浸出渣逆流洗涤试验研究
宇腾硒亚硫酸钠浸出渣实验报告

(ppm)
Cu
(ppm)
Pb
(ppm)
浸出率
(%)
25
38325
19972
1.5
174
27
79.79
30
41458
21156
3.1
176
31
86.25
35
49325
22851
3.3
176
38.9
100.1
45
49359
21759
4.6
172
40.8
100.1
50
45105
19856
3.82
157
Se
( ppm)
Hg
(ppm)
Ag
(ppm)
Cu
(ppm)
Pb
(ppm)
浸出率
(%)
浸出质量
浸出液
39589
20314
7.6
160
35.9
84.8
1370ml
浸出渣
144559
37555
470
164
97772
82.2
75.6g
2、沉硒实验
盐酸羟胺(g)
Se( ppm)
备注
0
46210
89.3
1333
溶液中Se含量的2.8倍
108.5
50
溶液中Se含量的3.4倍
121.3
32
溶液中Se含量的3.8倍
134
27
溶液中Se含量的4.2倍
146.8
15
溶液中Se含量的4.6倍
159.6
15
溶液中Se含量的5倍
四、实验现象
锌浸出渣浮选银的预处理研究报告

锌浸出渣浮选银的预处理研究报告锌浸出渣是一种常见的含银废弃物,其中含有大量的银元素。
为了有效地回收这些银,需要对锌浸出渣进行预处理。
本研究旨在探究锌浸出渣浮选银的预处理方法。
首先,我们对锌浸出渣进行了化学成分分析,得出了渣中各种元素的含量。
结果显示,锌浸出渣中的银元素含量约为1%,而其它元素的含量相对较低。
由于银元素含量较高,我们选择了浮选法进行银的回收。
接下来,我们对锌浸出渣进行了机械筛分,筛出的颗粒大小为0.074mm。
然后将筛分后的渣料浸泡在硝酸中,使其酸性pH 达到1.5~3.0。
在这种酸性下,银元素可以被氧化成Ag+,并且渣料表面的硫化物可以被溶解。
随后,我们加入了适量的氧化剂,如过氧化氢,以增强氧化反应。
然后加入xanthate作为浮选剂,将其搅拌30分钟。
在这个过程中,银元素可以与xanthate形成化合物,并且被溶于溶液中。
我们对浮选后的渣料进行了过滤、洗涤、干燥等处理,最终得到了银的精矿。
最后,我们通过烧灼法得到了锌含量较低的锌残渣。
这种锌残渣可以进一步用于锌的回收。
总的来说,本研究采用了将锌浸出渣浮选银的预处理方法。
通过化学成分分析、机械筛分、酸性氧化、加氧化剂和浮选剂等处理,成功地回收了含银废弃物中的银元素,同时还得到了锌残渣进一步回收。
这种预处理方法具有操作简便、回收效果好等优点,为含银废弃物的回收提供了一种可行的思路。
在研究过程中,我们对锌浸出渣进行了化学成分分析。
我们得到了如下表格所示的数据:元素|含量(%)-|-银(Ag)|1.05锌(Zn)|33.98铁(Fe)|0.66硫(S)|29.08铜(Cu)|0.02铝(Al)|0.02镁(Mg)|0.03钠(Na)|0.17钾(K)|0.15通过表格数据可以看出,锌浸出渣主要是由锌和硫构成的。
其中,锌含量高达33.98%,硫含量也相对较高。
银元素含量约为1.05%,位于各种元素中相对较低。
此外,其他元素的含量均较低,不会对银的回收造成影响。
逆流水洗工艺应用于PPTA粉体洗涤的应用及探讨

逆流水洗工艺应用于PPTA粉体洗涤的应用及探讨摘要:文章介绍了聚对苯二甲酰对苯二胺(简称PPTA)树脂粉体进行逆流水洗处理的工艺和设备,其中着重介绍采用真空带式逆流水洗机对PPTA树脂粉体进行水洗处理的相关情况,并针对真空带式逆流水洗机处理PPTA树脂粉体的过程中所存在的缺陷进行改进。
