连续搅拌反应釜系统的设计与仿真分析
搅拌反应釜设计论文
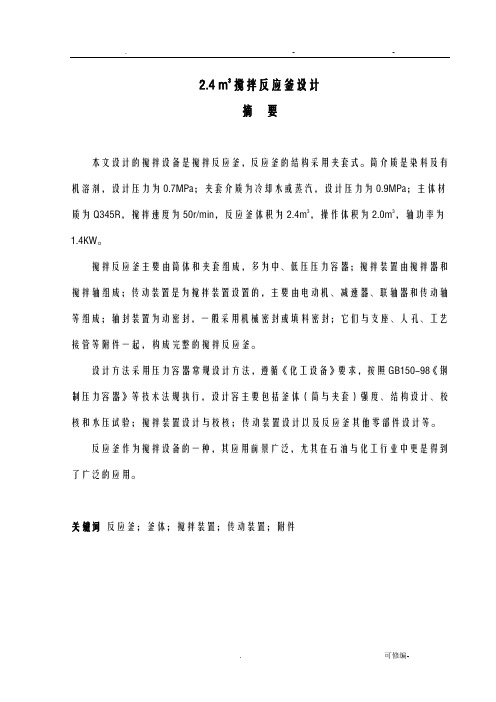
引言
反应釜的广义理解即有物理或化学反应的容器,通过对容器的结构设计与参数配置,实现工艺要求的加热、蒸发、冷却及低高速的混配功能。由于反应过程中的压力不同对容器的设计要求也不尽相同。不锈钢反应釜广泛应用于石油、化工、橡胶、农药、染料、医药、食品等生产型用户和各种科研实验项目的研究,用来完成水解、中和、结晶、蒸馏、蒸发、储存、氢化、烃化、聚合、缩合、加热混配、恒温反应等工艺过程的容器。反应釜是综合反应容器,根据条件对反应釜结构功能及配置附件的设计。从开始的进料到出料均能够以较高的自动化程度完成预先设定好的步骤要求,对反应过程中的温度、压力等重要参数进行严格的调整。
图5-6人孔……………………………………………………………………………………19
图5-7视镜……………………………………………………………………………………21
图6-1联轴器结构形式及尺寸………………………………………………………………24
图6-2 C型凸缘联轴器轴头…………………………………………………………………24
图6-3搅拌器型式……………………………………………………………………………25
图6-4桨式搅拌器的结构……………………………………………………………………25
图7-1电动机结构及安装尺寸………………………………………………………………27
图7-2 机架结构……………………………………………………………………………28
表格清单
表2-1 几种搅拌设备筒体的高径比…………………………………………………………6
表3-1 封头尺寸…………………………………………………………………………… 11
连续生产反应釜的设计
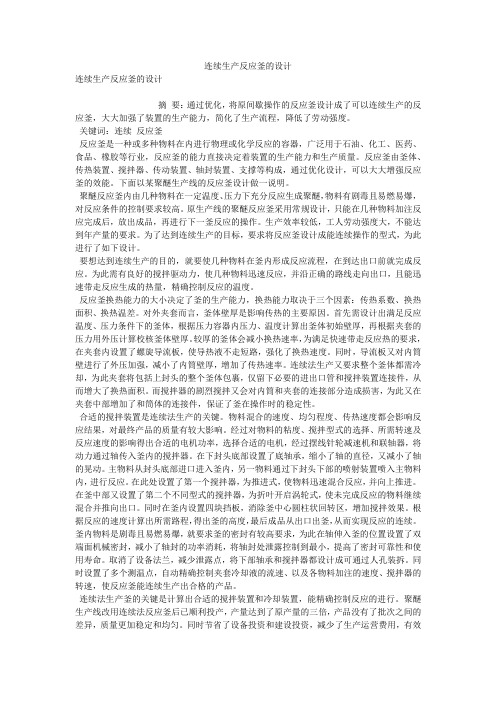
连续生产反应釜的设计连续生产反应釜的设计摘要:通过优化,将原间歇操作的反应釜设计成了可以连续生产的反应釜,大大加强了装置的生产能力,简化了生产流程,降低了劳动强度。
关键词:连续反应釜反应釜是一种或多种物料在内进行物理或化学反应的容器,广泛用于石油、化工、医药、食品、橡胶等行业,反应釜的能力直接决定着装置的生产能力和生产质量。
反应釜由釜体、传热装置、搅拌器、传动装置、轴封装置、支撑等构成,通过优化设计,可以大大增强反应釜的效能。
下面以某聚醚生产线的反应釜设计做一说明。
聚醚反应釜内由几种物料在一定温度、压力下充分反应生成聚醚,物料有剧毒且易燃易爆,对反应条件的控制要求较高。
原生产线的聚醚反应釜采用常规设计,只能在几种物料加注反应完成后,放出成品,再进行下一釜反应的操作。
生产效率较低,工人劳动强度大,不能达到年产量的要求。
为了达到连续生产的目标,要求将反应釜设计成能连续操作的型式,为此进行了如下设计。
要想达到连续生产的目的,就要使几种物料在釜内形成反应流程,在到达出口前就完成反应。
为此需有良好的搅拌驱动力,使几种物料迅速反应,并沿正确的路线走向出口,且能迅速带走反应生成的热量,精确控制反应的温度。
