PFMEA潜在失效模式分析标准表格
潜在失效模式及后果分析(PFMEA)

4 2 5 4 3
进料检验试产测试 要求供应商排版确认样品。 要求供应商排版确认样品。 要求供应商排版确认样品。 要求供应商提供确认样品。
2 2 3 2 3
32 28 75 40 54
保丽龙
重量 保丽龙 尺寸 外观不良 唛头
产品不安全,破损 外观不良,影响安全 客户投诉 唛头错误、客户投诉,
6 4 6 5
2
现行控制方法
l 来 料 检 验
外观不良
透明度不够,导致产品缺陷
供应商材料发生了变化
要求供应商固定客户原材料订购
树脂
浓度 重量 含铅 拉力不够
调配后产品收缩比列大,变形 数据预算错误,导致产品重量不足 不符合标准 翻次过低、影响使用次数
6 4 8 7
原材料过浓或者偏稀 供应商称重失误 供应商材料不达标 材料发生质变
3
按作业指导书操作。 现场巡检及日检查报表
4 3 2 3 3 2 2
60 0 12 48 27 12 20
2 4
现场巡检及日检查报表 现场巡检及日检查报表 现场管理巡检、操作员自检 现场巡检及日检查报表 核对产品所需物料全数清点
白坯检验功能不良
重量不符 尺寸
核对标准样件、按客户要求,每件称 3 重保重。 操4
供应商供应材料不符合欧美RoHS元素
3
要求供应商提供最新第三方检测报告,生产前送 第三方检测。
2
24
颜色易脱落,客服投诉 字体错误、印刷部清楚 导致条码无法读数,客户投诉 字体错误、印刷不清楚 产品不安全,破损
4 7 5 5 6
供应商品质部符合质量要求 供应商品质部符合质量要求 供应商品质部符合质量要求 供应商排版不挡 要求供应商按标准密度生产
PFMEA过程潜在失效模式及后果分析表模板
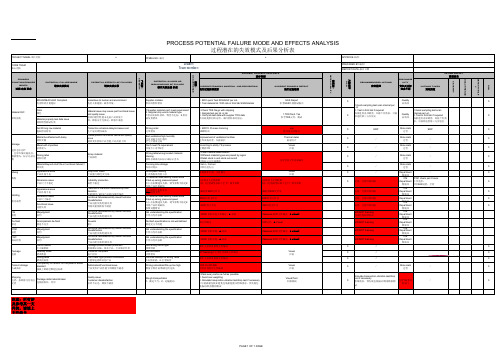
CURRENT PROCESS CONTROLS 现行控制
POTENTIAL CAUSES OR MECHANISAMS OF FAILURE
潜在失效起因/机理
CURRENT PROCESS CONTROL AND PREVENTION 现行过程控制预防
CURRENT PROCESS DETECT 现行过程检测
Instability produciton 成型不稳定
Molding 硫化成型
FAI 首检 De-flash 除边 IPQC 巡检 FQC 成品检查
Package 包装
Product storage 入成品库
Appereance issue 产品外观不良
Dimension issue 产品尺寸偏差
Functional issue 功能失效
Misjudgment 误判
Incomplement de-flash 除边不完全
Misjudgment 误判
Misjudgment 误判
Carton issuce 不正确纸箱 Quantity issue 错误数量 Wrong lable 错误的标签 The quantity of cartons On the pallet is above standard 栈板上纸箱层数超过标准
Get Wrong raw material 提取错误材料
Matrial be affected with damp 材料受潮
Storage
Mixed with impurities
进料仓库存贮
杂质混入
:仓库环境设施良好,
摆放整齐,标示记录完 Wrong label
整
材料用错
Production schedule delay/increase cost 生产延迟/增加成本 Cause product functional failure and quality issue 材质变坏影响产品性能,产品质量下降
注塑件过程失效模式及后果分析表模板(PFMEA)

