1-TPM---OEE培训材料
TPM培训资料完整版
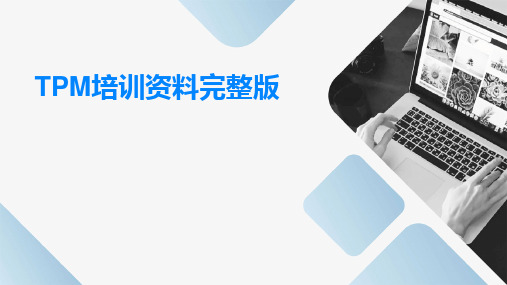
现场问题发现与解决能力提升
01
02
03
04
问题发现
鼓励员工积极发现问题,建立 问题反馈机制,及时收集和处
理现场问题。
问题分析
对收集到的问题进行深入分析, 找出根本原因,制定针对性解
决方案。
问题解决
按照解决方案实施改进措施, 跟踪验证效果,确保问题得到
有效解决。
能力提升
通过培训、交流等方式提高员 工的问题发现和解决能力,形
03
维修策略选择
根据设备的故障类型、故障原因以及维修成本等因素,选择合适的维修
策略,如事后维修、定期维修、状态维修等。合理的维修策略可以降低
维修成本,提高设备维修效率。
TPM实施方法与步骤
03
详解
自主保全活动推进方法
制定自主保全基准书
明确设备的基本条件、使用规则、 点检和保养方法等,为设备使用
者提供操作和维护的依据。
THANKS.
标杆企业案例分享和启示
案例选择
选择行业内具有代表性和先 进性的标杆企业作为学习对 象。
现场参观
组织相关人员到标杆企业进 行现场参观和学习,深入了 解其TPM实施情况和经验做 法。
案例分享
邀请标杆企业相关人员进行 案例分享,介绍其TPM实施 过程中的成功经验、教训和 改进措施。
启示与借鉴
通过标杆企业案例的分享和 学习,获得启示和借鉴,为 本企业TPM的持续改进提供 思路和方向。
明确设备的定期保全计划、保养方法、 维修流程等,为设备维修人员提供操 作依据。
实施定期保全计划
按照计划保全基准书的要求,定期对 设备进行全面的检查、保养和维修, 确保设备处于良好状态。
故障分析与改善
TPMOEE培训材料

TPMOEE培训材料一、介绍1.1 什么是TPMOEE?TPMOEE是指“Total Productive Maintenance for Overall Equipment Efficiency”,即全面设备效率的全面生产维护。
它是一种维修管理方法论,旨在最大程度地提高设备的可靠性和效率,从而提高生产效率和产品质量。
TPMOEE通过改进设备维修、保养和管理,可以减少设备故障、停机时间和能源浪费。
1.2 TPMOEE的重要性在现代制造领域,设备是生产线的核心,设备的运行状况和效率直接决定了生产效果和产品质量。
而设备的故障和停机时间会导致生产线的中断和产品的质量问题,进而影响整个生产计划和客户满意度。
因此,通过实施TPMOEE,可以最大程度地提高设备的可靠性和效率,从而降低故障率、提高生产效率和产品质量,为企业带来巨大的经济效益。
二、TPMOEE的基本原则2.1 以人为本TPMOEE的核心是人,要求全员参与。
每个员工都应了解TPMOEE的基本原则和方法,并积极参与,共同维护和改进设备。
企业应制定相关培训计划,培养员工的意识和技能,推动TPMOEE的实施。
2.2 预防维护传统的维修方法是“等到出问题再修”,而TPMOEE提倡“预防胜于治疗”。
通过定期检查、清洁、润滑和调整设备,可以发现问题的潜在因素并及时处理,以减少设备故障和停机时间。
2.3 数字化管理TPMOEE倡导使用数字化管理系统,对设备运行状况进行实时监控和数据分析。
通过这些数据,可以及时发现设备异常和潜在故障,并做出相应的调整和维修措施,从而提高设备的可靠性和效率。
2.4 持续改进TPMOEE是一个持续改进的过程。
通过设立维护团队、制定工作标准和管理指标,可以不断地改进设备的维修和保养方法,提高设备的性能和效率。
三、TPMOEE的实施步骤3.1 建立基础数据在实施TPMOEE之前,首先需要收集和分析设备的基础数据,包括设备的运行时间、故障时间、维修时间等。
2024年度-TPM经典培训资料

5
TPM实施意义及价值
实施意义
通过TPM的实施,企业可以建立全 员参与的设备管理体系,提高设备可 靠性和稳定性,保障生产顺利进行。
价值体现
降低设备维修成本、减少生产停机时 间、提高产品质量和生产效率、增强 企业竞争力。
