注塑车间生产控制程序
注塑作业流程
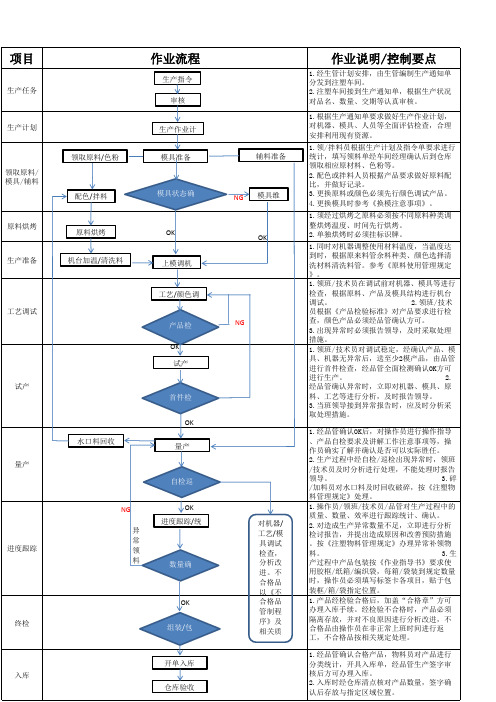
料、工艺等进行分析,及时报告领导。
3.当班领导接到异常报告时,应及时分析采
取处理措施。
1.经品管确认OK后,对操作员进行操作指导
、产品自检要求及讲解工作注意事项等,操
作员确实了解并确认是否可以实际胜任。 2.生产过程中经自检/巡检出现异常时,领班
/技术员及时分析进行处理,不能处理时报告
领导。
3.碎
/加料员对水口料及时回收破碎,按《注塑物
2.领班/技术
员根据《产品检验标准》对产品要求进行检
查,颜色产品必须经品管确认方可。
3.出现异常时必须报告领导,及时采取处理
措施。
1.领班/技术员对调试稳定,经确认产品、模
具、机器无异常后,送至少2模产品,由品管
进行首件检查,经品管全面检测确认OK方可
进行生产。
2.
经品管确认异常时,立即对机器、模具、原
1.根据生产通知单要求做好生产作业计划, 对机器、模具、人员等全面评估检查,合理 安排利用现有资源。
1.领/拌料员根据生产计划及指令单要求进行 统计,填写领料单经车间经理确认后到仓库 领取相应原材料、色粉等。 2.配色或拌料人员根据产品要求做好原料配 比,并做好记录。 3.更换原料或颜色必须先行颜色调试产品。 4.更换模具时参考《换模注意事项》。
数量确
终检 入库
OK 组装/包
开单入库 仓库验收
辅料准备
NG 模具维
OK
NG
对机器/ 工艺/模 具调试 检查, 分析改 进。不 合格品 以《不 合格品 管制程 序》及 相关质
作业说明/控制要点
1.经生管计划安排,由生管编制生产通知单 分发到注塑车间。 2.注塑车间接到生产通知单,根据生产状况 对品名、数量、交期等认真审核。
注塑车间细化管理制度

注塑车间细化管理制度一、生产计划管理1. 生产计划的制定:根据市场需求和企业生产能力,制定详细的生产计划,并及时更新和调整。
2. 计划执行情况的跟踪:通过生产数据的统计和分析,及时了解生产计划的执行情况,并做好跟踪管理。
3. 生产进度的监控:严格按照生产计划进行生产,对生产进度进行有效监控,确保按时完成生产任务。
二、设备管理1. 设备日常检查:设立设备检查表,对注塑机等生产设备进行日常检查,确保设备正常运转。
2. 设备维护保养:制定设备维护保养计划,定期对设备进行维护保养,延长设备的使用寿命。
3. 设备故障处理:设立设备故障报修流程,及时处理设备故障,确保生产不受影响。
三、原料管理1. 原料采购管理:建立原料供应商档案,严格把控原料的质量和供应周期,确保原料的及时供应。
2. 原料使用计划:根据生产计划制定原料使用计划,合理安排原料的使用,防止原料浪费。
3. 原料库存管理:建立原料库存台账,及时更新原料库存信息,避免原料过期损耗。
四、品质管理1. 品质标准制定:制定产品品质标准和验收标准,确保产品质量符合要求。
2. 品质检验:建立产品检验流程,对生产产品进行全过程抽检,确保产品合格率。
3. 品质异常处理:建立品质异常处理机制,对品质异常及时处理,并找出问题根源,防止问题再次发生。
五、安全管理1. 安全培训:定期进行安全培训,提高员工的安全意识,降低安全事故的发生率。
