全液压制动阀介绍
液压控制阀扥结构原理

第四节 流量控制阀
流量控制阀是用来控制输入执行元件的油液流量的大 小,从而控制执行元件运动的速度。流量控制阀是依靠改变 阀口通流面积的大小或通流通道的长短来控制流量的。 一、流量控制原理及节流口形式 二、普通节流阀 1.结构和工作原理 2.刚性 节流阀的刚性表示它抵抗负载变化的干扰,保持流量稳 定的能力,也就是当节流阀开口不变时,由于阀前阀后压力 差的变化而引起通过节流阀的流量发生变化的情况。流量变 化越小,说明节流阀的刚制阀是控制或调节液压系统中液流的压力、 流量和方向的。液压控制阀性能的优、劣,工作是否可 靠,对整个液压系统能否正常工作将产生直接影响。
液压控制阀可分为方向控制阀、压力控制阀和流 量控制阀三大类:
(1)方向控制阀
控制液流方向,如单向阀、换向
阀等。
(2)压力控制阀 控制液压系统或部分液压回路压
直动式和先导式两种溢流阀的流量压力特性的比较: (二)溢流阀的结构特点 1.阀口是常闭的; 2.控制阀口开闭的油液来自进油口; 3.泄油回油箱采用内泄方式。 以上三个结构特点很形象地反映在溢流阀的图形符号上。 (三)溢流阀的作用和性能要求 1.溢流阀的作用 (1)作溢流阀用
(2)作安全阀用 (3)作卸荷阀用 (4)作背压阀用 2.液压系统对溢流阀的性能要求 (1)定压精度高,当流过溢流阀的流量发生变化时,系 统中的压力变化要小。 (2)灵敏度要高,当液压缸突然停止运动时,溢流阀要迅 速开大。 (3)工作要平稳,且无震动和噪声。 (4)当阀关闭时,密封要好,泄漏要小。 二、减压阀 减压阀在液压系统中起减压作用,使液压系统中某一部 分得到一个降低了的稳定压力。 (一) 减压阀的结构和工作原理 (二)减压阀的结构特点 1. 阀口是常开的;
不同开口时的流量特性曲线如图示,由此可得出如 下结论: (1)同一节流阀,阀前后压力差相同,节流开口小 时,刚性大。 (2)同一节流阀,在节流开口一定时,阀前后压力 差越大,节流阀刚性越大。因此,为了保证节流阀 具有一定的刚性,必须保证阀前后具有一定的压差。 (3)取小的指数可以提高节流阀的刚度,因此在实 际使用中都希望采用薄壁小孔式的节流口。 三、调速阀 四、溢流节流阀
常用制动元件(制动阀、继动阀、调压阀、四回路保护阀等)工作原理简介

常用气制动元件工作原理简介装设在车辆上的所有各种制动系总称为制动装备。
任何制动系都具有四个基本组成部分:供能装置——包括供给、调节制动所需能量以及改善传能介质状态的各种部件。
其中产生制动能量的部分称为制动能源。
如空压机、人的肌体控制装置——包括产生制动动作和控制制动效果的各种部件。
如制动踏板机构,制动阀。
传动装置——包括将制动能量传输到制动器的各个部件,如制动总泵、制动轮缸制动器——产生阻碍车辆的运动或运动趋势的力(制动力)的部件,其中也包括辅助制动系中的缓速装置。
较为完善的制动系还具有制动力调节装置以及报警装置、压力保护装置等附加装置。
制动系还可按照制动能源来分类:以驾驶员的肌体作为唯一制动能源的制动系称为人力制动系;完全靠由发动机的动力转化而成的气压或液压形式的势能进行制动的则是动力制动系。
其制动能源可以是发动机驱动的空气压缩机或油泵。
兼用人力和发动机动力进行制动的制动系称为伺服制动系,如真空助力。
按照制动能量的传输方式,制动系又可分为机械式、液压式、气压式和电磁式等,我厂现有车型主要采用液压制动和气压制动两种传输方式。
液压制动式结构简单,主要用于490发动机以下小型工程车和平板车上,气压制动结构复杂,用于中型及以上车型。
下面只讨论一下我厂最常用的动力制动系中的气压制动。
气压制动系是发展最早的一种动力制动系,也是我厂现在最主要采用的制动形式。
