国外典型紧密纺纱系统的机械结构与性能特点
紧密纺纱技术的性能特点及生产实践
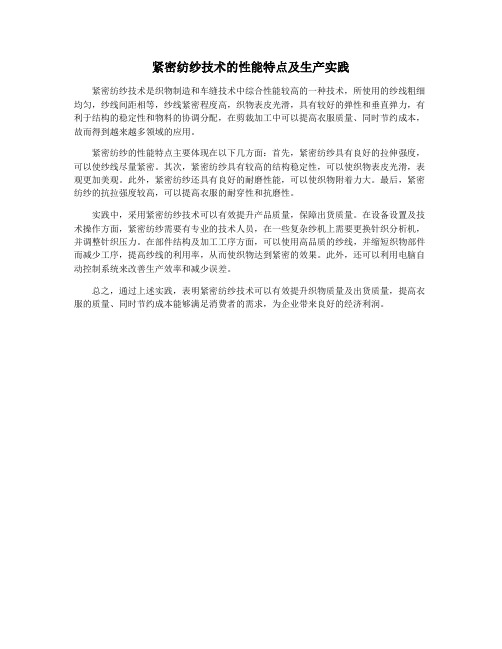
紧密纺纱技术的性能特点及生产实践
紧密纺纱技术是织物制造和车缝技术中综合性能较高的一种技术,所使用的纱线粗细均匀,纱线间距相等,纱线紧密程度高,织物表皮光滑,具有较好的弹性和垂直弹力,有利于结构的稳定性和物料的协调分配,在剪裁加工中可以提高衣服质量、同时节约成本,故而得到越来越多领域的应用。
紧密纺纱的性能特点主要体现在以下几方面:首先,紧密纺纱具有良好的拉伸强度,可以使纱线尽量紧密。
其次,紧密纺纱具有较高的结构稳定性,可以使织物表皮光滑,表观更加美观。
此外,紧密纺纱还具有良好的耐磨性能,可以使织物附着力大。
最后,紧密纺纱的抗拉强度较高,可以提高衣服的耐穿性和抗磨性。
实践中,采用紧密纺纱技术可以有效提升产品质量,保障出货质量。
在设备设置及技术操作方面,紧密纺纱需要有专业的技术人员,在一些复杂纱机上需要更换针织分析机,并调整针织压力。
在部件结构及加工工序方面,可以使用高品质的纱线,并缩短织物部件而减少工序,提高纱线的利用率,从而使织物达到紧密的效果。
此外,还可以利用电脑自动控制系统来改善生产效率和减少误差。
总之,通过上述实践,表明紧密纺纱技术可以有效提升织物质量及出货质量,提高衣服的质量、同时节约成本能够满足消费者的需求,为企业带来良好的经济利润。
紧密纺纱的原理性能特点及产品开发
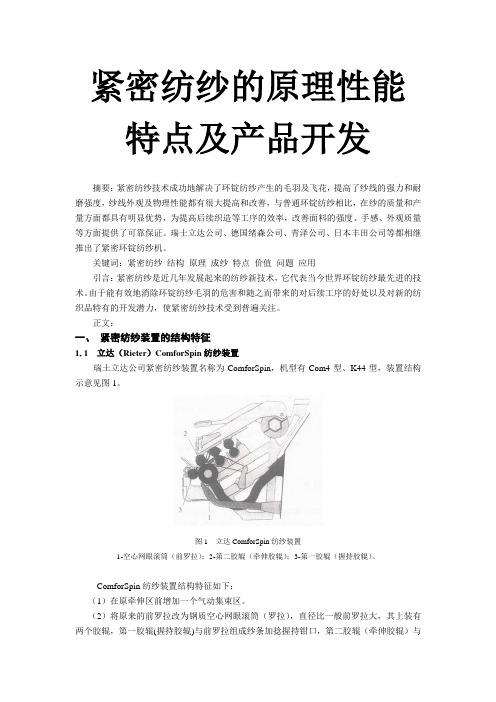
紧密纺纱的原理性能特点及产品开发摘要:紧密纺纱技术成功地解决了环锭纺纱产生的毛羽及飞花,提高了纱线的强力和耐磨强度,纱线外观及物理性能都有很大提高和改善,与普通环锭纺纱相比,在纱的质量和产量方面都具有明显优势,为提高后续织造等工序的效率,改善面料的强度、手感、外观质量等方面提供了可靠保证。
瑞士立达公司、德国绪森公司、青泽公司、日本丰田公司等都相继推出了紧密环锭纺纱机。
关键词:紧密纺纱结构原理成纱特点价值问题应用引言:紧密纺纱是近几年发展起来的纺纱新技术,它代表当今世界环锭纺纱最先进的技术。
由于能有效地消除环锭纺纱毛羽的危害和随之而带来的对后续工序的好处以及对新的纺织品特有的开发潜力,使紧密纺纱技术受到普遍关注。
正文:一、紧密纺纱装置的结构特征1.1 立达(Rieter)ComforSpin纺纱装置瑞土立达公司紧密纺纱装置名称为ComforSpin,机型有Com4型、K44型,装置结构示意见图1。
图1 立达ComforSpin纺纱装置1-空心网眼滚筒(前罗拉);2-第二胶辊(牵伸胶辊);3-第一胶辊(握持胶辊)。
