作业准备验证程序(含表格)
IATF16949作业准备验证表
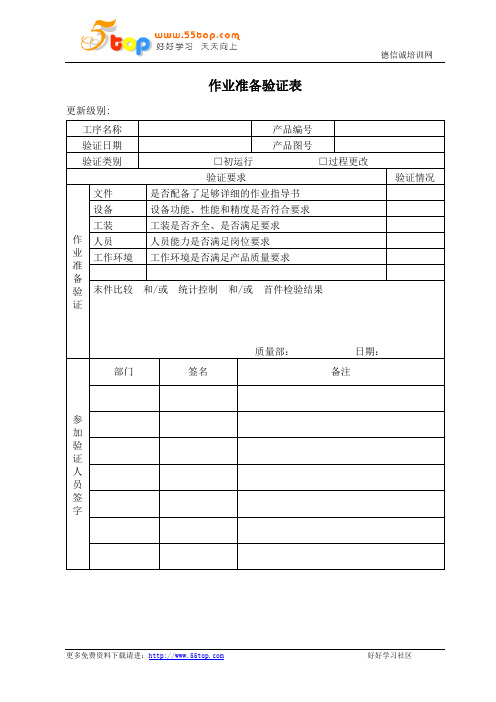
更新级别:
工序名称
产品编号
验证日期
产品图号
验证类别
□初运行□过程更改
验证要求
验证情况
作业准备验证
文件
是否配备了足够详细的作业指导书
设备
设备功能、性能和精度是否符合要求
工装
工装是否齐全、是否满足要求
人员
人员能力是否满足岗位要求
工作环境
工作环境是否满足产品质量要求
末件比较和/或统计控制和/或首件检验结果
质量部:日期:
参加验证人员签字
部门Biblioteka 签名备注作业准备验证结果认定:
生产部:日期:
作业准备的验证内审检查表模板
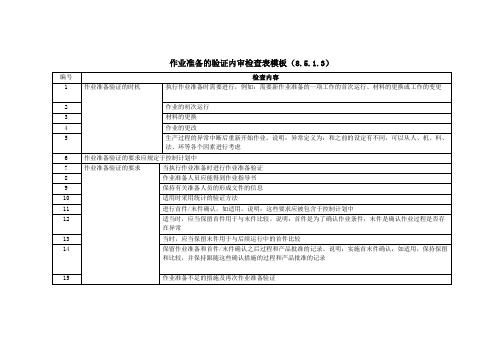
当时,应当保留末之后过程和产品批准的记录。说明:实施首末件确认,如适用,保持保留和比较,并保持跟随这些确认措施的过程和产品批准的记录
15
作业准备不足的措施及再次作业准备验证
作业准备的验证内审检查表模板(8.5.1.3)
编号
检查内容
1
作业准备验证的时机
执行作业准备时需要进行,例如:需要新作业准备的一项工作的首次运行、材料的更换或工作的变更
2
作业的初次运行
3
材料的更换
4
作业的更改
5
生产过程的异常中断后重新开始作业。说明:异常定义为:和之前的设定有不同,可以从人、机、料、法、环等各个因素进行考虑
6
作业准备验证的要求应规定于控制计划中
7
作业准备验证的要求
当执行作业准备时进行作业准备验证
8
作业准备人员应能得到作业指导书
9
保持有关准备人员的形成文件的信息
10
适用时采用统计的验证方法
11
进行首件/末件确认,如适用。说明:这些要求应被包含于控制计划中
12
适当时,应当保留首件用于与末件比较。说明:首件是为了确认作业条件,末件是确认作业过程是否存在异常
IATF16949作业准备验证程序(停工后验证)

按照4.2的内容,各项作业准备的验证项目均无异常后,开始正常生产。
5.相关文件
现场有产品的作业文件:包括工艺流程卡,图纸或者控制计划
挤压首、巡检记录表
检验员
15
做到5S
符合工5S管理程序的要求
不记录
检验员
16
选定检测所需的检具,计量器具,样件
符合检验指导书,图纸,控制计划上的要求
不记录
检验员
17
准备好生产产品的检验文件,例如图纸,控制计划
现场有检验文件:包括图纸或者控制计划
挤压首、巡检记录表
③自然灾害(比如火灾等)后造成生产停工
④公共设施中断(比如停电停水等)后造成生产停工
⑤劳动力短缺后造成生产停工
⑥基础设施的破坏后造成生产停工
4.工作流程及内容
4.1作业准备的内容
审核
批准
日期
-181-
编制部门:质量部
文件名称
作业准备验证程序(停工后验证)
编号:
版次:
版本号:
编制人:
第2页共5页
日期:
-180-
编制部门:质量部
文件名称
作业准备验证程序(停工后验证)
编号:
版次:
版本号:
编制人:
第1页共5页
日期:
1.目的
作业开始前,包括在计划或非计划生产停工期后的作业开始,通过对该作业工位上的人、机、料、法、环、测的检验或测验,来验证作业准备的精确性和准确性。确保作业开始后,能持续生产出合格的产品,避免产生批量的不合格品,预防产生不良的质量成本,确保生产作业的有效性。
检验员
3
转岗人员具备上岗资质
核查人员的培训记录,资质证书
