图4可见最高温度分布在刀具刚刚经过的伸长但受其他未加热和未挤压部分阻止不能伸长切削面以及前刀面与切削接触的部分这主要是由产生压应力
能. 有限元 方法在 切削工 艺 中的应 用表 明 , 切削工艺 和切 削形成 的有 限元 模拟 对 了解 切削机理 及 切削 的 形成等 有很大 帮助
切削加工过程的仿真方法研究与实现

切削加工过程的仿真方法研究与实现切削加工过程是制造行业中非常重要的一部分,它可以使用许多不同的切削工具和切削方法实现产品的制造,但是,切削加工的过程十分复杂,如何保证产品的质量和精度是制造行业面临的一个重大挑战。
为了解决这个问题,人们发展出了仿真切削加工过程的技术,从而获取更准确的加工参数和精度。
以往,对于切削加工过程的仿真都是采用数学模型的方法,例如切削力学的模型,磨削模型和热磨削模型等等。
这些模型往往是简单的,包括固定参数的方程,但是它也不能完全准确预测实际加工过程中发生的情况。
为此,最近几十年来,仿真切削加工过程的方法已经发展迅速,研究者利用复杂的数字技术来模拟实际加工过程。
本文将着重介绍仿真切削加工过程的方法研究及其实现。
首先,本文介绍仿真切削加工过程的目的,即精确预测切削过程中的参数和精度。
为了实现这一目的,必须采用复杂的数字技术来模拟加工过程中发生的一切。
具体而言,研究者采用计算机辅助设计(CAD)和数字辅助设计(CAM)技术来模拟机床切削过程中发生的一切,比如切削力、温度和振动等。
另外,采用有限元分析技术(FEA)可以准确地计算切削过程中的动力学性能和热传递性能,用来精确预测加工结果。
此外,在切削加工仿真系统中,还可以使用模拟软件来模拟切削工具的刃的运动状态。
使用模拟软件,可以准确地分析切削工具的偏转和漂移,以及刃的振动和腐蚀状况,可以提供更准确的参数和精度。
最后,介绍切削加工过程中使用的数字技术,包括数字控制系统、数控机床和虚拟机床。
数控机床是用于实现数字控制机床加工过程的硬件设备,它可以使用各种控制算法和参数来控制机床的加工过程。
虚拟机床是可以在计算机上仿真的机床,它可以用来模拟切削加工过程中的各种参数,以及改进机床的加工精度。
总之,本文介绍了仿真切削加工过程的方法研究和实现,以精确预测切削加工的参数和精度。
通过使用计算机辅助设计、有限元分析和模拟软件等数字技术,可以准确地模拟出加工过程中发生的一切,确保产品的质量和精度。
机械工程中的切削力仿真分析

机械工程中的切削力仿真分析机械加工过程中,切削力是一个非常重要的物理量,它的大小和方向会直接影响到加工精度和工件表面质量。
然而,在实际加工过程中,切削力是很难直接测量的,所以需要通过仿真分析的方法来预估切削力的大小和方向。
本文将探讨机械工程中的切削力仿真分析方法及其应用。
1.切削力的来源在机械加工中,切削力主要来自于以下几方面的因素:(1)切削区的物理特征:包括切削区的切削角、切削深度、进给量等几何参数,以及刀具和工件材料的硬度、强度等物理特性。
(2)加工参数:如刀具的锋角和后角、材料的切削速度、进给速度和切削深度,以及加工冷却液的流量和压力等。
(3)机床和刀具状况:机床和刀具的刚性、精度和磨损等因素也会对切削力产生影响。
2.切削力的计算方法切削力的计算方法主要分为经验公式法和数值仿真法两种。
其中,经验公式法主要是通过根据历史数据和经验关系来推导计算公式,一般适用于简单的加工过程和较为常见的材料;数值仿真法则是通过建立切削过程的物理模型来进行计算和分析,可以较为准确地预测切削力的大小和方向,适用于较为复杂的加工过程和材料。
数值仿真法主要分为有限元法和边界元法两种。
其中,有限元法是通过将加工过程抽象为一个有限元模型,在这个模型中计算力学变量的变化,来预测切削力的大小和方向;而边界元法则是通过在加工区域的表面上定义边界条件和切割区,并在此基础上计算力的分布,来预测切削力的大小和方向。
3.切削力仿真在机械工程中的应用切削力仿真在机械工程中有着广泛的应用,下面列举几个代表性的应用场景:(1) 优化加工参数:通过切削力仿真,可以预测不同加工参数下的切削力变化规律,寻找最优的加工参数组合,从而提高加工效率和加工质量。
(2) 帮助工艺设计:通过切削力仿真,可以较为准确地预测加工过程中的力和应力分布情况,帮助设计师对工艺进行合理设计,提高工件的稳定性和可靠性。
(3) 优化机床结构:通过切削力仿真,可以了解不同机床设计的刚性和精度,寻找最优的机床结构和机床参数组合,提高机床的性能和可靠性。
CFRP铣削有限元模型建立及切削力仿真分析
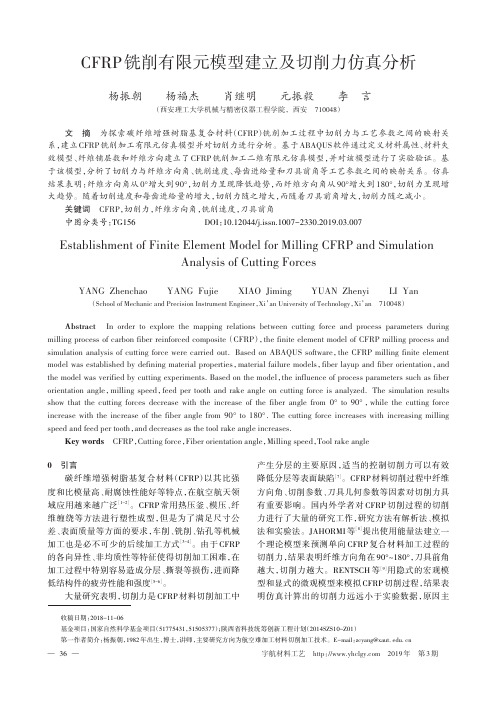
CFRP铣削有限元模型建立及切削力仿真分析杨振朝杨福杰肖继明元振毅李言(西安理工大学机械与精密仪器工程学院,西安710048)文摘为探索碳纤维增强树脂基复合材料(CFRP)铣削加工过程中切削力与工艺参数之间的映射关系,建立CFRP铣削加工有限元仿真模型并对切削力进行分析。
