基于Agent技术的辊弯成型过程系统结构模型研究
基于材料混合硬化模型的柔性辊弯成型仿真研究

基于材料混合硬化模型的柔性辊弯成型仿真研究柔性辊弯成型是一种常用的金属板材成形工艺,其在航空、汽车、电子等行业有着广泛的应用。
为了提高产品质量和生产效率,人们对柔性辊弯成型过程进行了深入研究。
本文基于材料混合硬化模型,对柔性辊弯成型进行了仿真研究。
柔性辊弯成型过程中,金属板材在辊轮的作用下发生塑性变形,最终形成所需的弯曲形状。
在仿真研究中,我们采用了有限元分析方法,将材料混合硬化模型引入模拟中。
材料混合硬化模型是一种能够描述金属材料在多次加载过程中的变形行为的模型,它能够考虑材料的弹性、塑性和硬化等特性。
首先,我们建立了柔性辊弯成型的有限元模型。
模型中包括了金属板材、辊轮和支撑结构等要素。
然后,根据材料的力学性能参数,我们确定了材料混合硬化模型的参数。
接着,我们对柔性辊弯成型过程进行了仿真。
通过仿真结果,我们可以得到金属板材的应力分布、应变分布和变形情况等信息。
同时,我们还可以通过模拟不同工艺参数对成型结果的影响进行分析。
这些结果对于优化柔性辊弯成型工艺和提高产品质量具有重要意义。
通过对柔性辊弯成型仿真研究的分析,我们发现材料混合硬化模型能够较好地描述金属材料在柔性辊弯成型过程中的变形行为。
同时,我们还发现柔性辊弯成型过程中的辊轮半径、辊轮间距和辊轮压力等工艺参数对成型结果有着重要影响。
因此,在实际生产中,需要合理选择和控制这些工艺参数,以获得满足要求的成型产品。
总之,基于材料混合硬化模型的柔性辊弯成型仿真研究为优化柔性辊弯成型工艺和提高产品质量提供了重要参考。
同时,该研究也为其他金属板材成形工艺的仿真研究提供了一定的借鉴和启示。
我们相信,在进一步的研究中,仿真技术将在柔性辊弯成型工艺的优化中发挥更大的作用。
基于Agent的智能制造系统设计与实现

基于Agent的智能制造系统设计与实现智能制造系统是指通过引入先进的信息技术和智能控制手段,实现生产制造过程的自动化、智能化和灵活化。
而基于Agent的智能制造系统则是在智能制造系统中引入Agent技术,将智能体作为自主决策和交互的实体来实现。
Agent是一种能够感知环境、作出决策并执行任务的软件实体,它能够与其他Agent进行交互和协作,并通过学习和自适应来提高自身的性能。
在基于Agent的智能制造系统设计与实现中,Agent成为了系统的核心组成部分。
首先,在基于Agent的智能制造系统中,每个Agent都具有独立的感知能力。
它能够通过传感器实时感知生产过程中的各种参数,如温度、湿度、压力等。
同时,它也能够获取生产任务和相关的产品信息。
通过感知能力,Agent可以对生产环境进行全面监测和分析,并根据实时数据作出相应的决策。
其次,基于Agent的智能制造系统具备自主决策和任务分配的能力。
每个Agent都具有一定的决策能力,它能够根据自身的目标和策略,对生产任务进行分析、计划和调度。
同时,Agent之间也可以进行交互和协作,通过协商和合作来实现任务的分配与执行,从而达到整体生产系统的优化。
再次,基于Agent的智能制造系统能够赋予生产设备自主感知和自主控制的能力。
通过与设备进行互联,Agent可以不仅能够感知设备的工作状态和运行参数,还能够通过控制指令对设备进行控制和调整。
这种自主感知和自主控制的能力使得智能制造系统可以迅速适应变化的生产需求,提高生产效率和质量。
此外,基于Agent的智能制造系统还具有学习和自适应能力。
Agent能够通过对历史数据的学习和分析,不断改进自身的决策和行为模式。
同时,Agent还能够根据外部的变化和反馈信息,调整自身的行为和策略,以适应不断变化的生产条件。
基于Agent的智能制造系统的设计与实现离不开先进的信息技术支持。
例如,需要建立强大的数据处理和分析平台,以处理和分析感知到的大量数据。
辊弯成型工艺研究

辊弯成型工艺研究辊弯成型工艺研究是金属材料加工中,一种常见的成形工艺。
它利用辊弯机将金属材料进行弯曲,从而得到所需要的外形尺寸、曲率半径及几何精度的带弯部件。
辊弯成型工艺是一种比较古老的工艺,早在20世纪50年代就开始使用。
在辊弯成型工艺中,金属材料通过两个相对运动的辊子,实现弯曲加工。
根据不同的材料及加工要求,可选择不同类型的辊弯机,如气动式辊弯机、液压式辊弯机、数控辊弯机等。
