玻璃的电熔化
玻璃工业窑炉 第四章电熔窑第四节电极选型与布置

•多用在小型电熔窑上。 •板状电极损坏时可由它代替。 •能产生强烈对流,热量集中在与电极 相接触耐材,易造成耐材损坏。
4.4.4水冷套 (1)水冷套的作用
由于金属钼的耐热性能特别好,可经受 2600℃的温度,属难熔金属。但它的氧化性能在 温度600℃以上明显加剧,因此,为了保护钼电 极,使其不致很快被氧化,必须采用电极水冷却 装置,否则会影响整个熔炉的正常运转,严重时 将迫使电熔窑停产。
•缺点:当防氧化措施不当时易损坏且更换 困难。池底侵蚀严重时有漏料危险。
•全电熔窑不采用。
③板状电极:
•紧贴布置侧墙上,使电流密度和热量分 布都较匀,电极侵蚀较小,适合硼玻璃 熔制及不希望有强烈对流的部位。如流 液洞、供料道上,能在小区域内均匀加 热,不使耐材过分侵蚀,
•缺点:运行间不能更换。
④塞状电极
缺点:只用于具有还原能力的玻璃,易 使玻璃着色(棕色),接触电阻大,允 许电流密度0.1~0.3A/ cm2,电极直径较 大(150~200mm)。
石墨电极通常水平安装在液面下25mm 处左右,玻璃中金属氧化物着色剂会被 还原成金属,沉淀在电极上,或产生碳 化物,改变玻璃色泽。因此,不能用于 熔制硼玻璃、彩色玻璃和铅玻璃。
③二氧化锡电极
•具有抗氧化作用的陶瓷材料,除用于熔 制 铅 玻 璃 , 还 可 熔 制 含 As2O3 、 CoO 、 Fe2O3的玻璃。
•块 状 ( 砖 块 ) 或 粗 棒 状 ( 12mm ) , 密 度6.8 kg/cm3,耐急热急冷性好,但抗拉 强度低。
•氧化锡电导体具有负的特性,在400℃时 电 阻 率 为 0.8~1.2Ω·cm,1000℃ 为 0.0025~0.0045Ω·cm,因此,须在高温下 向电极供电。
玻璃生产工艺流程
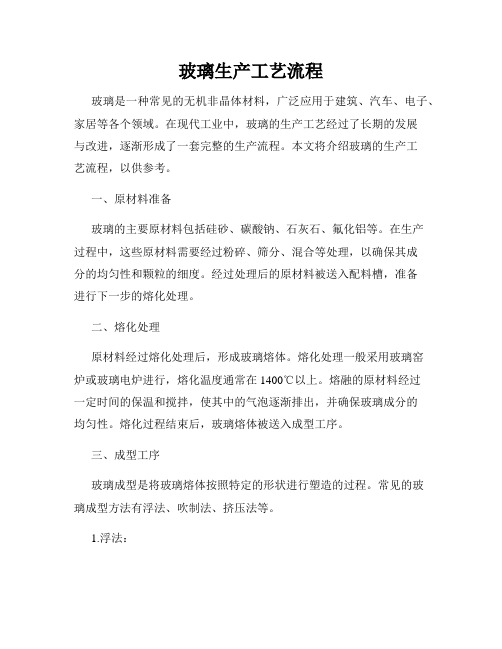
玻璃生产工艺流程玻璃是一种常见的无机非晶体材料,广泛应用于建筑、汽车、电子、家居等各个领域。
在现代工业中,玻璃的生产工艺经过了长期的发展与改进,逐渐形成了一套完整的生产流程。
本文将介绍玻璃的生产工艺流程,以供参考。
一、原材料准备玻璃的主要原材料包括硅砂、碳酸钠、石灰石、氟化铝等。
在生产过程中,这些原材料需要经过粉碎、筛分、混合等处理,以确保其成分的均匀性和颗粒的细度。
经过处理后的原材料被送入配料槽,准备进行下一步的熔化处理。
二、熔化处理原材料经过熔化处理后,形成玻璃熔体。
熔化处理一般采用玻璃窑炉或玻璃电炉进行,熔化温度通常在1400℃以上。
熔融的原材料经过一定时间的保温和搅拌,使其中的气泡逐渐排出,并确保玻璃成分的均匀性。
熔化过程结束后,玻璃熔体被送入成型工序。
三、成型工序玻璃成型是将玻璃熔体按照特定的形状进行塑造的过程。
常见的玻璃成型方法有浮法、吹制法、挤压法等。
1.浮法:浮法成型是将玻璃熔体浇入一个铁皮上,使得玻璃浮在熔锡池上,由于密度差,玻璃可以平均地自然延展成一片均匀的薄板。
