压铸模设计规范
压铸模具设计规范
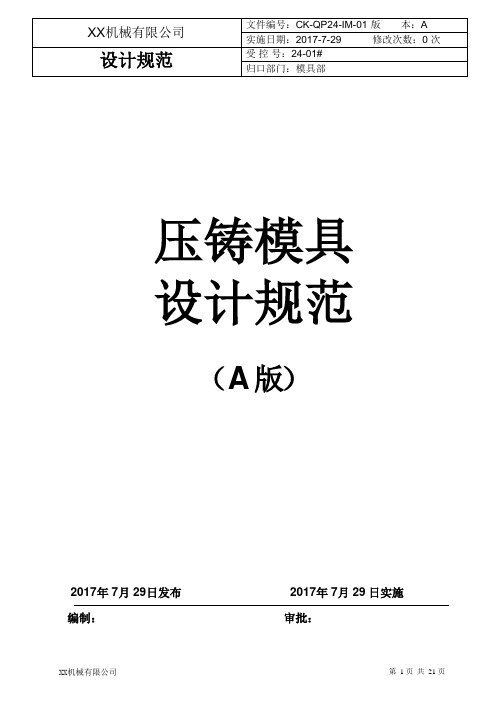
压铸模具设计规范(A 版)2017 年 7 月 29 日发布2017 年 7 月 29 日实施编制:审批:01. 目录一:模芯1.1模芯尺寸1.1.1模芯边距尺寸机型(T)160T 280T400T 500T-630T800T 1250T1600T三面(mm)55 60 70 80 100 120 140料筒面(mm)60 65 80 90 110 130 160 1.1.2模芯底面厚度尺寸机型(T)160T 280T400T500T-630T800T 1250T 1600T定模芯(mm)50 55 60 65 70 80 85动模芯(mm) 55 60 70 80 85 100 105敞开式滑块(mm)55 60 70 80 85 100 105 1.2模芯定位设计1.2.1模芯四角精定位斜度:动定模配合处单边 5°,与模框干涉处也要做斜度,单边 1.5°。
侧面转角圆角在 R8 以上。
定位的平面要避空 0.1mm,所有 R 角都要避空。
总高度最少 8mm。
1.2.2模芯周围一圈定位的斜度也做成 5°,平面不避空。
插入附件1.3,模芯冷却系统设计1.3.1:冷却水应设于流道附近、水管之间距保持 40mm-60mm,单独的孤岛处(凸起的)、大面积凹坑的侧边,产品最后凝固的厚壁处;1.3.2:环形冷却水的螺纹接口为 ZG1/4,冷却水管ø8-ø10mm,距离侧壁为 15mm 左右,距离顶面为 20~30mm,距离顶杆孔或销子孔至少 5mm;1.3.3:环形冷却水管经过的地方有高出平面的凸台或圆柱时应当采用隔水片的方式进行冷却,每一个环形最多允许有 6 个隔水片,隔水片孔与成型部位的距离参照点冷却;1.3.4:点冷却的水管直径为ø15.3mm-23mm 螺纹接口一般为 ZG3/8,距离侧壁为 15mm 左右,产品特殊厚壁可做到 6mm 左右,距离顶面为 15~25mm。
压铸件的设计规范标准介

压铸件的设计规范标准介压铸件的设计一定要考虑到压铸件壁厚、压铸件铸造圆角和脱模斜度、加强筋、压铸件上铸孔和孔到边缘的最小距离、压铸件上的长方形孔和槽、压铸件内的嵌件、压铸件的加工余量七个方面。
铸造圆角设计规范:通常压铸件各个部分相交应有圆角(分型面处除外),可使金属填充时流动平稳,气体也较容易排出,并可避免因锐角而产生裂纹。
对于需要进行电镀和涂饰的压铸件,圆角可以均匀镀层,防止尖角处涂料堆积。
压铸件的圆角半径R一般不宜小于1mm,最小圆角半径为0。
5mm。
压铸件内的嵌件设计规范:首先,压铸件上的嵌件数量不宜过多;其次,嵌件与压铸件的连接必须牢固,同时要求在嵌件上开槽、凸起、滚花等;再次,嵌件必须避免有尖角,以利安放并防止铸件应力集中,铸件和嵌件之间如有严重的电化腐蚀作用,则嵌件表面需要镀层保护;最后,有嵌件的铸件应避免热处理,以免因两种金属的相变而引起体积变化,使嵌件松动。
压铸件铸造圆角设计规范:通常压铸件各个部分相交应有圆角(分型面处除外),可使金属填充时流动平稳,气体也较容易排出,并可避免因锐角而产生裂纹。
对于需要进行电镀和涂饰的压铸件,圆角可以均匀镀层,防止尖角处涂料堆积。
压铸件的圆角半径R一般不宜小于1mm,最小圆角半径为0。
5mm。