2. 安全巡检:建立安全巡检制度,定期对注塑车间进行安全巡检,及时发现并处理安全隐患。
3. 安全应急预案:制定安全应急预案,做好安全事故的应急处理准备工作,确保员工人身安全。
以上便是注塑车间的细化管理制度,我们会严格执行以上规定,不断完善和提高管理水平,为企业的发展和生产顺利进行提供保障。
希望所有员工共同努力,遵守管理规定,共同创造一个安全、高效的生产环境。
注塑车间质量控制流程

注塑车间质量控制流程标题:注塑车间质量控制流程引言概述:注塑车间是制造企业中非常重要的一个环节,质量控制流程的严谨性直接影响产品的质量和客户满意度。
本文将详细介绍注塑车间质量控制流程的五个部分,包括原料检验、注塑成型过程控制、产品检测、包装和出厂检验。
一、原料检验1.1 确认原料的质量标准:根据产品要求,确定原料的材质、颜色、硬度等质量标准。
1.2 检查原料外观:检查原料是否有异物、色差、气泡等缺陷。
1.3 进行物理性能测试:对原料进行拉伸、弯曲等物理性能测试,确保原料符合要求。
二、注塑成型过程控制2.1 确定注塑工艺参数:根据产品要求,确定注塑工艺参数,包括注塑温度、压力、速度等。
2.2 进行模具调试:对模具进行调试,确保产品尺寸、外观等符合标准。
2.3 监控注塑过程:实时监控注塑过程,及时调整参数,确保产品质量稳定。
三、产品检测3.1 外观检测:对产品外观进行检测,包括色差、气泡、划痕等。
3.2 尺寸检测:对产品尺寸进行检测,确保产品尺寸符合标准。
3.3 功能性能测试:对产品进行功能性能测试,确保产品功能正常。
四、包装4.1 确定包装方式:根据产品特点和客户要求,确定包装方式,包括包装材料、包装方式等。
4.2 包装检验:对包装进行检验,确保包装完整、无损坏。
4.3 标识标签:在包装上标注产品信息、生产日期、批次号等标识标签。
五、出厂检验5.1 抽检产品:对部分产品进行抽检,确保产品质量符合标准。
5.2 检查文件齐全:检查产品质量检测报告、包装清单等文件是否齐全。
5.3 审核出厂:经过质量部门审核,确认产品符合要求后,方可出厂。
结论:注塑车间的质量控制流程是保障产品质量的重要环节,通过严格的控制流程,可以有效提高产品质量和客户满意度。
希望本文的介绍可以对注塑车间质量控制流程有所帮助。
注塑管理控制程序
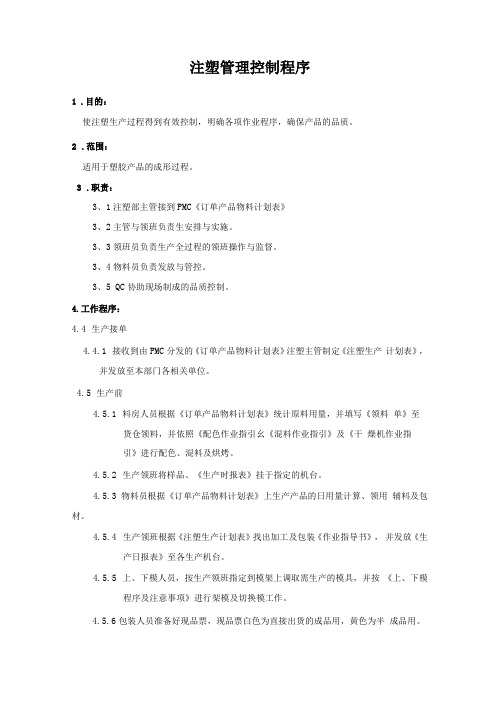
注塑管理控制程序1.目的:使注塑生产过程得到有效控制,明确各项作业程序,确保产品的品质。
2.范围:适用于塑胶产品的成形过程。
3.职责:3、1注塑部主管接到PMC《订单产品物料计划表》3、2主管与领班负责生安排与实施。
3、3领班员负责生产全过程的领班操作与监督。
3、4物料员负责发放与管控。
3、5 QC协助现场制成的品质控制。
4.工作程序:4.4生产接单4.4.1接收到由PMC分发的《订单产品物料计划表》注塑主管制定《注塑生产计划表》,并发放至本部门各相关单位。
4.5生产前4.5.1料房人员根据《订单产品物料计划表》统计原料用量,并填写《领料单》至货仓领料,并依照《配色作业指引幺《混料作业指引》及《干燥机作业指引》进行配色、混料及烘烤。
4.5.2生产领班将样品、《生产时报表》挂于指定的机台。