这种成型方法应用广泛,一般用于生产平板玻璃。
2.吹制法:吹制法是将玻璃熔体吹入空气中,利用气压和重力的作用,在金属模具上进行成型,然后经过冷却和退火处理。
这种成型方法适用于制作中空玻璃容器,如玻璃瓶、玻璃杯等。
3.挤压法:挤压法是将玻璃熔体挤压在两个金属轮之间,形成所需的截面形状,然后再经过冷却和退火处理。
这种成型方法常用于制造光纤、玻璃管等。
四、退火处理退火是将已成型的玻璃制品进行再加热,然后缓慢冷却的过程。
通过退火处理,可以消除玻璃内部的应力,提高其强度和耐热性。
不同种类的玻璃需要采用不同的退火工艺。
五、表面处理表面处理是指对玻璃制品表面进行加工或涂覆,以增强其功能或美观度。
常见的表面处理方法有抛光、涂层、镀膜等。
1.抛光:抛光是利用砂轮、抛光机等工具对玻璃表面进行研磨和抛光,以去除表面的划痕、毛刺等缺陷,使其光滑度得到提升。
电是如何熔化玻璃的
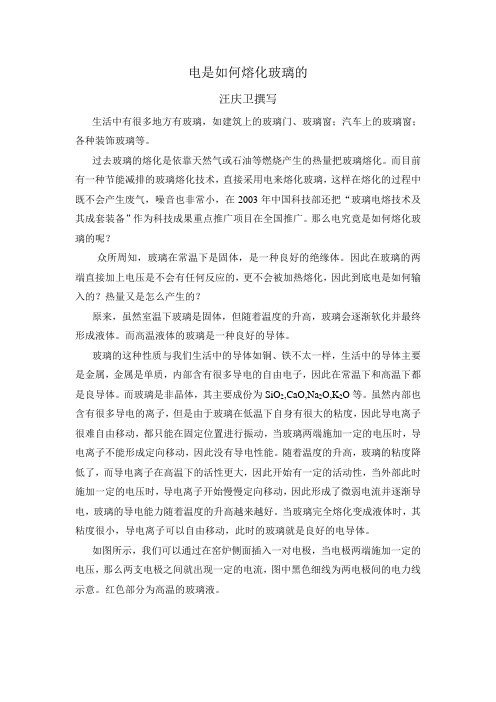
电是如何熔化玻璃的汪庆卫撰写生活中有很多地方有玻璃,如建筑上的玻璃门、玻璃窗;汽车上的玻璃窗;各种装饰玻璃等。
过去玻璃的熔化是依靠天然气或石油等燃烧产生的热量把玻璃熔化。
而目前有一种节能减排的玻璃熔化技术,直接采用电来熔化玻璃,这样在熔化的过程中既不会产生废气,噪音也非常小,在2003年中国科技部还把“玻璃电熔技术及其成套装备”作为科技成果重点推广项目在全国推广。
那么电究竟是如何熔化玻璃的呢?众所周知,玻璃在常温下是固体,是一种良好的绝缘体。
因此在玻璃的两端直接加上电压是不会有任何反应的,更不会被加热熔化,因此到底电是如何输入的?热量又是怎么产生的?原来,虽然室温下玻璃是固体,但随着温度的升高,玻璃会逐渐软化并最终形成液体。
而高温液体的玻璃是一种良好的导体。
玻璃的这种性质与我们生活中的导体如铜、铁不太一样,生活中的导体主要是金属,金属是单质,内部含有很多导电的自由电子,因此在常温下和高温下都是良导体。
而玻璃是非晶体,其主要成份为SiO2,CaO,Na2O,K2O等。
虽然内部也含有很多导电的离子,但是由于玻璃在低温下自身有很大的粘度,因此导电离子很难自由移动,都只能在固定位置进行振动,当玻璃两端施加一定的电压时,导电离子不能形成定向移动,因此没有导电性能。
随着温度的升高,玻璃的粘度降低了,而导电离子在高温下的活性更大,因此开始有一定的活动性,当外部此时施加一定的电压时,导电离子开始慢慢定向移动,因此形成了微弱电流并逐渐导电,玻璃的导电能力随着温度的升高越来越好。
当玻璃完全熔化变成液体时,其粘度很小,导电离子可以自由移动,此时的玻璃就是良好的电导体。
如图所示,我们可以通过在窑炉侧面插入一对电极,当电极两端施加一定的电压,那么两支电极之间就出现一定的电流,图中黑色细线为两电极间的电力线示意。
红色部分为高温的玻璃液。
