第6章过程控制
第六章控制图、过程能力和直方图
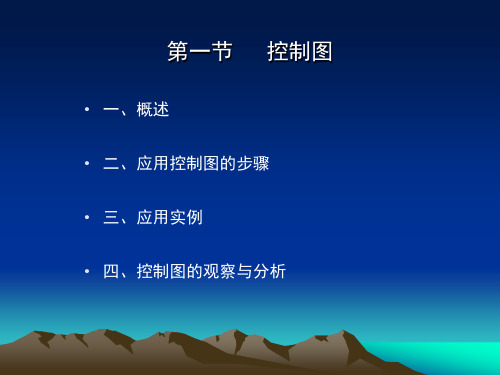
在工序控制中需要了解的三个方面,都能在控制图上得到。 (1) 在连续的生产监控中,有无变化的征兆; (2) 有无急剧的变化; (3) 有无越出控制范围的异常值。
--控制图的作用:
在质量诊断方面,可以用来度量过程的稳定性,即过程是否处于统计控制状态; 在质量控制方面,可以用来确定什么时候需要对过程加以调整,而什么时候则需使过程保持相应的稳定状态; 在质量改进方面,可以用来确认某过程是否得到了改进。
1.864
1.816
1.777
E2
2.660
1.772
1.457
1.290
1.134
1.109
1.054
1.010
0.975
m3A2
1.880
1.187
0.796
0.691
0.549
0.509
0.430
0.410
0.360
D3
-
-
-
-
-
0.076
0.136
0.184
0.223
d2
1.128
1.693
P
-
n -
(1- )
Pn
-
Pn
-
3
u
-
3
n
u
-
+
u
-
3
n
u -
c
-
3
c —
c
-
3
c +
控制系数选用表
n
2
3
4
5
6
7
8
9
10
A2
1.880
1.023
0.729
0.577
0.483
过程控制

第6章 过程控制系统的应用实例6.1 精馏塔的控制精馏是石油化工、炼油生产过程中的一个十分重要的环节,其目的是将混合物中各组分分离出来,达到规定的纯度。
精馏过程的实质就是迫使混合物的气、液两相在塔体中作逆向流动,利用混合液中各组分具有不同的挥发度,在互相接触的过程中,液相中的轻组分逐渐转入气相,而气相中的重组分则逐渐进入液相,从而实现液体混合物的分离。
一般精馏装置由精馏塔、再沸器、冷凝器、回流罐等设备组成,如图6.1所示。
图6.1 简单精馏控制示意图进料流量F从精馏塔中段某一塔板上进入塔内,这块塔板称为进料板。
进料板将精馏塔分为上下两段,进料板以上部分称为精馏段,进料板以下部分称为提馏段。
溶液中组分的数目可以是两个或两个以上。
实际工业生产中,只有两个组分的溶液不多,大量需要分离的溶液往往是多组分溶液。
多组分溶液的精馏在基本原理方面和两组分溶液的精馏是一样的。
本节只讨论两组分溶液的精馏。
6.1.1 精馏原理在恒定压力下,单组分液体在沸腾时虽然继续加热,其温度却保持不变,即单组分液体的沸点是恒定的。
对于两组分的理想溶液来说,在恒定压力下,其沸点却是可变的。
例如对于A、B两种混合物的分馏,纯A的沸点是140℃,纯B的沸点是175℃。
如果两组分的混合比发生变化,混合溶液的沸点也随之发生变化,如图6.2中的液相曲线所示。
第6章 过程控制系统的应用实例·333··333·150140160170180020406080100100806040200A :B :组分/(%)温度/℃图6.2 A 、B 两组分混合物温度-浓度曲线设原溶液中A 占20%,B 占80%,此混合液的沸点是164.5℃,加热使混合液体沸腾。
这时,与液相共存的气相组分比是A 占45.8%,B 占54.2%。
这些气体单独冷凝后所形成的混合液体中,A 占45.8%,B 占54.2%;如果使此冷凝后的混合液体沸腾,其沸点是154.5℃。
过程控制第六章大时滞过程控制系统

6.3 预估补偿控制方案
X (s)
F(s) Wf (s)
Wc (s)
W0 (s)es
Y (s)
图6-9 单回路系统框图
Y (s) X (s)
TI
KC (TI sW01(s)
s 1)(TDs 1)es KC (TI s 1)(TDs 1)es
Y (s) F(s)
TI
sW01(s)
TI ses KC (TI s 1)(TDs
