009-热轧钼板技术方案及轧制规程计算
热轧钢板的工艺流程

热轧钢板的工艺流程热轧钢板是一种常见的金属材料,广泛应用于建筑、机械制造、汽车制造等领域。
热轧钢板的生产工艺流程复杂多变,包括原料准备、炼钢、铸坯制备、热轧、表面处理等多个环节。
本文将详细描述热轧钢板的生产工艺流程,并对各个环节进行分析和解释。
一、原料准备热轧钢板的生产从原料准备开始,主要包括铁矿石、焦炭、石灰石、废钢等原材料的加工和准备。
首先,铁矿石、焦炭和石灰石等原料需经过破碎、研磨等工艺处理,将原料粉碎成一定粒径的颗粒。
然后,将粉碎后的原料混合配比,并送入高炉进行炼钢过程。
二、炼钢炼钢是制备热轧钢板的重要环节,主要包括高炉冶炼、转炉冶炼、电炉冶炼等工艺过程。
高炉冶炼是最常见的炼钢方式,其工艺流程包括炉料装料、炉料下料、喷吹燃料、给料、炉内反应等工序。
高炉内的铁水经过初步精炼后,将得到炼钢的母渣和初生铁。
三、铸坯制备炼钢后的母渣和初生铁经过连铸成坯,得到连铸坯。
连铸是将熔炼后的金属通过连续浇铸,制备成一定尺寸和形状的坯料。
连铸坯的质量和形状对后续的热轧工艺过程具有重要影响。
常用的连铸设备有直接暴露铸、直立式连铸和弧炉连铸等形式。
四、热轧热轧是将铸坯进行加热到一定温度后,经过轧制、冷却等工序,最终制备成所需的厚度、宽度和长度的钢板。
热轧工艺包括加热、轧制、冷却等多个过程。
首先,铸坯通过加热炉进行加热至适宜的温度。
然后,将加热后的铸坯送入轧机进行轧制,经过粗轧、中轧和精轧等道次,将铸坯制备成定尺寸的中间板。
最后,中间板经过冷却,得到最终的热轧钢板。
五、表面处理热轧钢板的表面处理是为了改善钢板的表面质量和提高防腐蚀性能。
表面处理包括酸洗、磷化、涂层等工艺。
首先,将热轧钢板进行酸洗处理,去除表面氧化皮、锈蚀等杂质。
然后,进行磷化处理,形成一层磷化膜,增加钢板的防腐蚀性能。
最后,进行涂层处理,给钢板表面涂覆一层保护层,提高钢板的表面光泽度和耐腐蚀性能。
六、质检热轧钢板的生产过程需要进行质量检验,以确保产品符合相关标准和要求。
热轧板带钢轧制规程设计

热轧板带钢轧制规程设计一、引言热轧板带钢是一种广泛应用于工业领域的金属材料,其性能的稳定性和质量的优越性对产品的质量和使用寿命至关重要。
因此,热轧板带钢的制造过程需要遵循一定的规程和标准,以确保产品质量的稳定性。
本文将介绍一个热轧板带钢的轧制规程设计。
二、设计目标本轧制规程的设计目标是制定一套科学合理的生产工艺和操作规程,以确保热轧板带钢的质量和性能达到预期要求。
具体的设计目标包括:1.确定合适的轧制温度和轧制速度,以确保给定的产品尺寸和机械性能的要求。
2.设计适当的冷却方式,以确保产品在冷却过程中达到理想的组织结构。
3.确定合适的轧制压力和辊缝尺寸,以确保产品的形状和尺寸的精度。
4.设计适当的轧制工艺和操作规程,以确保生产过程的稳定性和可控性。
5.设计合适的质量检验方法和标准,以确保产品的质量符合要求。
三、设计思路本轧制规程的设计思路是在充分了解产品需求和原材料性能基础上,通过迭代优化的方式确定最佳的轧制工艺和操作规程。
具体的设计思路包括:1.通过分析产品的尺寸要求、力学性能要求和成分要求等,确定轧制温度和轧制速度的范围。
根据产品的板厚和钢种,选择适当的温度和速度条件,以满足产品的性能要求。
2.设计合适的冷却方式,以确保产品在冷却过程中达到理想的组织结构。
根据产品的厚度和形状,选择适当的冷却方式,并确定冷却速度、冷却介质等参数。
