材料成型设备实验报告
生产实习报告材料成型及控制工程

生产实习报告材料成型及控制工程材料成型及控制工程是我在实习期间所从事的岗位,主要负责材料的加工和成型过程中的工艺控制。
以下是我对这段实习经历的总结和报告。
在实习初期,我首先了解了材料成型及控制工程的背景知识,包括材料的性质和加工方式,以及各种成型工艺和控制方法。
通过学习相关理论和实例,我对材料成型及控制工程的原理和应用有了初步的了解。
随后,我参与了具体的生产工作,包括材料选择、成型工艺方案的制定和实施等。
我学习了不同材料的特性和应用范围,通过与工程师的交流和观察,我了解了材料在不同工艺中的表现和特点,以及成型过程中可能出现的问题和风险。
在实习期间,我有机会参与了几个项目的材料选择和工艺方案的制定,也亲自操作过一些成型设备和机器。
在实际操作中,我学会了如何调整材料和工艺参数,以达到预期的成型效果。
在控制材料成型过程中,我学会了使用仪器仪表进行数据记录和分析,以便对工艺参数进行调整和优化。
我也学会了根据产品要求进行相关的测试和检测,以确保产品的质量和性能符合标准。
通过这些实践,我进一步理解了材料成型及控制工程的重要性和挑战。
在实习期末,我参与了一个项目的验收工作。
由于之前的实习经历和知识储备,我能够快速判断出材料加工过程中出现的问题,并提出相应的解决方案。
我与团队合作,完成了项目的验收任务,并得到了领导的认可和表扬。
通过这段实习经历,我深刻体会到了材料成型及控制工程的复杂性和重要性。
材料成型的每个环节和参数都需要精确控制,以确保产品的质量和性能。
同时,材料成型也需要多方面的知识和技能,包括材料的性质和选择、工艺的制定和优化、设备的操作和维护等。
这些知识和技能对于我未来在材料领域的发展将起到重要的支持和指导作用。
通过这段实习经历,我进一步树立了学习的决心和信心,我将进一步学习和掌握相关的知识和技能,以便在未来能够在材料成型及控制工程方面做出更大的贡献。
我也将时刻保持对新技术和新工艺的关注,以保持自身的竞争力和能力。
挤出成型实验报告

挤出成型实验报告挤出成型实验报告一、引言挤出成型是一种常见的塑料加工方法,通过将熔融状态的塑料材料挤出模具,使其冷却后得到所需形状的制品。
本实验旨在通过挤出成型实验,研究挤出过程中的工艺参数对制品质量的影响,并探讨挤出成型的优化方法。
二、实验材料与设备1. 实验材料:聚丙烯颗粒2. 实验设备:挤出机、模具、冷却装置、计时器、天平等三、实验步骤1. 准备工作:将挤出机清洗干净,并预热至适宜的温度。
2. 将聚丙烯颗粒加入挤出机的料斗中,并调整挤出机的温度、转速和压力等参数。
3. 打开挤出机,开始挤出成型。
同时,启动计时器记录挤出时间。
4. 将挤出的聚丙烯制品送入冷却装置进行冷却。
5. 将冷却后的制品取出,并进行质量检测。
四、实验结果与分析在实验过程中,我们分别调整了挤出机的温度、转速和压力等参数,并记录了挤出时间和制品的质量。
1. 温度对制品质量的影响我们分别设置了三组不同的挤出温度:低温组(180℃)、中温组(200℃)和高温组(220℃)。
实验结果显示,随着挤出温度的升高,制品的表面光滑度和尺寸一致性均有所提高。
这是因为较高的温度可以使聚丙烯颗粒更容易熔化,并减少挤出过程中的内部应力。
