产品检验规程
产品检验规程
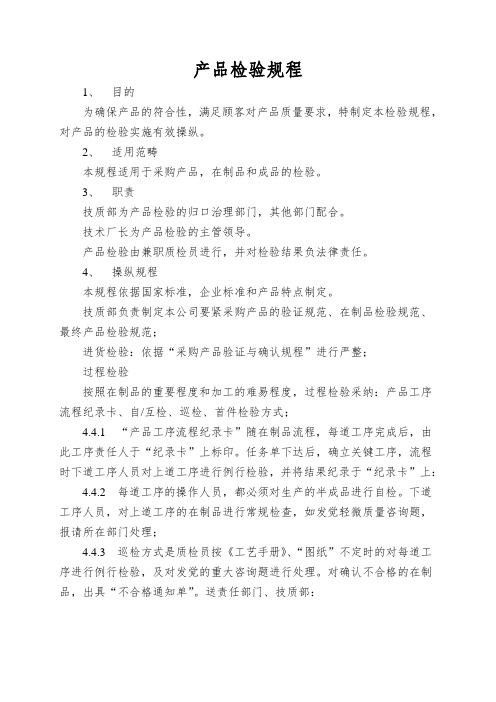
产品检验规程1、目的为确保产品的符合性,满足顾客对产品质量要求,特制定本检验规程,对产品的检验实施有效操纵。
2、适用范畴本规程适用于采购产品,在制品和成品的检验。
3、职责技质部为产品检验的归口治理部门,其他部门配合。
技术厂长为产品检验的主管领导。
产品检验由兼职质检员进行,并对检验结果负法律责任。
4、操纵规程本规程依据国家标准,企业标准和产品特点制定。
技质部负责制定本公司要紧采购产品的验证规范、在制品检验规范、最终产品检验规范;进货检验:依据“采购产品验证与确认规程”进行严整;过程检验按照在制品的重要程度和加工的难易程度,过程检验采纳:产品工序流程纪录卡、自/互检、巡检、首件检验方式;4.4.1“产品工序流程纪录卡”随在制品流程,每道工序完成后,由此工序责任人于“纪录卡”上标印。
任务单下达后,确立关键工序,流程时下道工序人员对上道工序进行例行检验,并将结果纪录于“纪录卡”上:4.4.2每道工序的操作人员,都必须对生产的半成品进行自检。
下道工序人员,对上道工序的在制品进行常规检查,如发觉轻微质量咨询题,报请所在部门处理;4.4.3巡检方式是质检员按《工艺手册》、“图纸”不定时的对每道工序进行例行检验,及对发觉的重大咨询题进行处理。
对确认不合格的在制品,出具“不合格通知单”。
送责任部门、技质部:4.4.4产品数量大于50樘:或结构过于复杂(技质部视情形而定),投入批量生产前,应进行首件检验,检验人员按《工艺手册》、《钢质防火门检验标准》规程进行,检验后填写《产品首件检验纪录单》;4.4.5对例行检验不合格的在制品,按《不合格品操纵程序》处理;4.4.6本公司对在制品不实行例外放行。
4.5最终产品检验只有在所有的检验(进货、过程检验)均已完成且结果符合要求条件下,车间才能提交质量部进行最终产品的检验。
技质部按照我公司制定的《钢质防火门检验标准》进行最终产品检验,做好《钢质防火门最终检验报告单》。
对检验不合格的最终产品,出具“不合格通知单”,按《不合格品操纵程序》处理;只有在文件规定的各项检验活动差不多圆满完成,且有关数据和文件齐备并得到认可后,加盖“合格证”标牌,产品才能出厂;如我公司负责产品安装,依据我公司制定的《防火门安装使用讲明书》进行,并按照我公司制定的《钢质防火门检验标准》进行产品安装检验。
产品检验规程
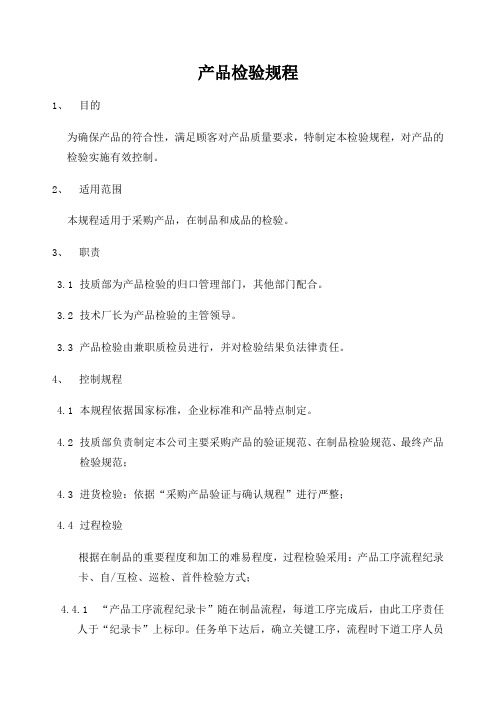
产品检验规程1、目的为确保产品的符合性,满足顾客对产品质量要求,特制定本检验规程,对产品的检验实施有效控制。
2、适用范围本规程适用于采购产品,在制品和成品的检验。
3、职责3.1技质部为产品检验的归口管理部门,其他部门配合。
3.2技术厂长为产品检验的主管领导。
3.3产品检验由兼职质检员进行,并对检验结果负法律责任。
4、控制规程4.1本规程依据国家标准,企业标准和产品特点制定。
4.2技质部负责制定本公司主要采购产品的验证规范、在制品检验规范、最终产品检验规范;4.3进货检验:依据“采购产品验证与确认规程”进行严整;4.4过程检验根据在制品的重要程度和加工的难易程度,过程检验采用:产品工序流程纪录卡、自/互检、巡检、首件检验方式;4.4.1 “产品工序流程纪录卡”随在制品流程,每道工序完成后,由此工序责任人于“纪录卡”上标印。