图为气压双回路气压制动系示意图:由发动机驱动的双缸活塞式空气压缩机将压缩空气经调压阀首先输入湿储气筒,压缩空气在湿储气筒内冷却并进行油水分离之后,再经过四回路保护阀,分别进入前桥储气筒、后桥储气筒和驻车储气筒,将气路分成三个回路;前、后储气筒分别与制动阀的上、下两腔相连,当驾驶员踩下踏板时,前筒气体通过制动阀上腔经快放阀到达前桥制动气室,实现前桥制动;后储气筒气体通过制动阀下腔,打开继动阀控制口,使后储气筒压缩空气直接经继动阀进入后桥制动气室,实现后桥制动;驻车储气筒与手控阀相连,在正常行车状态,驻车储气筒与手控阀和弹簧气室处于常通状态,当车辆停止时,将手刹手柄达到停车位置,阻断气源,弹簧气室内的压缩空气通过快放阀排入大气,实现驻车制动。
液压分配阀在全地形车制动系统中的应用

3 摩托车技术 2 2 1 4 0 20
计算
-1 。 . 6)
当 尸 单独输入压力时 ,排 气管道小活塞左右两侧的 3
活 塞移 动 到排 气 口小 孔时 , 和 之 间 管路 断开 , 开
始建压。图 1 P 处活塞直径为 1 m,面积为 S 中 。 9 m m ,P
处 活塞直 径为 一环状 受 力面 ,面积 为 i 。
P4
求 ,往往采用两套完整的制动系统 ( 管路系统) ,管路分
2 采用液 压分配阀的某款全地形车制动系统
采用液压分配阀的某款全地形车制动系统如图 2 所 示 ,将 分 配泵 直接 连接 在 制 动管 路 上 ,其 中 P 和 分 别
●
P1
t
P3
图1 分配阀结构图
此时,由P 到 P 的压力为 : 4 4 P =
. )皿
P 一0 0 . . 4( 4
单 位 为 MP ,为 整体 活 塞 移 动 所需 克 服 的 阻 力 ; a 经测 量
压力时, 和 P 连通 , 2 此时 ,尸 通过泄油管路 P =P ; 4
Ill
液压分配 阀在全地形车制动系统 中的应用
曹 晖 陈 冰 何 谆 ( 江苏林 海动力机械集 团公 司)
摘要 : 在全地 形车制动 系统 中采用 了液压 分配阀设计 ,通过试验及相 关验算 ,该设计 简化 了制 动管
路 ,可方便调整前后 轮制动 力分配系数,满足 全地 形车的制动要求 ,为 全地形车制 功 系统 的设计提 供 了
液压鼓式制动器的工作原理

液压鼓式制动器的工作原理
液压鼓式制动器:
1)原理:
液压鼓式制动器是采用液压原理进行制动的一种设备。
它主要由液压阀、外壳和液压马达等组成,通过手控动阀的控制和变速器的改变控
制液压马达的转速,使液压流量系统形成扭矩叠加的作用,从而达到
制动的作用。
液压鼓式制动器的优点是无需模具和铸件,省工节约材料。
它能够安装在简单的体系中,其能耗小,实现全无线操控,使制
动器运行更稳定,容量大,运行噪音小,也可根据客户的要求来定制
各种工艺技术参数。
2)工作原理:
液压鼓式制动器的工作原理是,液压流入液压马达的齿轮内,由于液
压的冲力,使液压马达的齿轮成锥形运动,使两齿轮之间形成摩擦力,从而转动液压马达。
由于液压力的作用,能够形成液压马达和外壳之
间的扭矩,这是液压鼓式制动器发挥作用的基础。
当控制压力恒定时,制动器的转动速度可以恒定;而当调整液压压力时,可以调节制动器
的转动速度,达到调节制动效果。
3)优点:
(1)液压鼓式制动器的优点是无需模具和铸件,省工节约材料;(2)它能够安装在简单的体系中;
(3)其能耗小,实现全无线操控,使制动器运行更稳定;
(4)容量大,运行噪音小,也可根据客户的要求来定制各种工艺技术参数。
液压制动系统讲义讲解

路分别控制车轮制动器。它主要用于对后轮制动依赖性较大的发动机 后置后轮驱动的汽车。
当一套管路失效时,另一套管路仍能保持一定的制动效能,制动 效能低于正常时的50%。
