刀具半径测量说明书
刀尖半径补偿编程及加工
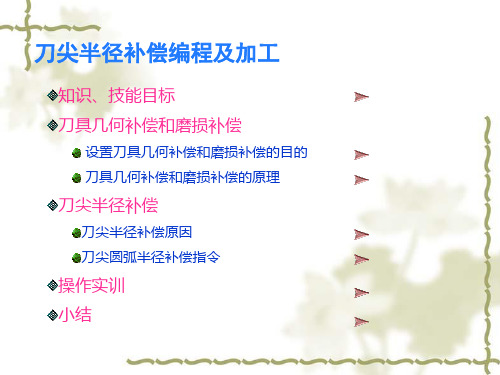
刀具几何补偿和磨损补偿的原理
当需要用多把刀加工工件时,编程过程中以其中一把刀为基准刀,事先测出 这把刀的刀尖位臵和要使用的各刀具的刀尖位臵差,并把已测定的这些值设定在 CNC刀具偏臵表中。这样在更换刀具时,采用刀具偏臵补偿功能后,不变更程序也 可以加工不同零件。
刀具补偿功能由程序中指定的T代码来实现,T代码后的4位数码中,前2位为 刀具号,后2位为刀具补偿号。刀具补偿号实际上是刀具补偿寄存器的地址号,该 寄存器中放有刀具的几何偏臵量和磨损偏臵量(X轴偏臵和Z轴偏臵),如图11-2 所示。
零件图工艺分析
数值计算 工件参考程序与加工操作过程
安全操作和注意事项
零件图工艺分析
(1)技术要求分析。如图11-11所示,零件包括圆柱面、圆锥面、凹凸圆弧、螺纹、沟槽、倒 角 等加工。零件材料为45#钢或铝。 (2)确定装夹方案、定位基准、加工起点、换刀点。毛坯为棒料,用三爪自定心卡盘夹紧定 位。工件零点设在工件右端面,加工起点和换刀点可以设为同一点,在工件的右前方距工件右 端面100mm,X向距轴心线50mm的位置。 (3)制定加工工艺路线,确定刀具及切削用量。加工刀具的确定如表11-1所示,加工方案的制 定如表11-2所示。
图11-3 刀尖图
图11-4 车削圆锥产生的误差
图11-5 车削圆弧面产生的误差
图11-6 半径补偿后的刀具轨迹
刀尖圆弧半径补偿指令
一般数控装置都有刀具半径补偿功能,为编制程序提供了方便。有刀具半径补偿功能的数 控系统编制零件加工程序时,不需要计算刀具中心运动轨迹,而只按零件轮廓编程。使用刀具 半径补偿指令,并在控制面板上手工输入刀尖圆弧半径,数控装置便能自动地计算出刀具中心 轨迹,并按刀具中心轨迹运动。即执行刀具半径补偿后,刀具自动偏离工件轮廓一个刀具半径 值,从而加工出所要求的工件轮廓。 当刀具磨损或刀具重磨后,刀具半径变小,这时只需手工输入改变后的刀具半径,而不需 要修改已编好的程序或纸带。 刀尖圆弧半径补偿是通过G41、G42、G40代码及T代码指定的刀尖圆弧半径补偿号,加入或取 消半径补偿。 G41:刀具半径左补偿,即站在第三轴指向上,沿刀具运动方向看,刀具位于工件左侧时 的刀具半径补偿。如图11-7所示。 G42:刀具半径右补偿,即站在第三轴指向上,沿刀具运动方向看,刀具位于工件右侧时 的刀具半径补偿。如图11-7 所示。 G40:刀具半径补偿取消,即使用该指令后,使G41、G42指令无效。
R规规格及使用
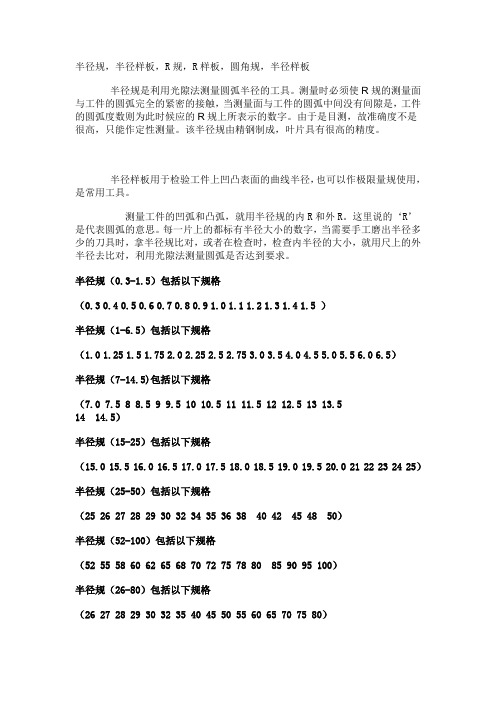
半径规,半径样板,R规,R样板,圆角规,半径样板半径规是利用光隙法测量圆弧半径的工具。
测量时必须使R规的测量面与工件的圆弧完全的紧密的接触,当测量面与工件的圆弧中间没有间隙是,工件的圆弧度数则为此时候应的R规上所表示的数字。
由于是目测,故准确度不是很高,只能作定性测量。
该半径规由精钢制成,叶片具有很高的精度。
