双色注塑模具设计36条经典经验分享——【塑胶件设计资料】
双色模具设计及注塑时要注意的事项

双色模具设计及注塑时要注意的事项双色模具就是两种塑胶材料在同一台注塑机上注塑,分两次成型,通常由两套模具组成,后模要旋转180度,而前模不动,但是产品只出模一次的模具。
一般这种模塑工艺也叫双料注塑,且需要专门的双色注塑机。
双色模具设计及注塑时要注意的事项有:1、两型腔和型芯的运水布置尽量充分,并且均衡、一样。
2、模具的前模以中心旋转180º后,必须与后模吻合。
设计时必须注意这一点。
3、99%的情况是先注塑产品的硬胶部分,再注塑产品的软胶部分。
因为软胶易变形。
先成型成型温度高的塑胶原材料,再成型温度低的。
4、三板模的水口最好能设计成可以自动脱模动作。
特别要注意软胶水口的脱模动作是否可靠。
5、在设计时,请仔细查看双色模具注塑机的参数数据,如,最大容模厚度、最小容模厚度、顶棍孔距离等。
6、注塑时,第一次注塑成型的产品尺寸可以略大,以使它在第二次成型时能与另一个型腔压得更紧,以达到封胶的作用。
7、前模的两个形状是不同的,分别成型1种产品。
而后模的两个形状完全一样。
(注意:如有不一样,要做前模滑块来保证后模一致)8、注意在第二次注塑时,塑胶的流动是否会冲动第一次已经成型好的产品,使其胶位变形?如果有这个可能,一定要想办法改善。
9、为了使两种塑胶“粘”得更紧,要考虑材料之间的“粘性”以及模具表面的粗糙度。
双色模具注塑有专门的TPU;而模具表面越光滑,它们“粘‘得更紧。
10、在设计第二次注塑的型腔时,为了避免型腔插(或擦)伤第一次已经成型好的产品胶位,可以设计一部分避空。
但是必须慎重考虑每一处封胶位的强度,即:在双色模具注塑中,是否会有在大的注塑压力下,塑胶发生变形,导致第二次注塑可能会有批锋产生的可能。
双色模具设计及双色注塑成型的36条经验
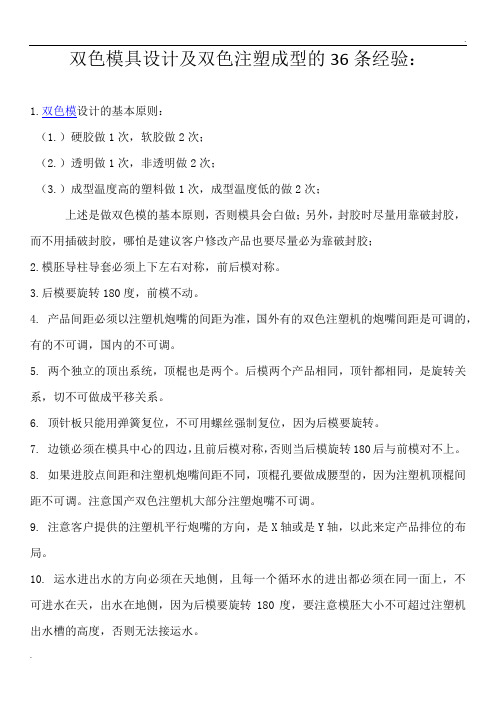
双色模具设计及双色注塑成型的36条经验:1.双色模设计的基本原则:(1.)硬胶做1次,软胶做2次;(2.)透明做1次,非透明做2次;(3.)成型温度高的塑料做1次,成型温度低的做2次;上述是做双色模的基本原则,否则模具会白做;另外,封胶时尽量用靠破封胶,而不用插破封胶,哪怕是建议客户修改产品也要尽量必为靠破封胶;2.模胚导柱导套必须上下左右对称,前后模对称。
3.后模要旋转180度,前模不动。
4. 产品间距必须以注塑机炮嘴的间距为准,国外有的双色注塑机的炮嘴间距是可调的,有的不可调,国内的不可调。
5. 两个独立的顶出系统,顶棍也是两个。
后模两个产品相同,顶针都相同,是旋转关系,切不可做成平移关系。