玻璃能导电了,那么电通过玻璃体,玻璃由于自身的电阻形成焦耳热,就像家里的电灯泡、电阻炉一样,电流经电阻后,由于导电粒子的持续流动产生的离子间、分子间等内部碰撞摩擦,使得玻璃体自身发热,该热量的持续产生使得玻璃体温度逐渐升高,直至玻璃自身被熔化。
玻璃生产过程(3篇)

第1篇一、引言玻璃是一种具有广泛应用领域的无机非金属材料,广泛应用于建筑、汽车、电子、光学、化工等领域。
玻璃的生产历史悠久,技术不断进步,如今已成为现代化工业的重要组成部分。
本文将详细介绍玻璃生产的过程,包括原料选择、熔化、成型、退火、检验等环节。
二、原料选择1. 纯碱(Na2CO3):纯碱是玻璃生产的主要原料之一,其主要作用是降低熔化温度,提高熔化速度,改善玻璃的化学稳定性。
2. 石灰石(CaCO3):石灰石在玻璃生产中起到稳定熔融玻璃的作用,可以减少玻璃中的铁、镁等有害成分,提高玻璃的透明度。
3. 硅砂(SiO2):硅砂是玻璃生产的主要原料,其含量决定了玻璃的化学成分,对玻璃的物理性能有重要影响。
4. 镁砂(MgO):镁砂可以提高玻璃的化学稳定性,降低热膨胀系数,提高玻璃的耐热冲击性能。
5. 铝土矿(Al2O3):铝土矿可以提高玻璃的化学稳定性,降低玻璃的软化温度,提高玻璃的耐热冲击性能。
6. 硼砂(B2O3):硼砂可以提高玻璃的化学稳定性,降低玻璃的热膨胀系数,提高玻璃的耐热冲击性能。
三、熔化1. 熔炉选择:根据玻璃的种类和生产规模,选择合适的熔炉。
常见的熔炉有池炉、窑炉、熔窑等。
2. 熔化过程:将选好的原料按照一定的比例进行混合,放入熔炉中加热熔化。
熔化过程中,熔炉内的温度控制在1200℃-1500℃之间,使原料充分熔化。
3. 混合:在熔化过程中,通过搅拌使熔融的玻璃充分混合,达到均匀的化学成分。
四、成型1. 拉丝法:将熔融的玻璃拉成细丝,经过冷却、拉伸、退火等工序,制成玻璃纤维。
2. 拉管法:将熔融的玻璃拉成管状,经过冷却、切割等工序,制成玻璃管。
3. 压延法:将熔融的玻璃压延成薄片,经过冷却、切割等工序,制成玻璃板。
4. 拉伸法:将熔融的玻璃拉伸成薄片,经过冷却、切割等工序,制成玻璃丝。
五、退火1. 退火目的:退火是为了消除玻璃内部的应力,提高玻璃的物理性能,如强度、耐热冲击性能等。
平板玻璃熔窑电助熔设计与计算

0引言玻璃液在高温熔融状态下是一种电导体。
电熔化已在玻璃行业广泛使用,电助熔热效率高、玻璃的热稳定性和均匀性好,具有提高玻璃质量和降低能耗等优点,有广阔的发展空间。
传统大型平板玻璃熔窑电助熔负荷未超过10%,节能效果有限,实现节能减排技术性突破,增大电助熔负荷势在必行。
平板玻璃熔窑稳定的玻璃液流和合理的液流位置及形态对玻璃熔窑的操作至关重要,电助熔玻璃熔窑的电功率输入及位置设计同样要以保证玻璃熔窑的配合料层、环流Ⅰ、环流Ⅱ以及生产流的稳定为前提。
电助熔功率分配和分区设计及电极布置是电助熔玻璃熔窑的设计难点和设计关键,需结合火焰空间热负荷保证工艺制度和温度梯度,为保证设计合理,必要时需借助数学模拟或物理模型等辅助手段。
