简介CAE分析技术在铸造生产中的应用
浅谈铸造CAE技术的发展与应用
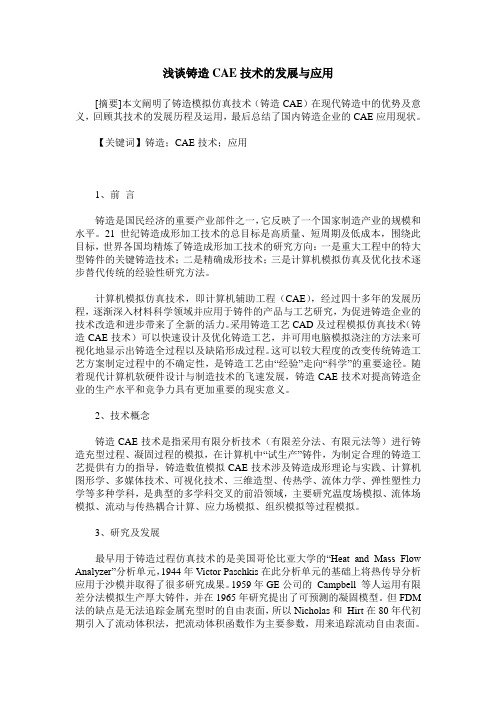
浅谈铸造CAE技术的发展与应用[摘要]本文阐明了铸造模拟仿真技术(铸造CAE)在现代铸造中的优势及意义,回顾其技术的发展历程及运用,最后总结了国内铸造企业的CAE应用现状。
【关键词】铸造;CAE技术;应用1、前言铸造是国民经济的重要产业部件之一,它反映了一个国家制造产业的规模和水平。
21世纪铸造成形加工技术的总目标是高质量、短周期及低成本,围绕此目标,世界各国均精炼了铸造成形加工技术的研究方向:一是重大工程中的特大型铸件的关键铸造技术;二是精确成形技术;三是计算机模拟仿真及优化技术逐步替代传统的经验性研究方法。
计算机模拟仿真技术,即计算机辅助工程(CAE),经过四十多年的发展历程,逐渐深入材料科学领域并应用于铸件的产品与工艺研究,为促进铸造企业的技术改造和进步带来了全新的活力。
采用铸造工艺CAD及过程模拟仿真技术(铸造CAE技术)可以快速设计及优化铸造工艺,并可用电脑模拟浇注的方法来可视化地显示出铸造全过程以及缺陷形成过程。
这可以较大程度的改变传统铸造工艺方案制定过程中的不确定性,是铸造工艺由“经验”走向“科学”的重要途径。
随着现代计算机软硬件设计与制造技术的飞速发展,铸造CAE技术对提高铸造企业的生产水平和竞争力具有更加重要的现实意义。
2、技术概念铸造CAE技术是指采用有限分析技术(有限差分法、有限元法等)进行铸造充型过程、凝固过程的模拟,在计算机中“试生产”铸件,为制定合理的铸造工艺提供有力的指导,铸造数值模拟CAE技术涉及铸造成形理论与实践、计算机图形学、多媒体技术、可视化技术、三维造型、传热学、流体力学、弹性塑性力学等多种学科,是典型的多学科交叉的前沿领域,主要研究温度场模拟、流体场模拟、流动与传热耦合计算、应力场模拟、组织模拟等过程模拟。
3、研究及发展最早用于铸造过程仿真技术的是美国哥伦比亚大学的“Heat and Mass Flow Analyzer”分析单元,1944年Victor Paschkis在此分析单元的基础上将热传导分析应用于沙模并取得了很多研究成果。
CAE技术指导优化铸造钢材质和性能
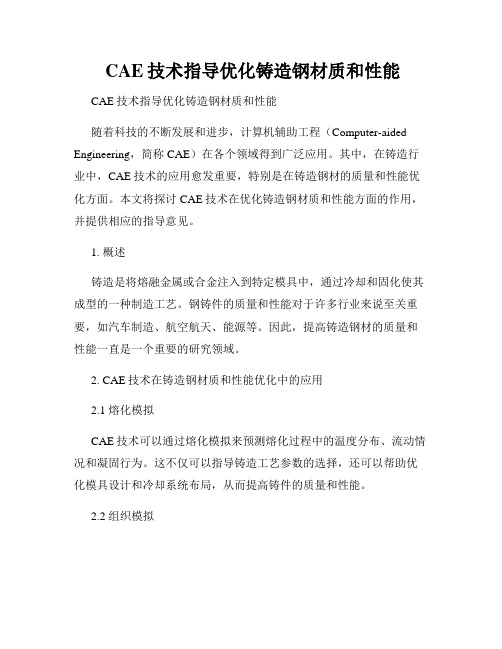
CAE技术指导优化铸造钢材质和性能CAE技术指导优化铸造钢材质和性能随着科技的不断发展和进步,计算机辅助工程(Computer-aided Engineering,简称CAE)在各个领域得到广泛应用。
其中,在铸造行业中,CAE技术的应用愈发重要,特别是在铸造钢材的质量和性能优化方面。
本文将探讨CAE技术在优化铸造钢材质和性能方面的作用,并提供相应的指导意见。
1. 概述铸造是将熔融金属或合金注入到特定模具中,通过冷却和固化使其成型的一种制造工艺。
钢铸件的质量和性能对于许多行业来说至关重要,如汽车制造、航空航天、能源等。
因此,提高铸造钢材的质量和性能一直是一个重要的研究领域。
2. CAE技术在铸造钢材质和性能优化中的应用2.1 熔化模拟CAE技术可以通过熔化模拟来预测熔化过程中的温度分布、流动情况和凝固行为。