2. 转速对制品质量的影响我们分别设置了三组不同的挤出转速:低速组(20 rpm)、中速组(40 rpm)和高速组(60 rpm)。
实验结果显示,随着挤出转速的增加,制品的密度和强度逐渐提高。
这是因为较高的转速可以增加聚丙烯颗粒的熔融程度,并促使其更好地填充模具。
3. 压力对制品质量的影响我们分别设置了三组不同的挤出压力:低压组(5 MPa)、中压组(10 MPa)和高压组(15 MPa)。
实验结果显示,随着挤出压力的增加,制品的密度和尺寸一致性均有所提高。
这是因为较高的压力可以使聚丙烯颗粒更紧密地填充模具,并减少挤出过程中的气泡和缺陷。
五、实验总结与展望通过本次挤出成型实验,我们对挤出过程中的工艺参数对制品质量的影响有了更深入的了解。
材料成型及控制工程专业综合实验报告

材料成型及控制工程专业综合实验报告实验报告:材料成型及控制工程专业综合实验一、实验目的:1.掌握材料成型及控制工程的基本原理;2.学习并了解材料成型及控制工程的实际应用;3.提高实验操作技巧和实验数据分析能力。
二、实验仪器和材料:1.数控铣床:用于完成加工实验;2.数控线切割机:用于完成线切割实验;3.材料样品:使用铝合金和塑料材料。
三、实验内容:1.数控铣床实验:a.将铝合金材料夹在数控铣床上,设定加工参数;b.进行铣削操作,实现铝合金材料的加工成型;c.调整加工参数,观察对加工结果的影响。
2.数控线切割机实验:a.将塑料材料放置在数控线切割机上,设定切割参数;b.进行线切割操作,实现塑料材料的切割成型;c.调整切割参数,观察对切割结果的影响。
四、实验过程:1.数控铣床实验:a.将铝合金材料夹在数控铣床上,设定加工参数,包括切削速度、进给速度、转速等;b.打开数控铣床电源,进行加工操作,观察铝合金材料的加工成型情况;c.根据加工结果,调整加工参数,观察对加工结果的影响。
2.数控线切割机实验:a.将塑料材料放置在数控线切割机上,设定切割参数,包括切割速度、电弧电压、电弧电流等;b.打开数控线切割机电源,进行切割操作,观察塑料材料的切割成型情况;c.根据切割结果,调整切割参数,观察对切割结果的影响。
五、实验结果及分析:1.数控铣床实验结果:a.观察到不同的加工参数对铝合金的加工效果有明显影响,例如切削速度过快会导致切削不够充分,切削速度过慢则会导致切削效果不理想;b.通过不断调整加工参数,得以实现较为满意的加工成型结果。
2.数控线切割机实验结果:a.观察到不同的切割参数对塑料材料的切割效果有明显影响,例如切割速度过快可能导致切割不完全,切割速度过慢则可能引起材料熔化;b.通过不断调整切割参数,得以实现较为满意的切割成型结果。
六、实验总结:材料成型及控制工程是一门综合性很强的工程学科,通过本次实验,我们了解到了材料成型和控制工程的基本原理和实际应用情况。
《材料成型综合实验》3D打印实验报告

《材料成型综合实验》3D打印实验报告一、实验目的1、掌握快速成型加工原理、方法及在模具加工中的应用;2、了解快速成型机床的组成、工作原理和操作方法。
二、实验仪器HTS-400pl快速成型机、树脂丝材、计算机等三、实验原理3D打印即快速成型技术的一种,又称增材制造,它是一种以数字模型文件为基础,运用粉未状金属或塑料等可粘合材料,通过逐层打印的方式来构造物体的技术。
RP技术基本原理:离散—堆积(叠加)。
3D打印技术与激光成型技术基本上是一样的。
