基于DEFORM的金属压力加工数值模拟_薛永栋
基于deform的纯铜管热挤压过程数值模拟

7819:;<!7 有限元 软件 5=6 对纯铜 管热挤 压 过 程
进行数值模拟分析 # 并着重研究挤压速度对变形 过程中热力学参数的影响规律 ! 模拟分析所需的
% 数值模拟结果及分析
%&$ 不同挤压速度下的温度场
金属塑性变 形 过 程 中 ";"E 以 上 的 变 形 能 以
"%
万方数据
! 铸造 锻 压 !"#
()*+,-./ / 0// 4// 123.,-.
材料与挤压模具工作带的摩擦产生了较高的剪切 应变 # 在试验的挤压速度变化范围内 "等效应变随 挤压速度的变化只产生很小的变化 " 且变化规律
88?* 的情况下 " 随着挤压速度的提高 " 压缩锥 和
定径区的最高等效应力值均提高 " 但当挤压速度 为 $"788?*7时 "等效应力反而有所降低 " 这可能是 因为高速变形时温度效应造成的 ! 在实际生产加 工时 " 因快速挤压引起的温度升高可能使纯铜坯 料产生动态再结晶 " 从而使变形抗力降低 ! 在数值 模拟过程中并未考虑动态再结晶的问题 " 因此关 于这一点 " 还有待更深入地分析 ! !热加工工艺 " !""# 年第 $% 卷第 &’ 期
"#$%&’ ’()’&*++,-.)%/00120$32*
L形铝合金控制臂预锻数值模拟及工艺优化
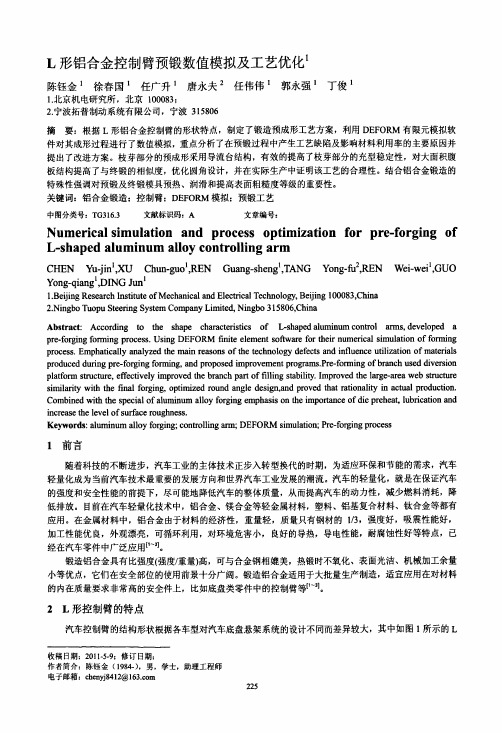
similarity with the final
forging,optimized
round angle design,and proved that rationality in actual production.
on
Combined with the special of aluminum alloy forging emphasis increase the level of surface roughness.
2
L形控制臂的特点
汽车控制臂的结构形状根据各车型对汽车底盘悬架系统的设计不同而差异较大,其中如图1所示的L
收稿日期:2011.5.9;修订日期: 作者简介:陈钰金(1984.),男,学士,助理工程师 电子邮箱:chenyj8412@163.com
225
形控制臂为常见的控制臂结构之一。其特点为:带枝芽和L形结构;腹板面积大.腹扳厚度薄:筋条窄; 枝芽位置体积较大等。这些特点使这类铝合金控制臂的锻造难度加大,对锻造的可行性、稳定性、成形质 量、材料利用阜等因素提出,新的考验。
匿8优化颈锻设置金属缓冲E域
Fig
囤9筋条目角**
Fig
80p胁=tpre-for自ng-semngmetalhIf陆zo”
9Webfo瑚d
an出d∞l辨
4模具预热、润滑及抛光对铝合金锻造的影响
铝合金流动粘性较大,较粗裢的表面将会增丈流动阻力。因此铝台金所用锻模,其表面状况直接影响
锻件表面质量,锻模型腔表面需经抛光赴理,使之达到V以下。模具预热是铝合金锻造工艺中的关键环节
f2】余忠±.张梅,"保自等常用铅☆垒&其热处目I艺饥热*a,2006,21(3):447 【3】赵培峰-任广升.沈智.徐春国6961镕台盘热E缩盘形条件对疏变&力的影响&其奉构方程的研究哪颦性工程学报. 2007.14{61:130-13a [4】孙春方,丁矗就。唐希文A16082铝台盘瘟势性能【J1汽车技术。2009.6:55.58 [5】冯海韩铝☆☆控制臂锻件锻造IZ自摸A设计棚金属铸锻埠挫术.2009,3s(9):133
《基于有限元的铝合金管材挤压成形数值模拟》范文
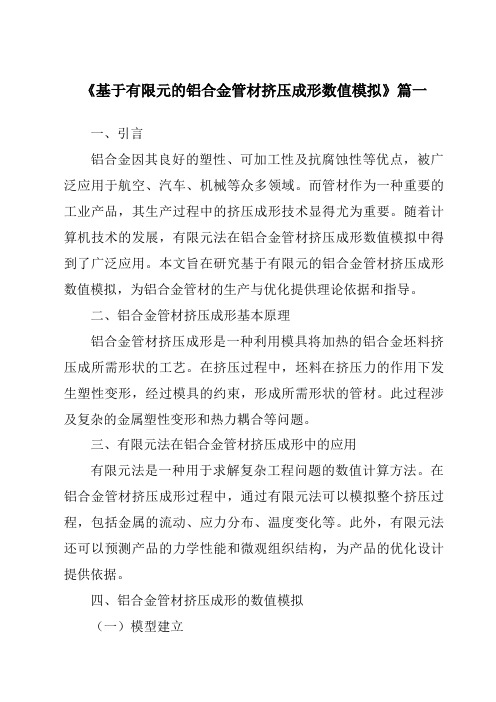
