激波控制鼓包在翼身融合体上的应用
翼身融合技术的发展过程

翼身融合技术的发展过程翼身融合技术是一种将机翼和机身融为一体的航空技术,它的发展经历了多个阶段。
本文将从最初的概念提出到现在的应用发展,介绍翼身融合技术的发展过程。
翼身融合技术最早的概念可以追溯到20世纪60年代。
当时,航空工程师们开始思考如何减少飞机的阻力,提高飞行效率。
他们发现,传统的机翼和机身之间存在着明显的间隙,这个间隙会导致空气流动的不连续,增加了阻力。
于是,他们开始尝试将机翼和机身融为一体,以减少这个间隙,提高飞行效率。
在翼身融合技术的初期阶段,航空工程师们主要通过改变机翼和机身的形状来实现融合。
他们设计了一些具有流线型外形的机翼和机身,使它们能够更好地连接在一起,减少了间隙。
这种方法在一定程度上提高了飞机的飞行效率,但仍然存在一些问题,比如结构强度不足和重量过大等。
随着科技的不断进步,翼身融合技术逐渐得到了改进和完善。
在20世纪80年代,航空工程师们开始采用复合材料来制造机翼和机身,以提高结构强度和减轻重量。
复合材料具有优异的力学性能和轻质化的特点,能够更好地满足翼身融合技术的需求。
同时,他们还引入了一些先进的制造工艺,如自动化制造和三维打印等,以提高生产效率和降低成本。
到了21世纪,翼身融合技术进一步得到了发展和应用。
航空工程师们开始将更多的功能集成到机翼和机身中,以提高飞机的性能和安全性。
他们在机翼和机身上安装了一些传感器和执行器,用于监测飞机的状态和控制飞行。
同时,他们还利用翼身融合技术设计了一些新型的机翼结构,如可变弯曲机翼和无尾翼机翼等,以进一步提高飞机的操纵性和机动性。
翼身融合技术的发展不仅在民用航空领域有所应用,也在军事航空领域发挥了重要作用。
在军用飞机中,翼身融合技术可以提高飞机的隐身性能,减少雷达反射面积,增加飞机的生存能力。
同时,它还可以提高飞机的载荷能力和作战效能,使飞机能够携带更多的武器和设备。
总的来说,翼身融合技术的发展经历了从概念提出到应用发展的过程。
随着科技的不断进步,翼身融合技术在航空领域的应用越来越广泛,为飞机的性能和安全性提供了更多的可能性。
超声速翼身组合体激波阻力优化的efce算法
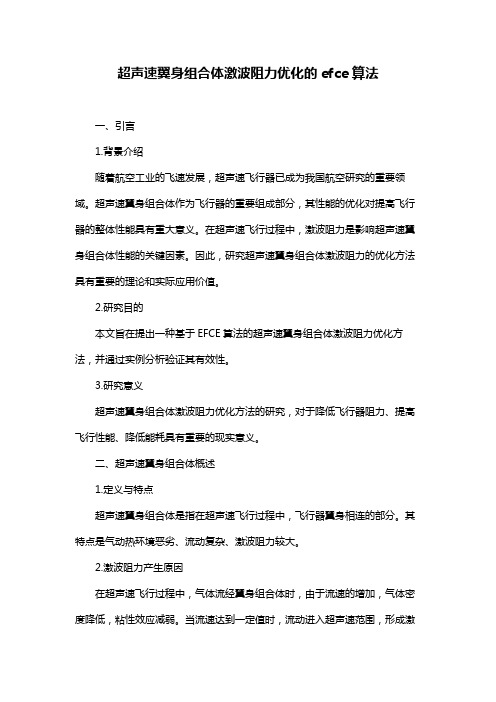
超声速翼身组合体激波阻力优化的efce算法一、引言1.背景介绍随着航空工业的飞速发展,超声速飞行器已成为我国航空研究的重要领域。
超声速翼身组合体作为飞行器的重要组成部分,其性能的优化对提高飞行器的整体性能具有重大意义。
在超声速飞行过程中,激波阻力是影响超声速翼身组合体性能的关键因素。
因此,研究超声速翼身组合体激波阻力的优化方法具有重要的理论和实际应用价值。
2.研究目的本文旨在提出一种基于EFCE算法的超声速翼身组合体激波阻力优化方法,并通过实例分析验证其有效性。
3.研究意义超声速翼身组合体激波阻力优化方法的研究,对于降低飞行器阻力、提高飞行性能、降低能耗具有重要的现实意义。
二、超声速翼身组合体概述1.定义与特点超声速翼身组合体是指在超声速飞行过程中,飞行器翼身相连的部分。
其特点是气动热环境恶劣、流动复杂、激波阻力较大。
2.激波阻力产生原因在超声速飞行过程中,气体流经翼身组合体时,由于流速的增加,气体密度降低,粘性效应减弱。
当流速达到一定值时,流动进入超声速范围,形成激波。
激波产生阻力,成为影响超声速翼身组合体性能的关键因素。
3.超声速翼身组合体激波阻力影响因素超声速翼身组合体激波阻力的影响因素主要包括:气动参数、几何参数、飞行速度、来流条件等。
三、EFCE算法介绍1.EFCE算法原理EFCE(Efficient Fluid Configuration Evolution)算法是一种基于梯度下降的优化算法,通过迭代更新翼身组合体的几何参数,以达到降低激波阻力的目的。
2.EFCE算法流程EFCE算法的流程主要包括:初始化参数、构建目标函数、计算梯度、更新参数、判断收敛。
3.EFCE算法优势EFCE算法具有以下优势:(1)收敛速度较快,计算效率高;(2)适用于多种超声速翼身组合体模型;(3)具有较强的全局搜索能力。
四、超声速翼身组合体激波阻力优化方法1.优化目标与指标优化目标:降低超声速翼身组合体激波阻力。
跨音速机翼采用鼓包主动减阻技术研究

A方程 模 型 。本 文首 先对鼓 包 控制激 波减 阻 的机 理
进 行 了分 析 , 后 将 该 技 术 应 用 到 了大 型客 机 上 , 然
气 的 排 放 。 因 此 , 一 代 民用 航 空 飞 机 的 设 计 最 下
进 行机 翼跨 音速 减 阻研究
民用 飞 机 设 计 与 研 究
式 中 , P e 和 k代 表密 度 、 强 、 量 、 度 P、、、 压 能 温 和热 传导 系数 , 是 沿 直角 坐标 系 方 向的 速度 分
其中, d为到 物面 的最 近距离 由式 ( ) 示 : 9表
量 性 应 的 量 =( ) , 切 力 分为 / 粘 . t 鲁+ +
在气 动 性 能 方 面 得 到 了相 当 大 的 改 善 , 提 高 效 在
率及 减 少 燃油 消耗 方 面也 取 得 了长 足 的进 步 。从 另 一个 角 度来 说 。 现 有 飞 机 外 形 基 础 上 。 果 没 在 如
对 民航 客机而 言 , 计 巡 航 速 度 大部 分 都 在跨 设 音 速 区域 _ , 2 如何减 少 跨音 速 飞 行 时 的激 波 阻 力 一 ] 直 是飞 机设 计 师 的一 项 重 要 工 作 内容 。本 文采 用 鼓 包 的方 式 对激 波进 行 控 制 以减 少 波 阻 , 高 飞 机 提
= z = “ 多G= “ F , + , 主
: : ,
:
,
多 () 2
0" i 3 1
1
.
1
1
i
 ̄ 3 + a pu ui p 3i
i
i
() e
十c T g 曩
S +
, L 2
() 8
翼身融合机翼焦点计算

翼身融合机翼焦点计算【实用版】目录1.翼身融合机翼的概念2.翼身融合机翼的优点3.翼身融合机翼焦点计算的方法4.翼身融合机翼焦点计算的实际应用5.翼身融合机翼的发展前景正文一、翼身融合机翼的概念翼身融合机翼,顾名思义,是指机身与机翼融为一体的航空器结构。
这种结构能够有效提高机翼的承载能力和刚度,从而使得飞行更加稳定。
在现代航空领域,翼身融合机翼已经成为了飞行器的一种重要设计理念。
二、翼身融合机翼的优点翼身融合机翼具有以下几个显著优点:1.提高机翼承载能力:翼身融合的设计使得机翼与机身的连接更加紧密,有利于提高机翼的承载能力。
2.提高机翼刚度:翼身融合的设计使得机翼与机身的材料可以更好地连接在一起,提高了机翼的刚度。
3.降低飞行阻力:翼身融合的设计使得机翼与机身的形状可以更好地融合在一起,降低了飞行阻力。
三、翼身融合机翼焦点计算的方法翼身融合机翼焦点计算是翼身融合机翼设计的重要环节。
其主要方法包括以下几种:1.解析法:通过解析机翼与机身的结构,计算出翼身融合机翼的焦点位置。
2.数值法:通过数值模拟的方法,计算出翼身融合机翼的焦点位置。
3.实验法:通过实验测试的方法,测量出翼身融合机翼的焦点位置。
四、翼身融合机翼焦点计算的实际应用翼身融合机翼焦点计算在实际应用中的作用主要体现在以下几个方面:1.优化翼身融合机翼设计:通过翼身融合机翼焦点计算,可以优化翼身融合机翼的设计,提高其性能。
2.指导飞行器制造:通过翼身融合机翼焦点计算,可以为飞行器的制造提供重要指导。
3.指导飞行器飞行:通过翼身融合机翼焦点计算,可以指导飞行器在飞行过程中的操作。
五、翼身融合机翼的发展前景随着航空技术的发展,翼身融合机翼的发展前景十分广阔。
在未来,翼身融合机翼将会在以下几个方面发挥重要作用:1.高速飞行器:翼身融合机翼的设计将有助于提高高速飞行器的性能。
2.无人机:翼身融合机翼的设计将有助于提高无人机的飞行稳定性和承载能力。
翼身融合机翼焦点计算
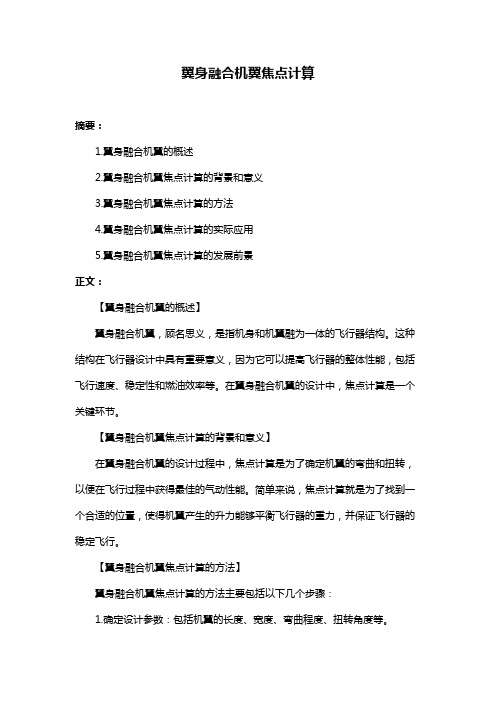
翼身融合机翼焦点计算
摘要:
1.翼身融合机翼的概述
2.翼身融合机翼焦点计算的背景和意义
3.翼身融合机翼焦点计算的方法
4.翼身融合机翼焦点计算的实际应用
5.翼身融合机翼焦点计算的发展前景
正文:
【翼身融合机翼的概述】
翼身融合机翼,顾名思义,是指机身和机翼融为一体的飞行器结构。
这种结构在飞行器设计中具有重要意义,因为它可以提高飞行器的整体性能,包括飞行速度、稳定性和燃油效率等。
在翼身融合机翼的设计中,焦点计算是一个关键环节。
【翼身融合机翼焦点计算的背景和意义】
在翼身融合机翼的设计过程中,焦点计算是为了确定机翼的弯曲和扭转,以便在飞行过程中获得最佳的气动性能。
简单来说,焦点计算就是为了找到一个合适的位置,使得机翼产生的升力能够平衡飞行器的重力,并保证飞行器的稳定飞行。
【翼身融合机翼焦点计算的方法】
翼身融合机翼焦点计算的方法主要包括以下几个步骤:
1.确定设计参数:包括机翼的长度、宽度、弯曲程度、扭转角度等。
2.建立数学模型:根据设计参数,建立翼身融合机翼的数学模型,以便进行后续的计算。
3.计算气动载荷:通过计算飞行器在飞行过程中所受到的气动载荷,为焦点计算提供依据。
4.确定焦点位置:根据气动载荷计算结果,确定机翼的焦点位置,以达到最佳的气动性能。
【翼身融合机翼焦点计算的实际应用】