6. 顶针板只能用弹簧复位,不可用螺丝强制复位,因为后模要旋转。
7. 边锁必须在模具中心的四边,且前后模对称,否则当后模旋转180后与前模对不上。
8. 如果进胶点间距和注塑机炮嘴间距不同,顶棍孔要做成腰型的,因为注塑机顶棍间距不可调。
注意国产双色注塑机大部分注塑炮嘴不可调。
9. 注意客户提供的注塑机平行炮嘴的方向,是X轴或是Y轴,以此来定产品排位的布局。
10. 运水进出水的方向必须在天地侧,且每一个循环水的进出都必须在同一面上,不可进水在天,出水在地侧,因为后模要旋转180度,要注意模胚大小不可超过注塑机出水槽的高度,否则无法接运水。
11. 第一次注塑的产品要放在非操作侧,因为第一次注塑后产品要旋转180度进行第二次注塑,正好转到操作侧,方便取产品。
12. 出口模的码模位要在操作侧和非操作侧,不可在天地侧,因为他们的产品要全自动。
13. 分型面的注意事项:后模分型面要将两个产品合并后取得的分型面为后模的;前模分型面要取单个产品的即可,不可取合并后的产品分型面。
14. 前后法兰的公差为负0.05mm,两法兰间距公差为正负0.02mm,顶棍与顶棍孔的间隙单边为 0.1mm,前后模导套导柱的中心距公差为正负0.01,模框四边和深度都要加公差,否则当后模旋转180度后,因高低不一致而产生批锋。
塑胶模具「双色模设计」共用一个模架2个炮筒产生90度样式!
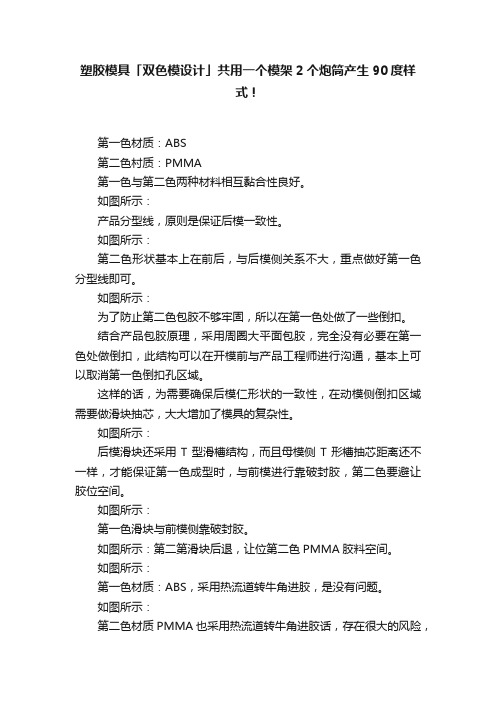
塑胶模具「双色模设计」共用一个模架2个炮筒产生90度样式!第一色材质:ABS第二色村质:PMMA第一色与第二色两种材料相互黏合性良好。
如图所示:产品分型线,原则是保证后模一致性。
如图所示:第二色形状基本上在前后,与后模侧关系不大,重点做好第一色分型线即可。
如图所示:为了防止第二色包胶不够牢固,所以在第一色处做了一些倒扣。
结合产品包胶原理,采用周圈大平面包胶,完全没有必要在第一色处做倒扣,此结构可以在开模前与产品工程师进行沟通,基本上可以取消第一色倒扣孔区域。
这样的话,为需要确保后模仁形状的一致性,在动模侧倒扣区域需要做滑块抽芯,大大增加了模具的复杂性。
如图所示:后模滑块还采用T型滑槽结构,而且母模侧T形槽抽芯距离还不一样,才能保证第一色成型时,与前模进行靠破封胶,第二色要避让胶位空间。
如图所示:第一色滑块与前模侧靠破封胶。
如图所示:第二第滑块后退,让位第二色PMMA胶料空间。
如图所示:第一色材质:ABS,采用热流道转牛角进胶,是没有问题。
如图所示:第二色材质PMMA也采用热流道转牛角进胶话,存在很大的风险,而且进胶点附近也容易产生流痕和气纹都是无法解决的。