《基于有限元的铝合金管材挤压成形数值模拟》篇一一、引言铝合金因其良好的塑性、可加工性及抗腐蚀性等优点,被广泛应用于航空、汽车、机械等众多领域。
而管材作为一种重要的工业产品,其生产过程中的挤压成形技术显得尤为重要。
随着计算机技术的发展,有限元法在铝合金管材挤压成形数值模拟中得到了广泛应用。
本文旨在研究基于有限元的铝合金管材挤压成形数值模拟,为铝合金管材的生产与优化提供理论依据和指导。
二、铝合金管材挤压成形基本原理铝合金管材挤压成形是一种利用模具将加热的铝合金坯料挤压成所需形状的工艺。
在挤压过程中,坯料在挤压力的作用下发生塑性变形,经过模具的约束,形成所需形状的管材。
此过程涉及复杂的金属塑性变形和热力耦合等问题。
三、有限元法在铝合金管材挤压成形中的应用有限元法是一种用于求解复杂工程问题的数值计算方法。
在铝合金管材挤压成形过程中,通过有限元法可以模拟整个挤压过程,包括金属的流动、应力分布、温度变化等。
此外,有限元法还可以预测产品的力学性能和微观组织结构,为产品的优化设计提供依据。
四、铝合金管材挤压成形的数值模拟(一)模型建立建立准确的有限元模型是进行数值模拟的关键。
模型应包括坯料的几何尺寸、材料属性、挤压过程中的边界条件等。
同时,还需要根据实际生产情况设定合理的挤压速度、模具参数等。
(二)网格划分网格的划分对数值模拟的精度和计算效率有着重要影响。
在划分网格时,应考虑到金属流动的复杂性和模具的几何形状等因素,合理设置网格密度和类型。
(三)材料模型及本构关系在数值模拟中,需要设定铝合金的材料模型及本构关系。
常用的材料模型包括弹塑性模型、粘塑性模型等。
本构关系描述了材料的应力-应变关系,对模拟结果的准确性有着重要影响。
(四)求解过程在设定好模型、网格、材料模型及本构关系后,即可开始求解。
求解过程包括前处理、求解过程和后处理三个阶段。
前处理主要包括模型的建立和网格的划分,求解过程则是通过有限元软件进行计算,后处理则是对计算结果进行可视化处理和分析。
基于DEFORM的冲压模具设计的仿真与分析

基于 DEFORM的冲压模具设计的仿真与分析摘要:本文利用DEFORM软件对车间出现不合格品较多的拉深件—碗状加强筋进行数值模拟分析,对金属塑性成形过程进行实时点跟踪描述,并演示整个成形过程,揭示金属流动规律、各种因素对变形行为的影响及成形过程中零件的应力、应变分布,从而获得金属成型过程中的速度场、应力场、应变场、负载场结果。
关键词: DEFORM,拉深件,模具设计1引言公司真空灭弧室产品中有60%的零件属于拉深件。
在生产中,一些拉深件的质量问题,如拉裂、裂纹、拉伤、起皱、椭圆、堆边等问题一直困扰着大家,碗状加强筋是构成真空灭弧室的关键零件之一,用量大,质量要求严,对它的拉深质量问题原因和解决方法都是凭经验,没有理论研究和系统的分析,使得在模具设计上存在一定的弊端,影响质量和生产。
1.碗状加强筋工艺分析碗状加强筋如图1所示,材料是06Cr19Ni10,料厚为2mm,批量生产。
为提高生产效率和节约成本,可选用普通的冲压机床(J23-80),经研究分析,确定零件的加工方法采用板料拉深完成零件成型,工艺路线:备料—落料—拉深成型—车达图—检验,入库。
图1 碗状加强筋设计图1.基于DEFORM的碗状加强筋成形仿真模拟DEFORM技术是一套基于有限元分析的仿真系统,可用来分析金属成形规律与金属工业的热处理和成形工艺。
通过计算机模拟仿真整个成形加工过程,帮助工程设计人员设计产品和工艺流程,降低现场试验成本,用以提高模具的设计速度,以此缩短产品的研发周期。
成形过程仿真系统的建立,是将刚塑性成形工艺学、弹塑性有限元理论、拟处理器和后处理三大模块组成。
有限元分析流程如图2。
