拉丝挤出的膜为何横向厚薄不均
BOPP薄膜中皱纹、条纹的产生原因及解决办法

BOPP薄膜中皱纹、条纹的产生原因及解决办法BOPP薄膜中皱纹、条纹的产生原因及解决办法双向拉伸后的BOPP薄膜经过切边、测厚、电晕处理(或不用),然后进入收卷。
为了适应宽幅高速生产和自动换卷的要求,BOPP收卷设备采用双工位收卷机,收卷方式采用中心主动收卷,并设有张力、压力自动控制系统。
收卷质量好坏直接影响薄膜的成品率、二等品率以及最终的利润。
在大多BOPP生产线上;皱纹、条纹缺陷是经常遇见并很难解决的,为此本文着重分析皱纹、条纹缺陷的产生原因以及介绍控制办法。
收卷张力对皱纹、条纹的影响及解决办法收卷张力实质是收卷速度增量引起的薄膜弹性伸长,只有保持适当的张力,薄膜才能平展地进行卷曲。
张力控制不当是皱纹、条纹产生的―个主要原因,反之控制好张力也是解决皱纹、条纹缺陷的主要办法。
在张力控制参数中,涉及到大小、斜度等因素,不但要控制好每一个因素,而且还要注意相互之间的协同效果。
1.1 张力大小的影响及解决办法张力大小的设定直接影响膜卷收卷质量的好坏,张力设定越大其横向的分配越不均匀,薄膜平整度越差,膜卷某部卷入的空气越不易排出,产生皱纹、条纹缺陷机会越大;张力设定值太小,膜卷在收卷时辊芯易压皱,膜卷硬度偏松,大分切时膜卷辊芯易脱芯,难以收卷。
而BOPP薄膜卷曲后仍有继续结晶而收缩趋势,随膜卷直径增加每圈长度增加纵向收缩量增大,如果生产中以恒定的张力收卷将会造成膜卷外紧内松,膜卷辊芯处大量膜产生皱纹、条纹缺陷(尤其O-4000m 最重)。
表1、表2是实际生产中22μm收缩膜张力(辊芯0―4000m张力)大小--皱纹、条纹产生米数(同温下)。
表1 张力大小对薄膜厚度皱纹和条纹的影响张力设定值(N/m) 70-80 100-110 120-130 140-150 160-170 1号薄膜皱纹和条纹长度,m 1500 1200 800 200 12002号薄膜皱纹和条纹长度,m 1500 700 200 1000 1500 表1(薄膜型号不同)说明生产同种型号膜时应采用某一特定范围内的张力;生产不同型号薄膜时应采用不同范围内的张力;表2说明在生产中不能使用恒定的张力,随着膜卷直径增大张力值要逐渐递减,以便保证膜卷有收缩空间,硬度达到内紧外松。
控制编织袋扁丝的拉伸强度提升措施
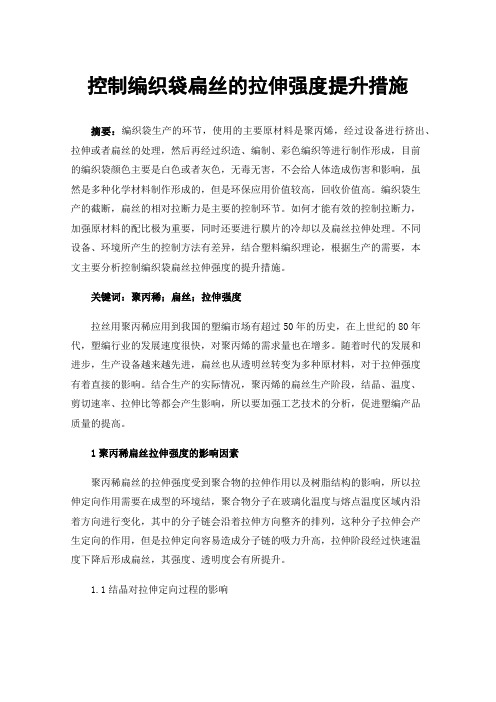
控制编织袋扁丝的拉伸强度提升措施摘要:编织袋生产的环节,使用的主要原材料是聚丙烯,经过设备进行挤出、拉伸或者扁丝的处理,然后再经过织造、编制、彩色编织等进行制作形成,目前的编织袋颜色主要是白色或者灰色,无毒无害,不会给人体造成伤害和影响,虽然是多种化学材料制作形成的,但是环保应用价值较高,回收价值高。
编织袋生产的截断,扁丝的相对拉断力是主要的控制环节。
如何才能有效的控制拉断力,加强原材料的配比极为重要,同时还要进行膜片的冷却以及扁丝拉伸处理。
不同设备、环境所产生的控制方法有差异,结合塑料编织理论,根据生产的需要,本文主要分析控制编织袋扁丝拉伸强度的提升措施。