任务单下达后,确立关键工序,流程时下道工序人员对上道工序进行例行检验,并将结果纪录于“纪录卡”上:4.4.2 每道工序的操作人员,都必须对生产的半成品进行自检。
下道工序人员,对上道工序的在制品进行常规检查,如发现轻微质量问题,报请所在部门处理;4.4.3 巡检方式是质检员按《工艺手册》、“图纸”不定时的对每道工序进行例行检验,及对发现的重大问题进行处理。
对确认不合格的在制品,出具“不合格通知单”。
送责任部门、技质部:4.4.4 产品数量大于50樘:或结构过于复杂(技质部视情形而定),投入批量生产前,应进行首件检验,检验人员按《工艺手册》、《钢质防火门检验标准》规程进行,检验后填写《产品首件检验纪录单》;4.4.5 对例行检验不合格的在制品,按《不合格品控制程序》处理;4.4.6 本公司对在制品不实行例外放行。
4.5 最终产品检验只有在所有的检验(进货、过程检验)均已完成且结果符合要求条件下,车间才能提交质量部进行最终产品的检验。
4.5.1技质部按照我公司制定的《钢质防火门检验标准》进行最终产品检验,做好《钢质防火门最终检验报告单》。
产品质量审核检验规程

产品质量审核检验规程
^0 :
检验顺序检验工作描述
100抽取样品
随机进行抽样,从最近生产日期检验合格带发运批次中抽取
200包装
一内外包装与产品包装的技术规范相附
一防止产品损伤
-附件齐全
一无错装、漏装
300标识
-按技术规氾进行标识
-按顾客要求进行标识
-标牌、铭牌、标签清晰
一出厂编号、批号
400外观
-外观、表面状态与图纸、规范要求相符合
-外观无污物、污染、无磕碰伤
尺寸
500
-顾客要求的尺寸
一与顾客产品交联的尺寸
一出厂检验规定的尺寸
性能
600
-出厂检验规定的性能项目检验
-要求的化学成分、物理性能检查
-顾客要求的检查项目
700其它
800确定产品审核结果,编写审核报告,要求采取的措施
一计算缺陷点数
一计算质量特性值(QKZ
当产品审核时出现关键、严重缺陷或QK^ 90时,要立即分析原因采取纠正措施。
说明。
生产过程质检规程

生产过程质检规程一、前言生产过程质检是指在产品从原材料投料到成品出厂的整个生产流程中,对每个环节进行严格的质量检查和控制。
其目的是确保产品质量稳定、符合标准和客户要求,提高产品竞争力和顾客满意度。
本质检规程旨在规范和指导生产过程质检工作,确保各环节在质量上达到要求。
二、生产过程质检流程1.原材料进货检验原材料是产品的基础,对原材料的质量进行严格的检验是确保产品质量稳定的第一步。
进货检验主要包括检查原材料的外观、尺寸、性能等方面。
原材料必须符合国家和行业标准,并提供合格的检验证书方能接收入库。
2.原材料投料检验在生产过程中,对原材料进行投料检验,以确保每个批次原材料的质量稳定。
投料检验主要包括检查原材料的外观、尺寸、性能等方面,确保原材料符合产品要求。
3.生产过程监控生产过程监控是对生产过程中各个环节的质量进行监控与控制。
监控内容包括生产设备的性能、操作工艺参数的稳定性、操作人员的操作规范等。
通过监控,及时发现生产过程中的异常情况,采取措施进行调整和修正,以保证产品质量的稳定。