这不仅可以指导铸造工艺参数的选择,还可以帮助优化模具设计和冷却系统布局,从而提高铸件的质量和性能。
2.2 组织模拟通过CAE技术进行组织模拟可以模拟钢铸件的凝固过程和组织形成。
这有助于预测铸造钢材的晶粒尺寸、相组成和组织均匀性等方面的参数,从而指导铸造工艺控制和材料优化。
2.3 应力和变形模拟铸造钢材在冷却和固化过程中会受到热应力和冷却收缩等因素的影响,可能导致铸件产生变形和应力集中。
CAE技术可以用于模拟这些因素对铸造钢材质和性能的影响,通过优化工艺和材料选择,减少铸件的变形和应力集中,提高铸件的质量和性能。
3. CAE技术的指导意见3.1 工艺参数优化通过CAE技术的应用,可以分析和模拟不同工艺参数对铸造钢材质和性能的影响。
在具体的铸造过程中,可以根据模拟结果选择合适的工艺参数,如浇注温度、浇注速度、冷却时间等,以优化铸件的质量和性能。
3.2 模具设计和冷却系统优化CAE技术可以模拟铸造过程中的温度分布和流动情况,从而指导模具设计和冷却系统的优化。
通过合理设计模具结构和布局冷却系统,可以均匀降低铸件温度梯度,减少组织偏差,提高材料的稳定性和性能。
CAD、CAM、CAE在铸造过程中的应用

!"# $ !"% $ !"& 在铸造工程中的应用
第三章 !"# $ !"% $ !"& 在 铸造工程中的应用
计算机技术的飞速发展, 已使计算机成为自电力发明以来最具生产潜力的工具。 、 计算机辅助工程分析 数字化时代正一步步向我们走来。计算机辅助设计 ( !"#) (!"%) 、 计算机辅助制造 (!"&) 等技术在铸造领域得到了广泛的应用, 并已成为铸造 学科的技术前沿和最为活跃的研究领域。只要将铸件图样、 铸型材料、 铸造合金热物 性参数、 凝固特性及数学模型等输入计算机, 即可计算出合理的浇冒口系统。运用相 应的数值模拟技术可对设计的工艺进行屏幕试浇, 模拟铸件凝固过程, 预测凝固缺 陷、 微观组织、 残余应力; 再利用先进的图像显示技术对屏幕试浇结果作逼真的三维 图像显示, 对缺陷位置、 程度进行全面的评估, 从而提出工艺改进措施, 进行新一轮工 艺设计优化、 屏幕试浇、 工艺校核。随着这一技术的逐渐成熟和实用化, 其应用已不 仅仅局限于对成形铸件进行工艺分析和评判, 研究人员已将其作为实现并行工程环 境下产品的虚拟制造的一个关键技术, 同计算机辅助产品设计、 计算机辅助加工工艺 规划、 计算机辅助制造集成在一起, 以达到从全局出发, 优化产品设计、 提高产品质 量、 缩短制造周期的目的。即产品设计不仅考虑产品的功能, 同时考虑产品的可制造 性。 众所周知, 铸造工艺是非常复杂的, 并具有显著的与生产实际经验紧密结合的特 点。同时, 人们也最先开始研究计算机辅助设计技术在这一领域的应用。多年的研 结 究和开发应用经验表明, 铸造工艺 !"# 软件必须在通用工艺参数设计的基础上, 合企业的具体情况开发应用才能收到好的效果。本章首先以铸钢件铸造工艺设计问 题为例, 介绍如何把传统的工艺设计问题转化为计算机辅助设计。在铸造工装设计 方面, 以介绍现代模具设计制造技术为重点。最后, 介绍并行工程的基本技术及其在 铸造工程中的应用。
廖敦明 华铸CAE及其在实际生产中的应用 for 百铸网