半径样板用于检验工件上凹凸表面的曲线半径,也可以作极限量规使用,是常用工具。
测量工件的凹弧和凸弧,就用半径规的内R和外R。
这里说的‘R’是代表圆弧的意思。
每一片上的都标有半径大小的数字,当需要手工磨出半径多少的刀具时,拿半径规比对,或者在检查时,检查内半径的大小,就用尺上的外半径去比对,利用光隙法测量圆弧是否达到要求。
半径规(0.3-1.5)包括以下规格(0.3 0.4 0.5 0.6 0.7 0.8 0.9 1.0 1.1 1.2 1.3 1.4 1.5 )半径规(1-6.5)包括以下规格(1.0 1.25 1.5 1.75 2.0 2.25 2.5 2.75 3.0 3.5 4.0 4.5 5.0 5.5 6.0 6.5)半径规(7-14.5)包括以下规格(7.0 7.5 8 8.5 9 9.5 10 10.5 11 11.5 12 12.5 13 13.514 14.5)半径规(15-25)包括以下规格(15.0 15.5 16.0 16.5 17.0 17.5 18.0 18.5 19.0 19.5 20.0 21 22 23 24 25)半径规(25-50)包括以下规格(25 26 27 28 29 30 32 34 35 36 38 40 42 45 48 50)半径规(52-100)包括以下规格(52 55 58 60 62 65 68 70 72 75 78 80 85 90 95 100)半径规(26-80)包括以下规格(26 27 28 29 30 32 35 40 45 50 55 60 65 70 75 80)测量工具使用,R规,半径规测内圆半径方法测量工具使用,R规,半径规测外圆半径方法。
刀具几何角度测量实验

刀具几何角度测量实验刀具的几何角度是影响切削加工质量的重要因素之一,包括切削刃角、前角、后角、楔角等。
因此,准确地测量刀具的几何角度对于保证加工质量至关重要。
本实验旨在通过测量半径刀具的几何角度来了解刀具的基本几何特征。
1. 实验原理(1) 切削刃角:指刀刃与切削方向所成的角度。
(2) 前角:指在刀具作用于工件前,前侧刀面与工件表面所成的角度。
(4) 楔角:指刀子锋利部位顶点的前后切割刃所组成的夹角。
2. 实验设备测量半径刀具的实验设备包括:精密圆柱度千分尺、台式显微镜、减速器、圆度测量平台。
3. 实验过程(1) 切削刃角的测量先将刀具置于圆度测量平台上,用微调螺丝调试使得其保持水平状态。
接着,将显微镜放在刀具的边沿位置,通过目视读数法测量出刀刃与显微镜中一条直线之间的夹角。
这里需要注意的是,测量时需要注意观察刀刃切口的角度,尤其要避免不同部位所测得的切口角度的差异,以免影响最终的测量结果。
(2) 前角、后角的测量将刀具置于台式显微镜的中心位置,保证其与显微镜的光路垂直,然后在显微镜下观测刀具前、后侧刃面与工件的沿径向的加工角度。
该实验需要不断转动刀具,在不同的角度下观测,以保证测量结果最为准确。
(3) 楔角的测量取平面度千分尺,在其上端夹入刀具刃口,然后将其与刀具的标准位置进行比较,读取其上端和下端所测得的读数差值,即为楔角。