4.在线抽检在线抽检是对生产过程中正在生产的产品进行抽样检验。
抽样方式采用随机抽样,抽样样品符合标准要求。
通过在线抽检,确保产品在生产过程中各个环节质量的控制。
5.半成品质检半成品质检是对已经生产完成的半成品进行全面的质量检验。
主要包括外观、尺寸、性能、可靠性等方面的检查和测试。
检查结果必须符合产品质量标准,否则需要退货或者返工处理。
6.终检终检是产品出厂前的最后一道质量关,主要对产品的外观、性能、可靠性等方面进行全面的检查和测试。
检查结果必须符合产品质量标准和客户要求,否则不允许出厂。
三、质检记录与报告在生产过程中,必须做好质检记录和报告,确保质检过程的可追溯性和透明度。
质检记录包括原材料进货检验记录、原材料投料检验记录、生产过程监控记录、在线抽检记录、半成品质检记录、终检记录等。
质检报告包括原材料质量报告、生产过程质量报告、产品质量报告等。
产品抽样及检验规程

产品抽样及检验规程凡公司购进的原材料或外购(协)件,必须通过公司专职质检员的验收。
检验办法如下:1、抽样办法(1)产品数量在10件以下时,可采用全检。
(2)产品数量在100件以下时,可采用10%的比例抽检。
(3)产品数量在1000件以下时,可采用5%的比例抽检。
(4)具体抽检数量可由质检员根据实际或抽样检验,情况灵活掌握。
(5)对于抽样检验不合格时,可以加倍抽检。
(6)专职检验员的产品工序检验的抽样,可以采用本办法。
2、检验规程(1)检验原材料或外购(协)件,必须有检验标准或检验依据,否则不能检验。
(2)检验必须严格按标准要求检验,对原材料的检验,可按国标或企业标准检验尺寸,以核对供方提供的材质书的办法检验材质,必要时可取样送检。
(3)对外购(协)件的检验,可按公司提供的加工图纸,选用适当的计量器具进行检验。
(4)抽检后,在《进货检验记录报告单》上签字,注明检验结果。
(5)工序检验规程,可按外购(协)件的检验规程检验,检验后,在《产品(半成品)质量检验记录》上签字,标明检验结果和处置办法。
3、对于工艺过程中规定的关键工序,必须认真检验。
对于整机产品组装工序为关键工序,必须认真检验。
4、本规程自下发之日起施行。
年月日洛氏硬度计安全操作规程1、洛氏硬度计必须有专业人员操作,操作人员初次操作前必须仔细阅读使用说明书,按说明书的要求安装调试好设备。
2、操作人员应定期检查缓冲器油缸中是否缺油,如果不满,应加满。
定期对硬度计检查保养。
3、试件的厚度应不小于10倍压痕的深度,试件表面必须精细制作,应平整、光洁,表面不得有氧化皮、裂纹凹坑、油脂及明显的加工痕迹,应防止试件发生局部退火现象。
4、测试时,将被试零件擦干净放在试台上,应使试件与试如表面紧贴,然后旋转手轮使试件上升与压头接触,并继续旋转手轮三圈施加初实验力至指示器的小指针于红点处,大指针垂直向上指于标记B 与C处,其偏移不得超过±5个硬度值,否则应另选一个测试。
产品检验规程
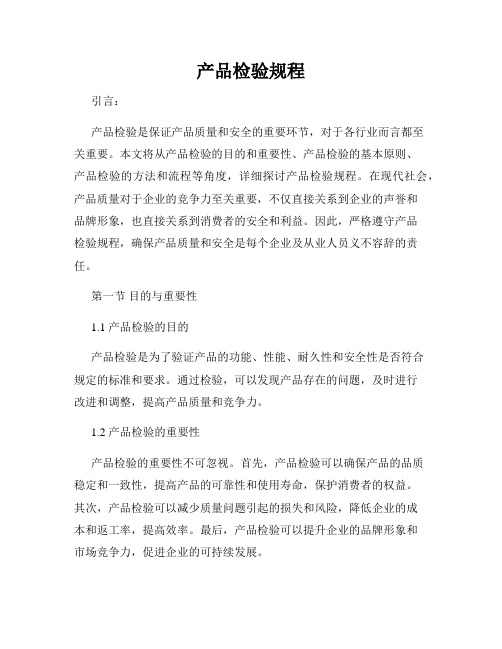
产品检验规程引言:产品检验是保证产品质量和安全的重要环节,对于各行业而言都至关重要。
本文将从产品检验的目的和重要性、产品检验的基本原则、产品检验的方法和流程等角度,详细探讨产品检验规程。