1)es
(6-3) (6-4)
由以上4个式子可见,微分先行控制方案和PID控制方案的特征方程完全相同。
X (s)
F(s) Wf (s)
Wc (s)
W0(s)es
W0 (s)
Y (s)
es
图6-10a) Smith预估补偿控制系统结构原理图
6.3 预估补偿控制方案
X (s)
Wc (s) U (s) W0(s)es Y (s)
Y1(s)
Y2
(s)
(1
es
6.1 大时滞过程概述
时滞现象在工业生产过程中是普遍存在的。时滞可分为两类,一类称为纯时滞,如 带式运输机的物料传输、管道输送、管道混合、分析仪表检测流体的成分等过程; 另一类为惯性时滞,又称为容积时滞。该类时滞主要来源于多个容积的存在,容积 的数量可能有几个甚至几十个,如分布参数系统可以理解为具有无穷多个微分容积。 因此,容积越大或数量越多,其滞后的时间就越长。
第6章高性能过程控制ppt

Y ' s G0 s e s Gs s G0 s U s
Gs s G0 s 1 e s
6.1 串级控系统
6.1.1串级控制系统的基本概 念 一、什么是串级控制?它是怎样提出来
图 6- 2
的?其组成结构怎样?(图6-1;)
工艺流程?控制要求?系统分析…
问题:过渡过程时间长,调节不及时
解决办法:串级控制(图6-3)
串级控制系统的一般框 结构特点… 图
6.1.2
G02* s
'
串 单
串 T01 T02 ' T01T02 ' 1 T01 T02 ' 单 T01 T02 T01T02 1 T01 T02
1 '2 T01 T02 1 T01T02 2 '
'2
结论:副回路改善了动特性、提高了响应速度和工作频率;当主、副时 间常数比值一定,副调节器的比例系数越大,工作频率越高;同样,当 比例系数一定,主、副时间常数比值越大,工作频率也越高。其结果使 振荡周期缩短,提高了系统的控制质量。
T2 T 1
q0 H 0 q f Cp
K0
dT2 H0 dq0 q f C p
C p (T2 T1 ) H0
该补偿器用比例调节器即可实现
2. 动态补偿:GB s GF s / G0 s
由于精确模型难以得到或难以实现,只有要求严格控制动态偏差时才采用。 6.2.4 前馈-反馈复合控制(图6-18) 作用机理分析:
第6章过程控制系统的应用实例-Read

第6章 过程控制系统的应用实例6.1 精馏塔的控制精馏是石油化工、炼油生产过程中的一个十分重要的环节,其目的是将混合物中各组分分离出来,达到规定的纯度。
精馏过程的实质就是迫使混合物的气、液两相在塔体中作逆向流动,利用混合液中各组分具有不同的挥发度,在互相接触的过程中,液相中的轻组分逐渐转入气相,而气相中的重组分则逐渐进入液相,从而实现液体混合物的分离。
一般精馏装置由精馏塔、再沸器、冷凝器、回流罐等设备组成,如图6.1所示。
图6.1 简单精馏控制示意图进料流量F从精馏塔中段某一塔板上进入塔内,这块塔板称为进料板。
进料板将精馏塔分为上下两段,进料板以上部分称为精馏段,进料板以下部分称为提馏段。
溶液中组分的数目可以是两个或两个以上。
实际工业生产中,只有两个组分的溶液不多,大量需要分离的溶液往往是多组分溶液。
多组分溶液的精馏在基本原理方面和两组分溶液的精馏是一样的。
本节只讨论两组分溶液的精馏。
6.1.1 精馏原理在恒定压力下,单组分液体在沸腾时虽然继续加热,其温度却保持不变,即单组分液体的沸点是恒定的。
对于两组分的理想溶液来说,在恒定压力下,其沸点却是可变的。
例如对于A、B两种混合物的分馏,纯A的沸点是140℃,纯B的沸点是175℃。
如果两组分的混合比发生变化,混合溶液的沸点也随之发生变化,如图6.2中的液相曲线所示。