修改设计
铸钢件应用实例1
新解决方案
其它工艺控制建议:
• 使用合理的浇注速度 • 控制实际的浇注温度 • 合理的落砂时间 • 合适的铸型刚度
模拟结果显示,新的工艺能够保证凝固过程中收缩平衡性,也 改善了内部的组织性能,有效的降低了裂纹出现的可能性。 用户已经采用该方案进行了实际的浇注,浇注件测试结果未 发现裂纹缺陷。
铸造CAE技术简介
概述
CAE技术又称数值模拟仿真技术, 是对研究对象(过程)进行数值建 模、分析求解、预测趋势。
铸造CAE
z针对铸造过程,建立数学模型,采用 科学合理的求解方式,来描述铸件的 生产过程,预测缺陷、优化工艺
2013/9/6
铸造CAE技术简介
z 数值模拟技术已成为人们研究、开发铸造技 术的重要工具。
应力分析
原方案
应力预测与裂纹缺陷分析
通过应力预测,发现底部 有应力集中现象。同时, 由于铸件的内部组织的致 密度强度问题,底部容易 出现裂纹缺陷
61
铸钢件应用实例1
工艺修改说明
新解决方案
初始设计
1: 浇注系统修改
修改设计
2013/9/6
铸钢件应用实例1
通过华铸CAE准确模拟功能,找到了裂纹出 现的原因,并制定了一系列的解决方案。
2013/9/6
华铸软件中心
•1983年开始铸造数值模拟研究,30多年的历史。 •目前,在职教授博导、副教授、讲师、工程师 10余人,博士、硕士40余人。 •全国最大的铸造模拟技术研发中心之一。 •材料成形及模具技术国家重点实验室的重要方向 •材料加工工程国家重点学科的重要方向。
华铸系列软件产品
拥有的自主知识产权的商品化系统:
华铸CAE 及其 在实际 生产中的应用
CAE仿真指导优化铸造关键工艺参数设计
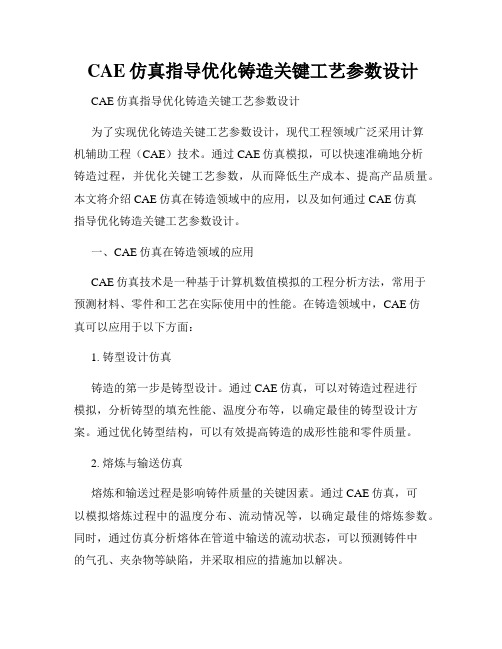
CAE仿真指导优化铸造关键工艺参数设计CAE仿真指导优化铸造关键工艺参数设计为了实现优化铸造关键工艺参数设计,现代工程领域广泛采用计算机辅助工程(CAE)技术。
通过CAE仿真模拟,可以快速准确地分析铸造过程,并优化关键工艺参数,从而降低生产成本、提高产品质量。
本文将介绍CAE仿真在铸造领域中的应用,以及如何通过CAE仿真指导优化铸造关键工艺参数设计。
一、CAE仿真在铸造领域的应用CAE仿真技术是一种基于计算机数值模拟的工程分析方法,常用于预测材料、零件和工艺在实际使用中的性能。
在铸造领域中,CAE仿真可以应用于以下方面:1. 铸型设计仿真铸造的第一步是铸型设计。
通过CAE仿真,可以对铸造过程进行模拟,分析铸型的填充性能、温度分布等,以确定最佳的铸型设计方案。
通过优化铸型结构,可以有效提高铸造的成形性能和零件质量。
2. 熔炼与输送仿真熔炼和输送过程是影响铸件质量的关键因素。
通过CAE仿真,可以模拟熔炼过程中的温度分布、流动情况等,以确定最佳的熔炼参数。
同时,通过仿真分析熔体在管道中输送的流动状态,可以预测铸件中的气孔、夹杂物等缺陷,并采取相应的措施加以解决。
3. 铸造工艺仿真铸造工艺参数对铸件质量起着决定性作用。
通过CAE仿真,可以模拟铸造过程中的铸件填充、凝固过程,分析温度变化、应力分布等,以指导优化铸造工艺参数的设计。
