颗粒剂、片剂、胶囊剂存在的问题及解决方法
药剂学-固体制剂第八章

②组分的密度:
若密度及粒度差异较大时:先将密度小(质轻)或粒径 大者先放入混合容器中,再放入密度大(质重)或粒 径小者,并选择适宜的混合时间。
③组分的粘附性与带电性
量大或不易吸附的药粉或辅料垫底,量少或易 吸附者后加入。
因混合摩擦而带电的粉末常阻碍均匀混合,通 常可加少量表面活性剂(如硬脂酸镁、十二烷 基硫酸钠)克服,也有人用润滑剂作抗静电剂。
2. 口腔用片剂 (1) 舌下片(Sublingual tablets)
舌下片是指至于舌下能迅速溶化,药物经舌下粘 膜的吸收而发挥全身作用的片剂。 可避免肝脏对药物的首过作用。如硝酸甘油片
(2) 口含片(toroches)
口含片是指含在口腔内缓缓溶化产生局部或全身治 疗作用的片剂。 常用于口腔及咽喉疾病的治疗。含片中药物是易溶 的,主要起消炎、杀菌、收敛、止痛或局部麻醉作 用,如复方草珊瑚含片
中药颗粒剂
西药颗粒剂
颗粒剂与散剂相比具有以下特点
(1)飞散性、附着性、团聚性、吸湿性等均较 少; (2)多种成分混合后用黏合剂制成颗粒,可防 止各种成分的离析; (3)贮存、运输方便; (4)必要时对颗粒进行包衣,根据包衣材料的 性质可使颗粒具有防潮性、缓释性或肠溶 性等。
二、颗粒剂的制备
物料 粉碎 过筛
§ 3.颗粒剂
一、概述
颗粒剂(Granules)是将原料药物与适宜的辅料混合而 制成的具有一定粒度的干燥颗粒状制剂。 一般按其在水中的溶解度分为可溶颗粒剂、混悬颗粒、泡 腾颗粒、肠溶颗粒、缓释颗粒和控释颗粒。 颗粒剂是可以直接吞服,也可以冲入水中饮服,应用和携 带比较方便,溶出和吸收速度较快。 在散剂(均匀混合粉末)基础上 ,加入黏合剂使粉末黏结成 更大的粒子。
散剂、颗粒剂、胶囊剂和丸剂知识点梳理.
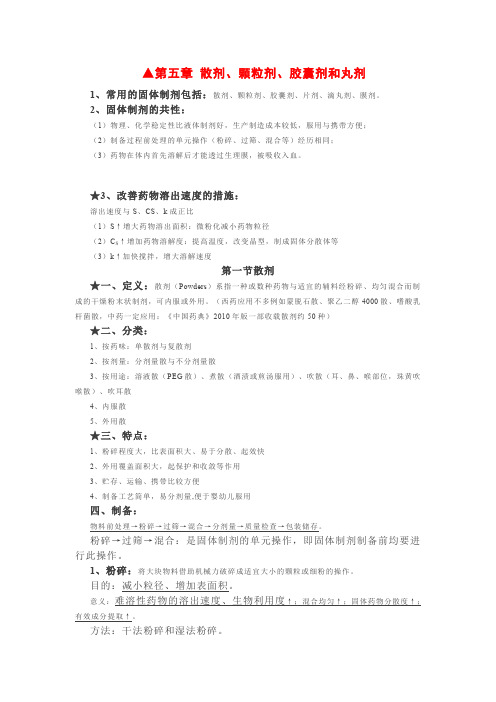
▲第五章散剂、颗粒剂、胶囊剂和丸剂1、常用的固体制剂包括:散剂、颗粒剂、胶囊剂、片剂、滴丸剂、膜剂。
2、固体制剂的共性:(1)物理、化学稳定性比液体制剂好,生产制造成本较低,服用与携带方便;(2)制备过程前处理的单元操作(粉碎、过筛、混合等)经历相同;(3)药物在体内首先溶解后才能透过生理膜,被吸收入血。
★3、改善药物溶出速度的措施:溶出速度与S、CS、k成正比(1)S↑增大药物溶出面积:微粉化减小药物粒径(2)C S↑增加药物溶解度:提高温度,改变晶型,制成固体分散体等(3)k↑加快搅拌,增大溶解速度第一节散剂★一、定义:散剂(Powders)系指一种或数种药物与适宜的辅料经粉碎、均匀混合而制成的干燥粉末状制剂,可内服或外用。
(西药应用不多例如蒙脱石散、聚乙二醇4000散、嗜酸乳杆菌散,中药一定应用:《中国药典》2010年版一部收载散剂约50种)★二、分类:1、按药味:单散剂与复散剂2、按剂量:分剂量散与不分剂量散3、按用途:溶液散(PEG散)、煮散(酒渍或煎汤服用)、吹散(耳、鼻、喉部位,珠黄吹喉散)、吹耳散4、内服散5、外用散★三、特点:1、粉碎程度大,比表面积大、易于分散、起效快2、外用覆盖面积大,起保护和收敛等作用3、贮存、运输、携带比较方便4、制备工艺简单,易分剂量,便于婴幼儿服用四、制备:物料前处理→粉碎→过筛→混合→分剂量→质量检查→包装储存。