作业准备验证程序(含表格)

作业准备的验证程序
(IATF16949-2016)
1.目的
对公司生产前工序作业准备规定必要的验证手段,保证生产可以正常、有效进行。
2.范围
适用于本公司产品生产前的作业准备。
3.职责
3.1 品质部负责制定验证记录表的相关内容。
3.2 车间班组长负责填写《作业准备验证记录》。
4.程序及要求
4.1在作业的初步运行、材料的改变、作业更改、运行间过长的停顿、变换产品生产/加工等情况下,均须进行作业准备验证,并记录于“作业准备验证记录表”中。
如验证结果不符合生产所要求,则由相关生产车间进行处理。
4.2每个工作班,工装、设备调整后生产的首件产品,按《产品监视和测量控制程序》执行首件检验。
作业准备产生的不合格品,按《不合格品控制程序》执行。
4.3新产品、过程更改,进行试生产后进行PPAP及生产确认试验,按APQP、PPAP 要求执行。
4.4 每次进行作业准备验证,都必须由验证人员认真填写《作业准备验证记录》,由生产部保存。
5.相关文件
监测资源控制规范
产品和服务放行控制规范
不合格控制规范APQP、PPAP 6.相关记录
6.1《作业准备验证记录》
作业准备验证记录
表.xl s。
作业准备验证记录
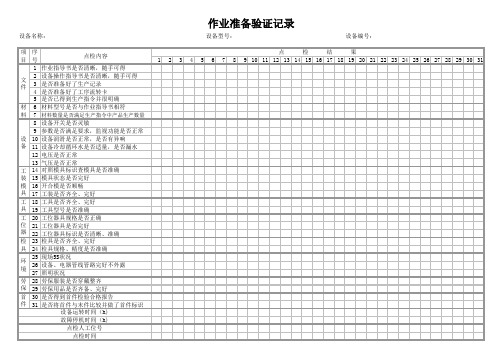
设 10 设备润滑是否正常,是否有异响
备 11 设备冷却循环水是否适量,是否漏水
12 电压是否正常
13 气压是否正常
工 14 对照模具标识查模具是否准确
装 15 模具状态是否完好
模 16 开合模是否顺畅 具 17 工装是否齐全、完好
工 18 工具是否齐全、完好
具 19 工具型号是否准确
工 20 工位器具规格是否正确
位 21 工位器具是否完好
器 22 工位器具标识是否清晰、准确 具检 23 检具是否齐全、完好
具 24 检具规格、精度是否准确
环 境
25 现场5S状况 26 设备、电器管线管路完好不外露
பைடு நூலகம்
27 照明状况
劳 28 劳保服装是否穿戴整齐
保 29 劳保用品是否齐备、完好
首 30 是否得到首件检验合格报告
件 31 是否将首件与末件比较并做了首件标识
设备运转时间(h)
故障停机时间(h)
点检人工位号
点检时间
作业准备验证记录
设备型号:
设备编号:
点
检
结
果
1 2 3 4 5 6 7 8 9 10 11 12 13 14 15 16 17 18 19 20 21 22 23 24 25 26 27 28 29 30 31
注:1、点检合格在空格内打“√”,不合格打“×”;2、点检不合格报告给班长,班长通知相关部门;3、所有点检项目合格时方可开始生产。
设备名称:
项序 目号
点检内容
1 作业指导书是否清晰,随手可得
文 件
2 设备操作指导书是否清晰,随手可得 3 是否准备好了生产记录
4 是否准备好了工序流转卡
5 是否已得到生产指令并很明确
作业准备验证记录

作业准备验证记录
为了保证作业的质量和准确性,对作业进行验证和准备是非常重要的一步。
下面是作业准备验证的记录,以确保作业的全面性和正确性。
1.作业目标:
-确保作业符合老师的要求和标准;
-确认作业的主题、关键点和结构是否清晰明了;
-确保作业的语法、拼写和标点符号正确。
2.作业内容验证:
-验证作业是否包含了所有必要的信息和细节;
-确认作业中的数据和事实是否准确和可信。