图 2 DEFORM成形问题有限元分析流程3.1 模型导入与网格划分在碗状加强筋成形过程中的工作部件为凸模和凹模,故仿真模拟中只导入毛坯、凸模和凹模,模型导入见图3。
绝对网格划分方式在网格尺寸总数设定后永不会变,它会增加模拟的正确性,故采用绝对网格划分方式。
基于deform 在金属塑性成形中的应用

基于deform 在金属塑性成形中的应用铜陵学院09材控一班陈军 0910121117摘要:由于deform-3D不具有三维造型功能,所以要实现塑性模拟过程所需要的物理模型均在其他三维软件中建立。
然后利用deform软件所具备的重新划分网格后,原节点的信息不会丢失。
设定变形物体的网格重划分网格标准,有两种选择:一个是绝对值,一个是相对值。
在deform软件的材料库中,各种材料都被分成易于选择的类别。
材料可以通过单位制或加工工艺类型进行检索。
这里主要介绍deform图形文件的生成及其相关功能键使用方法。
正文:一,deform软件的操作流程:(1)、定义几何特征。
Deform中对象的几何数据具有多种格式可供选择。
(2)、网格划分。
Deform网格划分生成四面体单元,这种四面体表面适合于表面成型。
(3)、初始条件。
如轧制时设置变形体、模具与周围介质间的热交换,变形体内部大变形生成热量及其传导都对产品的成形质量造成很大影响,对此问题的仿真模拟分析应按瞬间热-机耦合处理。
Deform软件可提供多种温度下的材料特性。
(4)、材料模型。
这里只研究钢塑性材料。
设定材料变形前,变形时,变形终了的温度和变形率下材料流动应力应变曲线和热膨胀系数、弹性模量、泊松比、热导率等随温度变化的曲线。
(5)、接触定义。
定义变形体与模具之间以及模具之间可能产生的接触关系。
变形的的温度、变形是待求量,变形体为接触体,刚性接触时只具有常温,起主动传递位移或合力作用。
如果需要模具的温度变化,可将模具上要关心的部分离散成单元,定义成允许热传递的刚性接触体,可以与外界催在热交换。
(6)、网格自动重划分。
模拟分析过程中,单元附着在材料上,材料流动中极易造成相应的单元格畸变,单元格畸变后会中断计算过程。
因此保证仿真过程中材料经大量流动后仍然可以继续,获得的结果仍然具有足够的精度。
Deform在网格畸变到一定程度后会自动进行网格重划分,生成搞质量的网格。
基于DEFORM的汽车轮毂轴管热挤压过程的数值模拟

FORGING2008年第2期1前言轮毂轴管(图1)是汽车后桥上一个重要的保安件,要承受各种复杂的交变应力与疲劳载荷[1]。
因此,其工作环境的特殊性决定了其较高的质量要求和挤压工艺参数的精确化。
传统挤压工艺的制定主要是建立在经验基础上,采用试错法不断调整工艺参数和修改模具,不仅研发周期长,而且挤压件的质量难以保证。
随着数值模拟技术的发展,可以采用计算机对金属成形过程进行分析,掌握变形过程中各种场量的变化情况。
并可对变形过程中工件内部缺陷等进行预测,对挤压工艺的制定具有重要的参考价值。
本文利用有限元软件DEFORM对轴管坯料的挤压过程进行了数值模拟。
并对挤压后工件的损伤、应力场、应变场及其分布的原因进行了分析,为制定生产工艺提供了参考[2]。
2建模及模拟条件应用DEFORM软件对汽车轮毂轴管热挤压过程的数值模拟,首先需建立有限元分析模型,如图2所示。
