亚铁离子对磷化膜质量影响的研究
磷化质量影响因素及其提高途径

磷化质量影响因素及其提高途径引言磷化是一种化学与电化学反应形成磷酸盐化学转化膜的过程。
早在1869年W. A. Ross 就申请了磷化专利技术 [ 2 ] ,随着科技的不断进步,金属磷化处理作为传统的表面处理技术在金属防护、减磨耐磨及涂层打底等方面得到广泛的发展和应用。
磷化处理有多种分类方法:按成膜体系可分为锌系、锌锰系、锰系、铁系、锌钙系及非晶相铁系等六大类;按磷化处理温度可分为常温(不加温)、低温(30~45℃)、中温(60~70℃)、高温(大于80℃)四类;按材质可分为钢铁件、铝件、锌件以及混合件磷化;其它的还有按磷化膜厚度或促进剂类型等分类。
用于防锈磷化的主要有铁系磷化、锌系磷化、锰系磷化三种;用于耐磨减磨磷化的种类有锌系磷化和锰系磷化;而锌锰系和锌钙系主要用于漆前磷化。
一磷化基本原理磷化成膜是一个化学动态平衡,目前,大多数学者认同的磷化原理由以下四个步骤组成:首先是金属的溶解过程。
当金属浸入磷化液中时,先与磷化液中的磷酸作用,生成一代磷酸铁,并有大量的氢气析出。
其化学反应为;Fe –2e→Fe2+2H+ + 2e→H2上式表明,磷化开始时,仅有金属的溶解,而无膜生成。
第二是促进剂加速形成磷化膜。
其化学反应式为:[O]+[H] → [R]+H2OFe2++[O] → Fe3++[R]式中[O]为促进剂(氧化剂),[R]为还原产物,由于促进剂氧化掉第一步反应所产生的氢原子,加快了反应(1)的速度,进一步导致金属表面H+浓度急剧下降。
同时也将溶液中的Fe2+氧化成为Fe3+。
第三是磷酸根的多级离解。
H3PO4→H2PO4-+H+→HPO42-+2H+→PO43-+3H+由于金属表面的H+浓度急剧下降,导致磷酸根各级离解平衡向右移动,最终离解为PO43-。
最后磷酸盐沉淀结晶成为磷化膜当金属表面离解出的PO43-与溶液中(金属界面)的金属离子(如Zn2+、Mn2+、Ca2+、Fe2+)达到溶度积常数Ksp时,就会形成磷酸盐沉淀Zn2++ Fe2++ PO43-+H2O→Zn2Fe(PO4)2·4H2O↓ (4)3Zn2++2PO43-+4H2O=Zn3(PO4)2·4H2O↓ (5)磷酸盐沉淀与水分子一起形成磷化晶核,晶核继续长大成为磷化晶粒,无数个晶粒紧密堆集形而上学成磷化膜。
磷化处理常见质量问题及排除方法

磷化处理常见质量问题及排除方法
质量问题
产生原因
排除方法
磷化膜结晶粗糙多孔
1、游离酸含量多
1、调整游离酸
2、硝酸根不足 2、补充硝酸根含量
3、工件表面有残酸 3、加强中和和清洗
4、亚铁离子含量过高 4、用促进剂调整
5、工件表面过腐蚀 5、控制酸浓度和腐蚀时间 膜层过薄、
无明显结
晶
1、酸总量过高
1、加水稀释或磷酸盐调整酸比
2、工件表面有硬化层
2、进行喷砂或强酸腐蚀
3、亚铁离子过低
3、补充磷酸二氢铁
4、温度过低
4、升温至规定温度 磷化膜耐蚀性差、生锈
1、磷化晶粒过粗或过细
1、调整酸比
2、游离酸含量过高 2、降低游离酸含量
3、基体金属被腐蚀
3、控制酸浓度和腐蚀时间
4、溶液中磷酸盐含量不足 4、补充磷酸盐含量
5、工件表面有残酸 5、加强中和及清洗 磷化膜有
白色沉淀
1、溶液中沉淀物过多
1、找出原因,排除沉淀
2、硝酸根不足
