感应电炉熔炼钢铁配料计算 全了
感应炉炼钢配料的计算
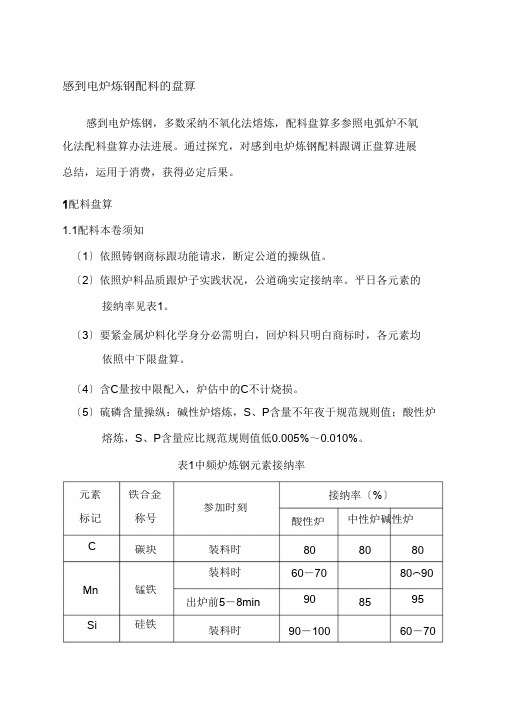
感到电炉炼钢配料的盘算感到电炉炼钢,多数采纳不氧化法熔炼,配料盘算多参照电弧炉不氧化法配料盘算办法进展。
通过探究,对感到电炉炼钢配料跟调正盘算进展总结,运用于消费,获得必定后果。
1配料盘算1.1配料本卷须知〔1〕依照铸钢商标跟功能请求,断定公道的操纵值。
〔2〕依照炉料品质跟炉子实践状况,公道确实定接纳率。
平日各元素的接纳率见表1。
〔3〕要紧金属炉料化学身分必需明白,回炉料只明白商标时,各元素均依照中下限盘算。
〔4〕含C量按中限配入,炉估中的C不计烧损。
〔5〕硫磷含量操纵:碱性炉熔炼,S、P含量不年夜于规范规则值;酸性炉熔炼,S、P含量应比规范规则值低0.005%~0.010%。
表1中频炉炼钢元素接纳率元素标记C 铁合金称号接纳率〔%〕中性炉碱性炉参加时刻酸性炉碳块装料时装料时8060-709080 8080⌒9095Mn Si 锰铁硅铁出炉前5-8min 85装料时90-100 60-70100 98 95 95 95 98 95 9095959595100出炉前5-8min装料时Mo Cr W 钼铁铬铁钨铁出炉前15-30min装料时9897-9895出炉前5-8min装料时100 出炉前15-30min 98出炉前>~10min92-9580-90出炉前5-8min95~9880-9080-9080-90含量<0.3%出炉前5-8min含量>1.0%V 钒铁90 90 90Nb Ni Al 铌铁镍板铝块出炉前5-8min 85 909890装料时100 100 出炉前3~5min 93-95 装料时100959898100Cu 电解铜出炉前15-30min 98Ti B50708592钛铁硼铁终脱氧后,冲包终脱氧后,冲包出炉前-9090-90908590石墨电极粉焦炭粉出炉前80 80 80 1.2配料盘算步调为了简化运算,以炉料咨询题替代钢液量。
〔1〕盘算铁合金参加量铁合金参加量炉料总量操纵值接纳率回炉料含该元素量铁合金中该元素含量低合金钢:铁合金参加量出钢量操纵身分炉内钢液元素含量收得率铁合金中元素含量单位高合金钢铁合金参加量炉内钢液量操纵身分炉内钢液元素铁合金身分操纵身分收得率〔2〕盘算碳素废钢〔或质料纯铁〕预加量碳素废钢预加量〔〕炉料总量〔〕―回炉料分量〔〕―铁合金总量〔〕〔3〕核算炉估中C、Si、Mn均匀含量种种炉料分量元素含量均匀含量炉料总量〔4〕盘算生铁、硅铁、锰铁参加量参加量炉料总量操纵值接纳率炉估中均匀含量生铁含量〔或硅铁、锰铁中、含量〕留意:运用高碳锰铁配料时,由于锰铁要带入较多的碳,生铁的加入量应比实践盘算后果恰当减小。
感应电炉的配料计算

具体配料 100kg中频感应电炉
配比(%)
炉料重量(kg)
炉前包(100kg)内处理
生铁(Q10) 66.5
66.5
球化剂1.5%:100×1.5%=1.5kg
回炉料(QT) 30.0
30.0
废钢 3.5
