Influence of ultrasonic vibration on micro-extrusion
超声波振落的原理

超声波振落的原理English:The principle of ultrasonic vibration is based on the phenomenon of the piezoelectric effect. Piezoelectric materials, such as quartz crystals or certain ceramics, can convert electrical energy into mechanical vibrations and vice versa. When an alternating current is applied to the piezoelectric element, it causes the crystal lattice to vibrate at a specific frequency, producing sound waves in the ultrasonic range. These sound waves are then transmitted through a medium, such as air or water, and can be used for various applications.Ultrasonic vibrations have several unique properties that make them useful in different fields. One important property is the high frequency range they operate in, typically above 20 kHz. This high frequency allows for precise control and fine detailing in applications like ultrasonic cleaning, cutting, or welding. Another property is the directionality of ultrasonic waves. They can be focused into a narrow beam, allowing for precision targeting in medical imaging or non-destructive testing. This focused energy can also be used to break down particles or remove dirt through a process known as cavitation.Cavitation occurs when the high-frequency sound waves create alternating pressure waves in a liquid or fluid medium. As the pressure decreases during the rarefaction cycle, the liquid can vaporize and form small gas-filled bubbles or cavities. When these bubbles collapse, they produce intense heat and shock waves, creating tiny shockwaves that dislodge particles or dirt from surfaces. This phenomenon is commonly used in ultrasonic cleaning devices or medical procedures like lithotripsy, where the shockwaves are used to break down kidney stones.The translation in Chinese: 超声波振落的原理基于压电效应。
超声振动作用原理

超声振动作用原理Ultrasonic vibration is a process in which high-frequency sound waves are used to agitate and generate mechanical energy. 超声波振动是利用高频声波来激发和产生机械能的过程。
This technology is widely used in various industries, including medical, automotive, and manufacturing. 这项技术广泛应用于医疗、汽车和制造等各个行业。
The principle behind ultrasonic vibration lies in the conversion of electrical energy into mechanical vibrations through the use of piezoelectric transducers. 超声波振动的原理在于通过压电换能器将电能转换为机械振动。
One of the main applications of ultrasonic vibration is in ultrasonic cleaning, where the high-frequency sound waves are used to remove dirt and contaminants from various objects. 超声波振动的主要应用之一是在超声波清洁中,高频声波用于从各种物体上去除污垢和污染物。
This process is highly effective in cleaning delicate and intricate parts that are difficult to reach using traditional cleaning methods. 这个过程在清洁难以用传统方法清洁、精细复杂部件时非常高效。
【机械专业英文文献】通过立式六轴控制并应用超声振动加工锐角转角

Manufacture of Overhanging Sharp Corner by Means of 6-Axis Control Machining with the Application of Ultrasonic Vibrations feliciano H.JAPITANA**,koichi MORISHIGE**,shugo YASUDA** and yoshimiTAKEUCHIThe study proposes a new machine method to creat an create an overhanging sharp corner. Sharp corners on overhanging surfaces are difficult to machine in conventional way or even in 3 to 5-aixs EDM especially if the surfaces have different angles. This is due to the limitation of the feed direction and the structure of the electrode wherein it must be symmetrical with the target shape. In present research, we try to machine the sharp corner with overhanging surfaces using the new machining method. The 6-axis control machining is applied to set a non-rotational tool at an arbitrary position with arbitrary position with arbitrary attitude against the workpiece. During cutting, the ultrasonic vibration is applied on the cutting edge of the tool, while the tool travels along the feed direction. As the cutting is performed, the 6-axis (X,Y,Z,A,B and C) move simultaneously, depending on the tool attitude at a certain cutting point. Form the experimental results, it is shown that the 6-axis control ultrasonic vibration cutting is capable of producing a sharp overhanging surface.Key Words: 6-axis Controlled Cutting, CAD/CAM System, Bore Byte Tool, Overhanging Sharp Corner, Ultrasonic Vibration Cutting Tool1.introductionThe flexibility of products may be extended greatly if the restriction in manufacturing process can be minimized or eliminated. If rotational tools such as ball end mills or square end mills are used in the production of a mould with an overhanging sharp corner (OHSC), it seems difficult to clearly obtain the target shape with sharp edge lines. This is due to the result of processing with the rotational tools, Which are symmetrical with the rotation. The arc-like radius remains are produced on adjoining surfaces, as shown in Fig.1 Conventionally, most of overhanging or inclined surface can be machined by setting the workpiece at a certain angle in the vise, swivelling the universal vise, or by setting the tool head to a certain angle and feeding the cutting tool head, as shown in Fig.2(a). In this process, the overhanging surfaces and the sharp edges at the bottom are produced. However, if the target is an OHSC consisting of two overhanging side surfaces, and theinclination angle of surface is not uniform, the processing of the target shape is difficult to achieve since the cutting direction in the process is fixed and limited only to linear cutting. Thus ,it needs a lot of jigs and fixtures to hold a workpiece ,to position correctly with respect to a machine tool and to support it during machining.Fig.1 5-axis control machining using rotational toolFig.2 method of producing sharp corner with overhanging surfacesThe other possible method to produce such a shape is multi-axis Electric Discharge Machining (EDM), as shown in Fig.2(b).However, even using this method ,it is difficult or impossible to produce an OHSC with different angle .It needs 6 degrees of freedom to fully execute the machining of the required shape.In the previous researches, ultrasonic vibration (USV) was applied in turning of ductile material and milling of glassfiber-reinforced plastic. The cutting force with USV is considerably reduced. However , in the former process ,the workpiece is rotated or moves to towards the cutting tool, and in the latter, machining is limited only to 2 or 3 axis control one. In the other field of research, multi-axis control machine tool is used to complete a machining in one setup, which leads to the production of workpiece with high accuracy and quality and to the reduction in machining time.In this study, 6-axis control cutting using a non-rotational cutting tool with the application of ultrasonic vibration (USV) is used, as shown in Fig.2(c).It is applied to scrutinize the validity of the method in the fabrication of OHSC, The C-axis rotates the non-rotational tool simultaneously together with X,Y,Z,A or B axis during machining .The movement of the axes is based on the tool attitude and the cutting point generated by a developed CAM software. The CAM program generates a collision free tool path to assure the safety of the process. The 6-axis control machine tool provides easily the machining capability of OHSC, since 6degrees of freedom make the machining execute fully the required product shape. Also, with the application of USV, a bore byte tool is utilizded, considering its size and stiffness during machining operation since the cutting force is greatly reduced.2.Experimental procedureThe experiment steup is shown in Fig.3, wherein the workpiece is mounted on the table of the 6-axis control machining center. The bore byte tool is mounted in the USV tool using an adaptor. The USV tool is turn mounted on the main spindle of the 6-axis control machining center.2.1Multi-axis control machine tool and bore byte toolThe 6-axis control machining center used in the study is shown inFig.4. The machining center provides multi-axis CNC machine tools.The 6-axis control machine tool has 3 rotational axes A,B and C. It is constructed by adding the rotational function C on the main spindle of a 5-axis control machining center which has 2 rotational axes,namely;A, which is a rotary tilting table and B, which is the rotary index table. The, and that of rotational one A,B minimum unit for translation movement X,Y and Z is 1mand C is 0.36 arc second. In the case of cutting of OHSC, A axis is used for determination of side surface and the inclination angle of sharp corner ,B axis for workpiece rotation ,C axis for determination of cutting tool direction, X and Y axis for the determination of feed direction of feed direction while the depth of cut is determined by Z axis. Fig 5 shows the non-rotational cutting tool (bore byte tool) used in the study. It is made of tungsten carbide usually used here in 6-axis control cutting. The total length and diameter of the tool are70mm and 6mm respectively.2.2Ultrasonic vibration toolFif.6 is a commercially available USV tool (SB-150:Taga Electric Co). used in the study. The USV is applied on the cutting edge of the tool.In order to perform an efficient and effective vibration cutting, the vibration direction must be set parallel to the cutting direction. Since the vibration direction is not always parallel with the feed direction, the tool attitude of the bore byte tool is subjected to arrangement. As illustrated in fig.7(a), the tool axis vextor T and the tool direction vector D and modified by arranging the rolling and the inclination angle respectively. These are converted into modified tool axis vector T and modified tool direction vector D, as shown in fig.7(b). The transformation of the tool axis vector and the tool direction vector are carried out in cutter location (CL) conversion.2.3CAD/CAM systemThe configuration of 6-axis CAD/CAM system is shown in fig.8, where 3D-CAD data of the target shape is generated . The type of bore byte tool must be selected, based on the target shape. The main processor generates the collision free CL data on the bases of tool information and tool orientation as well as 3D-CAD data of the target shape.The post processor converts CL data generated by the main processor into 6-axis control