在现代社会,产品质量对于企业的竞争力至关重要,不仅直接关系到企业的声誉和品牌形象,也直接关系到消费者的安全和利益。
因此,严格遵守产品检验规程,确保产品质量和安全是每个企业及从业人员义不容辞的责任。
第一节目的与重要性1.1 产品检验的目的产品检验是为了验证产品的功能、性能、耐久性和安全性是否符合规定的标准和要求。
通过检验,可以发现产品存在的问题,及时进行改进和调整,提高产品质量和竞争力。
1.2 产品检验的重要性产品检验的重要性不可忽视。
首先,产品检验可以确保产品的品质稳定和一致性,提高产品的可靠性和使用寿命,保护消费者的权益。
其次,产品检验可以减少质量问题引起的损失和风险,降低企业的成本和返工率,提高效率。
最后,产品检验可以提升企业的品牌形象和市场竞争力,促进企业的可持续发展。
第二节基本原则2.1 条件一致性原则产品检验应在与产品使用环境相似的条件下进行,以确保测试结果与实际应用情况的一致性。
例如,某种产品在高温环境下运行,那么产品的检验应在相应的高温环境下进行,以模拟真实使用情况。
2.2 标准严谨性原则产品检验应遵循相关标准和规范,确保检验结果的准确性和可靠性。
标准应具有科学性和权威性,能够客观、真实地评估产品的质量和性能,以便确保产品符合预期要求。
2.3 综合评价原则产品检验应综合评价产品的各项性能指标,包括功能性、安全性、环境适应性等,而不仅仅关注某一方面的指标。
通过综合评价,可以全面了解产品的性能和质量水平,进一步优化产品设计和制造过程。
第三节检验方法3.1 可靠性检验可靠性检验是评估产品在规定使用寿命内能否持续正常运行的一种方法。
通过模拟产品在正常使用过程中的各种不同环境和工况条件,对产品的可靠性进行评估,以确保产品的长期稳定性。
《电子产品检验规程》业务流程
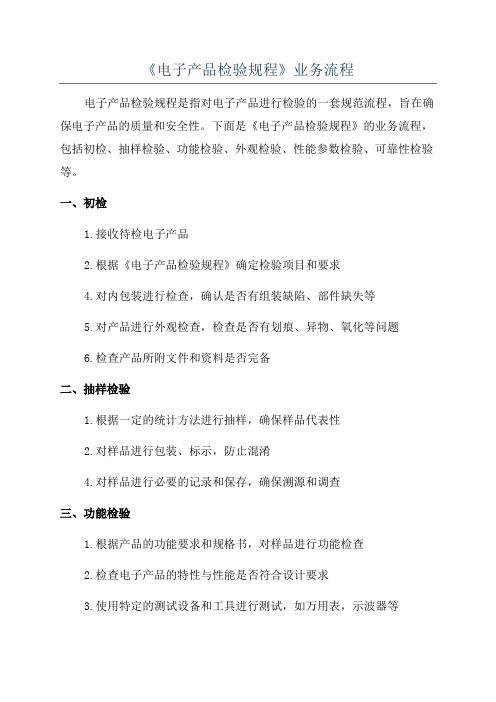
《电子产品检验规程》业务流程电子产品检验规程是指对电子产品进行检验的一套规范流程,旨在确保电子产品的质量和安全性。
下面是《电子产品检验规程》的业务流程,包括初检、抽样检验、功能检验、外观检验、性能参数检验、可靠性检验等。
一、初检1.接收待检电子产品2.根据《电子产品检验规程》确定检验项目和要求4.对内包装进行检查,确认是否有组装缺陷、部件缺失等5.对产品进行外观检查,检查是否有划痕、异物、氧化等问题6.检查产品所附文件和资料是否完备二、抽样检验1.根据一定的统计方法进行抽样,确保样品代表性2.对样品进行包装、标示,防止混淆4.对样品进行必要的记录和保存,确保溯源和调查三、功能检验1.根据产品的功能要求和规格书,对样品进行功能检查2.检查电子产品的特性与性能是否符合设计要求3.使用特定的测试设备和工具进行测试,如万用表,示波器等4.检查电子产品的主要功能是否正常工作5.进行必要的性能参数测试和记录,如电流、电压、功率等四、外观检验1.对电子产品外观进行检查,包括外壳、按键、显示屏等2.检查外观是否有划痕、开裂、氧化等问题3.检查外壳是否完整、是否有变形、松动等问题4.检查按键是否灵敏、回弹是否正常5.检查显示屏是否有亮点、暗点、坏点等问题五、性能参数检验1.根据产品的性能参数要求和规格书,对样品进行性能参数检查2.使用特定的测试设备和工具进行测试,如频谱仪、示波器等3.检查电子产品的性能参数是否符合设计要求4.进行必要的性能参数测试和记录六、可靠性检验1.对电子产品的可靠性进行检查,包括寿命、抗干扰等2.进行长时间的工作和负载测试,查看产品在不同环境条件下的工作情况3.对电子产品进行环境适应性测试,检查产品在高温、低温、湿度等条件下的性能表现4.检查电子产品是否具有抗干扰的能力,如抗电磁干扰、抗静电等以上就是《电子产品检验规程》的业务流程。