2、补充硝酸根含量
3、锌、铁、五氧化二磷含量过高
3、降低锌、铁、五氧化二磷的含量 磷化膜不1、工件表面有硬化层
1、进行喷砂或强酸腐蚀
易形成2、硫酸根含量高2、用钡盐处理
3、溶液中有杂质3、排除杂质或更换槽液
4、五氧化二磷含量低4、补充磷酸盐
磷化膜不均匀、发花1、脱脂不净1、加强脱脂
2、工件部分表面处于钝化状态2、加强喷砂或酸洗
3、工件热处理方法不对3、改进热处理方法
冷挤压后磷化膜产生条状脱
落1、肥皂填充液中有杂质1、清理溶液
2、皂化前工件表面有杂质和沉淀物2、重新磷化。
影响金属磷化膜效果的因素
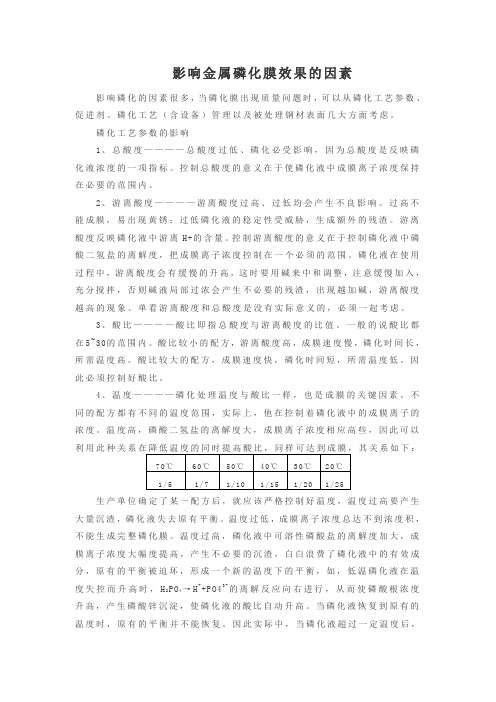
影响金属磷化膜效果的因素影响磷化的因素很多,当磷化膜出现质量问题时,可以从磷化工艺参数、促进剂、磷化工艺(含设备)管理以及被处理钢材表面几大方面考虑。
磷化工艺参数的影响1、总酸度————总酸度过低、磷化必受影响,因为总酸度是反映磷化液浓度的一项指标。
控制总酸度的意义在于使磷化液中成膜离子浓度保持在必要的范围内。
2、游离酸度————游离酸度过高、过低均会产生不良影响。
过高不能成膜,易出现黄锈;过低磷化液的稳定性受威胁,生成额外的残渣。
游离酸度反映磷化液中游离H+的含量。
控制游离酸度的意义在于控制磷化液中磷酸二氢盐的离解度,把成膜离子浓度控制在一个必须的范围。
磷化液在使用过程中,游离酸度会有缓慢的升高,这时要用碱来中和调整,注意缓慢加入,充分搅拌,否则碱液局部过浓会产生不必要的残渣,出现越加碱,游离酸度越高的现象。
单看游离酸度和总酸度是没有实际意义的,必须一起考虑。
3、酸比————酸比即指总酸度与游离酸度的比值。
一般的说酸比都在5~30的范围内。
酸比较小的配方,游离酸度高,成膜速度慢,磷化时间长,所需温度高。
酸比较大的配方,成膜速度快,磷化时间短,所需温度低。
因此必须控制好酸比。
4、温度————磷化处理温度与酸比一样,也是成膜的关键因素。
不同的配方都有不同的温度范围,实际上,他在控制着磷化液中的成膜离子的浓度。
温度高,磷酸二氢盐的离解度大,成膜离子浓度相应高些,因此可以利用此种关系在降低温度的同时提高酸比,同样可达到成膜,其关系如下:70℃60℃50℃40℃30℃20℃1/5 1/7 1/10 1/15 1/20 1/25生产单位确定了某一配方后,就应该严格控制好温度,温度过高要产生大量沉渣,磷化液失去原有平衡。
温度过低,成膜离子浓度总达不到浓度积,不能生成完整磷化膜。
温度过高,磷化液中可溶性磷酸盐的离解度加大,成膜离子浓度大幅度提高,产生不必要的沉渣,白白浪费了磷化液中的有效成分,原有的平衡被迫坏,形成一个新的温度下的平衡,如,低温磷化液在温度失控而升高时,H2PO4→H++PO43-的离解反应向右进行,从而使磷酸根浓度升高,产生磷酸锌沉淀,使磷化液的酸比自动升高。
常见的磷化质量问题及解决方法
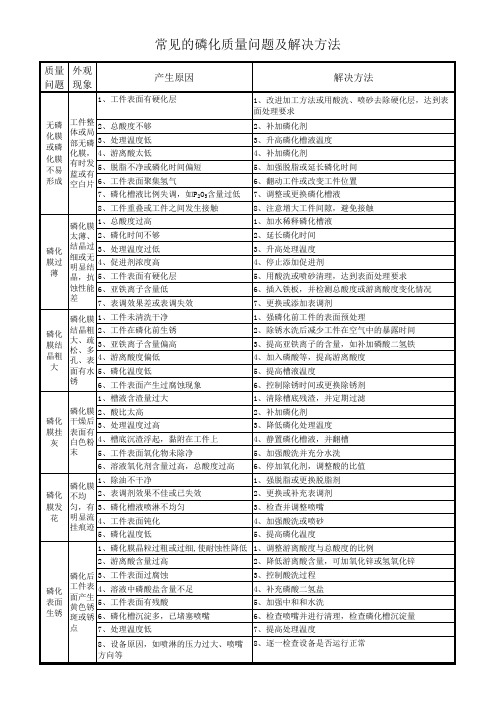
质量 外观 问题 现象 产生原因