NC data suitable for the coordinate system of the machining center with reference to the structure information of the machining center, setting information, cutting condition and vibration condition. In addition, so-called linearization operation is dine in order to keep the feed rate to the machining center structure constant and to minimize the tool path deviation. It leads to assure the smoothness of the product surface especially in dealing with curve surfaces.Before converting CL data into NC data, CL data must be firstly checked for collision to assure the safety of the machining process .If the collision is detected in this stage, the modification of CL data is carried out, using the main processor.3.Manufacture of Sharp Corner with Overhanging Surface3.1Determination of tool attitudeIn order to expresshe entire tool attitude for 9-axis control ultrasonic vibration cutting, the tool attitude of the bore byte tool, as shown in Fig.9, is appointed by the coordinates P for cutting point, the tool axis vector T and the tool direction vector D. These PTD coordinates are converted to NC data, and are in turn used in machining operation. In6-axis control cutting with application of ultrasonic vibration, the movement and the attitude of the tool must be determined in consideration of the vibration direction. Since the cutting direction changes rapidly, the tool attitude changes a lot to keep the tool angle constant to the surface shape.3.2Generation of tool pathThe tool path generating method for OHSC can be described as follows; the OHSC is composed with two ridgelines, as illustrated in Fig.10. The intersecting line is called as a bottom ridgeline and the cross section line is called as a side ridgeline .Finishing the side ridgeline as well as the bottom ridgeline is required to make a sharp corner.3.2.1Generation of tool path for side surfaceThe surface that makes a side ridgeline is composed with left and right surfaces respectively. In producing a side ridgeline of the sharp corner, machining of left and right surfaces is necessary. The outline of the tool path generation method for side surfaces of the OHSC is described in Fig.11.The side to be machined and the tool feed direction must be selected at first, based on the type of bore byte tool and the target shape. The adjoining surfaces that make a side ridgeline, is expressed with parameters u and v. The fix curve , which is equal to parameter v, is generated on the side from the upper part of the surface to the bottom. The division number of surface is input to sequentially generate the number of cutting points. Each cutting point on a reference line are generated, using the value of parameter u, so that the distance between the cutting points may settle below in the specified value.Changing the tool attitude at every point of the cutter location ,the tool moves sequentially on each cutting point from the start point until the side ridgeline is formed. Although the cutting point is connected each other in order to acquire the tool path, it is difficult to process both adjoining sides by one direction due to the tool structure and the target product shape. In addition , the collision may take place between the tool and the workpiece. In this situation, the tool starts from the start point of the tool path to process the left side surface, and ends at the corner where the ridgeline is to be formed. Thus is repeated until it reaches to the bottom surface. The depth of cut is based in the division number of the total length of curve for curve surface. The same thing is done on the right side surface since there is still an arc-like remain at the corner part of the side surface. The procedure is almost the same as with the processing of the left side surface, however thecutting end point is the same with the end point of the left side processing, to form the clear ridgeline .Processing of the right side surfaces is also done using the left hand tool.The tool direction vector D during the tool path generation for side surfaces is rotated by 10degrees to make the vibration direction parallel to the feed direction vector F. The tool path is generated by connecting the cutting points in order from the starting point to the end point. The tool attitude during cutting is determined from the normal vector N and the tool feed direction vector F at the cutting point. The tool feed direction vector D and the tool axis vector T can be expressed as D=F*N and T=N respectively.3.2.2Generation of tool path for bottom surfaceFigure 12 describes that tool path generating method for bottom surface that makes the bottom surface that makes the bottom ridgeline of the OHSC. After generating the tool path for side surfaces, the tool path for bottom ridgeline is successively generated, where the tool is inclined to the bottom surfaces. There are two methods of generating a tool path for bottom surfaces; one is one-path method shown on the upper left part, and the other multi-path method shown in the upper right part of the figure. In one –path method ,the cutting tip of the tool directly makes contact with the location of the bottom ridgeline. In this operation, the tool inclination angle is necessary to fully remove the arc-like remains on the bottom surface and to form a clear ridgeline. During the tool path generation, the tool axis vector T is inclined, based on the calculated inclination angle against the bottom surface and the clearance angle of the cutting tool, which is 5 degrees.The method of determining the cutting start point as well as the cutting end point is the same as that of generating a tool path for side ridgeline.In multi-path method, the pitch from the bottom surface is expressed by use of parameters u and v. The generation range of a cutting reference line is determined from the shortest distance between the arc-like remains after rouging and the reference line of thebottom ridgeline. Cutting points is generated on the basis of parameter v in each reference line. The systems determines the tool attitude during cutting from the tool axis vector N at the bottom surface and the tool feed vector F at cutting point along a cutting reference line. The tool axis vector T and the tool direction vector D can be express as T=N and D=N*F respectively. The cutting start point is assumed near the arc-like radius remains and it ends at the last point of the generated cutting point in the reference line. Moving the tool along each neighboring cutting point can make the tool path.4.Experimental Results4.1Effect on cutting forceThe cutting force was measured by use of piezoelectric dynamometer (9257B,Kistler Co,Ltd), thus averaging the measured cutting force and processing it in the root mean square(rms) manner.table1 measured cutting forceMachining was conducted both with USV and without USV. The cutting conditions used are as follows: feed speed of 400mm/min and different depth of cut of 0.1,0.2,and 0.3mm respectively. The vibration conditions are in the following; frequency of 19kHz,and rolling angle of 10 degrees. The acquired result is shown in amplitude of 36mTable1. It can be seen that the cutting force in cutting with USV is much smaller as compared to cutting without USV. Since the cutting force was greatly reduced, the stiffness of the tool can be maintained all throughout the process.4.2Machining of OHSCThe cutting experiment was also made in order to scrutinize the validity of the new machining method. The workpiece size used for the experiment is 100×100×20 mm and the material is an aluminimu alloy(JIS A5052), which is also commonly used for low cost mould with low molding pressurre such as blow moulding, vacuum forming, rubbermoulding,etc.Two types of OHSC model were tired in the experiment, one is OHSC with plane surface and the other is OHSC with curve surface. The side surfaces consist of different inclination angle. The inclination angle o the surface at the cutting start point is not the same as the inclination angle at the cutting end point. In this condition, the inclination angle is not uniform all thoughout.Shown in Fig.13(a) is the machining model for OHSC with plane surfaces, rugh cutting must be at firdt done in order to perform an effcient cutting by 5-axis control machining, using the rotational ball end mill with a radius of 3mm and 1.5mm respectively. Machining is carried out until the target product shape is almost obtained. Since the target sharp corner is not clearly obtained due to the arc-like remains, as shown in Fig .13(b), finishing will be performed, using the 6-axis control cutting with the application of theUSV. with plane surface. Inthis process ,the left side or right side surface is firstly machined, depending on the choice.Let us assume that the left side surface is machined. The cutting and vibration conditions listed in Table 2 were used in machining on the basis of NC instructions generated by the developed CAM program. After machining the side surface, the bottom surfaces is machined in the next step, using the one path method. The cutting conditions listed in Table 2 were also used except for the inclinations angle of 9 degrees and the depth of cut of about 1.5mm. The depths of cut were based on the arc-like remains of the ball end mill used during roughing.Machining of the left side surfaces is done, using the right hang tool.After finishing the machining of the left side surface, the right side is processed in the next step under almost the same conditions as the processing of the left side except that the tool used is a left hand too. Shown in Fig.13(d) is the result of machining experiment.The machining model for OHSC with curve surfaces is shown in Fig.14(a). In machining OHSC with curve surface, roughing must also be performed, as shown in Fig.14(b). The sequence of operation from roughing to finishing is almost the same as described previously. However, so-called linearization operation is required to make the product surface smooth. To process the bottom surface that makes the ridgeline, the multi-path method was emplyed since the method