ISO9001:2015内部审核报告英文版
ISO9001:2015全套文件英文版(含质量手册及全套程序文件)

Ningbo XXX Material TechnologyCo.,LtdISO9001:2015 Quality ManualRevision [A/0] - [2018/3/1](c) [Copyright Year Of 2018] [Ningbo XXX Material Technology Co.,Ltd]; all rights reserved. This document may contain proprietary information and may only be released to third parties with approval of management. Document is uncontrolled unless otherwise marked; uncontrolled documents are not subject to update notification.Revision [A/0] - [2018/3/1]Page 1 of 19TABLE OF CONTENTS0.0 Revision History and Approval ...................................................................................................................... 3 1.0 Welcome to Ningbo XXX Material Technology Co.,Ltd ................................................................................ 4 2.0 XXX Material: Who We Are ........................................................................................................................... 4 2.1 Determining Our Strategic Direction ......................................................................................................... 4 2.2 Scope of the Management System ........................................................................................................... 4 2.2.1 Scope Statement ............................................................................................................................... 4 2.2.2 Facilities Within the Scope ................................................................................................................ 4 2.2.3 Permissible Exclusions ..................................................................................................................... 5 2.2.4 Scope of the ISO9001:2015 Quality Manual ..................................................................................... 5 3.0 Quality Policy................................................................................................................................................. 5 4.0 Management System Structure and Controls ............................................................................................... 5 4.1 Process Approach .................................................................................................................................... 5 4.1.1 Process Identification ........................................................................................................................ 5 4.1.2 Process Controls & Objectives .......................................................................................................... 6 4.1.3 Outsourced Processes ...................................................................................................................... 7 4.2 Documentation & Records ....................................................................................................................... 7 4.2.1 General .............................................................................................................................................. 7 4.2.2 Control of Documents ....................................................................................................................... 7 4.2.3 Control of Records ............................................................................................................................ 7 4.3 Change Management ................................................................................................................................ 8 4.4 Risks and Opportunities ............................................................................................................................ 8 5.0 Management & Leadership ........................................................................................................................... 8 5.1 Management Leadership and Commitment .............................................................................................. 8 5.2 Customer Focus ........................................................................................................................................ 9 5.3 Quality Policy ............................................................................................................................................. 9 5.4 Organizational Roles Responsibilities & Authorities ................................................................................. 9 5.5 Internal Communication ............................................................................................................................ 