甲醇合成铜基催化剂催化活性及失活研
甲醇合成催化剂失活分析
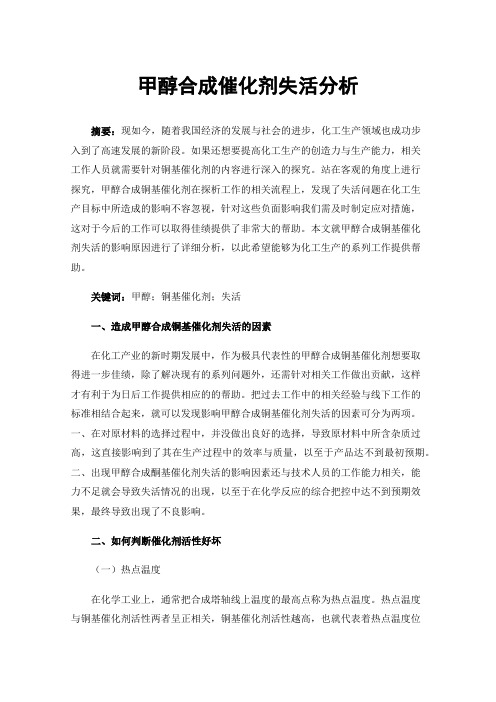
甲醇合成催化剂失活分析摘要:现如今,随着我国经济的发展与社会的进步,化工生产领域也成功步入到了高速发展的新阶段。
如果还想要提高化工生产的创造力与生产能力,相关工作人员就需要针对铜基催化剂的内容进行深入的探究。
站在客观的角度上进行探究,甲醇合成铜基催化剂在探析工作的相关流程上,发现了失活问题在化工生产目标中所造成的影响不容忽视,针对这些负面影响我们需及时制定应对措施,这对于今后的工作可以取得佳绩提供了非常大的帮助。
本文就甲醇合成铜基催化剂失活的影响原因进行了详细分析,以此希望能够为化工生产的系列工作提供帮助。
关键词:甲醇;铜基催化剂;失活一、造成甲醇合成铜基催化剂失活的因素在化工产业的新时期发展中,作为极具代表性的甲醇合成铜基催化剂想要取得进一步佳绩,除了解决现有的系列问题外,还需针对相关工作做出贡献,这样才有利于为日后工作提供相应的的帮助。
把过去工作中的相关经验与线下工作的标准相结合起来,就可以发现影响甲醇合成铜基催化剂失活的因素可分为两项。
一、在对原材料的选择过程中,并没做出良好的选择,导致原材料中所含杂质过高,这直接影响到了其在生产过程中的效率与质量,以至于产品达不到最初预期。
二、出现甲醇合成酮基催化剂失活的影响因素还与技术人员的工作能力相关,能力不足就会导致失活情况的出现,以至于在化学反应的综合把控中达不到预期效果,最终导致出现了不良影响。
二、如何判断催化剂活性好坏(一)热点温度在化学工业上,通常把合成塔轴线上温度的最高点称为热点温度。
热点温度与铜基催化剂活性两者呈正相关,铜基催化剂活性越高,也就代表着热点温度位置越高。
在其床层的上方位置反应物的浓度可以达到最高值,生成物的浓度相反确是最低点,这时所形成的运动反应是最剧烈的,铜基催化剂的温度也因此呈持续上升趋势。
当到达温度巅峰值后,生成物的浓度增加反应物的浓度降低,反应进程开始减慢。
反应的生成物热量被带走,床层的温度逐渐降低。
(二)铜基催化剂床层温差铜基催化剂的床层温度变化过大,就会造成部分床层温度达不到铜基催化剂活性温度的状况出现,这就会出现变化反应都集中在局部活性温度达标的地点,从而释放热量,因此化学反应越剧烈就会带动床层温度变化越大,铜基催化剂的活性温度也就因此变得更好了。
铜基催化剂的制备及其催化甲醇变换研究

铜基催化剂的制备及其催化甲醇变换研究近年来,铜基催化剂在催化领域中日益受到人们的关注。
铜作为一种廉价、易得、丰富的元素,具有很多种不同的氧化态,并能够形成不同的配位化合物,因此对于催化反应具有很好的应用前景。
本文将介绍铜基催化剂的制备及其在甲醇变换反应中的应用研究。
一、铜基催化剂的制备方法常用的制备铜基催化剂的方法有共沉淀法、沉淀还原法、浸渍法、脉冲喷雾法等。
其中,共沉淀法是一种常见的制备方法,其步骤简单,操作方便。
具体流程为:将金属铜盐和碱性沉淀剂(如氢氧化钠)按适当比例加入到有机溶剂中,并进行搅拌使其完全反应,然后过滤、洗涤、干燥即可得到催化剂。
沉淀还原法则是将金属铜盐与还原剂(如氢气)反应,使其还原为金属铜颗粒,可以得到高纯度、高催化活性的催化剂。
不过该方法操作性复杂,需要高温高压条件下进行。
浸渍法是将载体浸泡于预先配好的含有铜盐的溶液中,待溶液逐渐干燥后,再进行烧结,形成铜基催化剂。
该方法具有操作简便、催化活性较高等优点。
脉冲喷雾法则是一种新型的微粒制备技术。
利用电脉冲电压在短时间内将铜基溶液喷雾成微粒,并在空气中凝结,得到纳米级铜基催化剂,具有高比表面积、高分散度、可控制备等特点。
二、铜基催化剂在甲醇变换中的研究甲醇变换反应是将甲醇转化为一种更高级别、含碳量更高的化合物的过程,通常是甲醇制取甲烷、甲基氧化物或乙醇等。
铜基催化剂在该反应中具有重要应用价值。
铜基催化剂通常是将载体与合适的铜盐进行浸润或共沉淀,形成铜基催化剂。
同时,铜在反应中发挥的催化作用是氧化还原过程,其能够在反应中扮演氧化剂和/或还原剂的角色,控制反应中产物的选择性和活性。