模型初始条件为:①设定上下模为刚性模型,工件为弹性模型;TheNumericalSimulationofLargeCylinderForginginForgingProcessunderHighTemperatureXUFeixia,CUIZhenshan,CHENWen,FUQiang(Dept.ofPlasticityFormingEng.,ShanghaiJiaoTongUniv.,Shanghai200030,China)Abstract:Thistextisbasedonthetraditionalshellforgingtechnologyforlargescalecylinderathightempera-ture.Therelationshipsbetweenanvil'smovementandtherotationofthesustainingcolumninhigh-temperatureforg-ingprocessoflargecylinderforgings,anditsinfluenceonforgingsdimensionhavebeenresearchedbyfiniteelementsimulation.Besides,itraisesamoreaccuratemethodforjudgingforging'sprecisionbycomparingthesimulationre-sultswiththeforgingin3Dsoftware.Keywords:ForgingP Large-scalecylinderP NumericalsimulationP Quality!98!60+10!70!88!152!6519590380625015图1轮毂轴管零件图收稿日期:2008-01-17作者简介:温志高(1967-)男,硕士,高级工程师,从事热挤压工艺技术研究文章编号:1672-0121(2008)02-0058-03基于DEFORM的汽车轮毂轴管热挤压过程的数值模拟温志高(河南英威东风机械有限公司,河南南阳474674)摘要:本文建立了汽车轮毂轴管的有限元分析模型,利用DEFORM软件模拟了工件热挤压过程,并分析了工件的损伤、应力场及应变场的分布情况和原因。
基于DynaForm的高强钢液压拉深成形数值模拟研究
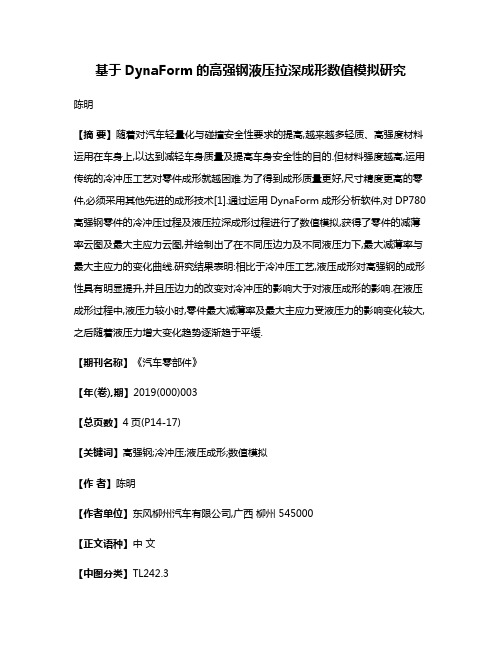
基于DynaForm的高强钢液压拉深成形数值模拟研究陈明【摘要】随着对汽车轻量化与碰撞安全性要求的提高,越来越多轻质、高强度材料运用在车身上,以达到减轻车身质量及提高车身安全性的目的.但材料强度越高,运用传统的冷冲压工艺对零件成形就越困难.为了得到成形质量更好,尺寸精度更高的零件,必须采用其他先进的成形技术[1].通过运用DynaForm成形分析软件,对DP780高强钢零件的冷冲压过程及液压拉深成形过程进行了数值模拟,获得了零件的减薄率云图及最大主应力云图,并绘制出了在不同压边力及不同液压力下,最大减薄率与最大主应力的变化曲线.研究结果表明:相比于冷冲压工艺,液压成形对高强钢的成形性具有明显提升,并且压边力的改变对冷冲压的影响大于对液压成形的影响.在液压成形过程中,液压力较小时,零件最大减薄率及最大主应力受液压力的影响变化较大,之后随着液压力增大变化趋势逐渐趋于平缓.【期刊名称】《汽车零部件》【年(卷),期】2019(000)003【总页数】4页(P14-17)【关键词】高强钢;冷冲压;液压成形;数值模拟【作者】陈明【作者单位】东风柳州汽车有限公司,广西柳州 545000【正文语种】中文【中图分类】TL242.30 引言板材冲压成形是一项十分重要的制造技术,广泛运用于汽车、电器、航空和国防工业等行业中,通常是在室温下进行,也称冷冲压[2]。
但传统的冷冲压成形性能不佳,容易产生变薄、拉裂、起皱、回弹、尺寸精度误差太大等问题,并且材料的强度越高,成形越困难,进而推动了许多如液压成形等先进的成形工艺的发展[3]。