压铸件壁厚的设计规范:薄壁比厚壁压铸件具备更高的强度和更好的致密性,鉴于此,压铸件设计中应该遵循这样的原则:在保证铸件具有足够强度和刚性的前提下应该尽可能减少壁厚,并保持壁厚具有均匀性。
实践证明,压铸件壁厚设计一般以2。
5-4mm为宜,壁厚超过6mm的零件不宜采用压铸工艺生产。
压铸件壁太厚、壁太薄对铸件质量影响的表现:如果设计中铸件壁太薄,会使金属熔接不好,直接影响铸件强度,同时会给成型造成困难;壁太厚或者严重不均匀时,容易产生缩瘪及裂纹,另一方面,随着壁厚的增加,压铸件内部气孔、缩松等缺陷也随之增多,同样会降低铸件强度,影响铸件质量。
模具铸件设计规范及注意事项

模具铸件设计规范及注意事项模具铸件设计规范一、铸件的铸造精度※模具设计时必须考虑要铸件的铸造精度二、铸件的结构设计1>筋的厚度及间距筋的厚度及间隙应注意看与厂家签订的技术要求,一般筋厚不低于30mm;筋的间距(图中A、B尺寸)一般为筋厚(T)8~12倍。
压料圈的筋间距一般取10倍,压料板可以取12~14倍,模板外周加强筋的间距可取至14~18倍2>筋的布置尽量避免斜交差米字型筋▼非直角时加大圆角▼筋设置避免集中交叉(T 字型筋为首选▼筋厚尽量均匀▼铸造困难处、或埋死、或开孔实型贴角困难处,手指不能伸进处都可视为铸造性不佳▼不同宽的筋交叉时的注意事项▼3>铸造孔设计减重孔▼可能情况下,筋全部设减重孔,但是铸件强度不足时,应慎重对待。
窥视孔从侧面查看压料板等是否到底▼为测定间隙,在上、下模的压件器,导向腿处开40X60 的窥视孔▼连接功能铸造孔▼偏重心的铸孔,当浇入铁水,实型气化后,砂芯会因偏重而变形,特别是铸空大、偏重心大时,必须在侧设置铸造孔与另一砂芯连接,以实现加强的功能。
废料滑道用铸孔,为方便安装滑道、清砂等▼安装零件用铸造孔▼安装冲孔凸模和斜楔滑块等用铸造孔排水孔▼模具清洗时,在模具不翻转的情况下保证清洗液流出,特别是带侧冲部件等;清除机械加工时的碎屑;漏水孔应该设计在立筋之间,应在铸造时铸出必须图纸说明,下凹的部件应设置一个以上装夹孔▼拉延凸模、压料板和侧冲滑块等铸件装夹用,设置于侧面最小100×40铸出孔或凹槽带型面的铸件如拉延凸模,在型面一侧应加工艺凸台4>挖空设计H<3A 或3B 时,上下侧挖空;H>3A 或3B 时,侧面挖空▼侧挖空尺寸▼注:A<100 时,则B=A;200<A<100 时,则B=1.5A;A>200 时,B(最大)=3A 超过上述规定时,在上、下底面及侧筋上开孔,见下图▼三、铸件的空刀设计加工面的空刀一般取10mm,挡块部分可取5mm两加工面相交处的空刀槽,宽度最小30mm,深度最大20mm四、倒角设计原则上凸角取5 X45°,凹角取15X45°,有强度要求时也可取大于上述值;铸件起吊时钢丝绳经过的部分去R20以上。
(整理)压铸模设计规范
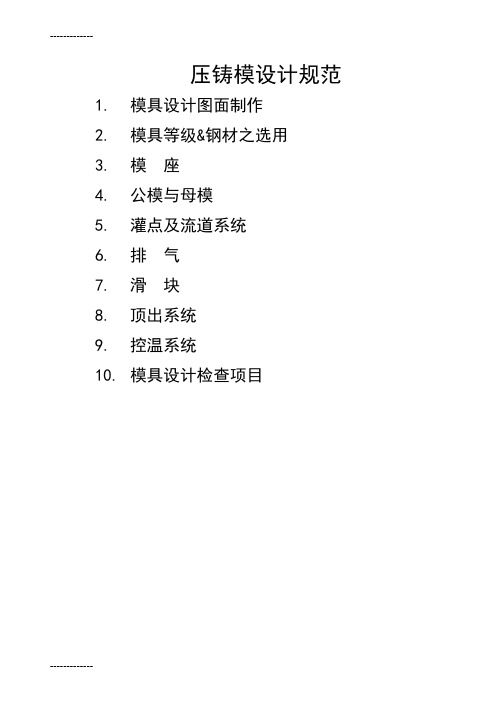
压铸模设计规范1.模具设计图面制作2.模具等级&钢材之选用3.模座4.公模与母模5.灌点及流道系统6.排气7.滑块8.顶出系统9.控温系统10.模具设计检查项目模具设计图面制作1.所有模具组立图需能完整表示出模具结构, 其图面应含一公,母模平面图, 纵向与横向剖视图, 和其他足以清楚表示模具结构之详细及剖视图.2.每张图面需有图框, 右下角要有标签栏.3.每张模具组立图需有材料栏, 其内容应含零件名称, 材料尺寸, 硬度, 零件在图面的编号及所需之数量.4.