简单来说,就是通过采用分层加工、迭加成形,逐层增加材料来生成3D实体。
称它为“打印机”的原因是参照了其技术原理,3D打印机的分层加工过程与喷墨打印机十分相似。
首先是运用计算机设计出所需零件的三维模型,然后再根据工艺需求,按照一定规律将该模型离散为一系列有序的单位,通常在Z向将其按照一定的厚度进行离散,把原来的三维CAD模型变成一系列的层片;然后再根据每个层片的轮廓信息,输入加工参数,然后系统后自动生成数控代码;最后由成型一系列层片并自动将它们连接起来,最后得到一个三维物理实体。
四、实验过程基本过程如下:对要打印的零件进行三维建模,绘制三维图形,保存STL通用格式。
用3D 打印软件打开保存的STL格式的零件,在3D打印软件中设置相关打印参数,生成路径。
将3D软件生成的GSD格式用插卡的形式放在打印机里。
随后启动打印机即可。
实验的详细过程如下:首先进行的三维模型构建经常使用的软件有Pro/E、UG、SolidWorks、激光扫描、CT断层扫描等。
然后要对三维模型做近似处理,也就是用三角形平面来逼近原来的模型(STL文件)。
近似处理后进行切片处理,即对加工方向(Z方向)进行分层(间隔一般取0.05m--0.5mm,常用0.1mm )。
之后进行打磨、抛光、涂挂、烧结等后处理步骤。
最后成型加工。
成型头(激光头或喷头)按各截面轮廓信息扫描。
其中分解(离散)过程由计算机完成,组合(堆积)过程由成型机完成,后处理过程中的结构与性能的加强由其他辅助设备完成。
材料成型实验报告
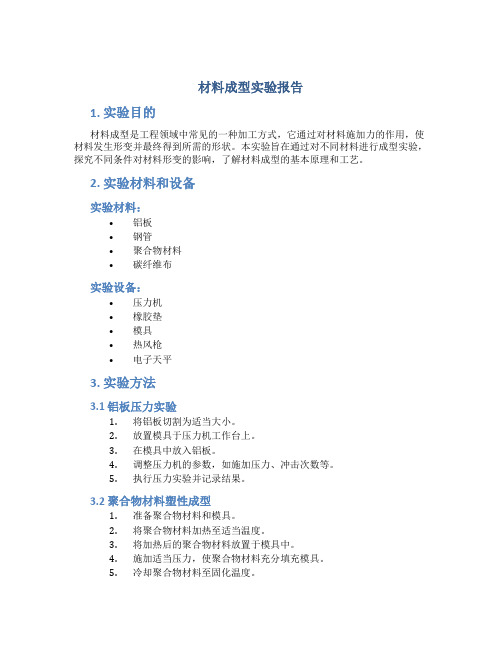
材料成型实验报告1. 实验目的材料成型是工程领域中常见的一种加工方式,它通过对材料施加力的作用,使材料发生形变并最终得到所需的形状。
本实验旨在通过对不同材料进行成型实验,探究不同条件对材料形变的影响,了解材料成型的基本原理和工艺。
2. 实验材料和设备实验材料:•铝板•钢管•聚合物材料•碳纤维布实验设备:•压力机•橡胶垫•模具•热风枪•电子天平3. 实验方法3.1 铝板压力实验1.将铝板切割为适当大小。
2.放置模具于压力机工作台上。
3.在模具中放入铝板。
4.调整压力机的参数,如施加压力、冲击次数等。
5.执行压力实验并记录结果。
3.2 聚合物材料塑性成型1.准备聚合物材料和模具。
2.将聚合物材料加热至适当温度。
3.将加热后的聚合物材料放置于模具中。
4.施加适当压力,使聚合物材料充分填充模具。
5.冷却聚合物材料至固化温度。
6.取出固化的聚合物制品。
3.3 碳纤维材料层脆性实验1.准备碳纤维布和热风枪。
2.将碳纤维布放置于平坦的表面。
3.使用热风枪将碳纤维布加热。
4.观察碳纤维布在加热过程中的形变情况。
5.将碳纤维布继续加热,观察其是否发生层脆性断裂。
4. 实验结果与讨论通过以上三种实验,我们得到了以下结果和讨论:铝板压力实验根据压力实验的数据记录,我们发现施加更大的压力会导致铝板的形变程度增加。
在其他实验条件保持不变的情况下,增加压力意味着对材料施加更大的力量,使得材料更容易形变。
但是当压力过大时,可能会导致铝板断裂。
因此在实际应用中,需要根据材料的特性和需要达到的成型效果来选择适当的压力。
聚合物材料塑性成型在聚合物材料塑性成型实验中,我们发现加热温度和施加压力对聚合物材料的成型效果有重要影响。