由于甲醇转化反应的反应机理复杂,导致铜基催化剂的研究存在一定的困难,但是学术界已经取得了一系列的研究成果。
一项研究结果表明,以La2O3负载的Cu-Zn-Al催化剂对甲醇转化反应有较好的活性和选择性。
在该反应中,氧化铜被还原形成Cu0,并参与反应产生甲烷,较少生成二甲醇、甲醛等不必要的副产物。
甲醇合成铜基催化剂催化活性及失活研

甲醇合成铜基催化剂催化活性及失活研究1引言甲醇是一种极其重要的化工原料,主要用于生产一系列化工产品,还可用作潜在的车用醇醚燃料电池的燃料等。
随着甲醇制烯烃等技术进步及下游产品的开发,特别是甲醇燃料电池的开发和应用,合成甲醇的研究越来越受到广泛重视。
目前,甲醇的工业生产主要是采用CO/CO2催化加氢技术,所以甲醇合成催化剂的研发是甲醇合成工业的基石。
甲醇工业的发展很大程度上取决于催化剂的研制及其性能改进。
在甲醇生产中,很多工业指标和操作条件都是由催化剂的性质决定的。
随着甲醇工业的快速发展,对甲醇合成催化剂的研究开发提出了更高的要求。
2 甲醇合成催化剂在甲醇合成过程中,催化剂的重要性显而易见,目前工业上使用的甲醇合成催化剂一般可分为锌铬催化剂和铜基催化剂两类。
国外比较有名的研究和生产甲醇合成催化剂公司主要有英国ICI公司、德国BASF公司、德国SudChemie公司和丹麦TopsΦe公司等,国内研究铜基催化剂的院所主要有南化集团研究院、西南化工研究设计院,西北化工研究院及齐鲁石化研究院等[1]。
锌铬(ZnO/Cr2O3)催化剂由德国BASF公司于1923年首先开发研制成功。
操作温度必须在590 K~670 K,操作压力必须为25 MPa~35MPa,锌铬催化剂的特点是:耐热性能好、对硫不敏感,机械强度高,使用寿命长,使用范围宽,操作控制容易,但是其活性低、选择性低、产品中杂质复杂,精馏困难。
铜基催化剂由英国ICI公司和德国Lurgi公司先后研制成功,操作温度为210℃~300℃,压力为5MPa~10MPa,比传统的合成工艺温度低得多,对甲醇反应平衡有利。
其特点是:活性好,单程转化率为7%~8%;选择性高,大于99%,易得到高纯度的精甲醇;耐高温性差,对合成原料气中杂质比较敏感。
目前工业上甲醇的合成主要使用铜基催化剂。
近年来,新型催化剂的研制也在一直进行,新型催化剂的研制方向在于提高活性,改善热稳定性及延长催化剂使用寿命等,如钯系、钼系及低温液相催化剂,但这些催化剂因活性不理想或对甲醇的选择性较差,还只停留在研究阶段未实现工业化。
铜基甲醇合成催化剂的TPR研究

有最佳 c / n 即5 4 的铜基催化剂 , uZ ( / ) 其主还原温度最低。考察了在不同p H值时进行并流共沉淀 所制备的催化剂的Ⅱ), R 表明沉淀时的 p H值对催化剂的结构有很大影响, 并对其本质原 因 进行了深 入探讨。另外, 了铝含量对催化荆还原行为的影响以 考察 厦在不同升温速率下 催化荆 T R的差异。 P 关 键词 : 成 甲醇 ; 合 铜基催 化剂 ; 一步并 流共 沉 淀法
维普资讯
0 0 第20卷 第 3期 1 2年 5月
工 业 催 化
I DUS N TRI = 札 YS S AL CA r I
Ma 0 2 y2 0 v0. 0 No 3 11
铜 基 甲醇 合成 催 化剂 的 T R研 究 P
郭宪吉,叶长明,赵 蕾 , 向宇, 王 李利 民
GUO Xinj ,Y C an - i g,Z a -i E h g r n u HAO L i e ,WANG Xi gy an - u,LILi n - mi
( e at n f hmi r Z e gh uUnvr t H nnZ egh u4 0 5 , hn ) D pr me t e s y, h n o i s y, e a h n z o 5 0 2 C i oC t a ei a A src: r so p e—ae aa s t iee t u Z t ( oe weep p rdb n - bt t A s i f o p r sd ctl t wi df rn / nr i m l) r r ae yo e a ee c b ys h f C ao e