通过按照规程进行初检、抽样检验、功能检验、外观检验、性能参数检验和可靠性检验,可以确保电子产品的质量和安全性,提高产品的稳定性和可靠性,并保护消费者的权益。
产品检验规程

产品检验规程
1. 目的和范围
本规程旨在确保产品的质量和符合标准要求。
适用于公司所有生产的产品。
2. 定义
2.1 产品:指公司生产的所有商品和物资。
2.2 检验:指对产品进行全面详细的测试和评估,以确保符合质量和标准要求。
3. 检验流程
3.1 接收产品:产品从生产线上下来后,由负责人接收,填写接收登记表,并将产品送至检验部门。
3.2 外观检验:检验部门对产品进行外观检查,包括检查外观是否完整、无明显瑕疵等。
3.3 功能检验:检验部门对产品进行功能测试,确保产品能够正常使用,并符合技术要求。
3.4 安全检验:检验部门对产品进行安全性测试,确保产品无安全隐患,并符合相关法规和标准要求。
3.5 记录结果:检验部门根据检验情况记录检验结果,并做出相应处理措施。
4. 检验标准
4.1 外观检验标准:根据产品外观设计和相关标准,判断产品外观是否符合要求。
4.2 功能检验标准:根据产品技术规格书和相关标准,测试产品功能是否正常。
4.3 安全检验标准:根据安全测试要求和相关法规,判断产品是否存在安全隐患。
5. 检验结果
5.1 合格:产品在各项检验中均符合标准要求。
5.2 不合格:产品在任何一个检验项目中未能达到标准要求。
5.3 处理措施:对于不合格产品,检验部门将通知生产部门进行整改,并追踪整改进展。
6. 术语定义
6.1 合格品:指符合产品质量和标准要求的产品。
6.2 不合格品:指未能达到产品质量和标准要求的产品。
7. 修订记录
版本号修订日期修订内容修订人。
- 1、下载文档前请自行甄别文档内容的完整性,平台不提供额外的编辑、内容补充、找答案等附加服务。
- 2、"仅部分预览"的文档,不可在线预览部分如存在完整性等问题,可反馈申请退款(可完整预览的文档不适用该条件!)。
- 3、如文档侵犯您的权益,请联系客服反馈,我们会尽快为您处理(人工客服工作时间:9:00-18:30)。
产品检验规程文件编号:AR-ZHCH-01版号:D生效日期:2016.01.16编制:审核:批准:分发号:状态:河北安仁实业集团轴承有限公司目录半成品检验规程 (1)首件检验规程 (2)轴承外委加工件检验规程 (3)成品检验规程 (7)附录:符号说明 (8)金相检验规程 (11)半成品检验规程一、车工车间半成品,操作者必须自己全检,车间检验员按照30%的比例进行抽检,并要留有记录。
检查依据为车间工艺文件,如果发现不合格品,要进行全检。
二、热处理车间的半成品,一般不进行工件的金相检验,主要靠工艺保证,如有特殊情况,要做破坏性检验。
对淬火件的硬度,一般在粗磨端面后,用里氏硬度计检验,检验标准为JBT 7361-2007 滚动轴承零件硬度试验方法,抽查率为30%,少于15件的要全检,能用洛氏硬度计的,要用洛氏硬度计抽查3-5件,如有不合格产品,则要求全检。