翼身融合机翼焦点计算在实际应用中具有广泛的应用,包括飞机、无人机、导弹等飞行器。
通过焦点计算,可以优化翼身融合机翼的设计,提高飞行器的性能。
【翼身融合机翼焦点计算的发展前景】
随着飞行器技术的不断发展,翼身融合机翼焦点计算也将迎来新的发展机遇。
飞行器设计新技术

飞行器设计新技术军用飞机发展很快,从20世纪50年代的第一代超音速战斗机起,到目前已经发展到第四代超音速战斗机,第三第四代战机采用了一系列新技术,下面就不同的方面浅谈一下飞行器设计中的新技术一、气动布局技术(一)近距耦合鸭式布局没有水平尾翼,但在机翼(亦称主翼)前面装有水平小翼的飞机称为鸭式布局飞机。
机翼前面水平小翼称为前翼或鸭翼。
鸭式布局有以下优点:1.前翼不受流过机翼的气流的影响,前翼操纵效率高。
2.飞机以大迎角飞行时,正常式飞机平尾的升力为负升力(向下),这样就减少了飞机的总升力(有人称它为挑式飞机,即机翼升力不仅要平衡飞机的重量,而且还要克服平尾的负升力),从而不利于飞机的起飞着陆和大迎角时的机动性能。
而鸭式飞机与此相反,前翼在大迎角飞行时提供的是正升力,从而使飞机总升力增大(有人称它为抬式飞机,即前翼与机翼共同平衡飞机重量),这样就有利于减小飞机起飞着陆速度,改善起飞着陆性能,同时也可以提高大迎角时的机动性能。
3.鸭式飞机配平阻力小,因而续航能力好。
鸭式飞机虽有上述优点,但是由于还存在不少问题有待解决,使鸭式飞机的主要优点(即鸭翼与机翼都产生正升力)的发挥受到很大的影响,因此在很长一段时间内,鸭式布局使用不广泛。
针对这一问题,航空界进行了一系列的研究工作。
所谓近距耦合鸭式布局飞机,就是这方面研究的成果。
近距耦合鸭式布局飞机(简称近距耦合鸭式飞机)是指前翼与机翼距离很近的一种鸭式飞机,这种飞机往往采用小展弦比大后掠的前翼,此时前翼形成的脱体涡流经主翼表面,使主翼升力提高,而前翼也将受到主翼上洗气流的影响而增加升力。
同时,主翼表面的低压抽气作用,又提高了前翼涡流的稳定性。
因此,前翼与主翼近距耦合的结果,既增加了飞机的升力,也推迟了飞机的失速。
近距耦合鸭式布局的研究成功,使鸭式布局在战斗机上重新流行。
(二)边条机翼边条机翼是一种组合机翼,它是由中等后掠角和中等展弦比的基本机翼和位于翼根前部的大后掠角、小展弦比尖前缘的边条组成。
飞行器主要减阻措施机理及其应用效果-力学论文-物理论文
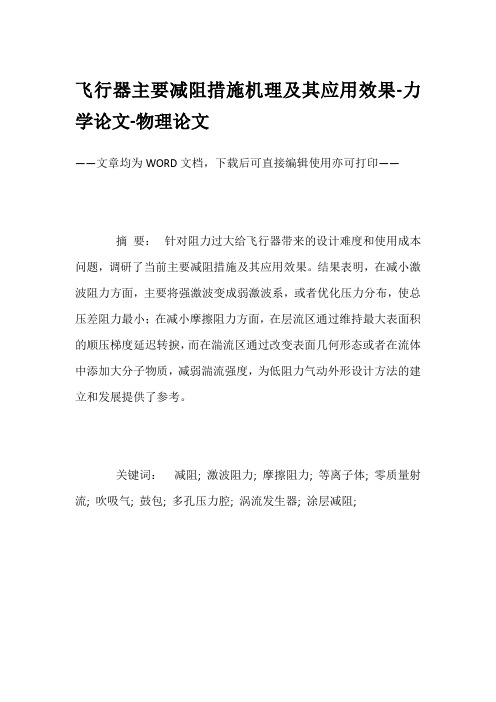
飞行器主要减阻措施机理及其应用效果-力学论文-物理论文——文章均为WORD文档,下载后可直接编辑使用亦可打印——摘要:针对阻力过大给飞行器带来的设计难度和使用成本问题,调研了当前主要减阻措施及其应用效果。
结果表明,在减小激波阻力方面,主要将强激波变成弱激波系,或者优化压力分布,使总压差阻力最小;在减小摩擦阻力方面,在层流区通过维持最大表面积的顺压梯度延迟转捩,而在湍流区通过改变表面几何形态或者在流体中添加大分子物质,减弱湍流强度,为低阻力气动外形设计方法的建立和发展提供了参考。
关键词:减阻; 激波阻力; 摩擦阻力; 等离子体; 零质量射流; 吹吸气; 鼓包; 多孔压力腔; 涡流发生器; 涂层减阻;Abstract:For the excessive drag problem which usually enlarges the design difficulty and cost of use, the flow mechanism effectiveness of drag reduction techniques has been investigated and analyzed, as well as its current effectiveness. The result shows that, the active and passive flow control techniques access the shock drag reduction though wakening the an strong shock to multi-wake shocks or reconstructing the an optimal pressure distribution, and access the fraction drag reduction by enlarging of the laminar region by favorable pressure gradient on laminar flow region and decreasing the strength of turbulence by changing the solid wall micro scale construction or adding large scale molecule to boundary. The flow mechanism can provide references for low drag aerodynamic design method construction.Keyword:drag reduction; shock wave drag; friction drag; plasma; zero-mass flux jet; push-pull airflow; bump; poros pressure chamber; vortex generator; coating drag reduction;1、引言减阻一直是航空航天领域关注的焦点,定型、批产、运营装备的各类航空运输飞机、战斗机、高空飞艇以及导弹的外形,一般都是当时技术能力下能达到阻力最小外形,飞行器的更新换代都会尽量吸收减阻技术的新成果,对外形进行持续的优化改进。
翼身融合技术
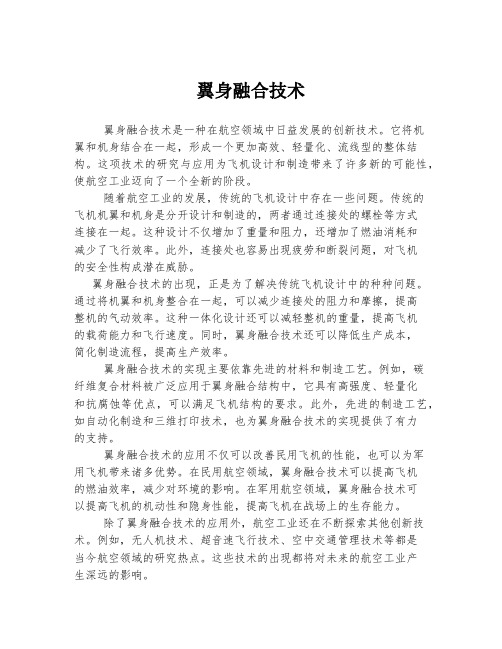
翼身融合技术翼身融合技术是一种在航空领域中日益发展的创新技术。
它将机翼和机身结合在一起,形成一个更加高效、轻量化、流线型的整体结构。
这项技术的研究与应用为飞机设计和制造带来了许多新的可能性,使航空工业迈向了一个全新的阶段。
随着航空工业的发展,传统的飞机设计中存在一些问题。
传统的飞机机翼和机身是分开设计和制造的,两者通过连接处的螺栓等方式连接在一起。
这种设计不仅增加了重量和阻力,还增加了燃油消耗和减少了飞行效率。
此外,连接处也容易出现疲劳和断裂问题,对飞机的安全性构成潜在威胁。
翼身融合技术的出现,正是为了解决传统飞机设计中的种种问题。
通过将机翼和机身整合在一起,可以减少连接处的阻力和摩擦,提高整机的气动效率。
这种一体化设计还可以减轻整机的重量,提高飞机的载荷能力和飞行速度。
同时,翼身融合技术还可以降低生产成本,简化制造流程,提高生产效率。
翼身融合技术的实现主要依靠先进的材料和制造工艺。
例如,碳纤维复合材料被广泛应用于翼身融合结构中,它具有高强度、轻量化和抗腐蚀等优点,可以满足飞机结构的要求。
此外,先进的制造工艺,如自动化制造和三维打印技术,也为翼身融合技术的实现提供了有力的支持。
翼身融合技术的应用不仅可以改善民用飞机的性能,也可以为军用飞机带来诸多优势。
在民用航空领域,翼身融合技术可以提高飞机的燃油效率,减少对环境的影响。
在军用航空领域,翼身融合技术可以提高飞机的机动性和隐身性能,提高飞机在战场上的生存能力。
除了翼身融合技术的应用外,航空工业还在不断探索其他创新技术。
例如,无人机技术、超音速飞行技术、空中交通管理技术等都是当今航空领域的研究热点。
这些技术的出现都将对未来的航空工业产生深远的影响。
总之,翼身融合技术是航空领域中一项重要的创新技术。
它通过将机翼和机身整合在一起,提高了飞机的性能和效率。
翼身融合技术不仅在民用航空领域具有广泛的应用前景,也在军用航空领域具有重要的战略价值。
随着科技的不断进步和创新的推动,相信翼身融合技术将会在未来的航空领域中继续发挥重要作用,推动航空工业迈向新的高度。
- 1、下载文档前请自行甄别文档内容的完整性,平台不提供额外的编辑、内容补充、找答案等附加服务。
- 2、"仅部分预览"的文档,不可在线预览部分如存在完整性等问题,可反馈申请退款(可完整预览的文档不适用该条件!)。
- 3、如文档侵犯您的权益,请联系客服反馈,我们会尽快为您处理(人工客服工作时间:9:00-18:30)。