4. 实验结果分析在实验过程中,可以有效地观察和分析刀具各项几何特征,了解切削刃角、前角、后角、楔角等参数对加工质量的影响。
例如,切削刃角的大小会影响切削面的质量,前角的大小会对切削力产生重要影响,后角的大小会对削屑排出产生影响,而楔角则直接关系到刀具的锋利度和持久性等方面。
总之,刀具的几何角度测量实验是一项非常重要的加工技术实验,实验过程中需要格外注意每一个步骤,并保证遵守严格的安全规范,以达到理想的实验效果。
5海德汉中文使用说明书

5编程:刀具5.1输入刀具相关数据进给率F进给率F是刀具中心移动的速度,单位为mm/分钟或英寸/分钟。
每一个轴的最大进给率可以是不同的,在机床参数中设置。
输入您可以在刀具调用程序行和每个定位程序行中输入进给率(参阅117页“用路径功能键建立程序行”)。
快速行程如果您要编制快速行程程序,输入F MAX。
要输入F MAX,在对话提示Feed rate(进给率)F=?出现在屏幕上以后即按下ENT键或者F MAX软键。
有效持续性按数字值输入的进给率在程序行执行到不同的进给率之前一直保持有效。
F MAX只有被编入程序行才起作用。
当有F MAX的程序行被执行以后,进给率即返回到之前最后一次设定的进给率数值。
在程序运行期间改变进给率在程序运行期间您可用进给率修调旋钮改变进给率。
主轴转速S在TOOL CALL程序行中主轴转速是按每分钟转数(rpm)输入的。
编程修改在零件程序中,您可以只输入主轴转速来修改TOOL CALL程序行中的主轴转速参数:编制刀具调用命令:按TOOLCALL键。
用NO ENT键忽略Toolnumber?(刀号)对话提问。
用NO ENT键忽略Workingspindle axis X/Y/Z ?(工作主轴轴线)对话提问。
在对话提问Spindle speed S=?(主轴转速)时输入新的主轴转速,用END键确认。
在程序运行时修改在程序运行期间您可用进给率修调旋钮改变主轴转速。
845.2刀具数据刀具补偿要求您通常是按工件图上的尺寸编制仿型路径程序的。
要使TNC能计算刀具中心路径,例如刀具补偿,您必须同时输入使用的每一把刀具的长度和半径。
刀具数据输入可以直接在零件程序中用TOOL DEF键输入或者在刀具表中单独输入。
在刀具表中,也可以输入指定刀具的附加数据。
在执行零件程序时,TNC会考虑输入的全部刀具数据。
刀号和刀具名称每一把刀具是根据编号来识别的,编号范围为0-254。
如果您正在用刀具表加工,您可以使用较大的编号,也可以输入每一把刀具的名称。
R规规格及使用
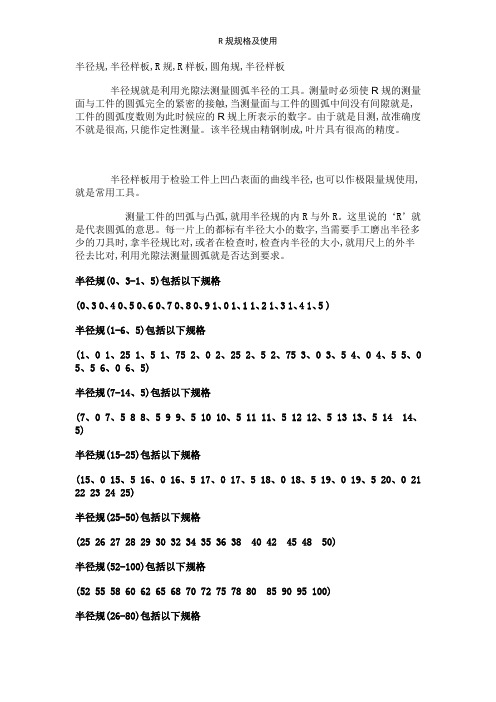
半径规,半径样板,R规,R样板,圆角规,半径样板半径规就是利用光隙法测量圆弧半径的工具。
测量时必须使R规的测量面与工件的圆弧完全的紧密的接触,当测量面与工件的圆弧中间没有间隙就是,工件的圆弧度数则为此时候应的R规上所表示的数字。
由于就是目测,故准确度不就是很高,只能作定性测量。
该半径规由精钢制成,叶片具有很高的精度。