通过合理调整工艺参数,可以降低缺陷率、提高产品质量。
二、CAE仿真指导优化铸造关键工艺参数设计的方法实施CAE仿真指导优化铸造关键工艺参数设计,需要遵循以下步骤:1. 确定铸造关键工艺参数根据具体铸造工艺的特点,确定需要优化的关键工艺参数,例如铸型温度、浇注速度、浇注温度等。
2. 建立仿真模型基于CAE软件,建立铸造过程的仿真模型。
包括铸型结构、材料性质、初始条件等。
3. 设置边界条件根据实际情况,设置仿真模型的边界条件,如环境温度、初始温度、填充时间等。
4. 进行仿真分析运行仿真模型,进行铸造工艺的仿真分析。
CAE技术实现先进铸造设备的远程智能监控

CAE技术实现先进铸造设备的远程智能监控CAE技术实现先进铸造设备的远程智能监控随着科技的发展,先进铸造设备的远程智能监控引起了人们的广泛关注。
在传统的铸造过程中,操作员需要亲身前往设备现场进行监测和控制,不仅费时费力,而且存在一定的安全隐患。
而借助于计算机辅助工程(Computer-Aided Engineering, CAE)技术,可以实现铸造设备的远程智能监控,提高生产效率、降低生产成本、提升产品质量和生产安全。
一、CAE技术概述CAE技术是指利用计算机辅助进行工程分析和设计的一种方法。
它通过数值模拟、计算机仿真等手段,实现对物理过程的预测、优化和控制。
在铸造领域,CAE技术可以模拟铸造过程中的流体力学、传热学、固相变形学等物理现象,帮助工程师更好地理解和控制铸造过程。
二、远程智能监控的意义远程智能监控是指通过远程控制和监测设备,在不同的时间和空间,实现对先进铸造设备的操作和管理。
它可以提供实时数据、检测设备状态和故障预警等功能,有效地提高了生产效率和设备利用率。
远程智能监控还可以减少人为因素对铸造过程的干扰,提高产品质量和生产安全。
三、CAE技术在远程智能监控中的应用1. 数值模拟与优化通过CAE技术,可以对铸造设备进行数值模拟,预测和优化铸造过程中的温度、流速、气流等参数。
同时,借助于优化算法,可以寻找最佳的工艺参数组合,提高铸件的成形质量和机械性能。
这些模拟和优化结果可以通过远程智能监控系统进行实时更新和传输,为操作员提供及时的参考和决策依据。
2. 传感器与数据采集远程智能监控系统通过传感器可以实时采集铸造设备的工作状态和环境参数,如温度、压力、振动等。
这些数据经过采集、处理和传输后,可以在远程终端进行监测和分析。
在发生异常或故障时,系统可以通过警报和预警信息通知操作员,及时采取措施,减少停机时间,提高生产效率。
3. 远程控制与故障诊断在远程智能监控系统中,操作员可以通过终端设备远程控制铸造设备的开关、运行状态等。
CAD CAE CAM 在铸造成型中的应用

12
3.Pro-CAST分析模块
① ② ③ ④ ⑤ ⑥ ⑦ ⑧
它主要由八个模块组成: 有限元网格划分MeshCAST基本模块 传热分析及前后处理Base License 流动分析Fluid flow 应力分析Stress 热辐射分析Rediation 显微组织分析Micromodel 电磁感应分析Electromagnetics 反向求解Inverse
CAD/CAE/CAM 在铸造成型中的应用
1
主要内容
铸造工艺概述