ComforSpin纺纱装置结构特征如下:(1)在原牵伸区前增加一个气动集束区。
(2)将原来的前罗拉改为钢质空心网眼滚筒(罗拉),直径比一般前罗拉大,其上装有两个胶辊,第一胶辊(握持胶辊)与前罗拉组成纱条加捻握持钳口,第二胶辊(牵伸胶辊)与前罗拉组成牵伸区的前牵伸钳口。
第一胶辊与第二胶辊间为须条的集聚区。
(3)前罗拉为钢质网眼滚筒,形似一个小尘笼,内有圆形截面吸聚管(负压)与吸风风机等组成吸聚罗拉,即有负压的前罗拉。
圆形截面吸聚管上装有一块开了一个由后向前逐渐变窄的V形狭槽的工程塑料部件组成的吸气槽,V形槽长度跟须条与前罗拉接触长度相适应,并与输出方向有一定偏斜度,当在主牵伸区须条离开牵伸钳口时,因负压的吸附作用,须条由V形槽控制在网眼前罗拉上,并向前输送到第一胶辊处,即握持钳口处。
1.2 绪森(Suessen)Elite纺纱装置德国绪森公司紧密纺纱装置名称为Elite,机型有Fiomax E1型、Fiomax E2型,装置结构示意见图2。
紧密赛络纺棉纱的结构及性能研究
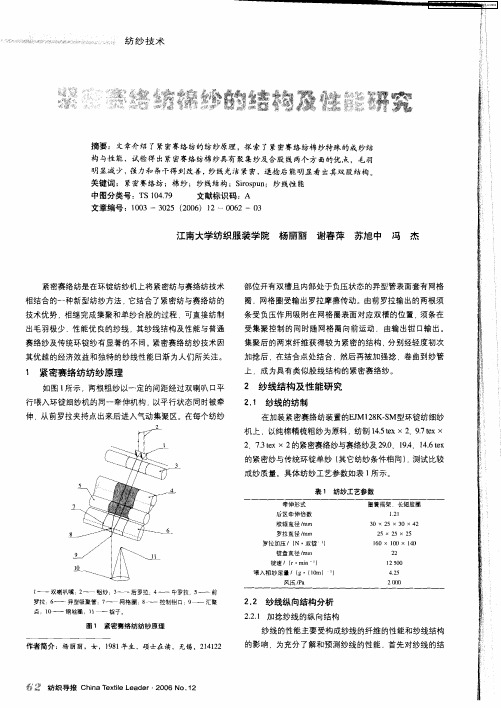
的紧密纱与传统环锭单纱 ( 其它纺纱条件相同) 测试 比较 成纱质量。具体纺纱工艺参数如表 1 所示。
表 1 纺纱工 艺参数
l 一一 双喇叭嘴 : 一一 粗纱 3 一 后罗拉 4 2 一 —— 中罗拉 , —— 前 5
罗拉,6 —— 异型吸聚管: 一 7 网格圈 8—— 控制钳 口j 9—— 汇聚
加捻 后 ,在 结合 点处 结 合 ,然后 再被 加强 捻 . 曲到纱 管 卷
相结合的一种新型纺纱方法 , 它结合 了紧密纺与赛络纺的
技术优势, 相继完成集聚和单纱合股的过程 可直接纺制
出毛羽 极少 .性 能优 良的纱 线 , 其纱 线 结构 及性 能与普 通
赛络纱及传统环锭纱有显著的不同。 紧密赛络纺纱技术 因
图 4 赛络 纺 棉 纱
是由于与赛络纺相比, 紧密赛络纺中的双股纱在合股前分 别经集聚作用 , 使纱线集聚紧密 紧密纺纱是明显均匀的 单股。
从图中可以看出 紧密赛络纺纱线的表面及外观与紧 密纺单纱相比较 具有更清晰的表面结构及紧密的状态 纱体均匀、圆滑 表面毛羽少 , 这主要是因为经过集聚区 后两根单纱不再有纺纱三 角区, 从而不会出现纤维从纱线
明 显减 少,强力和 条干得 到 改善 , 线光洁 紧密 ,退捻 后 能明显 看 出其双 股 结构 纱
关键词 :紧密赛络 纺;棉纱;纱线结构;Srsu ;纱线性 能 i pn o 中图分类号:T 0 , S14 9 7 文献标识码 :A 文章编号 :10 0 3—3 2 (0 6 2—06 05 20 )l 02—0 3
23 纱线性能的测试与分析 .