1、工件表面有硬化层 无磷 化膜 或磷 化膜 不易 形成 工件整 体或局 部无磷 化膜, 有时发 蓝或有 空白片 2、总酸度不够 3、处理温度低 4、游离酸太低 5、脱脂不净或磷化时间偏短 6、工件表面聚集氢气 7、磷化槽液比例失调,如P2O5含量过低 8、工件重叠或工件之间发生接触 磷化膜 太薄、 结晶过 磷化 细或无 膜过 明显结 薄 晶,抗 蚀性能 差 磷化膜 磷化 结晶粗 大、疏 膜结 松、多 晶粗 孔、表 大 面有水 锈 1、总酸度过高 2、磷化时间不够 3、处理温度过低 4、促进剂浓度高 5、工件表面有硬化层 6、亚铁离子含量低 7、表调效果差或表调失效 1、工件未清洗干净 2、工件在磷化前生锈 3、亚铁离子含量偏高 4、游离酸度偏低 5、磷化温度低 6、工件表面产生过腐蚀现象 1、槽液含渣量过大 磷化膜 2、酸比太高 磷化 干燥后 3、处理温度过高 膜挂 表面有 灰 白色粉 4、槽底沉渣浮起,黏附在工件上 5、工件表面氧化物未除净 末 6、溶液氧化剂含量过高,总酸度过高 1、除油不干净 磷化膜 磷化 不均 2、表调剂效果不佳或已失效 膜发 匀,有 3、磷化槽液喷淋不均匀 花 明显流 4、工件表面钝化 挂痕迹 5、磷化温度低 2、游离酸含量过高 磷化后 工件表 磷化 面产生 表面 黄色锈 生锈 斑或锈 点 3、工件表面过腐蚀 4、溶液中磷酸盐含量不足 5、工件表面有残酸 6、磷化槽沉淀多,已堵塞喷嘴 7、处理温度低 8、设备原因,如喷淋的压力过大、喷嘴 方向等
1、补加表调剂,或重新配槽 2、补加AC-131 3、检查喷嘴 4、调整链速 5、换板材
质 量外 观 问 题现 象
产生原因
解决方法
1、注意不用铜挂具,用铁屑置换除去或用硫化处理, 调整酸度 2、加强酸洗过程的质量控制 1、停加促进剂 2、充分搅拌,使之均匀 3、补加脱脂剂
磷化溶液中离子浓度对磷化液的影响

磷化槽中的离子浓度对液体的影响分析分析离子浓度对磷化液的影响,是关系到磷化膜质量的好坏,也关系到后续工艺中电泳成膜的影响。
在整个电泳工艺中,每一个步骤处理的好坏都关系到电泳质量的好坏,有时候为了避免由于电泳质量差带来的问题,对每个步骤的分析处理都显得很有必要。
下面我们就来说说在磷化槽中离子的浓度对磷化液有何影响。
磷化液中有铁离子、锰离子、锌离子、酸根离子等等。
(1)Fe2+离子,在常温和中温磷化液中保持一定数量的Fe2+离子,能提高磷化膜厚度和抗蚀性能。
但Fe2+离子易被氧化成Fe3+而沉淀。
当它转变成磷酸高铁,溶液呈乳白色时,磷化膜几乎不能生成,膜的质量恶化。
Fe2+离子含量过高,会使磷化膜晶粒粗大表面白色浮灰,耐蚀性和耐热性能降低。
一般中常温磷化中Fe2+离子宜控制在NaH0.5~2.5g/L之间。
过多的Fe2+离子可用H2O2除去,每降低1gFe2+约需加30﹪H2O21mL和ZnO0.5g.在高温磷化液中,Fe2+很不稳定,易氧化成Fe3+离子,并转变为Fe(PO4)3沉淀,使磷化液变浑浊游离酸度升高,需过滤和调整溶液成分后才能使用。
(2)Mn2+离子Mn2+能提高磷化膜硬度结合力和耐蚀性,并能使膜层结晶均匀呈深灰色,但在常温和中温磷化液中Mn2+离子含量不宜过高,否则磷化膜不易生成。
(3)Zn2+离子Zn2+离子可加快磷化速度,使膜层致密,闪烁有光。
Zn2+离子含量过高时使膜层晶粒粗大、脆弱、表面呈灰白色。
Zn2+离子含量过低时,膜层疏松且发暗。
内容不够完整,我来补充下:(1)No3-离子No3-离子可加快磷化速度,降低磷化槽液工作温度。