PMMA最大的缺点:1,较脆,容易断裂.如图所示:产品顶出样式。
如图所示:2色共用模架,但进胶点采用90度样式,第一色采用模具中心点直接进胶,但第二色在非工作操作侧90度炮筒进胶。
如图所示,还在采用后模旋转样式。
如图所示:双色模定模侧平面图。
如图所示:动模侧平面图样式。
如图所示:当第一色旋转180度时,进行第二色成型时,第一色产品进胶点需要设计避空。
如图所示:为了让第一色产品周圈能更好地封胶,在第二色成型时,封胶区域做预留0.05~0.1mm的预压量,第一色产品不封胶区域可以做避空0.2~0.5mm,重点方便模具加工。
如图所示,第二色内滑块样式。
干货分享-双色模具设计经验总结
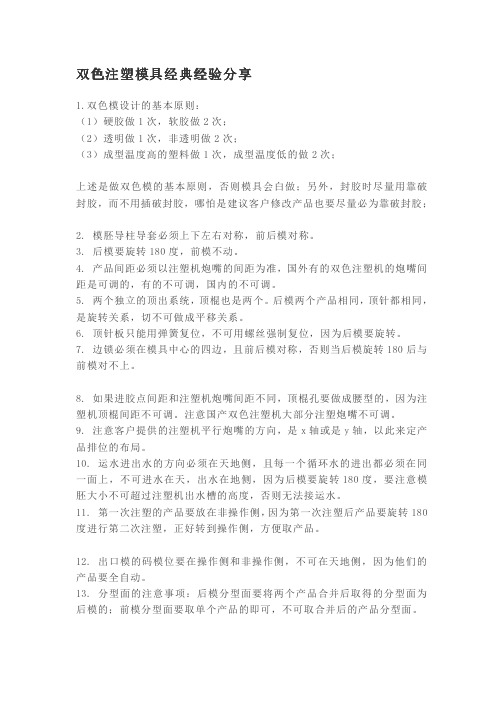
双色注塑模具经典经验分享1.双色模设计的基本原则:(1)硬胶做1次,软胶做2次;(2)透明做1次,非透明做2次;(3)成型温度高的塑料做1次,成型温度低的做2次;上述是做双色模的基本原则,否则模具会白做;另外,封胶时尽量用靠破封胶,而不用插破封胶,哪怕是建议客户修改产品也要尽量必为靠破封胶;2.模胚导柱导套必须上下左右对称,前后模对称。
3.后模要旋转180度,前模不动。
4.产品间距必须以注塑机炮嘴的间距为准,国外有的双色注塑机的炮嘴间距是可调的,有的不可调,国内的不可调。
5.两个独立的顶出系统,顶棍也是两个。
后模两个产品相同,顶针都相同,是旋转关系,切不可做成平移关系。
6.顶针板只能用弹簧复位,不可用螺丝强制复位,因为后模要旋转。
7.边锁必须在模具中心的四边,且前后模对称,否则当后模旋转180后与前模对不上。
8.如果进胶点间距和注塑机炮嘴间距不同,顶棍孔要做成腰型的,因为注塑机顶棍间距不可调。
注意国产双色注塑机大部分注塑炮嘴不可调。
9.注意客户提供的注塑机平行炮嘴的方向,是x轴或是y轴,以此来定产品排位的布局。
10.运水进出水的方向必须在天地侧,且每一个循环水的进出都必须在同一面上,不可进水在天,出水在地侧,因为后模要旋转180度,要注意模胚大小不可超过注塑机出水槽的高度,否则无法接运水。
11.第一次注塑的产品要放在非操作侧,因为第一次注塑后产品要旋转180度进行第二次注塑,正好转到操作侧,方便取产品。
12.出口模的码模位要在操作侧和非操作侧,不可在天地侧,因为他们的产品要全自动。
13.分型面的注意事项:后模分型面要将两个产品合并后取得的分型面为后模的;前模分型面要取单个产品的即可,不可取合并后的产品分型面。