标示出所有模板, 镶块尺寸及模座的长, 宽, 高.5.标示”天侧”(TOP OF MOLD)于模具天侧及”基”(OFFSET)于偏移之导柱.6.画出完整之水路于平面及剖视图上, 至少标示一个不同水路的尺寸及水管接头,并标示”IN”,”OUT”及编号于水路进出侧. 水管应制成沉头型式.7.每个进料点需以详图标示.8.为易于辩认各零部件, 可使用下列代号:(1) GB---导套 (2) GP---导柱 (3) RP---回位销(4) ST---停止销 (5) SP---支撑柱9.标示锁模块, 吊模孔位置与尺寸.10. 标示主流道及分流道尺寸.模具等级&钢材之选用模具等级1.CLASS A1.1 要求寿命: 100万模次1.2说明: 用于要求快速生产或非常高之生产量, 产品尺寸要求严格, 模具以最高品质之钢材制造而成. 模具费用高昂.1.3钢材:A)模座: RAMAX 不锈钢材料, HRC34~38°.B)模仁: ELMAX, STAVAX或CORAX不锈钢材料,需热处理至HRC54°以上.C)滑动件: 须与模仁不同材料(整面滑块可使用与模仁相同的钢材),硬度相差4°以上,并作氮化处理. 耐磨块,压块须与滑块不同材料, 可与模仁材料相同. 所有滑动件必须开油沟.D)附要求: 钢材于EDM加工或焊补后, 需再行热处理以消除应力及与始钢材硬度均一.2.CLASS B2.1 要求寿命: 50万模次3.2说明: 用于中高产量, 及精密的公差要求. 这是高品质,高价格的模具.2.3 钢材:A)模座: P-20或AISI-4130, 硬度为HRC28~32°.B)模仁: SKD61, S136. 硬度为HRC50°以上.C)滑动件: TDAC,NAK80,DH2F或H-13, 热处理+氮化处理, 硬度为HRC48~52°, 需使用耐磨块时,材质为SK3-SK5(HRC52~56°), 所有滑动件必须开油沟. 整面滑块可使用与模仁相同的钢材.D)附要求: 钢材于焊补后, 需再行热处理以消除应力及与始钢材硬度均一.3.CLASS C3.1 要求寿命: 30万模次3.2 说明: 用于中低产量.3.3 钢材:A)模座: S50C或S55C, 硬度为HRB85~90°.B)模仁: NAK80, TDAC, P20. 硬度为HRC38~42°.C)滑动件:所有滑动件必须开油沟. 整体滑块可使用与模仁相同的钢材.模座1.模板需加装4支导柱及导套, 超过2.5吨的模具加装黄油嘴.2.支撑柱使用螺丝固定于公模板, 其数量及位置需足以抵挡射出压力而不致造成公模板变形, 尤其灌嘴附近.3.导柱直径在合理范围内尽可能加大并且长度至少为模座厚度约减5mm.4.导柱伸出模座部分不可超出总长的3/4.5.当需要微动开关控制模具动作顺序, 以保护模具时, 必须确实将其安装妥当.6.导套底部要有良好之排气槽.8.模板之间连接至少需要3~4个沉头螺丝, 并且超过50磅的结合力.9.每块模板四周边缘需加上C2倒角.10.模具装置有油压缸, 冷却水路接头, 电子接头等时, 如妨碍模具安置则需有垫脚,以确保模具正确放置方向.11.开模行程必须容许成品可落下及机械手臂操作.12.模脚于操作员侧面, 必须加工模具标签凹槽, 以便装置财产标签.13.模具无论大小组, 公母模分模面处制作锁模块(1~4个), 以防止模具吊运过程中模具开启.14.