半径样板用于检验工件上凹凸表面的曲线半径,也可以作极限量规使用,就是常用工具。
测量工件的凹弧与凸弧,就用半径规的内R与外R。
这里说的‘R’就是代表圆弧的意思。
每一片上的都标有半径大小的数字,当需要手工磨出半径多少的刀具时,拿半径规比对,或者在检查时,检查内半径的大小,就用尺上的外半径去比对,利用光隙法测量圆弧就是否达到要求。
半径规(0、3-1、5)包括以下规格(0、3 0、4 0、5 0、6 0、7 0、8 0、9 1、0 1、1 1、2 1、3 1、4 1、5 )半径规(1-6、5)包括以下规格(1、0 1、25 1、5 1、75 2、0 2、25 2、5 2、75 3、0 3、5 4、0 4、5 5、0 5、5 6、0 6、5)半径规(7-14、5)包括以下规格(7、0 7、5 8 8、5 9 9、5 10 10、5 11 11、5 12 12、5 13 13、5 14 14、5)半径规(15-25)包括以下规格(15、0 15、5 16、0 16、5 17、0 17、5 18、0 18、5 19、0 19、5 20、0 21 22 23 24 25)半径规(25-50)包括以下规格(25 26 27 28 29 30 32 34 35 36 38 40 42 45 48 50)半径规(52-100)包括以下规格(52 55 58 60 62 65 68 70 72 75 78 80 85 90 95 100)半径规(26-80)包括以下规格(26 27 28 29 30 32 35 40 45 50 55 60 65 70 75 80)测量工具使用,R规,半径规测内圆半径方法测量工具使用方法,R规,半径规测外圆半径。
数控机床对刀仪的使用说明
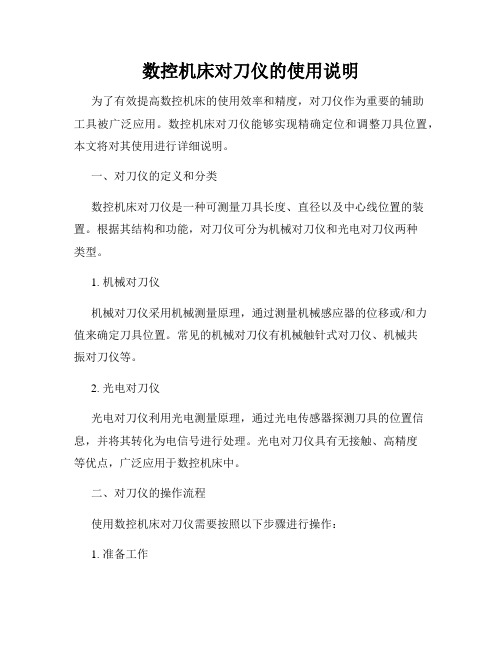
数控机床对刀仪的使用说明为了有效提高数控机床的使用效率和精度,对刀仪作为重要的辅助工具被广泛应用。
数控机床对刀仪能够实现精确定位和调整刀具位置,本文将对其使用进行详细说明。
一、对刀仪的定义和分类数控机床对刀仪是一种可测量刀具长度、直径以及中心线位置的装置。
根据其结构和功能,对刀仪可分为机械对刀仪和光电对刀仪两种类型。
1. 机械对刀仪机械对刀仪采用机械测量原理,通过测量机械感应器的位移或/和力值来确定刀具位置。
常见的机械对刀仪有机械触针式对刀仪、机械共振对刀仪等。
2. 光电对刀仪光电对刀仪利用光电测量原理,通过光电传感器探测刀具的位置信息,并将其转化为电信号进行处理。
光电对刀仪具有无接触、高精度等优点,广泛应用于数控机床中。
二、对刀仪的操作流程使用数控机床对刀仪需要按照以下步骤进行操作:1. 准备工作首先,确保对刀仪与数控机床正确连接,并确认连接稳固可靠。
其次,检查刀具是否安装正确,刀具应牢固固定在刀柄上,无松动现象。
2. 设置测量模式根据实际需要,选择对刀仪的测量模式。
常见的测量模式有刀长度测量、刀具半径测量和刀具边角测量等,根据不同的模式选择相应功能。
3. 启动机床和对刀仪打开数控机床和对刀仪的电源开关,并等待系统启动完成。