6
包装破损
零件污染,客户投 诉
5
产品碰伤砸伤 客户投诉
6
装箱时确认不足 货物堆积过高
搬运不规范
2
无
3
试验后制定合理堆 积标准
2
无
100目测 100目测 100目测
5 60 5 75 4 48
标签贴错 发错货,客户投诉 5
标签与实物未核对 2
无
100目测
4 40
产品数量不正确
客户投诉
6
80-出货检验
关键尺寸超差
第 1 页,共 2 页
注塑件过程失效模式及后果分析表模板(PFMEA)
零件号
设计责任部门
FMEA 编号
零件名称
关键日期
编制人
车型/年份
系统/子系统/部件
编制日期
核心小组
序号
过程
潜在的失效模式
严 潜在的失效后果 重
度
级 别
潜在的失效原因/机理
频 度 数
现行预防性设计控 制
现行探测性设计控 制
探 测 度
5 60 5 75
建议措施
责任人和目标 完成日期
无
采取的措施
严频探 R 重度测 P 度数度 N
无
无
无
无
不同产品分区放置, 并做好标识
6
2 5 60
无
对纸箱进行固定 6 2 5 60
无
无
无
无
无
不同产品分区放置, 并做好标识
6
2 5 60
无
对纸箱进行固定 6 2 5 60
无
40-原材料烘料
烘料时间不对 烘料温度不对
表面料花 色差
过程潜在失效模式与效果分析表(PFMEA)
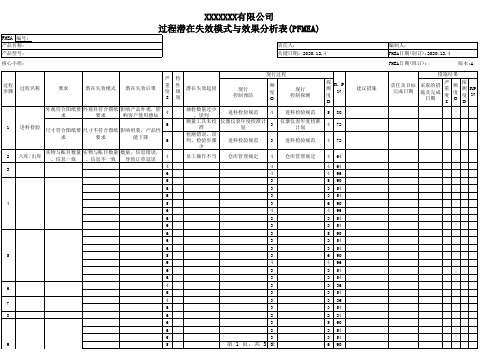
求
要求
响客户使用感知
4
1
进料检验 尺寸符合图纸要 尺寸不符合图纸 影响组装,产品性 6
求
要求
能下降
6
2
入库/出库
实物与账目数量 实物与账目数量 数量、信息错误, 、信息一致 、信息不一致 导致订单延误
4
抽检数量过少 、误判
进料检验规范
4
进料检验规范
5 80
测量工具未校 准
仪器仪表年度校准计 划
3
仪器仪表年度校准 计划
4 96
18
6
第 2 页,共 3 页4
4 96
18
6
4
4 96
5
4
4 80
19
5
4
4 80
6
3
4 72
6
4
4 96
20
6
4
4 96
6
4
4 96
21
4
4
5 80
4
4
4 64
22
4
4
5 80
23
4
4
4 64
备注:S、O、D评分标准详见《过程潜在失效模式后果分析PFMEA管理程序》,仅需对新部件进行评价分析,当RPN值超过200时要制定改善措施。
核准:
会签:
审查:
拟制:
表单 编 号:
第 3 页,共 3 页
6
4
4 96
6
3
3 54
6
3
3 54
6
3
5 90
6
3
3 54
6
3
3 54
13
5
3
PFMEA评分表

PFMEA评分表PFMEA评分表》是一种常用的品质管理工具,用于进行潜在失效模式与效应分析(Process Failure Mode and Effects Analysis,简称PFMEA)。
它的目的是识别关键步骤或流程中的潜在失效模式,并评估其对产品或服务质量的影响程度。
PFMEA评分表可以帮助团队全面分析和评估可能发生的失效模式,并制定适当的预防和纠正措施,从而最大程度地降低产品或服务质量风险。
通过对各种失效模式和其效应的评估,可以提前发现潜在问题并采取相应的控制措施,以确保产品或服务质量的稳定和可靠。
在PFMEA评分表中,各个步骤或流程会被列出,并根据其对产品或服务的潜在失效的重要程度进行评分。
评分标准可以根据具体情况进行制定,但通常包括失效模式的严重性、发生频率和检测能力等方面的考量。
评分结果可以帮助团队确定哪些步骤或流程需要重点关注和改进,从而优化生产或服务流程,提高质量稳定性。
综上所述,《PFMEA评分表》是一种重要的品质管理工具,用于识别和评估潜在的失效模式,以确保产品或服务质量的稳定和可靠。