2 . 纱线强伸性能 .1 3 用陕西长岭纺织机 电厂生产 的Y 0 3 自动单纱强 G6全
中分离出来或被嵌入到另一根纱中的现象 纤维须条整齐
紧密纺特点
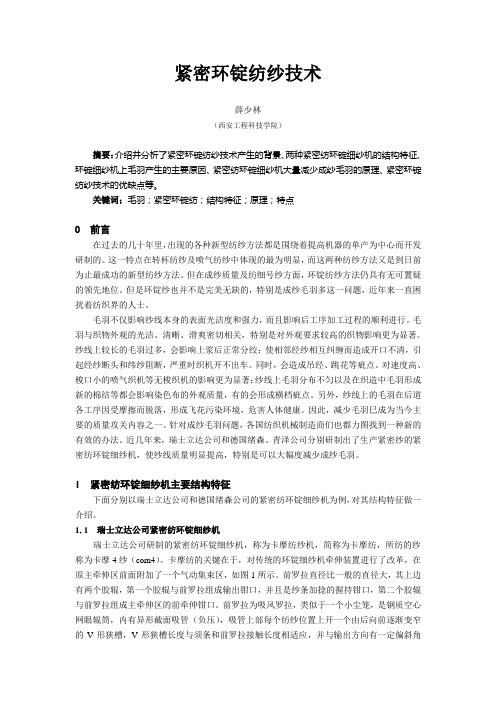
紧密环锭纺纱技术薛少林(西安工程科技学院)摘要:介绍并分析了紧密环锭纺纱技术产生的背景、两种紧密纺环锭细纱机的结构特征、环锭细纱机上毛羽产生的主要原因、紧密纺环锭细纱机大量减少成纱毛羽的原理、紧密环锭纺纱技术的优缺点等。
关键词;毛羽;紧密环锭纺;结构特征;原理;特点0 前言在过去的几十年里,出现的各种新型纺纱方法都是围绕着提高机器的单产为中心而开发研制的。
这一特点在转杯纺纱及喷气纺纱中体现的最为明显,而这两种纺纱方法又是到日前为止最成功的新型纺纱方法。
但在成纱质量及纺细号纱方面,环锭纺纱方法仍具有无可置疑的领先地位。
但是环锭纱也并不是完美无缺的,特别是成纱毛羽多这一问题,近年来一直困扰着纺织界的人士。
毛羽不仅影响纱线本身的表面光洁度和强力,而且影响后工序加工过程的顺利进行。
毛羽与织物外观的光洁、清晰、滑爽密切相关,特别是对外观要求较高的织物影响更为显著。
纱线上较长的毛羽过多,会影响上浆后正常分绞;使相邻经纱相互纠缠而造成开口不清,引起经纱断头和纬纱阻断,严重时织机开不出车。
同时,会造成吊经、跳花等疵点。
对速度高、梭口小的喷气织机等无梭织机的影响更为显著;纱线上毛羽分布不匀以及在织造中毛羽形成新的棉结等都会影响染色布的外观质量,有的会形成横档疵点。
另外,纱线上的毛羽在后道各工序因受摩擦而脱落,形成飞花污染环境,危害人体健康。
因此,减少毛羽巳成为当今主要的质量攻关内容之一。
针对成纱毛羽问题,各国纺织机械制造商们也都力图找到一种新的有效的办法。
近几年来,瑞士立达公司和德国绪森、青泽公司分别研制出了生产紧密纱的紧密纺环锭细纱机,使纱线质量明显提高,特别是可以大幅度减少成纱毛羽。
l 紧密纺环锭细纱机主要结构特征下面分别以瑞士立达公司和德国绪森公司的紧密纺环锭细纱机为例,对其结构特征做一介绍。
1.1 瑞士立达公司紧密纺环锭细纱机瑞士立达公司研制的紧密纺环锭细纱机,称为卡摩纺纱机,简称为卡摩纺,所纺的纱称为卡摩4纱(com4)。
几种紧密纺对比
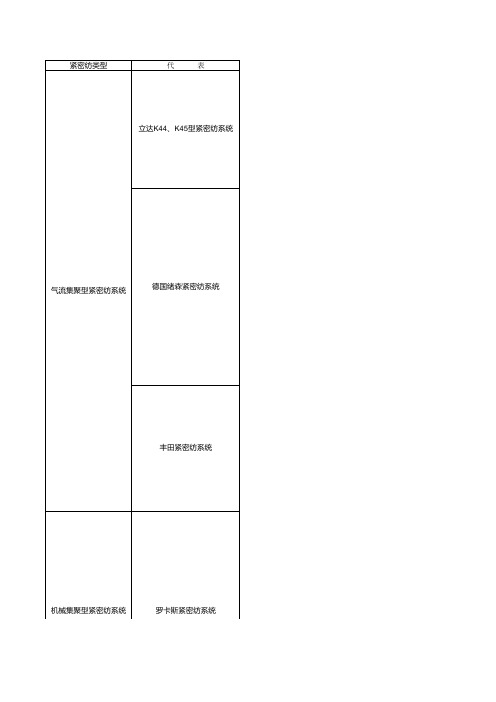
牵伸胶辊和控制胶辊的直径太小(最大仅为φ 21),皮辊加工和回磨比较困难,并且小规格的皮 辊轴承难以加工和制造,质量难以保证 集聚磁块位于牵伸皮辊和控制皮辊之间,前后移动 量很小,定位不准确极易造成皮辊的磨损,降低其 使用寿命,增加使用成本 由于前罗拉上面需要安装两个皮辊,使牵伸皮辊不 但不能前冲,而且必须后移以让出集聚磁块的空 间,使纱线条干受到一定影响
保持了原牵伸装置的部件和工艺不变,在前罗拉的前部增加一套紧密纺装置 集聚区采用异形截面的负压吸风管,外部套有尼龙材质网格圈,由控制皮辊提供的摩擦力带动网格圈转动,控 制皮辊由前皮辊直接传动
一节异形管上的六个网格圈的张力由一根重力棒提供
在原前罗拉的前面增加集聚装置,保持原细纱机的牵伸装置和工艺不变 集聚装置中包括一列控制罗拉,组成独特的四罗 网格圈的传动由控制罗拉和控制皮辊夹持积极运动 网格圈采用弹簧张力架提供张力,每只网格圈由一个张力架单独提供
结构简单,不需要负压系统 将原前罗拉上的牵伸皮辊更换为集聚组件,包括牵伸皮辊、集聚磁块和控制皮辊,集聚磁块利用磁性紧吸在前 罗拉表面
优
缺
点
利用带孔前罗拉取代了网格圈的使用 前罗拉转速较其它形式紧密纺低,纺纱更加稳定