反应釜换热能力的大小决定了釜的生产能力,换热能力取决于三个因素:传热系数、换热面积、换热温差。
对外夹套而言,釜体壁厚是影响传热的主要原因。
首先需设计出满足反应温度、压力条件下的釜体,根据压力容器内压力、温度计算出釜体初始壁厚,再根据夹套的压力用外压计算校核釜体壁厚。
较厚的釜体会减小换热速率,为满足快速带走反应热的要求,在夹套内设置了螺旋导流板,使导热液不走短路,强化了换热速度。
同时,导流板又对内筒壁进行了外压加强,减小了内筒壁厚,增加了传热速率。
连续法生产又要求整个釜体都需冷却,为此夹套将包括上封头的整个釜体包裹,仅留下必要的进出口管和搅拌装置连接件,从而增大了换热面积。
而搅拌器的剧烈搅拌又会对内筒和夹套的连接部分造成损害,为此又在夹套中部增加了和筒体的连接件,保证了釜在操作时的稳定性。
反应釜温控系统的积分分离算法及仿真

计算机控制技术课程设计专业:自动化班级:动201302姓名:邓笛学号:2指导教师:姜香菊兰州交通大学自动化与电气工程学院2016 年 07 月 15 日化工车间反应釜的温度控制系统设计1课程设计目的反应釜内的温度控制是化工生产过程的中心环节,目的是保证反应过程的产物达到一定质量和控制要求。
由于温度能较好地测量与分析,并且能够一定程度上反映出釜内反应过程,所以选用温度为间接参数是最有效的方法。
针对本次设计要求,是以实现小型实用反应釜的控制系统为目标,主要目的就是要实现温度的智能控制。
2设计方案及原理反应釜温度控制原理反应釜主要是在罐内装入物料,使物料在其内部进行化学反应。
为了测量釜内的温度,在罐内装有钢制的温度计套管,可将温度计或温度传感器放入其中。
在进行化学之前,先将反应物按照一定的比例进行混合,然后与催化剂一同投入反应釜内,在反应釜底部通过电阻丝加热,进而提高反应釜内的温度(升温阶段),通过搅拌使物料温度均匀,当釜内温度达到预定的温度时,保持一定时间的恒温以使化学反应正常进行(恒温阶段)。
总体方案设计本次设计的要求是系统的测温范围为0~100℃,升温结束阶段向恒温阶段切换时的超调量不超过5℃。
恒温阶段的控制精度要求绝对误差不超过±2℃。
通过研究反应釜的结构和工作原理,选用温度作为控制参量,在工业生产过程中,为了保证生产正常进行,工艺要求釜底温度维持在给定值上下,或在某一小范围内变化,所以直接选取釜底温度为被控参数。
单回路控制系统原理框图如图1所示:图1 单回路控制系统原理框图单闭环基本控制原理为: 传感器将实时测量的反应釜的温度值传送到控制器的中央控制单元, 采样值与温度设定值同时送入算法子程序进行运算得到输出控制量, 输出控制量通过固态继电器( 执行器) 作用到加热电阻丝上,通过控制一个时间段内加热电阻丝的通断时间来控制加热功率。
对于工业生产中的温度控制有较大的时间延迟,采用常规的PID算法控制往往不能得到理想的控制效果,通常系统伴有较大的超调以及较长的调整时间,所以本次设计采用积分分离式PID控制算法对系统进行控制,它除了具有常规PID 控制的优点外, 还能克服对象的容量滞后, 减小动态偏差, 提高系统的稳定性, 并显着降低被调量的超调量和调整时间, 使调节过程性能得以改善。