3.确定合适的轧制压力和辊缝尺寸,以确保产品的形状和尺寸的精度。
通过分析产品的厚度、宽度和长度要求,选取合适的辊缝尺寸,并确定合适的轧制压力。
4.设计合适的轧制工艺流程和操作规程,以确保生产过程的稳定性和可控性。
根据产品的尺寸和性能要求,确定轧制的工艺流程,并设计详细的操作规程。
5.设计合适的质量检验方法和标准,以确保产品的质量符合要求。
制定合适的质量检验方法和标准,进行产品的质量检验和评价。
四、设计步骤1.分析产品需求和原材料性能,确定轧制温度和轧制速度的范围。
2.设计合适的冷却方式,确定冷却速度和冷却介质。
热轧工艺流程

热轧工艺流程热轧是一种重要的金属加工工艺,主要用于生产各种类型的金属板材、型材和管材。
热轧工艺流程是指将金属坯料加热到一定温度后,通过轧机进行塑性变形,最终得到符合要求的金属产品的加工过程。
本文将介绍热轧工艺的基本流程和关键技术点。
首先,热轧工艺的第一步是原料准备。
通常情况下,原料是金属的坯料,如钢坯、铝坯等。
在进行热轧之前,需要对坯料进行除锈、清洁等预处理工作,以确保轧制出的产品表面质量。
第二步是加热。
将预处理好的坯料送入加热炉中进行加热。
加热的目的是使金属坯料达到一定的塑性温度,以便在轧制过程中能够获得良好的塑性变形能力。
第三步是轧制。
加热后的坯料经过轧机的多道次轧制,逐渐变形成所需的形状和尺寸。
在轧制过程中,需要控制好轧制温度、轧制速度、轧制力度等参数,以确保产品的成形质量。
第四步是冷却。
经过轧制后的金属产品需要进行冷却处理,以固定其内部组织结构,提高产品的硬度和强度。
最后一步是整理和检验。
经过冷却处理的金属产品需要进行整理,包括修整边角、切割成所需的长度等工序。
同时,还需要对产品进行质量检验,确保产品符合标准要求。
在热轧工艺流程中,还有一些关键技术点需要特别注意。
首先是加热温度的控制,加热温度过高或过低都会影响产品的成形质量。
其次是轧制参数的控制,包括轧制温度、轧制速度、轧制力度等,这些参数的选择对产品的成形质量有着重要影响。
此外,冷却工艺和质量检验也是热轧工艺中需要重点关注的环节。
总的来说,热轧工艺流程是一个复杂的加工过程,需要在每个环节都严格控制各项参数,以确保最终产品的质量。
通过不断优化工艺流程和技术手段,可以提高产品的成形质量和生产效率,从而满足市场对金属制品的需求。
希望本文能够对热轧工艺有所了解,并在实际生产中加以应用和完善。
热轧板材的制作方法介绍
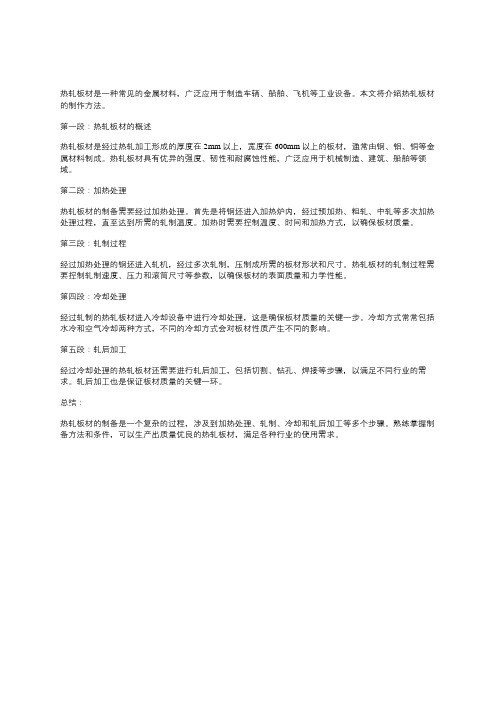
热轧板材是一种常见的金属材料,广泛应用于制造车辆、船舶、飞机等工业设备。
本文将介绍热轧板材的制作方法。
第一段:热轧板材的概述
热轧板材是经过热轧加工形成的厚度在2mm以上,宽度在600mm以上的板材,通常由钢、铝、铜等金属材料制成。
热轧板材具有优异的强度、韧性和耐腐蚀性能,广泛应用于机械制造、建筑、船舶等领域。
第二段:加热处理
热轧板材的制备需要经过加热处理。
首先是将钢坯进入加热炉内,经过预加热、粗轧、中轧等多次加热处理过程,直至达到所需的轧制温度。
加热时需要控制温度、时间和加热方式,以确保板材质量。
第三段:轧制过程
经过加热处理的钢坯进入轧机,经过多次轧制,压制成所需的板材形状和尺寸。
热轧板材的轧制过程需要控制轧制速度、压力和滚筒尺寸等参数,以确保板材的表面质量和力学性能。
第四段:冷却处理
经过轧制的热轧板材进入冷却设备中进行冷却处理,这是确保板材质量的关键一步。