锁模槽直接开在母模板和模脚上. 模具大小必须符合相应机台规格.公模与母模4.公模仁与母模仁须刻字表示出基准边.5.公母模仁硬度必须高于HRC50, 易断裂的局部或较厚除外.7.模仁尽可能不分割镶块, 以防止毛边过多.但一些RIB较深/较多的可以考虑加.8.公母模仁固定螺丝至少需有50磅的结合力. 螺丝从反向固定.9.所有拔模方向的产品侧壁均需加拔模角, 母模方向大于公模方向0.5~2°, 所有拔模均需减肉加铁, 以便后续修模.10.模具不可含有斜顶出结构, 对倒勾部分可另外加工. 可以含有滑块结构.11.公模仁分模面处比模座表面高0.5mm, 母模仁分模面处与模座表面相平.12.所有靠破面侧壁需有至少5°拔模角度.13.公母模仁精加工前要测试硬度是否符合要求.14.最后抛光方向须与脱模方向相同, 公模表面粗糙度比母模表面粗糙度至少低一级,以便成品不黏母模.15.BOSS孔底部可做成圆入子, 入子尺寸取整数遵循内大外小的原则. 入子与模仁间隙不超过0.013~0.025mm.16.重量超过20Kg 的模仁要做至少2个工艺螺丝孔, 模仁四周倒C2角, 以便加工搬运.17.产品肉厚尽可能均匀. 产品肉厚比超过1.2时, 不可直角转折, 须用R,角度或曲面过渡, 以利淌流.产品肉厚比超过2.0时, 一般要做偷肉, 以防产生消水现象.ψ18. BOSS 长径比一般不超过8. 长径比超过4时, 为便于充填, 开口周围倒0.3~0.5 C角或R 角.19. RIB,定位柱肉厚一般不低于过0.5mm, 长径比一般不超过15, 长径比超过5时, 开口周围倒0.1~0.3 C 角或R 角. 长径比=B/A 或D/C20. 对于公母模相靠破部分, 为防止公母模错位, 公模部分单边可偷肉加铁0.05~0.15mm.灌点及流道系统1.流道设计不可有直角转弯现象, 应以圆弧改变方向.2.流道大小, 以成品重量,进料点数量及流道长度为考量依据.3.流道断面形状采用梯形结构,宽厚比一般为3:1~1,底部倒R1~3,侧面单边做5~10°,以利脱模. 灌口、分流子的斜度根据成品重量, 流道大小而定, 一般为5~10°.104.流道系统以流动平衡为优先考量. 对于一些肉厚较大, 靠破,形状较多等不易充填的部分, 须增加GATE或流道尺寸. 对于侧面进料的产品, 如中间有靠破部分,须采用搭接促进淌流, 并选在易于充填产品的地方.5.流道,灌点尺寸位置需经由模流分析决定, 当无模流分析时, 由小尺寸做起. 模具图面需有进料点放大图, 并详细标示尺寸.6.流道末端, GATE对面, 大的靠破处及模流分析不易填饱的部分尽可能增加冷料井,冷料井要有1~3mm的缓冲区. 冷料井有半圆形和梯形的形状.7.進料點應選在有利於沖填、流程較短、不會對型芯產生直接沖擊的地方。
压铸模具的技术要求文档

压铸模具的技术要求文档压铸模具是现代工业生产中常用的一种模具,用于制造各种金属制品。
压铸模具的技术要求非常高,对模具的设计、制造、使用等方面都有相应的要求。
本文将从几个方面详细介绍压铸模具的技术要求。
一、设计要求1.模具结构设计要合理,要考虑到产品的结构特点、工艺要求等因素,并保证在模具使用中有较高的稳定性和精度。
2.模腔的设计要充分考虑充型性、冷却性、顶出性等要素,确保产品成型质量稳定。
3.模具的开口方式、进料方式等设计要符合产品要求,并能保证模具的安全操作。