《连续搅拌釜温度系统有限时间控制技术研究》
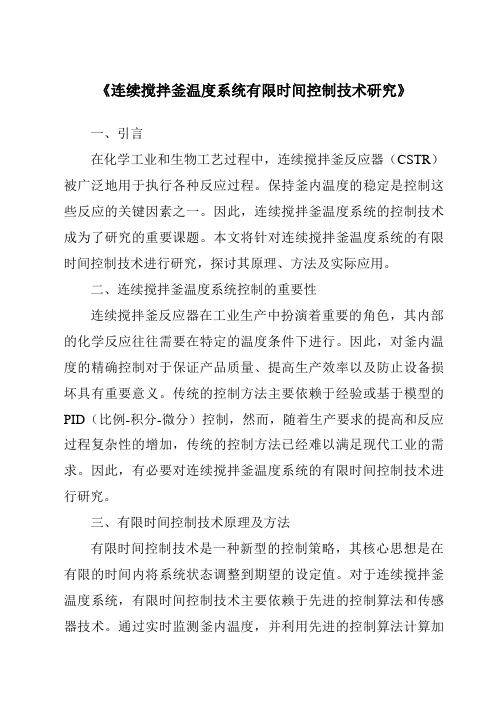
《连续搅拌釜温度系统有限时间控制技术研究》一、引言在化学工业和生物工艺过程中,连续搅拌釜反应器(CSTR)被广泛地用于执行各种反应过程。
保持釜内温度的稳定是控制这些反应的关键因素之一。
因此,连续搅拌釜温度系统的控制技术成为了研究的重要课题。
本文将针对连续搅拌釜温度系统的有限时间控制技术进行研究,探讨其原理、方法及实际应用。
二、连续搅拌釜温度系统控制的重要性连续搅拌釜反应器在工业生产中扮演着重要的角色,其内部的化学反应往往需要在特定的温度条件下进行。
因此,对釜内温度的精确控制对于保证产品质量、提高生产效率以及防止设备损坏具有重要意义。
传统的控制方法主要依赖于经验或基于模型的PID(比例-积分-微分)控制,然而,随着生产要求的提高和反应过程复杂性的增加,传统的控制方法已经难以满足现代工业的需求。
因此,有必要对连续搅拌釜温度系统的有限时间控制技术进行研究。
三、有限时间控制技术原理及方法有限时间控制技术是一种新型的控制策略,其核心思想是在有限的时间内将系统状态调整到期望的设定值。
对于连续搅拌釜温度系统,有限时间控制技术主要依赖于先进的控制算法和传感器技术。
通过实时监测釜内温度,并利用先进的控制算法计算加热或冷却的速率和量,从而在有限的时间内将釜内温度调整到期望的设定值。
四、有限时间控制技术的实现方法实现有限时间控制技术需要以下几个步骤:首先,通过传感器实时监测釜内温度;其次,利用先进的控制算法计算加热或冷却的速率和量;然后,通过执行器执行计算结果,即进行加热或冷却操作;最后,通过反馈机制对执行结果进行评估和调整。
其中,选择合适的传感器和控制算法是关键。
传感器需要具有高精度和高响应速度,而控制算法需要能够快速计算并给出最优的控制策略。
五、有限时间控制技术的应用及效果有限时间控制技术在连续搅拌釜温度系统中的应用已经得到了广泛的实践和验证。
通过采用这种控制技术,可以显著提高釜内温度的稳定性和响应速度,从而保证产品质量和生产效率。
基于CFD仿真分析的搅拌反应釜混合特性研究

[13] Birchall V S,Rocha S D F,Mansur M B,et al. A simplified mecha-
er Organic Ligands,Plenum Press,New York. p 3( 1976) .
nistic analysis of the hydration of magnesia [J]. Can. J. Chem.
Reactive Magnesium Oxide Using Hydration Agents,”J. Therm. A-
Japan ) 97: 683 - 689 ( 1987 ) ( In Japanese with English ab-
nal. Cal.,8[2]467 - 71( 2006) .