铸造CAD/CAE/CAM
应用举例—Pro-CAST
2
1.铸造工艺概述
1)、铸造生产工艺:
将金属熔炼成具有一定化学成分、一定温度 的液态金属,在重力场或外力场(压力或离心力 等)的作用下,浇注到具有一定几何形状、尺寸 大小的铸型型腔中,待液态金属结晶、凝固并冷 却到一定温度后,从铸型型腔中取出,经过清理、 切除浇冒口而获得铸件。
②
流体分析模块:
流体分析模块可以模拟所有包括充型在内的液体 和固体流动的效应。Pro-cast通过完全的 Navier-Stocks流动方程对流体流动和传热进行耦 合计算。本模块中还包括非牛顿流体的分析计算。 此外,流动分析可以模拟紊流、触变行为及多孔 介质流动(如过滤网),也可以模拟注塑过程。7来自2)铸件凝固过程CAE
在加工铸造模具和投入实际铸件生产之前,利用 计算机对铸件充型凝固过程进行模拟计算,预测 其缺陷所在,以便优化工艺设计。 研究内容: 铸件充型凝固过程的数值模拟及疏松、缩孔预测、 应力分析、微观组织模拟等方面。
8
3)铸造模具CAM
利用计算机对铸造模具的制造进行设计、监督、 控制和管理
9
3.应用举例—Pro-CAST
铸造CAE及其应用

8.3.2冒口系统CAD
冒口是消除缩孔等缺陷获得致密铸件的基本措施。冒口C AD的主要内容是采用计算机完成冒口数量及尺寸的确 定及计算,冒口形状及位置可以采用人机对话方式, 由操作者来确定。冒口尺寸的计算方法较多,有模数 法,比例法、补缩液量法、三次方程法,点模数法, 点热阻法,模数梯度法等。此节仅介绍三类,它们是简单形 体、等截面单元体、回转单元体和不规则形状单元体。
1)简单形体的体积和表面积
简单形体是指那些体积和表面积能用现成的公式计算的 一类几何体。如球、长方体、圆柱体,圆台等。计算 这类几何体的体积和表面积,只要输入该几何体的形 状特征尺寸即可。
2)等截面单元体的体积和表面积
2)测试样杯
样杯一般多采用树脂砂、合脂砂或油砂制成。其壁厚应使 之具有合适的冷却速度和足够的强度。样杯的内型尺寸 决定了铁液的容积即试样的大小。
3) A/D转换器和信号放大器
由于热电偶传感器产生的模拟信号为毫伏级,普通微型 计算机能够处理的是伏特级的数字信号,所以热电偶信 号必须进行放大和A/D转换。
8.1.1建立内节点差分方程
1.一维系统 所谓“节点”,就是在一个相当小的区域内,其性质相
差很小,可由其中的某一点来代表,这点就称为“节 点”,可以认为节点温度就是此区域( 范围内)各点 的平均温度。“内节点”,即与界面不相邻的节点。 假设铸件为长、宽无限(即长、宽方向无热流),
2.二维系统
3.凝固潜热的处理
金属凝固释放结晶潜热,使铸件温度下降速度减慢。 因此,在计算时必须把潜热的作用考虑进去。下面介 绍几种处理的方法。
(1)等价比热容法
等价比热容法是将凝固潜热折合成比热容,与铸件比
热容之和作为等价比热容cE 在计算中应用。
- 1、下载文档前请自行甄别文档内容的完整性,平台不提供额外的编辑、内容补充、找答案等附加服务。
- 2、"仅部分预览"的文档,不可在线预览部分如存在完整性等问题,可反馈申请退款(可完整预览的文档不适用该条件!)。