9 5.6 Management Review .............................................................................................................................. 10 6.0 Resources ................................................................................................................................................... 10 6.1 Provision of Resources ........................................................................................................................... 10 6.2 Human Resources .................................................................................................................................. 10 6.3 Infrastructure ........................................................................................................................................... 11 6.4 Work Environment ................................................................................................................................... 11 6.5 Organizational Knowledge ...................................................................................................................... 11 7.0 Operation ..................................................................................................................................................... 11 7.1 Operational Planning and Control ........................................................................................................... 12 7.2 Customer-Related Activities .................................................................................................................... 12 7.2.1 Capture of Customer Requirements ............................................................................................... 12 7.2.2 Review of Customer Requirements ................................................................................................ 12 7.2.3 Customer Communication ............................................................................................................... 12 7.3 Design and Development ........................................................................................................................ 13 7.4 Purchasing .............................................................................................................................................. 13 7.5 Provision of [Production of adhesive tape] .............................................................................................. 13 7.5.1 Control of Provision of [Production of adhesive tape] ..................................................................... 13 7.5.2 Identification and Traceability .......................................................................................................... 14 7.5.3 Property Belonging to Third Parties ................................................................................................ 14 7.5.4 Preservation .................................................................................................................................... 14 7.5.5 Post-Delivery Activities .................................................................................................................... 14 7.5.6 Process Change Control ................................................................................................................. 15 7.5.7 Measurement and Release of [Production of adhesive tape] ......................................................... 15 7.5.8 Control of Nonconforming Outputs .. (15)Revision [A/0] - [2018/3/1]Page 2 of 198.0 Improvement ............................................................................................................................................... 15 8.1 General .................................................................................................................................................... 15 8.2 Customer Satisfaction ............................................................................................................................. 15 8.3 Internal Audit ........................................................................................................................................... 16 8.4 Corrective and Preventive Action ............................................................................................................ 16 Appendix A: Overall Process Sequence & Interaction ........................................................................................ 