制氢装置转化部分技术问答..
制氢技术问答精讲

1
惠州炼油项目制氢装置技术问答
成分 CH4 C3H8 C5H12 H2 6.
组成(v%) 51.69 6.26 1.39 21.21
成分 C2H6 C4H10 N2 H2O
组成(v%) 16.51 2.89 0.04 0.00
尾气的工况、组成及去向? 尾气压力一般在 0.02MPa~0.05MPa,温度在 30℃左右,去往转化炉做燃料气。 成分 CH4 C3H8 i-C4H10 i-C5H12 n-C7H16 CO2 组成(v%) 13.01 0.769 0.058 0.135 0.129 48.422 成分 C2H6 n-C4H10 n-C5H12 n-C5H14 CO H2 组成(v%) 0.632 0.619 0.042 0.001 8.308 27.36
4
惠州炼油项目制氢装置技术问答
应。如甲烷化反应:CO2+4H2→CH4+2H2O。 10. 氢气主要有哪些制造方法? 氢气制造包括两个过程,即含氢气体制造及氢气提纯。根据氢气的用途不同,采用 不同的制造工艺, 得到不同纯度的氢气。 制造含氢气体的原料, 目前主要是碳氢化合物, 包括固体(煤) 、液体(石油、水)及气体(天然气、炼厂气) 。水是制造氢气的另一种 重要原料,可以采用单独从水中制取氢气,如:电解水,也可以用水与碳氢化合物相结 合反应制得氢气。 (1)煤的高温干馏法:即煤在隔绝空气的条件下在焦炉中加热到 900~1000℃,得 到主要产物焦碳,同时,还副产许多炼焦化学产品,如煤焦油、粗苯、氨及焦炉气等。 焦炉气中含有大量氢气,一吨原料煤可得焦炉气(STP)为 300~350m3。焦炉气中氢气占 55~66%( v%)。焦炉气在 20 世纪 50 年代以前是获取氢气的主要来源之一。 (2)部分氧化法:它是以烃类(主要为渣油或焦炭)为原料制取含氢气体的方法之 一。烃类与水蒸汽反应可制得氢气。该反应为强吸热反应,反应所需热量采用由燃烧部 分原料供给,故称之为部分氧化法。当以天然气为原料时,加入不足量的氧气,使部分 甲烷燃烧为 CO2 和 H2O 并放出大量的热。 CH4+2O2=CO2+2H2O+1802 kJ。 在高温及水蒸汽存在下,CO2 及水蒸汽可与未燃烧的 CH4 反应,得到主要产物 CO 及 H2,燃烧所得 CO2 不多,反应为强吸热反应。 CH4+CO2=2CO+2H2-206kJ; CH4+H2O=CO+3H2-247 kJ; 综合上述两个反应式则:CH4+0.5O2→CO+2H2 (3)烃类水蒸汽转化法:该方法是在有催化剂存在下进行的,烃类与水蒸汽反应生 成 CO 和 H2。所用原料主要是天然气,亦可用炼厂气、丙烷、丁烷、液态烃、轻石脑 油和重整拔头油,其与水蒸气反应生成 CO 和 H2。或者先经过预转化反应把烃类分解 成甲烷,再与水蒸气反应生成 CO 和 H2。 (4)炼厂低浓度氢气回收:炼厂气来源于各石油加工过程,在石油炼制过程中副产 气中含有不同浓度氢气组分,如催化裂化、热裂化、焦化、加氢裂化及催化重整等过程 产生的含氢气体,经过提纯之后可得到氢气。
制氢装置原料部分技术问答分解
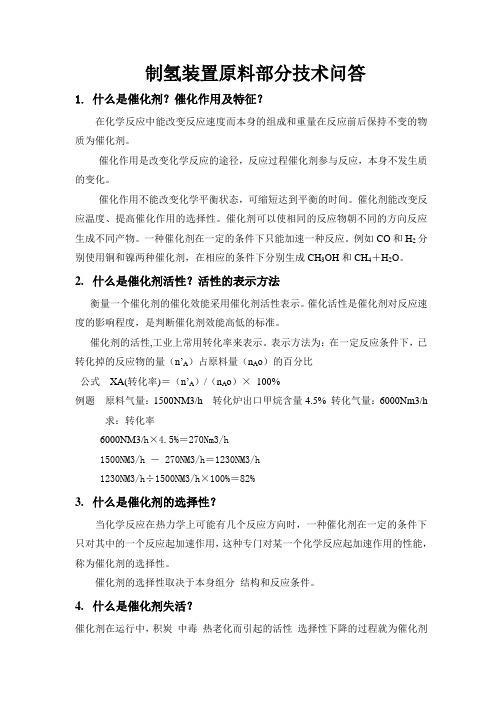
制氢装置原料部分技术问答1.什么是催化剂?催化作用及特征?在化学反应中能改变反应速度而本身的组成和重量在反应前后保持不变的物质为催化剂。
催化作用是改变化学反应的途径,反应过程催化剂参与反应,本身不发生质的变化。
催化作用不能改变化学平衡状态,可缩短达到平衡的时间。
催化剂能改变反应温度、提高催化作用的选择性。
催化剂可以使相同的反应物朝不同的方向反应生成不同产物。
一种催化剂在一定的条件下只能加速一种反应。
例如CO和H2分别使用铜和镍两种催化剂,在相应的条件下分别生成CH3OH和CH4+H2O。
2.什么是催化剂活性?活性的表示方法衡量一个催化剂的催化效能采用催化剂活性表示。
催化活性是催化剂对反应速度的影响程度,是判断催化剂效能高低的标准。
催化剂的活性,工业上常用转化率来表示。
表示方法为:在一定反应条件下,已转化掉的反应物的量(n’A)占原料量(n A o)的百分比公式XA(转化率)=(n’A)/(n A o)×100%例题原料气量:1500NM3/h 转化炉出口甲烷含量4.5% 转化气量:6000Nm3/h 求:转化率6000NM3/h×4.5%=270Nm3/h1500NM3/h - 270NM3/h=1230NM3/h1230NM3/h÷1500NM3/h×100%=82%3.什么是催化剂的选择性?当化学反应在热力学上可能有几个反应方向时,一种催化剂在一定的条件下只对其中的一个反应起加速作用,这种专门对某一个化学反应起加速作用的性能,称为催化剂的选择性。
催化剂的选择性取决于本身组分结构和反应条件。
4.什么是催化剂失活?催化剂在运行中,积炭中毒热老化而引起的活性选择性下降的过程就为催化剂失活。