1电助熔玻璃熔窑的设计与计算(1)电助熔加热功率及装机功率计算普通平板玻璃(12%碎玻璃)理论熔化热由以下几部分组成:①生成硅酸盐耗热:272 kJ/kg玻璃液;②玻璃液加热至1400 ℃所需热量:1842 kJ/kg玻璃液;③生成玻璃耗热:314 kJ/kg玻璃液;④蒸发水分耗热:104 kJ/kg玻璃液;理论熔化总热耗:2533 kJ/kg玻璃液(不含玻璃液生成气加热耗热),转换为电能为0.7 kWh/kg玻璃液,考虑到电极水套及变压器等能量损失,电助熔的热效率可达85%~90%,那么玻璃液所需输入功率为32~34 kW/t玻璃液(不包含窑炉散热损失),装机功率按40~45 kVA/t玻璃液配置。
(2)电助熔分区设计投料口区域池底温度低,一般理所当然地认为电助熔大部分功率应增设在该区域,事实上国内确实有厂家这样分区布置电助熔,但效果并不理想。
对此做数学模拟,方案1:前置四区均布电极,装机功率3600 kVA;方案2:前区均布三排电极,装机功率1500 kVA,热障区两排电极,装机功率2100 kVA 。
图1为600 t/d颜色玻璃电助熔数学模拟玻璃液流示意图。
图1 600 t/d颜色玻璃电助熔数学模拟玻璃液流示意图数学模拟对比显示,方案1池底热点前移,较大地改变了玻璃窑炉纵向液流形态,不利于玻璃的熔化和澄清。
玻璃制造工艺

玻璃制造工艺玻璃是一种常见且重要的建筑材料,它具有透明、坚固、耐腐蚀等优点,广泛应用于建筑、家居、食品等领域。
而玻璃的制造工艺则是将玻璃原料经过熔化、成型、退火等一系列工序制成成品玻璃的过程。
首先,玻璃的制造过程始于选择合适的原料。
玻璃的主要原料包括石英砂、碳酸钠、石灰石和氟化物。
其中石英砂是主要的成分,而碳酸钠则是增加玻璃熔化温度的关键。
制造高质量的玻璃需要精确控制原料含量和均匀混合。
其次,选定了原料后,将其置于玻璃窑中进行熔化。
玻璃窑一般采用高温电炉,将原料加热到接近1400摄氏度的高温,使其熔化成为高粘度的玻璃液体。
在熔化的过程中,需要加入适量的气体和助熔剂,以调整玻璃的流动性和成分。
接着,熔化的玻璃液体会被送入成型机中进行成型。
成型机通常采用两种方式:一种是浮法成型,将熔化的玻璃液流注在熔锡表面上,使其平稳流动,并形成平整的玻璃薄板。
另一种是吹制成型,将熔化的玻璃液注入吹制机内,利用气压的作用使其膨胀并成型成为容器或其他形状。
成型后的玻璃被送入退火炉进行退火处理。
退火是将玻璃加热到较高温度后缓慢冷却的过程,目的是消除内部应力,提高玻璃的强度和稳定性。
退火过程中需要严格控制温度和冷却速度,以避免出现裂纹和变形。
最后,退火后的玻璃将经过切割、打磨等加工工序,变成符合需求的成品玻璃。
切割工序将玻璃切割成各种尺寸和形状,而打磨则使其表面光滑度达到要求。
这些加工工序需要高度的精确性和专业技术,确保玻璃的质量和外观。
总结起来,玻璃的制造过程包括原料选择、熔化、成型、退火和加工等关键步骤。
在制造过程中,需要严格控制各个环节的参数,确保玻璃的品质和性能。