冷却方式常常包括水冷和空气冷却两种方式,不同的冷却方式会对板材性质产生不同的影响。
第五段:轧后加工
经过冷却处理的热轧板材还需要进行轧后加工,包括切割、钻孔、焊接等步骤,以满足不同行业的需求。
轧后加工也是保证板材质量的关键一环。
总结:
热轧板材的制备是一个复杂的过程,涉及到加热处理、轧制、冷却和轧后加工等多个步骤。
熟练掌握制备方法和条件,可以生产出质量优良的热轧板材,满足各种行业的使用需求。
热轧钢板技术规范

深圳市容光机电有限公司SHENZHEN RONG GUANG ELECTRONICS MACHINES EQUIPMENT CO.,LTD. 文件编制部门热轧钢板技术规范文件修订信息记录表目录一. 目的 (4)二. 适用范围 (4)三. 引用/参考标准或资料 (4)四. 术语及其定义...........................................................4。
五. 热轧钢板的技术要求 (4)1 常用牌号及化学成分.................................................... . 52 力学性能 (6)3 夏比(V 型缺口)冲击试验 (6)4 工艺性能 (6)5 表面质量 (6)6 不平度 (6)7 尺寸允许偏差 (7)六. 检验和试验 (8)1 试验方法 (9)2 检验规则 (9)3 检验报告 (9)4 封样 (9)5 说明 (9)一. 目的规范公司结构件原材料为热轧钢板的质量要求,以利于对原材料的质量控制和检验,为设计开发时选择原材料提供依据。
二. 适用范围本规范适用于公司结构件原材料为3.5mm~5mm 板厚的热轧钢板的来料检验以及设计人员对热轧钢板的选用。
三. 引用/参考标准或资料下列标准包含的条文,通过在本规范中引用而构成本规范的条文。
凡是注日期的引用标准,其随后所有的修改单(不包括勘误的内容)或修订版均不适用于本规范,然而,鼓励根据本规范达成协议的各方研究是否可使用这些文件的最新版本。
凡是不注日期的引用文件,其最新版本均适用于本规范。
GB/T 222-2006 钢的成品化学成分允许偏差GB/T 223 钢铁及合金化学分析方法GB/T 20066-2006 钢和铁化学成分测定用试样的取样和制样方法GB/T 228 金属材料室温拉伸试验方法GB/T 229-2007 金属材料夏比摆锤冲击试验方法GB/T 232 金属材料弯曲试验方法GB/T 2975 钢及钢产品力学性能试验取样位置及试样制备Q/ASB 271-2006 结构用热连轧钢板和钢带Q/ASB 330-2004 冷轧或冷成型用热连轧钢板和钢带Q/ASB 331-2004 普通结构用热连轧钢板和钢带Q/ASB 269-2006 热连轧钢板和钢带的尺寸、外形、重量及允许偏差Q/ASB 81 热轧钢板和钢带包装、标志及质量证明书GB 2828 逐批检查计数抽样程序及抽样表(适用于连续批的检查)GB 2829 周期检查计数抽样程序及抽样表(适用于生产过程稳定性的检查)IV-TSP-000811 材料标注规范四. 术语及其定义钢板:含碳量低于2.11%的平板状的铁碳合金称为钢板。
热轧讲义

热轧工艺操作技术规程一, 热轧工艺技术规程制定原则热轧轧制工艺制度主要包括变形制度(主要是确定总的变形量和道次变形量),速度制度(主要是确定各道次速度)和温度制度(主要是确定轧制时的温度区间)。
热轧工艺技术规程有三大类; 1.技术规程(包括安全操作规程)2.操作规程3. 工艺规程。