关键词:PPTA树脂粉体;逆流水洗;真空带式逆流水洗机;改进粉体是一种干燥、分散的固体颗粒组成的细微粒子,和颗粒不完全相同。
通俗来说,粉体比颗粒具有更细微的粒径尺寸。
目前工业化生产过程中,粉体得到了越来越广泛的应用,其种类也越来越广。
含有大量内部蜂窝结构的PPTA粉体就是其中的一种。
在PPTA树脂聚合的过程中,由于使用了有机溶剂和助溶剂,这些物质都均匀地镶嵌在PPTA聚合物树脂中,如果不将这些成分进行分离,不但无法满足PPTA树脂的各种工业应用需求,而且生产成本会非常高。
鉴于PPTA树脂不溶于水,而聚合生产过程中所使用的各种有机溶剂和助溶剂又都易溶于水这一特点,在工业化生产过程中,采用工业纯水作为洗涤介质,将PPTA粉体中融入的其它各种成分洗涤出来,是完全可行的。
在洗涤过程中,大量有机溶剂和助溶剂析出后,在PPTA树脂粉体内部形成了含有大量孔洞的蜂窝结构,这种结构的形成非常有利于PPTA树脂在浓硫酸中的溶解,能够缩短PPTA树脂配成纺丝浆液的时间,降低PPTA树脂的降解,生产高强度PPTA纤维。
另外,将水洗液进行相应的处理,即可实现有机溶剂的回收利用。
类似这种洗涤形式,工业上称为滤饼过滤。
在工业应用过程中,固液分离过程就是将一种物质从另一种物质中分开的基本操作过程,过滤是固液分离的基本手段,近年来,国内外对固液分离技术的发展都非常重视。
采用合适的技术和装备,一方面可以提高产品的质量,降低产品能耗,提高经济效益;另一方面可以减少乃至避免对环境的污染。
工业上,过滤操作分为两大类,即深层过滤和滤饼过滤。
所谓深层过滤,指的是固体颗粒被截留于过滤介质内部的孔隙中,介质表面一般不形成滤饼,这种过滤常用于料浆浓度极稀、固体颗粒粒径很小的场合;滤饼过滤又称表面过滤,过滤开始时,由于过滤介质的筛滤作用,液体通过过滤介质,固体颗粒被截留在介质表面通过沉积、架桥逐渐形成滤饼,一旦当滤饼形成,固体颗粒的沉积作用即转移至滤饼本身,介质仅起支撑作用。
两段逆流浸出从铁捕集物中富集铂族金属的研究_童伟锋

2015年2月 贵 金 属 Feb. 2015第36卷第1期Precious MetalsV ol.36, No.1收稿日期:2014-03-17基金项目:国家高技术研究发展(863)计划项目(2012AA063203)。
第一作者:童伟锋,男,工程师,研究方向:稀贵金属冶金。
E-mail :tong6756@*通讯作者:董海刚,男,博士,副研究员,研究方向:稀贵金属冶金。
E-mail :donghaigang0404@两段逆流浸出从铁捕集物中富集铂族金属的研究童伟锋,董海刚*,吴晓峰,赵家春,李博捷,吴跃东,保思敏,杨海琼(昆明贵金属研究所,贵研铂业股份有限公司 稀贵金属综合利用新技术国家重点试验室,昆明 650106)摘 要:对熔炼铁捕集物采用两段逆流浸出工艺富集铂族金属进行研究。
结果表明,在铁捕集物粉粒度为–0.425 mm ,一段浸出温度为常温,浸出硫酸浓度为1.7~1.8 mol/L ,固液比 (S:L)=1:10,反应时间为0.5 h ;二段浸出温度为75℃,浸出硫酸浓度为2 mol/L ,S:L=1:50,反应时间为4 h 。
经此两段浸出后,铂族金属的平均富集倍数为70.6,铂族金属回收率大于99.8%。
