浮法玻璃缺陷种类分析及处理办法
浮法玻璃技术讲座
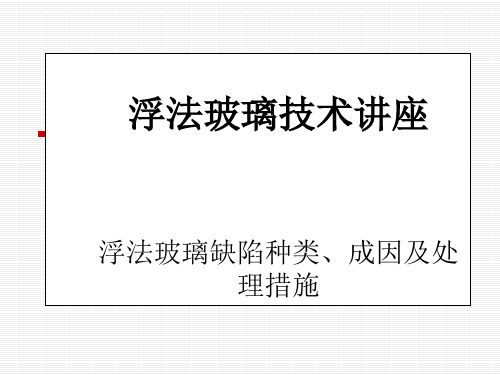
b. 麻点如压裂、硌伤等缺陷; c. 由锡槽滴落物产生的光畸变。
7.1.3 按显微结构可以分为两大类 (1)非晶态缺陷 气相缺陷(气泡); 玻璃相夹杂物(条纹和疖瘤); 由不均匀应力产生的缺陷; 硌伤和压裂。
(2)晶态缺陷 熔化残留物; 侵蚀的耐火材料; 玻璃熔体的析晶; 锡槽产生的上表面缺陷。
种原因都被排除的话,可认可这条原因)。
(3) 显微结构 结石中存在残余石英颗粒,周围可能伴随有羽 状鳞石英晶体。
(4) 应采取的措施 a. 严格控制硅砂的上、下限粒度,在混合机正常运转(如混合
机出故障,可排除以下其它产生原因)情况下,通过配合料均 匀度测定实验,给出合理的调合参数,以保证配合料具有良好 的均匀性。 b. 保证合理的配料参数及称量精度。 c. 加强熔化操作,保证在换火时,不切料,稳定料山及泡界线 位置。 d. 加强前区熔化,调整热负荷,建立合理的温度曲线,提高玻 璃液温度。 e. 冷修烤窑后及热修时,制定合理的操作方案,避免硅质泥料 落入窑中。
浮法玻璃技术讲座
浮法玻璃缺陷种类、成因及处 理措施
7.1 浮法玻璃缺陷的分类
7.1.1 按形成部位分成六大类
(1) 原料缺陷 由于各种原因,造成原料自身质量问题或外来
杂物引起的缺陷。
(2) 熔化缺陷 在熔化部,由于熔化不良引起的缺陷。
(3) 耐火材料缺陷 由于耐火材料的熔蚀和其它方式对耐火材
(4) 采取措施 a. 调整芒硝含率,控制芒硝加入量。 b. 结合芒硝、碳粉用量,恰当调整前区火焰气氛,保证芒硝在前区有
部分分解。
c. 适当提高热点温度,调整火焰气氛为中性至还原性。 d. 校核芒硝秤,确保称量的精度。 e. 校核输入的料方,如有错料及时扒出。 f. 检查芒硝、煤予混系统,确保正常运行。 g. 严禁在熔窑部位外加芒硝。 h. 及时清理流道、锡槽入口的冷凝物。 i. 控制料山泡界线的位置。 j. 控制燃料的硫含量,如果重油中含硫量过高,应对料方进行调整。 以上措施均无效时,调整芒硝与碳粉比率。
浮法玻璃退火产生的缺陷及控制

浮法玻璃中退火产生的缺陷及控制理工大学战营一、玻璃的退火玻璃退火的目的是减弱和防止玻璃制品中出现过大的剩余应力和光学不均匀性,稳定玻璃部的构造。
玻璃的退火可分成两个主要过程:一是玻璃中应力的减弱或消失,二是防止应力的重新产生。
玻璃中应力的减弱和消除是以松弛理论为根底的,所谓应力松弛是指材料在分子热运动的作用下使应力消散的过程,应力的松弛速度在很大程度上决定于玻璃所处的温度。
玻璃在加热或冷却过程中,由于其导热性较差,在其外表层和层之间必然产生温度梯度,因而在外层之间产生应力。
这种由于温度梯度存在而产生的应力称为温度应力或热应力,此种应力的大小,既取决于玻璃中的温度梯度,又与玻璃的热膨胀系数有关〔玻璃的化学成分决定玻璃的热膨胀系数〕。
热应力按其存在的特点可分为暂时应力和永久应力。
暂时应力,当玻璃受不均匀的温度变化时产生的热应力,随着温度差的存在而存在,随温度差的消失而消失,被称为暂时应力。
应力的建立和消失过程。
当制品冷却开场时,因为玻璃的外层冷却速度快,所以外部温度比部温度低,外层收缩大,而这时层温度较高,且力求阻碍外层收缩,这样造成玻璃外层产生应力,部产生压应力。
在应力过渡到压应力之间存在着中间层,其应力值为零。
当冷却接近完毕时,外层体积几乎不再收缩,但此时玻璃部仍有一定的温度,其体积力求收缩,此时造成外部受压应力,层受应力。