鼓励员工利用业余时间进行自我学习 ,通过阅读、网络课程等方式提升自 己的技能和知识水平。
交流学习
组织员工之间进行经验分享和交流, 促进彼此之间的学习和进步。
21
教育训练计划制定和执行情况回顾
制定教育训练计划
根据企业发展战略和员工实际需求,制定切实可行的教育 训练计划,明确培训目标、内容、时间和方式等。
的质量稳定。
实施持续改进
运用PDCA循环等质量管理工具,不 断发现和改进存在的问题,推动品质 保全工作的持续改进。
建立客户反馈机制
及时了解客户对产品和服务质量的反 馈意见,针对问题进行改进和优化, 提高客户满意度。
30
谢谢聆听
31
TPM经典培训资料
1
目录
• TPM概述与基本原理 • 设备自主保全体系建立与实践 • 计划保全体系建立与实践 • 个别改善体系建立与实践 • 教育训练与技能提升体系建设 • 初期管理体系建立与实践 • 品质保全体系建立与实践
2
01 TPM概述与基本原理
3
TPM定义及发展历程
要点一
TPM(Total Productive Mainte…
加强设备自主保全培训
对设备操作人员进行设备自主保全知识和技 能的培训,提高其设备维护和保养能力。
D
9
设备自主保全活动推进策略
TPM及OEE简介

后续目标计划
1.继续完善OEE表的统计制作工作。 2.做好预防性维护和备件管理工作,减少降低设备故障。 3.将工艺调试时间中切换工装、调试产品和等报告时间分开,并制定各自标 准。(目前已确定拆装工装时间标准)
4.对表现性低于80%的现场实测节拍,节拍无误的应分析原因,是操作工造成
的应对操作工进行考核。
80.0%
150.0 54.4% 100.0
60.0% 工时损失(H) 40.0% 累比例率
57.0
50.0 32.0 0.0 0.0 0.0 0.0% 20.0%
分析问题方法
头脑风暴法
OEE的定义 _
设备综合效率
OEE是什么?(来看看组成!)
OEE如何计算? OEE(设备综合效率) =时间开动率×性能开动率×良品率
★问题一:为什么机器停了? 答案一:因为机器超载,保险丝烧断了。 ★问题二:为什么机器会超载? 答案二:因为轴承的润滑不足。 ★问题三:为什么轴承会润滑不足? 答案三:因为润滑泵失灵了。 ★问题四:为什么润滑泵会失灵? 答案四:因为它的轮轴耗损了。 ★问题五:为什么润滑泵的轮轴会耗损? 答案五:因为杂质跑到里面去了。 经过连续五次不停地问“为什么”,才找到问题的真正原因和解决的方法, 在润滑泵上加装滤网。
时间开动效率= (开动 率) 负荷时间-停止时间 负荷时间
*负荷时间=日历工作时间-计划停机时间
计划节拍×产量 性能开动效率= 开动时间 (表现 性) 良品率= (质量指 数) 产量-不良数 产量
*开动时间=负荷时间-停止时间
*不良数=废品+返修数
OEE计算案例
OEE六大损失 机器故障
速度损失 开停机 切换 小停机
Planned Maintenance 计划维护
TPM培训资料

彻底 清 扫并 检查 针对污染 源 采 取 措 施 并 改 善 制 定 暂时性 的 标准 全 员设备的 检查和 保 养 自 主 保 全 的 开始 工 作 位 置 上 的 组织和 完 善 自 发的 设备管 理
5S
难点问题对策/实施
基 础 阶 段
制定点检标准 员工培训/点检实施 自主保全工作开始 目视化管理/优化项目
T P M
全员生产保全
(Total Productive Maintenance)
总 目 录
1. 企业生存的要求 2. 设备效率 3. PM (自主保全)说明 4. TPM(全员自主保全)说明
企业生存的要求
产出的产品 > 投
(服务/环境/情报)
入
(人/材料/设备)
方法1
方法2
大量增加设备投资
不花钱或少花
管理标准化/改善活动自主实施
实 施 阶 段
三、 TPM说明
目 录:
1.TPM定义 2.TPM发展史 3.TPM特点 4.TPM活动形式 5.TPM活动成果 6.TPM工作范畴/内容 7.TPM之树 8.TPM重新组合