3.5
一次孕育剂0.5%: 100×0.5%=0.5kg
(75Si-Fe)
65Mn-Fe 0.11 0.17 0.17
需加Si-Fe:0.4kg(不计烧损)
9
2)QT700-2(原铁液)(酸性炉)
类别
C
Si Mn
P
S
设计成分(%) 3.7 1.3 0.4 ≤0.06 ≤0.05
元素增减率A(%)
考虑元素增减后的 炉料成分(%)
-5 3.89
-7 1.40
-20 0
0
0.50 ≤0.06 ≤0.05
X 炉料
X 铁水 1 A
0.046 0.06
合格
12
注:
1. 电炉的S原一般在0.03~0.05%。 2. 原铁水含Si1.3%,加上球化剂(以1.5%计)
中含Si量0.60%和孕育剂(一次孕育0.5%, 二次或瞬时孕育0.1%)中含Si量0.45%,则 终硅为2.35%左右。 3. 0.5%Cu(电解铜板)在炉前包内冲入。
10
根据生产条件,确定球铁回炉料配比为30%。 设炉料总重为100%,其中生铁为x%, 则废钢为(100-30-x)=(70-x)(%)。 可根据各种炉料的含碳量,列出下式: 4.15x+0.15(70-x)+3.75×30=3.89×100 4.15x+10.5-0.15x+112.5=389 4.00x=266 x=66.5(%)生铁, 而废钢为(70-x)=(70-66.5)=3.5(%)。
电炉配料操作程序
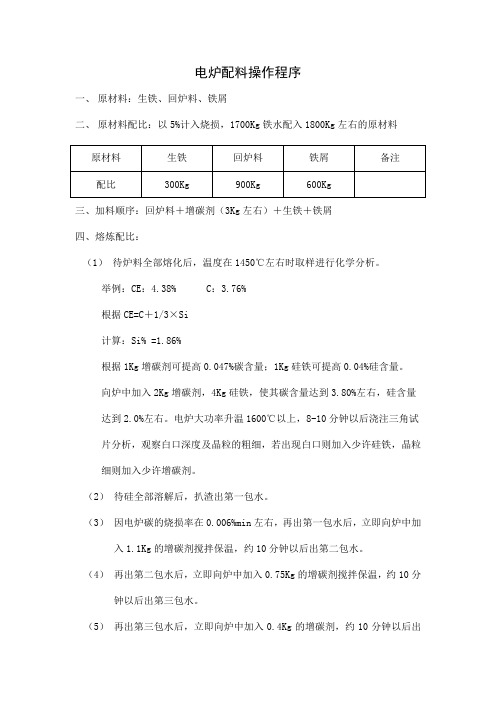
电炉配料操作程序
一、原材料:生铁、回炉料、铁屑
二、原材料配比:以5%计入烧损,1700Kg铁水配入1800Kg左右的原材料
三、加料顺序:回炉料+增碳剂(3Kg左右)+生铁+铁屑
四、熔炼配比:
(1)待炉料全部熔化后,温度在1450℃左右时取样进行化学分析。
举例:CE:4.38% C:3.76%
根据CE=C+1/3×Si
计算:Si% =1.86%
根据1Kg增碳剂可提高0.047%碳含量;1Kg硅铁可提高0.04%硅含量。
向炉中加入2Kg增碳剂,4Kg硅铁,使其碳含量达到3.80%左右,硅含量达到2.0%左右。
电炉大功率升温1600℃以上,8-10分钟以后浇注三角试片分析,观察白口深度及晶粒的粗细,若出现白口则加入少许硅铁,晶粒细则加入少许增碳剂。
(2)待硅全部溶解后,扒渣出第一包水。
(3)因电炉碳的烧损率在0.006%min左右,再出第一包水后,立即向炉中加入1.1Kg的增碳剂搅拌保温,约10分钟以后出第二包水。
(4)再出第二包水后,立即向炉中加入0.75Kg的增碳剂搅拌保温,约10分钟以后出第三包水。
(5)再出第三包水后,立即向炉中加入0.4Kg的增碳剂,约10分钟以后出
第四包水。
五、假如在取样进行化学分析时出现异常情况,碳含量在0.8%以上时如8.3%时怎办?
六、增碳剂能随流冲入包内吗?这会不会增碳剂的未熔部分引起铸件的渣孔缺陷?
七、在电炉内铁水高温保温期间,增碳剂能加入到2Kg吗?增碳剂量的增多是不是引起铸件缩孔、缩松的主要原因呢?