原料中的毒物影响,催化剂超温引起的热老化,积炭,进料比例失调,工艺条件波动以及长期使用过程中由于催化剂的固体结构状态发生变化或遭到破坏等原因都会引起的催化剂的活性、选择性衰减。
制氢技术问答

制氢技术问答1、制氢技术问答原料部分14.适用于蒸汽转化制氢的烃类原料有哪些?15.蒸汽转化制氢原料选择原则有哪些?16.为什么不能轻易选用炼厂二次加工油做转化原料?17.是否有可用做制氢原料的二次加工油?18.轻油的族组成对转化过程产生哪些影响?19.自然气用做制氢原料对转化催化剂有什么要求?20.不含烯烃的各种炼厂气对转化催化剂有什么要求?21.用炼厂干气做制氢原料时如何进行预处理?22.各种轻油对转化催化剂有什么要求?原料部分14.适用于蒸汽转化制氢的烃类原料有哪些?答:适用于蒸汽转化的烃类原料大体分为气态烃和液态烃。
〔1〕气态烃包括自然气、液化石油气和各种炼厂气自然气一般包括油田伴生气和气田气。
自然气的主要成份是甲烷,以及少量乙烷、丙烷等低级烃类,含有肯定量的氮、二2、氧化碳等惰性气体和有害杂质硫化氢。
其中气田自然气是以甲烷为主,含微量杂质的气体。
液化石油气是由丙烷、丁烷为主要成份组成的烃类,来源有两种,一种是油田和自然气田伴生出来的自然液化气,另一种是炼油厂和石油化工厂产生的液化石油气。
炼厂气是指原油加工过程中副产的各种尾气,包括催化裂化气、焦化干气、催化重整气、热裂解气、高压加氢裂解尾气等。
各种炼厂气的组成改变较大,其中含有烯烃的炼厂气,不宜直接用作蒸汽转化制氢。
但经过彻底的烯烃脱除或加氢饱和处理,可以和不含烯烃的加氢干气一样,是很好的蒸汽转化制氢原料。
〔2〕液态烃包括直馏石脑油、抽余油、拨头油以及二次加工油直馏石脑油是原油常压蒸馏所得210℃以下的馏份。
比重一般为0.63~0.77,含硫量小于0.05%,石蜡烃含量较3、高,芳烃含量小于13%,烯烃含量小于1%。
用作制氢原料的抽余油一般是重整抽余油,即重整抽提芳烃之后剩下的部分。
抽余油干点一般在130~150℃,芳烃含量很少。
拨头油一般也是重整拨头油,一般都是C5以下的烃类。
二次加工油指经裂化、焦化、减粘等一系列二次加工处理重油得到的轻油。
加氢、焦化、制氢技术问答

第一章工艺部分技术问答一、基础知识1.什么叫压力?什么叫压强?压力是指流体垂直作用在物体表面的力。
物体单位面积上所承受的压力称为压强。
2.什么叫表压?工程上所用的压力表指示值,即压力表测得的压力指示值称为表压。
3.什么叫绝对压力?把设备和物料实际所受的压力规定为绝对压力。
当容器中的压力低于大气压时,把低于大气压力的部分称为真空,真空也可以用百分比表示,我们称为真空度即用测得的真空水银柱高度,再化为百分数即可。
P真空=P大气压-P绝压4.绝压力、表压、大气压的关系?P绝压= P大气层+P大气压5.油品的沸点与单质的沸点有何区别?油品由于是混合物,其沸点是一个温度范围,称为馏程。
而单质的沸点是一个温度点。
6.压力单位如何换算?1标准大气压=1.033kgf/c㎡≈760mmHg=10.33MH2○=101325pa 1kgf/c㎡≈0.1Mpa7.什么叫密度?单位体积内油品质量称为油品的密度。
其单位为千克/米38.什么叫石油产品标准密度?石油产品标准密度是指内标准温度20℃,石油产品的密度,以d20表示。
9.什么叫比重?油品在t℃质量与同体积纯水在4℃时的质量比称为油品在t℃时的比重以dt4表示。
也可用油品的t℃时的密度与4t℃时纯水的密度比表示。
在国际单位制中比重称相对密度. 10.油品比重与温度关系?温度升高,油品受膨胀,体积增大,比重减少。
反之则增大。
11.油品比重与组成关系?同系物的比重随沸点的升高而增大,沸点范围相同时,含芳香烃越多比重越大,含烷烃愈多比重愈小。
12.什么叫流量?流量是指在单位时间内,流体流过管道有效截面积的量。
分为体积流量的重量两种。
流体在管路中流动时,单位时间内流过管路任一截面的流体体积,称为体积流量,常用符号Vt表示,其单位是米3/秒。
在单位时间内流过管路任一截面的重量,称为重量流量,常用符号Gt表示,其单位为公斤/秒。
二者之间关系为:Gt= Vt/A 式中A为管子横截面积。
制氢知识问答

催化剂基本知识1、什么是催化剂?催化作用的基本特征是什么?答:在化学反应中能改变能改变反应速度而本身的组成和重量在反应前后保持不变的物质叫催化剂。
加快反应速度的叫正催化剂;减慢的叫负催化剂。
通常所说的催化剂是指正催化剂。
催化作用改变了化学反应的途径。
在反应终了,相对于始态,催化剂虽不发生变化,但却参与了反应,例如形成了活化吸附态、中间产物等,因而使反应所需的活化能降低。
催化作用不能改变化学平衡状态,但却缩短了达到平衡的时间,在可逆反应中能以同样的倍率提高正、逆反应的速度。
催化剂只能加速在热力学上可能发生的反应,而不能加速在热力学上不可能发生的反应。
2、什么是活化能?答:催化过程之所以能加快反应速度,一般来说是由于催化剂降低了活化能。
从一般意义上来说,反应物分子有了较高的能量,才能处于活化状态发生化学反应。