[19] Martell AM and Smith RM,Critical Stability Constants,Vol. 5: First
Eng.,2010,79: 507 - 511.
Supplements,Plenum Press,New York. p 418( 1982) .
[14] D. Filippou,N. Katiforis,N. Papassiopi,and K. Adam,“On the Ki- [20] Nakanishi K,Fukuda T and Nomura J,Formation mechanism of Mg
Key words: CDF simulation; Stirred tank reactor; Mixing characteristics
DOI:10.16570/ki.issn1673-6850.2019.01.005
1 前言
搅拌反应釜设计范文
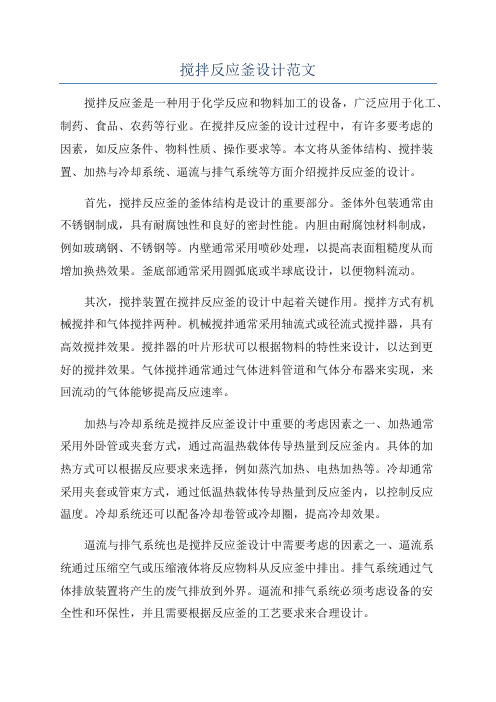
搅拌反应釜设计范文搅拌反应釜是一种用于化学反应和物料加工的设备,广泛应用于化工、制药、食品、农药等行业。
在搅拌反应釜的设计过程中,有许多要考虑的因素,如反应条件、物料性质、操作要求等。
本文将从釜体结构、搅拌装置、加热与冷却系统、逼流与排气系统等方面介绍搅拌反应釜的设计。
首先,搅拌反应釜的釜体结构是设计的重要部分。
釜体外包装通常由不锈钢制成,具有耐腐蚀性和良好的密封性能。
内胆由耐腐蚀材料制成,例如玻璃钢、不锈钢等。
内壁通常采用喷砂处理,以提高表面粗糙度从而增加换热效果。
釜底部通常采用圆弧底或半球底设计,以便物料流动。
其次,搅拌装置在搅拌反应釜的设计中起着关键作用。
搅拌方式有机械搅拌和气体搅拌两种。
机械搅拌通常采用轴流式或径流式搅拌器,具有高效搅拌效果。
搅拌器的叶片形状可以根据物料的特性来设计,以达到更好的搅拌效果。
气体搅拌通常通过气体进料管道和气体分布器来实现,来回流动的气体能够提高反应速率。
加热与冷却系统是搅拌反应釜设计中重要的考虑因素之一、加热通常采用外卧管或夹套方式,通过高温热载体传导热量到反应釜内。
具体的加热方式可以根据反应要求来选择,例如蒸汽加热、电热加热等。
冷却通常采用夹套或管束方式,通过低温热载体传导热量到反应釜内,以控制反应温度。
冷却系统还可以配备冷却卷管或冷却圈,提高冷却效果。
逼流与排气系统也是搅拌反应釜设计中需要考虑的因素之一、逼流系统通过压缩空气或压缩液体将反应物料从反应釜中排出。
排气系统通过气体排放装置将产生的废气排放到外界。
逼流和排气系统必须考虑设备的安全性和环保性,并且需要根据反应釜的工艺要求来合理设计。
另外,搅拌反应釜的设计还需要考虑控制系统和安全系统。
控制系统通常包括温度、压力、搅拌速度等参数的监测和控制。
安全系统通常包括温度、压力、液位等参数的监测和报警装置,以确保设备的安全运行。
总结起来,搅拌反应釜的设计需要综合考虑釜体结构、搅拌装置、加热与冷却系统、逼流与排气系统等因素。
实验二 连续搅拌釜式反应器液体停留时间分布及其流动模型的测定
实验二 连续搅拌釜式反应器 液体停留时间分布及其流动模型的测定一、实验目的当流体连续流过搅拌釜式反应器时,由于各种原因造成物料质点在反应器内停留不一定完全相同,因此形成不同的停留时间分布。
不同停留时间分布直接影响反应的结果(如反应的最终转化率可能不同)。
单级连续搅拌釜式反应器的理想流动模型为全混流模型,而实际反应器是否达到理想流动模型,需要通过实验来检验。
非理想流动反应器的流动模型也需要通过实验来确定。