14.前后法兰的公差为负0.05mm,两法兰间距公差为正负0.02mm,顶棍与顶棍孔的间隙单边为0.1mm,前后模导套导柱的中心距公差为正负0.01,模框四边和深度都要加公差,否则当后模旋转180度后,因高低不一致而产生批锋。
模具设计结构设计必备知识:双色注塑模具介绍
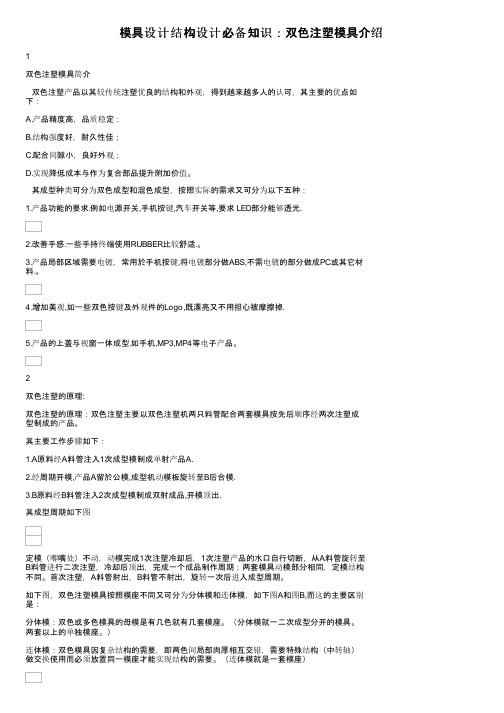
模具设计结构设计必备知识:双色注塑模具介绍1双色注塑模具简介双色注塑产品以其较传统注塑优良的结构和外观,得到越来越多人的认可,其主要的优点如下:A.产品精度高,品质稳定;B.结构强度好,耐久性佳;C.配合间隙小,良好外观;D.实现降低成本与作为复合部品提升附加价值。
其成型种类可分为双色成型和混色成型,按照实际的需求又可分为以下五种:1.产品功能的要求.例如电源开关,手机按键,汽车开关等,要求 LED部分能够透光.2.改善手感.一些手持终端使用RUBBER比较舒适.。
3.产品局部区域需要电镀,常用於手机按键,将电镀部分做ABS,不需电镀的部分做成PC或其它材料.。
4.增加美观,如一些双色按键及外观件的Logo,既漂亮又不用担心被摩擦掉.5.产品的上盖与视窗一体成型.如手机,MP3,MP4等电子产品。
2双色注塑的原理:双色注塑的原理:双色注塑主要以双色注塑机两只料管配合两套模具按先后顺序经两次注塑成型制成的产品。
其主要工作步骤如下:1.A原料经A料管注入1次成型模制成单射产品A.2.经周期开模,产品A留於公模,成型机动模板旋转至B后合模.3.B原料经B料管注入2次成型模制成双射成品,开模顶出.其成型周期如下图定模(唧嘴处)不动,动模完成1次注塑冷却后,1次注塑产品的水口自行切断,从A料管旋转至B料管进行二次注塑,冷却后顶出,完成一个成品制作周期;两套模具动模部分相同,定模结构不同。
首次注塑,A料管射出,B料管不射出,旋转一次后进入成型周期。
如下图,双色注塑模具按照模座不同又可分为分体模和连体模,如下图A和图B,而这的主要区别是:分体模:双色或多色模具的母模是有几色就有几套模座。
(分体模就一二次成型分开的模具。
两套以上的单独模座。
)连体模:双色模具因复杂结构的需要,即两色间局部肉厚相互交错,需要特殊结构(中转轴)做交换使用而必须放置同一模座才能实现结构的需要。
(连体模就是一套模座)3双色模材料的选择:材料的选择:原则上要求二次料的熔融温度要低於一次料的熔融温度,防止二次射出时产生熔胶一次料可选:PC.ABS.PC ABS.PMMA,二次料可选:PC.ABS.PC ABS.PMMA.TPU收缩率的选择:一般来说,双色模具的缩水率取决於一次材料,二次材料和一次材料选用相同的缩水率.一次材料为ABS(通常缩水率为0.5%),二次材料为TPR(通常缩水率为1.7%),双色模具中,二次料不会收缩太多,通常选用0.5%的缩水率。