粉碎→过筛→混合:是固体制剂的单元操作,即固体制剂制备前均要进行此操作。
1、粉碎:将大块物料借助机械力破碎成适宜大小的颗粒或细粉的操作。
目的:减小粒径、增加表面积。
意义:难溶性药物的溶出速度、生物利用度↑;混合均匀↑;固体药物分散度↑;有效成分提取↑。
方法:干法粉碎和湿法粉碎。
(1)干法粉碎法:药物干燥(水分<5%)后进行粉碎。
脆性或结晶性药物(撞击或锤式粉碎机);纤维性中药材(剪切式粉碎机)。
(2)湿法粉碎法:药物中加入适量水或其他液体实施研磨,又称为加液研磨法。
浅谈新版GMP下口服固体制剂(片剂、胶囊剂、颗粒剂)生产线的工艺设计

浅谈新版GMP下口服固体制剂(片剂、胶囊剂、颗粒剂)生产线的工艺设计摘要】《药品生产质量管理规范》(2010年修订)于2010年10月19日颁布,自2011年3月1日施行。
本文简要介绍了口服固体制剂在新版GMP下的工艺设计中的部分实例,使其在满足新版GMP下避免药品生产过程中污染、交叉污染以及混淆、差错的风险。
【关键词】新版GMP 口服固体制剂工艺设计[中图分类号]R197.32 [文献标识码]A [文章编号]1810-5734(2013)10-38-04引言新版GMP下对口服固体制剂的要求提高,对其减少污染从口服固体制剂设备角度来看,新版GMP中对粉尘处理提出了更高的要求。
结合实例对口服固体制剂生产线的设计作简要概述。
口服固体制剂典型生产工艺过程为合格原辅料经称量配料、粉碎、过筛、制粒、干燥、整粒、总混后得到干颗粒。
干颗粒或进入袋包间包装成颗粒剂产品,或进入胶囊生产区域制成相应规格的胶囊剂,或进入片剂生产区制成相应规格的片剂(非包衣片或包衣片),胶囊剂、片剂经内包装后,与颗粒剂产品一样各自分别去外包装、入库待检。
口服固体制剂典型生产工艺流程图见图1图1 口服固体制剂典型生产工艺流程图1 设计一般原则口服固体制剂生产线的设计原则应根据用户提供的URS,结合口服固体制剂的生产特征、批量大小以及用户的生产习惯确定。
一般来说,口服固体制剂各工序为间歇生产,需要通过半成品中间暂存来调节各工序之间的操作,按照销售的需求来排定生产计划。
通常可以按照以下方式进行厂房设计:1.1 按物料传送方式1.1.1 水平输送水平输送即是物料在水平方向同层输送,仅有设备垂直提升物料,局部垂直运输,整体水平输送。
1.1.2 垂直输送垂直输送即是垂直方向层间输送,输送方式又可以分为管道输送、层间提升机输送。
实例一运用层间提升装置,将物料在同层粉碎、过筛、制粒、混合后进入中间站暂存,再进入另一层压片(包衣)/胶囊填充、外包装。
这种形式适合于品种较多的间歇性生产方式。
药剂学概论-第六章-散剂、颗粒剂与胶囊剂

均匀混合的措施:
③混合时间(通过实验确定最佳混合时间)
④其他:含液体或易吸湿性的组分 如处方中有液体组分时,可用处方中其它组分 吸收该液体。常用吸收剂有磷酸钙、白陶土、 蔗糖和葡萄糖等。若有易吸湿性组分,则应针 对吸湿原因加以解决。
第三节 固体制剂的常用辅料
辅料:指生产药品和调配处方时所用的赋形 剂和附加剂。
固体制剂
常用的固体制剂包括:散剂、颗粒剂、胶囊剂、 片剂、滴丸剂、膜剂等
固体制剂的共性: (1)物理、化学稳定性比液体制剂好, 生产制造 成本较低,服用与携带方便; (2)制备过程前处理的单元操作经历相同; (3)药物在体内首先溶解后才能透过生理 膜,被吸收入血。