Page 6
6
制动时,踩下制动踏板,推杆推动双腔制动主缸的主 缸前、后活塞前移、使主缸前、后腔油压升高,制动液分别 同时流至前,后车轮制动轮缸。轮缸的活塞在制动液压力的 作用下,向外移动,进而推动制动蹄张开压向制动鼓产生制 动效能。
若前腔控制的回路发生泄漏时,前活塞不产生液压力,但在 后活塞液力作用下,前活塞被推到最前端,后腔产生的液压力仍 使后轮产生制动。
若后腔控制的回路发生泄漏时,后腔不产生液压力,但后活 塞在推杆作用下前移,并与前活塞接触而使活塞前移,前腔仍能 产生液压力控制前轮产生制动。
Page 21
21
若两脚制动时,踏板迅速回位,活塞在弹簧的作用下迅速回 退,此时制动液受到止回阀的阻止不能及时回到腔内,活塞前方 出现负压,油壶的油在大气压的作用下从补偿孔进到活塞前方, 使活塞前方的油量增多。再踩制动时,制动有效行程增加。
矿物制动液:溶水性差,使普通橡胶膨胀。
Page 13
13
4.双腔式制动主缸
(1)作用 制动主缸作用是将制动踏板机械能转换成液压能。双管
路液压制动传动装置中的制动主缸一般采用串联双腔或并 联双腔制动主缸。 (2)结构
主缸的壳体内装有前活塞、后活塞及前后活塞弹簧,前 后活塞分别用皮碗、皮圈密封,前活塞用挡片保证其正确 位置。两个储液筒分别与主缸的前、后腔相通,前出油口、 后出油口分别与前后制动轮缸相通,前活塞靠后活塞的液 力推动,后活塞直接由推杆推动。
制动时,推动推杆而后 推动活塞和皮碗,掩盖补偿 孔后,主缸内的液压开始建 立,克服弹簧力后,推开油 阀后将制动液送到轮缸,解 除制动后,踏板机构、主活 塞、轮缸活塞在各自的回位 弹簧作用下回位。
第5章 液压控制阀
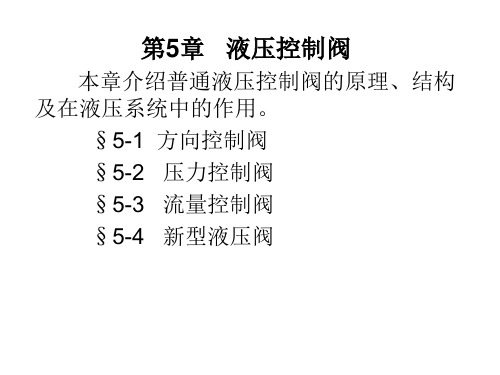
1、直动式溢流阀:(用于低压, p≤2.5MPa,反向不通) 如下页图所示,直动式溢流阀是利用系 统中的油液作用力,直接作用在阀芯上与弹 簧力相平衡的原理来控制阀芯的启闭动作, 以保证(油缸)进油口处的油液压力恒定。 进油口P处的压力油经阀芯的橫孔及阻尼 孔作用在阀芯底部的锥孔表面上。当进口 压力较小时,阀芯在弹簧的作用下处于下 端位置,P与T不能相通;当进口压力升高, 阀芯下端压力油产生的作换 向阀的优点,既可以很方便的控制换向,又 可以实现对较大流量回路的控制。 几点说明: ①液动阀两端控制油路上的节流阀可以调节 主阀的换向速度,从而使主油路的换向平 稳性得到控制; ②为保证液动阀回复中位,电磁阀的中位必 须是A、B、T油口互通。
③控制油可以取自主油路(内控),也可以 取独立油源(外控)。 • 思考:执能符号中六个油口分别接何处? 5、手动换向阀 通过控制手柄直接操纵阀芯的移动,换向 精度和平稳性不高,适用于间歇动作且无 需自动化的场合。
如图(a):向左推动手柄→左位工作; 向右推动手柄→右位工作。 弹簧复位。 如图(b):为钢球定位的手动换向阀, 与图(a)的区别:手柄可在三个位置上定 位,不推动手柄,阀芯不会自动复位。
§5-2 压力控制阀 压力控制阀是用来控制液压系统中油液 压力或利用压力信号实现控制(以液体压力 的变化来控制油路的通断)的阀类。按其功 能可分为溢流阀、减压阀、顺序阀、压力继 电器等。 本节主要介绍压力阀的工作原理、调节 性能、典型结构及主要用途。 一、溢流阀 溢流阀的作用是将系统的压力稳定在某 一调定值上,从而进行安全保护。按其调压 性能和结构特征划分,溢流阀可分为直动式 和先导式两大类。 (一)、溢流阀的工作原理及典型结构
二、换向阀 换向阀作用是利用阀芯和阀体间相对 位置的变化来接通、断开或改变系统中油液 的流动方向。
液压系统(完整)介绍