辊弯机可分为卧式及立式两种,其中立式辊弯机又可分为3轴辊弯机、4轴辊弯机及5轴辊弯机。
辊弯成型工艺具有加工精度高、效率高、成本低等优点,在航空航天、汽车、冶金、电子、机械等行业被广泛应用。
但是,辊弯成型工艺也存在一些缺点,如加工尺寸受到加工参数的限制,加工厚度范围狭窄,加工能力受到材料性能限制等。
因此,在辊弯成型工艺研究中,需要考虑许多因素,如设计理念、选择辊弯机型号、选择加工参数、选择工具材料等。
首先,要确定好设计理念,以便正确的选择辊弯机型号及加工参数。
其次,应仔细研究辊弯机的结构特点,确定合适的机型,以保证加工效率及加工精度。
在选择加工参数方面,要根据材料的性能及加工精度,选择合理的加工参数,以保证加工效果。
另外,在选择工具材料方面,也要考虑到工具使用寿命、曲率半径及弯曲精度等因素。
总之,辊弯成型工艺研究是一项比较复杂的工作,需要考虑许多因素,以保证加工效果及成型精度。
此外,要根据实际情况,不断优化辊弯成型工艺,以提高加工效率及精度,满足不断发展的加工要求。
Roll bending forming technology research is a common forming process in metal material processing. It uses roll bending machine to bend the metal material, so as to obtain the bent parts with required shape size, curvature radius and geometric precision. Roll bending forming technology is a relatively old technology, which has been used since the 1950s.In roll bending forming process, the metal material is bent by two relative moving rolls. According to different materials and processing requirements, different types of roll bending machines can be selected, such as pneumatic rollbending machine, hydraulic roll bending machine, CNC roll bending machine, etc. Roll bending machines can be divided into horizontal andvertical types, among which vertical roll bending machines can be further divided into 3-axis, 4-axis and 5-axis roll bending machines.Roll bending forming technology has advantages of high processing accuracy, high efficiency and low cost. It is widely used in aerospace, automobile, metallurgy, electronics, machinery and other industries. However, roll bending forming technology also has some disadvantages, such as the processing size is limited by processing parameters, the processing thickness range is narrow, and the processing capacity is limited by material properties.Therefore, in the research of roll bending forming technology, many