4.5.3物料员根据《订单产品物料计划表》上生产产品的日用量计算、领用辅料及包材。
4.5.4生产领班根据《注塑生产计划表》找出加工及包装《作业指导书》,并发放《生产日报表》至各生产机台。
4.5.5上、下模人员,按生产领班指定到模架上调取需生产的模具,并按《上、下模程序及注意事项》进行架模及切换模工作。
4.5.6包装人员准备好现品票,现品票白色为直接出货的成品用,黄色为半成品用。
4.5.7品质人员准备即将生产的项目样本、限度样本、《品质检验基准书》、及相关检查的记录表。
4.5.8领班员准备标准《成型条件表》、《机台运行状况表》及《模具保养记录表》,检查模具安装、物料投入等准备工作就绪:4.6试模4.6.1由项目部发《试模通知单》,注塑部在接单30分钟内安排生产有注塑部填写《试模报告》,由项目部、品质部、注塑部共同确认合格方可交模。
试模不合格由项目跟进修改进度再次试模。
试模报告一联:项目;一联:品质;一联:注塑。
4.7原材料来料检验和试料管理:4.7.1当采购物料回厂后,无论是新料或是粗粒料,当班巡检必须抽不同位置三处以上分多个小包装样品,每袋1KG左右进行机台试料,试料合格后必须作下检验记录,特别要求写清楚进料时间,厂家,并督促仓管进行产品时间、厂家的标识等,试样过程中留样要进行编号并收藏保管,直到材料开始正常生产为止;4.7.2每次换料生产时,要求不同的材料批次进行不同的标识区别,便于发生不良后进行产品追溯,具体操作是在巡检报表中注明换料的时间、厂家、产成品的包装顺序号等,发生异常可以追溯到哪个厂家、什么时间进货,哪天生产,从第几箱开始等;4.7.3试料合格后要填写来料检验报告,经品质主管审核确认后,和留样一起包装待查,若为不良则由技术组和采购、生产等部门进行评审和协调处理,报相关领导确认后执行4.8首检、记录和标识:4.8.1注塑生产过程中,开机和转模的3-5啤操作员送检IPQC进行首检;IPQC 检验产品的外观、尺寸、颜色,巡检员做好开机产品的首件签字封样,并填写《首检记录表》,生产过程中要按巡检要求进行产品抽检工作,每次检验项目要完整,并同时对打包产品、作业台产品和机台随机产品三个环节进行验证,发现问题,及时纠正和协调处理,并如实、认真填写《巡检记录》;4.8.2巡检要求操作工对自检不合格的产品进行返工,并对返工产品进行记录、标识和复查,直至达到产品质量要求,否则不允许盖章进仓,对不合格的产品在交接班时要确保信息完全传达给下班次巡检员,以防零部件、材料误产、误用;4.8.3每天要将巡检报表收回并检查巡检记录的情况,对记录有不实或存在疑问则找相关巡检员了解确认,如属工作粗心、失误、责任心不足则要求进行通报批评并在当天的绩效考核进行考核扣罚,对多次未按检验工作指导执行的巡检员将考虑换岗或劝退;4.8.4各注塑工段完成品合格后,巡检在包装外箱上盖QCPASS章,才能进仓或转入下一道工序,注塑的成品、半成品、合格和不合格品等,应按规定的区域整齐放置,并按标识和可追溯性管理原则进行标识,检验员有权对过程进行控制和协调,对标识不规范有权勒令员工整改或停机整顿。
注塑车间管理制度

注塑车间管理制度一、总则注塑车间是公司生产的重要环节之一,为了保证注塑车间的运作顺利,提高生产效率,确保产品质量,特制定本管理制度。