在适当条件下它与Fe作用生成少量No-,促使Fe2+离子稳定,No3-离子是常、中温磷化液的重要组成部分,但含量过高就会使磷化膜层粗而薄,易出现黄点或白点。
(2)No2-离子能大大提高常温磷化液的磷化速度,促使磷化膜结晶细致,减少孔隙,提高抗蚀性。
含量过多时,膜层易出现白点。
磷化溶液成分对磷化膜层质量的影响

磷化溶液成分对磷化膜层质量的影响成分作用与影响锌离子可加快磷化速度能,磷化膜致密,含锌盐的磷化溶液允许较宽的范围。
锌离子含量低时,磷化膜疏松发暗。
锌离子高时(特别是氟离子和五氧化二磷较高时),磷化膜脆,晶粒粗大锰离子可提高磷化膜的硬度、附着力和耐蚀性,并能使磷化膜的颜色加深,结晶均匀。
但中温和常温磷化溶液中锰离子含量过高时,磷化膜不易生成铁离子在高温磷化溶液中亚铁离子很不稳定,容易被氧化成三价铁离子并转化成磷化铁而沉淀,使磷化溶液浑浊,游离酸度升高。
在常温和中温磷化液中,保持一定数量的亚铁离子,能大大提高磷化层的厚度、机械强度和防护能力,工作范围较宽。
但当亚铁离子转化为三价铁离子并以磷酸铁沉淀出来时,磷化结晶不能生成,磷化膜的质量差。
当亚铁离子含量含量过高时,会使中温磷化膜结晶粗大,表面有灰白浮灰,防护能力降低,膜的耐热性下降。
五氧化二磷能加快磷化速度,磷化膜致密。
其主要来源于磷酸二氢盐,含量低时,磷化膜致密性和耐蚀性均差,甚至磷化不上。
含量高时,磷化膜结晶排列紊乱,附着力下降,工件表面灰白色浮灰较多硝酸根离子可加快磷化速度,提高磷化膜的致密性。
可在降低磷化溶液温度的条件下进行磷化处理。
在适当条件下,硝酸根与钢铁作用生成少量一氧化氮,有利于亚铁离子的稳定,因此他是磷化溶液中(特别是中温和常温)的一个重要成分。
硝酸根含量过高,会使高温磷化膜变薄;使中温磷化液中亚铁离子集聚过多;使常温磷化膜易出现黄色锈迹氟离子可加快磷化结晶核的生成速度,使结晶致密,耐蚀性增强。
在常温磷化溶液中其重要性尤为突出。
氟离子过多,使中温磷化工件表面易出现白色浮灰;使常温磷化溶液的寿命缩短亚硝酸根离子亚硝酸根在常温磷化溶液中可大大加快磷化速度,并能减少磷化膜的空隙,使结晶细致,提高膜的耐蚀性。
含量过高,磷化膜表面易出现白点项目高温磷化中温磷化低温磷化溶液操作温度(℃)90~98 50~70 室温。
关于磷化工序的浅解

关于钢丝〔盘条〕磷化的浅解1.0磷化的目的和基本原理:1.1钢丝表面涂着物的特性:钢丝的加工和使用,要求材料在保存或加工过程和加工结束后的一定时间段内,材料表面不产生锈蚀或表面涂着物不产生潮解;在加工过程中得到低的摩擦系数。
钢丝因再加工和使用的需要,钢丝表面选择的涂着物有:涂石灰、涂硼砂或其类似物、电镀金属、磷化等。
电镀金属仅是在一些特殊产品的要求而使用。
涂石灰是早期钢丝生产工艺中广泛使用的方式,它成本低;但是这种方式在再加工时产生粉尘有害健康且不适应高速拉拔。
涂硼砂是适用于高速拉拔且成本低廉的方式。
虽然它易于潮解,但对涂后的中间品有适当的管理措施是可以避免的。
且特别在涂后直接拉拔的工艺是被广泛选用。
目前国外虽开始限制使用硼砂产品,因此出现其类似物。
但是这种涂层只适用于中间产品的表面而不适用于最终产品的表面;因为它抗锈蚀能力差,但强于石灰涂层。
磷化的涂着层具有一定的抗锈蚀能力,和具有一定的电抗;在后加工过程中得到低的摩擦系数。