三、磨工车间半成品除按车工半成品检验规程进行检验外,还要在粗磨工序进行磁力探伤首件检查,必要时还要进行酸洗检查。
四、检测项目尺寸偏差、形位偏差、粗糙度、外观等。
其中全检项目包括D、△D mp、V DSP、V D m p、d、△d mp、V dsp、V dmp、d i、△d ip、V dip、De、△D ep、V De p抽检项目包括D0、D2、B、△B S、C、△C S、C2、C3、C4、Ke、Ki、S D、S d、S di、Se、Si、、V CS、V BS、E、D emp1-D emp2、D emp—D emp'、D mpmax-D mpmin、d imp—d imp'、抽检比例为20%,并且不少于5套/件。
首件检验规程一、首件产品的概念1、刚上班或接班后加工出来的第一件产品是首件产品。
2、调整设备后加工出来的第一件产品是首件产品。
3、调整或更换工装后加工出来的第一件产品是首件产品。
4、改变工艺参数或操作方法后加工出来的第一件产品是首件产品。
5、改变原材料毛坯或半成品后加工出来的第一件产品是首件产品。
二、首件检验的项目1、首件产品的尺寸参数、几何参数、表面质量及外观是否完全符合工艺文件的要求。
2、对照工艺文件检查所用量具、仪表、标准件及样板等等是否正确。
三、首件检验人员由操作者和车间检验员共同检测,检验员要签字,操作者确认,没有检验员的签字,操作者不得继续加工。
四、对首件检验不合格且返工两次仍不达标的,检验员应及时报告车间领导,查明原因,直到首件检验合格方可正式生产。
轴承外委产品进货检验规程1、非本公司生产制造而由其他公司生产制造提供的轴承相关产品,如毛坯套圈、成品套圈、保持架、滚动体(滚子和钢球)或成套轴承产品都是轴承外委产品。
2、轴承外委产品属于A类物资,须在我公司认可的合格供应商处购得,并应有能证明其质量合格的相关检验报告。
3、我公司每季度应对所有合格供应商进行一次综合评审。
4、轴承外委产品进公司后,供应人员要及时用部门联络单的形式通知技术检验部进行验收,联络单上要注明名称、型号、合格供应商、日期、数量、材质等项目。
5、毛坯套圈的检验:①毛坯套圈的检测量具主要是游标卡尺和卡钳等。
②毛坯套圈的检验项目有材质、尺寸、有无过烧及锻造裂纹、有无严重折叠等。
③毛坯套圈的检验标准是GBT 3203-1982渗碳轴承钢技术条件、GBT 18254-2002 高碳铬轴承钢技术条件、车加工工艺文件等。
④合格供方需随货提供材质理化检验报告。
⑤毛坯套圈实行抽检,抽检比例为10%,且数量不应少于5件,如发现质量问题,应全检,对不合格品进行退货处理。
⑥检查完毕,应做好质量记录,并正确填写和悬挂标识牌,作为此毛坯套圈最终标记的原始信息依据,使其具有可追溯性。
⑦检查人员要对检验结果负责,不允许有错检、误判现象。
6、保持架的检验:①保持架的检测量具主要是游标卡尺、深度尺和自制保持架量尺等。
②保持架的检验项目包括材质、尺寸、外观等。
③保持架的检验标准是GBT 5231-2012 加工铜及铜合金牌号和化学成分,GB/T 1176-1987 铸造铜合金技术条件,JB/T11841-2014金属实体保持架技术条件,产品图纸技术要求。