17 Appendix B: ISO 9001:2015 Cross Reference . (18)Revision [A/0] - [2018/3/1] 0.0 Revision History and ApprovalRev. Nature of changes Approval DateA/0 Original release. XXX 2018/3/1Page 3 of 19Revision [A/0] - [2018/3/1] 1.0 Welcome to Ningbo XXX Material Technology Co.,LtdNingbo XXX Material Technology Co., Ltd. Was established in 2000, with the UAE businessmen to build the joint venture company; 2004 Ming Shan founded Nissin special adhesive tape and adhesive tape company; 2008 due to the strategic adjustment of 3 company merger and reorganization, the establishment of Ningbo letter mountains adhesive products Manufacturing Co., Ltd..PVC insulation tape is one of China’s national standard drafting unit, the field of adhesive products governing unit of China, Ningbo, adhesives and related products Industry Association, honorary president of the unit.We produce more than 1000 varieties of products of 11 categories. The annual throughput more than 100,000,000 square of the adhesive and 10,000 ton of the adhesive.Our company located in Ningbo which the city of the east China sea, beside 500 kilometers of shanghai, 20 kilometers from Ningbo list airport and 50 kilograms of the Ningbo seaport. The transport is very convenient (Easy to ship to everywhere on the world).2.0 XXX Material: Who We Are2.1 Determining Our Strategic DirectionXXX Material has reviewed and analyzed key aspects of itself and its stakeholders to determine the strategic direction of the company. This involves:∙Understanding our core products and services, and scope of management system (see 2.2 below).∙Identifying “interested parties” (stakeholders) who receive our [Production of adhesive tape], or who may be impacted by them, or those parties who may otherwise have a significant interest in our company. These parties are identified in the document [Requirements and expectations list of interested parties].∙Understanding internal and external issues that are of concern to XXX Material and its interested parties; also identified in the document [Requirements and expectations list of interested parties]. Many such issues are identified through an analysis of risks facing either XXX Material or the interested parties. Such issues are monitored and updated as appropriate, and discussed as part of management reviews.This information is then used by senior management to determine the company’s strategic direction. This is defined in records of management review, and periodically updated as conditions and situations change.2.2 Scope of the Management System2.2.1 Scope StatementBased on an analysis of the above issues of concern, interests of stakeholders, and in consideration of its products and services, XXX Material has determined the scope of the management system as follows:Production of adhesive tapePage 4 of 19Revision [A/0] - [2018/3/1]Page 5 of 192.2.2 Facilities Within the ScopeThe quality system applies to all processes, activities and employees within the company. The facility is located at: Factory Add :XXX Tel :XXX Fax :XXX XXX XXX2.2.3 Permissible ExclusionsThe following clauses of ISO 9001 were determined to be not applicable to XXX Material.∙ 8.3 Design and development of products and services 2.2.4Scope of the ISO9001:2015 Quality ManualThis manual is prepared for the purpose of defining the company’s interpretations of the ISO 9001:2015 international standard, as well as to demonstrate how the company complies with that standard.This manual does not follow the numbering structure of ISO 9001. Instead, Appendix B presents a cross reference between the sections of this manual and the clauses of ISO 9001:2015.This manual presents “Notes” which are used to define how XXX Material has tailored its management system to suit its purposes. These are intended to clarify implementation approaches and interpretations for concepts which are not otherwise clearly defined in ISO 9001:2015. Notes appear in italics, with gray background.Where subordinate or supporting documentation is reference in this manual, these are indicated by bold italics .∙ Quality PolicyThe Quality Policy of XXX Material is as follows:Quality first, customer satisfaction;Scientific management, continuous improvement. ∙ Management SystemStructure and Controls 4.1Process Approach4.1.1 Process IdentificationXXX Material has adopted a process approach for its management system. By identifying thetop-level processes within the company, and then managing each of these discretely, this reduces the potential for nonconforming [Production of adhesive tape] discovered during final processes or after delivery. Instead, nonconformities and risks are identified in real time, by actions taken within each of the top-level processes.Note: not all activities are considered “processes” – the term “process” in this context indicates the activity has been elevated to a higher level of control and management oversight.The controls indicated herein are applicable only to the top-level processes identified.。