这个能量一般一般远较分子的平均能量为高,两者之间的差值就是活化能。
在一定温度下,活化能越大,反应越慢,活化能越小,反应越快。
也可以说,在化学反应中使普通分子变成活化分子所必须提供的最小能量就是活化能。
其单位通常用千卡/克分子或千焦/摩尔表示。
3、什么是催化剂的活性?具体有哪些表示方法?衡量一种催化剂的催化效能采用催化活性来表示。
催化活性是催化剂对反应速度的影响程度,是判断催化剂效能高低的标准。
对于固体催化剂的催化活性,多采用以下几种表示方法:(1)催化剂的比活性(2)反应速率表示法(3)工业上常用转化率来表示催化活性(4)用每小时每升催化剂所得到的产物重量的数值来表示活性。
4、什么是催化剂失活?失活的原因有哪些?对大多数工业催化剂来说,它的物理性质和化学性质随催化反应的进行发生微小的变化,短期之间很难察觉。
然而,长期运行过程中,这些变化累积起来,造成催化剂活性、选择性的显著下降,这就是催化剂的失活过程。
另外,反应物中存在的毒物和杂质,上游工艺带来的粉尘、反应过程中原料结碳等外部原因也会引起催化剂活性、选择性的下降。
制氢装置顶烧转化炉炉膛传热问题探讨
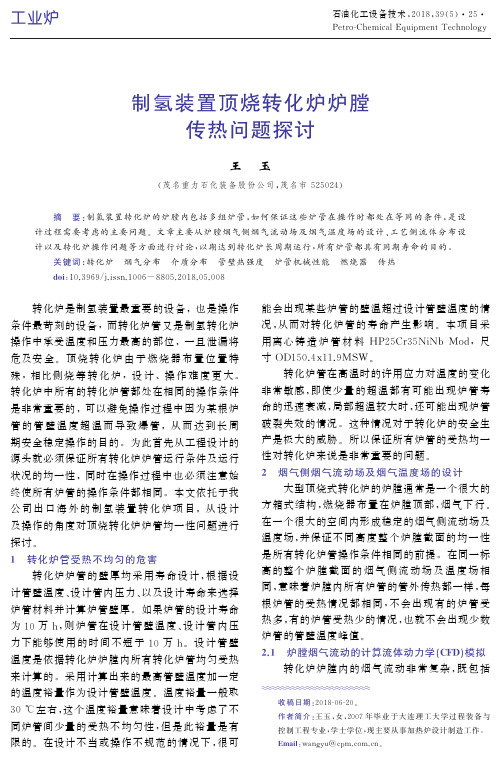
收稿日期:2018G06G20.作者简介:王玉,女,2007年毕业于大连理工大学过程装备与控制工程专业,学士学位,现主要从事加热炉设计制造工作.E m a i l :w a n g y u @c pm.c o m.c n .制氢装置顶烧转化炉炉膛传热问题探讨王㊀玉(茂名重力石化装备股份公司,茂名市525024)㊀㊀摘㊀要:制氢装置转化炉的炉膛内包括多组炉管,如何保证这些炉管在操作时都处在等同的条件,是设计过程需要考虑的主要问题.文章主要从炉膛烟气侧烟气流动场及烟气温度场的设计㊁工艺侧流体分布设计以及转化炉操作问题等方面进行讨论,以期达到转化炉长周期运行,所有炉管都具有同期寿命的目的.关键词:转化炉㊀烟气分布㊀介质分布㊀管壁热强度㊀炉管机械性能㊀燃烧器㊀传热d o i :10.3969/j.i s s n .1006-8805.2018.05.008㊀㊀转化炉是制氢装置最重要的设备,也是操作条件最苛刻的设备,而转化炉管又是制氢转化炉操作中承受温度和压力最高的部位,一旦泄漏将危及安全.顶烧转化炉由于燃烧器布置位置特殊,相比侧烧等转化炉,设计㊁操作难度更大.转化炉中所有的转化炉管都处在相同的操作条件是非常重要的,可以避免操作过程中因为某根炉管的管壁温度超温而导致爆管,从而达到长周期安全稳定操作的目的.为此首先从工程设计的源头就必须保证所有转化炉炉管运行条件及运行状况的均一性,同时在操作过程中也必须注意始终使所有炉管的操作条件都相同.本文依托于我公司出口海外的制氢装置转化炉项目,从设计及操作的角度对顶烧转化炉炉管均一性问题进行探讨.1㊀转化炉管受热不均匀的危害转化炉炉管的壁厚均采用寿命设计,根据设计管壁温度㊁设计管内压力㊁以及设计寿命来选择炉管材料并计算炉管壁厚.如果炉管的设计寿命为10万h ,则炉管在设计管壁温度㊁设计管内压力下能够使用的时间不短于10万h .设计管壁温度是依据转化炉炉膛内所有转化炉管均匀受热来计算的.采用计算出来的最高管壁温度加一定的温度裕量作为设计管壁温度.温度裕量一般取30ħ左右,这个温度裕量意味着设计中考虑了不同炉管间少量的受热不均匀性,但是此裕量是有限的.在设计不当或操作不规范的情况下,很可能会出现某些炉管的壁温超过设计管壁温度的情况,从而对转化炉管的寿命产生影响.本项目采用离心铸造炉管材料H P 25C r 35N i N b M o d,尺寸O D 150.4x 11.9M S W .转化炉管在高温时的许用应力对温度的变化非常敏感,即使少量的超温都有可能出现炉管寿命的迅速衰减,局部超温较大时,还可能出现炉管破裂失效的情况.这种情况对于转化炉的安全生产是极大的威胁.所以保证所有炉管的受热均一性对转化炉来说是非常重要的问题.2㊀烟气侧烟气流动场及烟气温度场的设计大型顶烧式转化炉的炉膛通常是一个很大的方箱式结构,燃烧器布置在炉膛顶部,烟气下行.在一个很大的空间内形成稳定的烟气侧流动场及温度场,并保证不同高度整个炉膛截面的均一性是所有转化炉管操作条件相同的前提.在同一标高的整个炉膛截面的烟气侧流动场及温度场相同,意味着炉膛内所有炉管的管外传热都一样,每根炉管的受热情况都相同,不会出现有的炉管受热多,有的炉管受热少的情况,也就不会出现少数炉管的管壁温度峰值.2.1㊀炉膛烟气流动的计算流体动力学(C F D )模拟转化炉炉膛内的烟气流动非常复杂,既包括工业炉㊀㊀石油化工设备技术,2018,39(5) 25P e t r o GC h e m i c a l E q u i p m e n tT e c h n o l o g y了烟气流动,又包括了沿炉管圆周方向和高度方向的传热.电子计算机技术普及以前,转化炉炉膛的烟气侧流动场及温度场设计主要靠经验及简单的手工计算,很难保证全截面的均一性.