八、能否进行孕育处理两次?第一次在铁液进入大包随流孕育处理,第二次在手包内浮硅孕育处理?。
电炉冶炼配料与计算

电炉冶炼配料与计算配料的要求与计算配料的首要任务是保证冶炼的顺利进行。
科学的配料既要准确,又要合理地使用钢铁料,同时还要确保缩短冶炼时间、节约合金材料并降低金属及其他辅助材料的消耗。
一、对配料的基本要求1、准确配料配料的准确性包括炉料重量及配料成分两个方面。
配料重量不准,容易导致冶炼过程化学成分控制不当或造成铸件浇不足,也可能出现过量而增加消耗。
炉料化学成分配得不准,会给冶炼操作带来困难,严重时将使冶炼无法进行。
以氧化法冶炼为例,如配碳量过高,会增加矿石用量或延长用氧时间;配碳量过低,熔清后势必进行增碳;如炉料中S、P太高,给炉前操作带来极大困难,不仅延长冶炼时间,而且对炉衬侵蚀严重,有时甚至要终止冶炼。
为了杜绝以上情况,配料前掌握有关钢铁料及铁合金的化学成分是十分必要的。
2、钢铁料的使用原则钢铁料的使用原则主要考虑冶炼方法、装料方法、钢种的化学成分以及产品对质量的要求等。
此外,在配料时,还应预先掌握好钢铁的块度和单位体积重量。
一般炉料中应配入大块料30~40%、中块料40~50%、小块料或轻薄料15~25%。
二、配料计算公式1、装入量=出钢量/钢铁综合收得率2、配料量=装入量—铁合金总量—矿石进铁量—余钢回炉量3、铁矿石进铁量=铁矿石加入量某含铁量某铁的收入率矿石加入量一般按出钢量的4%计算,矿石含铁量为55%,铁的收得率按80%回收,炉料总的综合收得率波动于92~96%,一般按94%计算。
装料方法及要求一、装料方法电炉炼钢最常见的是冷装料,按其入炉方式不同分为人工装料和机械装料。
人工装料多用于公称容量小于3t的电炉,缺点是装料时间长、生产率低、劳动强度大。
料筐顶装料是目前最理想的装料方法,速度快、热损失小,且炉料可事先提前装好,布料合理。
二、对装料的要求为了缩短时间,保证合金元素的收得率,降低电耗和提高炉衬的使用寿命,装料时要求做到:准确无误、装得致密、布料合理及快速入炉。
装料前,配料工要认真按计划炉号、钢种的要求配料,依据不同钢种工艺的要求,认真分析计算,准确配料。
合金吸收率及配料技术公式

合金元素的吸收率及配料技术公式1、 中频感应炉熔炼时,加入铁合金中的合金元素收得率是多少?在整个熔炼过程中碳、硅、锰等元素的变化规律是什么?熔炼低合金钢、单元高合金钢、多元高合金钢时,在配料时怎样计算特合金的加入量? 1)中频感应炉熔炼时合金元素的收得率,见表1表1 合金元素的收得率2)中频炉熔炼中,碳、硅、锰等元素的变化规律:①C 在熔炼全过程要烧损,炉料较好时碳烧损0.03%-0.06%。
废钢等熔清,经预脱氧后取炉前钢样到出钢碳烧损约0.02%(碳钢,低合金钢);②废钢熔清后的残硅:碱性炉约0.1%,中性炉约0.15%,酸性炉约0.25%;③废钢熔清后的残Mn :碱性炉、中性炉约0.2%~0.25%,酸性炉约0.1%~0.15%;④铁合金中的碳100%回收,硫、磷100%回收;⑤铁合金中的硅(稀土硅铁合金)100%回收;⑥酸性炉出钢前出现硅还原现象,钢液中增硅0.05%。