同时,为了推动玻璃制造工艺的发展和创新,我们也需要不断改进生产设备和技术,提高效率和质量。
对于从事玻璃制造业的企业和从业人员而言,掌握和了解玻璃制造工艺是至关重要的。
只有通过科学合理的工艺流程和严谨的操作,才能生产出高质量、符合标准的玻璃制品。
因此,希望相关行业能够加强技术培训和交流,共同推动玻璃制造工艺的进步和发展。
玻璃的熔化和淬火工艺
玻璃的熔化和淬火工艺玻璃是一种非晶态的无机材料,其具有高硬度、透明度高、耐高温等优点。
玻璃的熔化和淬火工艺是制备玻璃制品的重要过程,下面我将详细介绍玻璃的熔化和淬火工艺。
首先,我们来看一下玻璃的熔化工艺。
玻璃的原材料主要包括硅酸盐、碱金属氧化物、碱土金属氧化物等。
这些原材料按照一定比例混合后,放入大型电炉中进行熔化。
炉内的温度通常在1000以上,使原材料迅速熔化并混合均匀,形成玻璃熔液。
在熔化过程中,玻璃熔液需要经历一个退火过程,即将熔液加热到一定温度,然后缓慢冷却。
这是因为在熔化过程中,玻璃内部会产生一些微小的压力或应力,通过退火可以有效地消除这些内部应力,改善玻璃内部结构的稳定性。
玻璃的熔化温度通常很高,达到几百度甚至几千度,因此需要采用特殊的炉内材料和高温耐火材料来保证炉的正常运行。
同时,由于玻璃熔液是一种高粘度流体,容易粘附在炉内,因此熔化工艺中需要定期清理炉内的玻璃余渣,保持炉内环境的清洁。
熔化完成后,接下来是玻璃的淬火工艺。
淬火是指将玻璃制品迅速冷却,使其表面形成高压层,内部形成低温应力,从而使玻璃增加硬度和强度。
淬火可以有效地改善玻璃的物理性质,使其耐冲击性、耐磨性等得到提高。
淬火过程中,玻璃制品通常通过注入冷却介质或将其置于淬火槽中进行冷却。
常见的淬火介质包括冷水、冷油等。
选择合适的淬火介质主要根据制品的大小和形状来决定,以确保玻璃能够均匀冷却,并且不会产生应力集中。
淬火工艺需要严格控制冷却时间和温度,过快或过慢的冷却都会对玻璃的性能产生不良影响。
过快的冷却会导致玻璃内部应力过大,使其易碎;而过慢的冷却则会使玻璃保留部分受热时产生的高温应力,从而影响玻璃的表面质量和强度。
除了以上的熔化和淬火工艺,玻璃制品的生产还涉及其他工艺,如成型、抛光等。
成型工艺包括玻璃的注射成型、热成型、吹制等方式,这些成型方式能够按照不同的需求制作出各种形状的玻璃制品。
抛光则是通过机械或化学方法消除玻璃表面的细小瑕疵,提高其表面光洁度。
全电熔浮法工艺与特种功能玻璃
在 有害 烟尘散 布 的 问题 , 因此采 用 电熔 炉可 提高 环境
全 电熔 浮 法 玻璃 熔 窑 主 要 型式 是 用 电作 为 能 源 对玻璃 料加 热 ,利用 玻 璃液 在高 温 下导 电 的特 性 , 在
的品质 。全 电熔窑 炉 , 熔化率 一般 可达 到 2吨/ 其 平方 米 ・ 以上 ; 天 电熔 窑设 计 结 构 紧凑 、 占地 面 积少 、 用 使
2 我 国全 电熔 浮 法玻 璃 熔 窑 的 发 展
电熔 技 术 在 2 0世 纪 初 就 已经 在 国外 开 始 应 用 ,