factors need to be considered, such as design concept, selection of roll bending machine model, selection of processing parameters, selection of tool materials, etc. First of all, it is necessary to determine the designconcept in order to select the right roll bending machine model and processing parameters. Secondly, the structure characteristics of the roll bending machine should be studied carefully to determinethe appropriate model in order to ensure the processing efficiency and accuracy. In terms of selecting processing parameters, reasonable processing parameters should be selected according to the material properties and processing accuracy to ensure the processing effect. In addition, when selecting the tool materials, the service life of the tools, curvature radius and bending accuracy should also be taken into account.In a word, the research of roll bending forming technology is a complicated work, which needs to consider many factors to ensure the processing effect and forming accuracy. In addition, according to the actual situation, the roll bending forming technology should be optimized continuously to improve the processing efficiency and accuracy, so as to meet the constantly developing processing requirements.。
先进高强度钢辊弯成型有限元仿真研究

先进高强度钢辊弯成型有限元仿真研究摘要:本文通过有限元仿真方法,研究了先进高强度钢辊弯成型的工艺性能。
利用ABAQUS软件建立了辊弯成型的有限元模型,并通过调整辊弯成型过程中的力和速度参数,分析了辊弯成型过程中的应力分布、变形特征和成型质量。
研究结果表明,通过合理的辊弯成型参数可以获得较好的成型效果,提高先进高强度钢辊弯成型的质量和效率。
关键词:先进高强度钢;辊弯成型;有限元仿真;工艺性能1. 引言先进高强度钢材具有良好的力学性能和耐腐蚀性能,广泛应用于航空航天、汽车制造和建筑等领域。
辊弯成型作为一种常用的金属成形工艺,可以有效地将钢材弯曲成所需的形状。
为了提高辊弯成型的质量和效率,有限元仿真方法成为研究的重要手段。
2. 方法本研究选择了一种先进高强度钢材作为研究对象,利用ABAQUS软件建立了辊弯成型的有限元模型。
在模型中,考虑了材料的非线性特性和辊弯成型过程中的摩擦力。
通过调整辊弯成型过程中的力和速度参数,进行了多次有限元仿真计算。
3. 结果与讨论通过有限元仿真,得到了辊弯成型过程中的应力分布、变形特征和成型质量。
研究结果表明,合理的辊弯成型参数可以使得钢材在成型过程中受力均匀,避免出现应力集中和变形不均匀的问题。
同时,适当调整成型速度可以减小辊弯成型过程中的应力和变形,提高成型质量。