提高加热温度可以使聚合物材料更易流动和填充模具,但同时也会面临材料烧结或炭化的风险。
施加适当的压力可以使聚合物材料紧密地填充模具,并减少气泡和缺陷的产生。
因此,在聚合物材料的塑性成型过程中,需要综合考虑加热温度和施加压力,以达到所需的成型效果。
成型工艺综合实验报告

材料科学与工程学院实验报告书指导老师签名: 2014 年 05 月 25日实 验 名 称:成型工艺综合实验 年级专业及班级: 2011级材料成型及控制工程专业1班姓 名: 朱荣升 学 号: 22指 导 教 师:杨若绵、李辉、王金伙、谢建达评 定 成 绩: 教 师 评 语:(1)该落料件成形质量好,表面平整。
(2)拉深件在拉伸过程中容易出现拉深失效,主要是拉裂和起皱。
拉裂起皱拉深不足五、分析与讨论拉裂失效分析:拉深过程中,由于压边力过大、拉伸速度过快或润滑不足,导致拉伸变形力大于材料的实际抗拉强度以至拉裂。
起皱失效分析:拉深件起皱可能是原因是材料的相对厚度t/D较小、模具间隙过大,压边力过小,导致拉深件凸缘处切向压应力过大发生起皱。
拉深不足原因分析:拉深过程中,可能由于拉伸机的传感器故障,致使拉深未完成就已经开模。
(3)改善拉深工艺:设定合理的压边力及模具间隙、在凹模与板料接触面中进行润滑、采用合理的拉深工艺、选用合适的拉伸模、采取合理的拉深速度。
六、总结与建议通过微型冷冲、拉伸成型实验,在老师的指导下,我亲身体验了该成型机的实际操作,掌握了微型冷冲、拉伸成型机的使用方法及其工作原理。
该实验使用的材料是铝合金薄板,在冷冲过程中,为了使材料能够合理的利用,应选择合适的步距,尽量减少废料,使材料利用率达到最高。
在拉深过程中,会产生起皱和拉裂现象,这种现象可能是由于拉伸系数、压力大小、拉伸工序及润滑条件等因素造成的。
之前只在书本上大概了解过这些知识,通过这次实际操作以后,将理论与实际结合在一起,很好的巩固了之前学过的理论知识,为今后的学习奠定了不错的基础。
由于本次实验只使用了铝合金薄板这一种金属材料,无法进行对比,若能使用多种不同的金属材料进行实验,也许会收获更多。
实验序号 2 实验项目名称微型普通注塑实验地点模具中心指导老师李辉实验时间2014.05.20。
材料成形原理实验报告(3篇)
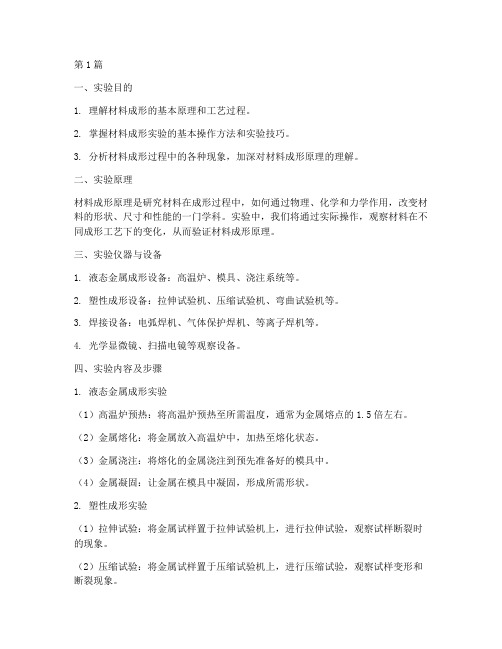
第1篇一、实验目的1. 理解材料成形的基本原理和工艺过程。
2. 掌握材料成形实验的基本操作方法和实验技巧。
3. 分析材料成形过程中的各种现象,加深对材料成形原理的理解。
二、实验原理材料成形原理是研究材料在成形过程中,如何通过物理、化学和力学作用,改变材料的形状、尺寸和性能的一门学科。
实验中,我们将通过实际操作,观察材料在不同成形工艺下的变化,从而验证材料成形原理。
三、实验仪器与设备1. 液态金属成形设备:高温炉、模具、浇注系统等。
2. 塑性成形设备:拉伸试验机、压缩试验机、弯曲试验机等。
3. 焊接设备:电弧焊机、气体保护焊机、等离子焊机等。
4. 光学显微镜、扫描电镜等观察设备。
四、实验内容及步骤1. 液态金属成形实验(1)高温炉预热:将高温炉预热至所需温度,通常为金属熔点的1.5倍左右。
(2)金属熔化:将金属放入高温炉中,加热至熔化状态。
(3)金属浇注:将熔化的金属浇注到预先准备好的模具中。