确保数控机床和对刀仪的通信正常。
4. 定位刀具和刀柄使用机械手或手动操作,将刀具和刀柄准确安装到数控机床的刀库中。
确保刀具和刀柄的编号与程序中一致。
5. 进行对刀操作按照数控机床的操作界面提示,选择对刀功能,并按要求操作。
对刀过程中,对刀仪将会自动测量刀具的位置信息,并将测量结果传输给数控机床进行相应调整。
6. 验证刀具位置对刀完成后,使用测量工具(如游标卡尺或三坐标测量机)验证刀具位置的准确性。
如果发现误差较大,应重新进行对刀操作。
三、对刀仪的注意事项在使用数控机床对刀仪时,需要注意以下事项,以确保操作的准确性和安全性:1. 定期校准对刀仪作为精密测量设备,需要定期进行校准,以保证测量的准确性。
《刀具半径补偿计算》课件

精加工中应用刀具半径补偿可以显著提高工件的加工质量和生产效率 。
刀具半径补偿在切削方式切换中的应用
在切削方式切换过程中,刀具 半径补偿可以自动调整切削参 数,以适应不同的切削条件和
工件材料。
在更换刀具或调整切削参数时 ,刀具半径补偿可以减少人工 干预和误差,提高加工精度和 效率。
少人为因素对加工结果的影响,为现代制造业的发展提供有力支持。
多轴联动加工中的刀具半径补偿技术
要点一
总结词
要点二
详细描述
多轴联动加工中的刀具半径补偿技术是未来发展的重点方 向,它能够实现复杂曲面的高精度加工,提高加工效率和 产品质量。
多轴联动加工是一种先进的加工技术,广泛应用于航空、 汽车、模具等领域。在多轴联动加工中,刀具半径补偿技 术对于实现高精度加工至关重要。通过精确控制刀具的轨 迹和补偿量,可以减小加工误差,提高加工精度和效率。 未来,多轴联动加工中的刀具半径补偿技术将进一步发展 ,为实现更高效、高精度的复杂曲面加工提供技术支持。
程,提高编程效率。
刀具半径补偿的计算原理
根据加工要求和刀具参数,确定刀具 半径补偿值。
补偿值的计算需要考虑多种因素,如 刀具类型、切削用量、工件材料等。
在数控加工过程中,根据刀具路径和 补偿值,对刀具路径进行相应的调整 ,以补偿因刀具半径而引起的加工误 差。
02
CATALOGUE
刀具半径补偿的分类
03
通过刀具半径补偿,还可以控制切削力的大小,以防止工件变形和刀 具破损。
04
粗加工中应用刀具半径补偿可以有效地提高加工效率和质量。
刀具半径补偿在精加工中的应用
Laser的校准和使用方法方法

BLUM Laser对刀仪的校准和使用方法一、Laser的校准方法1、安装标准刀,打出标准刀的长度和径向跳动偏摆,如下图1装好标准刀,手工测出标准刀的刀长(精确到0.001mm)。
再把测得标准刀刀长L和半径R(半径是在标准刀的图纸上有标示)输入到刀具表里面,标准刀在刀具表的刀号要与校准程序的刀号(H,D)对应。
1)、用千分表测出标准刀的最低端,到主轴端口的长度L,作为标准刀的长度(精确到0.001mm),记录下来,并输到对应的刀具表里边去。
(切记把标准刀长和半径输入到相应刀号的刀具表里)2)、用千分表打出标准刀径向跳动偏摆E,装标准刀时请注意,标准刀的跳动要严格控制在0.01mm内。