is suitable in curved surfaces. Table 2 lists the cutting and vibration conditions used in the process. Also, shown in Fig.14(c) and Fig.14(d) are the actual machining and the product after finishing process respectively. The total machining time with this experiment is 112 minutes including rough cutting time. Only one machine was used as well as one steup of the workpiece in the entire process.The cutting effciency has been drastically improved due to the increase of cutting speed by applying of ultrasonic vibration since the normal cutting speed of non rotational cutting tools is equal to the feed rate.ConclusionThe experimental results show that the usage of bore byte tool is maximized and that the tool stiffness is enough to carry out machining due to the significant reduction of cutting force by applying the ultrasonic vibrations. It is found that only one machine can cope with machining of the product from roughing to fingshing , which leads to the potential of cost saving since the extra process like set-up from one machine to another can be eliminated. As a result, the validity of the developed CAM to machine OHSCs with plane and curve surface is experimentally confirmed throughout the study.AcknowledgementThe authors would like to express their sincere appreciation to Mr.Crisanto de laCruz(MIRDC-DOST) and Mr.Tohru Ishida (The University of Elector-Communications) for their valuable support and information.A part of the study is funded by the grant in aid for Scientific Research of the Ministry of Education (B12450057).references(1)Cecil, J A Clamping Design Approach for Automated Fixture Design, The InternationalJournal of Advanced Manufacturing Technology, V ol.18, No.11(2001),pp.790-793. (2)Moriwaki, T, Shanmoto ,E. and Inoue, K,Ultrapresicion Ductile Cutting of Glass byApplying Ultrasonic Vibration, Annals of the CIRP,V ol.41, No.1(1992),pp.141-144. (3)Takeyama, H. and Iijima, N, Machinability of Glassfiber Reinforced Plastics andApplication of Ultrasonic Machining, Annals of the CIRP, V ol.37, No.1(1998),pp.93-96.(4)Shamoto, E. and Moriwaki, T, Study on Elliptical Vibration Cutting, Annals of theCIRP, V ol.43,No.1(1994),pp.35-38.(5)Moriwaki ,T. and Shamoto, E,Ultrasonic Elliptical Vibration Cutting ,Annals of theCIRP, V ol.44,No.1 (1995),pp.31-34.(6)Takeuchi, Y. and Suzuki, H. Efficient and Accurate Manufacturing by means ofMulti-Axis Control Machine Tools, Proceedings of the Japan-USA Symposium on Flexible Automation, ASME and ISCIEJ, Boston, Massachusetts, July7-10,1996,V ol.1,pp.343-347.(7)Radzevich, S.P. and Goodman, E .D, Efficiency of Multi-Axis NC Machining ofSculptured Surface, Proceedings of the International Conference on Sculptured Surface machining, Nov.9-11,1998,pp42-56.(8)Morishige, K, Kase,K and Takeuchi, Y, Collision-free Tool path Generation GenerationUsing 2-Dimensional C-Space for 5-Axis Control Machining, The International Journal of Advanced Manufacturing Technology, V ol.13, No.6(1997),pp.393-400.(9)Morishige, K, Kase,K and Takeuchi, Y, six Axis Control Character Line FinishingUsing Ultrasonic Vibrational Cutting Tool, 10th International Conference on Precision Engineering (ICPE), Yokohama, Japan, July 18-20,2001,pp.249-2563.。
超声骨刀英文版护理课件
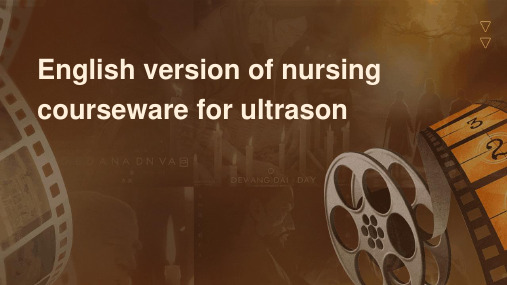
02
Preoperational care
Patient assessment
Physical condition
Assess the patient's general physical condition, including vital signs, weight, height, and body mass index
within normal limits
Monitor respiration
03
Monitor respiration regularly to ensure that it remains
within normal limits
Prevention of applications
Prevent infection
Prevent thromboembolism
Thromboembolism is a serious complication that can occur during surgery, so the number should ensure that all necessary measures are taken to
Assist the surgeon in sterilizing the surgical field
The nurse should assist the surgeon in sterilizing the surgical field and ensuring that all surgical instruments and equipment are sterile before the
Training and education
基于SIMPACK的车辆系统动力学性能分析

重载、曲线半径过小等问题ꎬ分析其动力学性能ꎮ 试验中根据脱轨系数、轮重减载率、轮轴横向
力等指标参数ꎬ对列车运行的平稳性及稳定性进行评估ꎮ
关键词:SIMPACKꎻ平稳性ꎻ安全性ꎻ直线运行ꎻ曲线通过
中图分类号:U270 文献标志码:B 文章编号:1671 ̄5276(2022)05 ̄0095 ̄03
根据建模后的离线分析结果ꎬ分别计算各运行速度下
平稳性等级
良好
的W y 、W z 、N MV 、Mα cy 、Mα cz 、Sα cy 及Sα cz ꎬ并根据所得数据进
表 3 客车运行平稳性指标与等级
2
TC2
E LNI
图 6 MP1 空车工况下平稳性指标平均值( 建模)
所有情况下的轮轨力以及其位置ꎬ因此还需进行更多相关
车轮滚动圆直径 / mm
耗ꎬ提高车辆的运行安全性和舒适性ꎬ基于车辆动力学理
钢轨 / ( kg / m)
种地铁线路缓和曲线线型进行研究ꎬ分析了各线型下的轮
车体质量 / kg
的研究 [6] ꎮ 周素霞等 [7] 为了减 轻 地 铁 运 行 中 的 轮 轨 磨
0.05
信号传输采用集流环装置ꎮ
0
5$
.1
DD4
B
6D2
,
AO
DFD(
0.4
图 7 轮对的蛇行运动
0.2
试验载荷工况包括:空车、重载ꎮ
列车在行使过程中会出现蛇行运动的现象ꎮ 蛇行运
0
动为非线性自激振动ꎮ 它是由蠕滑力和轮轨几何关系引
A Study on Ultrasonic Assisted Creep Feed Grinding of Nickel Based Superalloys -Procedia CIRP

P roc edia CIRP 1( 2012 )359 –364Available online at 2212-8271 © 2012 The Authors. Published by Elsevier B.V. Selection and/or peer-review under responsibility of Professor Konrad Wegener/ 10.1016/j.proc ir.2012.04.0645th CIRP Conference on High Performance Cutting 2012A study on ultrasonic assisted creep feed grinding of nickel basedsuperalloysD. Bhaduri a , S.L. Soo a,*, D.K. Aspinwall a , D. Novovic b , P. Harden c , S. Bohr d , D. Martin eaMachining Research Group, School of Mechanical Engineering, University of Birmingham, Edgbaston, Birmingham, B15 2TT, UKbTurbines, Rolls-Royce plc, Derby, DE24 9BD, UK cElement Six Ltd., Shannon, Co. Clare, Republic of IrelanddSaint-Gobain Diamantwerkzeuge GmbH & Co. KG, Schützenwall 13-17, D-22844 Norderstedt, GermanyeHardinge Machine Tools, Whetstone, Leicester, LE8 6BD, UK* Corresponding author. Tel.: +44-121-414-4196; fax: +44-121-414-4201.E-mail address: s.l.soo@.AbstractThe paper initially reviews research relating to ultrasonic (US) assisted grinding of various workpiece materials. Results from experimental trials to evaluate the influence of applying US vibration when creep feed grinding Inconel 718 with an open structured, alumina based grinding wheel (POROS 2) are then presented. A full factorial experimental array comprising 18 runs was conducted involving variation in wheel speed (30, 35 and 40m/s), table speed (200, 250 and 300mm/min) and grinding condition (with and without vibration). For tests with US vibration, the workpiece was actuated at a constant frequency (~20kHz)via a specially designed block sonotrode attached to a 1kW piezoelectric transducer-generator system. Reductions in vertical (F V )and horizontal (F H ) grinding force components of up to 23% and 43% for F V and F H respectively and surface roughness (S a ) of the ground slots by up to 45% were observed in the majority of tests when utilising US assisted operation. In terms of surface quality,SEM micrographs revealed greater side flow/ploughing and overlapping grit marks in slots machined with the workpiece vibrated in comparison to standard creep feed ground specimens. Three dimensional topographic measurement of grinding wheel surface replicas indicated that US vibration led to an increase in the number of active cutting points on the wheel.© 2012 Published by Elsevier BV. Selection and/or peer-review under responsibility of Prof. Konrad Wegener Keywords: Grinding; nickel; ultrasonics; vibration.1. IntroductionThe use of ultrasonic actuation as a method formaterial removal was first proposed in a paper by R.W.Wood and A.L. Loomis in 1927, with the first patent granted to L. Balamuth in 1945 [1]. Developments sincethen have seen ultrasonic machining (USM) applied to the cutting of hard but brittle materials such as glass, ruby and ceramics. Traditional USM operation involves a horn and tool arrangement vibrated at frequencies of20kHz with relatively small amplitudes of ~10-20μm,that is used to impact against an abrasive slurry betweenthe tool and workpiece causing localised fracture. The scope of the technology was further expanded to encompass ultrasonic vibration as an assistive mechanism in a ‘hybrid’ configuration with conventional metal cutting (turning, drilling, milling & grinding) aswell as metal forming processes.Some of the earliest work relating to ultrasonic assisted grinding (UAG) dates back to the mid-1950’s [2] and highlighted benefits such as reductions ingrinding temperature and workpiece tensile residual stresses, albeit at a cost of lower G-ratios due to a greater degree of wheel breakdown. Several years later, a project undertaken by the United States Air Forcereported work on excitation of the grinding wheel in a radial direction by attaching the transducer to a half-wave bar (the wheel hub) [3]. A novel technique involving the use of US vibration to clean and prevent loading of pores in a grinding wheel was proposed by Kaliszer and Limb [4], which utilised a special coolantactivator oscillating along its axis and radial to the wheel © 2012 The Authors. Published by Elsevier B.V . Selection and/or peer-review under responsibility of Professor Konrad WegenerD. Bhaduri et al. / P rocedia CIRP 1( 2012 )359 – 364 360periphery. The ultrasonically cleaned wheels exhibited greater permeability, higher G-ratio and reduced chatter vibrations in comparison to the non-ultrasonically treated wheels.The majority of published work on UAG over the past ~20 years can be broadly divided into two sub-categories, depending on whether the vibration was applied to the grinding wheel or workpiece. Nakagawa et al. [5] studied the effects of vibrating a cast iron fibre bonded diamond wheel during the grinding of alumina, silicon nitride and tungsten carbide. They found that larger depths of cut were possible leading to higher material removal rates (MRR) and improved dimensional accuracy, together with a 60-70% reduction in normal grinding force. A similar system was also shown to be capable of fabricating precision micro cylindrical tools and micro drills [6], as well as producing machined features having non-circular cavities and blind holes with sharp corners [7]. While not generally recommended for ferrous alloys, Hara et al. [8] demonstrated that it was possible to produce mirror surfaces when grinding die steel (NAK80) with diamond electroplated tools vibrating at a frequency of 60kHz