1, 热轧轧制压下规程设定1)板坯尺寸的确定:H = (100∽150)h H 为坯厚,h 为成品厚。
Lmax ≤B1―(200∽300) B1为加热炉内宽。
B = b+(50∽100) B 为坯宽,b为成品宽。
Lmin≥Bg+(100∽200) Bg为炉子固定梁间距。
2)粗轧机组压下量分配在粗轧机组轧制时由于轧件温度高,变形抗力小,塑性好,轧件又短,应尽可能采用大的压下量,考虑到粗精轧节奏的平衡,一般在粗轧机上的变形量约为总变形量的70%∽80%。
3)精轧机组压下量分配精轧机压下率分配的原则:精轧机压下量为总压下量的(10∽15)%,F1为便于咬钢尽可能大,比设备允许的最大值稍小,一般为(40∽50)%, F2 ∽F4尽可能给予最大压下量,F5 ∽ F7压下量应逐道减少,F7为(10∽15)%,对薄的板F7的压下率可以取得更小点。
2.热轧轧制速度制度设定图1 精轧机末架轧机的速度曲线热轧精轧机组的末架轧机的速度曲线如上图1所示,1点为穿带开始时间,选用的速度约为10m∕s 穿带速度,2点表示带钢头部出末架轧机后,以0.05 ∽0.1 m∕s2 加速度开始第一级加速,3点为带钢咬入卷取机后以0.05 ∽0.2 m∕s2加速度开始第二级加速, 4点表示带钢以工艺设定的最高速度轧制,5点为带钢尾部离开轧机机组中的第三架时, 机组开始减速,速度降到15 m∕s,6点为以15 m∕s 速度轧制等到待抛出,7点表示带钢尾部离开精轧机组开始第二级减速, 降到穿带速度,8点为开始以穿带速度等待下一条带钢,9表示下一条带钢开始穿带。
穿带速度取决于终轧温度,轧后冷却能力,卷取温度和卷取机咬入的稳定性来确定,一般在11 m∕s以下(指末架速度) 。
钼板轧制工艺 -回复

钼板轧制工艺-回复钼是一种重要的金属材料,具有高熔点、高密度、耐腐蚀等优异特性,因此在航空航天、电子、化工等领域有着广泛的应用。
而钼板则是钼材料的一种常见形式,它广泛用于制造航天器外壳、高温容器、电子元器件等。
钼板的制造是一个复杂的工艺过程,需要经过多个步骤来实现。
本文将以钼板轧制工艺作为主题,详细介绍钼板的制造过程。
第一步:原料准备钼板的制造首先需要准备优质的钼材料。
一般常用的原料是金属钼粉,它经过筛选、清洗等处理,确保材料的纯度和质量。
第二步:钼粉压坯将经过处理的钼粉放入模具中,施加一定的压力,使钼粉成型。
这个过程叫做钼粉压坯,通过调整压力和模具形状,可以使得钼粉得到所需的形状和尺寸。
第三步:烧结钼粉压坯完成后,需要进行烧结处理。
烧结是将压坯放入烧结炉中,在高温下进行加热处理,使得钼粉颗粒之间发生结合,形成致密坚固的结构。
烧结的加热温度和时间是根据具体材料的要求来确定的。
第四步:热轧烧结完成后的钼坯需要经过热轧工艺来得到所需的钼板。
热轧是指将钼坯加热至高温后通过轧机进行连续轧制的过程。
首先,将钼坯加热至适当温度,一般在1,100C到1,300C之间。
然后,将加热后的钼坯放入轧机中,通过一系列辊轧制,逐渐将厚重的钼坯轧制成薄板。
在热轧过程中,还需要根据需要进行多次轧制,以得到所需的板材尺寸和表面质量。
第五步:退火经过热轧后的钼板会出现一定的变形和应力,为了消除这些变形和应力,需要进行退火处理。
退火是将钼板加热至一定温度后,在恒定温度下保温一段时间,然后缓慢冷却。
这个过程有助于钼板恢复其本身的结构和性能,并提高板材的延展性和加工性能。
第六步:粗修磨经过退火处理的钼板需要进行粗修磨。
粗修磨是将钼板的表面进行打磨和修整,以去除可能存在的瑕疵和不良表面状态,并提升钼板的光洁度和平整度。