C C n mb rT 2 : Q 1 D ere t o eA A t l l 10 —14 (0 2 0 —02 —0 L u e : Q4 6 T 2 4 ouna d : ri ei 0 8 1 3 2 0 )3 0 5 4 c c D:
合成甲醇铜基催化剂及制备工艺研究进展
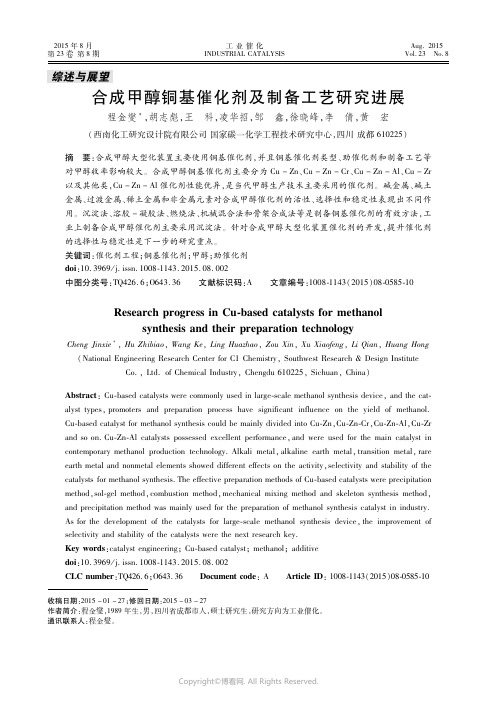
2015年8月第23卷第8期 工业催化INDUSTRIALCATALYSIS Aug.2015Vol.23 No.8综述与展望收稿日期:2015-01-27;修回日期:2015-03-27作者简介:程金燮,1989年生,男,四川省成都市人,硕士研究生,研究方向为工业催化。
通讯联系人:程金燮。
合成甲醇铜基催化剂及制备工艺研究进展程金燮 ,胡志彪,王 科,凌华招,邹 鑫,徐晓峰,李 倩,黄 宏(西南化工研究设计院有限公司国家碳一化学工程技术研究中心,四川成都610225)摘 要:合成甲醇大型化装置主要使用铜基催化剂,并且铜基催化剂类型、助催化剂和制备工艺等对甲醇收率影响较大。
合成甲醇铜基催化剂主要分为Cu-Zn、Cu-Zn-Cr、Cu-Zn-Al、Cu-Zr以及其他类,Cu-Zn-Al催化剂性能优异,是当代甲醇生产技术主要采用的催化剂。
碱金属、碱土金属、过渡金属、稀土金属和非金属元素对合成甲醇催化剂的活性、选择性和稳定性表现出不同作用。
沉淀法、溶胶-凝胶法、燃烧法、机械混合法和骨架合成法等是制备铜基催化剂的有效方法,工业上制备合成甲醇催化剂主要采用沉淀法。
针对合成甲醇大型化装置催化剂的开发,提升催化剂的选择性与稳定性是下一步的研究重点。
关键词:催化剂工程;铜基催化剂;甲醇;助催化剂doi:10.3969/j.issn.1008 1143.2015.08.002中图分类号:TQ426.6;O643.36 文献标识码:A 文章编号:1008 1143(2015)08 0585 10ResearchprogressinCu basedcatalystsformethanolsynthesisandtheirpreparationtechnologyChengJinxie,HuZhibiao,WangKe,LingHuazhao,ZouXin,XuXiaofeng,LiQian,HuangHong(NationalEngineeringResearchCenterforC1Chemistry,SouthwestResearch&DesignInstituteCo.,Ltd.ofChemicalIndustry,Chengdu610225,Sichuan,China)Abstract:Cu basedcatalystswerecommonlyusedinlarge scalemethanolsynthesisdevice,andthecat alysttypes,promotersandpreparationprocesshavesignificantinfluenceontheyieldofmethanol.Cu basedcatalystformethanolsynthesiscouldbemainlydividedintoCu Zn,Cu Zn Cr,Cu Zn Al,Cu Zrandsoon.Cu Zn Alcatalystspossessedexcellentperformance,andwereusedforthemaincatalystincontemporarymethanolproductiontechnology.Alkalimetal,alkalineearthmetal,transitionmetal,rareearthmetalandnonmetalelementsshoweddifferenteffectsontheactivity,selectivityandstabilityofthecatalystsformethanolsynthesis.TheeffectivepreparationmethodsofCu