and an amplitude of 4μm. Use of a vibrating CBN wheel for grinding small holes in stainless steel was also found to reduce both normal and tangential forces as well as workpiece surface roughness by ~20% [9].Research involving vibration of the workpiece has been more extensive, primarily due to the comparatively simpler experimental setup. Spur and Holl [10] utilised a workpiece based US assisted creep feed grinding system to achieve a 50% reduction in normal force when machining sintered silicon nitride and alumina, but at the expense of a marginal increase in wheel wear due to higher amounts of micro-splintering of grits under the hybrid configuration. A similar wear mechanism was observed by Uhlmann [11], whose study also revealed that vibration rendered an intermittent cutting action together with higher mechanical but lower thermal loads on the grits. Several investigations with nano-zirconia based ceramics revealed that the material removal mechanism changed from fracture in conventional grinding to a ductile regime when using UAG [12-13].Wu et al. [14] detailed the development of an innovative elliptic ultrasonic vibrating shoe (instead of two separate transducers) for centreless grinding, which was subsequently utilised in fabricating microscale cylindrical tungsten carbide components with a diameter of 60ȝm over a length of 15mm (aspect ratio of 250) [15]. In an attempt to minimise/eliminate the need for coolant, ultrasonic assisted operation was implemented to investigate the feasibility of dry surface grinding soft steels including 100Cr6 [16-17] and 42CrMo4 [18]. Significant reductions in normal and tangential forces (~30-50%) were obtained when applying ultrasonic actuation, which also decreased thermal damage/ grinding burn, thereby improving workpiece surface finish.The body of research on UAG to date has mainly focussed on the surface grinding configuration of materials such as ceramics, glass and various grades of steel (stainless, plain carbon, alloyed etc.), but little information is available on ultrasonic assisted grinding of advanced aerospace materials such as nickel based superalloys. The aim of the current work was to investigate the effect on grinding forces (vertical and horizontal), workpiece surface roughness/quality (2D and 3D topographical parameters) and wheel wear (G-ratio), when employing ultrasonic vibration during creep feed grinding (CFG) of Inconel 718with an alumina wheel.2.Experimental detailsThe experimental trials were conducted on a Bridgeport FGC1000 flexible grinding centre, with a maximum spindle speed of 6000rpm and power rating of 25kW. Rectangular blocks of solution treated and aged Inconel 718 (hardness of ~44±1HRC) measuring 110×50×10mm were used as the workpiece material. These were clamped onto a specially designed aluminium table/block sonotrode (similar to the one detailed by Azarhoushang and Tawakoli [19]) mounted on the machine worktable, which was connected to a 1kW piezoelectric transducer-generator system, see Fig.1. The transducer was attached to transmit the US vibration in a direction parallel to grinding feed. The alumina grinding wheels known commercially as POROS 2, had a plain geometry, vitrified bond, open structure (specification: 25A601 I 74 VPMCNN), a diameter of 220mm and a width of 25mm.The full factorial experimental array comprised 18 tests involving variations in wheel speed (30, 35 and 40 m/s), table speed (200, 250 and 300 mm/min) and grinding condition (with and without vibration). Depth of cut/pass was fixed at 1.0mm with all trials performed in a down grinding creep feed mode without spark-out. The experimental array is shown in Table 1. Each test involved a single pass of the workpiece (50mm cut length).Dressing of the POROS 2 wheel (after each trial) was carried out using a diamond roller dresser (ĭ 105mm) with an average grain size of ~800μm and spacing of ~1.5mm. Two high pressure pumping systems were used to supply fluid for wheel cleaning (70bar) and into the grinding zone (28bar) via laminar flow nozzles having rectangular cross-sectioned orifices measuring 0.5×20mm and 2×20mm respectively (25mm wide nozzles were not available). The grinding fluid was aD . Bhaduri et al. / P rocedia CIRP 1 ( 2012 ) 359 – 364 361water-based synthetic oil product, Trim C270, with a concentration of 7–10%.Fig. 1. Experimental setup; (a) Block sonotrode and transducerarrangement, (b) on-machine configurationTable 1. Full factorial experimental arrayTest no. Wheel speed, V c (m/s ) Table speed, V w (mm/min ) Condition ofvibration 1 30 200 OFF2 30 200 ON3 30 250 OFF4 30 250 ON5 30 300 OFF6 30 300 ON7 35 200 OFF8 35 200 ON 9 35 250 OFF10 35 250 ON 11 35 300 OFF12 35 300 ON13 40200 OFF14 40 200 ON15 40 250 OFF16 40 250 ON17 40 300 OFF18 40 300 ONFor trials involving US vibration, the workpiece was actuated at a constant frequency of ~20kHz, while the amplitude of vibration was specified on the generator interms of a percentage scale ranging from 0 to 50%. The actual amplitude of the block sonotrode under zero-load condition (workpiece mounted but without grinding) and vibrating at the 50% setting was measured using a Polytech OFV 3001 Laser Doppler Vibrometer coupled to an OFV 303 sensor head. The maximum amplitude recorded was 4.2μm, depending on the positions of the nodes and anti-nodes on the surface of the sonotrode.The block sonotrode exhibited multi-modal vibration in all 3-axes.Vertical (perpendicular to feed direction) and horizontal (parallel to feed direction) grinding forces were measured using a Kistler 9257A 3-component piezoelectric dynamometer coupled to charge amplifiers and a PC running Dynoware software. In order to determine the G-ratio, wheel diameters were measured before and after each grinding trial using a DEA Swift manual coordinate measuring machine (CMM)connected to a computer programmed with Delcam Power Inspect software. The wheels were assessed at 30different points around the periphery, each at 5 different levels of the wheel width.Both 2D and 3D topographical profiles of the ground workpiece surfaces were recorded using a Taylor Hobson Form Talysurf 120L, with 2D assessment involving a 0.8mm cut-off. Micrographs of the ground surfaces were taken using a JEOL 6060 scanning electron microscope (SEM). Due to space restrictions inthe SEM chamber, wheel surface topography was assessed by producing negative and positive replicas using a graphite block and rubber-resin compound respectively. For the former, the worn wheel was used to grind a graphite block at a wheel speed of 15m/s, table speed of 150mm/min and depth of cut of 1.0mm. Theresulting surface profiles were then traced, which represented negative profiles of the wheel surface (assumed zero wear from grinding of graphite block). In contrast, positive replicas of the wheel surfaces were obtained using a synthetic rubber and resin replicating compound (Microset), after which 3D surface profiles were measured using the Form Talysurf system. 3. Results and discussion 3.1. Grinding forces, radial wheel wear and G-ratio Figure 2 details the vertical (F V ) and horizontal (F H )grinding forces both with and without US vibration. It was observed that when operating without ultrasonics,grinding forces generally increased as the table speed was varied from 200 to 300mm/min due to a corresponding rise in the undeformed chip thickness.Conversely, no such trend was apparent with theincrease in wheel speed from 30 to 40m/s. TheD . Bhaduri et al. / P rocedia CIRP 1 ( 2012 ) 359 – 364362application of US vibration however led to lowergrinding forces in the majority of tests, although reductions in F H was more prominent and varied between 26 to 43%. This was most likely due to the intermittent cutting action of the abrasives under vibration leading to reduced frictional forces in the contact zone between the grits and workpiece as well as smaller average chip thicknesses, despite the modest amplitude generated by the ultrasonic transducer-generator system.Fig. 2. Vertical (F V ) and horizontal (F H ) forces under different grinding conditionsThe effects of operating conditions on radial wheel wear and G-ratio are shown in Fig 3. In general, radial wheel wear (RWW) decreased as the table speed increased from 200 to 300mm/min when operating under standard CFG mode. This was attributed to the shorter contact time between the wheel and workpiece material.Fig. 3. Radial wheel wear and G-ratio under different grinding conditionsWith the hybrid configuration, wheel G-ratio was seen to improve by between 7 to 45% in 5 of the 9 trials (Tests 2, 4, 6, 14, 18), although it was also found to decrease in 3 of the remaining 4 experiments (Tests 10,12, 16). The reason for the latter is unclear, but the highly porous and open structure of the alumina wheel could have led to errors during measurement of wheel diameters using the contact based CMM probe. 3.2. Workpiece surface topography and quality Fig. 4 details the 3D surface topographical parameters (S a , S t , S z ) measured for all tests, while Fig. 5 shows representative 3D topographies of the workpiece surfaces ground with and without ultrasonic assistance respectively. Average surface roughness (S a ) was generally lower when employing US vibration except for tests at the highest parameters (40m/s, 250mm/min and 40m/s, 300mm/min). This was possibly due to the increased incidence of overlapping cuts/greater number of active cutting points per revolution of the wheel compared to when machining under normal grinding conditions, see Fig. 6(a) & 6(b). Conversely, peak to peak (S t ) and 10-point average roughness (S z )parameters were generally higher with surfaces machined under US assisted mode. This was thought to be due to the vibration along the Z-axis of the sonotrode,i.e. in a direction radial to the wheel surface.Furthermore, greater levels of smearing and side flow/ploughing of the workpiece material were evident from the majority of samples analysed when operating with US vibration, which also suggested increased plastic deformation occurred [10], see Fig. 6(c).Fig. 4. 