1、TPM的定义
TPM(Total Productive
目 标
TPM说明
Maintenance)---全 员预防保全
2、TPM发展史
1960年前后
TPM说明
1980年以后 全面生产维护 TPM: Total Productive Maintenance 全员参加型的保养 生产维修(PM) Productive Maintenance 综合上述维护方法,系统的 维护方案
1960年前后
1955年前后
维修预防(MP) MaintenancePrevention 设计不发生故障的设备,设备 FMEA
《精益生产工具实战培训-TPM_OEE》教材共59页

谢谢你的阅读
❖ 知识就是财富 ❖ 丰富你的人生
71、既然我已经踏上这条道路,那么,任何东西都不应妨碍我沿着这条路走下去。——康德 72、家庭成为快乐的种子在外也不致成为障碍物但在旅行之际却是夜间的伴侣。——西塞罗 73、坚持意志伟大的事业需要始终不渝的精神。——伏尔泰 74、路漫漫其修道远,吾将上下而求索。——屈原 75、内外相应,言行相称。——韩非
《精益生产工具实战培训-TPM_OEE》 教材
36、“不可能”这个字(法语是一个字 ),只 在愚人 的字典 中找得 到。--拿 破仑。 37、不要生气要争气,不要看破要突 破,不 要嫉妒 要欣赏 ,不要 托延要 积极, 不要心 动要行 动。 38、勤奋,机会,乐观是成功的三要 素。(注 意:传 统观念 认为勤 奋和机 会是成 功的要 素,但 是经过 统计学 和成功 人士的 分析得 出,乐 观是成 功的第 三要素 。
TPM-主题改善培训资料

提高生产效率
设备故障停机时间和维修时间 会影响生产效率,专业维护可 以减少维修时间和停机时间,
提高生产效率。
专业维护保养的方法
定期检查
根据设备的特点和使用情况,制定 维护保养计划,定期对设备进行检 查,确保设备状态良好。
更换易损件
针对设备易损件,定期进行更换, 保证设备的正常运行。
调整和校准
定期对设备的各项参数进行校准和 调整,确保设备在最佳状态下运行 。
按照制定的标准和规范 ,定期对设备进行点检 、保养和维护,确保设 备的稳定性和可靠性。
问题反馈与解 决
及时发现和解决设备存 在的问题和故障,对不 能解决的问题进行反馈 Байду номын сангаас协调解决。
持续改进与优 化
根据实际情况和数据分 析,不断优化和改进设 备维护和管理流程,提 高设备的综合效率和企 业的整体效益。
02
润滑与清洁
定期对设备进行润滑和清洁,防止 设备过磨损和堵塞。
专业维护保养的流程
了解设备情况
了解设备的结构、性能和工作原理,制定 相应的维护保养计划。
测试与验证
完成维护保养后,对设备进行测试和验证 ,确保维护保养效果良好。
准备工具和材料
根据维护保养计划,准备相应的工具和材 料。
记录与归档
将维护保养的详细记录归档保存,以便于 后续查阅和维护。
进行维护保养
根据计划进行设备的检查、更换、调整、 润滑和清洁等操作。
04
故障分析与改善
故障分析的方法
初步检查
查阅资料
对故障设备进行初步的外观检查,确定故障 部位。
查阅设备相关资料,了解设备工作原理和常 见故障点。
实际测量
诊断分析
《TPM培训资料》课件

项目和持续监测。
产品质量的重要性。
《TPM培训资料》PPT课 件
什么是TPM
1 TPM的概念
2 TPM的历史发展
3 TPM的目标与原则
TPM ,即全员参与的生 产维护,是一种提高生产 效率、实现零故障、零事 故的管理方法。
TPM 起源于日本,经过几 十年的发展,成为全球制 造业改进生产效率的重要 工具。
TPM 的目标是通过员工培 训和共同参与,达到全面 质量管理和最佳设备维护 的综合改进。
手段,监测TPM的效果并进行持续改进。
7
公司的TPM推进计划
确定TPM实施的阶段、目标和时间计划, 明确推动TPM的责任和权力。
进行设备信息搜集与分析