PFMEA评分表是一种用于进行过程故障模式与影响分析的工具。
它由以下几个组成部分构成,并且包含一些必填项。
1.项目信息在评分表的顶部,需要填写一些项目信息,以便对分析的过程进行标识和跟踪。
这些信息可能包括项目名称、项目编号、评分表编制人员等。
2.设计和工艺流程步骤在评分表中,需要列出与该过程相关的设计和工艺流程步骤。
这些步骤可以按照顺序进行排列,并且需要明确指出每个步骤的名称和内容。
3.故障模式与影响分析针对每个设计和工艺流程步骤,需要进行故障模式与影响分析。
这部分需要列出可能的故障模式,并对其进行评估。
评估可以基于指标如严重性、发生频率和可探测性等进行。
4.推理控制计划在评分表中,需要制定推理控制计划,以预防或控制故障模式对产品或过程的影响。
这部分需要明确列出控制措施、控制方式以及执行者。
PFMEA表格

2
2.Melting the right ingot 2.熔正确的材料
3.The right material matching
3.材料配比要正确
melting the material.
5 70
2.员工熔炼之前要检查下材料和颜色是不是
自己需要熔的材料.
3.Operator will follow the melting operation
integrity affected
6
铝料成份不合格影响产品的真
实性
1.Ingot composition analysis per lot / For all
Incorrect alloy or alloy composition Deviate from A380 from supplier 进错料或材料成份超差
card to match the material
3.员工按照熔炼工艺卡去配比材料
Excessive gas and dregs in Liquid aluminum 铝液中有多余的气体和渣滓
Product will have inclusions 产品会有夹渣
6
Wrong Degassing&Skimming
Prepared By编制人: Qin RongLe Approved By批准:
Current Process Controls Detection 现行探测设计控制
DR
E
P
Recommend Actions
Responsible Person & Target Date
TN
探 序风
测 数险
度
顺
建议措施
PFMEA表格

剪钳力度过大,剪脚时有拔的动作 插件总检未完全压件,扶件 PCB铜箔氧化或零件脚氧化 作业疏忽 作业方法不正确&PCB漏V-CUT 插件时造成元件浮高、反向、漏件、错件
2 2 2 4 1 3
剪钳与PCB板平行,元件脚只可剪断不 可上拔,后锡面修补工位被焊 插件总检100%扶正,压件 来料检验重点检查/及插件时带手指套 防静电刷100%清洁/目视检查 作业动作标准化&挑选PCB 漏 V-CUT 不良产品。 加强压件检查管控力度 插DC线时制程控制,不可拖锡,加锡 后锡丝拆开1秒钟后方可移开烙铁。 自检 胶壳有卡槽防呆
5
每两小时确认一次焊锡品质
3
制工ME
2012/11/13
9
2
3
54
内有物
客户投诉
8
锡炉里有杂物
1
定期清洁锡炉(1周1次)
2
16
NA
8
1
2
16
剪脚 零件面检查 锡面修补
SMD碰破、翘皮 歪斜,浮高 焊点不上锡 PCB板有锡珠
电性不良 安装尺寸不符、电性不良 电性不良 异响 外观\电性不良 电性不良
8 8 8 8 6 6
检测失效 客诉 DC母座测试接触不良 卡不到位 外观不良、客诉 外观不良 产品方向不一致 产品方向不一致 外观不良 外观不良 外观不良 外观
8 6 8 5 6 4 3 3 4 5 4 6