3D topographical parameters of ground workpiece surfacesV w V c G r i n d i n g f o r c e s (N )V c V w G-ratioR a d i a l w h e e l w e a r (μm )V c V w 3D t o p o g r a p h y p a r a m e t e r s , S a , S t , S z (μm )D . Bhaduri et al. / P rocedia CIRP 1 ( 2012 ) 359 – 364 363Fig. 5. Representative 3D topographies of ground surfaces produced; (a) with ultrasonics; (b) without ultrasonicsFig. 6. SEM micrographs of representative ground workpiece surfaces machined; (a) without ultrasonics, (b), & (c) with ultrasonics3.3. Grinding wheel surface evaluationThe average surface roughness (S a ) of the graphite blocks and density of peaks (S ds ) from the resin replicas are shown in Fig. 7. The former value is representative of the post-grinding wheel surfaces, whereas the S ds parameter provides an indication of the static cutting edge density, according to Blunt and Ebdon [20].In general, S a increased as V w was incremented from200 to 300mm/min, irrespective of the wheel speed.Although not shown here, this trend corresponded to equivalent 2D roughness parameters of the ground workpiece surfaces. However following activation of US vibration, the roughness of the graphite replicas/wheel surface decreased in most cases compared to plain grinding, which suggested greater uniformity of the resulting grit heights. This was most likely caused by the ‘conditioning effect’ as a result of the vibration, which also translated to the lower workpiece surface roughness (S a ) detailed in the previous section.Fig. 7. S a of graphite replicas and S ds of resin replicas of the grinding wheel surfaceThe density of peaks (S ds ) of the resin (positive)replicas was found to increase in the majority of tests where vibration was applied (see Fig. 8), although slight reductions were observed in the 3 trials operating at a table speed of 250mm/min (Tests 4, 10 & 16).Fig. 8. Representative 3D topographical plots of wheel surfacesfollowing grinding; (a) with ultrasonics, (b) without ultrasonicsV c V w S ds of resin replica (pks/mm 2)S a o f g r a p h i t e r e p l i c a (μm )D. Bhaduri et al. / P rocedia CIRP 1( 2012 )359 – 364 364It has been reported that a decrease in wheel S ds is generally allied to a rise in workpiece surface roughness, and vice versa [21]. This was in line with results detailed in Fig. 4 & 7 where an increase in S ds (under vibration) corresponded to a lower workpiece surface roughness (S a). This was attributed to the greater number of active cutting points per grain (due to grit fracture) generated with use of US vibration. Butler et al. [21] further suggested that a decrease in S ds value signalled loss of grain sharpness, implying that wheels became sharper when using ultrasonic assisted grinding. In addition, no wheel loading was observed in any of the tests.4.Conclusions•The use of ultrasonic assisted operation typically resulted in the reduction of grinding forces and associated workpiece surface roughness when creep feed grinding Inconel 718 superalloy. Similarly, a corresponding reduction in radial wheel wear and improvement in wheel G-ratio of between 7 to 45%was obtained when grinding in the hybrid configuration.•In terms of surface quality, SEM micrographs revealed greater side flow/ploughing in slots which were machined with the workpiece vibrated in comparison to standard creep feed ground specimens. Furthermore, larger numbers of overlapping grit marks were visible on surfaces subject to ultrasonic assisted grinding.•Three-dimensional topographic measurements of grinding wheel surface replicas indicated that use ofUS vibration generally led to an increase in the number of active cutting points on the wheel. This subsequently resulted in a decrease of correspondingaverage workpiece surface roughness (S a).AcknowledgementsWe are indebted to Dr. A.C. Mathieson and Prof. M. Lucas from the University of Glasgow for the provision of facilities to measure the vibrational amplitude of the block sonotrode. Technical advice from M. Prokic of MP Interconsulting on the ultrasonic transducer and generator system is also gratefully acknowledged. Thanks are also due to Rolls-Royce, Element Six, Saint-Gobain Abrasives and Hardinge Machine Tools for additional funding, tooling and technical support.References[1] Thoe TB, Aspinwall DK, Wise MLH. Review on ultrasonicmachining. Int J Mach Tools Manuf 1998; 38:239-255. [2] Colwell LV. The effects of high-frequency vibrations in grinding,Transac ASME 1956;78:837-45.[3] Anon. Ultrasonic vibrations help grinding. Steel, TheMetalworking Weekly 1963;152:56-58.[4] Kaliszer H, Limb M. Application of ultrasonic technique ingrinding processes. Int J Mach Tools Des Res 1968;8:189–201. [5] Nakagawa T, Suzuki K, Uematsu T, Kimura M, Yoshida KogyoKK. Development of a new turning centre for grinding ceramicmaterials. CIRP Ann 1988;37:319–22.[6] Onikura H, Ohnish O, Take Y. Fabrication of micro carbide toolsby ultrasonic vibration grinding. CIRP Ann 2000;49:257-60. [7] Suzuki K, Tochinai H, Uematsu T, Mishiro S. A new grindingmethod for ceramics using a biaxially vibrated non-rotationalultrasonic tool. CIRP Ann 1993;42:375–8.[8] Hara K, Isobe H, Kyusojin A, Okada M. Study on mirror surfacegrinding of die steel by using ultrasonically assisted diamondtools. Int J Abrasive Technol 2008;1:265–73.[9] Nomura M, Wu Y, Kuriyagawa T. Investigation of internalultrasonically assisted grinding of small holes: effect of ultrasonic vibration in truing and dressing of small CBN grinding wheel. JMech Sci Technol 2007;21:1605-11.[10] Spur G, Holl SE. Ultrasonic assisted grinding of ceramics. J MaterProcess Technol 1996;62:287-93.[11] Uhlmann E. Surface formation in creep feed grinding of advancedceramics with and without ultrasonic assistance. CIRP Ann1998;47:249-52.[12] Yan Y, Zhao B, Liu J. Ultraprecision surface finishing of nano-ZrO2ceramics using two-dimensional ultrasonic assisted grinding.Int J Adv Manuf Technol 2009;43:462-7.[13] Gao GF, Zhao B, Xiang DH, Kong QH. Research on the surfacecharacteristics in ultrasonic grinding nano-zirconia ceramics. JMater Process Technol 2009;209:32-7.[14] Wu Y, Fan Y, Kato M, Kuriyagawa T, Syoji K, Tachibana T.Development of an ultrasonic elliptic-vibration shoe centerlessgrinding technique. J Materi Proc Technol 2004;155-156:1780-7.[15] Wu Y, Fan Y, Kato M. A feasibility study of microscalefabrication by ultrasonic-shoe centerless grinding. Prec Eng2006;30:201-10.[16] Tawakoli T, Azarhoushang B. Influence of ultrasonic vibrationson dry grinding of soft steel. Int J Mach Tools Manuf2008;48:1585-91.[17] Tawakoli T, Azarhoushang B, Rabiey M. Ultrasonic assistedgrinding of soft steel. Ind Diamond Rev 2009;1:40-44.[18] Tawakoli T, Azarhoushang B, Rabiey M. Ultrasonic assisted drygrinding of 42CrMo4. Int J Adv Manuf Technol 2009;42:883-91.[19] Azarhoushang B, Tawakoli T. Development of a novel ultrasonicunit for grinding of ceramic matrix composites. Int J Adv Manuf Technol 2011;57:945-55.[20] Blunt L, Ebdon S. The application of three-dimensional surfacemeasurement techniques to characterizing grinding wheeltopography. Int J Mach Tools Manuf 1996;36:1207-26.[21] Butler DL, Blunt LA, See BK, Webster JA, Stout KJ. Thecharacterisation of grinding wheels using 3D surfacemeasurement techniques. J Mater Process Technol 2002;127:234–7.。
平面振动存在对摩擦减小的影响

平面振动存在对摩擦减小的影响C. C. Tsai ·C. H. Tseng摘要:在不同的实验中已经观察到通过振动来减少摩擦。
通过调节振动,可以应用这种影响来控制摩擦力。
而且,控制摩擦力通常的方法依赖于润滑剂和适当的材料组合。
振动的叠加可以进一步降低摩擦力。
这项研究基于Dahl摩擦模型得到一种理论方法:描述了在任意角度的切向振动的存在下观察到的摩擦减小。
分析结果表明,在建立减小摩擦中振动的影响模型时,切向应当被考虑。
在任何的振动角度,触头的切向降低减小摩擦的效果。
平行于宏观速度的振动可以最有效的减小摩擦。
关键词:摩擦,振动,建模,Dahl1.介绍在不同的实验中已经观察到通过振动来减少摩擦。
振动的方向可以是接触表面的法向或者切向。
这种影响可以用于减小制造过程中的过程力,像是超声波加工和超声振动图,或者是解决在高真空环境中的位置控制问题,如电子显微镜,可以通过振动振幅的变化来控制摩擦。
探讨超声诱导减少摩擦的起源,Hesjedal和Behme实验研究在微观机械接触摩擦减少的现象。
他们得到结论:摩擦力减少的效果结果完全来自于垂直振动分量。
然而,以往的实验研究上的切向振动显示摩擦减少。
基于该刚性库仑摩擦的定量分析模型显示出相同的趋势作为实验数据,但这些模型有较低的价值。
对于这些类型的联系,以小幅度滑动位移的,Tani表明,刚性库仑摩擦模型是不足以形容摩擦性能的。
在微观水平上,显然光滑表面还是“粗糙的”,表面形貌在表面相互作用中起重要作用。
当这些表面彼此压靠,所述真实接触面积通常为用肉眼观察到的表观面积的1/400至1 / 10,000,如图1所示。
突起的特征被称为粗糙。
最古老,最简单的微模型是格林伍德威廉姆森模型,该模型假设表面是由半球形的凹凸倾1斜。
这些凹凸具有均匀球体半径和凸起体高度的对称高斯分布。
赫兹公式中球体和半空间的弹性接触被用来计算负荷,接触面积,和变形凹凸的接触压力。
实验已经观察到,当两个接触面互相滑动,实际体滑动开始之前,一个表面的运动比其他要早。
基于超声振动辅助车削的建模与仿真研究
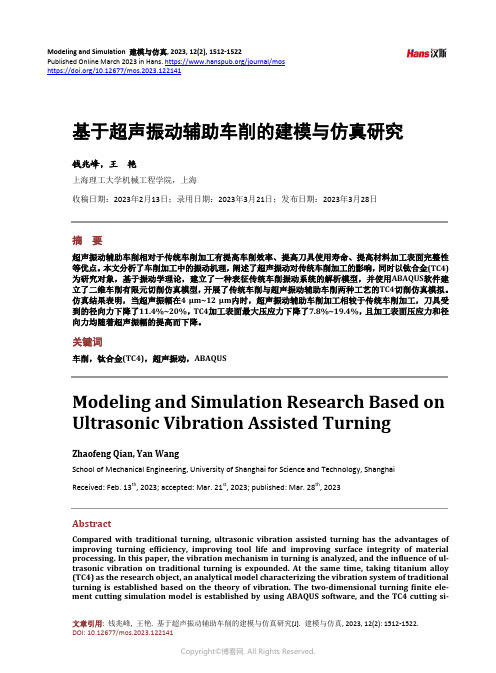
Modeling and Simulation 建模与仿真, 2023, 12(2), 1512-1522 Published Online March 2023 in Hans. https:///journal/mos https:///10.12677/mos.2023.122141基于超声振动辅助车削的建模与仿真研究钱兆峰,王 艳上海理工大学机械工程学院,上海收稿日期:2023年2月13日;录用日期:2023年3月21日;发布日期:2023年3月28日摘要超声振动辅助车削相对于传统车削加工有提高车削效率、提高刀具使用寿命、提高材料加工表面完整性等优点。
本文分析了车削加工中的振动机理,阐述了超声振动对传统车削加工的影响,同时以钛合金(TC4)为研究对象,基于振动学理论,建立了一种表征传统车削振动系统的解析模型,并使用ABAQUS 软件建立了二维车削有限元切削仿真模型,开展了传统车削与超声振动辅助车削两种工艺的TC4切削仿真模拟。
仿真结果表明,当超声振幅在4 μm~12 μm 内时,超声振动辅助车削加工相较于传统车削加工,刀具受到的径向力下降了11.4%~20%,TC4加工表面最大压应力下降了7.8%~19.4%,且加工表面压应力和径向力均随着超声振幅的提高而下降。
关键词车削,钛合金(TC4),超声振动,ABAQUSModeling and Simulation Research Based on Ultrasonic Vibration Assisted TurningZhaofeng Qian, Yan WangSchool of Mechanical Engineering, University of Shanghai for Science and Technology, ShanghaiReceived: Feb. 13th , 2023; accepted: Mar. 21st , 2023; published: Mar. 28th , 2023AbstractCompared with traditional turning, ultrasonic vibration assisted turning has the advantages of improving turning efficiency, improving tool life and improving surface integrity of material processing. In this paper, the vibration mechanism in turning is analyzed, and the influence of ul-trasonic vibration on traditional turning is expounded. At the same time, taking titanium alloy (TC4) as the research object, an analytical model characterizing the vibration system of traditional turning is established based on the theory of vibration. The two-dimensional turning finite ele-ment cutting simulation model is established by using ABAQUS software, and the TC4 cutting si-钱兆峰,王艳mulation of traditional turning and ultrasonic vibration assisted turning is carried out. The simu-lation results show that when the ultrasonic amplitude is within 4 μm~12 μm, compared with the traditional turning, the radial force of the tool is reduced by 11.4%~20%, and the maximum com-pressive stress of the TC4 machined surface is reduced by 7.8%~19.4%. The surface compressive stress and radial force decrease with the increase of ultrasonic amplitude.KeywordsTurning, Titanium Alloy (TC4), Ultrasonic Vibration, ABAQUSThis work is licensed under the Creative Commons Attribution International License (CC BY 4.0)./licenses/by/4.0/1. 引言钛合金(TC4)是一种难加工材料,具有材质较轻、强度硬度高、耐热性强、抗腐蚀性好等优点[1]。