第七步:精修磨粗修磨后的钼板还需要进行精修磨。
精修磨是对钼板进行更加细致的打磨和修整,以进一步提高钼板的表面质量和光洁度。
热轧轧制计划编制规范

热轧厂轧制计划编制规范1总则●炼铁厂应按炼钢厂的冶炼计划提供铁水:●炼钢厂应按热轧厂热装模式编制计划进行冶炼:●储运公司按热轧厂热装结构编排送料日程:●热轧厂根据计划及实际到料情况适时编制轧制单位进行热装轧制:●从用户需求到热轧计划,从热轧计划到炼钢计划,从炼钢计划到炼铁计划,根据各个单位的日程进度进行优化,进行整合对应,最终严格执行:实现以上目标是热轧厂实现有效热装计划的前提条件,而热轧厂轧制计划模式是整个热送热装的关键,问题直接影响热轧线正常的轧制单位编制及生产,根据以上问题,特制定特殊时期轧制单位编制要求,有关单位遵照执行:2 轧制单位编制总则:2.1 单位结构确定:轧制宽度1200140016001000(图1)典型轧制单位计划图轧制厚度1:次主轧材3:主轧材1烫辊材过渡材单位厚度正向过度限制54321800700600500400300200● 烫辊材(见图中1区):开轧规格,质量要求三级:● 过渡材(见图中2区):开轧规格与主轧规格之间的过渡材,质量要求二级,如果主材与过渡材轧制断面相同,可直接过渡到主轧材,单位中大的宽度变化中间的规格也成为过渡材:主轧材(见图中3区):单位主体,为单位的最大宽度,质量要求一级,分配主要轧制量轧制长度:●次主轧材(见图中4区):单位次主体或主体,为单位的较窄或最窄宽度,最窄宽度轧制前需过渡适量中间规格达到最小宽度,质量,一级或二级,单位结束时过渡到质量要求三级:●正常和标准单位,轧制量小于75km时,可以不使用工作辊窜辊:●原则上窄料单位采用逐步缩小行程的窜辊方式,宽料单位采用大行程的窜辊方式,单位结束前的最后1~2批,轧制2.5以下规格时,窜辊行程小于50注:质量要求:一级:热轧商品材,表面质量及尺寸要求最高(标准上限):二级:热轧商品材或冷轧材,质量要求次之;三级:再加工材,如供冷轧等,无特殊质量要求;单位编制必须保证热轧产品所有的质量要求,同时实物质量应高于标准要求,具体要求建关质量标准,故需限量轧制,在此基础上,划分产品质量级别。
- 1、下载文档前请自行甄别文档内容的完整性,平台不提供额外的编辑、内容补充、找答案等附加服务。
- 2、"仅部分预览"的文档,不可在线预览部分如存在完整性等问题,可反馈申请退款(可完整预览的文档不适用该条件!)。
- 3、如文档侵犯您的权益,请联系客服反馈,我们会尽快为您处理(人工客服工作时间:9:00-18:30)。
热轧钼板技术方案及轧制规程计算
目录
1 产品及原料 (2)
1.1 生产规模 (2)
1.2 产品方案 (2)
1.3 原料规格 (2)
2 机组配置及工艺流程 (2)
2.1 机组配置 (2)
2.2 工艺流程 (3)
3 轧制规程计算 (3)
3.1 变形抗力模型 (3)
3.2 温度制度 (4)
3.3 道次分配 (5)
3.4 典型轧制表 (5)
4 平面布置图 (6)
特别说明
1 《热轧钼板技术方案及轧制规程计算》基本为网络资源整理内容,在其后列出了参考文献。
2 关于轧制表计算是根据Mo1的变形抗力资料,经过计算后给出的,没有和实际生产轧制数据做比较,仅供参考。
3 文中错误与断章取义之处,还请谅解与告知。
1 产品及原料
1.1 生产规模
本热轧钼板生产线生产规模为:年产钼及钼合金板材XXXX t/a。
1.2 产品方案
