橡胶密封件模具结构的改进
橡胶制品常见问题及解决方法

不管是何种产品,其实都是有缺陷。
自然橡胶制品也不例外,那该产品比较常见的问题及解决方案有哪些呢吗,下边为您解答。
1、橡胶产品撕裂
原因分析:启模太快,受力不均匀;模具棱角、倒角不合理;隔离剂过多或是过少;胶料流动性差,半成品粘接性差;。
解决方案:启模时制品均匀受力,减小胶料的门黏度,改进模具设计,合理使用隔离剂。
2、橡胶产品缺胶
原因分析:胶料没有充分流动;半成品单耗不足或装胶量不足;模具排气性能差;模温太高。
解决方案:减慢模具上升速度并反复放气;从新制定模具装胶量;改善模具设计,降低模温。
3、橡胶产品出现卷边、抽边、缩边
原因分析:胶料加工性能差。
解决方案:采用铸压、注射法生产降低胶料的门尼黏度。
4、橡胶产品过于粗糙
原因分析:模具表面粗糙,没清洗干净;混炼胶焦烧时间过短。
解决方案:清洗模具;延长焦烧时间。
5、橡胶产品胶边过厚,以至于产品超重
原因分析:模具装胶料过多;平板压力不足;模具没有相应的余胶槽。
解决方案:严格控制半成品单耗;增大平板压力;改进模具设计。
6、橡胶产品有气泡
原因分析:配合剂中含有硫化分解加工时出现窝气;模腔中的空气没有排干净;模具无排气线。
解决方案:模具上增加排气线;生产合模前反复放气,配方中加适量氧化钙
7、橡胶产品出现裂纹
原因分析:胶料有脏物混入;隔离剂添加过多;胶料焦烧不够。
解决方案:保证胶料清洁无污染;合理使用隔离剂;延长焦烧时间。
综上就是橡胶制品常见7大问题及解决方法的介绍,希望对大家进一步的了解有所帮助,同时,如想了解更多有关橡胶制品信息可咨询巩义市鑫业供水材料有限公司。
管接头密封圈模具的改进
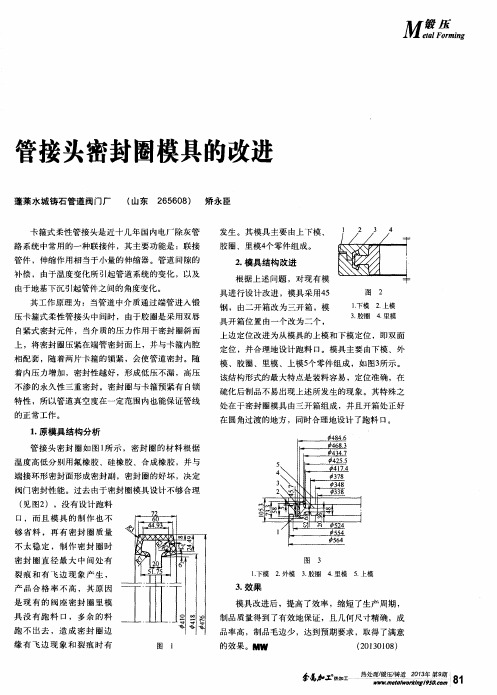
管件 ,伸缩作用相 当于小量的伸缩器。管道 间隙的 补偿 ,由于温度变化所 引起管道 系统的变化 ,以及 由于地基下沉引起管件之 间的角度变化 。 Βιβλιοθήκη 2 . 模具 结构 改进
根据上述问题 ,对现有模
具 进 行 设 计 改进 ,模 具 采 用4 5 钢 , 由二 开 箱 改为 三 开 箱 ,模 具 开 箱 位 置 由一 个 改 为 二 个 ,
1 . 原模具结构 分析
管 接 头 密 封 圈如 图 1 所 示 ,密 封 圈 的 材 料 根 据 温 度 高 低分 别 用 氟 橡胶 、硅 橡 胶 、合 成 橡 胶 ,并 与 端 接 环 形 密封 面 形 成 密封 副 ,密 封 圈的 好 坏 ,决 定 阀 门 密封 性 能 。过 去 由于 密 封 圈模 具 设 计 不够 合 理 ( 见 图2 ) ,没 有 设 计跑 料 口 ,而 且 模 具 的 制 作 也 不 够 省 料 , 再 有 密 封 圈 质 量
图 2
1 . 下模
3 . 胶圈
其工作原理为 :当管道 中介质通过端管进入锻
压卡箍式柔性管接头 中间时 ,由于胶圈是采 用双唇
自紧式 密封 元 件 ,当介 质的 压 力 作用 于 密 封 圈斜 面
2 . 上模 4 . 里 模
上 边 定 位 改进 为 从 模具 的上 模 和 下模 定 位 ,即双 面 定 位 ,并 合理 地 设 计跑 料 口。模具 主 要 由下模 、外 模 、胶 圈 、里 模 、上模 5 个 零 件组 成 ,如 图3 所示 。
上 ,将 密封圈压紧在端管密封面上 ,并与卡箍 内腔
相配套 ,随着两片卡箍的锁紧 ,会使管道密封 。随
着内压 力增加 ,密封性越好 ,形成低压不漏,高压 不渗的永久性三重密封 。密封圈与卡箍预紧有 自锁 特性 ,所以管道真空度在一定范 围内也能保证管线
改进零件模具结构

改进方案的实施步骤
确定改进目标,制定改进方 案
设计新的零件模具结构,进 行模拟分析