关键词:聚丙稀;扁丝;拉伸强度拉丝用聚丙稀应用到我国的塑编市场有超过50年的历史,在上世纪的80年代,塑编行业的发展速度很快,对聚丙烯的需求量也在增多。
随着时代的发展和进步,生产设备越来越先进,扁丝也从透明丝转变为多种原材料,对于拉伸强度有着直接的影响。
结合生产的实际情况,聚丙烯的扁丝生产阶段,结晶、温度、剪切速率、拉伸比等都会产生影响,所以要加强工艺技术的分析,促进塑编产品质量的提高。
1聚丙稀扁丝拉伸强度的影响因素聚丙稀扁丝的拉伸强度受到聚合物的拉伸作用以及树脂结构的影响,所以拉伸定向作用需要在成型的环境结,聚合物分子在玻璃化温度与熔点温度区域内沿着方向进行变化,其中的分子链会沿着拉伸方向整齐的排列,这种分子拉伸会产生定向的作用,但是拉伸定向容易造成分子链的吸力升高,拉伸阶段经过快速温度下降后形成扁丝,其强度、透明度会有所提升。
1.1结晶对拉伸定向过程的影响聚丙稀的结晶与扁丝力学存在着直接的关系,首先应综合分析原材料内晶体的含量以及晶体的结晶速率、大小以及形状。
在晶相的聚丙烯拉伸操作中,延伸区域内会存在细颈的结构,从而出现各个部分的尺寸不均匀问题,这是因为在细颈区的温度较高,而其他区域则没有出现拉伸的变化,或者拉伸例比较小,所以造成不同部位的形状不同,厚度也有一定的差异。
关于拉丝模具尺寸波动的分析

关于拉丝模具尺寸波动原因的分析1.拉丝模具的尺寸原因分析1.1模具加工制作水平模具加工制作水平对模具质量的影响,主要体现在两个方面;一是拉丝模的孔型尺寸,二是模孔内表面光洁度。
国外拉丝模具的研磨工艺普遍采用高速机械研磨机,以及表面镀以金刚石的金属磨针,该设备运行平稳,磨针的规格及使用规范化,产品精度高。
模子的孔型尺寸利用轮廓记录仪及孔径测量仪来检测,并用检查拉线模专用的显微镜来检查表面光洁度。
而国内许多厂家还在采用落后的设备,使用手工操作来研磨孔型,因此,存在着以下问题:孔型参数波动较大,难以加工出平直的工作锥;定径区与工作,缩短区交接处易研磨出过渡角,使线材在定径区中产生二次压缩,增加外摩擦力,减短了定径区长度模具的使用寿命;磨损的磨针修复频度因人而异,使用不规范,造成孔型的一致性差。
检测手段也落后,只能依靠目测或者放大镜、显微镜等简单工具检测,而且注重的是模内表面光洁度,对孔型尺寸不能有效检测,更谈不上控制了。
所以模具的加工制作水平是影响模具尺寸的一个原因。
1.2拉丝模在拉丝过程中使用不当因素(1)拉丝面缩率过大,导致模具产生裂痕或破碎。
裂痕或断裂纹绝大部分是内应力释放所产生。
在任何物料结构中,存在内应力是必然的,拉拔线材时产生的内应力本来可以增强金刚石微晶结构,但当拉丝面缩率过大、无法及时润滑从而温升过高就会导致金刚石模具表明部分物料被移走,微晶结构所承受的应力就大大增加,使其更容易产生裂痕或破碎。
(2)线材的拉伸轴线与模孔中心线不对称,致使对线材和拉线模产生应力作用不均匀,而机械振动产生的冲击也会对线材和拉线模造成很高的应力峰值,两者都将加速模子的磨损。
(3)因退火不均匀而造成的线材硬度不均匀等因素容易造成金刚石拉丝模具过早产生疲劳损伤,形成环形沟槽,加剧模孔磨损。