关键词:有色金属冶金;铂族金属;两段逆流;铁捕集物;富集中图分类号:TF83 文献标识码:A 文章编号:1004-0676(2015)01-0021-04Study on Enrichment of Platinum Group Metals in Iron-Trapping MaterialUsing Two-Stage Countercurrent LeachingTONG Weifeng, DONG Haigang *, WU Xiaofeng, ZHAO Jiachun, LI Bojie, WU Y uedong, BAO Simin, Y ANG Haiqiong(Kunming Institute of Precious Metals, State Key Laboratory of Advanced Technologies for Comprehensive Utilizationof Platinum Metals, Sino-Platinum Metals Co. Ltd., Kunming 650106, China)Abstract: The enrichment process of platinum group metals (PGMs) in the PGM-bearing iron-trapping material was investigated by using the “two-stage countercurrent leaching” technology. When particle size of iron-trapping material was –0.425 mm, the experimental condition for the first stage leaching was room temperature, sulfuric acid concentration of 1.7~1.8 mol/L, solid and liquid ratio (S:L) of 1:10 and leaching for 0.5 h, while that for the second stage leaching was 75, sul ℃furic acid concentration of 2 mol/L, solid and liquid ratio of 1:50 and leaching for 4 h. After two stages leaching, PGMs were enriched about 70.6 times in the iron-trapping material and at least 99.8 % of PGMs could be recovered.Key words: nonferrous metallurgy; platinum group metals (PGMs); two-stage countercurrent; iron-trapping material; enrichment铂族金属因其独特的物理化学性质,被广泛应用于日常生活、农业、传统工业、高新技术、军工宇航、医药卫生、环境保护、金融储备等各个领域,被誉为“现代工业的维他命”,而地壳中的铂族金属资源非常稀缺[1]。
浸出渣逆流洗涤试验报告2

浸出渣逆流洗涤试验报告5月,应公司要求,对生产线浸出渣进行逆流洗涤试验,探求较佳的洗涤工艺参数,以便解决现有生产工艺大量洗水难以平衡的问题,利于生产顺利进行,并在一定程度上降低成本。
试验组进行了相应的浓密逆流洗涤模拟试验,并取得一定效果。
试验情况如下:一、浸出渣情况取车间以下浸出渣做了检测,并自测比重及干份,以备后序试验:其中,渣1粘度比渣2较大,渣2呈较多细砂状,渣2 的沉降性能明显优于渣1。