Figure 1. Optimisation chain.By an inverse design method, the mean of an elliptic and a triangular spanwise load distribution was shown to provide better aerodynamic performance than that from an elliptic load distribution for the BWB geometry at Mach 0⋅85. However, the benefits of a BWB configu-ration can only be fully explored through further careful and detailed aerodynamic shape design and optimisation including multi-disci-plinary interaction with structures and flight dynamics. Aerodynamic optimisation of a BWB shape involves hundreds of design variables and constraints but with a relatively much smaller number of objective functions. By employing an efficient adjoint-based optimi-sation methodology, Le Moigne and Qin(5-7)carried out shape optimi-sation of the BWB for a given planform or including the sweep angle of the outer wing as a design parameter. The obtained optimised shape has resulted in significant drag reduction from the baseline configuration. The optimised shape has also been used within the European MOB project(8)on multidisciplinary optimi-sation of a blended wing body aircraft. Nonetheless, it still exhibits relatively strong shock waves on the outer wing and the winglet of the aircraft with their associated wave drag.There is a wide range of shock control methods proposed with the purpose of weakening the shock strength and hence controlling shock/boundary layer interaction, such as blowing and suction(9), local geometrical changes of the aerofoil profile by a bump near the foot of the shock(10), and local slots and grooves(11). Among these devices, shock control bumps stand out to be the most effective option. A shock control bump aims to replace the normal transonic shock with either near isentropic compression or a break up into multiple weaker shocks, e.g. a λ-shock structure, which significantly weakens the shock strength and hence reduces the wave drag. Earlier studies have shown that 2D shock control bumps are very effective in wave drag reduction, but a limitation in practical application is that they only performs well over a relatively narrow range of operation(12,13). In a more recent study by Qin et al(14), 3D shock control bumps were proposed and investigated for installation on transonic wings using computational simulations to explore the effect of three dimensionality on the range of bump performance. Some experimental studies were carried out by Holden et al(15)with 3D bumps installed on a transonic wind tunnel wall to reveal associated flow physics. Further study by Qin et al(16)for installation on transonic wings demonstrated that not only were the 3D bumps as effective as the 2D bump in reducing wave drag at the design point but they were also able to work over an improved range of operation as compared to the 2D bump.It is therefore interesting to explore whether a BWB shape incor-porating an array of 3D shock control bumps could lead to further improvement in BWB aerodynamic performance. Consequently, we need to include both the BWB shape defined by the aerofoil profiles at a series of master sections and an array of 3D bumps on the upper surface of the outer wing in the BWB shape parameterisation forFigure 2. Parameterisation of 3D bumps.of the local master section aerofoil as a design variable so that the BWB spanwise twist is optimised in the design.This aerofoil parameterisation is then extended to three dimen-sions to represent a wing or in this study, the BWB shape. The BWB is divided into a series of master sections. Across the fuselage or main body, the master sections are connected via a cubic spline in the spanwise direction for a smooth transition from one master section to the next. As for the master sections throughout the outer wing and the winglet, they are connected linearly as the planform has linear leading and trailing edges. Each of these master sections deforms according to the two-dimensional parameterisation presented earlier. Note that the twist angles of the winglet master sections are also design parameters for optimisation.4.03D BUMPS PARAMETERISATIONAND GRID UPDATEFigure 2 shows a schematic of the parameters for one half of a 3D bump, which is added ‘on-top’ of the wing surface. The shape of the x -y plane at the middle section of the bump is represented by a cubic spline expression. The same