ISO9001内部质量体系审核(中英文)
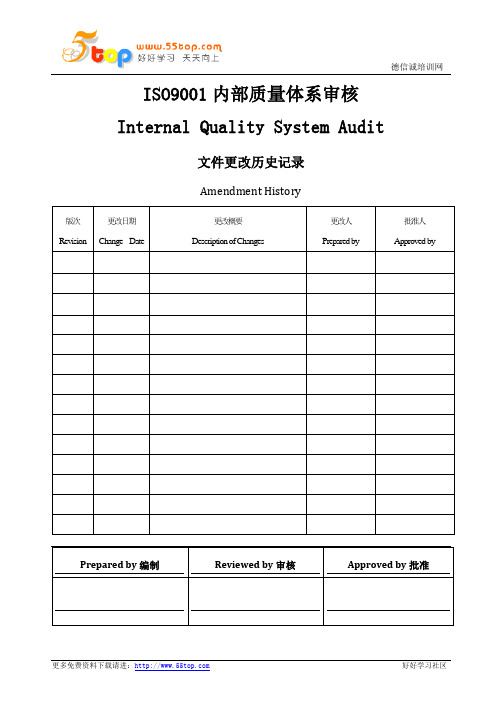
ISO9001内部质量体系审核Internal Quality System Audit文件更改历史记录Amendment History版次Revision更改日期Change Date更改概要Description of Changes更改人Prepared by批准人Approved byPrepared by编制Reviewed by审核Approved by批准ISO9001内部质量体系审核Internal Quality System Audit1.0目的 Purpose:本程序规定了开展内部质量审核的策划,准备,实施,审核,报告,跟踪验证各阶段的控制要求和方法,以确定本公司的质量管理体系是否符合标准要求并得到有效地实施和保持。
This procedure give the methods and control requirements of internal quality audit planning, preparing, implementing, auditing, reporting and following-up, to ensure that the quality management system is in compliance with requirements and is implemented and maintained effectively.2.0范围Scope:适用于本公司内部质量管理体系审核及质量体系涉及的所有部门或个人。
FP internal audit and all departments and persons related to quality management system 3.0定义Definitions: N/A3.1IQAR:内部质量审核报告Internal Quality Audit Report3.2NC:不符项(不符合ISO要求的项目)Non-conformance (item against ISOrequirement.)a)Major严重不符合项: there are systematic problem, territorial problem,and the findings will cause the major result during the system run; 体系运行出现系统性失效,体系运行出现区域性失效,出现影响产品或体系运行的严重后果的不合格现象.b)Minor一般不合格项: aim at the systematic requirements, the finding isseparate, occasional and isolated minor problem; 对不满足质量体系过程或体系文件的要求而言,是个别的、偶然的、孤立的性质轻微的问题.。
ISO9001-2015管理评审程序(中英文)
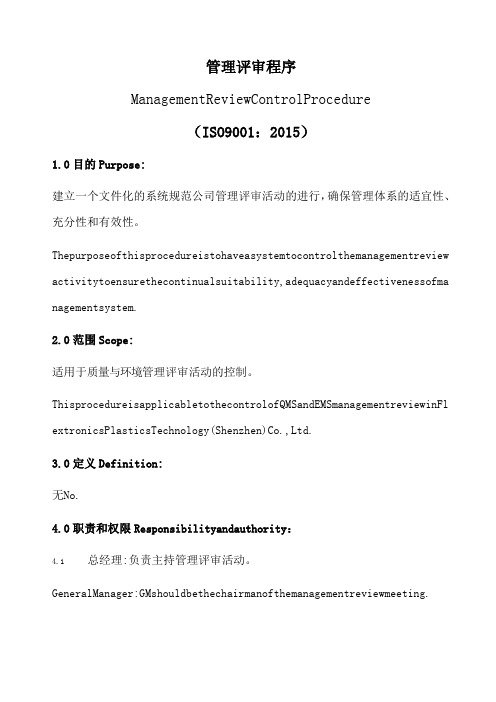
管理评审程序ManagementReviewControlProcedure(ISO9001:2015)1.0目的Purpose:建立一个文件化的系统规范公司管理评审活动的进行,确保管理体系的适宜性、充分性和有效性。
Thepurposeofthisprocedureistohaveasystemtocontrolthemanagementreview activitytoensurethecontinualsuitability,adequacyandeffectivenessofma nagementsystem.2.0范围Scope:适用于质量与环境管理评审活动的控制。
ThisprocedureisapplicabletothecontrolofQMSandEMSmanagementreviewinFl extronicsPlasticsTechnology(Shenzhen)Co.,Ltd.3.0定义Definition:无No.4.0职责和权限Responsibilityandauthority:4.1总经理:负责主持管理评审活动。
GeneralManager:GMshouldbethechairmanofthemanagementreviewmeeting.4.2管理者代表:负责管理评审计划的制定,落实及组织协调工作;负责评审报告的整理发放及改善行动的跟踪验证工作。
Managementrepresentative:MRshouldpreparemanagementreviewplan,carryou tandcoordinatethemanagementreviewmeeting;preparemanagementreviewrepo rtandfollowup/verifycorrectiveandpreventiveactions.4.3各有关部门:负责准备并提供与本部门工作有关的评审所需的资料,并对涉及本部门的不符合采取纠正或预防措施。
ISO9001:2015内部审核计划英文版

Date Scheduled
Date Conducted
Lead Auditor
OFI
Start by customCAizing PA
the
SETUP
form
tab
OFI
usingCAthe
PA
first.OFI
CA
PA
CA
PA
OFI
PA
OFI
CA
PA
OFI
If you need to unlock this form to access all the cells, click REVIEW -> UNPROTECT SHEET
ISO 9001 Clause
4.1 Understanding the Context 4.2 Interested Parties 4.3 Determining the Scope 4.4 QMS Processes 5.1 Leadership & Commitment 5.2 Policy 5.3 Organizational Roles Resp & Authorities 6.1 Risks and Opportunities 6.2 Quality Objectives 6.3 Planning of Changes 7.1.1 Resources: General 7.1.2 People 7.1.3 Infrastructure 7.1.4 Environment 7.1.5 Monitoring and Measuring Resources 7.1.6 Organizational Knowledge 7.2 Competence 7.3 Awareness 7.4 Communication 7.5 Documented Information 8.1 Operational Planning and Control 8.2.1 Customer Communication 8.2.2 Determining the Requirements 8.2.3 Review of Requirements 8.2.4 Changes to Requirements 8.3.1 Design & Development: General 8.3.2 Design and Development Planning 8.3.3 Design and Development Inputs 8.3.4 Design and Development Controls 8.3.5 Design and Development Outputs 8.3.6 Design and Development Changes 8.4 Control of Externally Provided… 8.5.1 Control of Production… 8.5.2 Identification and Traceability 8.5.3 Property Belonging to Customers … 8.5.4 Preservation 8.5.5 Post-Delivery Activities 8.5.6 Control of Changes 8.6 Release of Products and Services 8.7 Control of Nonconforming Outputs 9.1 Monitoring, Measurement… 9.2 Internal Audit 9.3 Management Review 10.1 Improvement: General 10.2 Nonconformity and Corrective Action 10.3 Continual Improvement
ISO 9001 2015 中英文
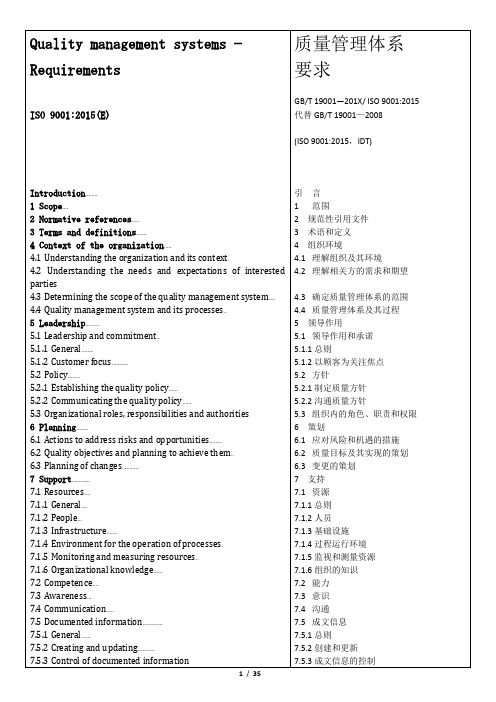