(4)线材表面粗糙,表面粘附氧化层、砂土或其他杂质等会使模具过快磨损。
当线材通过模孔时,硬、脆的氧化层及其他粘附杂质会象磨料一样地造成拉线模模孔很快磨损及擦伤线材表面。
拉丝生产工艺
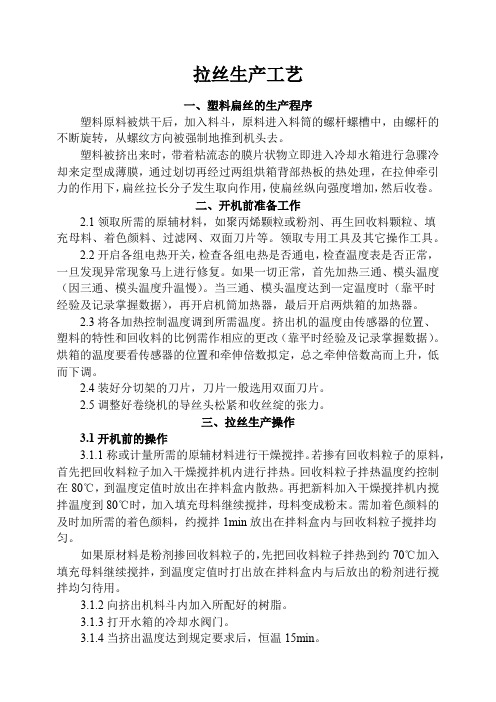
拉丝生产工艺一、塑料扁丝的生产程序塑料原料被烘干后,加入料斗,原料进入料筒的螺杆螺槽中,由螺杆的不断旋转,从螺纹方向被强制地推到机头去。
塑料被挤出来时,带着粘流态的膜片状物立即进入冷却水箱进行急骤冷却来定型成薄膜,通过划切再经过两组烘箱背部热板的热处理,在拉伸牵引力的作用下,扁丝拉长分子发生取向作用,使扁丝纵向强度增加,然后收卷。
二、开机前准备工作2.1领取所需的原辅材料,如聚丙烯颗粒或粉剂、再生回收料颗粒、填充母料、着色颜料、过滤网、双面刀片等。
领取专用工具及其它操作工具。
2.2开启各组电热开关,检查各组电热是否通电,检查温度表是否正常,一旦发现异常现象马上进行修复。
如果一切正常,首先加热三通、模头温度(因三通、模头温度升温慢)。
当三通、模头温度达到一定温度时(靠平时经验及记录掌握数据),再开启机筒加热器,最后开启两烘箱的加热器。
2.3将各加热控制温度调到所需温度。
挤出机的温度由传感器的位置、塑料的特性和回收料的比例需作相应的更改(靠平时经验及记录掌握数据)。
烘箱的温度要看传感器的位置和牵伸倍数拟定,总之牵伸倍数高而上升,低而下调。
2.4装好分切架的刀片,刀片一般选用双面刀片。
2.5调整好卷绕机的导丝头松紧和收丝绽的张力。
三、拉丝生产操作3.1开机前的操作3.1.1称或计量所需的原辅材料进行干燥搅拌。
若掺有回收料粒子的原料,首先把回收料粒子加入干燥搅拌机内进行拌热。
回收料粒子拌热温度约控制在80℃,到温度定值时放出在拌料盒内散热。
再把新料加入干燥搅拌机内搅拌温度到80℃时,加入填充母料继续搅拌,母料变成粉末。
需加着色颜料的及时加所需的着色颜料,约搅拌1min放出在拌料盒内与回收料粒子搅拌均匀。
如果原材料是粉剂掺回收料粒子的,先把回收料粒子拌热到约70℃加入填充母料继续搅拌,到温度定值时打出放在拌料盒内与后放出的粉剂进行搅拌均匀待用。
3.1.2向挤出机料斗内加入所配好的树脂。
3.1.3打开水箱的冷却水阀门。
钢丝性能不均匀问题探讨_吴中萱

钢丝性能不均匀问题探讨吴中萱(冶金工业部金属制品研究院 郑州450007)摘 要: 钢丝性能不均匀是我国钢丝质量存在的一个普遍性问题。
重点讨论盘条质量,拉丝、热处理工序对钢丝性能的影响。
认为化学成分的波动及偏析,钢的纯净度及轧制工艺是影响盘条质量的主要因素。
着重讨论了拉丝机冷却系统的影响。
对如何确定奥氏体化温度及时间、铅淬火温度提出了有益的建议与方法。
