汽车覆盖件冲压成形的数值模拟
基于仿真技术的汽车覆盖件冲压成形研究

陷
图 l 汽 车覆 盖件模具仿 真设计流程
本文对圆筒形件进 行计 算机仿真 的主要过程 为 :首 先在三维建模软件 C TA中建立零 件的几何模 型 ,转 入 AI 到冲压仿真软件 D nf m 中,然后在 冲压过程的力学模 ya r o 型基础上划分 网格构建 有限 元模 型。选择板 料的特性 参 数 ,设置成形工具 ( 如凹模 、凸模和压边圈等) ,设置包 括载荷 、模具的运动控制和边 界条件等在 内的成形参数 , 提交求解器进行计 算 ,最后对后 处理结 果进行分 析,评 估成形效果 ,从而得出相关分析结论和改进措施 。
压料 面和 工艺 补充 面 设计 布置 拉深 筋和 工艺 切 口 确 定成 形 工艺参 数 有限 元分 析 成 形无 缺 陷
汽车的三大总成 ,汽车车身是一个形 状复杂 的空间薄壁 壳体 ,它的主要零部件均 由钢板 、铝 合金板料 等冲压焊 接而成 ,然后进行涂漆 以增加美 观和 防蚀性 ,最后装上 各种 内饰件 ,形成完整 的车身 。 汽车 覆盖 件 主要是 指构 成驾 驶 室和 车身 的表 面零
维普资讯
p fDACP 2 ltoAC/P 垒 垒 f /MA C 。 I
鏖 旦
基 于 仿 真 技 术 的 汽 车 覆 盖 件
冲 压 成 形 研 究
南京工业大学 ( 江苏 2 0 1 ) 刘世豪 10 6
开发周期 ,降低 开发 成 本 方面 发挥 了越来 越 重要 的作
3 .圆筒形件冲压成形仿真的实现与分析
现以用 于某汽车油箱 的圆筒 形件 为例 ,对板料 冲压
2 汽车覆盖件冲压成形的仿真方法 .
汽车覆盖件大都是空间 曲面结构 ,形状 复杂 ,从而 决定 了在冲压成形过程 中的变形 复杂性 ,变形规 律难 以
基于 Dynaform 的汽车覆盖件冲压成型数值模拟及优化

基于 Dynaform 的汽车覆盖件冲压成型数值模拟及优化∗熊保玉【摘要】It has gradually been paid more attention to study forming law for automobile panel by applying numerical simulation.Left and right inner plates on automobile rear wheels are investigated,the stamping process of auto rear wheel is simulated based on Dynaform software.Simulation of stamping forming by changing magnitude of blank holder force and setting drawbead,predicting wrinkle,fracture,thinning,rebound and other defects is done.Blank holding force and draw-bead of process and technical parameters of left and right inner plates on automobile rear wheels are determined by compa-ring the simulation results,and it provides a scientific basis for the practical products shaping.