液压系统(完整)介绍一、液压系统的基本概念液压系统,是一种利用液体传递压力和能量的动力传输系统。
它主要由液压泵、液压缸(或液压马达)、控制阀、油箱、油管等部件组成。
液压系统广泛应用于各类机械设备中,如挖掘机、起重机、汽车制动系统等,其优势在于结构紧凑、输出力大、操作简便。
二、液压系统的工作原理液压系统的工作原理基于帕斯卡原理,即在密闭容器内,液体受到的压力能够大小不变地向各个方向传递。
具体来说,液压系统的工作过程如下:1. 液压泵:将机械能转化为液体的压力能,为系统提供动力源。
2. 液压缸(或液压马达):将液体的压力能转化为机械能,实现直线或旋转运动。
3. 控制阀:调节液体流动方向、压力和流量,实现对液压系统的控制。
4. 油箱:储存液压油,为系统提供油源。
5. 油管:连接各液压部件,传递压力和能量。
三、液压系统的分类1. 水基液压系统:以水作为工作介质,具有环保、成本低等优点,但易腐蚀金属、密封性能较差。
4. 气液联动液压系统:以气体和液体为工作介质,结合了气压传动和液压传动的优点,适用于特殊场合。
四、液压系统的关键部件详解1. 液压泵:作为液压系统的“心脏”,液压泵负责将低压油转化为高压油,为整个系统提供动力。
常见的液压泵有齿轮泵、叶片泵和柱塞泵等。
每种泵都有其独特的特点和适用范围,选择合适的液压泵对系统的性能至关重要。
2. 液压缸:液压缸是系统的执行元件,它将液压油的压力能转化为机械能,实现直线往复运动或推送力量。
根据结构不同,液压缸可分为活塞式、柱塞式和膜片式等。
3. 控制阀:控制阀是液压系统的“大脑”,它负责调节和分配液压油流动的方向、压力和流量。
常用的控制阀包括方向阀、压力阀和流量阀等,它们共同确保系统按照预定的要求稳定运行。
4. 滤清器:液压油中的杂质会对系统造成损害,滤清器的作用就是过滤液压油中的杂质,保护系统的正常运行。
合理选择和使用滤清器,对延长液压系统寿命具有重要意义。
五、液压系统的优势与应用1. 优势:力量大:液压系统能够实现大范围的力矩放大,轻松完成重物搬运等任务。
汽车液压制动系统 abs_esc 电磁阀技术要求及测试方法
汽车液压制动系统 abs_esc 电磁阀技术要求及测试方法
汽车液压制动系统 abs_esc 电磁阀技术要求及测试方法
随着汽车制造技术的不断发展,汽车液压制动系统 abs_esc 电磁阀也得到了广泛应用。
这种电磁阀可以控制汽车制动系统的压力,从而提高制动效果和安全性能。
在使用这种电磁阀时,需要注意一些技术要求和测试方法。
技术要求
1. 电磁阀的选择要根据汽车的型号和制动系统的要求来确定。
不同型号的汽车和不同类型的制动系统需要不同的电磁阀来控制制动压力。
2. 电磁阀的工作压力和流量要与汽车制动系统的要求相匹配。
如果电磁阀的工作压力和流量不足,会导致制动效果不佳。
3. 电磁阀的材料要具有耐腐蚀、耐高温、耐磨损等特性,以保证其长期稳定运行。
4. 电磁阀需要具有较高的密封性能,以避免制动系统漏油或进水等问题。
5. 电磁阀需要具有较高的工作可靠性和安全性能,以确保在紧急情况下能够及时响应并保证驾驶员和乘客的安全。
测试方法
1. 测试电磁阀的工作压力和流量。
可以使用压力表和流量计来测试电磁阀的工作压力和流量是否符合汽车制动系统的要求。
2. 测试电磁阀的密封性能。
可以使用气密性测试仪来测试电磁阀的密封性能,以确保其不会漏油或进水。
3. 测试电磁阀的工作可靠性和安全性能。
可以使用模拟器来模拟紧急情况下的制动操作,并测试电磁阀是否能够及时响应并保证驾驶员和乘客的安全。
总之,汽车液压制动系统 abs_esc 电磁阀是汽车制动系统中非常重要的一个部件,其选择、安装和测试都需要严格按照技术要求来进行,以确保汽车制动系统的正常运行和驾驶安全。