④保持架检验采用抽检的方法,抽检比例为10%,且数量不应少于5件,如发现质量问题,应全检,对不合格品进行退货处理。
⑤合格供方需随货提供材质理化检验报告。
⑥检查人员要对检验结果负责,不允许有错检、误判现象。
7、滚子和钢球的检验①滚子和钢球的检测量具主要是D051检查仪、外径千分尺、硬度计、探伤机,酸洗槽等。
②滚子和钢球的检验项目包括尺寸、硬度、有无烧伤或裂纹、粗糙度等。
③滚子和钢球的检验标准是JBT 8921-1999 滚动轴承及其商品零件检验规则、GBT 308-2002 滚动轴承钢球、GBT 4661-2002 滚动轴承圆柱滚子等。
④合格供方需随货提供材质理化检验报告。
⑤技术检验部对滚动体硬度用洛氏硬度计进行抽查检验,3000粒以内的,抽检10粒;8000粒以内的,抽检15粒;超过8000 粒的,抽检20粒。
抽查全部合格即判定本批产品合格,如有不合格的,须加倍抽查,第二次抽查如仍有不合格品则判定本批产品为不合格品,做退货处理。
⑥滚动体的酸洗检验由酸洗室进行抽检,每批每型号要酸洗2~3粒,如存在不合格品,在抽查15粒,如仍有不合格品,则要做退货处理。
⑦大型渗碳滚动体需进行探伤全检,绝不放过任何一个有瑕疵的产品。
8、成套轴承及成品零件的检验①成套轴承及成品零件的检测主要用到D713、D714、D901、游标卡尺、内径千分尺、外径千分尺、深度尺、塞尺和粗糙度仪等仪表和量具。
②成套轴承及成品零件的检验项目包括:尺寸偏差、形位偏差、粗糙度、装配高、游隙、旋转灵活性、外观等。
③成套轴承及成品零件的检验标准是:GB/T 307.1-2005滚动轴承公差JB/T 5389.1-2005 滚动轴承轧机用四列圆柱滚子轴承JB/T 5389.2-2005 滚动轴承轧机用双列和四列圆锥滚子轴承JB/T 3573-2004 滚动轴承径向游隙的测量方法GBT 4604-2006 滚动轴承径向游隙JB/T 6643-2004 滚动轴承四点接触球轴承轴向游隙JB/T 8236-2010 滚动轴承双列和四列圆锥滚子轴承游隙及调整方法JB/T 10336-2002 滚动轴承及其零件补充技术条件④合格供方需随货提供材质理化检验报告。
⑤技术检验部对成套轴承及成品零件进行抽查检验,低于20套的抽检2套;大于20套小于50套的抽检4套;50套以上抽检8 套。
抽查全部合格即判定本批产品合格,如有不合格的,须全检,不合格品,做退货处理。
成品检验规程一、成品检验主要用到D713、D714、D901、游标卡尺、内径千分尺、外径千分尺、深度尺、塞尺和粗糙度仪等仪表和量具。
二、成套轴承及成品零件的检验项目包括:尺寸偏差、形位偏差、粗糙度、装配高、游隙、旋转灵活性、外观等。
其中全检项目包括D、△D mp、V DSP、V D m p、d、△d mp、V dsp、V dmp、d i、△d ip、V dip、De、△D ep、V D e p抽检项目包括D0、D2、B、△B S、C、△C S、C2、C3、C4、Ke、Ki、Ker、Kir、Kea、Kia、S D、S d、S di、Se、Sea、Si、Sia、△Cir、V CS、V BS、E、D emp1-D emp2、D emp—D emp'、D mpmax-D mpmin、d imp—d imp'、Li、Le、T、△T抽检比例为20%,并且不少于5套/件。