%应用数值模拟技术对汽车覆盖件成型规律进行研究逐渐受到重视。
以汽车左、右后轮罩内板为研究对象,介绍了应用 Dynaform 软件对轮罩冲压成型进行数值模拟的步骤。
通过模拟产品在设置不同压边力数值及有、无拉延筋情况下的成型性能,预测板料成型中可能出现的如起皱、拉裂、变薄和回弹等缺陷问题。
汽车覆盖件冲压工艺数值模拟技术实例分析培训讲学
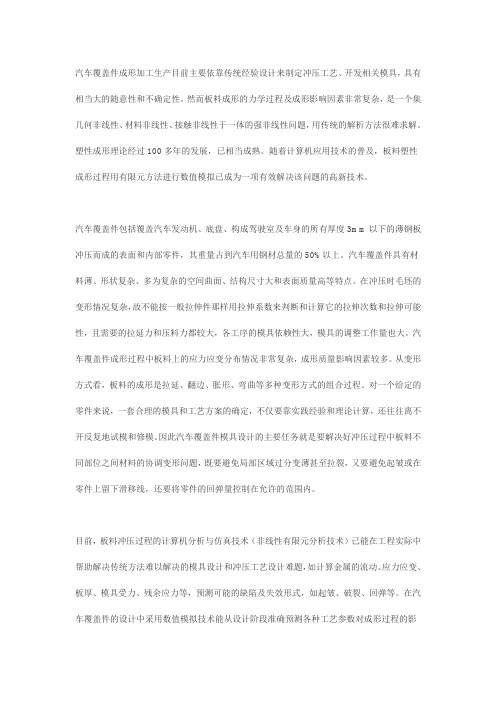
汽车覆盖件成形加工生产目前主要依靠传统经验设计来制定冲压工艺、开发相关模具,具有相当大的随意性和不确定性。
然而板料成形的力学过程及成形影响因素非常复杂,是一个集几何非线性、材料非线性、接触非线性于一体的强非线性问题,用传统的解析方法很难求解。
塑性成形理论经过100多年的发展,已相当成熟。
随着计算机应用技术的普及,板料塑性成形过程用有限元方法进行数值模拟已成为一项有效解决该问题的高新技术。
汽车覆盖件包括覆盖汽车发动机、底盘、构成驾驶室及车身的所有厚度3mm以下的薄钢板冲压而成的表面和内部零件,其重量占到汽车用钢材总量的50%以上。
汽车覆盖件具有材料薄、形状复杂、多为复杂的空间曲面、结构尺寸大和表面质量高等特点。
在冲压时毛坯的变形情况复杂,故不能按一般拉伸件那样用拉伸系数来判断和计算它的拉伸次数和拉伸可能性,且需要的拉延力和压料力都较大,各工序的模具依赖性大,模具的调整工作量也大。
汽车覆盖件成形过程中板料上的应力应变分布情况非常复杂,成形质量影响因素较多。
从变形方式看,板料的成形是拉延、翻边、胀形、弯曲等多种变形方式的组合过程。
对一个给定的零件来说,一套合理的模具和工艺方案的确定,不仅要靠实践经验和理论计算,还往往离不开反复地试模和修模。
因此汽车覆盖件模具设计的主要任务就是要解决好冲压过程中板料不同部位之间材料的协调变形问题,既要避免局部区域过分变薄甚至拉裂,又要避免起皱或在零件上留下滑移线,还要将零件的回弹量控制在允许的范围内。
目前,板料冲压过程的计算机分析与仿真技术(非线性有限元分析技术)已能在工程实际中帮助解决传统方法难以解决的模具设计和冲压工艺设计难题,如计算金属的流动、应力应变、板厚、模具受力、残余应力等,预测可能的缺陷及失效形式,如起皱、破裂、回弹等。
在汽车覆盖件的设计中采用数值模拟技术能从设计阶段准确预测各种工艺参数对成形过程的影响,进而优化工艺参数和模具结构,缩短模具的设计制造周期,降低产品生产成本,提高模具和冲压件产品品质。
汽车覆盖件冲压成形及其仿真研究
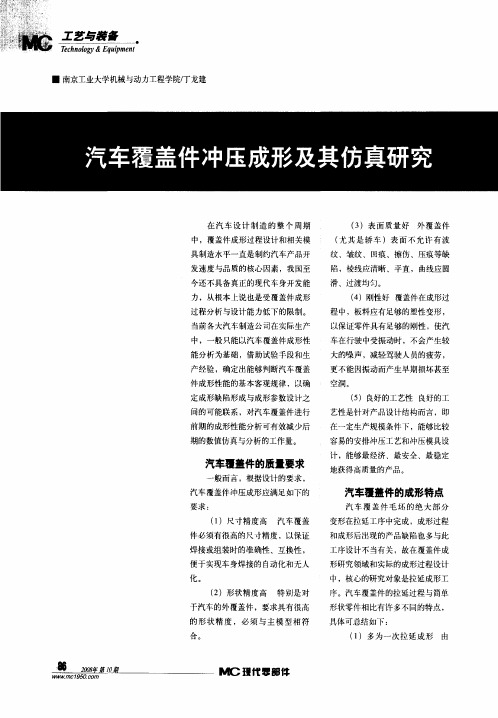
图1板料起皱类型
2破 裂 .