双色注塑模具设计及双色注塑成型注意事项与经验 共三十六条

双色注塑模具设计及双色注塑成型注意事项与经验共三十六条1.双色注塑模具设计的基本原则:(1.)硬胶做1次,软胶做2次;(2.)透明做1次,非透明做2次;(3.)注塑成型温度高的塑料做1次,成型温度低的做2次;上述是做双色注塑模具的基本原则,否则注塑模具会白做;另外,封胶时尽量用靠破封胶,而不用插破封胶,哪怕是建议客户修改产品也要尽量必为靠破封胶;2.模胚导柱导套必须上下左右对称,前后模对称。
3.后模要旋转180度,前模不动。
4. 产品间距必须以注塑机炮嘴的间距为准,国外有的双色注塑机的炮嘴间距是可调的,有的不可调,国内的不可调。
5. 两个独立的顶出系统,顶棍也是两个。
后模两个产品相同,顶针都相同,是旋转关系,切不可做成平移关系。
6. 顶针板只能用弹簧复位,不可用螺丝强制复位,因为后模要旋转。
7. 边锁必须在模具中心的四边,且前后模对称,否则当后模旋转180后与前模对不上。
8. 如果进胶点间距和注塑机炮嘴间距不同,顶棍孔要做成腰型的,因为注塑机顶棍间距不可调。
注意国产双色注塑机大部分注塑炮嘴不可调。
9. 注意客户提供的注塑机平行炮嘴的方向,是X轴或是Y轴,以此来定产品排位的布局。
10. 运水进出水的方向必须在天地侧,且每一个循环水的进出都必须在同一面上,不可进水在天,出水在地侧,因为后模要旋转180度,要注意模胚大小不可超过注塑机出水槽的高度,否则无法接运水。
11. 第一次注塑的产品要放在非操作侧,因为第一次注塑后产品要旋转180度进行第二次注塑,正好转到操作侧,方便取产品。
12. 出口模的码模位要在操作侧和非操作侧,不可在天地侧,因为他们的产品要全自动。
13. 分型面的注意事项:后模分型面要将两个产品合并后取得的分型面为后模的;前模分型面要取单个产品的即可,不可取合并后的产品分型面。
14. 前后法兰的公差为负0.05mm,两法兰间距公差为正负0.02mm,顶棍与顶棍孔的间隙单边为0.1mm,前后模导套导柱的中心距公差为正负0.01,模框四边和深度都要加公差,否则当后模旋转180度后,因高低不一致而产生批锋。
双色模具的设计及注塑成型
双色模具的设计及注塑成型
双色模具是指两种塑胶材料在同一台注塑机上注塑,分两次成型,但是产品只出模一次的模具。
一般这种模塑工艺也叫双料注塑,通常由一套模具完成,且需要专门的双色注塑机。
双色模具目前市场上日益盛行,这种工艺可以使产品的外观更加漂亮,易于换颜色而可以不用喷涂,但对设计及注塑成型的要求高。
1.双色模设计的基本原则:
(1)硬胶做1 次,软胶做2 次;