expression is used to model the variation of the y -z plane shape across various chordwise locations of the bump, which then define the full geometrical shape of the 3D bump. From Fig. 2, the 3D bump is parameterised by six design variables. These include the position of the bump crest, the relative position of the crest with the streamwise bump length, the maximum bump height, the spanwise width of the bump and finally the spanwise spacing between the neighbouring bumps. The gradient at the bump crest is set to zero and the intersections at the base of the bump are treated such that the continuity of the slope at the point of the wing surface is maintained.In this study, ten complete 3D bumps are placed on the upper surface of the outer wing and a further three on the inward surface of the winglet. They are shown in Fig. 3 along with a local view of the BWB outer wing and the winglet. Note that each of the bumps has their own six independent design variables so that they may vary in size and location independently.Once the surface geometry is modified and the 3D bumps are added onto the surface, the computational grid around the geometry has to be updated. This is carried out through an algebraic grid deformation technique that propagates smoothly the geometry change through the volume grid. This analytical method is analyti-cally differentiated to provide the grid sensitivities d X /d βk as needed in the calculations of the sensitivity derivatives in the adjoint solver.Even though this grid-updating module is only a relatively small part of the whole optimisation process, it is also necessary to paral-Figure 3. The array of 3D bumps on the wing.Figure 4. Parallel speed-up for flow solver.Figure 5. Parallel speed-up for adjoint solver.7.0RESULTSThe result presented here is an Euler optimisation of the BWB shape with winglets and a series of 3D bumps installed on the upper surface of the outer wing. The cruise condition is at a freestream Mach number of 0⋅85. The design C L is 0⋅41 based on the trapezoidal reference wing area of 842m 2. The objective of the optimisation task is to minimise the total drag whilst maintaining the lift at the target design condition and also satisfying the volume constraints. The BWB is divided into 34 master sections, four at the fuselage that are connected via a cubic spline expression in the spanwise direction.The rest are located on the outer wing and the winglet, which are connected linearly. Recall that all the master sections are parame-terised with 16 active Bézier parameters and a twist-increment design variable, except for the two most outboard sections on the outer wing and winglet junction. These two master sections are only allowed changes in twist without shape deformation to avoid complexity in the connection between the outer wing and the winglet. As a result, including the design variables for the 13 3D bumps, there are a total of 657 design variables for this optimisation task. The optimisation problem can be described as below:Minimise C DSubject toC L ≥0⋅41V oi ≤V i ≤2 V oi , i = 1, … , 34Here, in addition to the lift constraint, the internal volumes of the 34master sections, excluding the presence of the bumps, are also constrained. A strategy has been chosen such that the possible existence of a 3D bump over a master section would not lead to thinning of the internal volume of that section. As a result, the internal volumes constraint stated above will only take the volume defined by the aerofoil section geometry itself into account, excluding the possible additional volume imposed by the 3D bump. In order to resolve the geometry of the 3D bumps in both the chordwise and spanwise directions, the high-fidelity grid generated for this problem has a resolution of 236 ×33 ×288 or around 2⋅2m points.Consequently, this optimisation task involves a number of large flow and adjoint solutions, thus it can only be run on large high