收集设备数据并进行分析,找出影响设 备性能和可靠性的关键因素。
实施TPM的五大支柱
按照TPM的五大支柱进行改进和维护的 实施,逐步提高生产效率和设备性能。
TPM的五大支柱
5S整理与清洁
通过整理、整顿、清扫、清 洁、素养的五个步骤,创造 整洁的工作环境,提高生产 修和预防性更换等措施,减 少设备故障,提高生产稳定 性。
设备管理
通过日常管理、保养与维护, 延长设备寿命,确保设备正 常运转。
品质维护
通过品质检测与监控以及品质维护与改进的措 施,确保产品质量达到预期标准。
分享制造业中不同公司在TPM 实 施过程中遇到的挑战和取得的成 果。
总结与展望
1 TPM的实施效果和意
义
2 TPM的未来发展方向
展望TPM 在数字化时代的
3 下一步的行动计划
提出实施TPM 的下一步行
总结TPM 的实施对于提高
发展趋势,如智能化设备
动计划,包括培训、改进
- 1、下载文档前请自行甄别文档内容的完整性,平台不提供额外的编辑、内容补充、找答案等附加服务。
- 2、"仅部分预览"的文档,不可在线预览部分如存在完整性等问题,可反馈申请退款(可完整预览的文档不适用该条件!)。
- 3、如文档侵犯您的权益,请联系客服反馈,我们会尽快为您处理(人工客服工作时间:9:00-18:30)。
Step 1 - Hard To Access Areas
Items C = Cleaning L = Lubrication I = Inspection Planned Completi on Date
No.
Difficulty
Counter measure
Date Completed
• 拒绝停机和浪费 • 学习TPM并付诸实践:
– – – – 消除小毛病 消除停机 消除效率损失 改善设备和制程
TPM设备复原流程
• 鉴定设备状况 – 通过清洁进行检查 – 找出并记录异常 • 消除劣化 – 找出并消除异常的根因 – 通过清洁润滑紧固螺丝稳定设备基础 • 重建设备 – 完成所有维修工作 • 维护设备 – 通过每天的检查达到维护的效果
设备毛病的三种状况
• 小毛病 – 小问题,但如果长期不修理会导 致大问题 • 中等毛病 – 影响设备性能但不影响运行 • 大问题 – 导致停机
小毛病例子
• • • • • • • • 脏污 漏油漏气 松脱或缺螺丝垫片等 量具不好读 绝缘管磨损 塑料管或类似部件磨损 接头松脱 机器运行不顺畅
小毛病例子
TPM Services
TPM 帮助消除浪费
• 时间和精力的浪费是由于: – 停机 – 速度慢 – 质量差 • 资产的浪费是由于: – 低OEE – 需要额外的设备和人手 • 浪费是由于: – 大批量生产 – 大量安全库存
TPM Services
典型的TPM 结果
可操作性上升 25% 维护成本降 30% 到 50% 库存降低 50% 到 75% 停机的人力损失减少 50% 报废减少 70% 产能提高 25-40% 生产力提高 50%
TPM 5大支柱
1 5
Champion : HR/Mgt.
Champion : Engineering Equipment Design
设备早期管理/ 预防维护的设计 EEM
2
Champion : Production
培训/提高技能 TSD
自主维护 AM
设备
Champion : BU
3
Champion : Maintenance
4. Correct problems you can deal with within the time constraints allowed. All other
problems will be tagged at the conclusion of the training and the team will prioritize them for repairs at a later date either by the Team or by the Maintenance Department.