4. 结论通过有限元仿真研究,本文分析了先进高强度钢辊弯成型的工艺性能。
研究结果表明,通过合理的辊弯成型参数可以获得较好的成型效果,提高先进高强度钢辊弯成型的质量和效率。
本研究为进一步优化先进高强度钢辊弯成型工艺提供了一定的理论依据和技术支持。
5. 。
辊弯成型技术理论及应用研究现状
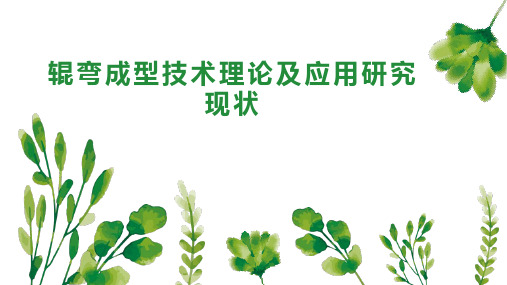
自20世纪80年代以来,快速成型技术得到了快速发展。目前,国际上已经出 现了许多具有代表性的快速成型技术,如立体光刻(SLA)、叠层实体制造 (LOM)、熔融沉积制造(FDM)等。这些技术的不断发展,使得快速成型设备的 性能和精度得到了显著提高,同时也降低了制造成本。
2、国内研究现状
近年来,我国在快速成型技术领域也取得了长足进展。众多科研机构和企业 纷纷投入巨资进行研发和应用,使得我国快速成型设备的生产和制造能力不断提 升。国内研究现状呈现出技术水平逐步提高、应用领域不断拓展的良好态势。
本次演示通过对光固化快速成型的理论、技术及应用的深入研究,发现该技 术在缩短产品开发周期、降低制造成本、提高产品质量等方面具有显著优势。同 时,光固化快速成型技术的应用前景广泛,可为各行各业提供个性化的定制服务, 满足多元化的市场需求。然而,光固化快速成型技术的发展仍存在一定的局限性, 例如设备成本高、材料价格贵等问题,需要进一步加以解决。
随着计算机技术的不断发展,计算机辅助设计系统在异形管连续辊弯成型工 艺中得到了广泛应用。通过引入计算机辅助设计系统,可以大大提高生产效率、 降低生产成本、缩短产品开发周期,同时还能提高产品的质量和精度。
计算机辅助设计系统在异形管连续辊弯成型工艺中的应用包括软件和硬件技 术的使用。在软件方面,常用的软件包括CAD、CAM和CAE等,这些软件可以帮助 设计师进行产品的设计、分析和优化。在硬件方面,随着计算机技术的不断发展, 高性能计算机和高速网络的使用为异形管连续辊弯成型工艺提供了强有力的支持。
三、辊弯成型应用研究
1、汽车制造业
在汽车制造业中,辊弯成型技术被广泛应用于制造汽车零部件,如车门、发 动机罩、后备箱等。利用辊弯成型技术可以生产出具有较高强度和稳定性的零部 件,提高汽车的整体性能和安全性。
650单机架轧机建立其液压弯辊伺服控制系统建立数学模型研究毕业论文

The650single stand millis discussed in this paper,and we will design the mathematical model aboutthe hydraulic servo control system of bending roll.Furthermore we will research and improve the accuracy, stability and rapidity of the model by using the matlab.At the same time ,we will know the effects of various parameters on the system. Through thispaper we will know how to design hydraulic roll bending system and the mechanism, which providing technical support for the future related research.
摘要
随着现代工业的发展,钢板和带钢作为在经济建设中应用最广泛的钢材,对钢铁企业提供的板带钢的尺寸精度和形状精度提出了更高的要求。
辊弯成型工艺研究
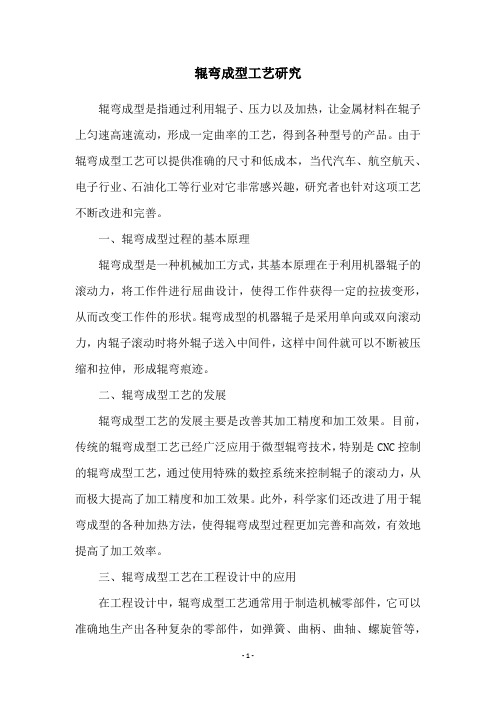
辊弯成型工艺研究辊弯成型是指通过利用辊子、压力以及加热,让金属材料在辊子上匀速高速流动,形成一定曲率的工艺,得到各种型号的产品。
由于辊弯成型工艺可以提供准确的尺寸和低成本,当代汽车、航空航天、电子行业、石油化工等行业对它非常感兴趣,研究者也针对这项工艺不断改进和完善。
一、辊弯成型过程的基本原理辊弯成型是一种机械加工方式,其基本原理在于利用机器辊子的滚动力,将工作件进行屈曲设计,使得工作件获得一定的拉拔变形,从而改变工作件的形状。