第6章 过程控制系统的应用实例·333··333·150140160170180020406080100100806040200A :B :组分/(%)温度/℃图6.2 A 、B 两组分混合物温度-浓度曲线设原溶液中A 占20%,B 占80%,此混合液的沸点是164.5℃,加热使混合液体沸腾。
这时,与液相共存的气相组分比是A 占45.8%,B 占54.2%。
这些气体单独冷凝后所形成的混合液体中,A 占45.8%,B 占54.2%;如果使此冷凝后的混合液体沸腾,其沸点是154.5℃。
过程控制第六章大时滞过程控制系统
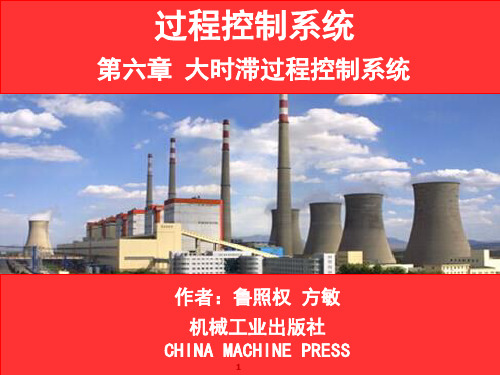
Y (s)
图6-5 PID控制方案
过程控制系统
9
6.2 常规控制方案
因此,实际上微分环节不能真正起到对被控参数变化速度进行校正的目的,克 服动态超调的作用是有限的。如果将微分环节更换一个位置,如图6-6所示,则微分 作用克服超调的能力就大不相同了。这种控制方案称为微分先行控制方案。
F (s)
X (s)
F (s)
X (s)
K C (1
1
TI s
)
W0 ( s )e s
Y (s)
TD s
图6-7 中间微分反馈控制方案
过程控制系统
13
6.2 常规控制方案
3. 常规控制方案比较
图6-8给出了分别用PID、中间微分反馈和微分先行三种方法进行控制的 仿真结果。从图中可看出,中间微分反馈与微分先行控制方案虽比PID方法的 超调量要小,但仍存在较大的超调,响应速度均很慢,不能满足高控制精度 的要求。 y PID
10
6.2 常规控制方案
微分先行控制方案的闭环传递函数如下:
1)给定值作用下
KC (TI s 1)es Y ( s) X (s) TI sW01 (s) KC (TI s 1)(TD s 1)es
(6-1)
2)在扰动作用下
Y ( s) TI se s F (s) TI sW01 (s) KC (TI s 1)(TD s 1)es
(6-2)
过程控制系统
11
6.2 常规控制方案
而图6-5所示的PID控制方案的闭环传递函数分别为
KC (TI s 1)(TD s 1)es Y ( s) X (s) TI sW01 (s) KC (TI s 1)(TD s 1)es
第六章生产过程控制

工段调度:根据作业计划具体分配各个工作地、各班次的 任务,做好生产准备和供应工作。
生产调度方法、制度和工具
方法:调查研究、召开调度会议、日常检查
制度:调度会议制度、调度值班制度、调度报告制度、 现场调度制度、班前班后小组会议制度
工具:工票、加工路线单、调度板
第三节 生产进度控制
桂林电子工业学院管理系
生产进度控制的内容
1、投入进度控制:对产品或零部件开始投入的日期、产量、 品种以及原材料、毛坯、零部件投入提前期的控制。 2、出产进度控制:对产品或零部件出产日期、出产提前期、 出产量、出产均衡性和成套性的控制。
3、工序进度控制:对产品或零部件在生产过程中经历的每 道加工工序的进度进行的控制。
生产进度控制的方法
准时制控制法
JIT的由来和特征
“丰田生产系统”的开发——70年代末,在石油危机的冲
击下,以消除制造过程中的一切浪费为宗旨的准时化生产制, 首先在日本丰田汽车制造公司发展起来,故又称为“丰田方式 ” 特 征
准时化生产(JIT)——只在需要时生产需要的东西
看板(Kanban)——日语“信号”或“符号”的意思
2
看板控制系统
“看板”:永久性卡片,上面记录着:零件号码、零件名称、 标准盛装箱容量、前道工序、后道工序等信息。 看板管理运作方式:当盛装箱空了的时候,操作人员立即将 看板挂在箱子上,自己或由专门的搬运人员送往看板上标明 的前道工序;前道工序的操作人员立即开始生产;待生产出 的零件装满箱子后,自己或由立即专门的搬运人员送往看板 上标明的后道工序。看板的作用相当于生产指令与搬运指令 ,指示前道工序生产多少,生产什么。什么时候生产和送往 何处。 单卡系统与双卡系统:(P161) 单卡系统:零件加工与搬运均依据同一张看板卡; 双卡系统:将生产指令与搬运指令分别用生产看板卡与搬 运看板卡来表示。