多级连续搅拌釜式反应器的流动特性和流动模型也都需要通过实验进行研究。
连续流动的搅拌釜式反应器的流动特性的研究和流动模型的确立,一般采用实验测定停留时间分布的方法。
实验测定停留时间分布的方法常用的脉冲激发——响应技术。
本实验采用脉冲激发的方法测定液体(水)连续流过搅拌釜式反应器的停留时间分布曲线。
由此了解反应器的流动特性和流动模型。
通过本实验,使实验者观察和了解连续流动的单级、二级串联或三级串联搅拌釜式反应器的结构、流程和操作方法;掌握一种测定停留时间分布的实验技术;初步掌握液体连续流过搅拌釜式反应器的流动模型的检验和模型参数的测定方法。
无疑,通过实验对于停留时间分布与返混的概念,以及有关流动特性数学模型的概念、原理和研究方法会有更具体的了解和更加深入的理解。
二、实验原理流体流经反应器的流动状况,可以采用激发—响应技术,通过实验测定停留时间分布的方法,以一定的表达方式加以描述。
本实验采用的脉冲激发方法是在设备入口处,向主体流体瞬时注入少量示踪剂,与此同时在设备出口处检测示踪剂的浓度)(t c 随时间t 的变化关系数据或变化关系曲线。
由实验测得的t t c -)(变化关系曲线可以直接转换为停留时间分布密度t t E -)(随时间t 的关系曲线。
由实验测得的t t E -)(曲线的图像,可以定性判断流体流经反应器的流动状况。
由实验测得全混流反应器和多级串联全混流反应器的t t E -)(曲线的典型图像如图1所示。
基于Koopman算子的连续搅拌反应釜的模型预测控制
基于Koopman算子的连续搅拌反应釜的模型预测控制目录一、内容描述 (2)1.1 研究背景 (3)1.2 研究目的与意义 (4)1.3 文献综述 (5)二、Koopman算子理论基础 (6)2.1 Koopman算子的定义与性质 (8)2.2 Koopman算子在连续系统中的应用 (9)2.3 Koopman算子与模型预测控制的结合 (10)三、连续搅拌反应釜的数学模型 (11)3.1 反应釜的动态平衡方程 (13)3.2 反应釜中的传递关系 (14)3.3 常微分方程组的建立 (15)四、基于Koopman算子的模型预测控制方法 (16)4.1 Koopman算子在线性化模型中的应用 (17)4.2 状态空间表示与Koopman算子的转换 (19)4.3 动态矩阵预测控制算法 (20)4.4 其他改进的Koopman模型预测控制方法 (21)五、仿真实验设计与结果分析 (23)5.1 仿真实验硬件平台与参数设置 (24)5.2 实验设计与工况选择 (25)5.3 结果分析 (26)六、结论与展望 (28)6.1 研究成果总结 (29)6.2 研究不足与局限性 (30)6.3 未来研究方向与应用前景 (31)一、内容描述CRF作为化工领域中的核心设备,其内部过程的动态特性复杂多变,传统的控制方法往往难以应对。
本文引入了Koopman算子,这一强大的数学工具,能够将非线性系统的状态空间表达式转换为线性可测的形式,从而为MPC的实现提供了新的途径。
在详细阐述Koopman算子理论的基础上,文档进一步讨论了如何将该理论应用于CRF的MPC设计中。
通过构建CRF的数学模型,并结合Koopman算子,我们实现了对反应釜温度、压力等关键操作参数的精确线性化表示。
这不仅简化了控制器的设计过程,还提高了控制精度和效率。
文档还重点介绍了所设计的MPC控制算法。
该算法结合了实时数据采集、预测控制、反馈校正等多个环节,能够根据实时工况智能地调整控制策略,以实现CRF的高效、稳定运行。
搅拌反应釜的方案设计书(2)