关键词: 钢丝 性能 盘条 拉丝 热处理Inquiring into the Irregularity of Steel Wire PropertiesWu Zhon gxu an(T he Research I nstitute of Steel W ire Pr oducts under M inistry of M etallurgical Industr y 450007)Abstract : T he ir reg ularity of steel w ire pro perties is a commo n pr oblem in the quality of steel w ire made in China 1T he effects of wir e rod quality,wir e-drawing and heat-tr eatment processes on steel wire proper ties are discussed emphatica-l ly 1It is considered that the fluctuation and segregation of elemental composition,the pur ity of steel and the rolling techno-l og y ar e the main factors affecting t he quality of wir e rod 1T he effects of cooling system of w ire dr aw ing machine ar e em -phatically di scussed 1Some useful advices and met hods on how to deter mine austenizing temperature and time and patenting temperatur e are put forward 1Keywords : steel w ire; property; wir e rod; w ire draw ing ; heat-tr eatment钢丝性能不均匀是个普遍性问题,也是我国与钢铁强国钢丝质量差距中的一个重要方面。
吹膜工艺的常见问题

吹膜工艺的常见问题1.问题1:薄膜出现褶皱原因:薄膜横向厚度不均匀,哪怕是很微小,经过积累后也可造成比较明显的褶皱,影响落膘实验、薄膜撕裂实验、薄膜摩擦系数等的测定数据。
解决方法:(1)降低熔体温度,可以有效降低熔体流动性,在模头挤出时比较结实,不因冷却风波动使膜泡歪斜而造成薄膜冷却不均。
(2)减少冷却风量或调解冷却风不匀的情况。
(3)人字板的夹角过大,使得薄膜在短时间内被压扁,因而出现褶皱的问题,应适当减小人字板的夹角。
(4)膜口挤料不均匀,应调解口模,使之处于竖直状态。
(5)收卷辊张力过大把膜拉褶。
应适当减小收卷辊张力。
2.问题2:薄膜透明度差原因:主要影响因素是树脂原料,降低结晶度及使球晶细小,特别是添加剂的影响。
解决方法:(1)挤出温度偏低,熔体塑化不良,透明度较大,应适当提高熔体温度。
(2)冷却效果不佳,影响了透明度,应适当增大冷却风量。
(3)树脂粒子中含有大量水分,应充分干燥粒子。
3.问题3:薄膜鱼眼多原因:树脂中的析出物造成的,不能从根本上消除。
主要方法:(1)一定时间后,加大螺杆速度,提高熔体挤出压力,带走析出物。
(2)定期清洁模具头。