破裂是拉深失稳在薄板冲压成形中的主要表现形式 。在板料成形过 程 中,随着变形的发展 ,板料 的承载面 积不断减小 ,其应变强化效应却
不断增加。当应变强化效应的增加 能够补偿承载面积缩减时 ,变形稳定
廓 内部带有局部形 状特征 ,这 对成 形控制技 术提 出更 多更高的要 求。
类 ,如 图 1 示 。 所
( )多 为拉 深 、胀形 的 复合 2 过程 汽车覆盖 件成 形过 程中毛坯
变形 并不是简单 的拉深 ,而 多是拉
深和胀形同时存在 的复合成形。
( )成形 过程 中常伴 有 多处 3
局部成形 由于车身的美观性和功能 性等 特殊需要 ,很 多覆盖件整 体轮
大小及主应 变之比等也随 之不断改 变 ,故毛坯材 料在拉延过程 中的路 径也不断变化。
束时 ,在毛坯体积 内,尤其是板料厚度方向上存在着残余应力。未脱模
时 ,这些残 余应 力与工具的接触力保持平衡关系。当工具 被释放后 ,拉 延件将寻找新的应力平衡位置 ,即局部应力的释放 ,随之导致成形件的
期的数值仿真与分 析的工作量。
汽车覆盖件的质量要求
一
地获得高质量的产 品。
般而言 ,根据设计的要求 ,
汽车覆盖件冲压成形应满足如下的 要求 :
汽车覆盖件的成形特点
汽 车 覆 盖 件毛 坯 的 绝大 部 分
( )尺 寸精度高 汽 车覆盖 1
件必须有很高的尺寸精度 ,以保证 焊接或组装时的准确性 、互换性 , 便于实现车身焊接的 自动化和无人
外覆盖件来说 ,多次拉延 易形成的
冲击线和 弯曲痕迹线也会 影响喷漆 后的表面 质量 。因此 ,汽 车覆盖件
汽车覆盖件冲压成形仿真研究及工程应用的开题报告

汽车覆盖件冲压成形仿真研究及工程应用的开题报告一、选题背景及意义汽车产业是国民经济中的重要部分,汽车零部件制造在汽车产业中占有重要地位。
而汽车覆盖件则是汽车外观设计中重要的组成部分,具有保护车身、美化外观等多重功能。
汽车覆盖件冲压成形是目前汽车覆盖件生产的主要工艺之一,如何提高汽车覆盖件冲压成形的质量和效率,是汽车覆盖件制造企业需要解决的关键技术问题。
汽车覆盖件冲压成形的仿真模拟可以帮助企业在减少试制样件、提高成形工艺效率基础上,优化冲压工艺参数、降低生产成本,最终提高汽车覆盖件的成形质量。
因此,本文选取了“汽车覆盖件冲压成形仿真研究及工程应用”作为研究对象。
二、研究内容1. 汽车覆盖件冲压成形的工艺分析通过对汽车覆盖件冲压成形工艺的分析,掌握汽车覆盖件的成形原理和工艺参数的影响规律。
2. 汽车覆盖件冲压成形仿真模型的建立采用商业有限元软件,建立汽车覆盖件冲压成形的仿真模型,并进行仿真计算。
3. 汽车覆盖件冲压成形仿真结果及分析对汽车覆盖件冲压成形仿真结果进行分析,掌握汽车覆盖件的成形变形规律和成形缺陷形成原因。
4. 汽车覆盖件冲压成形仿真分析在工程应用中的探讨依据仿真分析结果,探讨汽车覆盖件冲压成形仿真在工程应用中的可行性和实际应用效果,为企业提供冲压成形技术改进的方法。
三、研究方法1. 文献综述法通过查阅文献和资料,对汽车覆盖件冲压成形的工艺流程、成形原理、影响参数等进行了解和梳理。
2. 有限元方法采用有限元软件建立汽车覆盖件冲压成形仿真模型,并进行仿真计算。
3. 实验验证法通过对模拟仿真结果的实验验证,探究实际生产中的可行性和优化效果。
四、拟定时间计划1. 前期准备(1个月)查阅文献、了解相关领域常用软件、组建研究小组。