1.绪论搅拌可以使两种或多种不同的物质在彼此之中互相分散,从而达到均匀混合;也可以加速传热和传质过程。
在工业生产中,搅拌操作是从化学工业开始的,围绕食品、纤维、造纸、石油、水处理等,作为工艺过程的一部分而被广泛应用。
搅拌操作分为机械搅拌和气流搅拌。
气流搅拌是利用气体鼓泡通过液体层,对液体产生搅拌作用,或使气体群以密集状态上升借所谓气升作用促进液体产生对流循环。
与机械搅拌相比,仅气泡的作用对液体所进行的搅拌是比较弱的,对于几千毫帕.秒以上的高黏度液体是难以适用的。
但气流搅拌无运动部件,所以在处理腐蚀性液体,高温高压条件下的反应液体的搅拌是很便利的。
在工业生产中,大多数的搅拌操作是机械搅拌。
搅拌设备主要由搅拌装置、轴封和搅拌罐三大部分组成。
从1-1图中可以看出,一台反应釜大致由:釜体部分、传热、搅拌、传动及密封等装置组成。
釜体部分有包容物料反应的空间,由筒体及上下封头组成传热装置是为了送入或带走热量,图中的是夹套传热装置结构。
搅拌装置由搅拌器与搅拌轴组成。
为了给搅拌传动,就需要传动的装置,用电机经V带传动,蜗杆减速机减速后,在经过联轴器带动搅拌器转动。
反应釜上的密封装置有两种类型:静密封是指管法兰,设备法兰等处的密封;动密封是指转轴出口处的机械密封或填料密封等。
反应釜上还根据工艺要求配有各种接管口、人孔、手孔、视镜及支座等部件。
反应釜的机械设计是在工艺要求确定之后进行的。
反应釜的工艺要求通常包括反应釜的容积,最大工作压力,工作温度,工作介质及腐蚀情况,传热面积,搅拌形式,转速及功率,配备哪些接管等几项内容。
这些要求一般以表格及示意图形式反应在工艺人员提出的设备设计要求当中。
搅拌设备在工业中的作用和地位:化工过程可分为传递过程(热量传递、质量传递的物理过程)和化学反应过程。
通常,反应设备都是过程工业的核心设备。
本课题之所以介绍搅拌设备,这是因为搅拌设备是一种典型的在静态容器的基础上加入动态机械的特殊设备。
2.5 理想混合连续搅拌釜式反应器(CSTR)
将出口处的浓度、温度等参数代入得到出口处反应速率,将其代入基础
设计式即得。
如:恒温恒容不可逆反应
1 k
CA0 xA
n=0 n=1
CA0 xA kCA0 (1 xA)
xA k(1 xA)
n=2
CA0 xA
kC
2 A0
(1
xA )2
kCA0
x
A
(1
x
A
)2
图解法
在连续操作釜式反应器内,过程参数与空间位置、时间无关, 各处的物料组成和温度都是相同的,且等于出口处的组成和温度。
连续操作釜式反应器适用于产量大的产品生产,特别适宜对温 度敏感的化学反应。容易自动控制,操作简单,节省人力。稳定性 好,操作安全。
单个连续操作釜式反应器(1-CSTR)
基础设计式
连续操作釜式反应器 单个连续釜 多个串联连续釜
理想混合连续搅拌釜式反应器(CSTR)
连续操作釜式反应器的结构和间歇操作釜式反应器相同,但进 出物料的操作是连续的,即一边连续恒定地向反应器内加入反应物, 同时连续不断地把反应产物引出反应器。这样的流动状况很接近理 想混合流动模型或全混流模型。
例3-5、例3-6讲解
多个串联连续操作釜式反应器(N-CSTR)
为什么要采用N-CSTR代替1-CSTR?
由于1-CSTR存在严重的返混,降低了反应速率,同时容易在某些反应中导 致副反应的增加。
为了降低逆向混合的程度,又发挥其优点,可采用N-CSTR,这样可以使 物料浓度呈阶梯状下降,有效提高反应速率;
例题讲解。
图解法
适用于级数较高的化学反应,特别适于非一、二级反应,但只适于(rA)能用单一组分表示的简单反应,对复杂反应不适用。