- 3、如文档侵犯您的权益,请联系客服反馈,我们会尽快为您处理(人工客服工作时间:9:00-18:30)。
简介CAE分析技术在铸造生产中的应用
摘要: 近年来,计算机铸造工艺模拟软件开始被大多数铸造工厂所接受,应用这些软件可以较为准确的预测各种铸造缺陷,优化浇注系统设计、消除热裂等裂纹缺陷、提高工艺出品率。
本文介绍了应用ProCAST软件在实际铸造工艺优化设计中的一些实例,应用表明该软件能准确的预测铸件的多种铸造缺陷,有利于铸造工艺的优化和铸件的质量提高。
关键词: ProCAST CAE 数值模拟铸造
1 引言
铸造是国民经济的重要产业部件之一,它反映了一个国家制造工业的规模和水平。
随着航空、航天、船舶、汽车、机械等各行业的蓬勃发展,铸件的需求量越来越大,对铸造金属的性能及铸件本身的可靠性等要求越来越高。
先进制造技术的发展,要求铸件的生产向轻型化、精确化、强韧化、复合化及无环境污染方向发展。
计算机技术的飞速发展及其在铸造生产中的广泛应用,可以通过对制造工艺过程进行数值模拟及仿真,使得上述目标得以实现。
这项工作以数值计算为基本方法,对铸造过程中流场、温度场、应力场及微观组织形貌进行模拟,从而帮助工艺设计人员对不同时刻的金属流态、凝固过程温度分布、应力分布、结晶晶粒尺寸形貌等重要物理参数有所了解,并以此为依据,预测是否有缩孔、疏松、夹杂、偏析及热裂纹等缺陷出现,可以实现铸造工艺设计——校核——再设计——优化设计的全过程,以提高铸件质量,缩短试制周期,降低生产成本,提高市场竟争能力。
同时,用计算机等高新技术来改造制造传统产业是国内外科学技术发展的共同趋势,是铸造领域的学科前沿,也是铸造工艺由“经验设计”走向“科学指导”的重要途径,具有重大的实际意义。
图1展示了铸件工艺优化的整个流程。
2 ProCAST软件介绍
近年来,铸造CAE商品化软件功能逐渐增加,其中主要有美国的ProCAST、德国的MAGMASOFT、芬兰的CastCAE、法国的Simulor、西班牙的Forcast及日本的Soldia、Castem 等软件。
从功能上看,许多软件大都基于有限差分法,可以对砂型铸造、金属型铸造、精密铸造、压力铸造等多种工艺进行温度场、流场的数值模拟,并可以预测铸件的缩孔、缩松等缺陷,但对应力场的模拟及裂纹的预测显得力不从心。
ProCAST软件是由ESI公司开发的基于有限元法(FEM)的铸造过程模拟软件,能够进行流场、温度场、应力场三场耦合模拟。
ProCAST采用基于有限元法(FEM)的数值计算方法,与有限差分法(FDM)相比,有限元法具有较大的灵活性,特别适用于模拟复杂铸件成型过程中的各种物理现象。
ProCAST提供了能够考虑气体、过滤、高压、旋转等对铸件充型的影响,能够模拟出低压铸造、压力铸造、离心铸造等几乎所有铸造工艺的充型过程;在应力分析方面,通过采用弹塑性和粘塑性及独有的处理铸件/铸型热和机械接触界面的方法,使其具有分析铸件应力、变形的能力。
通过分析可以获得铸造过程的各种现象、铸造缺陷形成及分布、铸件最终质量的模拟和预测。
图2为ProCAST软件进行模拟分析的步骤。
3 应用实例
3.1 铸件充型模拟