液压阀基础知识
目录第一章液压阀基础知识 (3)1.1液压技术的原理与液压系统的组成 (3)1.2 液压阀的功用及重要性 (3)1.3 液压阀的基本结构原理 (4)第二章充液阀的基本知识 (6)2.1 充液阀概述 (6)2.2充液阀的典型结构 (6)2.3 充液阀的结构原理 (7)2.4 充液阀的工作原理及性能 (8)2.4.1 充液阀的工作原理 (8)2.4.2 充液阀的性能 (10)2.5 充液阀的作用 (11)第三章设计软件简介 (12)3.1 Solidworks的相关知识 (12)3.1.1 SolidWorks软件的特点 (12)3.1.2 SolidWorks 2010的新功能 (14)3.2 SolidWorks 2010操作界面介绍 (17)3.2.1 SolidWorks 2010操作界面 (17)3.2.2 基本操作与文件管理 (20)3.2.3 工具栏 (21)第四章充液阀的设计建模 (23)4.1 充液阀的设计计算 (24)4.2 先导阀体的组建 (25)4.1.1 绘制草图 (26)第一章液压阀基础知识1.1液压技术的原理与液压系统的组成液压传动与控制简称为液压技术,是以液体为工作介质,利用封闭系统中液体的静压能实现信息、运动和动力的传递及工程控制的计术。
由于液压技术在功率密度,结构组成、响应速度,调节范围,过载保护、电液整合等方面独特的优势,使其成为现代传动与控制的重要基础技术之一,其应用遍及国民经济各个领域。
除了工作介质外,一个液压系统通常都是由能源元件(液压泵)、执行元件(液压缸、液压马达或摆动液压马达)、控制元件(各种液压阀)和辅助元件(邮箱和管路等)四类液压元件所组成。
液压传动与控制的机械设备或装置工作时,其液压系统以具有连续流动性的液压油或难燃液压液或水作为工作介质,通过液压泵将驱动泵的原动机的机械能转换成液体的压力能,然后经过封闭管路及控制阀送至执行器中,转换为机械能去驱动负载、实现工作机构所需的直线运动或回转运动。
中位技能常见液压阀型号、结构及机能
中位机能有O型、H型、X型、M型、Y型、P型、J型、C型、K型,等多种形式。
其中P表示总进油口,T表示总回油口,A表示工作进油口,B表示工作回油口。
一、O型符号为结构:四个油口全部封闭,系统里处处有油压。
机能:油泵不卸载荷,活塞静止不动。
活塞工作时由于活塞内部充满油液有阻碍作用。
二、H型符号为结构:所有四个油口全部开通。
机能:泵可以下卸载荷,活塞不受油压作用,可以自由伸缩。
工作时,系统里没有油液阻碍,运行比较平稳。
三、Y型符号为结构:P口封闭,A、B与回油口相连。
机能:由于P处封闭,所以泵无法卸载载荷,活塞不受油压作用,可以自由移动。
四、K型符号为结构:在中位时,进油口P与工作油口A与回油口T连通,而另一工作油口B封闭。
机能:油泵于回油口相通,可以卸载载荷。
活塞顶在最底处,静止不动。
五、P型符号为结构:工作有口A,B与P 机能:1、对于直径相等的双杆双作用油缸,活塞两端所受的液压力彼此平衡,工作机构可以停止不动。
也可以用于带手摇装置的机构。
但是对于单杆或直径不等的双杆双作用油缸,工作机构不能处于静止状态而组成差动回路。
2、从停止到启动比较平稳,制动时缸两腔均通压力油故制动平稳。
3、油泵不能卸荷。
4、换向位置变动比H型的小,应用广泛。
六、X型符号为结构:在中位时,A、B、P油口都与T回油口相通。
机能特点:1、各油口与回油口T连通,处于半开启状态,因节流口的存在,P油口还保持一定的压力。
2、在滑阀移动到中位的瞬间使P、A、B与T油口半开启的接通,这样可以避免在换向过程中由于压力油口P突然封堵而引起的换向冲击。
3油泵不能卸荷。