好的磷化膜本身具有很好的塑性,在变形中能够很好地保持其连续性;同时,它不仅能和皂——硬脂酸钠,发生反应产生更有利于润滑的金属皂类,而且其表面又可以很好地附着皂液和润滑剂;这有利减小变形摩擦因数、减少模具磨损。
1.2 磷化膜的形成和特性:1.2.1 磷化技术的机理:磷化处理过程是化学与电化学反应过程,主要是由下述步骤组成:a.酸的浸蚀使基体金属表面 H+ 离子浓度降低。
当金属表面与酸性磷化液接触时,钢丝表面被溶解,使金属与溶液中酸反应产生氢,从而使界面的 PH 值上升,以致磷酸锌〔以锌系为例〕沉积于钢丝表面。
由于亚铁在溶液中的存在,不论因酸后的带入还是在槽内反应产生,磷酸铁锌也同时沉积于钢丝表面。
其总反应方程如下:5Zn(H2P04)2+Fe(H2P04)2+8H20--+ Zn 3(P04)2。
4H20+ Zn 2Fe(P04)2。
4H20+ 8 H3P04磷酸盐沉淀的副反应将形成磷化沉渣,即亚铁离子被氧化后同磷酸反应生成磷酸铁在溶液中沉淀:Fe³¯+ P04³¯==FeP04但是在这钢丝表面的二种磷膜沉积物有不同的特性;称前者Zn 3(P04)2。
影响磷化膜质量的因素

影响磷化膜质量的因素1、前言现代工业的迅速发展,市场对涂装要求急剧增加,涂装行业将会得到更快的发展,而涂装质量的好坏在一定程度取决于涂装前处理技术的高低,而磷化又是涂装前处理的关键,磷化膜的性能好坏直接关系到涂装质量的优劣,因此我们需要详细地了解影响磷化膜质量的因素。
2、影响磷化膜质量的因素2.1. 总酸度(TA)TA是反映磷化槽浓度的一项指标,是指槽液中配合酸(HSO42-)和FA浓度的总和。
控制TA的目的在于保持磷化槽液中成膜离子的浓度在规定的工艺范围内。
TA过高,磷化膜生成困难,磷化膜结晶粗燥,耐腐蚀性差。
2.2 游离酸度(FA)FA是指槽液中游离酸度H+浓度。
FA促使工件溶解产生晶核,使生成磷化膜容易。
控制FA的目的在于控制槽液中磷酸二氢盐的离解度,把成膜离子浓度控制在一个必须范围内。
FA过高,反映加快。
工件与槽液界面的离子浓度被破坏,届面PH值过低,造成成膜困难,成膜时间延长,结晶粗大多孔。
耐腐蚀性低。
FA过低,工件腐蚀缓慢,界面PH值升高,磷化膜薄甚至难以形成,膜成表面易产生浮粉(Zn(PO4) 2沉淀),磷化液易产生异常沉淀,导致Zn2+含量急剧降低。
2.3. 磷化温度磷化温度是形成磷化膜的一个关键因素,适当的提高温度不仅可以激活能量低的点形成“活化中心”使晶核数目增多,结晶速度提高,成膜速度加快,同时可以在枝晶上产生新的结晶,结晶密度提高,形成完整结晶的磷化膜,但温度过高,反映速度太快,膜层晶核粗大,孔隙较大,槽液稳定性差,易浑浊,形成含渣的超重灰磷化膜,耐腐蚀性低。
当温度过低,由于磷化是吸热反应,当所需的热量得不到足够补偿时,成膜速度缓慢,甚至磷化反映难以进行,在家和摩配行业磷化中,多以低温和常温磷化磷化为主。
由于温度低,反映相应减慢,因此必须通过其他途径来调节槽液的酸比,促进剂含量,浓度来补偿温度低而对磷化速度的影响,为满足批量生产,加你最好采用低温磷化为宜。
2.4. 磷化时间不同的磷化液,具有不同的磷化时间要求,随着磷化时间的不同,所获得磷化膜的外观,厚度,耐腐蚀性也不同,磷化时间与膜重不成线形关系,根据不同的板材来确定磷化时间,以获得理想的确凿磷化膜。