由此可见,在冷却完毕时,产生的应力恰好和冷却开场时产生的应力性质相反,两者可以得到局部抵消。
冷却全部完毕时,即当玻璃的外层温度和层温度趋向完全一致时,上述两种应力恰好抵消。
我们称这种应力为暂时应力。
永久应力,当温度消失时〔制品的外表和部温度均等于常温时〕,残留在玻璃中的热应力称为永久应力,又称为应力。
玻璃中永久应力的成因,是由于在高温的弹塑性阶段热应力松弛而形成的温度变形被“冻结〞下来的缘故。
当玻璃板逐渐冷却到室温均衡时,玻璃中残存的应力实际等于玻璃在高温阶段松弛掉的热弹应力,但方向相反。
玻璃缺陷的分类及形成
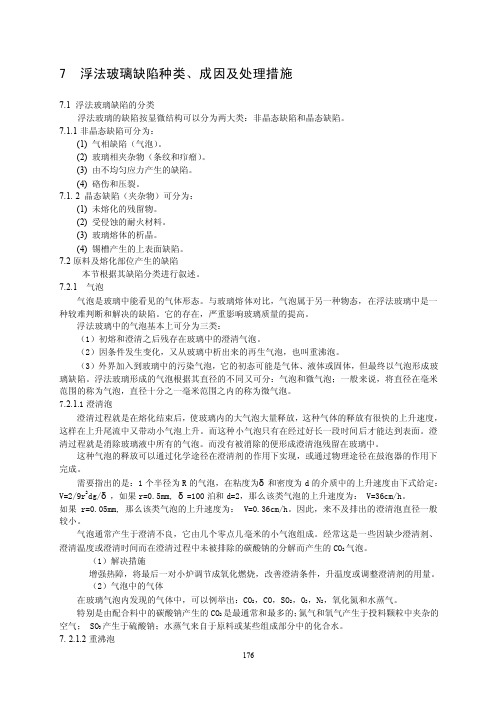
7 浮法玻璃缺陷种类、成因及处理措施7.1 浮法玻璃缺陷的分类浮法玻璃的缺陷按显微结构可以分为两大类:非晶态缺陷和晶态缺陷。
7.1.1非晶态缺陷可分为:(1) 气相缺陷(气泡)。
(2) 玻璃相夹杂物(条纹和疖瘤)。
(3) 由不均匀应力产生的缺陷。
(4) 硌伤和压裂。
7.1. 2 晶态缺陷(夹杂物)可分为:(1) 未熔化的残留物。
(2) 受侵蚀的耐火材料。
(3) 玻璃熔体的析晶。
(4) 锡槽产生的上表面缺陷。
7.2原料及熔化部位产生的缺陷本节根据其缺陷分类进行叙述。
7.2.1 气泡气泡是玻璃中能看见的气体形态。
与玻璃熔体对比,气泡属于另一种物态,在浮法玻璃中是一种较难判断和解决的缺陷。
它的存在,严重影响玻璃质量的提高。
浮法玻璃中的气泡基本上可分为三类:(1)初熔和澄清之后残存在玻璃中的澄清气泡。
(2)因条件发生变化,又从玻璃中析出来的再生气泡,也叫重沸泡。
(3)外界加入到玻璃中的污染气泡,它的初态可能是气体、液体或固体,但最终以气泡形成玻璃缺陷。
浮法玻璃形成的气泡根据其直径的不同又可分:气泡和微气泡;一般来说,将直径在毫米范围的称为气泡,直径十分之一毫米范围之内的称为微气泡。
7.2.1.1澄清泡澄清过程就是在熔化结束后,使玻璃内的大气泡大量释放,这种气体的释放有很快的上升速度,这样在上升尾流中又带动小气泡上升。
而这种小气泡只有在经过好长一段时间后才能达到表面。
澄清过程就是消除玻璃液中所有的气泡。
而没有被消除的便形成澄清泡残留在玻璃中。
这种气泡的释放可以通过化学途径在澄清剂的作用下实现,或通过物理途径在鼓泡器的作用下完成。
需要指出的是:1个半径为R的气泡,在粘度为δ和密度为d的介质中的上升速度由下式给定:V=2/9r2dg/δ,如果r=0.5mm, δ=100泊和d=2,那么该类气泡的上升速度为: V=36cm/h。
如果r=0.05mm, 那么该类气泡的上升速度为: V=0.36cm/h。
因此,来不及排出的澄清泡直径一般较小。
浮法玻璃成形缺陷及解决办法

浮法玻璃成形缺陷及解决办法熔融的玻璃经流道、流槽进入锡槽,在锡槽中成形后由过渡辊台进入退火窑,在这一过程中玻璃液(板)要与闸板、唇砖、锡液、拉边机、保护气体过渡辊台等直接接触,同时与锡槽水包、顶盖砖、底砖等密切相关,很容易形成与成形相关的各种缺陷,包括锡石、锡点(顶锡)、光畸变点(脱落物)、粘锡、虹彩、雾点、气泡等,除气泡之外的可统称为锡缺陷,这些成形缺陷严重制约着玻璃的质量等级与加工性能。
本文对其成因及防止措施作些探讨,以期有助于改善浮法玻璃质量。
1锡缺陷的成因分析1.1锡与锡槽中锡化合物的性质纯净的锡的熔点是232℃,沸点为2271℃,在600~1050℃的温度范围内锡具有较低的熔点和较高的沸点,较低的饱和蒸汽压,同时还具有较大的密度和容易还原的性质,以及锡液与玻璃液之间具有较大的浸润角(175°)几乎完全不浸润等性质,锡用来作为玻璃成形的良好载体。