液压成形属于一种柔性成形技术,是指采用液态的水、油或黏性物质作为传力介质,代替刚性的凹模或凸模,使坯料在传力介质的压力作用下贴合凸模或凹模而成形。
板料液压成形主要分为主动式和被动式两大类。
主动式液压成形是指液体代替凸模(见图1),被动式液压成形是指液体代替凹模[4](见图2)。
被动式在成形过程中需控制的参数有压边力、液体压力和凸模行程,而主动式则只需控制液体压力和压边力。
基于DEFORM-3D的不锈钢切削力有限元仿真

涉及到材料学、 学、 力 热学 及摩擦学等相关 知识 。以
前, 学者 通 常通过 试 验和解 析 的手段 来研 究切 削过 程 ,
往往耗时 、 耗力 、 成本高 , 难以精确测量切削力 、 应力应 变、 温度场分布等关键数据 , 而计算机技术的飞速发展 使 得利 用有 限元 方法 来研 究 切削加 工成 为 了可能 ¨ 引。
内牌 号 为 0 r8 i ClN9不锈 钢 ) 。
金属切削过程中, 刀具切人工件 , 使被加工材料发 生变形成为切屑所需要 的力称为切削力 , 它包含主切 削力 、 进给力 和背 向力 3 部分 。因为主切 削 力 是计算车刀强度 、 设计机床零件和确定机床功率 的主要依据 , 因此 , 择主切削 力 作为研究 对象。 选 相关 的仿真参数见表 1 。 表 1 仿真切削参数表
体常应变单元划分网格 。通常在一些场变量变化梯度 较大的区域 , 划分较为致密的网格 , 反之则应划分较为
稀疏 的 网格 。
4 2 相关结果分析 . 图2 表示主切削力 仿真曲线。从图中可看 出, 主切削力 先由零线性增大至最大值 , 然后减少并逐 步接近稳定 , 这与实际的切削过程一致。当刀具 开始
削过程进行 了建模与仿真 , 分析 O r8 i C lN9不锈钢的切 削力 变化 规律 以及切 削速 度和进 给量对其 切削 力的影响 . 同理 并 论计算 结果进行对比验证。研究表明 , E O M-D软件 所得仿 真数据与理论计 算结果吻合度 较高 , 明仿真 结果具 有 DFR 3 说 较 高的可信 度 , 系统 地研 究金 属的切削过程提供 了一种新 的途 径。图 4表 1参 1 为 0 关 键 词 : 削加 工; E O M一D软件 ; 切 DFR 3 有限元仿 真; 削力 切
- 1、下载文档前请自行甄别文档内容的完整性,平台不提供额外的编辑、内容补充、找答案等附加服务。
- 2、"仅部分预览"的文档,不可在线预览部分如存在完整性等问题,可反馈申请退款(可完整预览的文档不适用该条件!)。
- 3、如文档侵犯您的权益,请联系客服反馈,我们会尽快为您处理(人工客服工作时间:9:00-18:30)。
图 1 漏盘反挤模型
3. 2 网格划分与重划分 图 2是模拟漏盘反挤时所划的初始网格。
DEFORM 23D 软 件 只 能 划 分 四 面 体 网 格 。 DE2 FORM 23D 软件有强大的网格自动重划分功能 ,当 初始网格过大或模拟步长过大时 ,都有可能导致 模拟过程中出现网格畸变 ,这时为了保证模拟的 正确进行 , DEFORM 23D 软件便启动其网格自动 重划分功能 。
总 第 164 期 冶 金 设 备 2007年 8月第 4期
工件之间的热传导系数 ,指出工具和工件与环境 的热交换面 。图 7是 DEFORM 23D 软件进行热力 耦合分析给出的变形过程中工件的温度云图 ,图 中可以清楚地观察工件各个部分的温度情况 。
后处理器用于显示计算结果 ,结果可以是图 形形式 ,也可以是数字 、文字混编的形式 。可获 取的结果可为每一步的 ①有限元网格 ; ②等效应 力 、等效应变以及破坏程度的等高线和等色图 ; ③速度场 ; ④温度场 ; ⑤行程载荷曲线等 。此外 用户还可以列点进行定点跟踪 , 对个别点的轨 迹 、应力 、应变 、温度等进行跟踪观察 ,并可根据 需要抽取数据 。 3 D EFO RM 23D 实例分析