(4)金属凝固:让金属在模具中凝固,形成所需形状。
2. 塑性成形实验(1)拉伸试验:将金属试样置于拉伸试验机上,进行拉伸试验,观察试样断裂时的现象。
(2)压缩试验:将金属试样置于压缩试验机上,进行压缩试验,观察试样变形和断裂现象。
(3)弯曲试验:将金属试样置于弯曲试验机上,进行弯曲试验,观察试样变形和断裂现象。
3. 焊接实验(1)电弧焊:将金属板置于电弧焊机下,进行电弧焊,观察焊缝成形和焊缝组织。
(2)气体保护焊:将金属板置于气体保护焊机下,进行气体保护焊,观察焊缝成形和焊缝组织。
(3)等离子焊:将金属板置于等离子焊机下,进行等离子焊,观察焊缝成形和焊缝组织。
五、实验结果与分析1. 液态金属成形实验通过液态金属成形实验,我们观察到金属在高温下熔化,浇注到模具中后凝固成所需形状。
在实验过程中,我们掌握了金属熔化、浇注和凝固的基本原理。
2. 塑性成形实验通过塑性成形实验,我们观察到金属在拉伸、压缩和弯曲过程中,会产生不同程度的变形和断裂。
成型CAE实验报告完整版
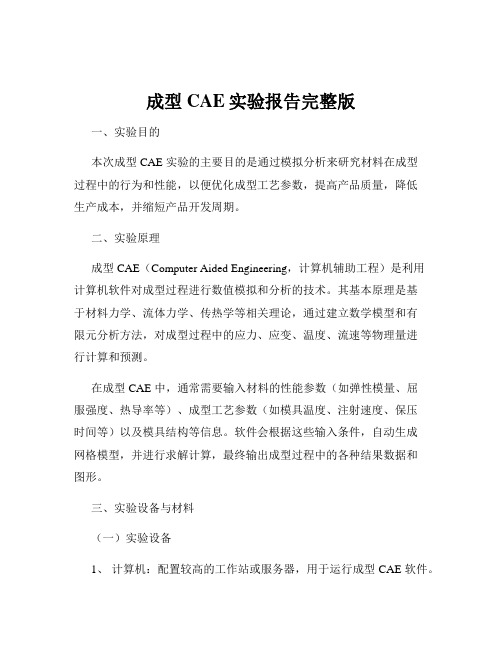
成型CAE实验报告完整版一、实验目的本次成型 CAE 实验的主要目的是通过模拟分析来研究材料在成型过程中的行为和性能,以便优化成型工艺参数,提高产品质量,降低生产成本,并缩短产品开发周期。
二、实验原理成型 CAE(Computer Aided Engineering,计算机辅助工程)是利用计算机软件对成型过程进行数值模拟和分析的技术。
其基本原理是基于材料力学、流体力学、传热学等相关理论,通过建立数学模型和有限元分析方法,对成型过程中的应力、应变、温度、流速等物理量进行计算和预测。
在成型 CAE 中,通常需要输入材料的性能参数(如弹性模量、屈服强度、热导率等)、成型工艺参数(如模具温度、注射速度、保压时间等)以及模具结构等信息。
软件会根据这些输入条件,自动生成网格模型,并进行求解计算,最终输出成型过程中的各种结果数据和图形。
三、实验设备与材料(一)实验设备1、计算机:配置较高的工作站或服务器,用于运行成型 CAE 软件。
2、成型 CAE 软件:选用了市场上较为成熟和广泛应用的_____软件,版本为_____。
(二)实验材料1、选用了_____材料,其主要性能参数如下:密度:_____弹性模量:_____屈服强度:_____热导率:_____四、实验步骤1、建立几何模型使用三维建模软件(如_____)创建成型产品的几何模型,并将其导入到成型 CAE 软件中。
2、划分网格在成型 CAE 软件中,对几何模型进行网格划分。
选择合适的网格类型(如四面体网格、六面体网格等)和网格尺寸,以保证计算精度和效率。
3、定义材料属性根据实验材料的性能参数,在成型 CAE 软件中定义材料的力学、热学等属性。
4、设置成型工艺参数根据实际的成型工艺条件,设置模具温度、注射速度、保压时间、冷却时间等工艺参数。
5、边界条件和加载确定模型的边界条件,如模具的固定约束、流体的入口和出口等,并施加相应的载荷。
6、求解计算运行成型 CAE 软件进行求解计算,等待计算完成。
- 1、下载文档前请自行甄别文档内容的完整性,平台不提供额外的编辑、内容补充、找答案等附加服务。
- 2、"仅部分预览"的文档,不可在线预览部分如存在完整性等问题,可反馈申请退款(可完整预览的文档不适用该条件!)。