perfor-mance computing facilities such as the UK national HPCx in Daresbury. In addition, the grid is decomposed into 128 size-balancedobjective function through the computational grid variations. The accuracies of the sensitivity derivatives computed by the adjoint solver have been validated with finite differences as investigated by Le Moigne and Qin (5).6.1ParallelisationWhen solving for the adjoint vector, we use the same parallelisation methodologies implemented in the flow solver as discussed earlier.This is because the coding structure of the adjoint solver bears similarities with the flow solver. The parallel efficiency of the adjoint solver has also been tested using the same way the parallel efficiency of the flow solver has been tested by using Equation (6).The speed-up graph for the adjoint solver is shown in Fig. 5. The performance of the adjoint solver is found to be very similar to the flow solver.The calculation of the sensitivity derivatives in Equation (15) is looped over the number of design variables. As indicated in this equation, each calculation of the derivatives involves large and time-consuming matrix multiplications. Therefore parallelisation of this part is essential to avoid a bottleneck in the optimisation process when the grid resolution and the number of design variables are very large.Again, from Equation (15), the grid sensitivities d X /d βk of the whole volume grid, which is updated by employing an analytical grid deformation technique as pointed out in Section 4.0, has to be recalculated for each of the design variables βk . For the code to be data-parallel efficient, each processor only stores the grid for its own block. However, each βk could have influences in multiple blocks because the wing surface has to be modified as a whole. Take the twisting angle of a master section and a block that is situated across this section as shown in Fig. 6 as an example. A change in this design variable will affect at least the whole section, which in turn spans across multiple blocks. Thus, the grid sensitivities in the volume grid of this block are influenced by this design variable and also several other design variables, such as the Bézier control points on the master sections that are located within this block.Consequently, each processor has to be provided with the complete surface grid modified by βk so that the grid sensitivities in its block can be computed properly. Each processor then computes Equation (15) separately but simultaneously. The values from each processor are summed up on the master node to form the final value of the sensitivity derivatives for βk .Figure 6. Dependency of the grid sensitivities in a block.Figure 7. Surface grid of the BWB with 3D bumps.In Refs 6 and 7, two BWB shapes without 3D bumps have been optimised with and without pitching moment constraint. Here, they are re-meshed at the same level of grid resolution of 2⋅2m grid points and the flow solutions are computed again. The re-computed aerody-namic coefficients for these two optimised shapes from the present calculations are also compared in Table 1. Even at the same grid resolution, both of the previously optimised shapes do not match the improvement gained by the present optimised shape with 3D bumps.Between the two previously optimised shapes, the one that is optimised without the pitching moment constraint performs slightly better than the one with this constraint.Comparison of the contours of pressure coefficient in Fig. 9indicates that the improvement is largely coming from the reduction of the wave drag. On the outer wing, some beneficial effects from the 3D bumps can be seen. Strong shock waves that formed on the blending area and fuselage of the baseline configuration have been largely eliminated in the optimised design. These effects are highlighted in Fig. 10 by comparing the computed shock structures from both cases. It can be observed that there is still