高等过程控制-第6章解耦控制

即
Y1 s W11 s W12 s D11 s D12 s T 1 s Y s W s W s D s D s s 22 22 2 21 21 T 2
yi 可表示为 qij j
yr
yi ij j
r
yi j
yr
上式即为μj到yi这个通道的相对增益; 由各通道相对增益构成的矩阵∧则称为相对增益 矩阵。
1 y1 11 y2 21 y i i1 yn n1 2 12 22 i2 n2 j 1i 2 j ij nj n 11n 2n in nn
二、相对增益的求取 1、基本方法
按定义对过程的参数表达式进行微分,分
别计算出第一和第二放大系数,然后得到相对增
益矩阵。
2、第二放大系数的直接计算法 以双变量耦合系统为例
三、相对增益矩阵的特性
相对增益矩阵中每行(或每列)元素之和为1
四、相对增益所反映的耦合特性
(1)当通道的相对增益接近于1,例如1.2>λ>0.8,则 表明其它通道对该通道的关联作用很小,不必采取特别 的解耦措施. (2)当相对增益小于零或接近于零,说明使用本通 道调节器不能得到良好的控制效果。即这个通道的变 量选配不恰当,应重新选择。 (3)一般在0.3<<0.7或>1.5范围内时,表明系统 中存在严重的耦合,需进行耦合设计。
2. 三角矩阵法
三、前补偿法
前面所述的解耦方法是加入补偿装置,将对象传递矩 阵变为对角阵、三角矩阵等,从而实现解耦控制。而前补 偿法是不加任何补偿装置,将对象传递矩阵经变换后变成 对角矩阵、三角矩阵等,达到解耦的目的。
- 1、下载文档前请自行甄别文档内容的完整性,平台不提供额外的编辑、内容补充、找答案等附加服务。
- 2、"仅部分预览"的文档,不可在线预览部分如存在完整性等问题,可反馈申请退款(可完整预览的文档不适用该条件!)。
- 3、如文档侵犯您的权益,请联系客服反馈,我们会尽快为您处理(人工客服工作时间:9:00-18:30)。
t
过程控制系统与仪表 第6章
3.合理选择检测点,避免测量造成对象纯滞后τ0
pHC
贮酸槽 LT 图6.15 pH值控制系统图 LC
pHT
中和槽
l0
4.测量信号的处理
测量信号的校正与补偿、测量噪声的抑制、测 量信号的线性化处理。
过程控制系统与仪表 第6章
6.2.3.2执行器的选择 1.调节阀工作区间的选择 正常工况下,调节阀的开度应在15%~85%区 间。据此原则计算、确定控制阀的口径尺寸。
其中最关键的设计是:
过程控制系统与仪表 第6章
6.2.2被控参数与控制变量的选择
6.2.2.1被控参数的选择 被控变量 — 生产过程中希望借助自动控制保 持恒定值(或按一定规律变化)的变量。 合理选择被控变量,关系到生产工艺能否达 到稳定操作、保证质量、保证安全等目的。 被控变量的选择依据: 1、根据生产工艺的要求,找出影响生产的关 键变量作为被控变量
控制系统原理方框图
给定值 操作量
干扰 被控变量
+ -
控制器
执行器
对象
测量变送器
载热介质
控制系统工艺流程图
冷物料 热交换器
TC
TT 热物料
过程控制系统与仪表 第6章
6.2简单控制系统设计 1. 过程控制系统方案设计的基本要求 生产过程对过程控制系统的要求可简要归纳为 安全性、稳定性和经济性三个方面。
影响变量
被控变量
过程控制系统与仪表 第6章
对象特性对控制品质影响的分析:
1.过程(通道)静态特性对控制品质的影响
如图所示为单回路控制系统的等效框图。