铸造充型过程对铸件的最终质量起着决定性的作用,许多铸造缺陷,如浇不足、冷隔、卷气、氧化夹渣乃至缩松、缩孔等都与铸造的充型过程密切相关,利用ProCAST软件能够较为准确的表达充型过程和缺陷生成过程,这对于优化充型系统设计,避免充型不合理引起的铸造缺陷具有重要的意义。
为了检验ProCAST软件在流场预测方面的准确性,我们选用了英国伯明翰的J.Campbell进行的纯铝充型的基准试验,来验证软件的准确性。
试验结果的X-射线充型结果如左图,右图为ProCAST软件的模拟情况,从图中可以看出,
ProCAST软件能够准确模拟整个铸件的充型过程,很好的预测出了浇注系统的卷气缺陷。
图3:实际浇注与ProCAST软件模拟结果对比
在叶轮铸件的铸造工艺设计中,我们应用ProCAST软件很好的预测了叶轮铸件浇注系统的不合理设计,并提出了工艺改进,使该铸件一次浇注成功。
原设计工艺中叶轮各个内浇口流量分布极为不合理,经改进后铸件充型较为均匀,各内浇口流量分布较为均匀。
图4:浇注系统改进前后对比
3.2 铸件凝固模拟
铸造过程中大部分缺陷主要是缩松和缩孔缺陷,而这些缺陷大都在铸件凝固过程中形成,因而,比较精确的再现铸件的凝固过程,对缩松和缩孔缺陷的预测显得极为重要,ProCAST软件能够较为准确的预测铸件的缩松和缩孔缺陷,软件提供多种基于不稳定热传导计算的铸件缩松和缩孔缺陷预测方法,常用的有:温度梯度法、固相率梯度法、凝固时间梯度法、Niyama 判据法及其变种、ProCAST软件自带的预密度相关的判据等。
工程师可以通过多种判据的综合应用,达到预测缩松和缩孔缺陷的目的。
我们在优化某铸钢件时,综合应用了多种判据,经过数次模拟分析,最终成功地解决了生产中的铸件缩松和缩孔问题。
最初铸件的工艺经模拟分析,应用温度梯度法和固相率梯度法显示无缺陷,而应用ProCAST 软件自带的判据显示两处有缩松和缩孔缺陷,这与实际铸件探伤结果一致,经过多次优化,最终解决了问题,所生产的铸件内部致密无缺陷。
3.3铸件应力场模拟
在铸造生产中进场由于铸件结构方面的原因及工艺处理不当而出现热裂,或者在某些部位存在较大的残余应力或残余变形,这是在铸钢件尤其是大型铸钢件中普遍存在,这些缺陷严重影响了铸件的质量和使用寿命,而这两种缺陷都直接和凝固过程中的热应力的产生和发展有关,铁别是热裂缺陷,一般产生在准固相区,而且随着铸件的后续冷却,裂纹不断扩大,经常造成铸件报废。
我们在生产的某材质为35CrMo的铸钢件时,经常在内浇口附近出现裂纹,并且经常扩展到铸件内部,严重影响了后续工作的正常开展,车间技术员曾在内浇口附近增加一块凸台补贴,以减少裂纹向铸件的扩展,但并未彻底解决问题,后来,应用ProCAST软件对铸件应力场进行了模拟,依据模拟情况,提出了改进措施,彻底消除了铸件中的裂纹缺陷。
图9:改进前后的内浇口应力分布对比
4 结论
(1)、ProCAST软件在流场预测方面,已能较好的反映铸造时金属的流动过程,能够准确预测铸造过程中的紊流和卷气。
(2)、应用ProCAST软件能够较为准确的预测铸造过程中所形成缩孔、缩松、热裂等铸造缺陷。
5 参考文献
[1] ProCAST User Manual 2004.1 ESI-Group
[2] 柳百成编《铸造工程模拟仿真与质量控制》机械工业出版社2001(end。