随着计算流体动力学(C F D )及电子计算机技术的发展,现在已经可以对转化炉炉膛内的烟气流动进行详细的数值分析,改变了过去只能定性分析的情况.制氢转化炉膛烟气流动的计算流体动力学(C F D )模拟的3维模型如图1所示.通过模拟,可以精确得到炉膛内不同部位的烟气㊁流体流动状态,流动速度,压力分布以及温度分布.这些结果可以直观地显示哪里有偏流㊁哪里有过热㊁哪里有死区,从而发现问题根源,找到改进的目标,指导设计,达到优化的目的.图1㊀炉膛烟气流动的计算流体动力学(C F D )模拟2.2㊀炉底烟道分布孔的设计转化炉烟气沿炉膛下行后到达炉底,炉底排列有一系列的通常由耐火砖筑砌而成的炉底烟道.这些炉底烟道的顶部是封死的,烟道侧面的墙上开了很多小孔,来自炉膛顶部的烟气从炉底烟道侧面墙上的这些小孔进入炉底烟道.小孔的作用是使烟气均匀分布,达到炉膛内的所有烟气都可以均匀下行㊁全炉膛烟气流动一致㊁没有偏流的效果.炉底烟道烟气能够均匀分布的原理是由于这些小孔在烟道侧墙上面不是均匀分布的,烟道墙靠近转化炉对流室一端开孔较少,远离转化炉对流室一端开孔较多,因为烟气压力分布的原因,炉膛内部的烟气就会均匀向下流动,进入炉底烟道的小孔,不会短路直接流入对流室.炉底烟道侧墙上面的小孔到底怎样分布才能达到炉膛里面的烟气都能均匀流动的效果?这是转化炉设计需要重点研究的课题,很多人都对此进行了深入的研究.本文利用C F D 软件分析了烟气通过每一个小孔的流动情况,得到炉膛中及烟道内的流场分布状态.图2是某台转化炉的烟气通过炉底烟道分布孔的C F D 流场模拟.通过模拟,对炉底烟道侧墙上面的开孔分布进行优化,并通过这些优化,使转化炉达到全炉膛烟气均匀流动㊁所有炉管都能均匀受热的效果.图2㊀烟气通过炉底烟道分布孔的C F D 模拟2.3㊀炉顶燃烧器的布置炉顶燃烧器的布置对于炉管的均匀受热也是非常重要的.燃烧器如何选型,燃烧器与炉管的相互位置关系,如何配风,如何组织燃烧,以及火焰的长度和形状等等都是需要考虑的问题.由于转化炉的重要性和特殊性,决定了其燃烧器必须要高度可靠,并与炉型相匹配.根据工艺操作的要求,燃烧器应该能够满足炉管表面热强度均匀性的要求,同时要满足炉膛高度方向的均匀度.本次设计火焰高度为炉膛高度的1/4左右.燃烧器的性能需要和管内的化学反应相协调,在化学反应最剧烈,最需要热量的炉管入口段应该能够迅速提供所需要的热量.制氢转化炉采用P S A 脱附气作为主要燃料ʌ1ɔ.脱附气里面氢含量较高,炉膛的温度又非常高,为了得到较大的燃烧器操作弹性,也为了防止燃烧器烧坏,燃烧器的燃烧配风一般采用外混形式.随着环保要求的日益提高,氮氧化物(N O x )的排放要求越来越严格,燃烧器通常需要采用低N O x 燃烧器,其结构大部分都是多级配风或多级配燃料.这些都可能造成燃烧器火焰不稳定,有时甚至会发生火焰舔到炉管,使管壁温度超温的情况.为避免此情况,燃烧器的能量通常不宜太大,每台控制在1.5MW 左右为宜.同时燃烧器布置时应考虑到与炉管的布置相互协调,使每根炉管的受热状态都相同,也就是说每台燃烧器面对的炉管数量应相同.通常每台燃烧器面 62 石㊀油㊀化㊀工㊀设㊀备㊀技㊀术2018年㊀对的炉管为3~4根,该项目为4根.2.4㊀炉顶燃烧器风道的布置炉顶燃烧器数量众多,为了保证所有炉管的受热一致性,要求每台燃烧器的燃烧状态都要相同.不仅每排中所有的燃烧器燃料量需要相同,每台燃烧器的配风量也需要相同,这样才能使每台燃烧器的燃烧状态相同.需要指出的是,虽然每台燃烧器的风道上面都配备了燃烧器入口挡板,但这些挡板的主要作用是开工点火时控制风量,日常操作时很难通过该挡板调节燃烧器的风量.因为不能利用每台燃烧器的挡板进行调节,所以就必须通过风道的布置使每台燃烧器的配风量一致.通常采用风道变截面的方式使每台燃烧器的配风均匀.具体截面大小,由流体动力学(C F D)模拟优化获得.该项目在每排燃烧器的风道尾部设置了平衡风道,使各排燃烧器的风道相互连接,以达到每排燃烧器的风道背压相互平衡,对每台燃烧器均匀布风的目的.3㊀转化炉炉管内工艺侧流体分布设计除了转化炉管外烟气侧流场及温度场均匀外,每根转化炉管管内工艺侧的流体分布也应该均匀,只有这样,每根炉管的管内传热才能相互一致,壁温状态才能相同.转化炉中所有的炉管都是并联的,并联管路中的流量都是自动分配,为保证每根炉管的流量均匀,就必须要求所有炉管的水力学状态完全相同.3.1㊀转化炉入口系统的设计转化炉入口系统包括入口集合管及入口猪尾管.小型转化炉的入口系统相对简单,比较容易达到所有炉管的水力学状态相同.大型转化炉的入口系统非常复杂,入口管系分配时应注意采用逐级对称分配的形式,同时需注意与入口猪尾管相连接的集合管的截面积应大于与其相连接的所有猪尾管的截面积之和.该项目单根集合管截面尺寸74671mm2,与其相连的猪尾管截面积42527mm2.3.2㊀转化炉出口系统的设计转化炉出口系统有很多种形式,不同专利商的结构都不相同.采用冷壁集合管,可因集合管内径较大,使之很容易达到各管程的水力学状态一致的效果.