二、车间管理职责1. 车间经理负责整个注塑车间的日常管理工作,包括生产计划安排、人员调配、设备维护等,确保车间正常运转。
2. 生产主管协助车间经理管理车间的生产工作,监督员工的操作流程,确保产品质量符合标准。
3. 设备维护人员负责注塑车间设备的维护、保养和故障排除工作,及时处理设备故障,以确保生产的连续性。
4. 品质检验员负责对注塑产品进行质量抽检,确保产品符合标准。
三、生产管理1. 生产计划根据客户订单和销售计划,制定注塑车间的生产计划,并及时调整以适应市场需求变化。
2. 安全生产车间内禁止吸烟、随地吐痰等不文明行为,严禁未经培训人员操作设备,确保员工的安全。
3. 工艺控制根据产品要求,制定标准工艺流程,确保生产过程中的稳定性和一致性。
4. 车间现场管理注塑车间要保持清洁整齐,每天结束后进行全面清理,确保生产环境的整洁和安全。
四、质量管理1. 原料检验对进入注塑车间的原料进行抽检,确保原料的质量符合标准。
2. 产品检验每批次生产完成后,进行产品的抽检,确保产品质量符合标准。
3. 不合格品处理对不合格品进行分类处理,包括返工、报废等,确保合格品率达到要求。
4. 质量记录每批次生产完成后,做好相应的质量记录,包括产品抽检结果、原因分析等,以便日后的追溯和改进。
五、安全管理1. 安全教育每名员工入职前都要进行安全教育培训,并定期组织员工进行安全知识的培训和考核。
2. 应急预案制定注塑车间的应急预案,针对可能发生的事故制定相应的处理措施,确保员工的生命和财产安全。
3. 设备安全定期对注塑设备进行安全检查和维护,确保设备的正常运行和工作人员的安全。
六、绩效考核1. 生产效率根据生产计划完成情况和产品合格率,评估注塑车间的生产效率。
2. 质量绩效根据产品抽检结果和客户投诉率,评估注塑车间的质量绩效。
控制程序及流程图)

青岛惠利塑胶有限公司注塑工序控制程序注塑工序控制程序1.目的使注塑料车间加工和注塑料的产品在受控状态下完成,保证注塑产品的质量。
2.适用范围适用于制造部注塑车间各生产活动的控制。
3.定义:无4.职责4.1 制造部下达《注塑生产计划单》。
4.2 注塑车间注塑和加工过程的控制。
4.3 质量保证部对注塑产品的过程监控和最终检验。
5.工作程序5.1生产计划5.1.1制造部按《生产任务单》制定《注塑生产计划单》,下发给注塑车间。
5.2生产前准备5.2.1车间物料员根据《注塑生产计划单》领取所需的原材料、辅助材料、包装材料、模具、治具等,并按要求放置在指定位置。
5.3原料烘干5.3.1加料员按《注塑烘干作业指导书》进行原料烘干。
5.4模具安装5.4.1技术员依据《模具安装作业指导书》进行模具安装。
5.5工艺参数调整5.5.1技术员依据《注塑工艺规定》或以往生产类似产品时的工艺条件对注塑工艺参数进行调整;技术员对试出的产品要进行自检,当产品质量稳定后,通知车间质检员共同进5.5.2行首检。
5.6首检5.6.1车间质检员和技术员按《注塑工序首检、巡检作业指导书》进行首检。
5.7注塑成型5.7.1技术员记录注塑工艺作为本批产品注塑时的工艺控制依据。
工艺更改时须同时填写《注塑工艺参数更改报告》。