strategic direction of the organization. Management of the processes and the system as a whole can be achieved using the PDCA cycle (see 0.3.2) with an overall focus on risk-based thinking (see 0.3.3) aimed at taking advantage of opportunities and preventing undesirable results.The application of the process approach in a quality management system enables:a) understanding and consistency in meeting requirements; b) the consideration of processes in terms of added value; c) the achievement of effective process performance;d) improvement of processes based on evaluation of data and information.Figure 1 gives a schematic representation of any process and shows the interaction of its elements. The monitoring and measuring check points, which are necessary for control, are specific to each process and will vary depending on the related risks.Figure 1 — Schematic representation of the elements of a single process0.3.2 Plan-Do-Check-Act cycleThe PDCA cycle can be applied to all processes and to the quality management system as a whole. Figure 2 illustrates how Clauses 4 to 10 can be grouped in relation to the PDCA cycle.NOTE Numbers in brackets refer to the clauses in this International 维(见0.3.3)对过程和整个体系进行管理,旨在有效利用机遇并防止发生不良结果。
ISO9001-2015_中英文
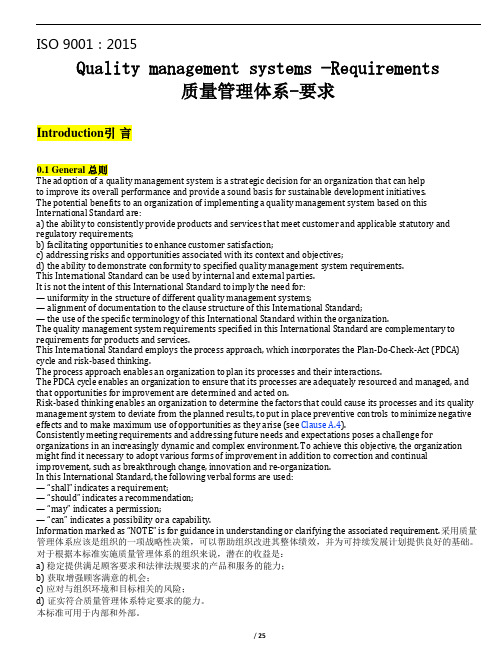
ISO 9001:2015Quality management systems —Requirements质量管理体系-要求Introduction引言0.1 General 总则The adoption of a quality management system is a strategic decision for an organization that can helpto improve its overall performance and provide a sound basis for sustainable development initiatives.The potential benefits to an organization of implementing a quality management system based on this International Standard are:a) the ability to consistently provide products and services that meet customer and applicable statutory and regulatory requirements;b) facilitating opportunities to enhance customer satisfaction;c) addressing risks and opportunities associated with its context and objectives;d) the ability to demonstrate conformity to specified quality management system requirements.This International Standard can be used by internal and external parties.It is not the intent of this International Standard to imply the need for:— uniformity in the structure of different quality management systems;— alignment of documentation to the clause structure of this International Standard;— the use of the specific terminology of this International Standard within the organization.The quality management system requirements specified in this International Standard are complementary to requirements for products and services.This International Standard employs the process approach, which incorporates the Plan-Do-Check-Act (PDCA) cycle and risk-based thinking.The process approach enables an organization to plan its processes and their interactions.The PDCA cycle enables an organization to ensure that its processes are adequately resourced and managed, and that opportunities for improvement are determined and acted on.Risk-based thinking enables an organization to determine the factors that could cause its processes and its quality management system to deviate from the planned results, to put in place preventive controls to minimize negative effects and to make maximum use of opportunities as they arise (see Clause A.4).Consistently meeting requirements and addressing future needs and expectations poses a challenge for organizations in an increasingly dynamic and complex environment. To achieve this objective, the organization might find it necessary to adopt various forms of improvement in addition to correction and continual improvement, such as breakthrough change, innovation and re-organization.In this International Standard, the following verbal forms are used:—“shall” indicates a requirement;—“should” indicates a recommendation;—“may” indicates a permission;—“can” indicates a possibility or a capability.Information marked as “NOTE” is for guidance in understanding or clarifying the associated requirement.采用质量管理体系应该是组织的一项战略性决策,可以帮助组织改进其整体绩效,并为可持续发展计划提供良好的基础。
ISO 9001 2015 中英文

strategic direction of the organization. Management of the processes and the system as a whole can be achieved using the PDCA cycle (see 0.3.2) with an overall focus on risk-based thinking (see 0.3.3) aimed at taking advantage of opportunities and preventing undesirable results.The application of the process approach in a quality management system enables:a) understanding and consistency in meeting requirements; b) the consideration of processes in terms of added value; c) the achievement of effective process performance;d) improvement of processes based on evaluation of data and information.Figure 1 gives a schematic representation of any process and shows the interaction of its elements. The monitoring and measuring check points, which are necessary for control, are specific to each process and will vary depending on the related risks.Figure 1 — Schematic representation of the elements of a single process0.3.2 Plan-Do-Check-Act cycleThe PDCA cycle can be applied to all processes and to the quality management system as a whole. Figure 2 illustrates how Clauses 4 to 10 can be grouped in relation to the PDCA cycle.NOTE Numbers in brackets refer to the clauses in this International 维(见0.3.3)对过程和整个体系进行管理,旨在有效利用机遇并防止发生不良结果。