在 三 、 四 十 年 代 随 着 金 属 钼 电极 的 发 现 而 迅 速 发 展 ,
熔 制 出 的玻 璃 液成 分 均 匀 , 品质 量 高 ; 产 过 程便 产 生
建筑 玻璃 与工 业玻 璃 2 1 , 0 0 №7
全 电熔 浮法工艺 与特种功能玻璃
中国洛 阳浮 法玻璃 集 团有 限责任 公 司 鲁鹏
摘 要 : 文通 过 对全 电熔 浮 法玻璃 熔 窑特 点 的分析 , 本 阐述 了全 电熔浮 法玻 璃熔 窑 生产特 种 功能玻 璃
的应 用前景 。 关键 词 : 电熔 全 浮法 功 能 特 种 玻 璃
1 前 言
玻璃 电熔 技术 是 目前 国际 上最 先进 的熔制 工艺 ,
插 人玻 璃 的每组 电极 上 加 以一定 的交 流 电压 , 电流 将
通 过 电极 引入玻 璃液 中 , 电后两 电极之 间 的玻璃 液 通 在交 流 电的作用 下产 生 焦耳 热 , 过 焦耳 效应 使玻 璃 通 加 热熔 融 , 时 玻璃 原料 由熔窑 上部 ( 这 顶端) 匀撒入 , 均 形成一 个 “ 冷顶 ” 整个熔 化 池玻璃 液表 面覆 盖着 配合 。 料层 , 阻挡 了熔 体 的热 辐 射 , 合料 层 下 玻璃 熔 体 缓 配 慢流 入 电极 区 , 通过 电极 不 断提 供 热 量 , 璃料 沿 垂 玻
玻璃的熔制及熔-1
3.1 玻璃熔制工艺原理☐玻璃熔制的五个阶段☐(1)硅酸盐形成阶段☐800~1000℃进行;最后变成由硅酸盐和二氧化硅组成的不透明烧结物;硅酸盐形成速度取决于配合料性质和加料方式。
☐(2)玻璃形成阶段☐1200 ~1300 ℃左右进行;☐硅酸盐和石英砂粒完全溶解于熔融体中,成为含大量可见气泡、条纹、在温度上和化学成分上不够均匀的透明的玻璃液。
☐(3)玻璃液澄清阶段☐1400~1500℃进行;☐气体因玻璃液黏度降低而大量逸出,直到气泡全部排出。
☐(4)玻璃液均化阶段☐此阶段结束时的温度略低于澄清温度;☐当玻璃液长时间处于高温下,由于对流、扩散、溶解等作用,玻璃液中的条纹逐渐消除,化学组成和温度逐渐趋向均一。
☐(4)玻璃液均化阶段☐此阶段结束时的温度略低于澄清温度;☐当玻璃液长时间处于高温下,由于对流、扩散、溶解等作用,玻璃液中的条纹逐渐消除,化学组成和温度逐渐趋向均一。
3.1.1 配合料的熔化(1)配合料的加热及初熔(2)各种反应简介多晶转变盐类分解水分的逸出(3)成分的挥发R2O的挥发由纯碱引入时:引入量×0.032%由芒硝引入时:引入量×0.06% ☐另外要考虑氧化铈、煤粉的挥发量。
☐(4)影响配合料熔化的因素☐熔化温度:温度每升高10℃,反应速度增加☐10%;☐原料的形式:颗粒度的搭配、加料方式;☐原料的易熔性:助熔剂的多少、原料的活性;3.1.2 玻璃的形成☐(1)玻璃的形成过程☐玻璃的形成过程的速度取决于石英颗粒的熔解和扩散速度。
☐助溶剂的多少(熔化速度);☐熔体的黏度(扩散速度);☐熔体温度(熔化速度);☐石英颗粒(熔解快慢)。