基于ABAQUS软件通过定义材料属性、材料失效模型、纤维铺层数和纤维方向建立了CFRP铣削加工二维有限元仿真模型,并对该模型进行了实验验证。
基于该模型,分析了切削力与纤维方向角、铣削速度、每齿进给量和刀具前角等工艺参数之间的映射关系。
仿真结果表明:纤维方向角从0°增大到90°,切削力呈现降低趋势,而纤维方向角从90°增大到180°,切削力呈现增大趋势。
随着切削速度和每齿进给量的增大,切削力随之增大,而随着刀具前角增大,切削力随之减小。
关键词CFRP,切削力,纤维方向角,铣削速度,刀具前角中图分类号:TG156DOI:10.12044/j.issn.1007-2330.2019.03.007 Establishment of Finite Element Model for Milling CFRP and SimulationAnalysis of Cutting ForcesYANG Zhenchao YANG Fujie XIAO Jiming YUAN Zhenyi LI Yan (School of Mechanic and Precision Instrument Engineer,Xi’an University of Technology,Xi’an710048)Abstract In order to explore the mapping relations between cutting force and process parameters during milling process of carbon fiber reinforced composite(CFRP),the finite element model of CFRP milling process and simulation analysis of cutting force were carried out.Based on ABAQUS software,the CFRP milling finite element model was established by defining material properties,material failure models,fiber layup and fiber orientation,and the model was verified by cutting experiments.Based on the model,the influence of process parameters such as fiber orientation angle,milling speed,feed per tooth and rake angle on cutting force is analyzed.The simulation results show that the cutting forces decrease with the increase of the fiber angle from0°to90°,while the cutting force increase with the increase of the fiber angle from90°to180°.The cutting force increases with increasing milling speed and feed per tooth,and decreases as the tool rake angle increases.Key words CFRP,Cutting force,Fiber orientation angle,Milling speed,Tool rake angle0引言碳纤维增强树脂基复合材料(CFRP)以其比强度和比模量高、耐腐蚀性能好等特点,在航空航天领域应用越来越广泛[1-2]。
- 1、下载文档前请自行甄别文档内容的完整性,平台不提供额外的编辑、内容补充、找答案等附加服务。
- 2、"仅部分预览"的文档,不可在线预览部分如存在完整性等问题,可反馈申请退款(可完整预览的文档不适用该条件!)。
- 3、如文档侵犯您的权益,请联系客服反馈,我们会尽快为您处理(人工客服工作时间:9:00-18:30)。
20 12年 4 月
兵 ห้องสมุดไป่ตู้
工
学
报
Vo . NO 4 1 33 . Apr . 2 2 01
ACTA ARMAM ENTARI I
正 交车铣加工切 削力仿真分析
朱 立 达 ,于天 彪 ,王 宛 山
( 北 大 学 机械 工 程 与 自动 化 学 院 ,辽 宁 沈 阳 10 0 东 104)
关键 词 :刀具技 术 ;正 交车铣 ; 削力 ;偏心 ; 模 切 建 中图分类 号 : P 9 T 31 文献 标 志码 :A 文章 编号 : 0 01 9 (0 2 0 -4 90 1 0 —0 3 2 1 ) 40 1 -6