测试治具受潮 漏听品流入下站, 超声波 噪声干扰 母座接触不良 卡纸较脆弱,员工操作不当导致 作业疏忽 搬运擦伤 作业疏忽 作业疏忽 作业疏忽 作业疏忽 作业疏忽 装箱未用隔板隔开,插脚放置方向错误
打AI&检查 印红胶
打反、打漏 漏点、点歪 极性反
过程潜在失效模式及后果分析表PFMEA--注塑焊接

3
1、每个风轮都 要动平衡的测量 目视检测平衡 。 机上参考的读 2、人离开机时 数确认 风轮不能停在机 台上。
3
1、每个风轮都 要经过动平衡 机的测量。 54 2、人离开机时 风轮不能停在 机台上。
1、每个风轮都要 经过动平衡机的测 1.IPQC检验记录 量。 6 3 3 54 表2、工艺卡 2、人离开机时风 轮不能停在机台上 。
1.工具校正后使用 不当出现错误 无法精准的 5 2.工具校正误差太 测量不良点 大,不适用 3.工具校正过期
3
1.建立工具保 养维护制度 2.培训正确使 用工具
1.核查设备校正 清单 2.考核设备使用 维护
5
1.定期设备校正 清单更新 2.设备使用维护 75 培训考核 3.设备编号特定 授权管理
1.工具设备清单 2.设备校正计划 表 3.设备校正报告 4.工具维修保养 记录
过程潜在失效模式及后果分析(PFMEA)
PFMEA编号:
项目阶段/过程:注塑件、焊接风轮 类别或产品型号: 核心小组 过程责任:塑料部 关键日期:2016-1-5 PFMEA日期(编制)2016-1-5 共1页,第 1 页 修订:2016-7-4
严 频 工序功能/ 潜在的失 潜在的失效 重 潜在的失效起因/机 现行过程控制 度 效模式 后果 度 预防 要求 理 (O) (S)
1. SV750-5A烘 干记录表2、过 程检验规范3、 《烘干作业指导 书》
1、投料前先试验 好烘干机发热情况 。2. 首检与客人签 6 3 3 54 样作对比目测确认 。
配料(依据 《配料作 色差 业指导书 》)
配料员配色母或色 影响外观要 7 种的比例不符合规 求 定,造成色差。
3
1.投料单注明 相关要求 2.首检确认
- 1、下载文档前请自行甄别文档内容的完整性,平台不提供额外的编辑、内容补充、找答案等附加服务。
- 2、"仅部分预览"的文档,不可在线预览部分如存在完整性等问题,可反馈申请退款(可完整预览的文档不适用该条件!)。
- 3、如文档侵犯您的权益,请联系客服反馈,我们会尽快为您处理(人工客服工作时间:9:00-18:30)。
(过程FMEA)共1页,第1页
产品名称吸塑托盘过程责任部门生产部编制人龚有恒
产品货号APP-VP-00003690-000关键日期2011.7.5FMEA日期(编制)2011.7.6
核心小组柴伟洋、尚有兵、舒剑新、林华元、龚有恒(修订)/
过程名称
潜在失效模式
潜在失效后果
严重度S
级别
潜在失效起因/机理
频度
O
现行过程控制
-预防
-探测
探测度D
风险顺序数RPN
建议措施
责任及目标完成日期
措施结果
采取的措施
S
O
D
RPN
产品成型
未吸到位
产品实物放置不到位,影响功能
6
吸塑机成型参数不符合导致
7
无
3
126
严格按成型条件参数表执行
柴伟洋∕2011.7.10
1.严格按成型条件参数表执行;
2011.7.10
1.产品层叠不能太紧,防止挤压导致变形;
2.吸塑部半成品放置防止重压,控制变形。
6
2
1
12
2.IPQC加强巡检力度,对其重点监视;
6
3
2
36
啤切
作业造成刮伤
影响外观
5
作业台面刮伤及人工操作引起
6
无
2
60
人员教育
尚有兵/
2011.7.10
1.在作业台面追加绒布,防止划伤;
2.作业时轻拿轻放,对作业人员教育宣传;
5
2
2
20
包装
托盘底部变形影响外观和功能6Fra bibliotek操作不当
5
无
2
60
作业方式改善
尚有兵/