2. 研究设计(3个月)对汽车覆盖件冲压成形的工艺流程、成形原理、影响参数等进行研究和分析,并建立有限元仿真模型。
3. 数据分析和处理(2个月)对有限元仿真结果进行分析和处理,探讨冲压成形的缺陷和变形原因。
基于AutoForm汽车覆盖件冲压成形模拟分析

析, 并对 C A D模 型进行 工艺补 充。 通过对计算 结果的查看 , 为可能 出现 的成形缺陷进行 预判, 为在 实际生产所设计 的冲 压成形各项参数 的确 定提供依据 。与传统的工艺设计 方法相 比 , 缩短 了模 具设计的周期 , 减 少 了试模 的次数 , 节 约了企
从而省去 了工程人员繁琐的网格划分过程 , 有 汽车在国民经济中的地位非常重要 , 它是评价一 功能, 个 国家制 造业水平 的标志之一 。汽车覆盖件 是汽车 的 利于使工程师将更多的时间用于其它 的工作上 , 尤 重要组 成部分 ,它是 将金属板 料利用模具在 成型设备 其适合复杂的深拉延和拉伸成形[ 4 1 。 中冲压而成形 , 其过程是一个集几何非线性以及边界 而且 A u t o F o r m 4 . 6的结果 生成 观察 十分 直观 , 可 条件非线性等问题为一体的复杂力学过程。 目 前覆盖 直 接查 看 板 料 的应力 、 应变 图, 板 料减 薄 情 况 , 以及
件模具 已成为 开发新车 型的关 键环节I 。
对板 料模 拟全 过程 进行 动 画显示 等『 5 1 。
1 . 2 汽 车 覆盖件 三维 模型及 其特 点
随 着科 学 技术 的不 断发 展 ,尤 其 是 最 近 十多 年
以某 汽车 覆盖 件为研 究 对象 , 利用 U G对 其 进行 有限元技术的不断完善 ,与其相适应 的是一些通用 及 专用 的板料 冲压 仿真 软件 ,如 D y n a f o r m、 A b a q u s、 i维建模 , 图1 为其三维数据模型 , 材料为汽车覆盖 F a s t a m p和 A u t o F o r m等 的出现 , 板 材 的 冲压 成 形有 限 件 常用材 料 D C 0 4 , 料厚 为 1 m m, 尺寸 约为 7 1 0m m x 元 分析 及数值 模拟 已逐渐 地进 入 了现实 生产 当中 , 它 9 4 m m x 1 0 m m, 外形 不 规 则 , 以拉 伸 为 主要 成 形 方
汽车覆盖件冲压成形仿真的应用与研究

机 械 设 计 与 制 造
一
第 5期 20 0 8年 5月
8 一 8
Ma hi e y De i n c n r sg
&
Ma u a t r n f cu e
文章编号 :0 l 3 9 (0 8 0 — 0 80 10 一 9 7 2 0 )5 0 8 — 3
函数的 速率本构方程可表示为:: 盯= e p s
~
() 4
() 5
L 6
~ 一
e
p
=
e p
一 一 —
设计 、 模具设计提供可靠 的判据 和合理 的工艺参数 , 已成 为当前 覆盖件工艺设计 、 模具设计 中一种重要手段。 通过在D N F R Y AO M 软件中对某汽车右侧壁上外板进行 冲压仿真 ,阐述了实现板料 成形有 限元仿真的基本步骤和仿真分析过程 中的一些关 键技术
汽 车覆 盖件 冲压 成 形仿 真 的应 用与研 究
刘世 豪 王 东方 苏 小平 徐 练 ( 京工业 大 学 机械 与 动力工 程 学院 , 南 南京 2 0 0 ) 10 9