(2)透明做1 次,非透明做2 次;
(3)成型温度高的塑料做1 次,成型温度低的做2 次;
上述是做双色模的基本原则,否则模具会白做;另外,封胶时尽
量用靠破封胶,而不用插破封胶,哪怕是建议客户修改产品也要尽量必为靠破封胶。
2.模胚导柱导套必须上下左右对称,前后模对称。
3.后模要旋转180 度,前模不动。
4.产品间距必须以注塑机炮嘴的间距为准,国外有的双色注塑机的炮嘴间距是可调的,有的不可调,国内的不可调。
5.两个独立的顶出系统,顶棍也是两个。
后模两个产品相同,顶针都相同,是旋转关系,切不可做成平移关系。
6.顶针板只能用弹簧复位,不可用螺丝强制复位,因为后模要旋转。
7.边锁必须在模具中心的四边,且前后模对称,否则当后模旋转180 后与前模对不上。
8.如果进胶点间距和注塑机炮嘴间距不同,顶棍孔要做成腰型的,因为注塑机顶棍间距不可调。
注意国产双色注塑机大部分注塑炮嘴。
注塑成型之双色成型技术
二:双色成型经验分享
经验分享---钳工 一、钳工在组立双色模最大的不同点,就是合模的顺序,步骤如下: 1)第一射公模与第一射的母模合配,修母模。以防公模与第二射母模合模时有成型 面。 2)第一射公模与第二射的母模合配,修公模。 3)第二射公模与第二射的母模合配,修公模。 4)第二射公模与第一射的母模合配,看情况修模。 二、钳工在打模号时,二射基准要统一标准,方便后续试模人员装机
混色射枪(单一模) 5
一.双色成型的基本概念
平行射枪双色成型机
6
一.双色成型的基本概念
双色双模共注射成型成型原理 1次成型模 2次成型模
1次成型品 2次成品
A料管 B料管
7
一.双色成型的基本概念
双色双模共注射成型成型原理
双色双模共注射成型成型是 在注射机上同时安装并使用两副 注射模,两副模具共享一个合模 系统,如右图所示。模具固定在 回转板6上,当其中一个注射系 统4向型腔内注射一定的A种塑料 以后(未注满型腔),回转板6 回转,将已注入A种塑料的型腔 转到注射系统2处,并马上由注 射系统2向由型腔和第一注射成 型的空腔内注射B种塑料,直到 塑料充满型腔,经过保压和冷却 定型后,形成分色明显的双清色 塑件,由推出系统推出塑件。
26
三.双色成型实例
试模验证:
•1.把热浇道浇口处温度调高30度,调试发现流痕有明显变化,
•但由于温度过高软胶易粘模.
•2.解剖热浇道,检查浇口封浇处,发现存有余胶.
•试模验证热浇道阀针模具,其封胶的作用并不能达到
•无残料效果
结论: 冷料造成流痕,对症下药,问题解决!
在浇口 反面加 冷料井
27
THANKS
24
三.双色成型实例
双色模具设计最详解资料,不看超后悔?