制造新的零件模具并进行试 验验证
分析现有零件模具结构的问 题和缺陷
优化和完善改进方案,进行 批量生产
Part Three
零件模具结构改进 的预期效果
提高生产效率
零件模具结构改进能够减少生产时间,提高生产效率。
通过优化模具设计,可以减少废品率,提高产品质量和生产效率。 改进后的模具结构更加稳定可靠,减少了维修和更换的频率,提高了生 产效率。 零件模具结构改进可以降低生产成本,从而提高了企业的市场竞争力。
风险评估:对已识别的风险进行量化和评估,确定其可能造成的影响和损 失
风险控制措施:根据风险评估结果,制定有效的控制措施,降低或消除风 险
风险控制效果评估:定期对风险控制措施进行评估,确保其有效性和可行 性
THANKS
汇报人:XX
Part Five
零件模具结构改进 的实施计划
实施计划的制定
确定改进目标:明确改进的目的和预期效果 分析现状:了解现有零件模具结构的问题和不足 制定改进方案:根据分析结果,制定具体的改进方案和措施 方案评估与优化:对改进方案进行评估,并根据评估结果进行优化和完善
实施计划的执行
制定详细的实施方案
提高产品质量
减少零件模具结构缺陷,提高产品合格率 优化零件模具结构,提高产品精度和稳定性 降低生产成本,提高生产效率 提高产品性能和可靠性,增强市场竞争力
降低生产成本
减少模具制作时间 提高生产效率 降低废品率 减少维护成本
Part Four
零件模具结构改进 的可行性分析
技术可行性分析
现有技术水平:评估当前技术是否能够实现零件模具结构改进 技术发展趋势:分析未来技术发展方向,预测零件模具结构改进的可行性 成本效益分析:评估零件模具结构改进的成本和效益,判断是否具有经济可行性 实验验证:通过实验验证零件模具结构改进的可行性,提供科学依据
橡胶密封件的塑型工艺优化

橡胶密封件的塑型工艺优化一、橡胶密封件概述橡胶密封件是工业领域中不可或缺的组成部分,广泛应用于机械、汽车、建筑等行业。
它们的主要功能是防止流体或气体泄漏,确保设备的正常运行和密封性能。
橡胶密封件的制造工艺直接关系到产品的性能和使用寿命,因此,对橡胶密封件的塑型工艺进行优化,具有重要的实际意义。
1.1 橡胶密封件的种类与特性橡胶密封件根据其材料和结构的不同,可以分为多种类型,包括但不限于O型圈、Y型圈、X型圈等。
每种类型的橡胶密封件都有其独特的物理和化学特性,例如耐温性、耐化学腐蚀性、弹性等。
1.2 橡胶密封件的应用领域橡胶密封件在各个行业中都有广泛的应用。
在汽车行业中,它们用于发动机、变速箱等部件的密封;在建筑行业中,用于门窗、管道等的密封;在机械制造中,用于液压系统、气动系统的密封等。
二、橡胶密封件塑型工艺现状分析当前,橡胶密封件的塑型工艺主要包括混炼、挤出、成型、硫化等步骤。
这些工艺步骤的优化对于提高生产效率、降低成本、提升产品质量具有重要作用。
2.1 混炼工艺混炼是橡胶密封件生产过程中的首要步骤,它涉及到将各种橡胶原料和添加剂混合均匀。
混炼的质量直接影响到橡胶的均匀性和密封件的性能。
2.2 挤出工艺挤出工艺是将混炼好的橡胶通过挤出机形成所需的形状。
挤出工艺的控制对于橡胶密封件的尺寸精度和表面质量至关重要。
2.3 成型工艺成型工艺是将挤出后的橡胶半成品进一步加工成最终产品形状的过程。
这一步骤通常涉及到模具的使用,模具的设计和制造精度对成型质量有着直接的影响。
2.4 硫化工艺硫化是橡胶密封件生产过程中的关键步骤,它涉及到将橡胶在一定条件下加热,使其从线性结构转变为三维网状结构,从而获得所需的弹性和耐久性。
三、橡胶密封件塑型工艺优化策略针对橡胶密封件塑型工艺中存在的问题,可以采取以下优化策略,以提高生产效率和产品质量。