ISO9001:2015内部审核程序英文版
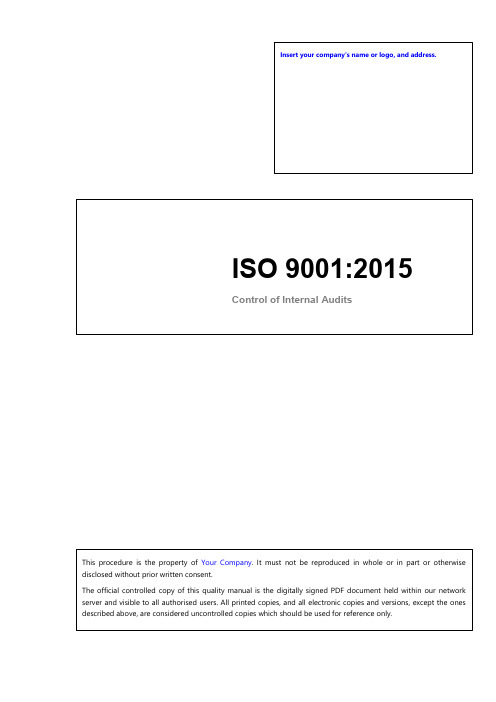
Contents1Control of Internal Audits _________________________________________________________________________________ 3 1.1Introduction & Purpose _______________________________________________________________________________ 31.1.1 Process Activity Map _______________________________________________________________________________ 31.1.2 References _________________________________________________________________________________________ 31.1.3 Terms & Definitions ________________________________________________________________________________ 3 1.2Application & Scope __________________________________________________________________________________ 4 1.3Responsibilities ________________________________________________________________________________________ 4 1.4Controlling Internal Audits ___________________________________________________________________________ 41.4.1 Selecting Internal Auditors ________________________________________________________________________ 41.4.2 Developing the Audit Programme _________________________________________________________________ 41.4.3 Preparing for the Audit ____________________________________________________________________________ 41.4.4 Conducting the Audit ______________________________________________________________________________ 51.4.5 Data Review & Initial Reporting ___________________________________________________________________ 51.4.6 Monitoring _________________________________________________________________________________________ 51.4.7 Final Reporting _____________________________________________________________________________________ 51.4.8 Review _____________________________________________________________________________________________ 5 1.5Conducting Audits ____________________________________________________________________________________ 51.5.1 System Audits ______________________________________________________________________________________ 51.5.2 Process Audits _____________________________________________________________________________________ 61.5.3 Supplier Audits _____________________________________________________________________________________ 61.5.4 Legislation Audits __________________________________________________________________________________ 7 1.6Corrective Action ______________________________________________________________________________________ 7 1.7Forms & Records ______________________________________________________________________________________ 7 1.8Internal Audit Process Map ___________________________________________________________________________ 81.2Application & ScopeThe scope of this procedure is focused on assessing the effectiveness of your organization’s quality management system. Where such processes are found to be deficient, the audit will lead to improvement in those processes. By applying the principles of auditing, outlined by ISO 19011:2011, your organization ensures that all internal audits are conducted with due professional care, integrity and independence. All conclusions derived from the audit are based upon objective and traceable evidence.1.3ResponsibilitiesIt is the responsibility of the Quality Manager<amend as appropriate> to coordinate the whole internal audit programme. The Quality Manager<amend as appropriate> is required to:∙Determine the root causes of non-conformities;∙Maintain a system for reporting audit results;∙Determine conformity to planned arrangements;∙Determine proper implementation and maintenance;∙Provide the results of audits to top management;∙Review the effectiveness of corrective actions taken.1.4Controlling Internal Audits1.4.1 Selecting Internal AuditorsTo ensure impartiality and objectivity, the audit team will include personnel from departments not directly associated with the area, process or department being audited. The Internal Auditors are selected on the basis of their:∙Education: secondary or higher;∙Work Experience: more than 5 years;∙Relevant Training: provided in-house or externally;∙Audit Experience: demonstrable knowledge/skills.1.4.2 Developing the Audit ProgrammeThe Quality Manager<amend as appropriate>is required to:∙Determine the status and importance of each process;∙Establish audit frequency based on the