三、成品轴承零件不得有黑角,外油槽不得带黑皮、内油沟不得有氧化皮、油孔不得有尖角。
四、成套轴承及成品零件的检验标准是:GB/T 307.1-2005滚动轴承公差JB/T 5389.1-2005 滚动轴承轧机用四列圆柱滚子轴承JB/T 5389.2-2005 滚动轴承轧机用双列和四列圆锥滚子轴承JB/T 3573-2004 滚动轴承径向游隙的测量方法GBT 4604-2006 滚动轴承径向游隙JB/T 8236-2010 滚动轴承双列和四列圆锥滚子轴承游隙及调整方法JB/T 10336-2002 滚动轴承及其零件补充技术条件四、技术检验部终检组对成套轴承及成品零件进行全检,不合格品按《产品质量管理规定》进行判定,并对责任者进行处罚。
附:符号说明1、内径dd:公称内径(轴承内圈内径)△d mp:单一平面平均内径偏差,△d mp=d mp—dd mp:单一平面内平均内径, d mp=(d max+d min)/2V dsp (椭圆):单一径向平面内径变动量,V dp=d max--d minV dmp(锥度):平均内径变动量,V dmp=d mpmax--d mpmind mpmax--d mpmin:同一轴承两内圈间,最大平均内径与最小平均内径之差S d(垂直差):内圈表面母线对基准端面的倾斜度的变动量△Cir(三角):圆度误差2、外径DD:公称外径(轴承外圈外径)△D mp:单一平面平均外径偏差,△D mp=D mp—DD mp:单一平面内平均外径, D mp=(D max+D min)/2V Dsp(椭圆):单一径向平面外径变动量,V Dp=D max--D minV Dmp(锥度):平均外径变动量,V Dmp=D mpmax--D mpminD mpmax--D mpmin:同一轴承两外圈间,最大平均外径与最小平均外径之差S D(垂直差):外圈表面母线对基准端面的倾斜度的变动量3、内圈滚道didi:外圈滚道V dip(椭圆):单一径向平面内,内圈滚道直径变动量K i(壁厚差):内圈滚道对内圆表面的厚度变动量L i:内圈滚道直线度d imp—d imp'(锥度):内圈滚道两端平均直径之差S di: (垂直差)内圈滚道母线对基准端面倾斜度的变动量4、外圈滚道DeDe:外圈滚道V Dep(椭圆):单一径向平面内,外圈滚道(沟道)直径变动量K e(壁厚差):外圈滚道(沟道)对外圆表面的厚度变动量K er:外圈一滚道(沟道)对另一滚道(沟道)的径向圆跳动量L e:外圈滚道直线度D emp1—D emp2(锥度):外圈两滚道单一平面平均直径之差D emp—D emp':外圈滚道两端平均直径之差3、宽度和高度T:(装配高)轴承公称高度Ts:(装配高)轴承实际高度△Ts:轴承实际高度偏差。
△Ts= Ts- TC:外圈公称宽度B:内圈公称宽度V BS(平行差):内圈宽度的变动量V CS(平行差):外圈宽度的变动量△C S---外圈单一宽度偏差△B S---内圈单一宽度偏差C2:小挡边宽度C3:中隔/平挡圈宽度C4:中挡边宽度V C2S、V C3S、V C4S:外圈挡边或外挡圈的宽度变金相检验规程1、试样的选取取样部位应按照实验目的和要求进行确定,取样时,不能使试样由于变形或受热而导致组织发生变化,影响判断结果。