basedcatalystswereprecipitationmethod,sol gelmethod,combustionmethod,mechanicalmixingmethodandskeletonsynthesismethod,andprecipitationmethodwasmainlyusedforthepreparationofmethanolsynthesiscatalystinindustry.Asforthedevelopmentofthecatalystsforlarge scalemethanolsynthesisdevice,theimprovementofselectivityandstabilityofthecatalystswerethenextresearchkey.Keywords:catalystengineering;Cu basedcatalyst;methanol;additivedoi:10.3969/j.issn.1008 1143.2015.08.002CLCnumber:TQ426.6;O643.36 Documentcode:A ArticleID:1008 1143(2015)08 0585 10Copyright ©博看网. All Rights Reserved. 586 工业催化 2015年第8期 在世界能源快速消耗的情况下,C1化学发挥的作用日益重要[1],甲醇作为C1化学的基石倍受关注。
甲醇合成催化剂知识

甲醇合成催化剂知识d i4 X+ }1 z! j0 v1 铜基催化剂的催化原理 + W7 b1 C1 Y9 W4 M1 h)o9 F0 t8 j* c: D q, |6 O 目前,低压甲醇合成铜基催化剂主要组分是 CuO、ZnO和Al2O3,三组分在催化剂中的比例随着生产厂家的不同而不同。
一般来说, CuO的质量分数在40% ~80%, ZnO的质量分数在10% ~30%, Al2O3的质量分数在5% ~10%。
铜基催化剂在合成甲醇时, CuO、ZnO、Al2O3三组分的作用各不相同。
CO和H2在催化剂上的吸附性质与催化剂的活性有非常密切的关系。
在铜基催化剂表面对CO的吸附速率很高,而H2的吸附则比CO 慢得多。
ZnO是很好的氢化剂,可使H2被吸附和活化, 但对CO几乎没有化学吸附,因此可提高铜基催化剂的转化率。
纯铜对甲醇合成是没有活性的,H2和CO合成甲醇的反应是在一系列活性中心上进行的,而这种活性中心存在于被还原的Cu-CuO界面上。
在催化剂中加入少量 Al2O3的首要功能就是阻止一部分氧化铜还原。
当催化剂被还原后,开始进行反应时,合成气中的H2 和CO都是还原剂,有使氧化铜进一步还原的趋势。
这种过度的还原,使得活性中心存在的界面越来越小,催化剂活性也越来越低。
从合成的整个过程来看,随着还原表面向催化剂的内层深入,未还原的核心越来越小,作为被还原的Cu-CuO界面的核心表面积也越来越小,催化剂的活性降低,合成反应速率随之降低。
研究认为,Al2O3在催化剂中作为结构助剂起阻碍铜颗粒烧结的作用, CuO/ZnO/Al2O3催化剂的活性远高于双功能催化剂CuO/ZnO的活性。
q7 h- G8 n9 ]$ B5 m- Q: ?& ]/ D2 铜基催化剂助剂6 j8 } x5 L! ?0 V1 l1 K4 H$ Q! m% g\5 K8 e) C+ g5 A)E! ~ 铜基催化剂助剂的研究是甲醇合成催化剂研究的一个重要课题。
甲醇合成铜基催化剂制备工艺的研究
o f y i e l d i n g c a t a l y t i c we r e c l o s e s t t o a c o mp a n y S i n d u s t r i a l s a mp l e s .