氧化锡SnO2,密度6.7~7.0g/cm3,熔点2000℃,高温时的蒸汽压非常小,不溶于锡液,正常生产时在锡槽的温度条件下为固体,往往以浮渣形式出现在低温区的液面上,通常浮渣都聚集在靠近出口端。
如果氧化严重,浮渣会延伸很长,容易形成玻璃板下表面划伤。
氧化亚锡SnO,熔点为1040℃,沸点为1425℃,固体为蓝黑色粉末,能溶解于锡液中,SnO的分子一般为其聚合物(SnO)x形式。
在中性气氛中SnO只有在1040℃以上才是稳定的,1040℃以下会发生分解反应。
在锡槽的还原性气氛中SnO可以存在,它往往溶解于锡液中和以蒸汽形式存在于气氛中。
硫化亚锡SnS,密度5.27g/cm3,固体为蓝色晶体,熔点为865℃,沸点为1280℃,具有较大的蒸汽压,800℃时为81.3Pa,正常生产时,在高温区易挥发进入气氛,低温区易凝聚滴落。
1.2锡槽中的硫、氧污染循环氧的污染主要来源于气氛中的微量氧和水蒸汽以及从锡槽缝隙漏入和扩散的氧。
在锡槽工况下,它们使锡氧化成SnO和SnO2浮渣,SnO溶解于锡液和挥发进入气氛,并在顶盖、水包处冷凝、聚集而落到玻璃表面。
浮法玻璃几种结石缺陷的处理方法
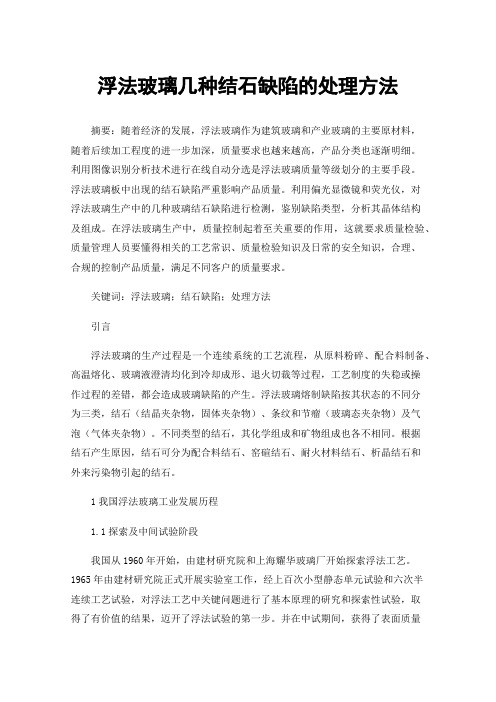
浮法玻璃几种结石缺陷的处理方法摘要:随着经济的发展,浮法玻璃作为建筑玻璃和产业玻璃的主要原材料,随着后续加工程度的进一步加深,质量要求也越来越高,产品分类也逐渐明细。
利用图像识别分析技术进行在线自动分选是浮法玻璃质量等级划分的主要手段。
浮法玻璃板中出现的结石缺陷严重影响产品质量。
利用偏光显微镜和荧光仪,对浮法玻璃生产中的几种玻璃结石缺陷进行检测,鉴别缺陷类型,分析其晶体结构及组成。
在浮法玻璃生产中,质量控制起着至关重要的作用,这就要求质量检验、质量管理人员要懂得相关的工艺常识、质量检验知识及日常的安全知识,合理、合规的控制产品质量,满足不同客户的质量要求。
关键词:浮法玻璃;结石缺陷;处理方法引言浮法玻璃的生产过程是一个连续系统的工艺流程,从原料粉碎、配合料制备、高温熔化、玻璃液澄清均化到冷却成形、退火切裁等过程,工艺制度的失稳或操作过程的差错,都会造成玻璃缺陷的产生。
浮法玻璃熔制缺陷按其状态的不同分为三类,结石(结晶夹杂物,固体夹杂物)、条纹和节瘤(玻璃态夹杂物)及气泡(气体夹杂物)。
不同类型的结石,其化学组成和矿物组成也各不相同。
根据结石产生原因,结石可分为配合料结石、窑碹结石、耐火材料结石、析晶结石和外来污染物引起的结石。
1我国浮法玻璃工业发展历程1.1探索及中间试验阶段我国从1960年开始,由建材研究院和上海耀华玻璃厂开始探索浮法工艺。
1965年由建材研究院正式开展实验室工作,经上百次小型静态单元试验和六次半连续工艺试验,对浮法工艺中关键问题进行了基本原理的研究和探索性试验,取得了有价值的结果,迈开了浮法试验的第一步。
并在中试期间,获得了表面质量好的浮法玻璃,这是我国浮法发展史中一个重大突破。
期间,还试验了锡槽槽底材质、流槽安装位置、拉边机拉薄试验等一系列内容,为工业性试验提供了比较全面的工艺根据。
当时的国家科委、计委和经委,对浮法工艺的研究、试生产,给予了高度重视和支持。
在1966年试验室工作取得结果后,1967年12月,国家科委批准了浮法中间试验,投资180万元,使浮法研究能及时地进入中间试验阶段。