5.7.2注塑机操作工注塑产品时依照《注塑机操作规程》操作注塑机,需要压定型的产品按《产品压定型作业指导书》规定作业。
5.7.3记录每班注塑生产情况。
5.8注塑过程监督5.8.1注塑组长对操作工的注塑作业进行监督,并每2小时填写一次《注塑生产控制分析表》,统计注塑生产过程中的实际产量及异常情况;5.8.2注塑组长对车间生产的各机台、模具、产品进行巡视,发现异常及时处理;5.8.3车间质检员每3~4小时巡查一次注塑工艺参数并记录于《产品巡检记录表》中。
5.9产品加工5.9.1员工加工时按照《注塑加工作业指导书》要求进行产品加工。
注塑流程图

品管课:FQC员 品管课长
1、FQC检查记录表 注塑课:操作 注塑课长/
员
班长
1、入库单 2、标签卡
注塑课:物运
员
车间主任
资材课:仓库管
员
资材课长
编制
注塑课:班长/ 生产部经理
技术员
/课长
品管课:品管 品管部经理
员
/课长
1、自主检查表 2、巡检表 3、生产日报表 4、标签卡
注塑课班长
注塑课:操作员 /碎/加料员
/技术员/课 长
品管课:巡检员
品管课长
1、生产指令单 2、领料单
注塑课:操作 注塑课长 员/班长/技术 员/领拌料员
生管员
生管课长
3、标签卡
2、经品管确认异常时,立即对机器、模具、原料、工艺 等进行分析,及时报告主管。
3、主管接到异常报告时,应及时分析采取处理措施 1、经品管确认OK后,对操作员进行操作指导、产品 自检要求及讲解工作注意事项等,操作员确实了解 并确认是否可以实际胜任。
2、生产过程中经自检/巡检出现异常时,班长/技术 员及时分析进行处理,不能处理时报告主管。
2、注塑车间接到生产通知单,根据生产状况对品名 、数量、交期等认真审核。
1、根据生产通知单要求做好生产作业计划,对机器 、人员、模具等全面评估检查,合理安排利用现有 资源。
1、领/拌料员根据生产计划及指令单要求进行统 计,填写领料单经课长确认后到仓库领取相应原材 料、色粉等。
2、配色或拌料人员根据产品要求作好原料配比,并 做好记录。
对机器/工 艺/模具调 试检查,
分析改进。 不合格品 以《不合
格品管制 程序》及 相关质量
管理规定 流程办理。
1、班长/技术员在调试前对机器行机台调试。
注塑部生产控制程序
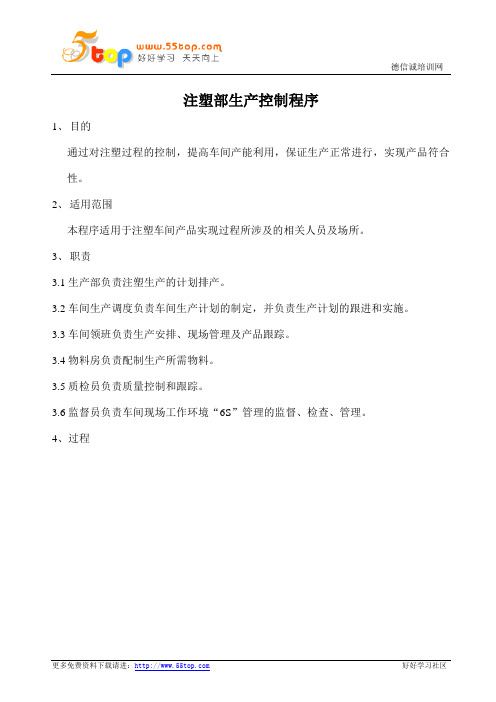
注塑部生产控制程序
1、目的
通过对注塑过程的控制,提高车间产能利用,保证生产正常进行,实现产品符合性。
2、适用范围
本程序适用于注塑车间产品实现过程所涉及的相关人员及场所。
3、职责
3.1生产部负责注塑生产的计划排产。
3.2车间生产调度负责车间生产计划的制定,并负责生产计划的跟进和实施。
3.3车间领班负责生产安排、现场管理及产品跟踪。
3.4物料房负责配制生产所需物料。
3.5质检员负责质量控制和跟踪。
3.6监督员负责车间现场工作环境“6S”管理的监督、检查、管理。
4、过程
注塑流程
4.1 生产准备
4.1.1车间生产调度结合车间产能状况,对生产部下达的《注塑生产通知单》核实生产可行性,并确认接单。
- 1、下载文档前请自行甄别文档内容的完整性,平台不提供额外的编辑、内容补充、找答案等附加服务。