该项目采用冷壁集合管结构,并且采用较为先进的双层衬里结构.单根冷壁集合管衬里内侧截面尺寸138544mm2,与其相连的催化剂管截面积53800mm2.采用热壁集合管,则会由于出口温度很高,集合管材料在该温度下的许用应力低,导致采用大管径时壁厚非常厚,很难做到集合管的截面积大于与其相连接的所有猪尾管的截面积之和,同时又能保证各管程的流动状态相同的要求.3.3㊀转化管内催化剂的装填转化管内催化剂的装填对于管内流量分配是非常重要的,因为催化剂床层的压降占了高温管系压降的绝大部分,其装填不均匀会严重影响管内流量的分配,造成开工后偏流㊁管壁温度超温等现象.目前检测催化剂装填好坏的唯一手段,就是应用阻力降测试装置对每根炉管进行真实准确的阻力降测定.将催化剂分段装填,全部下段催化剂装完并且空高标定合格后,对全部炉管进行一次阻力降测试.各管阻力基本均匀,符合装填要求后,再以相同的方法步骤装填上段催化剂.上段催化剂全部装完后再对所用炉管进行一次阻力降测试,算出全炉平均阻力降.单管阻力降与平均值相差ʃ5%以内者为合格,如果偏差大于5%就要考虑卸出该管催化剂,重新装填.4㊀转化炉的操作如何保证炉管受热均一性转化炉除了设计方面需要考虑管外烟气侧传热的均匀性㊁管内介质侧流动的均匀性以外,在操作方面也必须要保证所有炉管的均一性.转化炉操作过程中,必须保证每台燃烧器的负荷都一致,火焰高度都相同.所有燃烧器都必须通过控制系统统一调整,不宜单独对某一台燃烧器调整燃料量或空气量,更不允许正常操作过程中将其中的某台燃烧器熄灭.这点对于高温转化炉尤其重要,否则就会造成严重的偏流㊁红管㊁甚至炉管破裂.转化炉操作过程中对炉管壁温进行实时监测也是非常重要的.通常采用红外测温仪对所有炉管各部位的外壁温度进行日常监测,并对监测的数据进行记录,发现问题应及时分析原因并做出相应的调整.5㊀结论设计转化炉时,为保证炉膛内所有炉管受热的均一性,应从管外烟气侧流场㊁温度场㊁管外传(下转第33页)72㊀第39卷第5期王㊀玉.制氢装置顶烧转化炉炉膛传热问题探讨图9㊀制氢装置加热炉原有燃烧器燃烧情况图10㊀制氢装置加热炉低N O x 燃烧器燃烧情况㊀㊀表1为更换低N O x 燃烧器前后加热炉N O x 排放浓度对比.这一检测结果的对比更准确地反映了低N O x 燃烧器的效果.由表1可以看出:加热炉更换低N O x 燃烧器后,N O x 浓度大幅下降,治理效果明显,N O x 排放优于现行环保标准要求,说明使用低N O x 燃烧器技术防治加热炉N O x 是目前行之有效的技术手段.表1㊀更换低N O x 燃烧器前后加热炉排放浓度对比34㊀未来加热炉N O x 防治的发展方向随着国家生态文明的发展和人民对优美生态环境需求的进一步提高,加热炉烟气污染物排放标准将更加严格,现有成熟的加热炉烟气N O x 治理手段将难以达到理想效果,加热炉N O x 防治将面临更加迫切㊁严峻的任务.在这样的背景下,综合运用燃料分级㊁空气分级㊁烟气循环等技术的超低N O x 排放技术燃烧器将进一步的发展.受燃料燃烧效率㊁加热炉操作弹性等因素约束,采用低N O x 燃烧技术将烟气可靠地降到40m g /m 3以下非常困难.此时,S C R 脱硝技术将成为加热炉N O x 防治的主要手段,多台加热炉烟气集中脱硝后排放将成为趋势.低N O x 燃烧技术将与S C R 脱硝技术组合起来,共同保证加热炉烟气达标排放.如果N O x 排放限制进一步趋严,燃烧中和燃烧后的防治措施都将面临难以逾越的技术障碍,若O 2制备技术进一步发展㊁制备成本降低,那么全氧燃烧技术将极有可能成为一种可靠的N O x 防治技术,从根本上避免加热炉产生N O x .参考文献:[1]㊀王广盛,赵显坤,桂永亮.工业锅炉的N O x 污染及防治[J ].石油化工环境保护,2003,26(2):52G53,61.[2]㊀周跃花.燃烧时N O x 的转化与控制[J ].西安联合大学学报(自然科学版),2000,3(4):70G74.[3]㊀新井纪男.燃烧生成物的发生与抑制技术[M ].赵黛青,赵哲时,王昶,等,译.北京:科学出版社,2001.(上接第27页)热以及管内介质侧流体流动㊁管内化学反应及传热等方面选择合理的设计参数.在操作过程中应对炉管壁温加强监测及调整.总结为以下4点:1)转化炉管的壁温温差应控制在设计规定的范围内,延长炉管的使用寿命;2)转化炉内烟气流动场主要受控于炉底烟道设计和炉顶燃烧器的布置,C F D 的计算模拟可用于优化工程设计,以获得良好的烟气流动场及烟气温度场;3)转化炉炉管内工艺侧流体分布的设计,需使管系各个流路的压降均匀一致;4)转化炉的操作中应加强巡检并及时调整燃烧器,保证炉管受热均匀一致.参考文献:[1]㊀郝树仁,董世达.烃类转化制氢工艺技术[M ].北京:石油工业出版社,2009.33 ㊀第39卷第5期袁成志.加热炉烟气N O x 防治。
制氢问答