TPM 活动的目标
1. 优化设备状况,提高设备有效性 2. 开发针对设备整个生命周期的维护计划 3. 开发出相关标准和检查表 4. 提高操作员和维修人员技能 5. 系统的提高工作环境 6. 全员参与提高大家团队精神 7. 练习目标管理的过程
• 所有设备都应该像最好的时候一样运行 • 设备只有当技术淘汰时才会被更换 • TPM 活动包含寻找并消除所有小的停机
让我们来看看现场中设备的异常 现象
TPM活动前后设备对比
第一步结束后利用第一步的发 现组建团队
• • • • • • 异常清单 带改善区域清单 修复问题追踪表 一点课 难以到达区域地图 初始清洁检查表
Abnormality Summary Sheet
作
用
旧习惯 我操作 – 你维修 TPM 习惯 人人都有维护设备的 责任
故障:人为引起的障碍
– ①减少设备停机损失, 提高可预知运行时间 – ②减少不良 – ③减少设备相关其他损 失 – ④减少制造过程中的其 他损失
TPM 有助于提高主人翁责任感
维护良好的设备可以给我们
• 维护良好的设备可以保质保量的生产 • 缺乏维护的设备产量低质量差 • 坏的设备做不出任何产品
4
系统化的改进过程/ SEI
改进维护过程 MPI
自主维护活动七步走
初步清洁检查 --以5S为手段发现问题并填写问题卡 消除污染源和难以到达的区域 --解决问题卡上记录的问题,并 尽量使以后的清洁检查容易实施 建立临时标准 --建立定期清洁检查及维护的机制,保持前两阶段的成果 开展全面检查的培训 --为全面实施自主维护开展培训(知识,技能,标 准) 进行全面检查 --开展自主维护团队主导的自主维护,建立系统 改善工厂管理 --深化自主维护活动 继续上面六步并参与高级改善活动--人员,设备,组织整体水平
• • • • • • • • 感应器不良 液位低 固定销松或缺失 安全防护缺失或松脱 部件磨损 声音异常 异味 振动
提醒!!
所有的大问题都是由于被忽视的小毛病导致
TPM 从发现小毛病 开始到避免灾难性后果
停机
团队
正常的维护从这里开始 不用很长时间你就可以发现很多被忽视的小问题.,...
TPM 团队目标:
设备缺乏维护是因为:
• 设备缺乏维护
– 维护部的问题 – 操作员的问题
• 操作员不具备操作知识 • 设备设计问题 • 糟糕的制程设计
TPM 如何为精益服务
• TPM 提高设备效率 – 减少投资 – 提高现有资产效率 • TPM 取保零停机和高可靠性 – 允许短期计划和小批量 – 确保生产顺畅 • TPM 提高质量 – 制程更可靠 – 充分减少不良 • TPM 强调 – 操作员技能 – 设备和周围环境表现 – 全员参与和责任心
Auburn, IN
Three Rivers, MI
Jackson AMD, Ms
Gainsboro, TN
To TPM
六种损失对设备可生产时间的影响
总机器可用时间
8 小时
设备可用性角 度衡量
总可操作时间
6小时
停机损失
设备停机 换型和调整
生产效率角度衡 量
等待和微小停机 速度减缓
剩余操作时间
4.8小时
for cleaning.
3. Systematically clean each part of the equipment using the checklist on the next
page. Note: An "abnormal condition" is defined as any condition within, or around the machine that affects the appearance and performance of the machine or production cell. a "normal condition" is defined as a condition in which the machine's appearance and performance is in "like new" condition and no waste is generated in time, resources, or materials. An abnormal condition can be a broken bolt, a leak, a worn or damaged part, it can also be a dirty part. As you document these conditions on your "Abnormality Summary Sheet" try and discover the reasons for them. Ask yourself the following questions: Why did this happen? What other problems could this have caused? How can I prevent this from recurring?
自主维护
第一步目标
• • • • • • 停止设备劣化 学习如何在清洁中进行检查 学习如何发现问题并找出根因 学习如何制定标准 与设备亲密接触并培养责任感 帮助整个团队前进
清洁和检查活动
• • • • • • • 团队一起进行目视检查并记录不良 清除脏污 用四种感知手段进行检查 记录所有问题和发现 为异常点拍照片 找到并记录待改善区域 为制定临时标准收集数据
5. Document the cleaning tasks that you complete. Use your camera to take pictures
to document the "before" condition of the machine and to document the "after" condition to depict your accomplishments. Began to develop countermeasures for keeping the machine clean.
TPM Services
美国工厂 平均水平
30-45% OEE
55-70%
世界级
85% OEE
15%
损失
损失
隐藏的工厂
最
大
产
能
TPM Services
OEE
如何计算OEE
设备有效性 X 生产效率 X 质量结果
停机
等待 & 微小停机
制程不良
换型 & 调整
其他OEE 衡量制造过程中的六种损失
record of your accomplishments. This will also serve as your "Baseline" for all future improvements.