固体剂型的制备工艺流程图
物料 准备
②各组分的粒度与密度: 若密度及粒度差异较大时, 应将密度小(质轻)或粒径大者先放入混合容器 中,再放入密度大(质重)或粒径小者,并选择 适宜的混合时间。
等量递增法(配研法):药物 各组分的量相差悬殊时常用
方法:先取量少的组分及等量 的量大组分,同时置于混合器 中混合均匀,再加入与混合物 等量的量大组分混匀,如此倍 量增加直至加完全部量大的组 分为止。
不稳定药物的粉碎。
(四)粉碎设备
冲击柱式粉碎机 万能粉碎机
冲击、剪切、摩擦及 物料间的撞击
适用于性质不同的
物料。球因磨粉碎机过程
会发热,故不适用
万
于含挥发性成分、
能
遇热发黏的物料
粉
碎
机
锤击式粉碎机
球磨机示意图
适用于物料微粉碎,贵重物料、无菌粉碎、干湿法粉碎。 粉碎时间较长,粉碎效率低
振动磨
2、设备类型的影响(混合机的形状及尺寸,内 部插入物,材质及表面情况等。)
制剂生产过程中常见问题和处理方法

制剂生产过程中常见问题和处理方法1. 异常物质残留在制剂生产过程中,常常会出现一些异常物质的残留问题。
这些异常物质可能来源于原料杂质、生产设备、环境污染等。
为了保证制剂的质量和安全性,需要及时发现和处理这些问题。
处理方法:•严格控制原料的使用,确保原料的质量符合相关标准。
•定期对生产设备进行清洁和维护,防止污染物附着和残留。
•加强环境监测和控制,防止环境污染对制剂生产造成影响。
•建立严格的监管和管理制度,规范制剂生产过程中的各项操作。
2. 产品稳定性问题制剂的稳定性是制剂生产中的一个重要问题。
制剂的稳定性问题会直接影响产品的质量和有效期。
常见的制剂稳定性问题包括药物降解、物理性质变化等。
处理方法:•优化制剂配方,选择稳定性良好的原料。
•对不稳定的原料进行预处理,降低其对制剂稳定性的影响。
•使用适当的包装材料,保护制剂免受外界环境的影响。
•控制制剂的储存条件,避免光照、温度、湿度等因素对制剂产生不利影响。
3. 配方调整问题在制剂生产过程中,可能会出现需要对配方进行调整的情况。
配方调整可能涉及到原料的替换、比例的调整等。
正确处理配方调整问题对确保产品的质量和稳定性非常重要。
处理方法:•在调整配方之前,要充分了解原料的性质和作用,确保新的配方能够达到预期的效果。
•对配方调整进行严格的试验和验证,确保调整后的配方能够满足产品的要求。
•在调整配方之后,要进行充分的监测和评估,及时发现问题并采取相应的措施进行处理。
4. 生产设备故障生产设备故障是制剂生产过程中常见的问题之一。
设备故障可能会导致生产过程的中断和产品质量问题。
及时发现和处理设备故障对保证生产进度和产品质量具有重要意义。
处理方法:•建立设备维护和保养计划,定期对生产设备进行检查和维修,预防潜在的故障。
•在生产过程中要严格按照操作规程操作设备,避免不当操作导致设备故障。
•对设备故障进行及时的排除和修复,确保生产过程的连续性和稳定性。
5. 工艺参数偏差在制剂生产过程中,工艺参数的偏差可能会对产品的质量和稳定性产生影响。
小试,中试到放大生产的常见问题及解决

小试,中试到放大生产的常见问题及解决把处方筛选和工艺参数筛选工作做充足,在生产出现问题时能够准确的判断解决问题的方向。
(例如关键辅料的加入量从少到多对制剂的影响;关键工艺参数(温度,时间等)的可行性范围,超出范围下限会怎样影响制剂,超出上限会怎样影响制剂等。