KEYWO RD S DEFORM software Plastic deformation FEM analysis Coup ling analysis
金属塑性加工是金属加工的一种重要工艺 方法 。利用模具和设备的动力作用 ,把金属坯料 加工成棒材 、板材 、管材以及各种机器零件 、构件 或日用器具 ,具有生产效率高 、原材料消耗少 、可 以有效地改善金属材料的力学性能和组织的特 点 ,广泛用于工业生产中 。随着塑性加工工业的 发展 , 新工艺 、新技术 、新设备和新产品层出不 穷 ,传统的采用基于经验试错设计的方法已不能 满足实际需要 ,引入以计算机为工具的现代分析 手段已成为人们的共识 ,也是提高塑性加工行业 的科学化水平的关键 。 1 D EFO RM 23D 系统简介
© 1994-2010 China Academic Journal Electronic Publishing House. All rights reserved.
薛永栋等 :基于 DEFORM 的金属压力加工数值模拟
2007年 8月第 4期
方向应力 、最大主应力 、方向应变 、等效应变 、方 向应变速率 、等效应变速率 、温度等参数随变形 时间或行程的变化情况 。 3. 6 行程 —载荷分析
图 3 变形过程中工件的 z向应变图
图 4 变形过程中工件的 z向应变率图
图 7 变形过程中工件温度图
3. 5 材料流动和定点追踪 图 8和图 9分别是定点追踪时点的初始位置
和点追踪过程中的位置 。从这二图可以很清晰 地观察金属流动的过程和判断金属流动的历史 , 这有利于在金属塑性变形过程中观察缺陷的生 成和分析缺陷的原因 ,也有利于控制金属的流动 趋势 。追踪点功能还可以给出点在变形过程中的
在塑性成形中 ,钢锭底部的沉积锥一般都是 直接被切除的 ,在这个过程中因有很多有用的金 属被同时切除而造成很大的浪费 ,漏盘反挤能பைடு நூலகம் 效地解决这个问题 。用漏盘反挤作为例子来说 明 DEFORM 23D 的功能 。 3. 1 模型的建立和导入
D EFORM 23D 软 件 支 持 多 种 CAD 系 统 , 如 PRO 2ENGINEER、IDEAS、PATRAN 以及 STL / SLA 格式 。采用 PRO - ENGINEER 建模 ,另存为 STL 后导入 DEFORM 23D 软件前处理器 ,如图 1所示 。 中间是钢锭 ,上下分别是上漏盘和下漏盘 。
Xue Yongdong Han J ingtao
(M aterials Science and Engineering School, University of Science and Technology B eijing)
ABSTRACT In this paper, the module structure of DEFORM is described simp ly. Some typ ical app lications of DEFORM are demonstrated in simulating metal p lastic deformation such as the distribution of effective stress and effective strain, calculation of load2stroke, tracking of point, analysis of p lastic flow, coup ling analysis of temperature.