- 3、如文档侵犯您的权益,请联系客服反馈,我们会尽快为您处理(人工客服工作时间:9:00-18:30)。
实验报告
实验课程:
学生姓名:
学号:
专业班级:
2010年 11 月
学生姓名: 学 号: 专业班级: 实验类型:□ 验证 □ 综合 □ 设计 □ 创新 实验日期: 实验成绩:
曲柄压力机动态应力测试
一、实验目的
1.掌握动态应力测试的实验技术,培养学生贴片、焊接、组桥的实际动手能力;
2.对J23-6.3T 开式压力机机身动态应力进行应力分析计算,进一步掌握压力机机身强度鉴定方法;
3.测定J23-6.3T 开式压力机工作时的冲裁力和机身动态应变,掌握力,应力测试仪器的使用方法,掌握动态信号测试的基本方法。
二、实验原理
开式压力机机身强度计算可将其简化为偏心拉伸的开口刚架,并取其喉口处I-I 截面为危险截面。
当机身受标称压力Pg 作用时,此截面受拉力Pg 和附加弯矩M 的组合作用,应力应为Pg 和M 所引起应力的叠加,即I-I p M σσσ=+.其最大应力应在立柱内侧面E 点处,该处应力仍处于主应力方向已知的单向应力状态。
如图1所示
图1 机身应力分析
因此,测定机身在工作载荷作用下的冲裁力P 和应变ε,根据机身弹性变形的线性关系和虎克定律,可确定机身危险截面在标称压力Pg 作用下的最大应力
max σ,判断该应力是否小于机身的许用应力[σ],是鉴定机身强度的有效方法。
学生姓名:学号:专业班级:实验类型:□验证□综合□设计□创新实验日期:实验成绩:
本实验采用冲裁模加载,冲裁板料厚度为1mm的Spcc钢板,直径为Φ36mm 圆孔。
冲裁力为一冲击信号,压力机机身由此而产生的应变也是随时间变化的动态应变,冲裁力信号可利用安装在冲裁模内的压电式力传感器转变成电荷量的变化,此变化量经电荷放大器放大后,由记录仪可得冲裁力波形,冲裁力大小可由波峰电压值及传感器电压灵敏度确定。
动态应变信号可由电阻应变片作为转换元件,测量前,在I-I截面E、F点处分别沿主应力方向以及与主应力方向垂直的方向各贴一片应变片,组成半桥,如图2所示。
当压力机工作时,电阻应变片将机身的弹性变形转变成电阻的变化,致使应变电桥输出电压发生变化,此变化量经动态应变仪放大后由记录仪可记录其应变波形。
动态应变的大小可由波峰电压值及标定应变电压值确定。
测试系统框图如图2所示。
三、实验仪器与设备
1.J23-6.3T开式压力机
2.冲裁模一副
3.5112压电式力传感器(航天部七0二所)
4.DHF-2电荷放大器(北京测振仪器厂)
5.YD-15动态应变仪(华东电子仪器厂)
6.CF-920数据采集分析系统(日本)
7.绘图仪
四、实验步骤
学生姓名: 学 号: 专业班级:
实验类型:□ 验证 □ 综合 □ 设计 □ 创新 实验日期: 实验成绩:
1.实测机身I-I 截面尺寸,将测量结果填入图3中
2.严格按照粘贴工艺分别在E 、F 部位沿铅直方向和水平方向各贴一片电阻应变片,铅垂方向应变片为工作应变片,水平方向应变片为补偿应变片,并在两应变片附近粘贴一接线端子。
3.粘贴胶固化后,将应变片引出线和连接导线焊接在接线端子上,组成半桥电路,并按图2所示连接好所有接线。
4.经指导教师检查无误后,通电预热。
稍后对应变仪进行平衡调节,估计被测信号幅值大小和频率范围,调节好各旋钮或按键的位置。