(3)适当提高熔体温度,充分塑化。
4.问题4:薄膜横向厚度不均匀.原因:在模口的出料量不均匀。
解决方法:(1)模具唇间隙调节不当,需局部调整或全部重新调整。
(2)模腔中有杂物,从而引起物流紊乱,出料不均,应当定期清洗口模。
(3)熔体压力或温度过高或波动太大,这样造成挤出熔流不稳,影响厚度不均,可调解温度,挤出速度改善。
5.问题5:膜泡扭动不稳原因:外部原因:如吹膜机没有在封闭区域内,室内对流严重,造成膜泡扭动解决方法:关闭门窗即可。
内部原因:(1)模具唇间隙调节不当,出料不均匀。
解决方法:需局部调整或全部重新调整。
(2)冷却风不匀。
解决方法:调节冷却风使其均匀。
(3)人字板的夹角过大。
解决方法:应适当减小人字板角度。
结论要想使试验数据准确,就必须吹制出优质的膜片试样,而吹制出优质的膜片,就难免会遇到上述问题,那么就可以参照上面论述的方法加以解决。
挤出薄膜出现条纹的原因
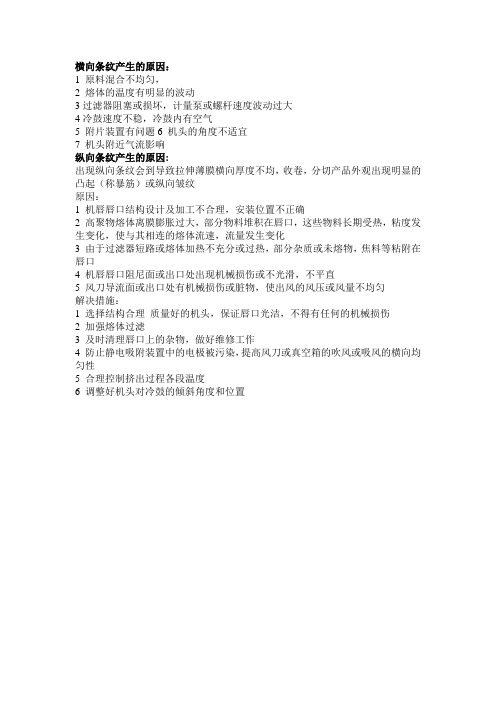
横向条纹产生的原因:
1 原料混合不均匀,
2 熔体的温度有明显的波动
3过滤器阻塞或损坏,计量泵或螺杆速度波动过大
4冷鼓速度不稳,冷鼓内有空气
5 附片装置有问题
6 机头的角度不适宜
7 机头附近气流影响
纵向条纹产生的原因:
出现纵向条纹会到导致拉伸薄膜横向厚度不均,收卷,分切产品外观出现明显的凸起(称暴筋)或纵向皱纹
原因:
1 机唇唇口结构设计及加工不合理,安装位置不正确
2 高聚物熔体离膜膨胀过大,部分物料堆积在唇口,这些物料长期受热,粘度发生变化,使与其相连的熔体流速,流量发生变化
3 由于过滤器短路或熔体加热不充分或过热,部分杂质或未熔物,焦料等粘附在唇口
4 机唇唇口阻尼面或出口处出现机械损伤或不光滑,不平直
5 风刀导流面或出口处有机械损伤或脏物,使出风的风压或风量不均匀
解决措施:
1 选择结构合理质量好的机头,保证唇口光洁,不得有任何的机械损伤
2 加强熔体过滤
3 及时清理唇口上的杂物,做好维修工作
4 防止静电吸附装置中的电极被污染,提高风刀或真空箱的吹风或吸风的横向均匀性
5 合理控制挤出过程各段温度
6 调整好机头对冷鼓的倾斜角度和位置。
压延薄膜(片材)成型故障的成因及对策

(11)辊筒中部区域的供风量不足。应增加辊筒中部区域的冷却,还可在解脱辊前增设风冷装置
纵向厚度不均匀
(1)熔料的剥离性能较差,有粘辊倾向。应调整原辅材料的配方,改善熔料的剥离性能。 (2)熔料混炼不均匀。应加强混炼。
(3)辊筒表面有污物。应清除辊面?亏物,保持辊而清洁。
应增加辊筒中部区域的冷却还可在解脱辊前增设风冷装置纵向厚度不均匀1熔料的剥离性能较差有粘辊倾向
压延薄膜(片材)成型故障的成因及对策
故障名称
成 因 及 对 策
横向厚度不均匀
(1)辊温分布不均匀,辊筒两端温度太低。应适当调整辊筒表面温度,使其分布均匀。 (2)辊隙压力太大,引起辊筒弯曲。应适当调整辊筒间隙。
(3)辊简表面有污物。应清理辊面,去除污物。
(4)熔料混炼的均匀性太差。应加强混炼,提高塑化的均匀性。
(5)润滑剂混合不够均匀。应增加混合时间,使润滑剂分散均匀。