3)熔炼低合金钢时,铁合金加入量按下式计算:序号 合金名称 作用及加入时间 合金元素收得率 碱性炉 中性炉 酸性炉 1 FeSi 合金化,出钢前5~8min 85 90 100 2 FeMn 合金化,出钢前5~8min 90~95 85 75~80 3 FeCr 合金化,出钢前5~8min 95 95 95 4 FeNo 熔毕,或出钢前15~30min 98 95 95 5 FeW 熔毕,或出钢前15~30min 98 95 95 6 FeTi 铝终脱氧后加入,或冲包50~70 50~70 50~70 7 FeV 合金化,出钢前5~-8min (质量分数小于0.3%) 80~9080~90 80~90 合金化,出钢前5~8min (质量分数大于1.0%)95 90 90 8 FeNb 合金化,出钢前5~8min90 90 85 9 FeB 冲包40~60 40~60 40~60 10 金属镍 合金化,出钢前15~30min 98 98 95 11 金属铜 合金化,出钢前15~30min 98 98 95 12 石墨电极粉 增碳,出钢前5~8min 90 90 90 13焦炭粉增碳出钢前5~8min808080铁合金加入量 =4)熔炼单元高合金钢时,铁合金加入量按下式计算:铁合金加入量 =5)熔炼多元高合金钢时,各元素加入量都很大,一种铁合金加入,钢液量随之增大,影响其他元素在钢中的含量,故采用“补加系数”法计算(补加系数是指每加入100kg 合金料需补加的量),程序如下:① 各项合金占有量 =② 纯钢液占有量=100%-各项合金占有量之和 ③ 补加系数 =④ 钢液综合收得率=95%~97%。
感应加热经验公式
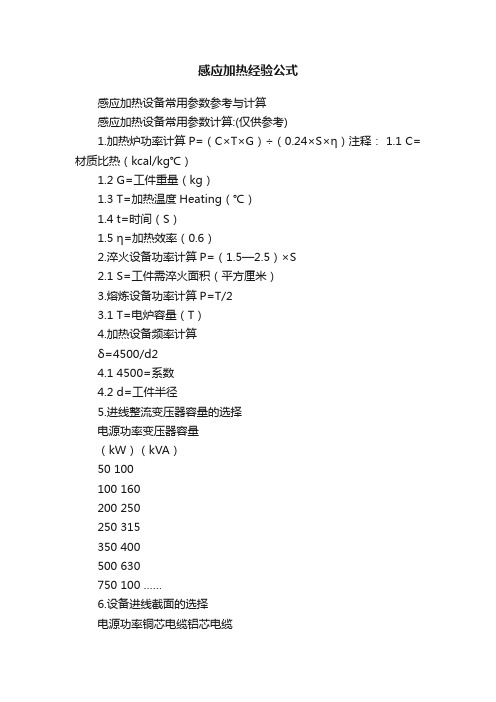
感应加热经验公式感应加热设备常用参数参考与计算感应加热设备常用参数计算:(仅供参考)1.加热炉功率计算P=(C×T×G)÷(0.24×S×η)注释: 1.1 C=材质比热(kcal/kg℃)1.2 G=工件重量(kg)1.3 T=加热温度Heating(℃)1.4 t=时间(S)1.5 η=加热效率(0.6)2.淬火设备功率计算P=(1.5—2.5)×S2.1 S=工件需淬火面积(平方厘米)3.熔炼设备功率计算P=T/23.1 T=电炉容量(T)4.加热设备频率计算δ=4500/d24.1 4500=系数4.2 d=工件半径5.进线整流变压器容量的选择电源功率变压器容量(kW)(kVA)50 100100 160200 250250 315350 400500 630750 100 ……6.设备进线截面的选择电源功率铜芯电缆铝芯电缆(kW)(mm2)(mm2)50 25 35100 50 75200 95 150250 2×70 2×120350 2×95 2×185500 3×95 3×185750 4×95 4×1851000 5×95 5×1857.中频输出电缆截面的选择中频功率电源的输出频率KW kHz0.5 1.0 2.5 4.0 8.0以下电缆截面积单位为:mm250 35 50/90 70 95 120100 50 70 95 2×70 2×95200 95 2×70 2×95 4×70 4×95250 2×70 2×95 3×70 5×90 5×95350 2×95 3×95 4×95 5×100 5×100500 3×95 4×95 5×100 5×150 5×200750 4×95 5×100 5×150 5×200 (5×150)×31000 5×100 5×150 5×200 (5×150)×2 (5×150)×48.冷却水流量的选择8.1 进水压力:0.15—0.3Mpa8.2 冷却水温度在5—30°范围内,水质硬度不超过8度,浑浊度不大于5,PH值在6.5—8的范围内。
电炉配料计算
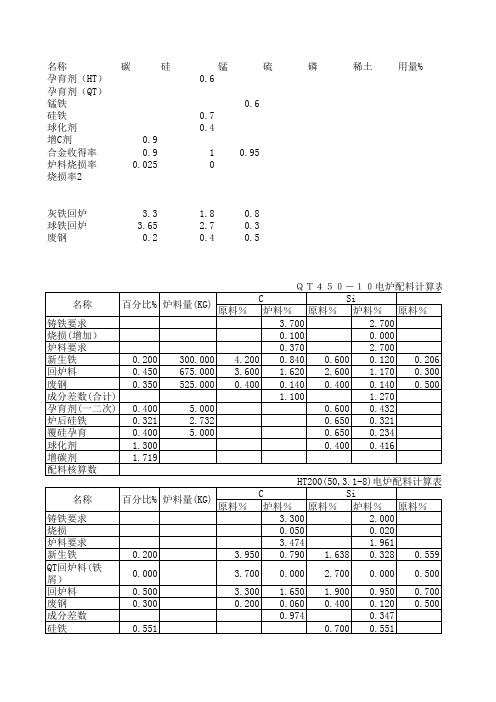
0.046 0.120 0.120 0.050
0.082 0.018 0.080 0.050
0.7 0.8 -0.1
0.040 0.050 0.050