3.结构和逻辑验证:
-检查作业的结构是否合理,逻辑是否清晰;
-确认作业的各个部分是否相互衔接,是否符合作业要求;
-检查作业的段落之间是否有适当的过渡,确保内容的连贯性。
-检查引用的准确性和完整性,确保作业的学术可靠性。
5.语法和拼写验证:
-检查作业中的语法错误,例如主谓一致、时态一致等;
-检查作业中的拼写错误,确保作业的准确性;
-检查标点符号的使用,确保作业的流畅和易读。
6.格式验证:
-确认作业的格式是否符合要求,例如字体、字号、行距等;
-检查作业的标题、页眉、页脚等格式是否正确。
7.内容总结和提取验证:
-确认作业是否达到了预期的目标;
-提取作业的关键信息和要点,确保作业的准确性和可读性。
作业准备验证记录表

质量部: 日期:
参加验证人员签字
部 门
签 字
备 注
作业准备验证结果认定:
生产部: 日期:
xxxxx有限公司
作业准备验证记录表
工序名称
产品名称验证日期产品图号 Nhomakorabea验证类别
□初运行
□过程更改
验证要求
验证情况
作 业 准 备 验 证
文 件
是否配备了足够详细的作业指导书
设 备
设备功能,性能和精度是否符合要求
工 装
工装是否齐全,是否满足要求
人 员
人员能力是否满足岗位要求
工作环境
工作环境是否满足产品质量要求
作业准备验证
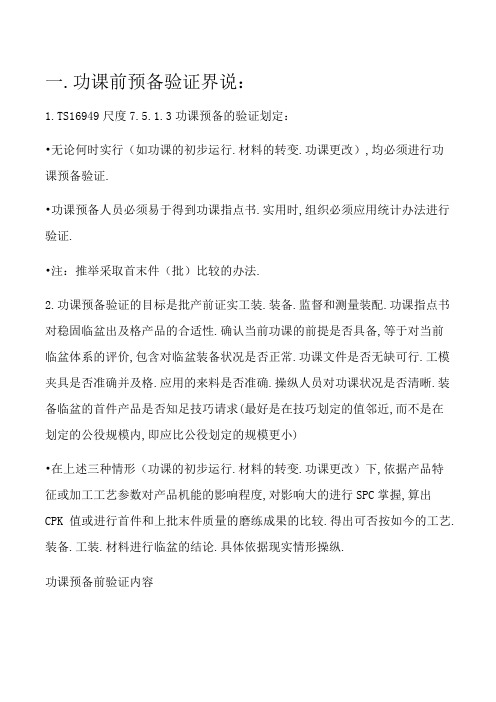
一.功课前预备验证界说:1.TS16949尺度7.5.1.3功课预备的验证划定:•无论何时实行(如功课的初步运行.材料的转变.功课更改),均必须进行功课预备验证.•功课预备人员必须易于得到功课指点书.实用时,组织必须应用统计办法进行验证.•注:推举采取首末件(批)比较的办法.2.功课预备验证的目标是批产前证实工装.装备.监督和测量装配.功课指点书对稳固临盆出及格产品的合适性.确认当前功课的前提是否具备,等于对当前临盆体系的评价,包含对临盆装备状况是否正常.功课文件是否无缺可行.工模夹具是否准确并及格.应用的来料是否准确.操纵人员对功课状况是否清晰.装备临盆的首件产品是否知足技巧请求(最好是在技巧划定的值邻近,而不是在划定的公役规模内,即应比公役划定的规模更小)•在上述三种情形(功课的初步运行.材料的转变.功课更改)下,依据产品特征或加工工艺参数对产品机能的影响程度,对影响大的进行SPC掌握,算出CPK值或进行首件和上批末件质量的磨练成果的比较.得出可否按如今的工艺.装备.工装.材料进行临盆的结论.具体依据现实情形操纵.功课预备前验证内容1)进程参数:正式临盆前须要对装备的参数进行设置,那么这里就有参数的设置尺度.所以要看现实的设置和尺度的请求是否一致?2)装备的状况:是否知足正常临盆的需求的检讨和点检.3)对象:检讨装备操纵和产品磨练等的对象.工位器具是否到位,是否无缺可用?4)原料.物料:是否按照请求预备到位?是否准确?5)首件检讨:成果是否OK?6)记载表格:SPC掌握用表格和其他记载等是否到位?7)劳保用品:操纵人员是否按照请求穿戴?8)等...功课前预备验证与首件磨练的差别•首件磨练只是功课验证的一部分.•一般的功课预备验证指的是指开机前的预备,它的验证工作包含:临盆前预备状况检讨和首件磨练.它是随后持续临盆的预备.•假如在每日临盆进程中有变动,材料的改换.功课的更改,还应对临盆中产生变动的内容进行的确认 .