双色模具设计最详解资料,不看超后悔?今天给大家带来的是双色模具基础技术讲解基本概况:双色模具是由两组或以上组合形成的能生产两种塑胶素材的特种模具。
双色成型机台分卧式与立式两种,装载两套或以上模具由机台旋转180度或120度两次注塑成型。
双色注塑机与传统单色注塑机类似,区别于它有两个成型射嘴及成型动作机构不同.一、塑材特性双色双料通指2种塑材2种颜色,塑材通常分为硬胶与硬胶包合~软胶与硬胶包合。
(硬胶常用ABS PC PP PVC..软胶常用TPU TPE TPR);成型后的产品有外观质感防碰防摔等诸多功能。
二、包胶方式决定了双色模具的基本结构半包或insert采用2组或以上模胚旋转,2次注塑成型;全包采用一组整体模胚由活动中板旋转,2次注塑成型三、产品结构包胶方式决定了双色模具的基本结构;半包或insert采用2组或以上模胚旋转,2次注塑成型;全包采用一组整体模胚由活动中板旋转,2次注塑成型。
模胚与组立图四、模具结构双色模胚钢材采用S60C高碳钢制作;模胚需求极高的精度标准;内部机构务必四面分中加工,同规格板材可任意翻边`旋转`互换均能达到组合整精度要求,定位环通常采用直径Φ120或Φ150;模胚务必采用‘富得巴’标准。
注意:两组模胚厚度务必一至;模胚上下固定板外侧均需做C角旋转避让;固定模具务必用贯穿螺丝紧固以确保安全,并须在脱料板母模:模脚上作出相应避让以方便拆装螺丝五、加工流程做好开模前的结构检讨,了解模具的加工工艺。
母模二次需保留相应的预压(取0.05~0.10mm)。
常规双色公模仁相同,可同步加工。
模胚务必做好精度检测,未达公差要求之模胚决不可使用。
六、双色模合模程序一次母模与两组公模同时合模(母模涂红丹,修整公模),合至两组公模到丹一致且完全吻合。
→取任意一组公模与二次母模相合,致到丹完全(公模涂丹,修二次母模)。
做好试模前动作检测,不可漏装,错装上机(错装模具将会导致2组以上模仁报废)。
双色注塑模工艺分析及模具设计
双色注塑模工艺分析及模具设计
1.工艺分析
a.产品结构和尺寸:双色注塑产品的结构和尺寸对注塑工艺有很大的
影响。
需要分析产品的复杂程度、壁厚分布、缩水率等因素,确定是否适
合双色注塑工艺。
b.材料特性:双色注塑产品通常由两种不同的材料组成,需要对两种
材料的熔融温度、熔融指数、流动性等进行分析,确保两种材料能够良好
地结合在一起。
c.注塑工艺参数:包括注射压力、注射速度、模具温度、冷却时间等。
需要通过试验和仿真模拟,确定合适的注塑工艺参数,避免产品缺陷如翘曲、留痕等。
2.模具设计
a.模具结构设计:双色注塑模具通常由注塑模芯、注塑模腔、移位机构、分色机构等部分组成。
需要根据产品的结构和成型要求设计合理的模
具结构,确保双色注塑成型的准确性和可靠性。
b.分色机构设计:双色注塑需要通过分色机构实现两种不同颜色材料
的注入和分离。
需要考虑分色机构的类型(旋转式、滑动式等)、分色位
置和过渡区域的设计,确保双色注塑产品的色彩和图案能够完美呈现。
c.冷却系统设计:双色注塑需要通过冷却系统来散热降温,快速固化
成型。
需要设计合理的冷却水路,保证模具表面温度均匀分布,避免产品
变形和缺陷。
d.模具材料选择:双色注塑模具通常由优质的工具钢制成,需要根据
产品的批量和质量要求,选择合适的模具材料,以确保模具寿命和成型效果。
以上就是双色注塑模工艺分析及模具设计的简要介绍。
在实际生产中,还需要通过试制和改进不断优化工艺和模具设计,提高双色注塑产品的质
量和产能。
- 1、下载文档前请自行甄别文档内容的完整性,平台不提供额外的编辑、内容补充、找答案等附加服务。
- 2、"仅部分预览"的文档,不可在线预览部分如存在完整性等问题,可反馈申请退款(可完整预览的文档不适用该条件!)。
- 3、如文档侵犯您的权益,请联系客服反馈,我们会尽快为您处理(人工客服工作时间:9:00-18:30)。
双色注塑模具设计36条经典经验分享!