3.1 混炼工艺的优化优化混炼工艺可以通过改进混炼设备、调整混炼参数、使用高性能的添加剂等方法实现。
橡胶模压制品常见缺陷及解决方法

橡胶模压制品常见缺陷及解决方法 :::::::::::::::喷霜混炼胶或硫化胶内部的液体或固体配合剂因迁移而在橡胶制品表面析出形成云雾状或白色粉末物质的现象。
这是由于硫、石蜡、某些防老剂、软化剂的使用量超出了它们在橡胶中的溶解度而引起的。
为防止喷霜,上述各种配合剂用量要适当,对常见的硫黄喷霜可采用不溶性硫黄加以防止。
在橡胶中适当加入松焦油,液体古马隆等可增加胶料对上述配合剂的溶解度,以减少喷霜现象。
喷霜-定义和由来喷霜又名喷出(blooming),是橡胶加工过程中常见的质量问题,它是指未硫化胶或硫化胶中所含的配合剂迁移到表面并析出的现象。
有时,这种喷出物呈霜状结晶物,故习惯上称“喷霜”。
较多见的喷霜物为硫,因为硫黄是通用橡胶中应用最广泛的硫化剂,且在橡胶中的溶解度低因而容易产生喷霜。
其实从喷出物外观来看,也未必都呈霜状,也有呈油状(软化剂、增塑剂)或粉粒状(多为填充剂、防老剂、促进剂等)的物质喷出,甚至炭黑喷出也有所见。
喷霜-防霜剂硅胶也会有喷霜现象,采用双二四硫化剂(通常用在挤出成型工艺)高温分解后会产生低分子量的酸性物质,其与硅橡胶不相容,在存放过程中会转移到硅胶表面结晶从而出现喷霜。
防霜剂主要成分为碱性物质,通过酸碱中和反应来达到防霜的目的。
高硬度的硅胶往往加入比较多的内脱模剂,遇水也会喷白,水的酸性对此有遏制作用硅橡胶模具制作方法及注意事项模具是快速模具里的一种最为简单的方法,一般是用硅胶将RP原型进行复模,但寿命很短,只有10-30件左右!他具有很好的弹性和复制性能,用硅橡胶复制模可不用考虑拔模斜度,不会影响尺寸精度,有很好的分割性,不用分上下模可直接进行整体浇注。
再沿预定的分模线进行切割取出母模就可以了!室温硫化硅橡胶又分为加成型和缩合型两种!原料及配方采用专用模具硅橡胶,该品系以双包装形式出售,A组份是胶料,B组份是催化剂。
配制时要考虑室温、模具的强度和硬度,以此来确定AB组份的重量配制比例。
橡胶模压制品常见缺陷及解决方法

喷霜混炼胶或硫化胶内部的液体或固体配合剂因迁移而在橡胶制品表面析出形成云雾状或白色粉末物质的现象。
这是由于硫、石蜡、某些防老剂、软化剂的使用量超出了它们在橡胶中的溶解度而引起的。
为防止喷霜,上述各种配合剂用量要适当,对常见的硫黄喷霜可采用不溶性硫黄加以防止。
在橡胶中适当加入松焦油,液体古马隆等可增加胶料对上述配合剂的溶解度,以减少喷霜现象。
喷霜-定义和由来喷霜又名喷出(blooming),是橡胶加工过程中常见的质量问题,它是指未硫化胶或硫化胶中所含的配合剂迁移到表面并析出的现象。
有时,这种喷出物呈霜状结晶物,故习惯上称“喷霜”。
较多见的喷霜物为硫,因为硫黄是通用橡胶中应用最广泛的硫化剂,且在橡胶中的溶解度低因而容易产生喷霜。
其实从喷出物外观来看,也未必都呈霜状,也有呈油状(软化剂、增塑剂)或粉粒状(多为填充剂、防老剂、促进剂等)的物质喷出,甚至炭黑喷出也有所见。
喷霜-防霜剂硅胶也会有喷霜现象,采用双二四硫化剂(通常用在挤出成型工艺)高温分解后会产生低分子量的酸性物质,其与硅橡胶不相容,在存放过程中会转移到硅胶表面结晶从而出现喷霜。
防霜剂主要成分为碱性物质,通过酸碱中和反应来达到防霜的目的。
高硬度的硅胶往往加入比较多的内脱模剂,遇水也会喷白,水的酸性对此有遏制作用硅橡胶模具制作方法及注意事项模具是快速模具里的一种最为简单的方法,一般是用硅胶将RP原型进行复模,但寿命很短,只有10-30件左右!他具有很好的弹性和复制性能,用硅橡胶复制模可不用考虑拔模斜度,不会影响尺寸精度,有很好的分割性,不用分上下模可直接进行整体浇注。