二、试验方式、步骤用4个1000mL的烧杯,按下述方式、步骤,进行了9份4级浓密逆流洗涤模拟试验:1、参照前期沉降试验数据,选择可行的底流浓度,以湿渣:水(第1份试验时)或前次第4级液=1:1(重量比),在第1级烧杯中调制成固含量为37.5~40%的起始料浆。
2、按60~130g絮凝剂/吨干渣,将絮凝剂配成一定浓度溶液,加入起始料浆,搅匀。
3、在上述料浆中加入原湿渣量的一定倍数(0.5~1.5倍)的水(第1份试验时)或前次第2级洗液,搅匀,此时料浆固含量为25~26.7%(1倍液)或21.4~22.8%(1.5倍液),静置。
4、当静置后上清液达到步骤3中所加水或洗液量时,抽移该体积量上清液。
剩余料浆则与起始料浆固含量相对一致,将其加入第2级烧杯中,加入同样倍数的水(第1份试验时)或前次第3级洗液,搅匀,静置。
5、当静置后上清液达到步骤3中所加水或洗液量时,抽移该体积量上清液。
剩余料浆继续保持与起始料浆固含量相对一致,将其加入第3级烧杯中,加入同样倍数的水(第1份试验时)或前次第4级洗液,搅匀,静置。
6、当静置后上清液达到步骤3中所加水或洗液量时,抽移该体积量上清液。
剩余料浆加入第4级烧杯中,加入同样倍数的水,搅匀,静置。
7、当静置后上清液达到步骤3中所加水或洗液量时,抽移该体积量上清液。
剩余料浆进行抽滤,滤液返回步骤1调制起始料浆。
滤渣实物态送化。
简单示意图如下:三、试验数据第1份(A循环)步骤3为洗水量为原湿渣量的0.5倍(重量比),第2~4份(B~D循环)步骤3为洗水量为原湿渣量的1倍,第5~9份(E~I循环)步骤3为洗水量为原湿渣量的1.5倍;第1~6份原渣为渣1,第7~9份原渣为渣2;静置分相时间,1~1.5小时即可分出所需体积的上清液。
半逆流多级浸出工艺和连续逆流浸出工艺及设备选择
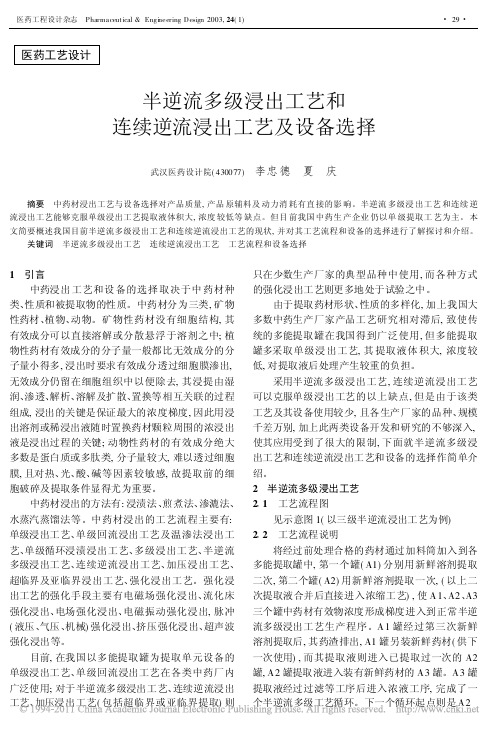
33
浓度次之的提取液 PF2, 在 C 柱中加入新溶剂, 循环 提取 2/ 4t 后, 得到浓度更次的提取液 PF 4。PF1 至 PF4 形成了有效成分含量递减的浓度梯度, 再将柱 A 至柱 E 中加入新鲜药材, 将 PF 1 加入 A 柱对 A 柱 药材进行第一次提取, 得提取液 A1 去浓缩, 将 P F2 至 PF4 分别加入 A 柱对药材进行第二至四次提取 得提取液 A2, A3, A4, 将新溶剂加入 A 柱对药材进 行第五次提取, 得提取液 A5, 将 A2 加入 B 柱药材 进行第一次提取得提取液 B1 去浓缩, 将 A3、A4、A5 分别加入 B 柱对药材进行第二至四次提取 得提取 液 B2、B3、B4, 第五次加入新溶剂得提取液 B5, 柱 A 的药材提取 5 次后排渣、加新鲜药材( 等下一 次使 用) 。此时循环由 B 柱至 F 柱, 依次类推, 每柱的药 材提取 5 次后分别去排渣、加新鲜药材, 此工艺过程 中, 6 根柱子同时按上述流程独立进行, 只不过每柱 中的物料有效成分含量和溶剂 中有效成分含 量不 同。 5 3 工艺设备配置
蒙古丹龙药业、内蒙古五原九郡药业公司、宁夏多维 药业公司、沈阳植物提取厂、长春海王生物制药有限 公司等。 5 柱组式连续逆流提取装置 5 1 工艺流程图
见示意图 4( 以六级柱为例)
5 2 工艺流程说明 该工艺的关键在于预先在各柱制造浓度梯度。
首先分别在柱 A 至柱 E 中装入经前处理合格并且 粗碎的新鲜药材, 在贮罐 5 中加入新溶剂, 经泵 11