对纱线的集聚效果更加充分 对使用环境温湿度控制要求较高 前罗拉直径的增加带来主牵伸区的浮游纤维区的长 度增加,不利于对纤维的控制,特别是短纤维 前罗拉加工难度较大,成本较高 改造相对方便,结构紧凑,不需要更换前罗拉和增 加控制小罗拉 由于纱线集聚效果一直延伸到控制皮辊,集聚效果 较好,毛羽指标较好 由于集聚区的传动形式为前皮辊带动控制皮辊,所 以对皮辊直径的要求较高,皮辊直径直接关系到集 聚区的牵伸倍数,而皮辊在使用过程中就存在一定 变形,造成集聚区的牵伸倍数差异较大,纱线指标 不稳定 前皮辊和控制皮辊为特殊件,与普通皮辊不能通 用,需要专用的回磨设备,并且该皮辊成本较高, 增加了紧密纺的投入和使用成本 前皮辊通过皮辊组件内部的尼龙齿轮带动控制皮 辊,该尼龙齿轮容易磨损,需定期更换。并且磨损 后不易被发现。不但增加了使用成本,而且对纱线 质量造成及大隐患 需要定期对皮辊组件打开清洁,并检查尼龙齿轮的 磨损情况 集聚区由前罗拉通过过桥齿轮带动控制罗拉转动, 传动比可靠,不会发生变化,传动稳定性高 网格圈由控制罗拉和控制皮辊夹持,积极传动,传 动更加可靠 每只网格圈单独张紧,张紧力更加均匀 紧密纺装置的稳定性好,纱线质量的一致性较好, 各项数据的锭间差异较小 控制皮辊、前皮辊与普通环锭纺皮辊通用,使用保 养更加方便,使用成本较低 由于增加一列控制罗拉,造成纱线集聚后有需经过 一段自由区后进入控制钳口,纤维进入控制钳口前 集聚效果有稍微回弹 改造较为简单,对原机设备改动较小 不需要负压系统,能降低能耗 由于磁块紧贴在前罗拉表面,使用过程中噪声较 大,并且长期使用对前罗拉损坏较大 通过机械形式对纱线集聚,纱架有一定阻力,在高 速情况下断头较多 品种支数差别较大时需要更换集聚磁块,产品的适 应性较差,尤其不适应高支品种 纱线在落筒过后毛羽回弹较大
紧密纺特点
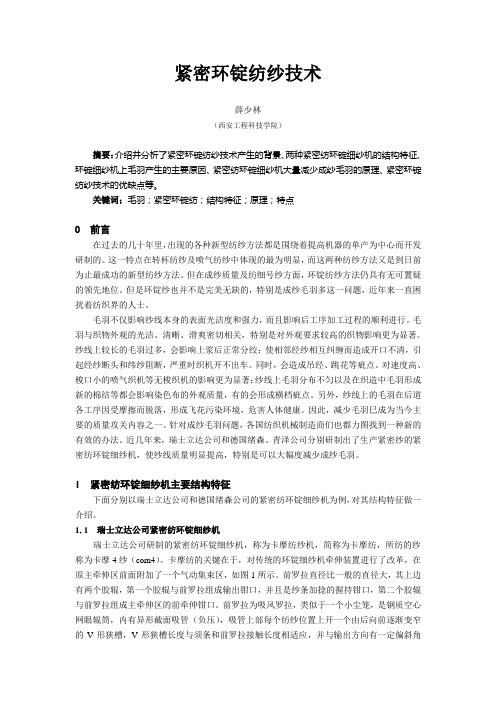
紧密环锭纺纱技术薛少林(西安工程科技学院)摘要:介绍并分析了紧密环锭纺纱技术产生的背景、两种紧密纺环锭细纱机的结构特征、环锭细纱机上毛羽产生的主要原因、紧密纺环锭细纱机大量减少成纱毛羽的原理、紧密环锭纺纱技术的优缺点等。
关键词;毛羽;紧密环锭纺;结构特征;原理;特点0 前言在过去的几十年里,出现的各种新型纺纱方法都是围绕着提高机器的单产为中心而开发研制的。
这一特点在转杯纺纱及喷气纺纱中体现的最为明显,而这两种纺纱方法又是到日前为止最成功的新型纺纱方法。
但在成纱质量及纺细号纱方面,环锭纺纱方法仍具有无可置疑的领先地位。
但是环锭纱也并不是完美无缺的,特别是成纱毛羽多这一问题,近年来一直困扰着纺织界的人士。
毛羽不仅影响纱线本身的表面光洁度和强力,而且影响后工序加工过程的顺利进行。
毛羽与织物外观的光洁、清晰、滑爽密切相关,特别是对外观要求较高的织物影响更为显著。
纱线上较长的毛羽过多,会影响上浆后正常分绞;使相邻经纱相互纠缠而造成开口不清,引起经纱断头和纬纱阻断,严重时织机开不出车。
同时,会造成吊经、跳花等疵点。
对速度高、梭口小的喷气织机等无梭织机的影响更为显著;纱线上毛羽分布不匀以及在织造中毛羽形成新的棉结等都会影响染色布的外观质量,有的会形成横档疵点。
另外,纱线上的毛羽在后道各工序因受摩擦而脱落,形成飞花污染环境,危害人体健康。
因此,减少毛羽巳成为当今主要的质量攻关内容之一。
针对成纱毛羽问题,各国纺织机械制造商们也都力图找到一种新的有效的办法。
近几年来,瑞士立达公司和德国绪森、青泽公司分别研制出了生产紧密纱的紧密纺环锭细纱机,使纱线质量明显提高,特别是可以大幅度减少成纱毛羽。
l 紧密纺环锭细纱机主要结构特征下面分别以瑞士立达公司和德国绪森公司的紧密纺环锭细纱机为例,对其结构特征做一介绍。
1.1 瑞士立达公司紧密纺环锭细纱机瑞士立达公司研制的紧密纺环锭细纱机,称为卡摩纺纱机,简称为卡摩纺,所纺的纱称为卡摩4纱(com4)。
紧密纺纱技术及其纺纱系统评述
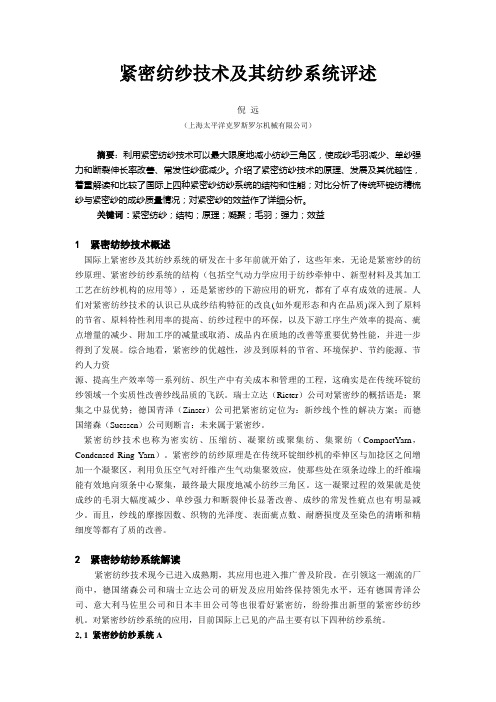