- 2、"仅部分预览"的文档,不可在线预览部分如存在完整性等问题,可反馈申请退款(可完整预览的文档不适用该条件!)。
- 3、如文档侵犯您的权益,请联系客服反馈,我们会尽快为您处理(人工客服工作时间:9:00-18:30)。
编号:Q/MG-1025-2007 页次:1/5
注塑车间生产控制程序
1、目的
通过对注塑过程的控制,提高车间产能利用,保证生产正常进行,实现产品符合性。
2、适用范围
本程序适用于注塑车间产品实现过程所涉及的相关人员及场所。
3、职责
3.1生产部负责注塑生产的计划排产。
3.2车间生产调度负责车间生产计划的制定,并负责生产计划的跟进和实施。
3.3车间领班负责生产安排、现场管理及产品跟踪。
3.4物料房负责配制生产所需物料。
3.5质检员负责质量控制和跟踪。
3.6监督员负责车间现场工作环境“6S”管理的监督、检查、管理。
4、过程
编号:Q/MG-1025-2007 页次:2/5
注塑流程
编号:Q/MG-1025-2007 页次:3/5 4.1 生产准备
4.1.1车间生产调度结合车间产能状况,对生产部下达的《注塑生产通知单》核实生产可行性,并确认接单。
4.1.2车间生产调度应认真核对订单,对订单内容有分歧或疑义时及时反馈车间主管,并与生产部沟通联系。
4.2 生产过程
4.2.1车间生产调度根据生产部下达的《注塑生产通知单》,编制《注塑生产进度日报表》并分发至物料房及配色房。
4.2.2根据《注塑生产进度日报表》合理安排模具颜色及物料的转换,排出车间各机台《生产通知单》,通知车间领班做好生产安排,当机台确实无法按时完成《生产通知单》时,生产调度应及时通知车间主管,并及时与计划协调,确保生产作业通畅。
4.2.3车间领班确认接单后应及时通知相应生产机台,并通知注塑机修工至模具仓库领取相应生产模具,准备生产所需的辅助工具及检查设备状况,出现异常及时反馈车间领班。
4.2.4机台批量生产前,质检员应对注塑成品进行首件判定,确认合格制作《产品首件样板卡》,记录设备工艺参数,经注塑质检组长确认后(新产品及产品原料发生变迁经工艺技术部主管确认后),挂于机台显眼位置作为质检、巡检依据及工艺制定标准后通知机台生产。
4.2.5操作工在注塑生产过程中,应不间断实施自检,车间领班应对自检合格产品进行随机抽检,出现异常应及时反馈。
4.2.6质检员对分管机台按《注塑检验规范》执行抽检,做好产品标识,并填写《注塑巡检记录》,当检验发现不合格产品时按《不合格品控制程序》(Q/MG-1037-2007)执行。
4.2.7产品生产完毕由车间物料员按产品规格、型号秤重定量拼装,经质检检验合格后标识产品信息,由物料员填写《半成品入库单》办理产品入库手续,移交中转仓。
4.2.8当日生产完毕,应将作业相关信息反馈接班人员,并填写《注塑机操作工交接记录表》。
4.3 生产变更
4.3.1当机台生产作业计划完成前,车间生产调度应在《注塑生产进度日报表》内重点标注,提前通知物料房做好物料更单准备。
4.3.2常规生产产品,生产部需紧急更单时,需提前下达《紧急更单通知单》,并由车间主管签收,车间生产调度需重新调整生产计划任务,及时通知物料房及车间领班避免造成生产混乱。
4.4 生产统计