- 1、下载文档前请自行甄别文档内容的完整性,平台不提供额外的编辑、内容补充、找答案等附加服务。
- 2、"仅部分预览"的文档,不可在线预览部分如存在完整性等问题,可反馈申请退款(可完整预览的文档不适用该条件!)。
- 3、如文档侵犯您的权益,请联系客服反馈,我们会尽快为您处理(人工客服工作时间:9:00-18:30)。
Influence of ultrasonic vibration on micro-extrusionCristina Bunget,Gracious Ngaile ⇑Mechanical and Aerospace Engineering Department,North Carolina State University,Raleigh,NC 27695,USAa r t i c l e i n f o Article history:Received 5November 2007Received in revised form 1January 2011Accepted 2January 2011Available online 5January 2011Keywords:Ultrasonic forming Micro-forming Micro-extrusion Tribologya b s t r a c tMicro-forming is a miniaturization technology with great potential for high productivity.Some technical challenges,however,need to be addressed before micro-forming becomes a commercially viable manu-facturing process.These challenges include severe tribological conditions,difficulty in achieving desired tolerances,and short tool-life due to inability of available die materials to withstand the forces exerted on miniature dies and punches.Some of these problems can be mitigated using ultrasonic technology.The principal objectives of this work were to investigate the possibility of applying ultrasonic vibra-tions in the micro-forming process,to design a set of tooling for ultrasonic micro-extrusion and to observe experimentally how ultrasonic oscillations influences the forming load and the surface finish.The test results showed a significant drop on the forming load when ultrasonic vibrations were imposed,and also a significant improvement in the surface of the micro-formed parts.Based on the preliminary test results,the study demonstrated high potential for using ultrasonic oscillations as a way to overcome the difficulties brought by the miniaturization.Ó2011Elsevier B.V.All rights reserved.1.IntroductionThe production of micro-parts has become more important in fields such as electronics,computers,communication,biotechnol-ogy,medicine,optics and environmental monitoring.Typical example for such parts are pins for IC-carriers,fasteners,micro-screws,lead frames,sockets,and any kind of connecting element (Fig.1).Traditionally these precision mechanical parts are fabri-cated by machining.The net shape or near net shape processes,such as metal forming processes,are best suited for miniaturiza-tion because of the higher productivity and accuracy.Despite the advantages of micro-forming,full utilization of this process has not been realized.Besides the problems that appear in conventional forming processes,like tool design and wear,there are also specific problems related with the miniaturization itself,such as material behavior,higher friction and fabrication of tools.When the process is scaled down,the microstructure and the sur-face topography remain unchanged resulting in different material flow as compared to conventional process.A series of tests in sheet micro-forming has shown that flow stress of material decreases with miniaturization and also tribological conditions are more se-vere at the micro-scale level.The influence of size on flow stress has thoroughly been investigated and well understood [2,3].The tribological effects are,however,not well understood.The dou-ble-cup extrusion test was used to study lubrication conditions for different specimen sizes ranging from 4mm down to 0.5mm diameter.The results showed an increase in apparent friction fac-tor by a factor of 20when the specimen size decreased to 0.5mm diameter [4].The authors formulated a mechanical–rheological model which assumes that the friction stress is affected by minia-turization.This approach was based on the generalized friction law given in Eq.(1).s f ¼f Áa RC Ák ;ð1Þwhere s f is the friction factor,k is the shear yield strength of the material,f is the friction factor,and a RC is the real contact area ratio.They showed that both f and a RC are not constant,but they are size dependent and become larger as the process is scaled down.Another approach of investigating the effect of miniaturization on friction was proposed by Bunget [5].Finite element analysis was used to simulate backward-cup extrusion tests for the same specimen size and different dimensions of the punch,going from 6mm (macro-forming)down to 0.5mm in the cup wall thickness (micro-forming).The ratio of the frictional energy to the total energy at different percent of the stroke was calculated.A compar-ative analysis between deformation in macro-forming and micro-forming can be drawn by considering the deformation energy associated with metal forming as expressed by the functional [6]:Y¼I 1þI 2ÀI 3¼ZVr d _ edV þk ZV_eV d _e V dV ÀZSFF i d u i ds ð2Þwhere k is a penalty constant,_eV is the volumetric strain rate, r is effective stress, e is effective strain,_ eis effective strain rate,and F i represents traction.The 1st term represents the energy due to deformation,the 2nd term volumetric strain energy,and the 3rd0041-624X/$-see front matter Ó2011Elsevier B.V.All rights reserved.doi:10.1016/j.ultras.2011.01.001Corresponding author.Tel.:+19195155222.E-mail address:gracious_ngaile@ (G.Ngaile).term energy due to friction at the tool/workpiece interface.In the presence of good lubrication (i.e.,shear friction factor m =0.1–0.15),which could result to non-defective parts,the ratio between frictional energy and deformation energy (R macro =I 3/I 1)associated with classic macro-forming is usually of the order of 0.1or less.With micro-forming,however,the ratio of friction energy to defor-mation energy increases significantly (Fig.2).This dramatic in-crease implies that much better lubrication is imperative in micro-forming because the interface friction can become dominant in the process.Furthermore,the typical lubricants used in cold macro-forming,such as zinc phosphate +metal soap,become inef-fective for micro-forming because the lubricant film thickness (e.g.,20l m)may exceed the tolerance level of the micro-parts.The investigations have also shown an increase in scattering with miniaturization [3],and therefore difficulty in achieving de-sired tolerances.Other problems that appear in micro-forming are the fabrication of the tools,which need to be very small with very close tolerances and a good surface quality.The fact that mi-cro-forming tools are also subjected to forces that may exceed the capacity of available die materials presents a great challenge as these tools are prone to short tool life.New manufacturing meth-ods have been developed,such as micro-electrical discharging machining:micro-wire EDM,micro die sinking,electrical dis-charge drilling,micro-electrical discharge milling and grinding,but the problem of the high forces exerted on the tools still needs to be resolved [7].There is a great potential to overcome some of the drawbacks of the miniaturization by applying the ultrasonic vibration during mi-cro-forming process.The application of ultrasonic vibration in me-tal forming at macro-scale has been discussed for many years and some benefits were observed,such as a reduction in the flow stress and a considerable reduction of the external friction between tool and workpiece.The flow stress was observed experimentally to be considerably lowered by the ultrasonic oscillations superimposed on the compressive forming process [8].This phenomenon was attributed to dynamical effects of stress,velocity and acceleration due to vibration,and also thermal effects due to heat generation.Earlier studies of the effects of the longitudinal oscillations im-posed on the wire drawing revealed two possible effects of the ultrasonic oscillations superimposed on the forming process:vol-ume effects and surface effects [8–10].The volume effects are re-lated with a decrease in the flow stress.The surface effects are related with the changing of the frictional conditions at the die/specimen interface.The application of longitudinal,radial and tor-sional oscillations in rolling processes resulted in changes in the apparent friction coefficient,as a result of the pumping of the lu-bricant phenomenon,softening or melting the asperities,separa-tion of the surfaces,allowing a re-distribution of the lubricant [11].Investigations on superimposing ultrasonic oscillations on the tube drawing showed a significant reduction in the flow stress [12].Other investigations were carried out to study the effect of the shape and length of the concentrator,or the tool attachment,an important part in the ultrasonic system.The concentrator shapes that were found to be more effective were conical,stepped and exponential [13].Most studies on the applications of ultra-sonic vibrations on metal forming seem to reach the same conclu-sions regarding the benefit of ultrasonic oscillations:reduction of the forming forces,reduction of the flow stress,reduction of the friction between die and workpiece and production of better sur-face qualities and higher precision.Despite these benefits wide application of this technology is still limited.This is due to high cost of designing a ultrasonic system and the cost associated with energy that is required to induce the vibrations [14].The objectives of this study are to investigate the possibility of applying the ultrasonic vibrations in the micro-forming process and to investigate their influence on material flow,forming load and tribological characteristics.It is anticipated that ultrasonic technology can overcome some of the difficulties brought by miniaturization.2.Ultrasonic micro-extrusion process mechanismThe following sections examine the physics of the extrusion process when longitudinal ultrasonic oscillations are superim-posed on the dies.Three different extrusion processes will be dis-cussed:forward-rod extrusion,double-cup