紧密纺纱技术及其纺纱系统评述倪远(上海太平洋克罗斯罗尔机械有限公司)摘要:利用紧密纺纱技术可以最大限度地减小纺纱三角区,使成纱毛羽减少、单纱强力和断裂伸长率改善、常发性纱疵减少。
介绍了紧密纺纱技术的原理、发展及其优越性,着重解读和比较了国际上四种紧密纱纺纱系统的结构和性能;对比分析了传统环锭纺精梳纱与紧密纱的成纱质量情况;对紧密纱的效益作了详细分析。
关键词:紧密纺纱;结构;原理;凝聚;毛羽;强力;效益1 紧密纺纱技术概述国际上紧密纱及其纺纱系统的研发在十多年前就开始了,这些年来,无论是紧密纱的纺纱原理、紧密纱纺纱系统的结构(包括空气动力学应用于纺纱牵伸中、新型材料及其加工工艺在纺纱机构的应用等),还是紧密纱的下游应用的研究,都有了卓有成效的进展。
人们对紧密纺纱技术的认识已从成纱结构特征的改良(如外观形态和内在品质)深入到了原料的节省、原料特性利用率的提高、纺纱过程中的环保,以及下游工序生产效率的提高、疵点增量的减少、附加工序的减量或取消、成品内在质地的改善等重要优势性能,并进一步得到了发展。
综合地看,紧密纱的优越性,涉及到原料的节省、环境保护、节约能源、节约人力资源、提高生产效率等一系列纺、织生产中有关成本和管理的工程,这确实是在传统环锭纺纱领域一个实质性改善纱线品质的飞跃。
瑞士立达(Rieter)公司对紧密纱的概括语是:聚集之中显优势;德国青泽(Zinser)公司把紧密纺定位为:新纱线个性的解决方案;而德国绪森(Suessen)公司则断言:未来属于紧密纱。
紧密纺纱技术也称为密实纺、压缩纺、凝聚纺或聚集纺、集聚纺(CompactYarn,Condensed Ring Yarn)。
紧密纱的纺纱原理是在传统环锭细纱机的牵伸区与加捻区之间增加一个凝聚区,利用负压空气对纤维产生气动集聚效应,使那些处在须条边缘上的纤维端能有效地向须条中心聚集,最终最大限度地减小纺纱三角区。
这一凝聚过程的效果就是使成纱的毛羽大幅度减少、单纱强力和断裂伸长显著改善、成纱的常发性疵点也有明显减少。
紧密纺纱技术及紧密纺纱特性分析

第3期2005年9月化纤与纺织技术ChemicalFiber&TextileTechnology文章编号:1672—500X(2005)03—001l一03紧密纺纱技术及紧密纺纱特性分析陶珏(淮安东方清棉纺织有限公司,江苏淮安223002)摘要:介绍紧密纺纱技术如何消除纺纱三角区来提高成纱质量,介绍紧密纺纱技术的纺纱机理及其特性。
关键词:紧密纺纱纺纱三角区毛羽环锭纺条干中图分类号:TS103.27+7文献标识码:B1引言一种在普通环锭纺纱机纺纱原理的基础上发展而成的紧密纺纱技术已被成功地研制和推广。
紧密纺作为一种新型纺纱方法,以其独特的纺纱原理,改善了环锭纺成纱的结构,其优越的纱线性能,显著的经济效益,引起了国内外纺织行业的密切关注。
据统计国内引进紧密纺纱设备已有几十万纱锭,国内各纺机厂也相继开发研制紧密纺纱机。
除个别厂大都有以网眼(格)胶圈加吸风槽为基本形式。
现就国产紧密纺纱机进行研究和分析。
2传统纺纱机的缺陷和紧密纺纱技术的纺纱机理传统环锭纺细纱机就是在牵伸区对粗纱施加一定的牵伸比,以获得所需要的纱线支数。
为了使纱线获得所要的强度必须加上捻度,束纤维在细纱前罗拉输出处到加捻成细纱加捻点之间形成纺纱加捻三角区。
当纤维进入三角区时几乎失去控制,完全处于松散状态,边缘纤维在加捻前脱离主体成为飞花,据统计细纱车间约有80%以上的飞花由此处造成,也有的可能成为毛羽,是因为纤维一端被捻入纱体,另一端就造成毛羽,另外在纺纱三角区中,’三角形两边的纤维比三角形中间的纤维所受的张力大,纺出的纱在受力时纤维不能平均负担,两边的纤维先断,成纱断裂强度达不到应有的水平,造成强力或高或低不稳定,因此普通环锭纺加工过程还得进一步改善。