4、换向性能介于0型和H型之间。
七、U型符号为结构特点:A、B工作油口接通,进油口P、回油口T封闭。
机能特点:1、由于工作油口A、B 连通,工作装置处于浮动状态,可在外力作用下运动,可用于带手摇装置的机构。
2、从停止到启动比较平稳。
3、制动时也比较平稳。
4、油泵不能卸荷。
八、K型符号为结构特点:在中位时,进油口P与工作油口A与回油口T连通,而另一工作油口B封闭。
- 1、下载文档前请自行甄别文档内容的完整性,平台不提供额外的编辑、内容补充、找答案等附加服务。
- 2、"仅部分预览"的文档,不可在线预览部分如存在完整性等问题,可反馈申请退款(可完整预览的文档不适用该条件!)。
- 3、如文档侵犯您的权益,请联系客服反馈,我们会尽快为您处理(人工客服工作时间:9:00-18:30)。
一种全新的全液压制动系统介绍
1、技术背景
工程机械制动系统是行走机械的关键部件。
现有行
走类工程机械大都采用气/液助推制动系统,即以压缩
空气作为助推介质,通过一气液增压缸(俗称加力
器),将制动总泵内制动液增压后送入制动分泵实施
制动,属于双流体(气体液体)制动,该系统技术成
熟,价格低廉,在国内应用广泛。
但同时也存在不可
避免的缺陷:需单独的压缩气源,元件数量多,且尺
寸较大需气液两套管路,排气时噪声大,液压管路内易进入空气而造成制动不灵等故障。
近年来,国外的主要装载机厂商(如卡特、小松)对其主机制动系统进行全面改造,采用全液压制动系统,其原理是以液压油作为一介质,传递制动力,借用装载机液压系统作为其动力油源,通过液压控制元件,直接将压力油送至制动分泵实施制动,解决了气液助推制动系统的上述不足,成为今后轮式工程机械制动系统发展方向,是目前气动、气液制动系统工程及元件理想的替代产品。
一种用于工程机械的全液压制动阀,其特点是利用工作系统的油液进行全制动系统控制。
主要由充液系统、保压系统、管路防爆系统、双路制动系统、紧急制动系统、动力切断系统和止回阀及各连接制动器的油口和信号接口。
其优点在于一个阀包含了整个制动系统。
从而简化了工程机械的全液压制动系统元件的安装和管路连接。
该阀能完成优先充液、系统保压、制动压力输出、动力切断和多重保护等功能。
2、工作原理如下,
全液压制动系统主要由充液系统、保压系统、管路防爆系统、双路制动系统、紧急制动系统、动力切断系统和止回阀及各连接制动器的油口和信号接口等组成。
具体工作原理如下:
从油泵来油首先进入充液阀P口,通过滤芯2、单向阀3、压力调节阀4,到畜能器6。
在畜能器6内的压力没有达到压力调节阀4设定压力时,充液阀1的后腔被封闭,阻止了油液流向下一个回路N,油液通过单向阀3进入畜能器6。
双路制动阀7没有踏下工作时,a回路是封闭的,此时畜能器6被充压。
当畜能器内的压力达到压力调节阀4的开启压力时,压力调节阀的调压前腔的压力推动阀芯使充液阀的后腔与回油腔相通,充液阀后腔的压力下降,进油口P处的压力就推动充液阀芯后腔的弹簧,打开另一路油口N,油液流向下一个工作装置。
畜能器的油液由于有进油单向阀3和压力调节阀4作用而封闭,在畜能器6中形成保压。
当双路制动阀7被踏下时,畜能器的油液从a通过管路防爆阀5到b1、b2油路通向双路制动阀7,双路制动阀7减压后从e1、e2进入紧急制动阀8、通过紧急制动阀8后从br1、br2口输出到制动管路g1、g2,在制动器油缸15前装有止回阀14,制动油通过止回阀14进入制动器油缸15实现制动。
当多次制动后畜能器6内的压力下降到压力调节阀4设定的最低压力时,压力调节阀4的弹簧关闭了充液阀1的后腔,从而关闭了另一路N油口,重新为畜能器6充压、保压。
实现制动的连续性。