some remaining weak shock wave on the outer wing, which is more pronounced near the outer wing-winglet intersection. This is due to the fact that the master section at the outer wing-winglet connection is not subjected to shape deformation but just twist increment. In addition, the initial strong normal shock on the winglet has been significantly weakened.The sizes of several 3D bumps have decreased due to a weaker shock wave, particularly at places inboard of the wing. On the other hand, the optimiser produces larger-size 3D bumps that are located towards the outboard of the outer wing and at the winglet, where the shock waves are still relatively strong. The varying heights of the 3D bumps are listed in Table 2. Note that the 3D bump numbered 1 is positioned closer to the inboard and the 3D bumps with increasing numbers (up to number 10) are positioned progressively towards the outboard. The last three bumps (11-13) are placed on the winglet.All the 3D bumps started with a height of 0⋅6%c . Once again, the reduced heights for most of the 3D bumps suggest a weak remaining shock in that region of the wing. On the other hand, the increasedblocks, which is to be run on the 128-processor queue on HPCx. The multiblock grid can be seen in Fig. 6 shown earlier. In addition, Fig. 7presents a clearer view of the distribution strategy of the grid resolution on the surface.Figure 8 shows the progression of the objective function, i.e. the drag coefficient with respect to the major design cycles. Due to the limitation of the maximum allowable computing time on a 128-processor queue on HPCx, the 19 design cycles shown in Fig. 8 were not carried out in one run but in a few runs. The optimisation converges after 19 design cycles when the SQP optimiser has indicated that an optimised solution has been found. Note that each improved design is a feasible design satisfying the constraints as we adopted a feasible optimisation strategy.Table 1 compares the aerodynamic coefficients of the optimised BWB shape with 3D bumps. First of all, it should be noted that in Refs 6 and 7, the calculated drag coefficient for the baseline configu-ration is different from the present calculations. This discrepancy is because the resolution of the high-fidelity Euler grid (around 100thousands points) employed in Refs 6 and 7 is much lower than the resolution of the current high-fidelity Euler grid, which has over 2m points. As stated earlier, this level of resolution is required to resolve the shapes of the 3D bumps. As shown in Table 1, the optimised design has provided a significant drag reduction of 30% or around 47 drag counts from the baseline configuration. Since in this optimi-sation problem, the pitching moment is not considered as a constraint, it has slightly increased. When the 3D bumps are taken away manually from the optimised wing shape, calculations indicate that the drag increases by around one drag count. Therefore, the improvement from the 3D bumps still account for around 1% of the total drag. This could still be significant for a large wing-body configuration such as this BWB. Additionally, it should also be noted that the heights for the 3D bumps at the winglet are limited to a certain height due to possible grid quality degradation when the height is over a certain limit. Therefore, this approach may have some impact on the overall performance of the 3D bumps, since the shock remains fairly strong at the winglet.Figure 8. Optimisation history of the objective function.Table 1Comparison of performance, M ∞= 0⋅85, C L = 0⋅41C LC D L /D C M Baseline (present high-fidelity grid)0⋅41120⋅0155426⋅460⋅09715Present optimised shape with 3D bumps0⋅41150⋅0108837⋅820⋅12301Present optimised shape (3D bumps manually removed)0⋅41110⋅0109937⋅410⋅12223Optimised shape without C M constraint (Refs 6 and 7)0⋅41130⋅0122233⋅660⋅14330Optimised shape with C M constraint (Refs 6 and 7)0⋅41140⋅0127232⋅340⋅02178Figure 