( 1) 该工艺适用于经试验生产后的成熟工艺。 ( 2) 适用于常年生产的大品种或大比量集中性 生产的品种。 ( 3) 适用于提取次数较多的药材提取。 ( 4) 既可适用于老厂生产工艺技术改进, 也适用 于新厂建设。 3 5 应用实例 河南安阳第三制药厂采用五级加压逆流提取冬 凌草, 实验证明, 五级逆流提取浓度为单罐错流二次 提取液的 2 9 倍, 热能单耗降低 56 7% , 逆流提取 的乙醇用量仅为错流提取的 1/ 3 左右, 单耗降低约 40% 。河北石家庄神威 药业亦采用了 此种提取工 艺。 4 螺旋输送式连续逆流提取装置 4 1 工艺流程图 该连续式浸出器有 U 形、直线式、平转型、履带 式, 履带传动吊斗式等效多种型式, 主要在粮油行业 使用, 部分在香料行业。在药厂中较多应用直线式, 故在此以直线式为例, 工艺流程见示意图 3。 4 2 工艺流程说明 经前处理合格的药材自投料口自动定量加入, 溶剂从高位槽经流量计控制流量进入进液口( 依靠 投料口略低于排渣口, 液位差逐次流入下一级提取 段) 。药材在螺旋输送机的推动下, 从投料口向排渣 口运动, 药材在提取装置中的停留时间可以通过调 节螺旋推进器的转速来控制。每级浸出装置外加设 加热夹套, 以适应提取不同品种药材。浸出液和药 材在装置中形成反向运动的连续逆流浸出过程, 有 效成分得到充分浸出的提取液从投料口一端流出, 经过一步过滤处理后去浓缩。药渣从排渣口排出, 经挤渣机挤渣后由排渣筒进入出渣小车, 药渣翻转 入渣斗内, 用小货车运走。 4 3 工艺设备配套 该设备是一种较新型动态提取设备, 已获国家 专利, 如配套冷凝器等辅助设备, 可满足溶媒回收要 求。 目前主要有江苏省丹阳市制药机械厂等单位生 产。 4 4 适用场合 ( 1) 适用于小品种或批量不大的生产品种, 或是 试验性生产, 摸索工艺参数和操作条件等。 ( 2) 该装置载热体可为蒸汽、热水、导热油, 浸出 温度可为 60- 100 , 物料和溶剂在不断逆流翻动 中加热, 受热均匀, 适用于热敏性药材的提取。
硫化锌精矿两段逆流氧压浸出原理及综合回收镓锗工艺研究
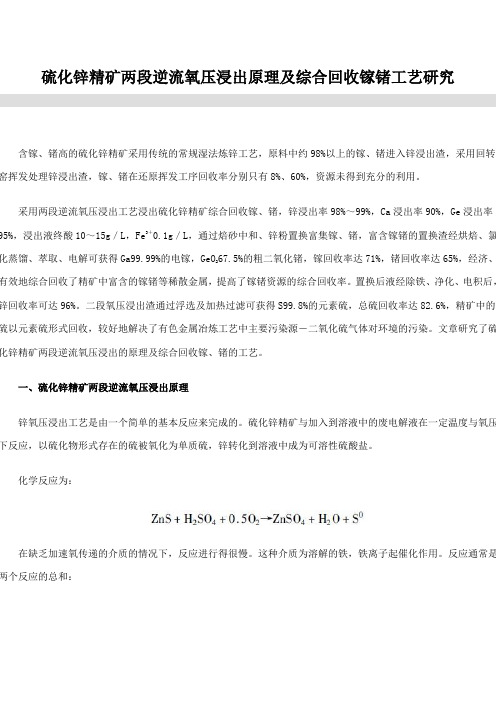
硫化锌精矿两段逆流氧压浸出原理及综合回收镓锗工艺研究含镓、锗高的硫化锌精矿采用传统的常规湿法炼锌工艺,原料中约98%以上的镓、锗进入锌浸出渣,采用回转窑挥发处理锌浸出渣,镓、锗在还原挥发工序回收率分别只有8%、60%,资源未得到充分的利用。
采用两段逆流氧压浸出工艺浸出硫化锌精矿综合回收镓、锗,锌浸出率98%~99%,Ca浸出率90%,Ge浸出率95%,浸出液终酸10~15g/L,Fe3+0.1g/L,通过焙砂中和、锌粉置换富集镓、锗,富含镓锗的置换渣经烘焙、氯化蒸馏、萃取、电解可获得Ga99.99%的电镓,GeO67.5%的粗二氧化锗,镓回收率达71%,锗回收率达65%,经济、2有效地综合回收了精矿中富含的镓锗等稀散金属,提高了镓锗资源的综合回收率。
置换后液经除铁、净化、电积后,锌回收率可达96%。
二段氧压浸出渣通过浮选及加热过滤可获得S99.8%的元素硫,总硫回收率达82.6%,精矿中的硫以元素硫形式回收,较好地解决了有色金属冶炼工艺中主要污染源-二氧化硫气体对环境的污染。
文章研究了硫化锌精矿两段逆流氧压浸出的原理及综合回收镓、锗的工艺。
一、硫化锌精矿两段逆流氧压浸出原理锌氧压浸出工艺是由一个简单的基本反应来完成的。
硫化锌精矿与加入到溶液中的废电解液在一定温度与氧压下反应,以硫化物形式存在的硫被氧化为单质硫,锌转化到溶液中成为可溶性硫酸盐。