0.008 0.023 0.018 0.048
0.018 0.020 0.050
配料计算表 Mn 炉料% 0.750 0.000 0.750 0.112 0.000 0.350 0.150 0.138 0.325 原料% P 炉料% 原料% 0.100 0.100 0.009 0.000 0.060 0.015 0.016 S 炉料% 0.080 0.080 0.016 0.000 0.040 0.015
名称 孕育剂(HT) 孕育剂(QT) 锰铁 硅铁 球化剂 增C剂 合金收得率 炉料烧损率 烧损率2
碳
硅 0.6
锰
硫
磷
稀土
用量%
0.6 0.7 0.4 0.9 0.9 0.025 1 0 0.95
灰铁回炉 球铁回炉 废钢
பைடு நூலகம்
3.3 3.65 0.2
1.8 2.7 0.4
0.8 0.3 0.5
名称 铸铁要求 烧损(增加) 炉料要求 新生铁 回炉料 废钢 成分差数(合计) 孕育剂(一二次) 炉后硅铁 覆硅孕育 球化剂 增碳剂 配料核算数 名称 铸铁要求 烧损 炉料要求 新生铁
增碳剂 孕育剂 配料核算数
1.202 0.400
0.900
1.202 0.600 0.216
炉内铁水重量 烧损 硅铁 锰铁 废钢 增C剂
目标成份 差额
3.5 3.2 0.3
1.8 1.8 0
重量(千克)
配料计算表 Mn 炉料% 0.300 0.000 0.300 0.041 0.135 0.175 (0.051) 原料% P 炉料% 原料% 0.050 S 炉料% 0.020 0.500 0.004 0.009 0.018 0.045
电炉炼钢铁合金加入量计算法

电炉炼钢铁合金加入量计算法一、计算公式算法举例计算中有关问题的说明1、炉料的收得率炉料的收得率与炉料的好坏,炉料中能被氧化元素的含量以及冶炼方法等有关。
一般而言,炉料的收处率如下:氧化法为95~96%,不氧化法为96~97%,返回吹氧法为95~97%。
炉料的收处率简称收得率。
计算铁合金加入量时以炉料实重进行计算。
炉料实重=炉料重×收得率。
2、铁合金中合金元素的回收率炼钢中使用的镍、钴、铜、钼钨铁、铬铁、锰铁、钒铁、铌铁、矽铁等,作为合金化材料有冶炼操作规程规定的时期加入时,由于这些铁合金元素的回收率相当高,在计算中为了简化起见其回收率均可按100%计算。
在回收率低的元素有硼、钛、铝。
硼铁中硼的回收率一般为30~50%。
钛铁中钛的回收率一般为40~60%。
铝的回收率:当冶炼含铝量为1%左右的钢种时,铝在氧化渣扒出后加入时一般为50~60%,在还末期扒渣后加入时一般为65~80%,当冶炼含铝量较高的钢种时铝的回收率有所升高。
当冶炼含铝量高达5%左右的高铝钢时,铝的回收率可大于95%。
即使是对于硼铁、钛铁和铝,在计算时为了简便起见,同样可以把回收充的因素考虑在所控制的成分之上。
如以冶炼38CrMoAIA钢为例,铝的规格范围为0.70~1.10%,当采用扒还元渣后加入的工艺时,铝按1.20~1.30%加入,而将铝的回收率皆当作100%。
又比如冶炼高矽钢时,出钢前加入矽铁后不再分析矽的含量,这时虽将矽铁中矽的回收率当作100%,但控制成分时应将矽量偏上限控制。
铁合金中合金元素的回收率简称回收率。
收得率与回收率的意义相当,但为了使炉料与铁合金相区别故分别名为收得率与回收率。
在实际冶炼中控制钢的化学成分时,对于冶炼含铬、含锰而对炭量有规格要求的钢种时,为了便于炭量的调整,在加入铬铁锰铁进行合金化时,不宜一下就把铬、锰加到要求达到的成分,而应稍低于要求达到的成分,以便在补加铬铁、锰铁时,可使用高炭铬铁、高炭锰铁来补足不足的炭量。