其中,O 点为压力机打击中心,0y 为压力机机身内壁到ox 轴之间距离,0110y mm =
图3 机身截面图
5.加载试测,观察所记录波形是否满意,并可通过调节工作频率范围和量程调整波形,直到满意为止。
6.重复测量六次,每次测量时,利用光标读取每次记录波峰的电压值,填入表1。
测量结束前,利用动态应变仪标定旋钮输出标准应变ε标(100με),并利用记录仪读取标准应变ε标对应输出电压值u 标。
学生姓名: 学 号: 专业班级:
实验类型:□ 验证 □ 综合 □ 设计 □ 创新 实验日期: 实验成绩:
五、数据处理
1.计算动态应变值和冲裁力的大小,将结果填入表1 1)动态应变 测点应变:11ˆ11i i εεμμ=
=++i u u εε⋅ 式中:μ——材料泊松比 0.28
μ= i u ε——第i 次测量E 或F 点应变波峰电压值 ε标——应变仪输出标准应变值,ε标=100με
u 标——标准应变对应电压值,u 标=
平均应变:1
1
N
i
i N
εε
==
∑
均方根误差:σ=
测量结果:ε±
2)冲裁力
第i 次测得冲裁力:pi i u
u P s =
式中:pi u ——第i 次测量冲裁力波峰电压值 u s ——压电式力传感器电压灵敏度 u s =0.1V/KN
平均冲裁力:1
1N
i i P P N ==∑
均方根误差:σ=
标
标
南昌大学实验报告
学生姓名: 学 号: 专业班级:
实验类型:□ 验证 □ 综合 □ 设计 □ 创新 实验日期: 实验成绩:
测量结果
P ±表1 冲截力、动态应变测量结果
2.根据机身截面尺寸计算该截面形心C 的坐标C (,c c x y )及对形心轴c x 的
惯性矩:
0c x = i i
c i
F y y F ∑=
∑ 2xc xci i i J J a F =∑+∑
式中:c x ——形心c x 轴坐标 c y ——形心c y 轴坐标
i F ——I-I 截面中第i 个子截面面积
i y ——I-I 截面中第i 个子截面形心i C 离x 轴距离 xc J ——I-I 截面对形心轴c x 的惯性矩
xci J ——第i 个子截面对各自形心轴ci x 的惯性矩
南昌大学实验报告
学生姓名: 学 号: 专业班级:
实验类型:□ 验证 □ 综合 □ 设计 □ 创新 实验日期: 实验成绩:
i a ——第i 个子截面形心i C 离形心轴c x 的距离 3.计算机身在冲裁力P 作用下E 、F 处的应变值 1()1c c o E xc y y y P E F J ε⎡⎤
--∆=
+⎢⎥⎣⎦
20()1c c F xc y h y y P E F J ε⎡⎤--∆+=-⎢⎥⎣⎦
式中:P ——实测冲裁力的平均值
E ——机身弹性横量 11
2
1.610/E N m =⨯ F ——I-I 截面横截面积 h ——I-I 截面机身宽度
1∆——贴片部位E 距机身内壁的距离 2∆——贴片部位F 距机身外壁的距离
4.比较实测应变值与理论计算应变值的大小,分析,评价本实验的可靠性,指出产生误差的可能原因。
六、主要参考书
《材料成形设备》 王卫卫 主编 机械工业出版社 2005年
《冲压与塑料成型设备》 范有发 主编 机械工业出版社 2006年
《工程力学》 机械工业教育协会组编 机械工业出版社 2001年。