T ea pia ina d r s a c fh t mpn r s mua inf r u o h p l t n e r ho esa c o e t igf m i lt t mo ieb d a es O o o a t o yp n l v L U S iho WA G D n —ag S io pn , U La N nigU ies yo e h o g , aj g2 0 0 , h a I h- a , N o g fn ,U X a— ig X i n( aj nvri f c n l y N ni 10 9 C i ) n t T o n n
基于DYNAFORM的汽车车身覆盖件冲压成形数值模拟
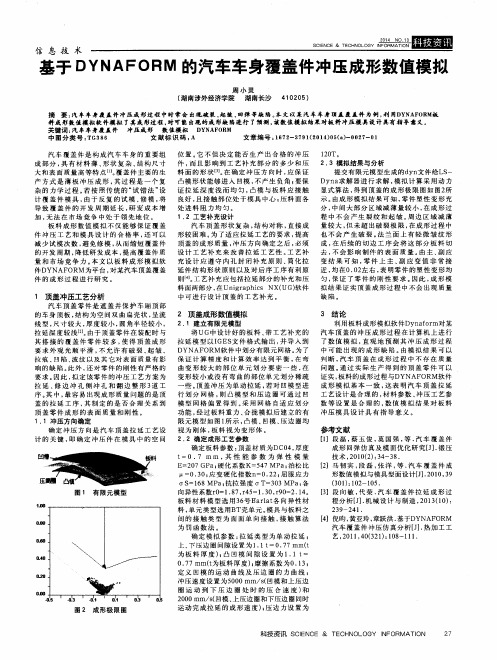
S C I E N C E & T E C H N O L 0 G Y
基于 D Y N A F O R M 的汽 车车 身覆盖 件冲 压成形 数值 沙
4 1 0 2 0 5 )
摘 要: 汽车车 身覆盖 件冲 压成 形过程 中时 常会 出现破 裂 , 起 皱 回弹 等缺 陷 。 本 文 以某汽 车 车身顶 盖晨 盖件 为例 , 利 用D Y N A F O R M ;  ̄ ; . . 料成 形数值模 拟软 件模 拟 了其成 形过 程 , 对可 能 出现 的成形缺 陷进行 了预 测, 该数值 模拟 结果对板 料 冲压模具设 计 具有指导 意义 。 关键词 : 汽车车 身覆 盖件 冲压成 形 数值模拟 D Y N A F O R M 中 图分 类 号 : T G 3 8 6 文 献标 识 码 : A 文 章编 号 : I 6 7 2 — 3 7 9 l ( 2 0 1 4 ) 0 5 ( a ) 一0 0 2 7 —0 1 汽 车 覆 盖 件 是 构 成 汽 车 车 身 的 重 要组 成部分 , 具有材料薄 、 形状复杂 、 结 构 尺 寸 大 和 表 面 质量 高等 特 点 … 。 覆盖 件 主 要 的生 产 方式是薄板 冲压成形 , 其 过 程 是 一 个 复 杂 的力学过程 。 若按 照传统的“ 试错法 ” 设 计 覆盖件模具 , 由于 反 复 的 试 模 、 修模 , 将 导致 覆盖件 的开发周期延 长 , 研 发 成 本 增 加, 无 法 在 市 场 竞 争 中处 于 领 先 地 位 。 板 料 成 形 数 值 模 拟 不 仅 能 够 保证 覆 盖 件 冲压工艺和 模具设计 的合格率 , 还 可 以 减少试模次数 , 避 免修 模 , 从 而 缩 短 覆 盖 件 的开 发 周 期 , 降 低研 发 成 本 , 提 高 覆 盖 件 质 量 和市场竞争 力。 本 文 以板 料 成 形 模 拟软 件D YNAF 0R M为 平台 , 对 某 汽车 顶 盖覆 盖 件 的成形过程进行研 究。 位置 。 它 不 但 决 定 能 否 生 产 出合 格 的 冲 压 件, 而 且 影 响 到 工 艺 补 充 部 分 的 多 少 和 压 料面的形状I 3 】 。 在确 定冲压方向时 , 应 保 证 凸模 形 状 能够 进 入 凹模 , 不产生负角; 要 保 证拉延深 度浅而均 匀, 凸模 与 板 料 应 接 触 良好 , 且接 触 部 位 处 于 模 具 中 心 ; 压 料 面 各 处进料 阻力均匀 。 1 . 2 工艺补 充设计 汽车 顶 盖 形状 复 杂 , 结构对称 , 直 接 成 形较困难。 