紧密纺是在环锭纺纱细纱机上进行重大革新和创造的纺纱技术,在环锭纺纱机上的牵伸与加捻之间加上一种特殊的新型纺纱装置——集聚装置,来彻底消除环锭纺中存在的加捻三角区。
即扁平的须条从前罗拉输出时,纤维束受空气负压气流的压缩与控制,在负压气流与一定角度的吸风口复合作用下,很快地把一定宽度的纤维束横向收缩,使纤维束的宽度柔和地转化为成纱的宽度,边缘纤维向中间集聚,须条在纤维排列平顺、紧密、受力均匀的情况下被加捻,纤维之间的抱合力大大增加,成纱的结构和机械物理性能及纤维的强力利用情况都将得到明显的改善。
- 1、下载文档前请自行甄别文档内容的完整性,平台不提供额外的编辑、内容补充、找答案等附加服务。
- 2、"仅部分预览"的文档,不可在线预览部分如存在完整性等问题,可反馈申请退款(可完整预览的文档不适用该条件!)。
- 3、如文档侵犯您的权益,请联系客服反馈,我们会尽快为您处理(人工客服工作时间:9:00-18:30)。
国外典型紧密纺纱系统的机械结构与性能特点王维亚【摘要】Compact spinning is the important innovation and upgrading of ring spinning.Asthe most prominent technological advances in ring spinning,it attracts people′s wide attention.The principle of compact spinning and six typical overseas compact spinning system%紧密纺是环锭纺的重大革新与升级,它作为环锭纺最具标志性的技术进步受到了纺织界人士的普遍关注。
介绍了紧密纺纱原理和六种具有代表性的国外紧密纺纱系统,对其结构特征和性能特点作了详细分析。
【期刊名称】《纺织科技进展》【年(卷),期】2011(000)004【总页数】5页(P13-17)【关键词】紧密纺纱;加捻三角区;机械结构【作者】王维亚【作者单位】广东纺织职业技术学院,广东佛山528041【正文语种】中文【中图分类】TS103.271 紧密纺纱原理紧密纺是指粗纱经过细纱机罗拉牵伸后,在加捻之前,利用负压气流或机械作用,将须条横向收缩、聚拢,使须条边缘纤维有效地向纱干中心集聚,最大限度地缩小输出须条的宽度,减小甚至消除加捻三角区,纤维获得致密化加捻,从而大幅度降低毛羽,减少飞花,提高纤维利用系数和成纱强力的一种新型环锭纺纱技术。
2 国外典型的紧密纺纱系统目前国外比较有代表性的紧密纺纱系统主要有瑞士立达(Rieter)公司的Comfor Spin紧密纺纱系统、德国绪森(Suessen)公司的EliTe紧密纺纱系统、德国青泽(Zinser)公司的CompACT3紧密纺纱系统、日本丰田(Toyota)公司EST紧密纺纱系统、意大利马佐里(Marzoli)公司的Olfil紧密纺纱系统、瑞士罗托卡复特(RotorCraft)公司Rocos紧密纺纱系统等。
2.1 瑞士立达公司的Comfor Spin紧密纺纱系统瑞士立达公司的Comfor Spin紧密纺纱系统国内音译为卡摩纺。
我国的山东鲁泰、新疆溢达等多家纺织大型企业都引进了该公司的紧密纺细纱机。
该机构以传统的三罗拉长短皮圈牵伸装置为基础,保留中罗拉的胶圈和后牵伸区结构,将细纱机原来牵伸机构的实芯前罗拉改为直径为59mm的钢质中空网眼滚筒(也称集聚罗拉),在集聚罗拉中间部分周向布有吸风小孔,内部装有吸风插件,吸风插件上有与吸风小孔对应的吸风口,与负压吸风系统相连。
集聚罗拉上装有两个胶辊,前面为新增的输出胶辊,它与集聚罗拉组成输出钳口或加捻钳口。
第二个为原来牵伸装置的前胶辊,它与集聚罗拉构成主牵伸区的前钳口,这样,在集聚罗拉圆柱形的表面上,由最前方的输出胶辊和原来的前胶辊所控制的圆弧区域便形成了集聚区。