二、材料要求1.模具材料应具有良好的刚性、韧性和耐磨性,能够承受较大的冲击负荷和高温环境,如工具钢、合金钢等。
2.模具的热处理要求良好,能够使模具硬度均匀、稳定,延长使用寿命。
三、制造要求1.模具加工要求高精度、高质量,要保证模具的尺寸精度和表面质量。
2.维修和保养要定期进行,及时处理模具的磨损、损伤等问题,确保模具的正常使用和寿命。
四、使用要求1.模具的操作人员要具备一定的技能和经验,严格按照操作规程进行操作,保证操作的安全和准确性。
2.模具的使用环境要保持清洁、干燥,避免灰尘、水汽等对模具的损坏。
3.模具的顶出装置、冷却装置等要保持良好的工作状态,及时进行维修和更换。
五、质量控制要求1.模具的尺寸精度、表面质量等要进行严格的检测和控制,保证产品的准确性和一致性。
2.定期对模具进行检测和维修,及时发现并解决模具的问题,防止因模具问题引起的产品质量问题。
总结:压铸模具的技术要求非常高,对模具的设计、制造、使用等方面都有严格要求。
只有合理的设计,良好的材料和制造工艺,正确的使用和维护,才能保证模具的高质量和长寿命,从而保证产品的质量和生产效率。
因此,在实际应用中,需要充分重视压铸模具的技术要求,综合考虑各方面因素,确保模具的高效稳定运行。
压铸模国标

压铸模具国家标准(GB/T 8847 2003、GB/T 8844 2003)压铸模标准(国标2003)一、压铸模术语 GB/T 8847 20031 范围本标准界定了有关压铸模的常用术语。
本标准适用于压铸模常用术语的理解和使用。
2 一般术语2.1 压力铸造 die casting将熔融合金在高压、高速条件下填充模具型腔,并在高压下冷却凝固成型的铸造方法。
2.2 压铸模 die-casting die压力铸造成型工艺中,用以成型铸件所使用的模具。
2.3 定模 fixed die固定在压铸机定模安装板上的模具部分。
2.4 动模 moving die随压铸机动模安装板开合移动的模具部分。
2.5 型腔 cavity模具闭合后用以充填熔融合金,成型铸件的空腔。
2.6 分型面 parting line模具上为取出铸件和浇注系统凝料可分离的接触表面。
2.7 投影面积 proieot area模具型腔、浇注系统及溢流系统在垂直于锁模力方向上投影的面积总和。
2.8 收缩率 shrinkage在室温下,模具型腔与铸件的对应线性尺寸之差和模具型腔对应线性尺寸之比。
2.9 锁模力 locking force在充型过程中,为了保证动、定模相互紧密闭合而施加于模具上的力。
2.10 压力中心 pressure centre在平行于锁模力的方向上,熔融合金传递给模具的压力合力的作用点。
2.11 充填速度 filling velocity熔融合金在压力作用下通过内浇口的线速度。
2.12 压射速度 injection speed压射冲头运动的线速度。
2.13 压射比压 injection pressure充型结束时压射冲头作用于熔融合金单位面积上的压力。
2.14 脱模斜度 draft为了使铸件顺利脱模,在模具型腔壁沿脱模或抽拔方向上设计的斜度。
2.15 闭合高度 die shut height模具处于闭合状态下的总高度。
2.16 最大开距 maximum opening daylight压铸机动模、定模安装板之间可分开的最大距离。
压铸模标准