extrusion,and forward-rod-backward-cup extrusion.A schematic diagram of the ultrasonic forward-rod extrusion pro-cess is shown in Fig.3.The punch pushes down the billet,forcing it to go through the die cavity,in order to form a rod with a reduced diameter.The workpiece goes through three zones:the guiding zone (Zone I ),the deformation zone (Zone II ),and the exit zone (Zone III ).All three zones are characterized by sliding friction,but the deformation zone also experiences plastic deformation.In the ultrasonic extrusion process,the ultrasonic oscillation can be im-posed on the die or on the punch.It is usually more practical to oscillate the dies,since the purpose is to have a large relative mo-tion between the die and workpiece.In this case,the ultrasonic oscillations are imposed on the die,and it is assumed that the vibratory motion is not transmitted to the punch.The material will enter with velocity v 0,given by the punch,but will exit with adif-Fig.1.Extruded micro-parts [1].15%20%25%30%35%40%n e r g y / T o t a l E n e r g y[%]Wall thickness 0.5Wall thickness 2.551(2011)606–616607ferent velocity,v e .The die will vibrate with an oscillatory velocity v D ,and an amplitude a (Fig.3).This velocity is larger than the velocity of the material to be deformed.Because of the relative velocity between the die and material,micro gaps between die and material are created and closed at every cycle of oscillation.This changes the contact pressure characteristics at the interface.It can be observed that under ultrasonic oscillations the direction of the friction force reverses for every period of oscillation,thus changing the friction characteristic at the tool-workpiece interface.Therefore,with proper design of an ultrasonic micro-forming sys-tem,tribological performance can be enhanced.The schematic of ultrasonic double cup backward extrusion pro-cess is shown in Fig.4.The billet is placed in the die,between the two punches.The lower punch is stationary and the upper punch is moving down,forcing the workpiece material to flow and to form the two cups.There are three distinctive zones:zones I and III where the lower and upper cups are formed respectively,characterized by sliding friction and Zone II where plastic deforma-tion occurs.The application of ultrasonic oscillations can be accomplished in a similar manner as forward-rod extrusion dis-cussed above.In the classical double-cup extrusion process,the material flows easier in the upper cup in the presence of friction.But the periodic change in direction of the friction force causedIn examining various extrusion processes,emphasis was on identifying changes pertaining to the relative velocities between the die and the workpiece that are associated with the introduction of ultrasonic oscillations.Altering relative motion in time and space from motions that could be observed in classical metal form-ing without ultrasonic necessarily affects friction characteristics,interface pressure characteristics,and other process variables.These changes/transformations can be exploited to enhance the process by carefully designing an ultrasonic forming system.Other key aspects pertaining to the application of ultrasonic technologies include;(a)the ultrasonic oscillations are brought in the deforma-tion zone through a concentrator connected to a transducer as shall be discussed in the next section,(b)the ultrasonic oscillations could be imposed on the die or the punch,and in rare cases on the workpiece because the workpiece undergoes changes in dimensions and shape during the deformation process.In general,it is preferred to impose the oscillations on the dies,(c)Because of high relative velocity between the die and deforming billet a signif-icant heat can be generated at the interface.The increase in the temperature at the die-specimen interface will influence the behavior of the lubricant,and (d)for classical metal forming,the application of ultrasonic oscillations is practical only when the sav-ings in the energy required for providing the forming load is larger Fig.3.Ultrasonic forward-rod extrusion process schematic.Fig.4.Ultrasonic double cup backward extrusion process schematic.a unified design which offers the possibility of changing the form-ing tools to accommodate all variants of micro-extrusion processes shown in Figs.3–5,(b)be able to micro-extrude billets made from aluminum,brass and copper materials with billet dimension rang-ing from 0.5to 2mm diameter and 1to 5mm length,(c)conceive a design that will attain maximum relative velocity at the die-work-piece interface and that the transmission of the oscillations to the rest of the structure should be minimal,(d)the setup should be de-signed for 2kW ultrasonic generator at frequencies between 20kHz and 21kHz,(e)the setup should be designed for an ultra-sonic transducer which operates at a natural frequency of 20kHz and oscillation amplitude of 10l m,and (f)the set-up should pro-duce useful mode shapes,i.e.longitudinal and radial-torsional at a natural frequency of 20kHz.In order to fulfill the above design requirements a preliminary design shown in Fig.6was conceived.The main parts of the ultra-sonic micro-extrusion system are,the ultrasonic generator which is connected to the ultrasonic transducer,the concentrator which takes the oscillations from the transducer and transmits them to the lower forming unit,the upper and lower forming units,and the hydraulic actuation cylinder which provides the forming load tothe upper part of the forming unit.The actuation cylinder is con-nected to the pump and the control system.Fig.7a shows a concentrator assembly which is comprised of several parts;die,punch,outside cone,inside cone,lock nut and the concentrator body.A simplified model of the concentrator is shown in Fig.7b.The simplified model shows that a longitudinal wave transmitted by the piezoelectric transducer at the base of the concentrator attains maximum amplitude at the deformation zone.The figure also shows that a radial wave transmitted into the disc attains zero amplitude at the clamping zone.As shown in Fig.7b,the geometric parameters to be established for the con-centrator are L i ,L m ,L o ,/d ,/i ,/m ,/o ,and t .Some of the concentrator dimensions are imposed by the practical aspects of the design such as dimensions of the dies and punches,provision for clamping the concentrators,etc.Table 1shows material properties and other parameters that were used for the design.It can be seen from Table 1that a wave length of 260mm will be exhibited at the desired fre-quency of 20,000Hz.To attain zero displacement amplitude at the clamping zone (Fig.7b)the diameter of the disc should be equal to the wave length.All other geometric parameters were iterated with the aid of the finite element method as discussed in the next section.3.1.Modal analysisIn the course of optimizing the ultrasonic micro-extrusion sys-tem,finite element analysis was carried out.In order to ensure that the natural frequency is close to the excitation frequency given by the transducer,several finite element iterations were carried out to determine the remaining dimensions of the system.Fig.8shows the boundary conditions used in the modal analysis.At location A,all nodes on the bottom surface of the base plate were con-strained in all degree of freedom.The model was also constrained at location B.This is the location where the ultrasonic transducer will be connected.In order to mimic the type of the boundary con-ditions resulted from the application of the ultrasonic oscillations all nodes on the connection surface were constrained in the axial direction.Several useful mode shapes were found in the range between 19,000Hz and 21,000Hz:Fig.9a shows a radial mode shape at 20,176Hz,and Fig.9b shows a longitudinal mode shape at 20,354Hz.Both mode shapes may result in enhancement of the tribological conditions at the die-workpiece interface.Some of the benefits of longitudinal mode shape are due to the fact that this mode shape will result in friction force reversal and formation of gaps,particularly,for forward extrusion and forward-rod-back-ward-cup extrusion processes.The benefit emanating from radial mode shape includes enhancing uniform distribution of lubricant at theinterface.Fig.5.Ultrasonic forward rod backward extrusion process schematic.Actuation Ultrasonic Ultrasonic Hydraulic pump forming unit forming unit transducerand ControlConcentratorto the superimposed oscillations,and to check if the stresses inthe structure are within permissible limits.Similarly to the previ-ous analyses,the bottom surface of the base plate was constrained Ultrasonic oscillations Dieimposed by piezoelectric Lower punch Outside cone Inside cone Lock nutConcentrator body DiscL oL iL m Ød =λftØo ØmØiTable 1Material and ultrasonic oscillation parameters used in concentrator design.Material Steel typeFig.8.Boundary conditions applied in the modal analysis [ANSYS Workbench].610 C.Bunget,G.Ngaile /Ultrasonics 51(2011)606–616100Hz step size.The frequency responses of the structure taken atpoint Rs(top surface of die holder)for three input displacements are plotted in Fig.10.The maximum displacement is reached at the resonance frequency of20,400Hz,and all the mode shapes cor-responding to the three input displacement were longitudinal. Fig.10shows that for input displacement of1l m,5l m and 10l m,the die exhibited longitudinal displacement amplitudes of 47l m,237l m and474l m respectively.3.3.Conceived tooling setupFig.11shows the developed ultrasonic micro-extrusion set-up. Before carrying out the experiment the actual displacement of the die due to ultrasonic vibration had to be established.Strain gauges were mounted on the top part of the die holder(outer cone,see Fig.7a)and on the top head of the piezoelectric transducer.The strain gauges provided local elongation and contraction of the die holder as the wave propagated.These values were later correlated with harmonic response analysis.Fig.12shows displacement amplitude at the location where the strain gauges were mounted for the outer cone and