为 了适 应 拉 延 工 艺 的要 求 , 提 高 顶 盖 的 成 形 质量 , 冲 压 方 向确 定 之 后 , 必 须 设计工 艺补充来 改善拉延工艺性 。 工 艺 补 充 设 计 应 遵 守 内孔 封 闭 补 充 原 则 、 简 化 拉 延 件 结 构 形 状 原 则 以及 对 后 序 工 序 有 利 原 则 …。 工 艺补 充 应 包括 拉 延 部 分 的补 充和 压 料面 两部 分 , 在 Un i g r a p h i c s NX( UG) 软 件 中可 进 行 设 计 顶 盖 的 工 艺 补 充 。
- 1、下载文档前请自行甄别文档内容的完整性,平台不提供额外的编辑、内容补充、找答案等附加服务。
- 2、"仅部分预览"的文档,不可在线预览部分如存在完整性等问题,可反馈申请退款(可完整预览的文档不适用该条件!)。
- 3、如文档侵犯您的权益,请联系客服反馈,我们会尽快为您处理(人工客服工作时间:9:00-18:30)。
汽车覆盖件冲压成形的数值模拟
作者:王家昆李琦胡东勇罗英李再参
一、引言
对于制造业来说,21 世纪竞争的核心将是新产品的竞争。
围绕新产品的竞争,一场以信息技术为特征的新的制造业革命正在全球波澜壮阔地展开。
如何实现高质量、低成本、短周期的新产品开发,是赢得这场竞争的关键。
汽车覆盖件与一般薄板拉伸件相比,具有材料相对厚度小、结构尺寸大、形状复杂、尺寸精度和表面质量要求较高的特点。
其零件大多是由复杂的空间自由曲面组成,成形时,坯料上各部分的变形复杂、差别较大,各处应力也很不均匀,使零件的冲压工艺性较差,拉伸过程中容易产生起皱或破裂现象。
车身覆盖件的成形过程涉及几何非线性、材料非线性和复杂的接触与摩擦等问题,在传统的冲压生产过程中,无论是覆盖件模具的设计、制造,还是坯料形状和尺寸的确定,冲压工序、工艺参数的规划,都要设计制造原型,经过多次试生产和多次调试修正才能确定,这是一个试错逼近的过程,造成人力、物力和财力的大量消耗,生产成本高,周期长,质量不易控制。
随着计算机技术的不断发展,计算机辅助工程(CAE) 已广泛应用于板料成形过程分析,不仅可用于后期的工艺分析及模具设计,也可用于产品设计阶段,以确保零件具有较好的冲压成形工艺性。
预先在计算机上进行实际生产过程模拟,可在计算机屏幕上观察毛坯的成形过程,预示汽车覆盖件零件冲压成形的可行性,然后通过少量试模验证,就可得出较可靠的可行性结论。
现使用法国ESI 公司开发的PAM-STAMP 2G商业化专业板料冲压成形软件对汽车后盖内覆盖件进行冲压模拟分析。
二、数值模拟
1、PAM-STAMP 2G软件简介
PAM-STAMP 2G软件的新的系统框架可以在各模块之间进行无缝数据交换,还提供了可以客户化的应用程式编程界面。
PAM-DIEMAKER 通过参数迭代的方法获得实际的仿真模型,能在几分钟内生成模面和工艺补充面,并快速分析判断零件有无过切(负角) ,并计算出最佳的冲压方案,然后可非常简单地对模面和工艺补充面的几何形状进行修改,并参数化地完成所有前期模具设计的控制。
PAM-QUIKSTAMP 提供的是一个快速成形分析,在精度、计算时间、计算结果三者之间折衷出最优的方案,能让模具设计师快速检查和评估其模具设计,包括模面和工艺补充部分以及其他模具设计的合理性。
PAM-AUTOSTAMP 可为用户提供在实际工业条件下,如考虑重力影响、压料过程、多步成形、各种拉伸、切边、翻边和回弹等复杂情况下的可视化冲压成形模拟。