压铸模具制造标准目录一、总体要求:1、按本公司的压铸机尺寸设计外形,防止干涉。
(88T~800T)见附表(1)。
2、吊装孔至少为M30深45的,顶部至少2个,大型模具800T-900T为M42深60mm,,动定模架上要各2个,需设于模具的重心上(每半模),以利于吊装时的安全。
3、模具码模槽,最小30 mm×30 mm(400T以下),40 mm×40 mm(400T以上),到型板高最小30 mm(400T以下),40 mm(400T以上)。
4、跨距大于150 mm时都应考虑加支撑。
支撑柱直径(或宽)不小于60 mm,尽可能靠近压射变形位。
5、为减小变形,动模架支撑模芯的厚度至少为悬空位宽度的三分之一(大于或等于80mm)。
定模架支撑模芯的厚度大于或等于70mm。
特殊指定除外。
6、分流锥和浇口套按本公司的标准设计。
浇口套与压铸机熔杯联接处尺寸ΦD,ΦD1,L2参照附表(1)。
下图为本公司普通压铸的标准化浇口套:10模具有形状相同或对称的镶件,抽芯等必须设计防呆结构,动定模芯不能设计为正方形。
11模具各部份的尺寸关系,如果没有特殊说明,按以下关系设计。
B1D2 D1FT2T1E1E2P2P1WABBA二、模芯:1、加工后热处理前做去应力处理。
真空淬火热处理硬度:500吨及以上模具为HRC46°-48°,500吨以下模具为HRC48°-50°。
平面分型的,型腔位不深的(例如:电烫斗等)可以做到50°-52°。
精加工后按模具工艺之具体规定再做去应力处理,2、省模和抛光按客户要求的粗糙度和模具出模方向执行。
3、型腔最小圆角R0.5,最小拔模斜度1.5°~2°。
特殊指定的除外。
4、多腔模模芯可以分为两块制造,以利于热处理。
制造配合间隙在0.1mm以内。
350T以下除外。
5、模芯上有镶件必须线割时,必须预先打穿丝孔,当跨距大于200mm时,穿丝孔要做2个。
压铸模设计
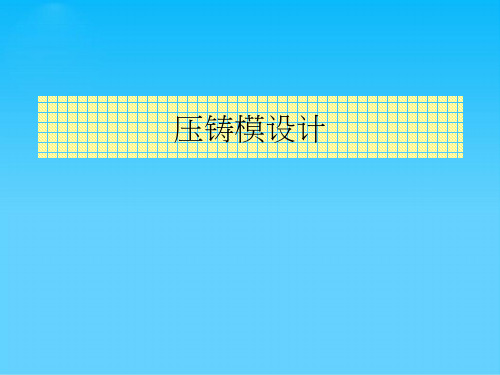
成
Cu
.10max .25max 075~1.25 .75~1.25 2.6~2.9
.10max
.0
.075
.10
.075
.075
.075
Pb
份
Cd
.004 .005 .004
.005
.004
.002
.003
.003 .004 .003
.004
.003
.002
.002
Sn
.002 .003 .002
(压射力与时间关系曲线见右图) 利用这特性,可便以型腔排气.
定壓义射2比﹕壓压與射壓压(射力壓二就力是)成在正压充比模铸﹐刚與合结壓束金射时沖之压頭射锌的冲截合头面作金積用成在反金比属。液面上的力。
t2:开始进入型腔﹐因浇口急减﹐阻力
壓热射室比 压壓铸與锌壓合热射金壓中室力的压成合正金铸比元用素﹐與锌壓合射沖金頭中的截面積成反比。
--
26.7
--
32.3 --
21.8
--
性
硬 度 (勃 式 )
82
72
91
80
100 98
80
67
衝 擊 強 度 (J)
30.2 28.8
33.7
28.1 24.6 3.5 30.2
28.8
質
疲勞強度
( K g / m m 2, 5 % 1 0 3
4.85
--
5.76
--
5.98 -- 4.78
--
非配合面
外(α) 內(β) 外(α) 內(β)
鋅合金 10' 15' 15' 45'
鋁合金 15' 30' 30' 1。