化学反应为:在缺乏加速氧传递的介质的情况下,反应进行得很慢。
这种介质为溶解的铁,铁离子起催化作用。
反应通常是两个反应的总和:正常情况下锌精矿中有足够的酸溶铁来满足反应需要,三价铁的存在消除了酸溶硫化锌产生硫化氢。
浸出时,锌精矿中的镓、锗和大量的微量元素一起浸出至溶液中。
硫化锌精矿中铁的行为:)中的硫元素被氧化成硫酸,在相对低的温度和氧分压力下,这类反应速度很慢;在较低温度较黄铁矿(FeS2高酸度氧气不足时黄铁矿被氧化生成元素硫。
低酸条件下三价铁水解生成水合氧化铁和水合氢黄铁矾沉淀。
一种逆流串级浸出提取草木灰中钾盐的方法[发明专利]
![一种逆流串级浸出提取草木灰中钾盐的方法[发明专利]](https://img.taocdn.com/s3/m/fca17233b42acfc789eb172ded630b1c59ee9bcb.png)
(10)申请公布号(43)申请公布日 (21)申请号 201510263608.8(22)申请日 2015.05.22C01D 7/00(2006.01)(71)申请人温军杰地址266038 山东省青岛市浮山后四小区57号楼2-602申请人王毅 徐继尚(72)发明人温军杰 王毅 徐继尚(54)发明名称一种逆流串级浸出提取草木灰中钾盐的方法(57)摘要本发明公开了一种逆流串级浸出提取草木灰中钾盐的方法,技术原理为逆流串级溶出,采用至少2个串级浸出槽,在每个浸出槽内保持一定的灰水质量比、搅拌速度、浸出时间及浸出温度,浸出完成后静置沉降一定时间后固液分离,草木灰及热水固液两相通过泵在浸出槽间逆向传输,得到液相即为钾肥半成品。
该方法成本低廉,反应易控制,工艺过程简单,省时省力,易于工业化大生产。
进行的对比测试表明,工艺整体可比同类技术节省时间30%~50%左右。
采用的工艺是热水,对草木灰可溶性钾进行溶出,可有效避免产生有剧毒的偏磷酸。
本方法所用液相为满足生产工艺用的自来水,未对提取介质有严格要求是“去离子水”,故应用面极广泛。
(51)Int.Cl.(19)中华人民共和国国家知识产权局(12)发明专利申请权利要求书1页 说明书4页 附图1页(10)申请公布号CN 104944445 A (43)申请公布日2015.09.30C N 104944445A1.一种逆流串级浸出提取草木灰中钾盐的方法,其特征在于,该工艺由至少2个浸出槽串联组成,固液两相在浸出槽间逆向转移,具体步骤如下:(1)准备:粉碎至16目以下的原料草木灰,加热至60℃以上的生产工艺用水,可单独控制浸出时间、灰水质量比、搅拌转速、槽内温度的数个串级浸出槽,脱水设备;(2)装料:向浸出槽内装入待提钾的草木灰原料和工艺用热水,灰水质量比1:1.5-1:10,并开动搅拌装置进行工艺启动;(3)逆向串级提钾:浸出过程中满足浸出时间10-65min、搅拌转速40-400r/min、槽内温度65-99℃的要求;每个提钾工段结束后静置沉降2min以上,提钾后的草木灰自左端转移至下一个浸出槽;脱水草木灰与滤液在浸出槽间通过泵逆向输送,依次进行每个浸出提钾工段,液固两相经过在浸出槽内的逆向移动在生产线两端分别进行进料和出料,并可及时补充所缺物料;(4)分离:经历过以上所有浸出槽的固相送入脱水设备操作0.5-15min;液相经过与最后一个浸出槽出液口连接的过滤装置滤去大部分固体,即得到钾肥半成品。
- 1、下载文档前请自行甄别文档内容的完整性,平台不提供额外的编辑、内容补充、找答案等附加服务。
- 2、"仅部分预览"的文档,不可在线预览部分如存在完整性等问题,可反馈申请退款(可完整预览的文档不适用该条件!)。