玻璃缺陷的分类及形成

7 浮法玻璃缺陷种类、成因及处理措施7.1 浮法玻璃缺陷的分类浮法玻璃的缺陷按显微结构可以分为两大类:非晶态缺陷和晶态缺陷。
7.1.1非晶态缺陷可分为:(1) 气相缺陷(气泡)。
(2) 玻璃相夹杂物(条纹和疖瘤)。
(3) 由不均匀应力产生的缺陷。
(4) 硌伤和压裂。
7.1. 2 晶态缺陷(夹杂物)可分为:(1) 未熔化的残留物。
(2) 受侵蚀的耐火材料。
(3) 玻璃熔体的析晶。
(4) 锡槽产生的上表面缺陷。
7.2原料及熔化部位产生的缺陷本节根据其缺陷分类进行叙述。
7.2.1 气泡气泡是玻璃中能看见的气体形态。
与玻璃熔体对比,气泡属于另一种物态,在浮法玻璃中是一种较难判断和解决的缺陷。
它的存在,严重影响玻璃质量的提高。
浮法玻璃中的气泡基本上可分为三类:(1)初熔和澄清之后残存在玻璃中的澄清气泡。
(2)因条件发生变化,又从玻璃中析出来的再生气泡,也叫重沸泡。
(3)外界加入到玻璃中的污染气泡,它的初态可能是气体、液体或固体,但最终以气泡形成玻璃缺陷。
浮法玻璃形成的气泡根据其直径的不同又可分:气泡和微气泡;一般来说,将直径在毫米范围的称为气泡,直径十分之一毫米范围之内的称为微气泡。
7.2.1.1澄清泡澄清过程就是在熔化结束后,使玻璃内的大气泡大量释放,这种气体的释放有很快的上升速度,这样在上升尾流中又带动小气泡上升。
而这种小气泡只有在经过好长一段时间后才能达到表面。
澄清过程就是消除玻璃液中所有的气泡。
而没有被消除的便形成澄清泡残留在玻璃中。
这种气泡的释放可以通过化学途径在澄清剂的作用下实现,或通过物理途径在鼓泡器的作用下完成。
需要指出的是:1个半径为R的气泡,在粘度为δ和密度为d的介质中的上升速度由下式给定:V=2/9r2dg/δ,如果r=0.5mm, δ=100泊和d=2,那么该类气泡的上升速度为: V=36cm/h。
如果r=0.05mm, 那么该类气泡的上升速度为: V=0.36cm/h。
因此,来不及排出的澄清泡直径一般较小。
7--浮法玻璃缺陷种类
(4) 采取措施 a. 严格控制原料质量,杜绝含铝硅质、高铝质夹杂物的引入。 b. 严格控制钾长石水份。 c. 严格控制钾长石上、下限颗粒组成。 d. 采取措施,均匀调合。 e. 采取措施,保证玻璃液的对流、液面、料堆、温度稳定。 f. 严禁液面的大起大落,减轻对池壁的严重冲刷。 g. 采用优质α-β刚玉砖。 h. 若玻璃中有大的夹杂物,应切除后再进入碎玻璃循环系统。
e. 定期处理后山墙的挂帘子。 f. 提高重油质量,降低水份含量,稳定风量及窑压。
7.2.2.3 霞石 (1) 外观 为白色颗粒结石,有时在疖瘤内呈半透
明析晶状。
(2) 显微结构 显微镜单偏光下呈羽毛状或阶梯状, 显微镜正交光下,有鲜艳的干涉色。
(3) 可能产生的原因 a. 铝硅质原料中(钾长石)有大颗粒。 b. 钾长石水份偏大,细粉过多造成结团。 c. 原料加工、运输、贮存的过程中引入了铝硅质、
f. 重油含硫量过高,水分过大或助燃风量过大,对碹砖的冲击 及侵蚀。
(4) 采取措施 a. 减少熔窑前区粉料的飞散及配合料组成的挥发。 b. 调整火焰角度,减少火焰对碹顶的上扬烧损。 c. 在不影响熔化的前题下,可考虑适当降低熔窑温
度。
d. 在满足澄清的前题下,尽量减少澄清剂芒硝的 用量。
个颗粒的聚合体。结石周围有较宽的扩散层, 在窑内停留时间长的结石,表面瓷化,周边 与玻璃界限不很清晰。
未熔石英
硅砂富集