9. Left —baseline configuration; Right —optimised design.The improvements on the winglet are shown more clearly in Fig.12. The pressure contour near the root of the winglet is less clustered than before in the optimised design, implying a much-weakened shock wave. As a result, a weaker shock wave is now reflected at the outboard of the outer wing. However, due to the limitation of shape deformation at the winglet tip, a strong shock wave remains there.Note that the constraint on the maximum winglet thickness is 10%c while the original aerofoil of the winglet is NACA0012.The shape of a section near the main body and a section close to the outboard of the outer wing with some visible changes are displayed in Fig.14. The obtained improvements in aerodynamic performance are significant even though the shape changes are relatively small. Fig. 13 shows the shape changes at the winglet. In addition to the significant shape changes, it also shows that the winglet tip has been twisted slightly outwards.ones (bumps 9-13) imply a fairly strong remaining shock. The position of the crests of each 3D bumps varies between 5-7%c downstream of the original shock wave. The chordwise length of the 3D bumps all remains in the range of 35-36%c . As for the bump width, changes are not apparent, where the values lie close to 15%c with variations less than 0⋅2%c . It should be noted that the bump tips of the consecutive 3D bumps are very close to each other and,therefore, the bump width more or less represents the spacing between the centreline of consecutive 3D bumps. Figure 11 presents the close-up view of a number of 3D bumps on the surface of the outer wing.The preceding discussions are based on inviscid Euler calcula-tions. If the viscous effects were taken into account, the shock strength will be weakened and hence displaced slightly upstream as compared to the inviscid case. Consequently, the positions of the 3D bumps can be adjusted upstream with response to the displaced original shock wave such that the relative positions between the original shock wave and bump crests are maintained. Additionally,due to the weakened shock wave and viscous effects, it is also necessary to lower the heights of the 3D bumps. Qin et al (16)have demonstrated that an effective 3D bump could achieve significant amount of wave drag or pressure drag reduction that is only accom-panied by a negligible skin friction drag penalty.Figure 11. Close-up view of the 3D bumps.Table 2List of 3D bump heights.3D bump No.Height y /c %10⋅3320⋅2130⋅2340⋅2650⋅3560⋅4670⋅4980⋅4990⋅63101⋅09110⋅89120⋅89130⋅88Figure 10. Computed shock wave structure on the upper surfaces of left —baseline configuration; right —optimised design.Figure 12. Improvements at the winglet. Left —baseline configuration; Right —optimised design.Figure 13. Profile changes on the wing.ACKNOWLEDGEMENTSThe computer time is provided by the UK high performance computing facility (HPCx) through the Applied Aerodynamics Consortium (UK AAC) under EPSRC Grant GR/S91130/01. We would like to acknowledge supports from BAE Systems and Airbus UK on shock control research at Sheffield.REFERENCES1.P ORTSDAM , M.A., P AGE , M.A. and L IEBECK , R.H. Blended wing body analysis and design, 1997, Paper AIAA-1997-2317, Aerospace Sciences Meeting and Exhibition, Reno, NV.2.B IKSYNOVSKYM , A.L., B UZOVERYA , N.O., G UREVICH , B.I., D ENISOV ,V.E., D UNAEVSKY , A.I., S HKADOV , L.M., S ORIN , O.V., U DZHUZHU , A.J.and Z HURIHIN , J.P.Flying wing-problems and decisions, Aircr Design ,December 2001, 4, pp 193-219.3.S MITH , H. College of Aeronautics Blended Wing Body Development Programme, 2000, ICAS Paper 1.1.4, International Council of the Aeronautical Sciences 2000 Conference.4.Q IN , N., V AVALLE , A. and L E M OIGNE , A.Spanwise lift distribution for blended wing body aircraft, J Aircr , March-April 2005, 42, (2), pp 356-365.5.L E M OIGNE , A. and Q IN , N.Variable-fidelity aerodynamic