再沿预定的分模线进行切割取出母模就可以了!室温硫化硅橡胶又分为加成型和缩合型两种!原料及配方采用专用模具硅橡胶,该品系以双包装形式出售,A组份是胶料,B组份是催化剂。
配制时要考虑室温、模具的强度和硬度,以此来确定AB组份的重量配制比例。
室温在20-25度时,A:B=100:1.5。
室低时(但不能低于10度)则适当增加B组份0.1-0.3份。
联轴器护套橡胶模结构设计的改进

() 3 脱模 困难 , 由于镶块较多 , 型腔相对较 深, 脱模 时制品
与 上 、 模 腔 粘 连 在 一起 , 模 时 经 常要 用 铜 钎 撬 出制 品 , 下 脱 因此
制 品的表面易受损伤 , 工作效率低 ( ) 边多 , 4溢 由于压制 时 , 型腔死角排气差 , 胶料流动不均
具硫化加 压闭合时 , 容易造成型芯偏移 , 很 导柱销 和导柱孔 易
磨损和变形 , 影响定位精度 , 使制品上 、 凹槽分度精 度误 差过 下 大 , 成制 品的壁厚不均。 造
和使用寿命 。 如该联轴器护套橡胶模原设计结构采用直开式镶 块镶嵌压制结构 , 结构不合理 , 加料过程繁琐 , 品脱模 困难 , 制 溢边多 , 制品的致 密性差 , 胶料利用率和生产效率低 :因此 , 模
维普资讯
Eq i me t u p n Ma u a t n e h oo y NO. 2 0 n f cr g T c n lg i 8, 0 7
联 轴器 护 套橡 胶模 结构 设计 的 改进
李恒 扬
( 广西 柳 州 职 业 技 术 学 院 , 西 柳 州 5 5 0 ) 广 4 0 6
中图分类号 :G7 T 6
文献标识码 : A
文章编号 :6 2 5 5 (0 70 — 1 8 O 1 7 — 4 X2 0 )8 0 1 一 3
一
般来说 , 对于同样一 件橡胶制品 , 由于使用 的设备不 同,
销加工得较长 , 使上模的导柱销孑 能对准下模的导柱销。当模 L
加工工艺不同 , 可以设计 出各种不同结构 的模具。模具结构 的 形式直接关系到制 品的质量 、 生产效率 、 模具本身加 ]的难 易 二
橡胶产品基本缺陷产生原因和解决措施方案
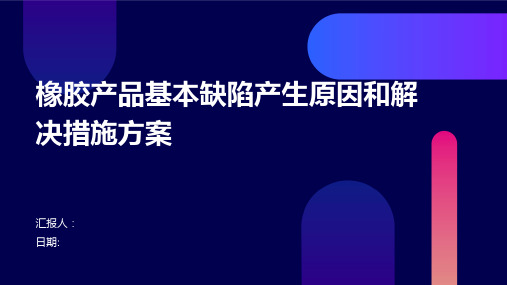
解决措施
针对以上原因,可以采取以下措施:严格控 制原材料的混合质量,保证混炼温度适中, 避免焦烧;优化硫化工艺,确保硫化时间适 当,保证硫化充分。对于已经出现气泡的轮
胎,可以进行返工处理,重新进行硫化。
案例二:橡胶密封圈变形问题解决方案
原因
橡胶密封圈变形通常是由于材料硬度不当、硫化时间过 短或硫化温度过低导致的。此外,密封圈设计不合理或 使用过程中受到不适当的压力也可能导致其变形。
加工问题
加工过程中温度过高或者过低,导 致材料脱皮。
03
解决措施方案
气泡
原因
橡胶材料混合不均匀,或者橡胶材料中存在水分、挥发物等杂质,或者硫化过程中温度和压力不足。
解决措施
加强橡胶材料的质量控制,确保混合均匀,避免杂质的存在;适当提高硫化过程中的温度和压力,保 证橡胶充分硫化。
变形
要点一
原因
橡胶材料硫化不足或者热稳定性差,导致在储存和使用过 程中发生变形。
解决措施
优化配方,添加增粘剂,改进模具设计,选择合适的脱模剂。
02
产生原因分析
气泡
材料问题
原材料不纯净,有杂质。
搅拌问题
搅拌不充分,导致材料混合不均匀。
硫化问题
硫化时间过短,导致气泡不能完全排出。
变形
01
02
03
材料问题
使用的橡胶材料质量不好 ,容易发生变形。
结构设计问题
产品结构设计不合理,导 致受力不均匀,产生变形 。
变形
产生原因
硫化程度不足或局部硫化不均匀,导致橡胶物理性能不稳定。
解决措施
调整硫化剂和促进剂用量,采用多段硫化工艺,加强硫化过程的监控。
表面粗糙