S m ul to o i a i n f r Cuti r e o r ho o lTur m i i g tng Fo c f O t g na n・ l n l
i g p o e s h h o ei a d lo u t o c s fun e y u i ah mai t o a e n t e n r c s ,t e t e r t lmo e fc ti fr e i o d d b sng m t e t me h d b s d o h c ng c m a h n n rn i e,a d t e c a e r lso u t o c swih t oa in a g e fc t rwe e smu a c i i g p i cpl n h h ng u e fc ti f r e t her t t n lso u t r i l - ng o e t d i h o i o swi n t o c e ti i e n t e c nd t n t a d wih ute c n rct i h y,r s e tv l . T i l t n r s ls s o t t e p cie y he smu a i e u t h w ha ,wi o t h t e i c e s ff e ae a d e c nrct h n r a e o d r t n c e tiiy,t e c ti g fr e i r a e n t e s m e c ti g p r me e sa d i e h u tn o c nc e s si h a u tn a a tr n t i g e n e c n rc t h n t a n n n—c e tii sbig ri c e tii t a h ti o e c n rc t Th r f r t h o eia u t oc o e r ・ y y. e eo e, he t e r tc lc ti fr e m d lp o ng v d s r fr n e f rt e r s ac n o t o o a u n mil g me h n s . i e e e e c o h e e r h o rh g n lt r — li c a im n
Key w or ds:c ti g t o e h oo y;o t o o a u n m i i g; c ti g f r e;e c n rct u tn o ltc n lg rh g n lt r - l n l u tn o c c e tii y;mo e ig dl n
ZHU Lid — a,YU a bio, W ANG a s a Tin— a W n-h n
( c o l fMe h nc lE gn eiga d A tmain,Not esen U ies y h n a g 1 0 0 S h o o c a ia n ie r n uo t n o r a tr nv ri ,S e y n 1 0 4,La nn ,C ia h t io ig hn )
0 引 言
正交车 铣是 利用 铣刀 和工 件 同时旋 转 的合 成 运
动 来 实现切 削加 工 , 加工 精度 、 使 加工 效 率等 多方 面 达 到实 用要 求 的一种 先进切 削加 工 方法 ¨ 。其 中 正 交 车铣切 削力 对加 工 中的切 削振 动 、 削效 率 、 切 切
Abs r c :Ai d a h ha a trsi so a ib e c tn e t n h c n s n t rh g n lt r mil ta t me tt e c r c e itc fv ra l ut g d p h a d t i k e si heo t o o a u n— l— i
摘要 :针对 正交 车铣 加工 变深度 、 变厚度 的切 削特 性 , 于其 加工 原理采 用 数 学方 法建 立 切 削 基 力的理论 模 型 , 在无偏 心 和偏 心二 种情况 下分 别 仿 真 圆周 刃和 端 面 刃 的切 削力 随 铣 刀 转角 的 变 并 化 规律 。通过 切 削参 数对切 削力 影 响规律 的仿 真结 果 分析 表 明, 圆周 刃在 整个 切 削过 程 中起 到 主 导作用 ; 在相 同切 削参 数条 件下 , 着进 给量和 偏心 距 的增大 , 削力增 大 , 随 切 而偏 心切 削力大 于无偏 心 切 削力 。 因此该 切 削力 的理论 模 型为 正交 车铣加 工机 理 的研 究提供 理论基 础和 参考 依据 。
究奠 定 了坚实 基础 , 但其侧 重 于无偏 心切 削力 ; 周敏 等 以次摆 线 运 动 轨迹 研 究 微 小 型 正 交 车 铣 单 齿 圆周 刃理 论 切 削 力 ; k r S oi c等 利 用 车 铣 技 术 对 旋