1.双色模设计的基本原则:
(1)硬胶做1次,软胶做2次;
(2)透明做1次,非透明做2次;
(3)成型温度高的塑料做1次,成型温度低的做2次;
上述是做双色模的基本原则,否则模具会白做;另外,封胶时尽量用靠破封胶,而不用插破封胶,哪怕是建议客户修改产品也要尽量必为靠破封胶;
2. 模胚导柱导套必须上下左右对称,前后模对称。
3. 后模要旋转180度,前模不动。
4. 产品间距必须以注塑机炮嘴的间距为准,国外有的双色注塑机的炮嘴间距是可调的,有的不可调,国内的不可调。
5. 两个独立的顶出系统,顶棍也是两个。
后模两个产品相同,顶针都相同,是旋转关系,切不可做成平移关系。
6. 顶针板只能用弹簧复位,不可用螺丝强制复位,因为后模要旋转。
7. 边锁必须在模具中心的四边,且前后模对称,否则当后模旋转180后与前模对不上。
8. 如果进胶点间距和注塑机炮嘴间距不同,顶棍孔要做成腰型的,因为注塑机顶棍间距不可调。
注意国产双色注塑机大部分注塑炮嘴不可调。
1
9. 注意客户提供的注塑机平行炮嘴的方向,是x轴或是y轴,以此来定产品排位的布局。
10. 运水进出水的方向必须在天地侧,且每一个循环水的进出都必须在同一面上,不可进水在天,出水在地侧,因为后模要旋转180度,要注意模胚大小不可超过注塑机出水槽的高度,否则无法接运水。
11. 第一次注塑的产品要放在非操作侧,因为第一次注塑后产品要旋转180度进行第二次注塑,正好转到操作侧,方便取产品。
12. 出口模的码模位要在操作侧和非操作侧,不可在天地侧,因为他们的产品要全自动。
13. 分型面的注意事项:后模分型面要将两个产品合并后取得的分型面为后模的;前模分型面要取单个产品的即可,不可取合并后的产品分型面。
14. 前后法兰的公差为负0.05mm,两法兰间距公差为正负0.02mm,顶棍与顶棍孔的间隙单边为0.1mm,前后模导套导柱的中心距公差为正负0.01,模框四边和深度都要加公差,否则当后模旋转180度后,因高低不一致而产生批锋。
框深公差为负0.02mm。
15. 如果在模胚厂已经将模胚加工完,本厂要加工唧嘴和顶棍孔时,要以4个导柱导套孔的间距中心为基准取数,否则偏差太多,容易卡死模。
订模胚时要注明是双色模胚,四个导柱导套和框对称,后模旋转180度后能与前模匹配。
1
16. 如果是后模旋转的双色话就简单多了,两个前模芯一样,一边注塑好硬胶后.旋转180度(注意产品转的时候不能掉落,浇口可以自动分离) , 转到另外一边后再注塑软胶,注塑硬胶无需布置顶针,只需布置在软胶这边模芯即可,另外缩水要注意,如果软胶完全把硬胶缠住,则只需放硬胶的缩水,如果是轮廓相接则硬胶软胶都要放缩水。
17. 如果是一套模具的双色模具的话,那就是一个直炮筒,一个90度的炮筒射胶,不需要旋转,只需一个模芯,软胶与硬胶的分离方法靠行位封胶。
18. cavity的两个外形是不同的,分别成型1种产品。
而core的两个外形完好一样。
19. 模具的前、后模以中心旋转180°后,必需吻合。
设计时必需做这个检查动作。
20. 留意顶针孔的位置,最小间隔210mm。
大的模具须恰当增加顶棍孔的数量。
并且,由于注塑机本身附带的顶针不够长,所以我们的模具中必需设计加长顶针,顶针长出模胚底板150mm左右。
21. 后模底板上必需设计2个定位圈。
22. 前模面板加a板的总厚度不能少于170mm。
请认真查看这种型号的注塑机的其它参考数据,比方,最大容模厚度、最小容模厚度、顶棍孔间隔等。
1。