optimisation for turbulent flows using a discrete adjoint formulation, AIAA J , July 2004, 42, (7), pp 1281-1192.8.0CONCLUSIONAn Euler aerodynamic optimisation problem with a large number of design variables has been carried out on a high-performance parallel computing facility. The scale of the problem, which has a grid resolution of over 2m mesh points and over 650 design variables, highlights the importance to parallelise the main computational components in the optimisation loop, i.e. the flow solver and the adjoint solver. It is demon-strated that both of the parallel efficiencies of the two solvers are reasonably good for the given problem up to 256 processors. Results from the optimisation of the BWB shape with 3D bumps, which also includes optimising the winglet profiles, have demonstrated that the parallelised optimisation setup is able to work on large-scale aerody-namic problems efficiently. The optimised design has shown some inter-esting improvement on the outer wing and the winglet with ~30% drag reduction being achieved for the given fixed planform design. The designs of the 3D bumps vary across the outer wing and winglet, which indicate the strength of the remaining shock in the region. For example,the 3D bumps placed near the outboard of the outer wing and at the winglet have significantly larger heights since the remaining shock is still strong at these locations. The optimisation has modified the design of the winglet aerofoil sections substantially due to the much lower local mean sweep angle. The tip of the winglet is slightly twisted outwards.However, the strongest shock remains on the inside of the winglet, which can be relieved by introducing some trailing edge sweep for the winglet.Figure 14. Profile changes at the winglet.6.Q IN, N., V AVALLE, A., L E M OIGNE, A., L ABAN, M., H ACKETT, K. andW EINERFELT, P.Aerodynamic considerations of blended wing body aircraft, Prog in Aerospace Sciences, 2004, 40, (6), pp 321-343.7.L E M OIGNE, A. and Q IN, N. Aerofoil profile and sweep optimisation fora blended wing-body aircraft using a discrete adjoint method, AeronautJ, 2006, 110, (1111), pp 589-604.8.M ORRIS, A. MOB a European distributed multi-disciplinary design andoptimisation project, 2002, Paper AIAA-2002-5444, Ninth AIAA/ISSMO Symposium on Multidisciplinary Analysis and Optimization, Atlanta, GA.9.Q IN, N., Z HU, Y. and S HAW, S.T.Numerical study of active shockcontrol for transonic aerodynamics, Int J o f Numerical Metho ds fo r Heat and Fluid Flow, 2004, 14, pp 444-466.10.F ULKER, J.L. and S IMMONS, M.J. An experimental study of shockcontrol methods, 1994, DRA/AS/HWA/TR94007/1.11.D IMA, C. and DE M ATTEIS, P. Effects of shock and boundary-layercontrol techniques on transonic flows about airfoils, 2000, Paper AIAA-2000-0517, 38th Aerospace Sciences Meeting and Exhibition, Reno, NV.12.B IRKEMEYER, J., R OSEMANN, H. and S TANEWSKY, E. Shock control on aswept wing, J Aerospace Sci And Tech, 2000, pp 147-156.13.S TANEWSKY, E., D ELERY, J., F ULKER, J.L. AND DE M ATTEIS, P.Dragreduction by shock and boundary layer control, Results of the ProjectEUROSHOCK II, No tes On Numerical Fluid Mechanics andMultidisciplinary Design, 80, Springer.14.Q IN, N., M ONET, D. and S HAW,S.T. 3D bumps for transonic wing shockcontrol and drag reduction, 2002, CEAS Aerospace Aerodynamics Research Conference.15.H OLDEN, H.A. and B ABINSKY, H. Shock/boundary layer interactioncontrol using 3D devices, 2003, Paper AIAA-2003-447, 41st Aerospace Sciences Meeting and Exhibition, Reno, NV.16.Q IN, N., W ONG, W.S. and S ELLARS, N.Validation and optimisation of3D bumps for transonic wing drag reduction, 2005, CEAS/K ATnet Conference on K ey Aerodynamic Technologies, 20-22 June 2005, Bremen, Germany.17.W ONG, W.S., Q IN, N. and S ELLARS, N. A numerical study of transonicflow in a wind tunnel over 3D bumps, 2005, Paper AIAA-2005-1057, 43rd Aerospace Sciences Meeting and Exhibition, Reno, NV.。