F(s) Gf(s) X(s) + Gc(s) - Go(s) + Y(s)
+
Gc(s) —控制器的传递函数;
Go(s) —广义控制通道(包括执行器和变送器)的传递函数; Gf(s) —扰动通道的传递函数。
Go(s)
-
+
Y(s)
过程控制系统与仪表 第6章
G f ( s) G0 ( s )Gc ( s ) 将 Y ( s) X( s) F ( s) 1 G0 ( s )Gc ( s) 1 G0 ( s)Gc ( s)
代入系统偏差公式中:
E( s) X ( s) Y ( s)
Gf ( s ) 1 E( s) = X ( s) F ( s) = E x ( s) + Ef ( s) 1 + Gc ( s )Go ( s) 1 + Gc ( s )Go ( s)
过程控制系统与仪表 第6章
3、被控变量必须有足够大的灵敏度 被控变量必须灵敏,容易被测量。 4、选择被控变量时,必须考虑工艺合理性 上例中,选择塔内温度作被控变量,就是考 虑了工艺上,塔内压力是最佳分离效率控制系统的 被控变量。 上例中,若塔顶、塔底的产品纯度都分别设 置温控系统,会相互干扰,存在关联。因此,若采 用简单控制系统,只能设置一个温控系统,保证塔 顶或塔底一端的产品质量。
加热蒸汽流量(Q蒸)、 冷凝器冷却温度等。
过程控制系统与仪表 第6章
这些影响因素分为可控的和不可控的两大类:
回流量和蒸汽流量为可控因素 其它基本为不可控因素
TT
过程控制系统与仪表 第6章
在两个可控因素中,选蒸汽流量为操纵变量。 因为: 1、蒸汽流量对提馏 段温度影响比回流量 对提馏段温度影响更 迅速、更显著。 2、从节能角度来讲 , 控制蒸汽流量比控制 回流量消耗的能量要 小。
过程控制系统与仪表 第6章
被控参数y(t)受到设定信号x(t)和干扰信号f(t)的 共同影响: 干扰通道
G f ( s) G0 ( s)Gc ( s) Y ( s) X( s) F ( s) 1 G0 ( s)Gc ( s) 1 G0 ( s)Gc ( s)
控制通道
X(s) + + Gc(s) F(s) Gf(s)
F ( s)
K0越大,控制作用越强,稳态误差越小;
K0越大,被调参数对控制作用的反应越灵敏, 系统的闭环稳定性越低。
Kf越大,干扰作用越强,稳态误差越大。
故应选放大系数大的变量作为控制变量。
过程控制系统与仪表 第6章
2.过程(通道)动态特性对控制品质的影响
1)干扰通道动态特性对控制品质的影响
过程控制系统与仪表 第6章
2)控制通道动态特性对控制品质的影响
控制通道G01的时间常 数T01增大,使控制速度变 慢,最大偏差增大。
G02是控制、干扰共用 通道,T02不影响最大偏差
y yk(t) y2(t) y1(t) t
f GF
r
e
GC
GV
GO1 Gm
GO2
y
过程控制系统与仪表 第6章
过程控制系统与仪表 第6章
f1(t)通道惯性小,受干扰后被调参数变化速度 快;当控制作用见效时,被调参数已经变化较大— —造成动态偏差较大。 所以扰动进入系统的位置离被控参数检测点越 远,干扰对被控参数影响越小。
y yk(t) y yk(t) y(t) t t y(t) t y yk(t)
y(t)
过程控制系统与仪表 第6章
例1中,影响储槽液位的主要因素有:液体流 入量和。这两个变量影响力相当,显然,液体流出 量可控。故选液体流出量作为控制变量。
Qi
TT LC
h
Qo
过程控制系统与仪表 第6章
例2中,影响出口温度的主要因素有:载热介 质温度、载热介质流量、冷物料温度、冷物料流量 等。显然,载热介质流量影响力最大且可控。故选 载热介质流量作为控制变量。
过程控制系统与仪表 第6章
6.2.2.2控制变量选择 把用来克服干扰对被控变量的影响,实现控制 作用的变量称为控制变量或操纵变量。最常见的操 纵变量是介质的流量,也有以转速、电压等作为操 纵变量的。