4.4.1车间统计员根据每日成品生产数量,以电子备档形式编制《生产日报表》共享于车间主管及生产部。
4.4.2车间统计员根据生产入库产品及物料领用情况,分析编制《机台生产及物料报废登记表》。
4.4.3车间质检组长每月根据产品质量状况,统计编制《产品质量状况统计表》及《车间产品质量情况分析表》。
4.5 设备管理
编号:Q/MG-1025-2007 页次:4/5 4.5.1操作员需按各设备《安全操作规范》规范作业流程。
4.5.2设备使用过程中出现异常应立即停机,通知车间机修工判断故障原因,并填写《注塑车间停修记录表》
4.5.2.1模具异常由机修工编制《模具修理(改)通知单》交模具车间。
4.5.2.2机器设备故障由机修工填写《设备故障请修单》交设备管理部报修。
4.5.3设备使用人员每天作业完毕后应对设备实施日常维护保养,并填写《设备日常维护保养记录》。
4.6产能控制
4.6.1产能设定
4.6.1.1各生产车间在新产品生产前及产品生产工艺调整后应及时评估设定实际生产产能,并将设定后生产产能编制《车间产能统计表》经车间主管确认交生产副总批准后及时更新电子版本《车间产能统计表》,对更新项目以颜色重点标注,并共享于生产计划部,生产计划部应以车间实际产能情况制订生产计划,确保产能利用率。
4.6.2产能变更
4.6.2.1各生产车间已设定生产产能变化幅度在5%之内,一般情况不作随意变更,各生产车间技术主管每生产3个月订单后,根据车间生产统计及实际产能情况对现有产品、工艺产能进行设定调整、更新、编制《车间产能统计表》经车间主管确认交生产副总批准后及时更新电子版本《车间产能统计表》,生产计划部按更新后产能排产。
4.6.3产能异常控制
4.6.3.1当生产设备(生产机器、模具等)发生故障,车间应按《设备管理控制程序》、《模具管理控制程序》执行处理,并将停机情况填写《车间停修记录表》,及时共享反馈生产计划部。
4.6.3.2生产计划部对产品产能实际达成情况做月统计分析,如连续生产3个月订单产能有提高或降低超过标准产能的5%,将酌情提出产能变更申请,经车间主管会签后,提交生产副总批准后进行标准产能的变更。
4.6.3.3当特殊情况,如原产品标准产能设定与实际生产产能相差超过5%,即使调整时间没有超过3个月,生产车间技术主管可以进行设定调整、更新、编制《车间产能统计表》经车间主管确认交生产副总批准后,生产计划部按更新后产能排产。
4.7 作业现场环境管理
4.7.1作业现场环境管理按《工作环境控制程序》(Q/MG-1012-2007)执行。
4.7.2车间监督员按环境检查相关项目检查,并记录编制《注塑车间作业环境检查表》。
相关记录:
1、注塑生产通知单
2、注塑生产进度日报表
3、产品首件样板卡
4、注塑巡检记录
5、半成品入库单
6、注塑机操作工交接记录表
编号:Q/MG-1025-2007 页次:5/5
7、机台生产及物料报废登记表
8、产品质量状况统计表
9.车间产品质量情况分析表
10.模具修理(改)通知单
11.设备故障请修单
12.设备日常保养表
13.注塑车间作业环境检查表
14.生产日报表
15.注塑车间停修记录表
16.紧急更单通知单
17.零件检验记录表
18.车间产能统计表
19.车间停修记录表。