status and importance of each process;∙Develop and communicate the audit schedule;∙Appoint audit team leader where required;∙Select audit team;∙Assign audit duties to the auditor team.1.4.3 Preparing for the AuditThe Internal Auditors <amend as appropriate>are required to:∙Review relevant management system documents and records;∙Determine their adequacy with respect to the audit criteria and with ISO 9001;∙Review and prepare the internal audit checklist;The audit team then reviews the process inputs and outputs using the Turtle Diagram at the front of this procedure. The audit is conducted using the ISO 9001-2015 Supplier Audit Checklist.1.5.4 Legislation AuditsAt least once per year, audit is conducted on the scope and applicability of the register of applicable legislation in order to verify continued compliance. Using the register of legislation, the auditor determines the most significant legislation applicable to our organization at the time of the audit, by taking a sample and seeking objective evidence that the legislation is current and is being complied with.Samples of legislation are noted and the register brought up to date as required. The samples taken are selected based on current risks but ensures that the whole register is audited at least once in each 3 year period.1.6Corrective ActionThe corrective actions are identified on the Internal Audit, Non-conformity & Correct Action Tracker along with the person responsible and the timescales for completion. The process or procedure is re-audited and the issue closed out when all corrective actions are completed. A member of the audit team will then sign off the audit report. An audit summary is prepared for management review.1.7Forms & RecordsAll documentation and records generated by the internal audit process are retained and managed in accordance with the Control of Documented Information procedure.。
- 1、下载文档前请自行甄别文档内容的完整性,平台不提供额外的编辑、内容补充、找答案等附加服务。
- 2、"仅部分预览"的文档,不可在线预览部分如存在完整性等问题,可反馈申请退款(可完整预览的文档不适用该条件!)。
- 3、如文档侵犯您的权益,请联系客服反馈,我们会尽快为您处理(人工客服工作时间:9:00-18:30)。
Y/N
(or N/A)
Evidence or Notes Sheet Ref. #
In general, does the[Short Client Name]documentation meet the requirements of[ISO 9001 or AS9100]?
Review any customer requirements that may be applicable to this process. (If there are none, enter “N/A” in the middle column.) In general, does the[Short Client Name]documentation meet these requirements?
Indicate any suggestions for improvement related to the documentation:
STEP T
Compare the requirements of[ISO 9001 or AS9100], the[Quality Manual Doc Title]and other documentation against whatemployees are actually doing in everyday practice.
Indicate any problemovide brief details on any areas that you found were well-implemented, particularly effective or worth noting as positive traits of the process.
Does the process appear to adequately meet the requirements of[ISO 9001 or AS9100]and the[Short Client Name]documentation?
Does the process appear to adequately meet all customer or regulatory requirements?
Requirement
Reference
Question
Y/N
(or N/A)
Evidence or Notes Sheet Ref. #
Review previous audits for this process. Review previous[CAR Form Abbreviation]s issued against this process, or as a result of previous audits for this process. Add additional checklist questions here, based on the previous audits,[CAR Form Abbreviation]s or other documents or requirements, as you see fit.
STEP ONE: Audit
Process to Audit (Audit Scope):
Audit Date(s):
Lead Auditor:
Audit #:
Auditor(s):
Site(s) to Audit:
Applicable Clauses of[ISO 9001 or AS9100]Standard:
STEP F
Based on the findings andnonconformitiesyou have recorded in the previous sections, summarize the necessary actions needed. For type, choose one of the following:
Question
Y/N
(or N/A)
Evidence or Notes Sheet Ref. #
Are theprocedure stepsaccurate and complete as compared to true practice?
Are there sufficient check steps (inspections, tests, reviews, approvals, sign-offs, etc.) that ensure theprocessoutputs meet requirements before passing onto the next process?
Review any statutory or regulatory requirements that may be applicable to this process. (If there are none, enter “N/A” in the middle column.) In general, does the[Short Client Name]documentation meet these requirements?
Requirement
Reference
Question
Y/N
(or N/A)
Evidence or Notes Sheet Ref. #
STEP
Review the applicableprocedure(s)for this processand answer the questions below.
Applicable Documents to Audit
Rev.
[Quality Manual Doc Title]
STEP T
Compare the[Short Client Name]documentation with the applicable clauses of[ISO 9001 or AS9100].