Ke y wo r d s
( Ke y L a b o r a t o r y o f Ma t e r i a l Co r r o s i o n a n d Pr o t e c t i o n,S i c hu a n Un i v e r s i t y o f S c i e n c e a n d En g i n e e r i n g ,Z i g o n g 6 4 3 0 0 0 ) Ab s t r a c t Co p p e r b a s e d me t h a n o l s y n t h e s i s c a t a l y s t p r e p a r a t i o n p r o c e s s wa s s t u d i e d a n d t h e i mp a c t o f t h e f e e -
甲醇 是一 种重 要 的化 工 产 品 和 化工 原 料 , 有 着 广 泛 的用 途 , 然 而我 国的 甲醇工业 还 比较落 后 , 加 之 大量 低价 进 口 甲醇 的 涌人 , 对 我 国的 甲醇产 业产 生很 大 的 冲击 。 甲醇 催 化 剂 是 甲 醇生 产 中的关 键技 术 , 因 此 积极 开 发 、 应 用新 型 甲醇 合 成 催 化刺 可 以增强 国 内甲醇 产业 的竞 争 力 l 2。 目前 , 甲醇催 化 剂 的研 究方 向是 : 低温节能、 高 活性 、 高热稳定性、 高 机械 强 度
文献标识码 : B
甲醇合成催化反应机理及催化剂失活因素分析
甲醇合成催化反应机理及催化剂失活因素分析摘要:在甲醇生产过程中,甲醇合成催化剂常会发生中毒、高温烧结、失活等现象,大大影响了甲醇产量,也降低了催化剂的寿命,使生产成本进一步提高。
本文主要对甲醇合成催化反应机理及催化剂失活因素进行分析。
关键词:甲醇合成催化反应机理失活一、反应机理甲醇合成催化反应机理一直是研究人员关注和争议的焦点,不同的反应原料(CO/H2,或CO2/H2)、不同的催化剂、甚至相同的催化体系,催化剂结构不同,也可能导致反应机理不同。
有关反应机理的研究,主要集中在甲醇合成反应的直接碳源、反应的中间物种、反应的控速步骤以及CO在反应中的作用等问题。
早期研究者多数以动力学和H2、CO吸附等问接的实验结果为基础进行反应机理的研究;而现在多数基于同位素标记、光谱测定以及动力学模拟计算等比较直接的证据,但仍不能得出统一明确的结论。
本文按合成甲醇直接碳源的不同,将机理划分为以下3种:CO与CO2共同作为直接碳源机理、CO作为直接碳源机理以及CO2作为直接碳源机理。
(一)一氧化碳和二氧化碳作为直接碳源在CO和CO2加氢合成甲醇反应机理研究中,人们普遍认为甲酰基和甲酸基是反应过程的重要中间物种,CO吸附活化后直接生成甲酰基,而CO2吸附活化后生成甲酸基,并且CO和CO2可以通过表面氧或甲酸基等物种相互转化。
也有不同的观点认为CO吸附活化后与表面羟基结合生成甲酸盐,而CO则与表面氧结合生成碳酸根离子。
(二)一氧化碳作为直接碳源CO加氢合成甲醇的机理,可分为以下两种观点。
一种观点认为,CO首先在活性位上吸附活化,然后与吸附态的氢原子发生分步加氢反应,最终生成甲醇;而原料气中的CO2仅为补充碳源。
这种机理不能解释原料中少量CO2的存在能够明显促进甲醇合成反应的现象。
第二种观点认为,活化态的CO在加氢过程中同时与羟基、表面氧等物种发生反应,生成甲酸盐、甲氧基以及碳酸盐等中间物种,中间物种再通过脱氧及水解等反应生成甲醇。
甲醇合成铜基催化剂末期运行优化分析
甲醇合成铜基催化剂末期运行优化分析袁向平【摘要】在刚开始进行甲醇的合成生产时候,会经常面临开车以及停车的现象,具有复杂的工况以及比较大的操作变化,这样一来就非常容易造成氢碳之间的比例不符合规定,而且有毒物质所积累的时间也会比较长.一般来说,当甲醇合成催化剂处于生产末期的时候,其热点的温度会相应地有所下降,造成甲醇的产量降低.主要讨论了如何实现对于气体组分的有效控制,例如对于一氧化碳或者二氧化碳的有效控制,此外,还讨论了面对惰性气体的相对含量比较高的情况下通过对汽包的压力大小进行控制将合成塔的相对温度降低,从而可以有效地延长催化剂的使用寿命.