•须要做功课预备验证的机会,是指人机料法环相干的任何一项产生变更时都要做.•假如可以由首件产品的验证来解释产品的质量的话,那么,首检就是功课预备验证的输出.但有的进程质量是不克不及仅仅靠首件磨练来确认的,如特别进程.•当产生材料更改.装备更改.场地变动等变更时,这些变更是须要经顾客同意后,才干投入批量临盆.•当投入批量临盆前,对临盆功课预备状况也要进行检磨练证.是在顾客同意的PPAP前提未产生变更的情形下,对临盆功课预备情形的验证.谁来进行验证?1)假如是产生材料更改.装备更改.场地变动等变更时,这些变更是须要经顾客同意的,由技巧部分发放PPAP验证筹划,并由技巧部分来组织实行.2)假如已被同意可以批量临盆的,由公司的多功效小组来组织,把具体请求写入掌握筹划.功课指点书来进行掌握.3)一般由操纵者进行验证(包含首末件检讨),品管人员仅进行首末件复核确认.目标是进步操纵者的自检意识.4)当在临盆进程,人.机.料.法.环产生变更时,都应当做首件磨练,但不必定非得做其他项目标验证(看情形).4.什么时刻做首检?1)首件产品检讨,一般指天天早上开机半小时内就要做的工作,假如一世界来产品没有换批只需做一次,假如换产品又要从新做一次首检.2)当人机料法环产生变更,不必说更须要从新首检.3)一般企业内的症结.主要工序,首件检讨是由品管人员(巡检员)确认才算数.功课人检讨了,没有品管的确认也是不算数的.特别是有掌握图等统计办法请求的工序.5.功课预备的首磨练证可能包含以下请求:1)磨练;2)进行首/末件比较;3)应用统计办法(如计量型特别特征)来确认.二.功课前预备验证记载的主要性1.功课前预备验证记载表的感化:1)最主要的一条,就是作为是否具备前提进行临盆的证据应用.2)给班组长进行工作检讨用.3)当产生质量问题时进行追溯应用.4)进行统计剖析,进行科学决议计划时用.2.对记载的请求:真实反应现实的情形.3.当操纵者发明验证记载表格中的项目,现实情形跟验收请求不一致时,处理请求如下:1)假如可以由操纵者进行装备调剂的,由操纵者进行装备调剂.假如划定不克不及,向班组长反馈或者按第2条履行;2)假如是装备问题,假如班组长有授权的,由操纵者填写装备维修单报装备科.假如不是,由班组长填写装备维修单报装备科,或者由车间的维修人员来处理; 3)假如是工艺问题,由班组长陈述主督工艺工程师处理;4)假如是产品不及格问题,可以由操纵者请质检员来处理;5)不临盆,等待处理成果.4.当平常情形解决后的工作步调:1)在当时的时光,从新验证引起平常的参数或者装备是否正常,从新首检.并且填写功课前预备记载.2)请质检员进行首检确认.5.假如平常情形一向得不到处理时:1)报车间引导,由车间引导决议主动停机或者停线;2)通知质检员,由质检员开启停机/停线通知单.6.填写记载表格,不许可消失以下情形:1)没有看过装备中各内心的现实情形,随意填写一个相符的数字.2)没有查对装备运行中的现实情形,或者没有查对原材料的现实情形,乃至于没有发明平常状况,就随意打√.3)产品现实没有及格,没有检讨或者检讨发明不及格,但仍然填写及格.4)其他不相符事实,不具备开机前提记载的填写.7.处罚:1)以上所说的不相符情形,是不遵照工艺规律的表示.2)一般情形下,由车间负责进行处罚.3)对于反复发明的问题,假如造成必定影响的话,公司有《反复发明的不相符问题扣罚治理细则》,由质量治理部分报财务部分进行经济扣罚.义务人50-180元/次.4)假如产生了重大质量变乱,公司有《质量变乱义务穷究处罚条例》进行经济扣罚和行政处罚.义务人50-300元/次,或者降薪.同时,班组长和部分引导也要负连带义务,一路被扣罚.而行政处分分离有:书面警告.记小过.记大过.降职等.辞退.解雇.。