二.安装标准刀,找出Laser的中心位置(只在初次安装或位置有变动时才找中心位置)注:现场安装的LASER为激光束位于X/Y平面且与X轴平行;1.用千分表将Laser本体侧面平行度确定在0.01mm内(发射端与接收端),如下图:2.手摇手轮,把标准刀移动到Laser的中心位置(目测),用卡尺把标准刀定位在Laser的发射端与接收端的中心位置(精确到0.01mm),记录当前机械坐标值并停止移动。
例如:Laser与机床的X轴平行,就记录当前X轴的机械坐标值。
3.开启Laser(如执行#51524=1 (活塞开启)#51512=1 (模式E0开启)#51513=1 (模式E1开启)),移动标准刀(半径轴方向(Y轴)),手摇手轮,慢慢把标准刀定位到Laser的光线中心处,观察laser上的标有Out put信号灯,当信号灯Out put刚好显示红色时,停止移动,此时的Y轴机械坐标值减去标准刀半径值,将这个值记录;4.手摇手轮移动Z方向,慢慢把标准刀的下端面定位到Laser的中心处,观察信号灯Out put,当信号灯Out put刚好显示红色时,停止移动,此时的Z轴机械坐标值减去标准刀的长度,将这个值记录;如图:三.修改程序参数在O9671程序中找出以下参数,并进行修改:1、laser位置定义1)#104等于刀半径测量轴机械坐标值2)#105等于平行激光轴的机械坐标值3)#106等于刀长测量轴的机械坐标值2、标准刀长度定义1)#138标准刀类型定义:=0:BLUM专用标准=1:自备直棒标准刀2)#126等于标准刀的长度L,3)#127等于标准刀的半径R(该半径在标准刀图纸上有标示,请等于标示值)4)#1 等于标准刀的径向跳动偏摆E5)#128等于标准刀的T台高度H(标准刀图纸上有标示,请等于标示值)具体细见下图2图2四、执行校准程序O0601,校准Laser程序调用G65 P9601 H…D…A... R… X... Z...H .D 刀具长度和半径补偿编号A 重复测量的次数R 测量结果间的最大偏差值X 测量长度时测量位置的径向偏移Z 测量半径时测量位置的轴向偏移例如:O0601T1M06M03S3000.G65P9601 H1 .A3. R0.01 X5. Z5.M30五、执行完程序,整个校正就完成了。
- 1、下载文档前请自行甄别文档内容的完整性,平台不提供额外的编辑、内容补充、找答案等附加服务。
- 2、"仅部分预览"的文档,不可在线预览部分如存在完整性等问题,可反馈申请退款(可完整预览的文档不适用该条件!)。
- 3、如文档侵犯您的权益,请联系客服反馈,我们会尽快为您处理(人工客服工作时间:9:00-18:30)。
1、将刀具装载在主轴上,将量仪固定在工作台上(下文测量方法以固定在X轴方向上为例);
2、假设刀具触碰到量仪表面时的触发信号是X03.0,在PLC里如下图这样编辑:
X03.0:一号测头接触信号
G31.0:一号测头信号输入
3、编写程序如下:
(1)、将刀具由X负方向到正方向接触量仪,刀具接触到量仪的瞬间,触发X03.0信号后,程序自动停止,并将此时的机床坐标值保存到宏变量#1400~#1409中(依次为X、Y、Z等机床坐标值),记录下此时的X机床坐标值即#1400的值
(2)、程序继续运行,将刀具由X正方向到负方向接触量仪,刀具接触到量仪的瞬间,触发X03.0信号后,程序自动停止,并将此时的机床坐标值保存到宏变量#1400~#1409中(依次为X、Y、Z等机床坐标值),再一次记录下此时的X机床坐标值即#1400的值
(3)、将两次记录下的X机床坐标值取差值再减去量仪的宽度后再除以2即为刀具半径值
4、编程实例如下:(假设从X方向来测量)
#20=100 记录量仪的宽度
... ... 将刀具移动到量仪一端表面外
G91 G31.1 X100 F100 刀具由X负方向到正方向接触量仪,刀具接触到量仪的瞬间,
触发X03.0信号后,程序自动停止
#21=#1400 记录X轴机床坐标值
G01 X-10 F1000 使刀具远离量仪表面
Z50 抬刀
X150 将刀具移动到量仪另一端
Z-50
G91 G31.1 X-100 F100 刀具由X正方向到负方向接触量仪,刀具接触到量仪的瞬间,
触发X03.0信号后,程序自动停止并记录X轴机床坐标值#22=#1400 记录X轴机床坐标值
#23=(#22-#21-#20)/2 计算出刀具半径值
5、附上相关编程G指令及PLC信号的用法
(1)、跳转指令用于实现测量功能。
G31.x指令为轴移动指令,类似G01,其速度由F指定。
在执行G31.x指令时,向终点位置移动过程中,若系统检测到指定的外部信号有输入,则停止执行当前段,跳转到指定的程序段继续执行。
G31.1~G31.6可分别检测6个不同的外部输入信号(即PLC中的G31.0~G31.5信号)。
指令格式
G31.1/G31.2/G31.3/G31.4/G31.5/G31.6 IP_ F_ L_;
IP_: 绝对值指令时是终点的坐标值;增量值指令时是刀具移动的距离。
F_:指定进给速度
L_: 检测到外部输入时跳转的目标程序段,若未指定L,则自动跳转到下一段。
(2)、PLC的G信号的使用说明
G31.0 一号测头信号输
入
将一号侧头信号连接到G31.0
G31.1 二号测头信号输
入
将二号侧头信号连接到G31.1
G31.2 三号测头信号输
入
将三号侧头信号连接到G31.2
G31.3 四号测头信号输
入
将四号侧头信号连接到G31.3
G31.4 五号测头信号输
入
将五号侧头信号连接到G31.4
G31.5 六号测头信号输
入
将六号侧头信号连接到G31.5
(3)、触发G31.0信号后,对应保存机床坐标值的宏变量为#1400~#1409
触发G31.1信号后,对应保存机床坐标值的宏变量为#1410~#1419 触发G31.2信号后,对应保存机床坐标值的宏变量为#1420~#1429 触发G31.3信号后,对应保存机床坐标值的宏变量为#1430~#1439 触发G31.4信号后,对应保存机床坐标值的宏变量为#1440~#1449 触发G31.5信号后,对应保存机床坐标值的宏变量为#1450~#1459。