TT h
LC
过程控制系统与仪表 第6章
控制变量的确定
被控变量选定以后,应对工艺进行分析,找出 所有影响被控变量的因素。在这些变量中,有些是 可控的,有些是不可控的。 在诸多影响被控变量的因素中选择一个对被控 变量影响显著且便于控制的变量,作为控制变量; 其它未被选中的因素则视为系统的干扰。
Tr Qr
载热介质 TC TT
Ti Qi 冷物料
热交换器
热物料
过程控制系统与仪表 第6章
例3中,若选择提馏段某块塔板(灵敏板)的 温度作为被控变量。那么,影响灵敏板温度T灵的因 素主要有:
进料的流量(Q入)、
进料的成分( x入)、 进料的温度(T入), 回流的流量(Q回)、 回流的温度(T回),
TT
Yf (s) G f ( s) 1 Gc (s)Go (s) F ( s) K f (To s 1) (To s 1)(Tf s 1) Ko Kc (T f s 1) F ( s)
干扰通道的惯性因子(Tf s+1)使干扰作用的 影响缓慢。 Tf 越大,干扰对被控变量的影响越缓慢,越有 利于控制。 干扰进入系统的位置离被控变量检测点越远, 则Tf 越大,控制时最大偏差越小。
过程控制系统与仪表 第6章
第6章 简单控制系统的设计与参数整定
6.1简单控制系统的结构与组成 指由一个测量变送器、一个控制器、一个控制 阀和一个对象所构成的单闭环控制系统。
第1位字母表示被控参数 后续字母表示仪表功能 TC
TT
LC
仪表符号标准
后续数字表示仪表序号
206
第1位数字表示工段号
过程控制系统与仪表 第6章
02
2τ
02
t
y
过程控制系统与仪表 第6章
因此,控制通道时间常数T0 小一些好。表明控 制变量对被控变量的影响迅速,有利于控制。 控制通道纯滞后τ0越小越好。 τ0会使控制时间 延长、最大偏差增大。 控制变量的选择原则: 1、控制通道应当放大系数大、时间常数小、纯 滞后越小越好。 2、控制变量应是工艺上允许控制的变量,并且 要考虑工艺的合理性与生产的经济性。
2、当不能用直接工艺参数作为被控变量时, 应选择与直接工艺参数有单值函数关系的间接工艺 参数作为被控变量。
例3 化工的精馏物纯 度控制系统 精馏工艺是利用被分
苯 苯—甲苯
离物中各组分的挥发温度
不同,将各组分分离。
如图将苯—甲苯混合
液进行分离。
甲苯
过程控制系统与仪表 第6章
苯 苯—甲苯
该精馏塔的工艺 要求是要使塔顶(或塔 底)馏出物达到规定的 纯度。按照被控变量的 选择原则1,塔顶(或 塔底)馏出物的组分应 作为被控变量。 但是,没有合适 的仪表在线检测馏出物 的纯度,则不能直接作 为被控变量。
过程控制系统与仪表 第6章
例:某控制系统中,干扰f1、f2、f3 分别在三个 位置进入系统。干扰离被控变量检测点越远,则干 扰通道的时间常数越大,对被控变量的影响越慢。
G 01 (s)G 02 (s)G 03 (s) Yf ( s) F3 ( s) 1 G0 ( s)Gc ( s )
G 02 ( s)G 01 (s) G01 ( s) F2 ( s ) F1 ( s ) 1 G0 ( s )Gc ( s ) 1 G0 ( s )Gc ( s )
甲苯
过程控制系统与仪表 第6章
只好在与馏出物的
纯度有单值关系的工艺
参数中,找出合适的变
苯 苯—甲苯
量作为被控变量,进行
间接参数控制。
经工艺分析发现,
塔内压力和塔内温度都
对馏出物纯度有影响。 需要对二者进行比较试
甲苯
验,选出一个合适的变 量。
过程控制系统与仪表 第6章
间接控制参数的确定
经试验得出,塔顶馏出物苯的浓度分别与压力 和温度有单值对应关系。(塔底馏出物甲苯也一样) 从工艺合理性考虑,选择温度作为被控变量。