- 3、如文档侵犯您的权益,请联系客服反馈,我们会尽快为您处理(人工客服工作时间:9:00-18:30)。
浸出渣逆流洗涤试验研究
摘要:当前很多公司都面临着现有生产工艺大量洗水难以平衡的问题,为此,对生产线浸出渣进行逆流洗涤试验,探求较佳的洗涤工艺参数,有利于生产顺利进行,并在一定程度上降低了成本。
试验组进行了相应的浓密逆流洗涤模拟试验,并取得一定效果,希望实验效果能对同类公司有所帮助。
关键词:浸出渣;逆流洗涤试验;洗涤工艺参数
1浸出渣情况
取车间以下浸出渣作检测,并自测比重及干份,以备后序试验。
详见表1。
其中,渣1粘度比渣2较大,渣2呈较多细砂状,渣2的沉降性能明显优于渣1。
2试验方式、步骤
用4个1 000 mL的烧杯,按下述方式、步骤,进行了9份4级浓密逆流洗涤模拟试验:
①参照前期沉降试验数据,选择可行的底流浓度,以湿渣:水(第1份试验时)或前次第4级液=1:1(重量比),在第1级烧杯中调制成固含量为37.5~40%的起始料浆。
②按60~130 g絮凝剂/吨干渣,将絮凝剂配成一定浓度溶液,加入起始料浆,搅匀。
③在上述料浆中加入原湿渣量的一定倍数(0.5~1.5倍)的水(第1份试验时)或前次第2级洗液,搅匀,此时料浆固含量为25~26.7%(1倍液)或21.4~22.8%(1.5倍液),静置。
④当静置后上清液达到步骤3中所加水或洗液量时,抽移该体积量上清液。
剩余料浆则与起始料浆固含量相对一致,将其加入第2级烧杯中,加入同样倍数的水(第1份试验时)或前次第3级洗液,搅匀,静置。
⑤当静置后上清液达到步骤3中所加水或洗液量时,抽移该体积量上清液。
剩余料浆继续保持与起始料浆固含量相对一致,将其加入第3级烧杯中,加入同样倍数的水(第1份试验时)或前次第4级洗液,搅匀,静置。
⑥当静置后上清液达到步骤3中所加水或洗液量时,抽移该体积量上清液。
剩余料浆加入第4级烧杯中,加入同样倍数的水,搅匀,静置。
⑦当静置后上清液达到步骤3中所加水或洗液量时,抽移该体积量上清液。
剩余料浆进行抽滤,滤液返回步骤1调制起始料浆,滤渣实物态送化。
简单示意图如图1所示。
3试验数据
第1份(A循环)步骤3为洗水量为原湿渣量的0.5倍(重量比),第2~4份(B~D循环)步骤3为洗水量为原湿渣量的1倍,第5~9份(E~I循环)步骤3为洗水量为原湿渣量的1.5倍;第1~6份原渣为渣1,第7~9份原渣为渣2;静置分相时间,1~1.5 h即可分出所需体积的上清液。
试验化验数据见表2。
4分析与建议
4.1分析
①试验数据表明,当第4级上清液钴含量在2.3 g/L以下时,抽滤后洗渣总钴在0.14%以下,达到排放标准。
生产线可抽样检测第4级上清液钴含量,以该级上清液钴含量控制在1.4~1.8 g/L来调节洗水用量。
②试验数据表明,在起始料浆及每级底流料浆浓度都控制在37.5~40%时,洗水量为投入的压滤后湿渣的1.5倍(重量比)或3倍(体积比)左右,即可达到洗涤要求。
4.2建议
①选择适当的底流浓度,以压滤后湿渣:第4级液=1:1(重量比),或压滤后湿渣:第4级液=1:2(体积比),调制成固含量为37.5%~40%的起始料浆。
②按60~130 g/t的絮凝剂干渣,将絮凝剂配成一定浓度溶液,加入起始料浆,搅匀。
③控制洗水量为投入的压滤后湿渣的1.5倍(重量比)或3倍(体积比)左右,4级浓密逆流洗涤。
抽样检测第4级上清液钴含量,以该级上清液钴含量控制在1.4~1.8 g/L来调节洗水用量,同时以洗渣中钴含量作为调节参数。
参考文献:
[1] 黄利伟.浸出矿浆多级连续逆流洗涤的计算方法[J].矿冶,2009,(6).。