1.怎样调节转化负荷?负荷的调节提负荷时,必须先提工艺蒸汽的量,再提原料的量;降负荷,必须先降原料的量,再降工艺蒸汽的量,这是原则,必须遵守,否则,很有可能因水/烃比过低,而使催化剂积炭而失去活性。
因此,改变负荷时,必须密切注意水/烃比值使其保持在2.05,同时,也要通过调节炉入口压力、炉出口温度,直到通过炉出口取样分析,使得转化气中的甲烷含量在6.89%(VOL)为止。
2. 主要硫化物的性能?一般说,天然气中含硫化氢比较多,还有部分低沸点有机硫,如甲硫醇、甲硫醚等。
液烃中的硫化物比较复杂。
经分析,可识别的77种硫化物中,36种为硫醇,23种为直链硫醚,18种为环状硫醚和噻吩。
大多数液态烃中还有二硫化物。
此外,氧硫化碳和二硫化碳也是常见的硫化物。
为此,一般把硫化氢称为无机硫;硫醇(R-SH),硫醚(R-S-R),二硫化物(R-S-S-R‘),多硫化物(R-S n-R’),噻吩及其同系物称为有机硫。
硫化氢性质:硫化氢为无色气体,有类似腐败鸡蛋的恶臭味,性极毒。
它在水中的熔解度比较大,其水溶解度比较大,其水溶液呈弱酸性,能与碱作用生成盐。
硫化氢具有很强的还原能力很容易被氧化成硫磺和水。
硫化氢还易与金属氧化物或金属的盐类反应生成金属硫化物。
氧化锌脱硫就是根据这一性质。
而金属硫化物一般难溶于水,但在高温下与水蒸汽作用又可能分解出硫化氢来。
因而在变换系统中,如果气体中含有硫化物,则在管道中就会有金属硫化物沉积。
停车后重新开车,温度提高,水蒸汽浓度增大时,短时期后可观察到气体中硫化氢含量显著增高的现象。
硫醇:低分子的硫醇具有极度难闻的臭味。
硫醇有毒,不溶于水,可与铁作用,腐蚀管道及设备。
它的酸性比相应的醇类要强。
能与金属盐类或碱作用,发生下面化学反应R-SH+NaOH=R-S-Na+H2O硫醇加热时可分解成烯烃及硫化氢,分解温度为250-500℃故易被除去。
硫醚:梳醚无味中性,与碱不发生作用,化学性质相当稳定。
制氢技术问答(书)

第一部分催化剂基本知识1、什么是催化剂?催化作用的特征是什么?答:在化学反应中能改变反应速度而本身的组成和重量在反应前后保持不变的物质叫催化剂。
加快反应速度的称正催化剂;减慢的称负催化剂。
通常所说的催化剂是指正催化剂。
催化作用改变了化学反应的途径。
在反应终了,相对于始态,催化剂虽然不发生变化,但却参与了反应,例如形成了活化吸附态,中间产物等,因而使反应所需的活化能降低。
催化作用不能改变化学平衡状态,但却缩短了达到平衡的时间,在可逆反应中能以同样的倍率提高正、逆反应的速度。
催化剂只能加速在热力学上可能发生的反应,而不能加速热力学上不可能发生的反应。
所以,催化作用的实质是一种动力学功能。
催化作用的选择性。
催化剂可使相同的反应物朝不同的方向反应生成不同的产物,但一种催化剂在一定条件下只能加速一种反应。
例如CO和H2分别使用铜和镍两种催化剂,在相应的条件下分别生成CH3OH和CH4+H20.一种新的催化过程,新的催化剂的出现,往往从根本上改变了某种化学加工过程的状态,有力推动工业生产过程的发展,创造出大量财富,在现代的无机化工、有机化工、石油加工和新兴的是有化工工业中这样的例子不胜枚举,在与人类的生存息息相关的诸多方面如资源的充分利用,提高化学加工过程的效率,合成具有特定性能的产品,有效的利用资源,减少和治理环境污染以及在生命科学方面,催化作用具有越来越重大的作用。
2、什么是活化能?答:催化作用之所以能加快反应速度,一般来说,是由于催化剂降低了活化能。
为什么催化剂能降低活化能呢?关键是反应物分子与催化剂表面原子之间产生了化学吸附,形成了吸附化学键,组成表面络合物,它与原反应物分子相比,由于吸附键的强烈影响,某个键或某几个键被减弱,而使反应活化能降低很多。
催化反应中的活化能实质是实现上述化学吸附需要吸附的能量。
从一般意义来说,反应物分子有了较高的能量,才能处于活化状态发生化学反应。
这个能量一般远较分子的平均能量为高,两者之间的差值就是活化能。
- 1、下载文档前请自行甄别文档内容的完整性,平台不提供额外的编辑、内容补充、找答案等附加服务。
- 2、"仅部分预览"的文档,不可在线预览部分如存在完整性等问题,可反馈申请退款(可完整预览的文档不适用该条件!)。
- 3、如文档侵犯您的权益,请联系客服反馈,我们会尽快为您处理(人工客服工作时间:9:00-18:30)。
制氢装置转化部分技术问答1.轻油转化工段的主要任务是什么?答:轻油蒸汽转化的目的是使组成为Cn Hm的轻油和水蒸汽通过催化剂转化为有用的气体,H2和CO,同时伴生CO2和少量的残余CH4。
对于工业制氢装置来讲,其中的H2是我们的目的产物,而每个CO分子再经变换工段从水中夺取一分子的氢,再产生一部分H2。
根据工厂最终产品的需要,适当调节转化工段的工艺条件,合理设置下游工艺,即可分别生产出工业氢气、冶金还原气、氨或醇的合成气。
2.轻油蒸汽转化反应过程如何?答:与甲烷为主的气态烃原料相比,液态烃的各种轻油组成比较复杂,有烷烃、环烷烃、芳烃。
转化过程中,一方面这些烃类与水蒸汽发生催化转化反应,另一方面,烃类还会发生催化裂解反应和均相热裂解反应。