集聚罗拉担负着牵伸、吸风集聚和加捻握持三大任务。
须条在牵伸之后、加捻之前,受到由集聚罗拉和双胶辊组成的集聚控制区的气流吸风作用,负压气流透过集聚罗拉上的小孔、吸风口构件的槽形吸口排向中央吸风系统。
在此过程中,纤维受到自上而下、由边缘到中心的集聚约束,使须条宽度逐渐变窄,加捻三角区缩小,纤维保持紧密顺直的状态,被加捻成为紧密纱。
典型机型有K44和最新的K452,该紧密纺纱系统具有以下特点。
(1)结构简洁,大直径集聚罗拉集牵伸、集聚、输出、加捻握持等多项作用于一身。
(2)集聚部分无易损件,寿命长,运行成本低。
(3)须条一出牵伸钳口就进入集聚区直到输出钳口,实现了全程集聚,集聚效果好。
(4)输出胶辊与前胶辊均由集聚罗拉驱动,意味着两者之间,即集聚区内无法设置张力牵伸,对纤维伸直不利。
(5)集聚罗拉与吸风组件设计要求高、制造难度大,比较适应立达公司自身细纱机,不便与其他机型配套。
因而这种类型以瑞士Rieter公司为唯一的成功代表,目前鲜有他人采用。
图1为Rieter Comfor Spun紧密纺系统图,图2为关键机件分拆图。
2.2 德国绪森公司的EliTe紧密纺纱系统德国绪森的EliTe紧密纺纱系统示意图见图3,它保持原牵伸装置不变,在前罗拉前方设置集聚机构,即加装异形截面吸风管、网格集聚圈和输出胶辊,输出胶辊与原来的前胶辊两者组合在一起成为一个紧凑的双胶辊套件(见图5)。
集聚圈套在异形截面吸风管上,并由撑杆张紧。
输出胶辊和前胶辊的铁壳内侧附有相同齿数的齿轮,这样前胶辊通过过桥齿轮传动输出胶辊,再依靠输出胶辊对集聚圈的摩擦,带动集聚圈在异形截面吸风管上回转输送须条,吸风管与输出胶辊构成输出钳口或加捻握持钳口,吸风管固定不动并与吸风系统相连,吸风管上部工作面在对应每个纺纱位处,开有一个与纤维输出方向略呈一定角度倾斜的吸风口,纤维离开牵伸前钳口后,受到集聚区内吸风管的吸风作用,空气透过集聚圈的网孔,从吸风口经异形吸管排向中央吸风系统,纤维则被吸附到集聚圈对应有吸风口的位置处,纤维便处于压缩集聚状态,随集聚圈的回转,按照倾斜吸风口的横向吸引速度和集聚圈的向前输送速度的合成速度方向,顺着斜槽输送到输出胶辊钳口处,被握持加捻成为紧密纱。
图1 Rieter Comfor Spun紧密纺系统图图2 集聚罗拉输出胶辊前胶辊吸风插件分拆图应用该系统原理衍生的紧密纺纱机类型较多,其优点如下。
(1)紧密纺装置单独设置,集聚圈制造简单,成本低,更换方便,适合对普通细纱机的改造加装,因而这种模式已成为国内将传统环锭纺升级为紧密纺采用的主要方式之一。
(2)吸风口的长度方向和集聚圈的运动方向有一定角度的倾斜,倾斜吸风口的负压吸引力使受控须条横向运动,产生了环绕自身轴线的切向力矩,因此对须条的集聚效果有进一步辅助增强的作用。
(3)输出胶辊的直径稍大于前胶辊,可使牵伸前钳口与输出钳口之间的集聚区里产生一定的张力牵伸,有利于提高纤维的伸直平行度。
但缺点是异形截面吸管虽然尽量深入到牵伸钳口处,但仍不能做到零距离,所以无法实现全程集聚控制。
图3 Suessen EliTe紧密纺系统示意图1输出胶辊;2双胶辊架;3异形截面吸风管;4集聚圈;5断头吸管;6前罗拉;7中罗拉;8后罗拉;9进气口图4 Suessen EliTe紧密纺实物图图5 Suessen EliTe输出胶辊与前胶辊组合套件2.3 德国青泽公司的CompACT3紧密纺纱系统德国青泽公司的紧密纺纱机构示意图见图6,该机构是在传统的牵伸装置的前罗拉前方增加一根输出罗拉,其上加装输出胶辊,两者组成输出钳口,输出胶辊上装有皮圈架组件,在输出胶辊与皮圈架组件上套有集聚胶圈,胶圈的中部打有一串连贯的椭圆和圆形相间的透气孔,皮圈架内部装有吸风管,皮圈架向下的一面对应每个纺纱位处开有吸风口,通过装在摇架上的塑料管通向中央吸风系统。