摘要 介绍了塑性成形有限元分析软件 DEFORM 的模块结构 ,并通过实例分析介绍了该软件在网格划 分 、应力和应变分析 、载荷计算 、点的跟踪和温度耦合分析等方面的应用 。
关键词 DEFORM 软件 塑性成形 有限元分析 耦合分析 中图分类号 TG315 文献标识码 A
Applica tion of D EFO RM Software in S im ula tion of M eta l Pla stic D eforma tion
DEFORM 23D 是美国 B attelle Columbus实验 室开发的一套有限元分析软件 。DEFORM 23D 在
一个集成环境内综合建模 、成形 、热传导和成形 设备特性进行模拟仿真分析 ,适用于热 、冷 、温成 形 ,并提供极有价值的工艺分析数据 。如 : 材料 流动 、模具填充 、锻造负荷 、模具应力 、晶粒流动 、 金属微结构和缺陷产生发展情况等 。DEFORM 2 3D还具有以下特点 :不需要人工干预 ,全自动网 格再剖分 ;前处理中自动生成边界条件 ,确保数 据准备快速可靠 ; 单步模具应力分析方便快捷 , 适用于多个变形体 、组合模具 、带有预应力环时 的成形过程分析 ;材料模型有弹性 、刚塑性 、热弹 塑性 、热刚粘塑性 、粉末材料 、刚性材料及自定义 类型 ;实体之间或实体内部的热交换分析既可以 单独求解 ,也可以耦合在成形模拟中进行分析 。 这些特点使 DEFORM 23D 这一有限元分析软件在
[ 3 ]李尚健主编. 金属塑性成形过程模拟. 北京 :机械工业 出版社 , 1999
[ 4 ]Hong Sukmoo, Lee Seungyoon, Kim Naksoo. A paramet2 ric study on form ing length in roll form ing[ J ]. Journal of M aterials Processing Technology, 2001, Vol. 113 (1~3) : 774~778
[ 5 ]陈学文 ,王进. 热锻成形过程数值模拟与多目标设计 优化技术研究. 塑性工程学报 , 2005, Vol. 8 (4) 80~84
[ 6 ]孙明月 ,李殿中 ,李依依. 大型船用曲轴曲拐的弯锻过 程模拟 与 实 验 研 究. 金 属 学 报 , 2005, Vol. 12 ( 12 ) : 1261~1266
在金属的变形过程中 ,大量的机械功经由塑 性变形和工具 —工件界面的摩擦力转化为热。如
— 35 —
© 1994-2010 China Academic Journal Electronic Publishing House. All rights reserved.
① 作者简介 :薛永栋 ,男 , 1975年出生 ,北京科技大学在读博士生
— 34 —
© 1994-2010 China Academic Journal Electronic Publishing House. All rights reserved.
参考文献
[ 1 ]王祖城 ,汪家才. 弹性和塑性理论及有限单元法. 北 京 :冶金工业出版社 , 1983
[ 2 ]Montm itonnet P, Gratacos P, Ducloux R. App licationof anisotrop ic viscop lastic behaviour in 3D finite2element simulations of hot rolling [ J ]. Journal of M aterials Pro2 cessing Technology, 1996, Vol. 58 (3) : 201~211
真正的有限元分析过程是在模拟处理器中 完成的 , D EFORM 运行时 ,首先通过有限元离散 化将平衡方程 、本构关系和边界条件转化为非 线形方 程 组 , 然 后 通 过 直 接 迭 代 法 和 N ew ton2 Raphson法进行求解 ,求解的结果以二进制的形 式进行保存 ,用户可在后处理器中获取所需要 的结果 。 2. 3 后处理器
AToutgaul
No. 164 st 2007
M E TA L冶LU R金G IC A设L
备 EQU
IPM
EN
T 2 00 7总年第8月16第4期4期
基于 D EFO RM 的金属压力加工数值模拟
薛永栋 ① 韩静涛
(北京科技大学材料学院 北京 100083)
图 10 行程 - 载荷图
4 结论 DEFORM 23D 软件的前后模拟处理器方便而
可行 ,它的特点决定了这一有限元分析软件在工
业生产中实用而可靠 。利用 DEFORM 有限元软 件对金属的塑性变形进行模拟 ,有利于帮助设计 人员优化工艺参数 ,有利于缩短工艺的设计开发 周期 ,以及现在愈来愈快的工作站都大大减少了 设计人员的工作量 ,提高了社会生产效率 。
图 5 变形过程中工件的 z向应力图
图 8 追踪点的初始位
图 6 变形过程中工件的最大主应力图
果产生的这个热很显著 ,或者如果工件的初始温 度与周围环境及工具有很大的差别 ,就势必要进 行热力耦合分析了 。应用 DEFORM 23D 软件进行 热力耦合分析只需要在前处理器中设置工具与