管路防爆阀组5用于防止在工作过程中某一制动管路出现意外,造成制动失灵的情况下而设置的保护装置;紧急制动阀组8用于防止双路制动阀的意外故障,造成制动失灵而设置的保护装置;畜能器放油阀9、畜能器安全阀10主要是起安全保护作用;变速箱动力切断阀组11是为改善制动效果而设置的;止回阀14主要是改变制动油液的流向,保证每一次制动过程中的油液是新的,以尽量减少频繁制动造成的油液升温。
管路防爆阀组5由一个阀芯、两端各有一个弹簧组成。
a为主进油路,中间两个油路b1、b2分别通向双路制动阀7的进油路。
边上的两个弹簧腔n1、n2分别与双路制动阀7的出油口e1、e2相通。
当制动阀正常工作时,两个弹簧腔n1、n2的压力基本相同。
此时阀芯始终保持在中间位置,进油路与双路制动阀的进油路相通,油液顺利通过不受影响。
当出现某一管路出现爆裂时,该管路的输出油压降为零,而另一路压力正常。
此时,压力正常腔就会推动阀芯移动切断通往爆裂管路的油路。
(如n2路出现故障,制动输出时e2管路就无压力。
而e1输出正常。
此时e1的压力通过n1将阀芯推下,切断通向n2的油路。
)保证在某一管路出现爆裂时。
另一管路还能继续工作。
紧急制动阀8是由阀杆和弹簧组成中间分别从双路制动阀7的出油口、畜能器6的油口及通往制动器br1、br2的出油口。
当双路制动阀正常工作时,从畜能器6来的油口是封闭的。
双路制动阀7的出油口与制动器15的进油口是相通的。
双路制动阀7作用时制动压力可直接作用于制动器15上形成制动。
当双路制动阀7由于某种原因无法制动时,只要拉动紧急制动阀8,此时畜能器6的油口与制动器15的油口直接相通,而双路制动阀7的油口被封闭,制动压力油从畜能器6通过S油路直接作用于制动器15上形成制动。
从而防止双路制动阀7意外故障造成无法制动情况发生。
该阀也可作临时停车制动用。
变速箱动力切断系统是由梭阀13及压力调节阀11组成。
主要是在某些制动情况下要求切断传动动力而设计,由于工程机械主要为液力传动。
其本身的动力性能可以保证在传动动力下进行制动,但效果有时不太好。
故增加动力切断。
压力调节阀11一路与双路制动阀7输出口相接,一路通操纵阀切断回路,一路与回油路相通。
正常情况下,操纵阀切断油路与回油路相通,没有压力油送到操纵阀切断回路。
当制动阀压力输出时,通过梭阀13把输出制动的最高压力就送到动力切断阀,当制动压力达到压力调节阀11设定压力时,压力调节阀打开了通往操纵阀的切断回路,并关闭了该路的回油路。
操纵阀在压力油的作用下切断变速箱油路形成动力切断。
这样制动效果与动力切断各取其一,从而既保证了制动性能又提高了制动效果。
止回阀14是安装在各个制动器进油口。
目的是让进油路与回油路分开,其由阀体、一个小阀芯和弹簧组成,一端h与进油口相连,一端T 与回油口相通,中间k口与制动器进口连接。
当没有制动压力油来时,
制动器的k口与T回油口相通。
当制动压力油来时,阀芯迅速关闭T回油口打开h进油口,保证制动压力油能进入制动器,实现制动效果。
当制动结束后,小阀芯在弹簧的作用下,迅速关闭进油口h,打开T回油口,让制动器内的油从k到回油口T流出。
达到每次进油都是新鲜油液,以尽量减少频繁制动造成的油液升温。
畜能器放油阀9主要是为修理制动器时把畜能器内的压力油放空。
以达到安全修理目的。
畜能器安全阀10保证畜能器意外超压时可以得到保护而设定畜能器内的最高压力。
整个制动系统由阀体1(制动阀)、阀体2(紧急阀),阀体3(止回阀)组成。
三组阀体可进行不同制动回路组合。
满足不同客户的需求。
在三个阀体上面分别加工有各种联接油口。
可分别接进油口、回油口、N油口、畜能器、低压报警开关、制动信号发生装置等等,保证整个系统的电器连接接口。
并与目前国内常用的液压制动系统可以互换互用。