吸风产生的负压使空气透过小孔和纤维束由下而上、由边缘向中心排风,同时产生的托持力使须条紧贴胶圈向前输送,机械力和空气控制力结合完成了集聚作用,随后得到加捻成为紧密纱。
图6 Zinser紧密纺示意图1输出罗拉;2集聚胶圈;3皮圈架;4前胶辊;5进气口;6前罗拉;7中罗拉;8后罗拉;9吸风系统图7 Zinser紧密纺实物图图8 Zinser集聚胶圈其典型特征是属于上置式吸风集聚型紧密纺系统,特点如下:(1)能在前罗拉钳口和输出钳口之间的集聚区内设置符合工艺需要的张力牵伸,有利于进一步提高纤维的伸直平行度。
(2)由于通气孔与须条运行方向一致,集聚区内的须条无法绕自身轴线回转,再加上多孔胶圈运行到输出钳口处时,多孔胶圈的通气孔会被输出罗拉暂时封闭,使纤维在此处失去气流的集聚作用,产生一定程度的回弹发散,集聚效果受到产生一定程度的影响。
2.4 日本丰田公司EST紧密纺纱系统丰田公司EST紧密纺系统示意图见图9,该系统是在传统的三罗拉长短皮圈牵伸装置前方设置集聚机构,由异形截面吸管、网格集聚圈与输出罗拉、输出胶辊等组成。
输出罗拉和输出胶辊安装在原前罗拉前胶辊前方,输出罗拉和输出胶辊两者组成输出钳口,在输出罗拉和前罗拉之间配合两者弧形设置一根倒三角形的异形截面吸管,集聚圈套在异形吸管和输出罗拉上,传动动力来自前罗拉,通过前罗拉齿轮、中间过桥齿轮与输出罗拉齿轮啮合,传动输出罗拉回转,输出罗拉从集聚圈的内壁积极摩擦驱动集聚圈绕异形吸管转动,与此同时输出胶辊因紧压套圈,受集聚圈外壁的摩擦而转动。
异形吸管表面开有位置相对应的纵向槽形吸口,依靠以上各部分和吸管负压的配合,对到达槽形吸口位置的须条实施集聚作用。
其特点是:结构简洁合理,凝聚元件运行稳定性好,凝聚元件不受前胶辊和加捻胶辊直径的影响,能在前罗拉钳口到加捻钳口之间设置符合工艺需要的张力牵伸。
但气流导向口没能延续到阻捻钳口下,故凝聚作用不能持续到加捻钳口的下方,对凝聚效果有所影响。
图9 Toyota EST紧密纺系统示意图1前罗拉;2前胶辊;3输出罗拉;4输出胶辊;5异形截面吸管;6集聚圈;7撑杆;8中间过桥齿轮2.5 意大利马佐里公司Olfil紧密纺纱系统意大利Marzoli Olfil紧密纺系统与绪森的紧密纺系统在结构上有很多相似之处,都属于下置式的吸风管套织物集聚圈式的气流吸风系统。
不同的是吸风管形状为圆形,其上的吸风口为直线形即与纤维运行方向一致。
传动情况是前胶辊通过同步带传动输出胶辊,输出胶辊再摩擦传动集聚圈,集聚圈绕圆形吸风管回转产生吸风集聚和输送出纤维的作用。
图10 Toyota EST紧密纺实物图图11 Toyota EST紧密纺集聚装置与其他系统相比,Olfil系统的特点是吸风狭槽比较短。
吸风管与输出胶辊组成控制钳口,控制钳口的压力可按照需要通过组合件上的螺栓调节。
Olfil紧密纺纱系统的模块化和一体化设计可按需要在普通环锭纺和紧密环锭纺之间简易地来回变换。
图12 Marzoli Olfil紧密纺系统图1吸风管;2集聚圈;3前罗拉;4输出胶辊;5前胶辊;6同步带2.6 瑞士罗托卡复特公司Rocos紧密纺纱系统该机构属纯粹的机械式集聚器件,是在传统的三罗拉牵伸装置的前罗拉上设置集聚区(图14)。
前罗拉1上包围有前胶辊2,输出胶辊3和磁性集聚器4、两钳口线之间是集聚区。
双胶辊架控制着两个胶辊,并套在前胶辊芯轴上,依靠板簧的压力使输出胶辊与前罗拉之间有足够的控制力。
图13 Marzoli Olfil紧密纺实物图图14 RotorCraft Rocos紧密纺系统图1前罗拉;2前胶辊;3输出胶辊;4磁性集聚器图15 RotorCraft Rocos前胶辊输出胶辊磁性集聚器组合套件磁性集聚器选用高性能磁性材料,其精确的外部弧形加上磁力吸引使集聚器与罗拉之间没有间隙并向前靠拢,与前罗拉形成一个完全封闭的区域。