3.1.3 澄清☐(1)目的☐消除玻璃液中的气泡☐(2)玻璃液中的气泡形态和种类☐形态:可见气泡、溶解气泡、化学结合的气☐体。
还有熔体表面上的气体。
☐种类:CO2、SO2、SO3、N2、O2、H2O、H2☐(3) 排泡与去气☐澄清是排出玻璃液中的可见气泡;☐去气是全部排除玻璃液中的气体,包括化学结合的气体。
浮法玻璃大功率电熔化工艺的应用分析赵会杰1王长军2孙飞虎3
浮法玻璃大功率电熔化工艺的应用分析赵会杰1 王长军 2 孙飞虎3发布时间:2023-07-04T04:29:37.315Z 来源:《科技新时代》2023年8期作者:赵会杰1 王长军 2 孙飞虎3[导读] 文章分析大型浮法玻璃溶窑大功率复合熔化技术的使用可行性,主要论述浮法玻璃电熔化工艺上存在的问题,论述该工艺在当前的使用。
当前浮法玻璃复合熔化技术并没有普及,仅仅有少部分在生产线使用,技术突破对行业发展十分重要。
河北视窗玻璃有限公司河北省廊坊市 065000摘要:文章分析大型浮法玻璃溶窑大功率复合熔化技术的使用可行性,主要论述浮法玻璃电熔化工艺上存在的问题,论述该工艺在当前的使用。
当前浮法玻璃复合熔化技术并没有普及,仅仅有少部分在生产线使用,技术突破对行业发展十分重要。
关键词:浮法玻璃;电熔化;技术;行业;效益近现代社会发展不断变革,国家发改委与工信部、生态环境部门联合发布《高耗能行业重点领域节能降碳改造升级实施指南(2022年版)》,对玻璃行业的节能降碳改造升级提出相关意见,指出行业发展速度快,为顺应时代发展的潮流,要进一步提升玻璃行业的生产效率,保障行业的节能效果,增强绿色低碳节能。
玻璃熔制是在高温状态下进行的,反应比较复杂,因此技术研发也存在诸多难度。
1.浮法玻璃大功率电熔化工艺发展现状1.1 生产现状在玻璃生产制造中,大功率电熔化技术就是指将电能转化成为热能融化玻璃的技术,技术的关键就是电熔能力在总熔能力的占比,如果占比超过50%,则可以称为是电主熔技术,相反如低于50%,则是助熔技术。
国外的浮法玻璃复合熔化技术已经成熟,但是国内的总熔化能力只有10%。
在浮法玻璃电熔化应用中,某集团曾经在熔化量700t/d溶窑中安装助熔系统,安装为6750KW,该系统的最大能力仅占总熔化能力只有25%,这是该领域内所记录的浮法玻璃溶窑复合熔化技术中的最大电熔功率。
现阶段玻璃纤维行业内,溶窑可采用的复合熔化技术能力达到400t/d,电熔能力方面,国外技术可占熔化能力的45%,国内技术为25%。
- 1、下载文档前请自行甄别文档内容的完整性,平台不提供额外的编辑、内容补充、找答案等附加服务。
- 2、"仅部分预览"的文档,不可在线预览部分如存在完整性等问题,可反馈申请退款(可完整预览的文档不适用该条件!)。
- 3、如文档侵犯您的权益,请联系客服反馈,我们会尽快为您处理(人工客服工作时间:9:00-18:30)。
玻璃成型与热处理
模具温度的控制:
I.玻璃不粘模 II.玻璃不炸裂
退火工艺
谢谢!