(2)可能产生原因 a. 硅砂颗粒过大,形成的未熔石英; b. 配合料调合不均匀,局部硅砂富集形成的; c. 配合料输送及窑头料仓贮存过程中的分层; d. 硅砂细粉过多形成的料蛋; e. 助熔剂(Na2CO3 、Na2SO4)过少; f. 跑料或边部切料; g. 熔化温度过低(主要是玻璃液温度); h. 碹顶硅质泥料掉入窑中进入玻璃液。(若以上7
浮法玻璃几种结石缺陷的处理方法
0引言浮法玻璃熔制缺陷按其状态的不同分为三类,结石(结晶夹杂物,固体夹杂物)、条纹和节瘤(玻璃态夹杂物)及气泡(气体夹杂物)。
不同类型的结石,其化学组成和矿物组成也各不相同。
根据结石产生原因,结石可分为配合料结石、窑碹结石、耐火材料结石、析晶结石和外来污染物引起的结石。
本文对三种比较典型的结石缺陷进行分析、化验,提出处理措施。
1玻璃缺陷样品取样分析针对三类缺陷各取样品5个,样品A和样品B类缺陷全位于玻璃板上表面,C类缺陷4个位于玻璃板上表面,1个位于玻璃板中偏上位置,C类缺陷尺寸多为1.0 mm以上缺陷,形状大部分是长条状、少量圆形、规则三角形,尺寸多为1~5 mm;B类缺陷位于玻璃带一侧边部位置,A类、C类缺陷位置不固定。
(1)偏光显微镜分析在偏光显微镜下观察缺陷样品的晶体结构,如图1所示。
A类样品为熔融鳞石英(低温区),B类样品为鳞石英、方石英,C类样品为刚玉结石,部分形成单晶结石、伴有霞石。
图1偏光显微镜下的玻璃缺陷晶体结构(2)荧光成分分析利用金相切割机将缺陷样品切割成尽量小,尽可能去掉没有缺陷的玻璃,利用玛瑙研钵研磨,按照荧光制样标准制取样品1;取同量的正常玻璃用同样的方法制取对比样品2,利用荧光仪测量的数据见表1。
通过对比,可判定缺陷为铝质缺陷。
2缺陷产生原因分析(1)样品A熔融鳞石英缺陷熔融石英结石缺陷的主要来源为石英质流量闸板,其次为高温熔蚀的碹顶硅砖。
流量闸板形成结石的原因有两个,一是持续处于高温环境下的流量闸板发生自身析晶,在受到温度反复波动后剥落进入玻璃液形成结石;二是闸板受到高温熔蚀的剥落物进入玻璃液形成结石。
通过窑炉检查结合窑内拍照发现卡脖靠近冷却部后半部分碹顶有部分区域存在剥落现象,抽出空间冷却水包清理,发现水包上表面凝结物里有一定数量的白色颗粒,与样品A内缺陷相同,偏光镜观察晶相为熔融鳞石英,分析为该区域穿有空间冷却水包,距离碹顶较近、且清理频繁,造成受侵蚀的硅砖表层剥落形成缺陷。
浮法玻璃生产中玻璃的缺陷及处理
程 技术 大 学 ,2012.
4 总 结
由于地质条件复杂 、软弱 围岩 的变化较为频繁等方面 因素 的影 响, 煤矿基建软弱 围岩 的施工过程 中仍然存在 很多的 问题,给施工单位造成 了一定的人员损失、财产损失或者工期延误等 。为了保证施 工安全 ,相关
『41何富连,王宁博,魏 臻 ,卫文彬 ,许华威.采动剧烈影 响软弱 围岩巷 道失 稳机理及支护『J].煤矿 开采 ,2015(05). f51赵 勇,刘建友 ,田四明.深埋隧道软弱 围岩支护体系受力特征 的试 验研 究fJ].岩石力学与工程学报 ,2011(O8).
(8)其他疵滴 。①导 向挡板斑点:上表面细微的斑 点,在玻璃带边缘 。 ② 溅疵滴:一个元素锡 中心核被 一个含 有很 细元素锡粒子圈 围绕 出现 于锡槽 的较热区域。③褐色疵点:很大的褐色滴,出现 于边缘 部位与拉 引 的玻璃 带成角度 。
(9)冷玻璃“拉 引 ”线道 t拉 引线道是ห้องสมุดไป่ตู้出现 在玻璃底 表面 的连 续或 间 断的细小划痕。线条平行于玻璃流动 的方 向。
.
.