)充分了解和掌握原辅料的性质,熟悉小试和生产的设备(小试和生产设备原理最好一致)。
1.原料药待收集2.中药提取待收集3. 片剂片剂的制备方法主要有湿法制粒压片法、干法制粒压片法、粉末直接压片法这三种,最常用的是湿法制颗粒压片法。
主要工艺步骤有粉碎、混合制粒、干燥、整粒、混合、压片和包衣。
粉碎:一般不会出现问题粘合剂:粘合剂溶液的加入量,从小试到放大,比例是更大还是更小?例如,小试粘合剂溶液用量是粉末量的10%,放大10倍后,一般是12%,还是8%?因为制粒系统或参数不一致,所以达到相应润湿度,需要溶液不一样,一般放大后需量略小。
如果是粉末添加,建议10%不要改变,根据制粒情况适量变动润湿剂的用量。
否则处方变动,对后续影响较大。
混合制粒:这是比较关键的步骤,也经常出现问题,首先要测试能够混合均匀的时间,混合不均匀,含量会不合格;其次,粘合剂润湿剂的加入量,和小试不是单纯的加倍关系,要摸索,加少了可能会造成细粉多,不成粒,流动性不好,加多了制备的颗粒太硬影响压片,或者物料结块影响收率;机器的搅拌和剪切速度以及时间要摸索,小试中得不到这些参数,这些参数也影响所制备颗粒的质量。
对于制粒完过筛,我遇到过特别腻筛的,因为物料本身原因。
粘合剂是水,比例是物料重的45%(经比例摸索得出较好的),制粒后过筛在中试放大特别堵(正常的24目),解决方式为,先过10目筛把物料颗粒整碎一点,烘干(水分3%以下)后再用24目整粒,效果良好。
目前做的缓控释制剂,由于本身API有液体,加入乙基纤维素后比较黏,用做粘合剂。
小试处方以筛完,放大中试怕粘合剂损失过多,还未找到稳妥的办法。
颗粒剂和胶囊剂制剂通则以及质量控制

1、胶囊剂定义:胶囊剂系指将饮片用适宜方法加工后,加入适宜辅料填充于空心胶囊或密封于软质囊材中的制剂,胶襄剂分硬胶囊剂、软胶囊剂(胶丸)和肠溶胶囊剂,供口服用。
1。
1.硬胶囊剂系指将提取物、提取物加饮片细粉或饮片细粉与适宜的辅料制成均匀粉末、细小颗粒、小丸、半固体或者液体等,填充于空心胶囊中的胶囊剂。
1.2.软胶囊剂系指将提取物、液体药物或与适宜辅料混匀后用滴制法或压制法密封于软质囊材中的胶囊剂.1。
3.肠溶胶囊剂系指不溶于胃液,但能再肠液中崩解或释放的胶囊剂。
1.4.硬胶囊剂的特点:可掩盖药物的不良臭味;药物的生物利用度高;可弥补其他固体制剂的不足;提高药物的稳定性;延缓药物的释放;可是胶囊具有各种颜色和印字,有利于识别且外表美观。
1.5胶囊剂的制法1.5.1。
硬胶囊的制备①空胶囊的囊材主要成型材料是明胶。
以骨骼为原料制成的骨明胶质坚性脆,以猪皮为原料制成的猪皮明胶可塑性好,以骨、皮混合明胶较为理想。
为增加其坚韧性与可塑性,可加入适量的甘油、山梨醇、CMC-Na、HPC、油酸酰胺磺酸钠等;为减小其流动性、增加胶冻力,可加增稠剂琼脂等;对光敏感的药物,可加遮透剂二氧化钛(2%~3%);为增加美观,便于鉴别,可加入柠檬黄、胭脂红等食用染料做着色剂;为防止胶囊霉变,可加入防腐剂尼泊金等。
必要时亦可加入芳香性矫味剂.当然,不是任一种空胶囊都必须有以上组分,而应根据目的要求选择.②空胶囊的制备流程溶胶→蘸胶(制坯)→干燥→脱模→截割→(囊体与囊帽)套合。
一般在空气洁净度100000级,温度10~25℃,相对湿度35%~45%的环境条件下,由自动化生产线完成。