- 1、下载文档前请自行甄别文档内容的完整性,平台不提供额外的编辑、内容补充、找答案等附加服务。
- 2、"仅部分预览"的文档,不可在线预览部分如存在完整性等问题,可反馈申请退款(可完整预览的文档不适用该条件!)。
- 3、如文档侵犯您的权益,请联系客服反馈,我们会尽快为您处理(人工客服工作时间:9:00-18:30)。
作业准备验证程序
(IATF16949-2016/ISO9001-2015)
1.0目的
作业开始前,包括在计划或非计划生产停工期后的作业开始,通过对该作业工位上的人、机、料、法、环、测的检验或测验,来验证作业准备的精确性和准确性。
确保作业开始后,能持续生产出合格的产品,避免产生批量的不合格品,预防产生不良的质量成本,确保生产作业的有效性。
2.0适用范围
公司内部新作业准备的一项工作的首次运行的验证,量产作业准备的验证,每道工序的作业准备的验证,计划生产停工期后的作业准备的验证,以及非计划生产停工期后的作业准备的验证。
3.0术语
3.1 首件:每个班次刚开始时或过程发生改变(如人员的变动、换料及换工装、设备的调整、工装模具夹具的调换修理等)后加工的第一或前几件产品。
3.2 末件:当班生产线或生产设备在结束生产或停工停机时,加工的最后一件产品。
3.3造成计划生产停工的情况如下,但不限于下述情况:
①5S工作
②更换产品型号
③更换工装模具
④员工计划性培训或会议
3.4 造成非计划生产停工的情况如下,但不限于下述情况:
①关键设备故障后造成生产停工
②供应链中断后造成生产停工
③自然灾害(比如火灾等)后造成生产停工
④公共设施中断(比如停电停水等)后造成生产停工
⑤劳动力短缺后造成生产停工
⑥基础设施的破坏后造成生产停工
4.0工作流程及内容
4.1作业准备的内容
4.2作业准备的验证
4.3产品首件检查的管理内容
①首件检查的数量:n=1
②操作员依据工艺操作规程、样件对首件做自检,由班组长复检,最后由检验员依图纸、标准专检确认,确认合格后方能继续生产
③对首件进行标示,并将首件放置在生产指定的区域
④当人、机、料、法、环、测发生变化时(如:工装模具维修更换、材料批次更换、设备维修更换、交接班后),需做首件检查
⑤首件检查若不合格,须暂停生产线并反应给生产班组长、生产主管做适当的处理,操作员和班组长需按照工艺操作规程的要求进行调整,直到做出合格的产品
⑥当操作员和班组长遇到无法自身解决的问题时应上报车间主任,如需要修理工装、设备,应及时联络车间主任,由生产主管调整生产计划
⑦首末件比较,最近一次运行的最后一批不仅应该对照规定的要求,而且应该与新运行的第一批进行比较,以参考新的准备的质量水平
⑧首末件比较无明显差异后,一同转至下工序
⑨当新作业准备的一项工作的首次运行时,或者制造过程不稳定时,可以采用统计的验证方法
4.4作业准备验证后的生产
按照4.2的内容,各项作业准备的验证项目均无异常后,开始正常生产。
5.0相关文件
5.1工艺流程卡
5.2图纸
5.3控制计划
5.4检验指导书
6.0相关记录
6.1《挤压首、巡检记录表》
首、巡检记录表.xl
s。