现 SnO:。它与顶部斑点有所 不同,是 结晶体 的形状 。 (2)上表面 细气泡 :该疵 点在上表 面 内出现 ,气泡直 径一般 不超 过
0.1mm,在镀银 和边部照 光检查 时较容 易发现 。
(3)幕状伤痕 :以连续、细微擦伤或伤 痕出现在 玻璃带上 。
(4)上表面斑 点:疵 点表现 为一种元素锡 的中心核加上一个 反应 圈,
该疵点可在涂银样板或在检查架上或边部照光时看出疵点处的玻璃表面有严重的痕伤通常情况下疵点是在比锡渣冷的区域形成的但在有的情况下尤其是生产厚玻璃的时候退火窑热端的辊道同样会带来该疵点疵点内有极少量的锡渣等物质
浮法玻璃几种结石缺陷的处理方法
浮法玻璃几种结石缺陷的处理方法摘要:随着社会的进步,浮法玻璃生产中常出现结石、气泡和条纹等缺陷。
其中结石缺陷常导致光散射,使玻璃透光能力降低,还因结石与玻璃体膨胀系数的差异,导致玻璃较大内应力而降低玻璃强度和热稳定性。
玻璃产品均需要分析研究结石成因和来源,以保证较高的成品率和市场竞争力。
关键词:浮法玻璃;几种结石;缺陷;处理方法引言浮法玻璃熔制缺陷按其状态的不同分为三类,结石(结晶夹杂物,固体夹杂物)、条纹和节瘤(玻璃态夹杂物)及气泡(气体夹杂物)。
不同类型的结石,其化学组成和矿物组成也各不相同。
根据结石产生原因,结石可分为配合料结石、窑碹结石、耐火材料结石、析晶结石和外来污染物引起的结石。
1平板玻璃工业发展趋势1.1环保、智能的建筑玻璃有极大的发展空间用于建筑物的特种玻璃将在建筑物实现节能减碳以及零碳建筑、负碳建筑中发挥强大作用。
如低辐射膜、自洁净膜等各种功能的镀膜玻璃、涂膜玻璃等的广泛应用;用于光敏、可切换或电致变色玻璃的智能镜子和高度绝缘的玻璃窗,用于保密区域空间的电屏蔽镀膜玻璃等。
1.2新能源玻璃将大行其道玻璃在新能源方面的作用越来越明显,如光伏压延玻璃、光伏超白浮法玻璃以及发电玻璃,已成为新能源的基础材料,是光伏产业、光热产业不可或缺的材料之一,并在BIPV中大行其道。
2电熔刚玉砖在浮法玻璃熔窑中的应用池底和池壁都是与玻璃液直接接触的部位。
对所有直接接触玻璃液的部位来说,耐火材料最重要的性能就是抗侵蚀性能,即要求耐火材料与玻璃液之间不发生化学反应。
从三元相图上分析在作业温度范围内没有共熔点,并且要求耐火材料与玻璃液间的界面层相对稳定,即耐火材料虽处于被侵蚀状态中,但其表面仍是完整的,不会脱落到玻璃液中产生结石等缺陷。
近年来考核与玻璃液直接接触的电熔耐火材料的质量指标时,除化学成分、理化指标、矿物组成外,还必须考核以下三个指标:抗玻璃侵蚀指数、析出气泡指数与析出结晶指数。
随着对玻璃质量要求越高、熔窑的生产能力越大,电熔砖的使用范围就越广。
- 1、下载文档前请自行甄别文档内容的完整性,平台不提供额外的编辑、内容补充、找答案等附加服务。
- 2、"仅部分预览"的文档,不可在线预览部分如存在完整性等问题,可反馈申请退款(可完整预览的文档不适用该条件!)。
- 3、如文档侵犯您的权益,请联系客服反馈,我们会尽快为您处理(人工客服工作时间:9:00-18:30)。
7.2.2.3 霞石 (1) 外观 为白色颗粒结石,有时在疖瘤内呈半透 明析晶状。 (2) 显微结构 显微镜单偏光下呈羽毛状或阶梯状, 显微镜正交光下,有鲜艳的干涉色。 (3) 可能产生的原因 a. 铝硅质原料中(钾长石)有大颗粒。 b. 钾长石水份偏大,细粉过多造成结团。 c. 原料加工、运输、贮存的过程中引入了铝硅质、 高铝质夹杂,如:粘土质、莫来石、煤矸石、刚玉 石及耐火砖砖屑等。
(4) 采取措施 a. 配合料混合均匀 b. 检查石灰石秤和计算机料方输入,保证准确无 误。 c. 检查石灰石颗粒,是否有大颗粒和细粉过多问题, 吸水的石灰石要晾干再用。 e. 保证玻璃液均化良好,避免局部富钙。 f. 避免来自冷却部边部及后山墙死角处的凉玻璃液 进入成型流,若有,采取措施处理。 g. 保持玻璃液有合理的冷却降温制度。
7.1.3 按显微结构可以分为两大类 (1)非晶态缺陷 气相缺陷(气泡); 玻璃相夹杂物(条纹和疖瘤); 由不均匀应力产生的缺陷; 硌伤和压裂。
(2)晶态缺陷 熔化残留物; 侵蚀的耐火材料; 玻璃熔体的析晶; 锡槽产生的上表面缺陷。
7.2 原料及熔化过程产生的玻璃缺陷及 处理