大量裂解产物经过进一步的聚合、芳构化和氢转移等反应都会导致结炭,结炭反应是轻油蒸汽转化过程中必然发生的副反应,这正是轻油蒸汽转化过程和以甲烷为主的气态烃(如天然气和油田气)蒸汽转化过程的最基本的差别。
由于轻油原料的组成比较复杂,反应又处于450~800℃的列管式变温催化床层内,因此,轻油加压水蒸汽转化制取氢气或合成气过程是一种包含多种平行反应和串联反应的复杂反应体系。
由于床层温差较大,不同部位的反应情况变化较大,包括高级烃的热裂解、催化裂解、脱氢、加氢、结炭、消炭、氧化、变换、甲烷化等反应,反应机理可用下图形象地表示。
3.轻油蒸汽转化过程中结炭反应机理如何?答:轻油蒸汽转化过程中,在一定的水碳比之下,结炭反应是一种必然发生的热力学过程,关键是选择良好的催化剂和相应的工艺条件以尽量减少积炭,保证正常运行。
结炭反应是转化过程中的一种副反应,它和转化过程密切相关。
进入催化反应床层的反应物只有轻油(Cn Hm)和水(H2O),很显然,我们的目的产物H2来自CnHm和H2O。
我们可以设想轻油的转化首先必须裂解,并伴随进一步脱氢、加氢产生了低碳数的烃和H2,也同时产生了新生态的碳,而碳与水蒸汽反应便生成了CO和H2。
因此,轻油水蒸汽转化过程实际上首先是一个裂解过程,而后才是二次产物的进一步反应,最终形成H2、CO、CO2和残余CH4的平衡。
根据很多研究结果和理论分析,我们可以把轻油水蒸汽转化的全过程做如下描述:(1)床层温度低于600℃时:C n H m 吸附于活性金属Ni 表面上,首先发生催化裂解。
Ni …C n H m →C(a)+H(a)+CH x (a)+C 2H y (a)+…+C f H g …………①C(a)(a)CH (a)CH (a)CH CH 2-x 1-x x 4⇔⇔⇔⇔………………②C(a)+H 2O(a)→CO +H 2…………………………………………③CO(a)+H 2O(a)→CO 2+H 2 ……………………………………④H 2O(a)+M →O(a)+H(a) ………………………………………⑤a 表示吸附态,M 代表载体和金属Ni 。
可以认为水蒸汽先被载体吸附,逆流至Ni 上被解离吸附,钾碱亦有可能对H 2O 发生解离吸附。
由于Ni 对烃类吸附性能强,烃类占据Ni 的活性中心,故使用碱性助剂可提高催化剂对蒸汽的吸附能力。
这对增加气化速度,抑制结炭十分重要。
①式表明C n H m 催化裂解产生低分子烷烃、烯烃、甲烷、氢气和炭。
低分子烷烃会进一步发生如①式表征的裂解。
烯烃聚合→聚合物→聚合炭 ……………………⑥烯烃脱氢芳构化→聚合物→聚合炭 ………………⑦反应⑥、⑦产生的聚合炭实际是含有一定氢元素的高分子缩合产物,即所谓“炭的先驱物”,有的称为焦油炭,或称为封贴炭膜,它对催化剂表面的活性中心起封闭作用,降低了催化剂的活性。
②式表示碳碳键断裂产生的吸附态自由基CHx(x 在0~3)既可能向左加氢而生成CH4,也可能向右逐步加氢而形成炭。
生成的炭和水蒸汽反应即形成气体产物,正如③、④式所示。
这也说明结炭反应和消炭气化反应处于竞争之中。
该过程中形成的炭通常认为是通过Ni 晶粒扩散成“核”,然后以Ni 晶粒为顶点逐渐生成为须状炭。
这种炭对活性影响不大,但碳纤维可能堵塞催化剂孔隙和破坏催化剂颗粒。
(2)床层温度高于600℃时:C n H m 主要发生均相热裂解,产生低分子烷烃、烯烃、甲烷、氢气和炭。
在这部分高温段床层所发生的反应仍然可以用①~⑦式来表征,最终积炭的形态不同于低温段。
烯烃聚合→聚合物→脱氢→焦炭 ……………………⑧烯烃脱氢、芳构化→稠环芳烃→热裂解焦炭…………⑨此段床层内由于温度升高,结炭反应加快,因此积炭较多,这些积炭在高温下很容易转化为有光泽的石墨化炭,石墨化炭掩盖活性表面导致催化剂活性下降,这已被工业装置的实践所证明。
在固定的反应温度和空速下,维持一定的水碳比,催化剂上是否产生积炭,则主要取决于工艺过程中积炭和消炭的动力学平衡,即结炭和消炭反应的相对速度。
而轻油转化催化剂的关键就是要使转化过程中消炭反应速度大于结炭反应速度,从而避免催化剂上炭的沉积,促进目的产物的生成。
4.如何理解“热力学结炭”?一般发生在什么条件下?答:所谓热力学结炭可理解为轻油蒸汽转化过程中,结炭反应的不可避免性。
在高于烃类分解的温度下,又有酸性或金属催化作用的存在,烃类的裂解是必然要发生的。
然而在一般的设计工艺条件下,热力学结炭不会大量产生,只有当水碳比失调造成水碳比急剧下降或大幅度波动时,才会发生热力学结炭。
5.如何理解“动力学结炭”?一般发生在什么条件下?答:在轻油蒸汽转化过程中,一般有多种反应引起结炭,另一方面还存在着碱性消炭反应,即炭的水煤气反应。
当水蒸汽分压提高,消炭反应就可以加速。
在固定的反应温度、空速和水碳比条件下,催化剂上是否产生积炭,则取决于积炭和消炭的动力学平衡,即结炭和消炭两种反应的相对速度,当结炭速度大于消炭速度时,就会在催化剂上产生动力学积炭。