2、汽车覆盖件冲压成形数值模拟流程
汽车覆盖件冲压成形数值模拟流程见图1。
图1 汽车覆盖件冲压成形数值模拟流程
3、汽车覆盖件拉伸工艺及选择参数应注意的问题
(1) 选用合理、经济的覆盖件材料。
汽车覆盖件的拉伸实际就是以金属的塑性性能为基础的冲压加工,因此一般选用屈服点ζs 和屈服强度ζs/ ζb 较低,伸长率δ、厚向异性指数n 较高的薄板材料。
(2) 覆盖件的拉伸深度。
在符合产品尺寸的条件下尽可能平缓均匀,让各处的变形程度趋于一致。
(3) 拉伸方向。
覆盖件拉伸方向的确定,不但决定能否拉伸出满意的拉伸件,而且影响到工艺补充部分的多少和压料面的形状,合理的拉伸方向应从以下几方面考虑:a) 保证凸模能够进入凹模,当覆盖件有局部凹形或反拉伸要求时,覆盖件本身的凹形和反拉伸要求就决定了拉伸的方向。
a) 凸模与毛坯在开始拉伸时,应保证良好的接触状态。
拉伸开始时,凸模与毛坯保持较大的接触面积,并位于凸模中心部分,这样毛坯才不易发生局部应力集中而使零件产生破裂,而且材料能均匀地拉入凹模,不会因毛坯发生挪动而影响拉伸质量。
毛坯能完整地贴紧凸模,拉伸后可获得完整的凸模形状。
(4) 正确确定压料面的形状。
压料面是覆盖件工艺补充面的一个组成部分,即位于凹模圆角半径以外的那一部分毛坯。
拉伸前,压料圈将要拉伸的毛坯压紧在凹模压料面上,不形成皱纹或折痕,在拉伸过程中,压料面逐步进人凹模内,同时尽可能降低拉伸深度,保证进入凹模的材料不皱、不裂,获得合格的拉伸件。
因此确定压料面要做到如下几点:a) 压料面尽可能为平面、圆柱面、圆锥面或曲率很小的双曲面等可展面,当毛坯被压紧时,不应该产生皱纹或扭曲现象,以便材料向凹模内顺利流动。
b) 压料面与拉伸凸模的形状应保持一定的几何关系,保证在拉伸过程中毛坯始终处于拉胀状态,拉入凹模内的材料不会多料,也就不会产生皱纹。
(5) 合理增加工艺补充面。
工艺补充面的作用在于改善覆盖件拉伸时的工艺条件,使材料各处变形均匀,也是拉伸后修边和翻边工序的需要。
因工艺补充面在拉伸后要被修掉,所以应尽量少用工艺补充面,节约材料。
同时,在尺寸满足的情况下,应尽量采用浅拉伸,让制件容易成形。
三、实例
1、模型的建立与计算条件
在UG软件中完成汽车后盖内覆盖件的几何建模,并修改处理成拉伸工序件模型,包括冲压方向、压料面、工艺补充面等,数字模型用IGES 格式导入PAM-STAMP 软件中,利用软件中的前处理工具来对几何模型进行网格划分,建立冲压成形的有限元模型凹模。
采用OFFSET或者TOOLS BUILDING方式形成凸模及压边圈的有限元模型。
图2 为汽车后盖内覆盖件冲模的有限元模型。
图2 模型
2、材料参数和边界条件
汽车后盖内覆盖件材料采用宝钢ST14 ,厚0. 8mm,杨氏模量E = 206 MPa ,泊松比ν= 0. 33 ,密度ρ= 7. 8 ×106 ,硬化系数K= 0. 59 MPa ,硬化指数n =0. 249 ,各向异性指数r0 = 1. 88 ,r45 = 1. 4 ,r90 = 2. 33 ,硬化曲线ζ= k (ε0 +εP) n。
边界条件如下:确定摩擦系数为0. 12 ,压边力为2 000 kN。
3、模拟结果
模拟可显示各加载时刻板料的变形、应力、应变分布及板料厚度变化和成形极限图等,其中厚度变化和成形极限是工程界最为关心的2 个物理量。
图3~图5 所示为计算机模拟冲压成形后的板厚分布,其中最薄处减薄量达65 % ,已处于破裂范围,起皱也非常明显。