%At the beginning of the synthesis of methanol production,it often faces the phenomenon of driving and parking,with complex conditions and relatively large operating changes,so it is very easy to cause the ratio between hydrogen and carbon not to meet the requirements,And the accumulation of toxic substances will be longer time. In general,when the catalyst for methanol synthesis is in the final stage of production,the temperature of hot spots decreases correspondingly,resulting in the decrease of methanol production. It mainly discusses how to effectively control the gas components,such as the effective control of carbon monoxide or carbon dioxide. In addition,it is also discussed that when the relative content of inert gas is relatively high,the pressure of the steam drum is controlled to control the synthesis The relative temperature of the tower decreases,which can effectively extend the service life of the catalyst.【期刊名称】《化工设计通讯》【年(卷),期】2018(044)002【总页数】2页(P14,82)【关键词】甲醇合成;铜基催化剂;催化剂末期;工艺优化【作者】袁向平【作者单位】陕西神木化学工业有限公司,陕西榆林 719319【正文语种】中文【中图分类】TQ223.1211 概述从目前来看,对于甲醇的合成所采取的方法主要就是鲁奇工艺,通过将气冷合成塔与水冷合成塔相互串联来实现对于甲醇的有效合成。
甲醇合成催化剂知识-推荐下载
铜基催化剂1 铜基催化剂的催化原理目前,低压甲醇合成铜基催化剂主要组分是CuO、ZnO和Al2O3,三组分在催化剂中的比例随着生产厂家的不同而不同。
一般来说, CuO的质量分数在40% ~80%, ZnO的质量分数在10% ~30%, Al2O3的质量分数在5% ~10%。
铜基催化剂在合成甲醇时, CuO、ZnO、Al2O3三组分的作用各不相同。
CO和H2在催化剂上的吸附性质与催化剂的活性有非常密切的关系。
在铜基催化剂表面对CO的吸附速率很高,而H2的吸附则比CO慢得多。
ZnO是很好的氢化剂,可使H2被吸附和活化, 但对CO几乎没有化学吸附,因此可提高铜基催化剂的转化率。
纯铜对甲醇合成是没有活性的,H2和CO合成甲醇的反应是在一系列活性中心上进行的,而这种活性中心存在于被还原的Cu-CuO界面上。
在催化剂中加入少量Al2O3的首要功能就是阻止一部分氧化铜还原。
当催化剂被还原后,开始进行反应时,合成气中的H2 和CO都是还原剂,有使氧化铜进一步还原的趋势。
这种过度的还原,使得活性中心存在的界面越来越小,催化剂活性也越来越低。
从合成的整个过程来看,随着还原表面向催化剂的内层深入,未还原的核心越来越小,作为被还原的Cu-CuO界面的核心表面积也越来越小,催化剂的活性降低,合成反应速率随之降低。
研究认为,Al2O3在催化剂中作为结构助剂起阻碍铜颗粒烧结的作用, CuO/ZnO/Al2O3催化剂的活性远高于双功能催化剂CuO/ZnO的活性。
2 铜基催化剂助剂铜基催化剂助剂的研究是甲醇合成催化剂研究的一个重要课题。
铜基催化剂耐热强度较低,使用时间过长或操作温度过高都会造成铜的晶体长大使催化剂失去活性。
其热稳定性差,很容易发生硫、氯中毒,使用寿命短等缺点,一般通过加入其他助剂得以改善,由此形成具有工业价值的新一代铜基催化剂。
锌就是铜基催化剂的最好助剂,很少量的锌就能使铜基催化剂的活性提高。
加入Al2O3,可以使催化剂铜晶体尺寸减小,活性提高。
- 1、下载文档前请自行甄别文档内容的完整性,平台不提供额外的编辑、内容补充、找答案等附加服务。
- 2、"仅部分预览"的文档,不可在线预览部分如存在完整性等问题,可反馈申请退款(可完整预览的文档不适用该条件!)。
- 3、如文档侵犯您的权益,请联系客服反馈,我们会尽快为您处理(人工客服工作时间:9:00-18:30)。
甲醇合成铜基催化剂催化活性及失活研究1引言甲醇是一种极其重要的化工原料,主要用于生产一系列化工产品,还可用作潜在的车用醇醚燃料电池的燃料等。
随着甲醇制烯烃等技术进步及下游产品的开发,特别是甲醇燃料电池的开发和应用,合成甲醇的研究越来越受到广泛重视。
目前,甲醇的工业生产主要是采用CO/CO2催化加氢技术,所以甲醇合成催化剂的研发是甲醇合成工业的基石。
甲醇工业的发展很大程度上取决于催化剂的研制及其性能改进。
在甲醇生产中,很多工业指标和操作条件都是由催化剂的性质决定的。
随着甲醇工业的快速发展,对甲醇合成催化剂的研究开发提出了更高的要求。