the transducer head.The gauge on the trans-ducer shows a displacement of1.3l m and the strain gauge on the die holder shows an average displacement of10l m.Harmonic analysis was then carried out for transducer input displacement of1.3l m.The frequency response curve for the top surface of the die holder and the displacement map are shown in Fig.13.A maximum displacement of61.6l m is observed.From the values given on the displacement map scale,local elongation of the die holder can be determined.For example,by subtracting the top two displacement values on the scale(61.626–54.094=7.5l m) we can obtain local elongation of the die holder.This implies that, the top5mm length of the die holder exhibited a maximum elon-gation of about7.5l m.The strain gauges mounted at this location gave an average of10l m.Since these two values are close,we could assume that the displacement values obtained from har-monic analysis are reasonable.I.e.,the die can therefore be as-sumed to oscillate at maximum amplitude of61.6l m.During the experiment the tooling exhibited a resonance frequency of 20,490Hz.As shown from Fig.13the resonance frequency fromharmonic analysis was 20,400Hz.Only a slight difference of 90Hz is observed between experiment and simulation.3.4.Experimental set-up and test proceduresThe developed test set-up discussed above was used to study the influence of lubricant on the ultrasonic vibrations for forward extrusion (FE),double-cup extrusion (DCE)and forward backward extrusion (FBCE)processes.As shown in Fig.11,the main compo-nents of the test set-up are;punch and die assemblies,lever for actuating the forming load,2kW ultrasonic generator and 20kHzHarmonic response analysis for a 1.3l m transducer displacement input (frequency response is taken at the top surface of the die holder).Fig.14.Dies and punches for (a)FE and (b)DCE.Table 2Test matrix and lubricant types.LubricantNumber of experiments FEDCE FBCE Lub 1[Polymeric lubricant]6138Lub 2[Dailube DR-38]344Lub 3[Lubsol W-72SK]111116Polymeric lubricant (C –84%,O –15%,Na –0.2%,Si –0.05%,P –0.3%,S –0.45%).Dailube DR-38.Lubsol W-72SK (C –84.74%,O –12.75%,Na –1.25%,Si –0.08%,P –0.22%,S –0.98%).612 C.Bunget,G.Ngaile /Ultrasonics 51(2011)606–616tools are a combination of those used in the other two tests.Thematerials used for the experiments were aluminum(AA1100) and brass.The samples were cut from a long wire of2mm diame-ter in small pieces of5mm length for forward-rod extrusion,4mm for forward-rod-backward-cup extrusion tests,and3mm length for double-cup extrusion test.Table2presents the test matrix, specifying the number of experiments carried out for each case and the three lubricants used in the experiments.Before the test,the diameter and length of each billet were measured.After that,the billet is dipped in the lubricant.In order tofind thefilm thickness,the billet is weighed before and after lubricant application.Table3presents the lubricantfilm thickness for some of the billets.Just before the forming load is applied, ultrasonic vibration is activated from the generator.As discussed in Section3.3the ultrasonic amplitude applied to the die for all the tests was61l m.The time for application of the ultrasonic oscillations is10s.Fig.15presents the micro-parts obtained from the experiments.After the experiments,micrographs were taken using scanning electron microscopy(HITACHI S3200NSEM)which was used to study the influence of the ultrasonic oscillations on the surface quality.Table3Film thickness for different lubricants and specimens.Lubricant Billet size(mm)Weight lubricant(g)Surface billet(mm2)Film thickness(g/mm2) Lub1£1.91Â5.110.00636.370.1650Â10À3Without Ultrasonic With UltrasonicWithout UltrasonicWith UltrasonicWithout Ultr asonicWith Ultr asonicC.Bunget,G.Ngaile/Ultrasonics51(2011)606–616613614 C.Bunget,G.Ngaile/Ultrasonics51(2011)606–616cants in all tests was enhanced by ultrasonic vibrations.The lubri-cant found more effective was lubricant1for DCE test,and lubri-cant3for FE and FBCE tests.4.2.Influence of ultrasonic oscillations on surfacefinishUsing scanning electron microscope,a comparison between the surfacefinish of the specimens obtained after the tests with and without ultrasonic oscillations was carried out.This aspect of the surface is a key factor in understanding the lubrication mechanism. Micrographs were taken for all types of tests and all lubricants.The surface quality was observed to be improved in all ultrasonic tests.Fig.20brings together the micrographs for forward-rod extru-sion tests and forward–backward-cup extrusion with and without ultrasonic oscillation[6].Sample locations where micrographs were taken are also shown.Fig.20shows a significant improve-ment in the surface quality when ultrasonic vibration was used.The differences between the surfacefinish obtained after classic double-cup micro-extrusion test and the ultrasonic test are pre-sented in Fig.21[6].Micrographs were taken in different zones. The surfaces obtained in non-ultrasonic conditions presents scars which indicate sticking conditions and localized smearing with subsequent shearing of the junctions.The surfaces obtained when ultrasonic oscillations were used show a significant improvement in the lubrication regimes.There are some isolated scars in zone 1.Zone3does not show much scars,rather this zone exhibit roughening and formation of tiny lubricant pockets,indicating a much more favorable lubrication condition.The differences in the surface quality are attributed to various factors,some of which can be understood by studying the possible lubrication mechanisms in non-ultrasonic and ultrasonic test. Ultrasonic oscillation results in high instantaneous relative veloci-ties at the tool/workpiece interface.This leads to reduction of adhesive bond formation and hence better lubrication conditions.At the same time,because of the change in the direction of the rel-ative movement,there is a change in the direction of the friction force that helps the material toflow easier than in the classic test.Also because of the relative velocity,the pockets formed by the surface roughness trap the lubricant and keep it in the deformation zone.The lubricant is better distributed at the interface and keeps up with the expansion of the surface and the generation of the new surface during the deformation process.Due to these changes,the lubrication conditions are improved leading to reduction in the friction coefficient at the tool-workpiece interface.5.ConclusionsIn this paper the influence of ultrasonic vibration on micro-extrusion processes is investigated.An ultrasonic micro-forming tooling was developed and micro-extrusion experiments were con-ducted.The forming load and the surfacefinish after deformation were some of the aspects studied.Based on results of the tests, the following conclusions were reached:Ultrasonic oscillations influence significantly the friction and lubrication mechanism at the die/workpiece interface.Higher instantaneous sliding velocities help to shift a boundary lubri-cation regime to a mixed-film regime and sticking conditions to a boundary regime.Better lubrication conditions and better surfacefinish with ultrasonic oscillations suggest that ultrasonic micro-forming isa viable process for difficult-to-lubricate materials.The magnitude of the ultrasonic oscillations effects depends on the type of the extrusion process,but is also influenced by the lubricant composition.The reduction in friction will result in a reduction in load,thus in less energyconsumption.In conclusion,the study has demonstrated that there is high po-tential for using ultrasonic vibration as a way to overcome some the difficulties brought by the miniaturization. AcknowledgmentsThe authors would like to acknowledge the National Science Foundation,Project#CMMI0900148,through which this work was partially funded.Any opinions,findings,and conclusions or recommendations expressed in this material are those of the authors and do not necessarily reflect the views of the National Sci-ence Foundation.Sincere gratitude should also go to Mr.Florian Scherer,who participated in the early stage of tooling design. References[1]F.Vollertsen,Z.Hu,H.Schulze Niehoff,C.Theiler,State of the art in microforming and investigations into micro deep drawing,Journal of Materials Processing Technology151(2004)70–79.[2]M.Geiger,F.Vollertsen,R.Kals,Fundamentals on the manufacturing of sheetmetal microparts,Annals of the CIRP45/1(1996)277–282.[3]A.Messner,U.Engel,R.Kals,F.Vollertsen,Size effect in the FE-simulation ofmicro-forming processes,Journal of Materials Processing Technology45 (1994)371–376.[4]U.Engel,Tribology in microforming,Wear260(2006)265–273.[5]C.Bunget.Microforming and Ultrasonic Forming.MS Thesis,North CarolinaState University,2006.[6]G.Ngaile, C.Bunget,Influence of ultrasonic vibration on microforming,Transaction of NAMRI/SME36(2008)137–144.[7]E.Uhlmann,S.Piltz,U.Doll,Machining of micro/miniature dies and moulds byelectrical discharge machining–recent development,Journal of Materials Processing Technology167(2005)488–493.[8]O.Izumi,K.Oyama,Y.Suzuki,Effects of superimposed ultrasonic vibration oncompressive deformation of metals,Transactions of the Japan Institute of Metals7(1966)162–167.[9]C.E.Winsper,D.H.Sansome,Fundamentals of‘ultrasonic’wire drawing,Journalof the Institute of Metals97(1969)274–280.[10]C.E.Winsper,G.R.Dawson,D.H.Sansome,An introduction to the mechanics ofoscillatory metalworking,Metals and Materials4(1970)158–162.[11]V.P.Severdenko,V.V.Klubovich, A.V.Stepanenko.Ultrasonic Rolling andDrawing of Metals.New York,1972.[12]C.E.Winsper,D.H.Sansome,Application of ultrasonic vibrations to the plugdrawing of tube,Metal Forming3(1971)71–75.[13]M.J.R.Young,C.E.Winsper,D.H.Sansome,The effect of tool attachment on theresonant characteristics of ultrasonic waveguides,Applied Acoustics3(1970) 217–224.[14]W.Presz,B.Andersen,Flexible tooling for vibration-assisted microforming,Journal of Achievements in Materials and Manufacturing Engineering Year21(2)(2007)61–64.616 C.Bunget,G.Ngaile/Ultrasonics51(2011)606–616。