<6)增塑剂分散不均匀。应加强混炼,使其分散均匀。
(7)供料不均匀。应向辊隙内均匀供料。
(8)辊筒的轴交叉角度太大。应适当调小。
(9)辊筒的形体尺寸精度较差,无法满足成型要求。应修整辊筒,提高形体精度。
(10)供料不均匀。应向辊隙内均匀供料。
(11)出膜处的辊筒温度太低。应适当提高。
(12)润滑剂用量太多。应适当减少。
(13)增塑剂和延展剂用量不当。应适当调整。
(14)压延机传动齿轮模数太大或传动不平稳。应进行调整和检修
表面水波纹
(1)辊筒温度太低。应适当提高。
(2)辊筒表面温度不均匀。应减小辊筒轴向的温度差,可利用远红外加热器进行局部温度补偿。
(3)牵引速度太快。应适当减慢。
- 1、下载文档前请自行甄别文档内容的完整性,平台不提供额外的编辑、内容补充、找答案等附加服务。
- 2、"仅部分预览"的文档,不可在线预览部分如存在完整性等问题,可反馈申请退款(可完整预览的文档不适用该条件!)。
- 3、如文档侵犯您的权益,请联系客服反馈,我们会尽快为您处理(人工客服工作时间:9:00-18:30)。
拉丝挤出的膜为何横向薄厚不均
节选自《拉丝疑难问题分析及处理》之二百九十五
王永仁著
【四川来电】我单位的拉丝机组,挤出机模口挤出的熔融膜横向薄厚不均,有的地方厚,有的地方薄,很难调整,请问除了模口间隙不均,还有哪些原因?
【答疑参考】挤出机挤出熔膜横向薄厚波动,模口间隙是主要原因,除此,还有其它原因,归纳起来如下:
1、模口间隙调节不均
模口间隙不均,可能是由于调节不当。
如冷态调节后,检测均匀,可是加热后模唇变形又不均匀,应当再进行热态调节。
切莫企图把模口间隙调小,以便使挤出的熔膜变薄,因为强行把模口间隙调小,在长期受热过程中会产生“时效”变形,膜口间隙更难调节。
应当减少挤出量,用提高牵引速度(一牵)来把熔膜拉薄。
2、模口材质和加工精度
模口材质应当是耐热钢,不耐热钢在反复加热过程中会产生热变形并难恢复,使用一段时间后难调节模口间隙;模口的流道加工应当很光滑,精度很高,把熔体流动阻力降低到最小。
3、模口流道形状
模口流道形状非常重要,设计时要充分考虑不同树脂流到模唇远近各部位的阻力降尽量相等,挤出的熔膜才能均匀,如衣架式平模头。
4、模口各部位温度
模口各部位加热温度,对粘流状态的熔体在模口整个宽度上各个部位流动速度影响很大,温度高的部位熔体流动快,熔膜可能厚。
为此,合理设计模口整个宽度上的加热元件分布和功率很关键。
5、原料流变行为
原料的流变行为,包括原料的熔融指数、分子量分布、熔体流动粘度等对熔膜挤出后拉丝的平模头各部位薄厚有相当的影响。
能适用拉丝挤出的树脂,只有拉丝级料才能拉丝。
粉料不如粒料挤出薄膜均匀,再生料不如粉料挤出薄膜均匀。
6、模口间隙过窄
设计的模口间隙过窄,或调节的模口间隙过窄,熔体流动通过时的阻力增大。
由于温度难免非常均匀,流道阻力难免非常均匀,而且挤出胀大量也不等,使熔膜挤出阻力不均,产生薄厚不均。
如果模口间隙略大,这些影响因素相对减弱。
7、机头压力不足等
机头压力不足,螺杆混炼不均,滤网半堵塞状态等,也可能使挤出的膜片薄厚不均。