2 甲醇合成催化剂在甲醇合成过程中,催化剂的重要性显而易见,目前工业上使用的甲醇合成催化剂一般可分为锌铬催化剂和铜基催化剂两类。
国外比较有名的研究和生产甲醇合成催化剂公司主要有英国ICI公司、德国BASF公司、德国SudChemie公司和丹麦TopsΦe公司等,国内研究铜基催化剂的院所主要有南化集团研究院、西南化工研究设计院,西北化工研究院及齐鲁石化研究院等[1]。
锌铬(ZnO/Cr2O3)催化剂由德国BASF公司于1923年首先开发研制成功。
操作温度必须在590 K~670 K,操作压力必须为25 MPa~35MPa,锌铬催化剂的特点是:耐热性能好、对硫不敏感,机械强度高,使用寿命长,使用范围宽,操作控制容易,但是其活性低、选择性低、产品中杂质复杂,精馏困难。
铜基催化剂由英国ICI公司和德国Lurgi公司先后研制成功,操作温度为210℃~300℃,压力为5MPa~10MPa,比传统的合成工艺温度低得多,对甲醇反应平衡有利。
其特点是:活性好,单程转化率为7%~8%;选择性高,大于99%,易得到高纯度的精甲醇;耐高温性差,对合成原料气中杂质比较敏感。
目前工业上甲醇的合成主要使用铜基催化剂。
近年来,新型催化剂的研制也在一直进行,新型催化剂的研制方向在于提高活性,改善热稳定性及延长催化剂使用寿命等,如钯系、钼系及低温液相催化剂,但这些催化剂因活性不理想或对甲醇的选择性较差,还只停留在研究阶段未实现工业化。
对铜基催化剂的改进研究主要集中在两个方面[2],一是添加除铜锌铝以外的其他组分,另一方面是改进催化剂的制备方法和工艺。
3 铜基催化剂的催化原理目前,低压甲醇合成铜基催化剂系列品种较多,有铜锌铬系(CuO/ZnO/Cr2O3)、铜锌铝系(CuO/ZnO/Al2O3)、铜锌硅系(CuO/ZnO/Si2O3)、铜锌锆系(CuO/ZnO/ZrO)等,其中铜锌铝系(CuO/ZnO/Al2O3)应用较为广泛,下面就该系列讨论铜基催化剂催化原理。
铜锌铝系主要组分是CuO、ZnO和Al2O3,三组分在催化剂中的比例随着生产厂家的不同而不同,具体表1所示。
表1 铜基催化剂各组分所占比例组分CuO ZnO Al2O3质量分数40%~80% 10%~30% 5%~10%铜基催化剂在合成甲醇时,CuO、ZnO、Al2O3三组分的作用各不相同。
CO和H 在催化剂上的吸附性质与催化剂的活性有非常密切的关系。
在铜基催化剂表面对CO的吸附速率很高,而对H2的吸附则比CO慢得多。
ZnO是很好的氢化剂,可使H2被吸附和活化,但对CO几乎没有化学吸附,因此可提高铜基催化剂的转化率。
实验证实,纯铜对甲醇合成是没有活性的。
催化理论认为,氢和一氧化碳合成甲醇的反应是在一系列活性中心上进行的,这种活性中心存在于被还原的Cu—CuO 界面上。
在催化剂中加人少量Al2O3的首要功能就是阻止一部分氧化铜还原。
Fujitani T等[3]认为,在由共沉淀法制备的催化剂中,ZnO对增进Cu分散和增强催化剂活性具有重要的作用。
当催化剂被还原后,开始进行反应时,合成气中的H和CO都是还原剂,有使氧化铜进一步还原的趋势。
这种过度的还原,使得活性中心存在的界面越来越小,催化剂活性也越来越低。
从合成的整个过程来看,随着还原表面向催化剂的内层深入,未还原的核心越来越小,作为被还原的Cu-CuO界面的核心表面积也越来越小,催化剂的活性降低[4],合成反应速率随之降低。
Kurtz M等[5]人研究认为,Al2O3在催化剂中作为结构助剂能够阻碍铜颗粒烧结。
4 制备条件对催化剂活性的影响目前,铜基甲醇合成催化剂主要制备方法有沉淀法、球磨法、复频超声法、火焰燃烧法、碳纳米管促进法等。
由于沉淀法操作过程简单、制得的催化剂性能优越,因此铜基甲醇催化剂的工业生产均采用沉淀法。
对沉淀法制备铜基甲醇合成催化剂的影响因素及研究进展进行了探讨。
表2 铜基合成催化剂制备方法优缺点一览表制备沉淀法球磨法[6]复频超声法[7]火焰燃烧法[8]碳纳米管促进法[9]方法优点纳米级颗粒混合均匀,活性高CuO/ZnO间作用强,比表面积大分散均匀,粒径小,协同作用强易形成良好结构,如高比面积CNTs对H2吸附活化力强,活性高缺点耐热性与抗毒性较差需要高强度的机械混合操作较为复杂,且产物纯度不高仪器相当复杂,不能普遍使用要制备符合特定条件的碳纳米管共沉淀过程包括沉淀、陈化、洗涤、干燥、煅烧、压片成型等,还包括最终的还原活化,每一步对催化剂的性能都有一定的影响,特别是沉淀、陈化、煅烧、还原步骤更关键。
沉淀是催化剂制备的关键因素,沉淀条件的微小变化都会对活性产生巨大影响。
4.1沉淀过程对催化剂性能的影响沉淀过程包括晶核的生成和晶核的长大两个过程。
如果晶核生成速率远超过晶核长大速率,则离子很快聚集为大量的晶核,溶液的过饱和度迅速下降,溶液中没有更多的离子聚集到晶核上,于是晶核迅速聚集成细小的无定形颗粒,得到非晶型沉淀,甚至是胶体;如果晶核长大速率远超过晶核生成速率,溶液中最初形成的晶核不是很多,有较多的离子以晶核为中心,依次排列长大而成为颗粒较大的晶型沉淀。