(3)玻璃板下表面的缺陷 一种类似于玻璃上表面的如气泡(闭口泡)、结石 这样的缺陷; 由锡或裂纹产生的一种下表面缺陷; 一种产生于流道流槽、唇砖或锡槽的下表面开口泡。 光学性质缺陷 a. 玻璃缺少化学均匀性而产生的光学变形(光学 变形角低); b. 麻点如压裂、硌伤等缺陷; c. 由锡槽滴落物产生的光畸变。
①夹杂物(固体夹杂缺陷); ②气泡(气体夹杂缺陷); ③光学变形(非晶体缺陷)。 本部分根据缺陷的类别针对常见缺陷的外观、 产生原因、解决措施,逐一论述。
7.2.1 夹杂物
7.2.2.1 未熔石英颗粒(残余石英) (1) 外观 大多在玻璃板的上表面,呈白色小粒状或多 个颗粒的聚合体。结石周围有较宽的扩散层, 在窑内停留时间长的结石,表面瓷化,周边 与玻璃界限不很清晰。
(3) 显微结构 结石中存在残余石英颗粒,周围可能伴随有羽 状鳞石英晶体。 (4) 应采取的措施 a. 严格控制硅砂的上、下限粒度,在混合机正常运转(如混合 机出故障,可排除以下其它产生原因)情况下,通过配合料均 匀度测定实验,给出合理的调合参数,以保证配合料具有良好 的均匀性。 b. 保证合理的配料参数及称量精度。 c. 加强熔化操作,保证在换火时,不切料,稳定料山及泡界线 位置。 d. 加强前区熔化,调整热负荷,建立合理的温度曲线,提高玻 璃液温度。 e. 冷修烤窑后及热修时,制定合理的操作方案,避免硅质泥料 落入窑中。
(4) 采取措施 a. 调整芒硝含率,控制芒硝加入量。 b. 结合芒硝、碳粉用量,恰当调整前区火焰气氛,保证芒硝在前区有 部分分解。 c. 适当提高热点温度,调整火焰气氛为中性至还原性。 d. 校核芒硝秤,确保称量的精度。 e. 校核输入的料方,如有错料及时扒出。 f. 检查芒硝、煤予混系统,确保正常运行。 g. 严禁在熔窑部位外加芒硝。 h. 及时清理流道、锡槽入口的冷凝物。 i. 控制料山泡界线的位置。 j. 控制燃料的硫含量,如果重油中含硫量过高,应对料方进行调整。 以上措施均无效时,调整芒硝与碳粉比率。
7 浮法玻璃缺陷种类、成因及处 理措施
7.1 浮法玻璃缺陷的分类
7.1.1 按形成部位分成六大类 (1) 原料缺陷 由于各种原因,造成原料自身质量问题或外来 杂物引起的缺陷。 (2) 熔化缺陷 在熔化部,由于熔化不良引起的缺陷。 (3) 耐火材料缺陷 由于耐火材料的熔蚀和其它方式对耐火材 料的侵蚀引起的缺陷。 (4) 成型缺陷 在成型部位形成的缺陷。 (5) 退火缺陷 退火过程中,由于退火制度不合适或事故造成 的缺陷。 (6) 冷玻璃加工和储存缺陷 玻璃切裁、包装和储存过程中形 成的缺陷
7.2.2.4 硅质析晶(方石英,鳞石英) (1) 外观 在玻璃中呈白色、乳白色半透明 的夹杂物,有时呈颗粒、有时成串、有时星 星点点在玻璃板面出现,严重时可布满整个 玻璃板。 (2) 显微结构 晶体呈骨架状方石英,部分 有树枝状鳞石英析出。
磷石英析晶×200
方石英析晶×100
(3) 产生原因 a. 配合料混合不均,产生富硅相。 b. 渗出的耐火材料玻璃相进入玻璃液。 c. 配合料分层(在输送及窑头料仓分层), 造成硅砂与助熔剂分离。 d. 硅质耐火材料结石二次入窑,再次熔化 后形成局部高硅相。
(4) 应采取的措施或补救方法 a. 改善配合料的均匀性。 b. 严格控制白云石粉料上下限粒度。 c. 保证白云石加入量正确。 d. 避免边部及死角处凉玻璃液进入成型流。 e. 保持玻璃液有合理的冷却降温制度。
7.2.2.7 芒硝结石 (1) 外观 该类泡大多呈枣核形状,里面充 满白色晶体,在玻璃板的上表面,泡周围有 波纹。有的呈不规则颗粒状,浮在玻璃上表 面,呈白色或乳白色,颗粒旁有波纹。 (2) 显微结构 呈半透明的云雾状或裂纹状, 显微镜下正交光下呈鲜艳的干涉色,无光性。
(4) 采取措施 a. 采取必要措施,保证配合料的均匀度达 到要求。 b. 保证配合料的水分、温度,减少配合料 的分层现象。 c. 稳定熔化温度制度,减少耐火材料玻璃相 的渗出。 d. 剔除玻璃带中的大结石夹杂物。
7.2.2.5 硅灰石 (1) 外观 在玻璃板中呈毛虫状、线团状、 半透明析晶体杂物。 (2) 显微结构 呈棒状、板状、放射状或薄 的柱状晶体。
7.2.3 气泡
7.2.3.1 澄清泡 (1) 外观 泡在玻璃板面分布均匀,泡径大 小从0.1mm至1.0mm,小泡呈圆形,大泡 呈椭圆形,多分布在玻璃板中。 (2) 显微结构 空泡,泡壁无凝结物。气泡 成分分析泡内N2、CO2气体较多。