举例:
某厂k9连熔炉 温度与功率分 配情况
熔化池 上电极 中电极 下电极
1330℃ 21kw 54kw 24kw
澄清池
工作池
1380 ℃ 50kw 1250 ℃ 18kw
光学玻璃连续熔炼的质量
光学玻璃连续熔炼的质量控制关键在于保持熔炉的稳 定运行
了解光学玻璃的熔炼方法和技术,了解融体中的缺陷如 气泡、条纹、结石和失透的原因和克服方法。
二硅化钼电热元件(硅钼棒)
硅钼棒是一种以二硅化钼为基础制成的电阻发热元件,氧化 气氛下高温使用,表面玻化,生成一层光亮致密的石英 (SiO2)玻璃膜,能保护硅钼棒不再氧化,因此硅钼棒元件 具有独特的高温抗氧化性。在氧化气氛下,元件最高使用温 度为1700℃,根据用户需求可制成棒状,U型、W型、U型直角 等形状。
电阻率(Ω.cm) 800℃ 1000℃
抗折强度(MN/m2) 20℃
热膨胀系数(k-1) 导热性(w/mk) 200℃ 600℃ 800℃
指标 6.38~6.58
0.02 0.015
115 4.9x10-6
60 40 35
钼电极
钼电极性能
◇ 物理性质:钼电极表面光滑致密、呈灰色金属光泽,密度大 于10.2g/cm3. ◇ 化学性能:适用范围广,能熔化大多数玻璃,如难熔玻璃、 粘度大的玻璃、挥发组分高的玻璃等,除了铅玻璃以外,钼对 其他玻璃组分都是稳定的。在钠钙玻璃中,钼电极有较好的抗 侵蚀性能。
注意:硅钼棒不宜在400~700 度范围内使用,否则元件会因 低温强烈氧化而粉化
电极间玻璃液电阻的计算
欧姆定律及经验公式对电阻的估算
两列水平电极间电阻: R=K×ρ ×L/(H ×W)
三相接法中两电极间电阻:
R K ln 2b L d
b为电极间距,L为电极插入 深度
熔炉大小流液洞及铂金料管的设计
耐火材料的选择
选材原则主要考虑耐火材料的侵蚀性和电阻特性。 使用最广泛是含ZrO2 33~41%的电熔锆刚玉砖
AZS-41 为一种高品质防火材料,并具有防腐、抗污染的特性。 用于熔炉中对抗腐蚀要求较高的部位,如:电熔炉,流量口, 注料口拐角砖等。
AZS-36 为一种中间产品 (33~41之间) ,具有较强的防腐,抗 污染性能。 用于熔炉中与玻璃熔液直接接触的部位。如:壁砖
熔炉大小由出料量Q决定 电熔窑的熔化率最高为2.4~3t/m² • d 铂金料管与流液洞大小:
Q r 4g(h l) 8l
烤炉
烤炉工艺
℃
温 1200 度 ( 1000 ) 600
60
90 100
时间(H)
电极的保护 耐火材料晶相的转变
烤炉注意事项
熔炉中的玻璃液流
功率分配与控制
熔化上电极中电极与下电极的关系 熔化池、澄清池与均化池
采用一阶梯型的 薄层浅区结构
手工 成型
均化部
成型部
电极 电极纯电熔
电与煤 气混熔
密布电极 均匀加热
机压 成型
• 硅酸盐的形成 • 玻璃的形成 • 玻璃注意的若干问题
• 玻璃牌号与炉型设计的对应 • 电极与耐火材料 • 电熔工艺与稳定 • 二次气泡 • 直流分量
AZS-33具有出色的抗污染性能,可有效防止结块,气泡及淅出。 用于熔炉的上部结构, 池壁,底砖,进料口等。
二氧化锡(SnO2)电极性能
二氧化锡(SnO2)电极广泛应用于高档光学玻璃的熔 炼以及电解铝行业,尤其适用于火石类玻璃、钡火石、 钡冕,以及重冕玻璃等的熔炼,且对玻璃不产生污染。
项目 体积密度(g/cm3)
玻璃的电熔化
• 玻璃电熔的原理 • 玻璃电熔化工艺 • 玻璃电熔化应注意的若干问题
主要内容
玻璃电熔的原理
• 玻璃高温熔化后变成导体,直接对玻璃通 电,使其产生焦耳热来达到不断熔化玻璃 的目的和所需的工艺温度。
• 熔化 • 澄清 • 均化 • 成型
玻璃电熔化工艺
冷炉顶
熔化部
澄清部
连续熔炉的结构