图6 所示为成形后的应变分布; 图7 为成形后的应力分布; 图8 是拉伸成形后的成形极限图( FLC) ,图中成形曲线( FLC) 由材料参数和屈服理论确定,从图中8 可看出,制件已经处于破裂期。
图3 计算机模拟冲压成形后板厚分布
图4 计算机模拟冲压成形后板厚分布左下角局部放大图
图5 计算机模拟冲压成形后板厚分布右下角局部放大图
图6 计算机模拟冲压成形后应变分布
图7 计算机模拟冲压成形后应力分布
图8 计算机模拟拉伸成形后的成形极限图(FLC)
实际冲压结果图9、图10 是实际冲压零件照片。
通过实冲,验证了计算机模拟冲压成形分析的准确性,从图中可以看出,下部两角出现破裂,与数值模拟结果比较接近。
图9 实际冲压零件照片(中心的裂口为工艺裂口)
图10 实际冲压零件照片(右下角局部)
4、模具和工艺参数的调整与优化
从模拟结果和实际冲压结果可以看出: 成形件下面两角均出现明显的破裂和起皱,说明所设定的冲压条件(模具和工艺参数) 不合理,但应该调整哪些参数才能获得满意的结果?经过多次数值模拟知,在模具系统和工艺参数中,拉伸(冲压) 方向、压料面和工艺补充面的形状、压边力、拉伸筋、入模圆角、摩擦情况、冲压速度等参数对零件工艺性和质量有很大的影响,直接影响着零件起皱、破裂、表面皱纹和回弹等。
在覆盖件成形过程中,为了防止起皱,提高产品的刚性,一般都要通过采用拉伸筋的方式来控制材料的流动。
本例中,在压料面上,距凹模口25 mm处设置了1 圈拉伸筋,统一为圆筋形式,高度为10mm,为了便于以后根据不同的部位、不同的进料程度调整拉伸筋的阻力和筋的高度,在实际生产中,可以根据模拟结果在相应部位进行修磨。
在增加了拉伸筋后的模拟结果中,周边起皱情况得到了很好的控制,零件的成形质量得到了很大的改善,但是两角处的减薄加重,因此必须通过调整压边力、拉伸筋、模面和工艺补充面形状等来解决。
两角处的破裂是由于拉伸较深,进料困难,当拉应力过大时,便产生破裂。
通过多次调试,将压边力适当减小至1 800 kN,拉伸筋的高度降低为5 mm,阻力也相应减小,两角处能够有较多的进料。
通过这种压边力和拉伸筋调整,两角处的开裂得到了一定的改善。
经过多次模拟发现,仅仅依靠调整压边力和拉伸筋的设置,很难完全消除开裂,而在此处修改模面和工艺补充面的形状,却能够很好地满足减小进料阻力的要求。
后在两角处修改了工艺补充面,使其拉应力减小,从而使零件的起皱和破裂得到了解决。
经过上述模拟优化过程,得到了合格的成形件,如图11、图12 所示(从FLC图看,虽仍有破裂趋势,但不在产品范围内) 。
图11 修改模面后计算机模拟的冲压成形板厚分布
图12 修改模面后计算机模拟的拉伸成形极限图(FLC)
四、结束语
汽车覆盖件冲压成形的数值模拟,可以修改、优化工艺参数,提高模具设计制造质量,缩短模具制造、调试周期,降低制模成本。
现对汽车后盖内覆盖件冲压成形过程进行了模拟分析及实冲验证,模拟结果和实冲结果吻合较好,表明采用PAM-STAMP软件是可靠的,采用的方法是可行,说明利用数值模拟技术所得的结果是正确的,可以准确模拟汽车覆盖件冲压成形过程。
通过对汽车后盖内覆盖件的模拟,找到了引起拉裂缺陷的原因,并找到了消除缺陷的方法,通过对模具和工艺参数的调整和优化,给出了合理的工艺参数,优化了模面和工艺补充面,模拟结果为实际生产提供了较好的依据。
(end)。