辊弯成型的机器辊子是采用单向或双向滚动力,内辊子滚动时将外辊子送入中间件,这样中间件就可以不断被压缩和拉伸,形成辊弯痕迹。
二、辊弯成型工艺的发展辊弯成型工艺的发展主要是改善其加工精度和加工效果。
目前,传统的辊弯成型工艺已经广泛应用于微型辊弯技术,特别是CNC控制的辊弯成型工艺,通过使用特殊的数控系统来控制辊子的滚动力,从而极大提高了加工精度和加工效果。
此外,科学家们还改进了用于辊弯成型的各种加热方法,使得辊弯成型过程更加完善和高效,有效地提高了加工效率。
三、辊弯成型工艺在工程设计中的应用在工程设计中,辊弯成型工艺通常用于制造机械零部件,它可以准确地生产出各种复杂的零部件,如弹簧、曲柄、曲轴、螺旋管等,它可以满足复杂零部件的任何特殊要求,并有效地提高了工程效率。
辊弯成型工艺还可以用于制作各种表面质量高、材质软、硬度可调的金属制品,它能够有效地提高工程所需产品的精度度和硬度。
四、辊弯成型工艺的可能发展辊弯成型工艺的未来可能会发展出更多可能性,如运用三维扫描技术,提高辊弯成型工艺的加工效率,增加辊弯成型机械的精度,降低加工的能耗,提高加工的质量,以使辊弯成型工艺能够更好地适应多样化的加工环境和复杂的结构要求。
综上所述,辊弯成型工艺目前已经得到了实际应用,未来还将会不断发展,完善其加工效率、质量及精度,为各大行业提供更优质的产品。
辊弯成形过程仿真与参数优化
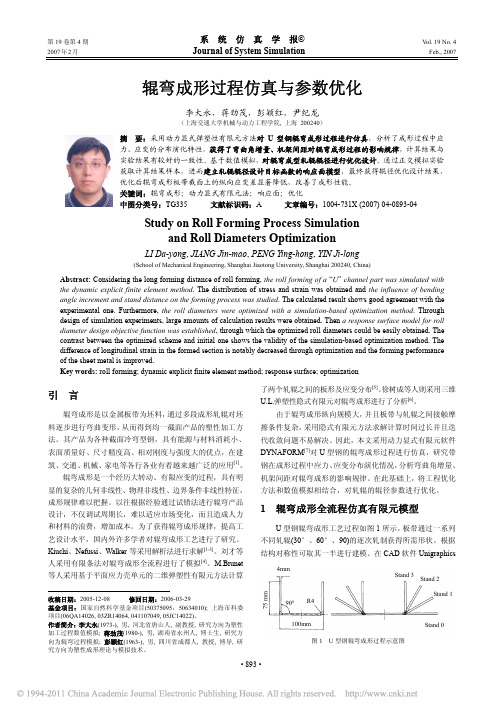
第19卷第4期 系统 仿 真 学 报© V ol. 19 No. 42007年2月 Journal of System Simulation Feb., 20074mm4mm 100mmStand 0Stand 1Stand 2Stand 375 m m90°R4辊弯成形过程仿真与参数优化李大永,蒋劲茂,彭颖红,尹纪龙(上海交通大学机械与动力工程学院, 上海 200240)摘 要:采用动力显式弹塑性有限元方法对U 型钢辊弯成形过程进行仿真,分析了成形过程中应力、应变的分布演化特性,获得了弯曲角增量、机架间距对辊弯成形过程的影响规律,计算结果与实验结果有较好的一致性。
基于数值模拟,对辊弯成型轧辊辊径进行优化设计。
通过正交模拟实验获取计算结果样本,进而建立轧辊辊径设计目标函数的响应面模型,最终获得辊径优化设计结果,优化后辊弯成形板带截面上的纵向应变差显著降低,改善了成形性能。
关键词:辊弯成形;动力显式有限元法;响应面;优化中图分类号:TG335 文献标识码:A 文章编号:1004-731X (2007) 04-0893-04Study on Roll Forming Process Simulationand Roll Diameters OptimizationLI Da -yong , JIANG Jin -mao , PENG Ying -hong , YIN Ji -long(School of Mechanical Engineering, Shanghai Jiaotong University, Shanghai 200240, China)Abstract: Considering the long forming distance of roll forming, the roll forming of a “U ” channel part was simulated with the dynamic explicit finite element method . The distribution of stress and strain was obtained and the influence of bending angle increment and stand distance on the forming process was studied . The calculated result shows good agreement with the experimental one. Furthermore, the roll diameters were optimized with a simulation-based optimization method . Through design of simulation