相同反应物经过不同条件产生不同前驱体,分解得到的催化剂活性也就大不相同。
魏蓉等[10]认为最佳Cu/Zn为1和2,铜锌间具有较强的协同作用;铝含量不超过10%;沉淀温度不低于70℃;沉淀pH值在7-9之间。
4.2 煅烧过程对催化剂性能的影响煅烧是使催化剂具有活性的重要步骤,可能发生如下变化:①热分解,使其转化成所需的化学形态;②固态反应、互溶和再结晶获得一定晶型、比表面积等;③烧结,提高催化剂的机械强度,获得较大孔隙率。
煅烧温度与催化剂活性的关系煅烧过程一般为吸热过程,故升高温度有利于分解反应,但温度过高会烧结,使催化剂活性下降,而煅烧温度降低则达不到活化的目的。
因此研究者对合适的煅烧条件一直在不断的探索。
许勇等[11]发现煅烧温度能改变催化剂表面积、催化活性、晶相组成等,Al2O3的加入有利于提高催化剂的热稳定性,阻止CuO晶粒长大,提高催化剂活性。
煅烧温度为350-650℃为宜,当温度高于650℃,催化活性显著下降,这是由于煅烧温度太高使氧化物烧结颗粒长大所致。
洪中山等[12]提出合适煅烧条件为:富氧气氛、较低的升温速率和350℃煅烧。
该煅烧条件获得的催化剂比表面积高、铜粒径小,选择性高。
甲醇收率随煅烧温度的升高先增加后降低,煅烧温度为350℃时达到最高。
4.3 添加助剂还有一些特殊助剂,作用就是有助分散铜晶体,阻止高温下铜晶体生长,特别是在超温时,减小对催化剂的伤害,延长使用时间,提高效益,刘艳霞等[13]研究发现γ-A12O3的添加量为催化剂量的3%时,催化剂的初活性和耐热后的活性明显高于其他催化剂。
杨意泉等[14]在Cu-Zn-Al甲醇合成催化剂中添加适量的氧化锆助剂制得Cu-Zn-Al-Zr催化剂,它对CO的吸附量大于Cu-Zn-Al催化剂对CO的吸附量。
随着当代催化工业迅速发展和新型催化技术开发和应用,沉淀法制备铜基甲醇催化剂技术也应不断吸收新兴技术的优点。
比如微乳液技术[15]、溶胶凝胶技术[16-17]分别与沉淀法相结合,这些技术各有特点且各种技术常可相互关联运用并取得令人满意的结果,因而受到人们广泛关注。
5反应条件对催化剂活性的影响5.1 反应温度的影响合成甲醇反应:2H2+CO=CH3OH,其△r G m= –114.17+0.244 KJ/mol,因此,从热力学上来说,升高温度对合成甲醇是不利的。
但升高温度使得反应速率加快,即在动力学上升温是有利的。
所以,甲醇合成必有一个合适的反应温度。
在实验操作中发现催化剂活性先随反应温度升高而升高,后又随反应温度升高而下降。
温度过高,会使催化剂发生热烧结而降低活性甚至丧失活性。
但是反应温度在280℃以下,铜基甲醇催化剂的热烧结因素几乎可以忽略。
因为我们无论在测试催化剂耐热前的活性还是耐热后的活性时,在120℃~280℃的温度范围内,都通过反复的升温、降温,进行过多次测试,活性结果的重现性均很好。
这也就是说,两种催化剂的活性(无论是耐热实验前还是耐热实验后的活性)在210℃~280℃的反应温度范围内的变化趋势,都主要是反应热力学和动力学这两种效应的综合体现。
5.2 合成气空速的影响空速增加,合成气在反应器内的停留时间减少,与催化剂的接触时间减少,从而不利于副反应的发生,这样甲醇的选择性就会有所提高,进而使催化剂的生产能力提高,甲醇收率提高,所以我们说增加空速可以提高了催化剂的活性。
如果采用高空速,催化剂的生产强度虽然可以提高,但增大了预热所需的面积,出塔气热能利用价值较低,系统阻力增大,压缩循环气功耗增加,同时增加了分离反应产物的费用,当空速增大到一定程度后,催化剂的床温度难以控制。
适宜的空速与催化剂活性,反应温度及进塔气体组成有关,在铜基催化剂上为10000-20000h-1。
5.3合成气组成的影响由合成气合成甲醇的反应相当复杂,除主反应外,还有低碳醇合成反应,F-T合成反应和水煤气变换反应。
反应进行的方向、程度及其产物组成取决于催化体系及相应反应条件。
水煤气变换反应是甲醇、低碳醇及烃类合成反应的副反应。
此外合成甲醇反应中氢与CO的理论分子比为2:1,但反应气体受催化剂表面吸附的影响,CO在催化剂表面上的吸附速率远大于H2,存在吸附竞争。
因此,要求反应气体中的H,含量要大于理论量,以提高反应速度,增加甲醇产率,所以一般入塔气中的H/C之比要大于4。
5.4 反应压力的影响合成甲醇反应CO+2H2=CH3OH是一个气体分子数减少的反应,故增加压力可使反应平衡向右移动,即升高压力在热力学上对合成甲醇是有利的。
从动力学上来说,由于多相催化反应动力学的复杂性,表面反应过程,反应物在催化剂表面上的吸附以及产物在催化剂表面上的脱附均有可能成为多相催化反应的控制步骤。
而无论那个是控制步骤,反应压力均有可能影响反应速率。
在实验操作过程中发现,增加压力,甲醇收率(mol/g·h)随反应总压的增加而增高。
压力增加10%,甲醇产率增加10%,达到8MPa以上开始下降[18]。