(3) 产生原因 a. 澄清剂加入不足,造成澄清不良。 b. 热点气氛偏氧化,使 SO3无法排出,不能充分 发挥澄清剂作用。 c. 热障(热点形成的玻璃液流动障碍)不充分。 d. 熔窑最后一对小炉呈强还原性气氛运行。 e. 熔化不良,造成泡界线后移,澄清区太短。 f. 熔化温度过低。
7.2.2.6 透灰石 (1) 外观 透灰石外观同硅灰石 (2) 显微结构 晶体外形与硅灰石相似,呈 束状、放射状。
透灰石析晶×200
透灰石析晶×100
(3) 产生原因: a. 配合料中白云石混合不均。 b. 白云石粉料含有大颗粒或细粉过多结团。 c. 白云石秤故障或料方错误造成白云石多加。 d. 死角凉玻璃液进入成型流。 e. 玻璃液的冷却降温制度不合理。
(4) 采取措施 a. 严格控制原料质量,杜绝含铝硅质、高铝质夹杂物的引入。 b. 严格控制钾长石水份。 c. 严格控制钾长石上、下限颗粒组成。 d. 采取措施,均匀调合。 e. 采取措施,保证玻璃液的对流、液面、料堆、温度稳定。 f. 严禁液面的大起大落,减轻对池壁的严重冲刷。 g. 采用优质α-β刚玉砖。 h. 若玻璃中有大的夹杂物,应切除后再进入碎玻璃循环系统。
7.1.2 按在玻璃中的位置分成三大类 (1)玻璃板中的缺陷 这是一种由熔化或配合料引起的缺陷,通常 以固体夹杂物(结石)和气体夹杂物(气泡) 的形式出现。
(2)玻璃板上表面的缺陷 结石——这是一种碹顶滴落物(液滴、粉尘) 所造成的缺陷; 上表面气泡——这种缺陷往往是闸板部位形 成的闸板泡,一般泡径较多呈矛头状双晶, 单偏光下,呈浅黄色,突起较低,正交光下,有灰 白、浅黄的干涉色。
(3) 产生原因 熔化部碹顶硅砖的剥落物,产生部位从前区L型 吊墙至熔化部后山墙都有。产生部位不同,其化学组成及物相 组成都有所不同。 a. 产生于前区L型吊墙。(晶型排列不整齐)。 b. 产生于前区碹顶的中部。(晶体排列整齐,呈玉黍状或团粒 状) c. 产生于前区碹顶边部(晶型排列如L型吊墙)。 d. 产生于热点后部碹顶(晶型排列整齐)这个部位是温度相对 较低,碱性组分、芒硝分解产物易在此处凝聚,侵蚀较严重。 e. 产生于熔化部后山墙(晶体中含有硫元素),呈钟乳石状的 熔融凝聚物,可能有残砖存在。 f. 重油含硫量过高,水分过大或助燃风量过大,对碹砖的冲击 及侵蚀。
未熔石英
硅砂富集
(2)可能产生原因 a. 硅砂颗粒过大,形成的未熔石英; b. 配合料调合不均匀,局部硅砂富集形成的; c. 配合料输送及窑头料仓贮存过程中的分层; d. 硅砂细粉过多形成的料蛋; e. 助熔剂(Na2CO3 、Na2SO4)过少; f. 跑料或边部切料; g. 熔化温度过低(主要是玻璃液温度); h. 碹顶硅质泥料掉入窑中进入玻璃液。(若以上7 种原因都被排除的话,可认可这条原因)。
(4) 采取措施 a. 减少熔窑前区粉料的飞散及配合料组成的挥发。 b. 调整火焰角度,减少火焰对碹顶的上扬烧损。 c. 在不影响熔化的前题下,可考虑适当降低熔窑温 度。 d. 在满足澄清的前题下,尽量减少澄清剂芒硝的 用量。 e. 定期处理后山墙的挂帘子。 f. 提高重油质量,降低水份含量,稳定风量及窑压。
7.2.2.2 碹滴 (1) 外观 是一些尺寸大小不等的不透明的或半透 明的结石,颜色为白色、灰色、深色、浅黑色等。 结石中央呈原砖状,边部有溶解蚀变和析晶。结石 旁波及较大,常常还伴随有裂纹。 (2) 显微结构 呈方石英,鳞石英晶体,晶体粗大 的鳞石英多呈矛头状双晶,单偏光下,呈浅黄色, 突起较低,正交光下,有灰白、浅黄的干涉色。
×40
×40 正交光下
(3) 产生原因 a. 芒硝含率过高,熔化时在玻璃液的表面产生过量的硝水。 b. 前区火焰调整不合适,火焰氧化性过强,使碳粉提前烧掉,造成芒 硝过量。 c. 热点温度低,空间气氛氧化性强,使熔入的芒硝来不及分解排出, 闷在玻璃液中。 d. 芒硝称失灵或料方输错造成芒硝加入过量。 e. 芒硝、煤予混系统出题造成芒硝在配合料中局部富集。 f. 错误操作,在熔窑的某部位外加芒硝(如大水管处)。 g. 小炉口、流道锡槽入口及搅拌等较凉处凝结的芒硝落入成型流。 (这些部位落入的芒硝冷凝物形态往往无规则)。 h. 碳粉含率偏低。 i. 熔窑内料山位置不合理。 j. 重油中的硫含量过高。