代表品种:纯钼、MT合金
代表牌号:Mo1、Mo2、Mo1-1、Mo2-1、Mo-0.5%Ti
板材厚度: 4.0-20.0 mm
板材宽度:400-600mm
板材长度:1000-3000mm
产品方案:见表1-1
1.3 原料规格
坯料形式:压制板坯
板坯厚度:60-80mm
板坯宽度:400-600mm
板坯长度:600-1200mm
板坯重量:Max.450kg
2 机组配置及工艺流程
2.1 机组配置
1)主要设备组成:
氢气保护加热炉2台
液压剪2台
四辊可逆轧机1台
2)轧制压力:Max.2500t
2.2 工艺流程
热轧钼板生产工艺流程图,见图2-1。
3 轧制规程计算3.1 变形抗力模型
合金牌号:
Mo1
图2- 1:热轧钼板生产工艺流程图
化学成分:见表3-1
表3- 1:Mo1化学成分表(单位:%)
牌号
主要成分杂质含量,不大于
Mo W Ti Zr C Al Ca Fe Mg Ni Si C N O
Mo1 余
量
- - - - 0.002 0.002 0.010 0.002 0.005 0.010 0.010 0.003 0.008
变形抗力模型采用北京科技大学陈程等的研究结果:
σ=59.67469 exp (2332.765/T)γ0.2000093μ0.06509
T=t+273,K;
t——变形温度,℃;
μ——变形速度,s-1;
γ——变形程度(对数应变),轧制时用γm代替γ
γm=ll�11−23ε�
a1~a6 ——回归系数,其值取决于钢种。
本计算采用的钢种系数见表3-2。
牌号σ0/MPa a1 a2 a3 a4 a5 a6 Mo1 236 8.541 4.001 3.201E-5 0.0158 0.367 1.284 3.2 温度制度
钼板坯加热温度制度,见表3-1。
表3- 2:钼板坯加热温度制度表
钼板坯开轧温度与成材率的关系,见表3-2。
各火次的加热温度呈50~80℃递减。
以上为在文献收集的资料。
通过与业内人士交流,通常开轧温度1350℃,当温度<800℃时进行再加热,一般加热到1000~1100℃。
3.3 道次分配
各道次加工率不应过大,在分配上遵守由大到小的原则,热轧的道次加工率一般为20%~30%。
采用72mm×450mm×320mm 的板坯时,在开坯轧制阶段,开坯温度低于1350℃、平均道次变形率大于21.5%、轧制速度低于48m/min 时,易导致轧件内部产生裂纹,且后续轧制中随加热温度的递减而造成微裂纹的扩展。
采用72mm×450mm×320mm 的板坯时,最佳开坯温度、平均道次变形率和轧制速度应分别控制在1450~1500℃、20%~22%和48~53m/min 。
3.4 典型轧制表
工艺 方案 开坯 温度/℃ 终轧 温度/℃ 预热 时间/min 平均道次 变形率/%
板厚3.0mm 成材率/%
板厚1.0mm 成材率/%
1 1500 1300 40~20 20 88 70
2 1300 1100 30~15 20 85 76 3
1300
1100
30~15
10
80
65
4 平面布置图
在此给出布置示意图:
参考文献:
[1]彭志辉,稀有材料加工工艺学[M],中南大学出版社,2003.
[2]杨松涛等,纯钼及钼合金板材轧制加工工艺探讨[J],材料研究与应用,2010(3).
[3]杨松涛等,大单重钼板热轧工艺研究[J],稀有金属与硬质合金,2010(4).
[4]陈程等,钼塑性变形抗力数学模型的研究[J],塑性工程学报,2007(2).。