experiments, large amounts of calculation results were obtained. Then a response surface model for roll diameter design objective function was established , through which the optimized roll diameters could be easily obtained. The contrast between the optimized scheme and initial one shows the validity of the simulation-based optimization method. The difference of longitudinal strain in the formed section is notably decreased through optimization and the forming performance of the sheet metal is improved.Key words: roll forming; dynamic explicit finite element method; response surface; optimization引 言辊弯成形是以金属板带为坯料,通过多段成形轧辊对坯料逐步进行弯曲变形,从而得到均一截面产品的塑性加工方法。
- 1、下载文档前请自行甄别文档内容的完整性,平台不提供额外的编辑、内容补充、找答案等附加服务。
- 2、"仅部分预览"的文档,不可在线预览部分如存在完整性等问题,可反馈申请退款(可完整预览的文档不适用该条件!)。
- 3、如文档侵犯您的权益,请联系客服反馈,我们会尽快为您处理(人工客服工作时间:9:00-18:30)。
基于Agent技术的辊弯成型过程系统结构模型研究目前广泛应用于国民经济各个领域的冷弯型钢是一种低能耗的截面轻型薄
壁钢材。
辊弯成型是生产冷弯型钢的重要方法之一,是一种复杂的钢带深加工方法。
其复杂性表现在变形过程是材料、几何以及接触边界等一系列非线性的弹塑性大变形过程,并且变形过程的影响因素非常多。
因此,对辊弯成型过程进行深入的、系统的理论研究,揭示变形过程中的成型规律,开发一套可以模拟成型过程并能够指导实际生产过程中孔型设计的计算机辅助设计软件,既具有重大的理论意义,又具有一定的实用价值。
多Agent系统起源于分布式人工智能,正由探索性研究向着实用化方向发展。
Agent组织是多Agent系统的一种特殊形式,基于Agent组织的求解可以减少系
统的内部冲突,扩展个体Agent的认知能力和物理能力,是一种十分有效的问题
求解方式。
将多Agent理论与技术应用到冷弯成形过程的分析和研究中,可以提高冷弯成形过程分析的信息化和智能化水平。
首先,系统分析了Agent与多Agent 系统的研究和应用现状,尤其是在制造业等相关领域的应用现状。
综述了国内外关于辊弯成型工艺技术、成型理论和成型过程信息化的研究进展情况以及冷弯型钢的生产现状。
其次,在总结Agent组织的特点后,建立了一种包含抽象层和实例层的Agent组织模型,分析了抽象层、实例层的组成以及Agent 组织的实例化过程和形成机制。
Agent间的通信是Agent组织内部或不同的Agent 组织之间实现知识与信息共享、进行交互与协商,进而分工合作解决复杂的问题的根本途径。
比较了多种Agent通信语言,选择了KQML语言作为Agent组织中的Agent通信语言,并根据样条有限条法的应用需要扩充了KQML原语。
再次,结合Agent组织的特点进一步完善了基于修正的拉格朗日法的弹塑性大变形样条有限条法及其相应的计算列式。
为了在保证计算精度的基础上提高系统的运行效率,在均分样条区域的基础上选择接触性特征有限条并分析了特征有限条对非特征有限条的影响。
最后,将Agent组织应用到样条有限条法中,建立了一个基于Agent组织的样条有限条法模型。
根据该模型将辊弯成型理论与辊弯成型设计、数值模拟有机的集成到一起,初步建立了一个具有智能性的计算机辅助设计仿真系统。
使用该系统模拟了普通槽钢的成型过程,并将实验结果与文献数据进行比较,
验证了模型的正确性。