6.“结炭和积炭”的含义有何不同?答:“结炭”一般可理解为一种热力学过程,指在轻油转化过程中导致生成炭的反应,而“积炭”可理解为一种动力学结果,是指当总的结炭反应速度大于消炭反应速度时产生了炭的积累,谓之“积炭”。
7.如何判断催化剂的积炭?答:催化剂表面轻微积炭时,因积炭掩盖活性中心,活性下降,吸热减少而出现花斑、热带、出口尾气中芳烃增加等现象,但有时催化剂中毒或钝化活性下降时也会出现类似的现象,因此要结合对容易造成结炭的工艺条件变化和分析做出判断。
催化剂床层严重积炭时,表现为床层阻力迅速增加,转化炉管表面温度很快升高,直至出现红管。
8.催化剂积炭的原因有哪些?如何防止?答:积炭的发生一般是由于催化剂装填不均匀,水碳比失调,负荷增加,原料油重质化,催化剂中毒或被钝化,活性或抗积炭性能下降,转化温度和压力的大幅波动等原因引起。
消除上述可能引起积炭的因素就可以防止积炭。
应该严格按照设计的正常操作条件操作,防止因设备、仪表、操作等事故引起的水碳比失调和温度、压力的大幅度波动。
严格选用符合催化剂要求的原料,严格控制原料净化工段的工艺条件,保证催化剂始终处于还原态,防止水和原料的脉冲进料(脉冲进料的实质是水碳比瞬时失调),保证催化剂装填均匀和转化炉炉膛温度的均匀等等即可防止大量产生积炭。
9.转化催化剂常用的烧炭再生条件是什么?答:催化剂轻微积炭时,可采用缓和的烧炭方法,例如降低负荷,增大水碳比,配入一定量的还原气等条件下运转数小时,以达到除碳的目的。
积炭严重时,必须切除烃类原料用水蒸汽烧炭。
蒸汽量为正常操作蒸汽量的30~40%,压力为1.0MPa左右。
严格控制温度不高于运转时的温度。
出口尾气CO2下降并稳定到一个较低数值时(每隔半小时分析一次),则烧炭结束。
空气烧炭热效应大,反应激烈,对催化剂危害大,不宜采用。
但必要时,可在水蒸汽中配入少量空气,但要严格控制氧含量,防止超温。
烧炭结束后,重新还原方可投料。
经过烧炭仍不能恢复正常操作时,则停车更换催化剂。
10.为什么抗积炭性能是轻油蒸汽转化催化剂的主要性能?答:在比较经济的运行工艺条件下,轻油蒸汽转化催化剂上积炭往往是难以避免的,而积炭危害又很大,大量积炭是导致催化剂寿命缩短的最主要原因。
积炭使催化剂活性下降,大量积炭又使催化剂床层阻力增加,导致转化过程无法完成。
虽然可以消炭,但消炭再生会使催化剂表面剥蚀,使催化剂强度下降,并进而影响其使用寿命。
积炭的形态各不相同,床层低温段的聚合炭和高温段的石墨化炭对催化剂的表观活性影响最大。
因此,良好的抗积炭性能是轻油蒸汽转化催化剂的最主要的性能。
11.转化炉管压差增大的原因有哪些?答:催化剂装填过程中因高空跌落而引起部分炉管内催化剂粉碎,催化剂的机械强度或热稳定性不好在使用过程中发生粉碎,中毒或水碳比失调等事故状态引起的催化剂床层热力学积炭,催化剂长期运行中积炭增加,压力急剧下降或烧炭反应激烈引起催化剂粉碎,催化剂水合引起的粉化等,都是造成转化炉管压差增大的原因。
具体分析如下:(1)催化剂部分破碎引起阻力降增加。
催化剂在装填、使用过程中,压力急剧变化造成催化剂的破碎,会使催化剂的装填密度增大,空隙减小,导致转化炉系统压差增大。
(2)催化剂积炭造成转化炉压差增大。
在使用过程中,催化剂表面积炭将堵塞气流通道,导致气流受阻,压差增大。
此外催化剂积炭后的烧炭再生过程中也会由于烧炭速度过急引起催化剂粉碎或“剥皮”,催化剂碎块或粉末堵塞转化管底部出气口也会造成转化炉压差增大。
(3)增大反应负荷、增大水碳比也会导致转化炉压差增大。
反应负荷的增加,增大了气流量,使得系统阻力增大。
12.何谓转化催化剂的毒物?中毒的过程以及如何再生?答:转化催化剂的毒物主要有硫、氯、砷等非金属以及铅、铜、钒、铁锈等。
硫中毒:主要由原料脱硫不合格引起,中毒后催化剂活性下降,上部温度升高,出口甲烷偏高,芳烃穿透,严重时炉管上部出现花斑,并逐渐向下扩展。
在正常操作条件下,Z402、Z409、Z417、Z405G、Z418催化剂等要求原料中硫含量小于0.5ppm。
RKNR及Z403H催化剂要求小于0.2ppm。
当然原料中的实际硫含量越小越好,只要严格控制进入转化炉的硫含量,一般不会出现明显的硫中毒的情况,而目前的脱硫技术和工艺一般都能将原料中的硫含量降至规定的指标以下。
当操作波动时,脱硫不合格时会引起硫中毒。
中毒首先发生在上部低温段的转化催化剂上。
经验表明,在排除了发生积炭的可能性以后,当上部转化管出现温度升高,出口甲烷也升高,就可判断是催化剂中毒了。
硫中毒的发生和床层温度有关,在转化炉出口800℃的温度下,原料中的硫含量大约在5ppm才会引起催化剂中毒。
而在床层入口500℃时,0.01ppm的硫就会引起催化剂的中毒。
这是因为硫中毒的过程是一种简单的放热吸附过程,温度低时有利于硫的吸附反应。
在实际生产中,目前的脱硫技术还无法使原料轻油中的硫达到0.01ppm,但一般催化剂活性有余地,所以轻油脱硫指标要求小于0.5ppm 即可。