空胶囊含水量14%~15%为宜,除可用各种颜色区别外,还可在每个空胶囊上印字,以便识别。
全自动生产空胶囊的机器,由自动浸、转、干燥、剥落、整理和联结胶囊的机械组成,并使用电子计算机进行监测控制。
电子分选机取代了原来用眼检查剔除废品的工作。
③空胶囊的质量空胶囊的成品,应作必要的检验,以保证其质量。
颗粒剂
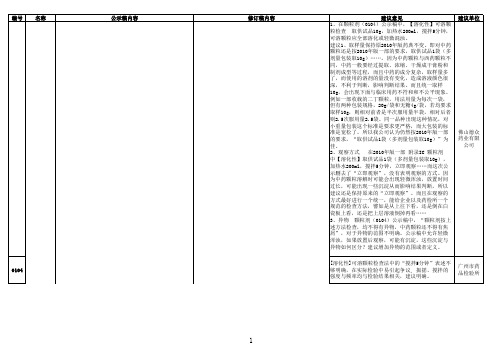
泡腾颗粒检查法 取供试品3袋,将内容物分别转移至盛有200ml水的烧杯中,水温为15~25℃,应迅速产生气体而呈泡腾状,5分钟内颗粒均应完全分散或溶解在水中。
颗粒剂按上述方法检查,均不得有异物,中药颗粒还不得
有焦屑。
混悬颗粒以及已规定检查溶出度或释放度的颗粒剂可不进
行溶化性检查。
泡腾颗粒检查法 取供试品3袋,将内容物分别转移至盛有200ml水的烧杯中,水温为15~25℃,应迅速产生气体而呈泡腾状,5分钟内颗粒均应完全分散或溶解在水中。
颗粒剂按上述方法检查,均不得有异物,中药颗粒还不
得有焦屑。
混悬颗粒以及已规定检查溶出度或释放度的颗粒剂可不
进行溶化性检查。
化性应符合规定。
溶化性应符合规定。
- 1、下载文档前请自行甄别文档内容的完整性,平台不提供额外的编辑、内容补充、找答案等附加服务。
- 2、"仅部分预览"的文档,不可在线预览部分如存在完整性等问题,可反馈申请退款(可完整预览的文档不适用该条件!)。
- 3、如文档侵犯您的权益,请联系客服反馈,我们会尽快为您处理(人工客服工作时间:9:00-18:30)。
颗粒剂、片剂、胶囊剂存在的问题及解决方法颗粒剂、片剂、胶囊剂存在的问题及解决方法本文作者为北京中医药大学生药系研究生王建辉一.颗粒剂中药颗粒剂也称中药冲剂,指药材的提取物加适量赋型剂或部分药材细粉制成干燥顺粒或块状的内服药剂。
是在汤剂和糖浆剂的基础上发展起来的一种新剂型,一般按溶解性分为可溶性冲剂、混悬性冲剂和泡腾冲剂。
它保持了汤剂作用迅速,又克服了汤剂临用时煎煮不便的缺点,且口感好、体积小、服用、贮藏、运输方便。
但容易吸潮,由于工艺原因造成颗粒不均,色泽不均,它直接影响着顺粒剂质量和外观,现主要讨论一下色泽不均问题:1.如直接制粒时,稠浸肴与药粉及辅料棍合不均匀,浸膏不能均匀地湿润辅料,这时会出现色泽不一现象,为解决这一问题,经过多次实验证明,首先要把药粉及辅料充分混合均匀,再加稠浸青混合均匀,制粒时如色泽不均可加适量浓度乙醉调整,如再不均匀,制粒时把湿颗粒再次过筛,即可得外观颜色一致颗粒。
2.如要二次制粒是将浸青和药粉、辅料拌膏干燥粉碎的药粉进行制粒,制出的湿颗粒由于加乙醇浓度的不同,有时会出现大颗粒,烘干后颗粒大,整粒后颗粒不均匀。
解决这一方法是在湿粒未干时进行整粒.然后均匀喷洒些乙醇闷上后再烘干。
颗粒大,色泽深是由于乙醇浓度低、量大造成的。
如注意到以上几点可使颗粒均匀。
3.制备颗粒剂所用药粉或辅料粒度过大,可使颗粒色泽不一,解决方法是将药粉、辅料过筛,通常为100目筛为宜,这样可有效解决这一问题。
此外,由于原材料不同,药材质量、产地、采时、用药部位等方面可影响每批质量及外观,所以要尽可能保持原材料一致,不要轻易更换进药产地等方面。
在提取过程中每批要按同一处方投入(在没有特殊情况下),浸泡时间、加水量、温度、每批浓缩出的相对密度和体积都要保持一致。
所用辅料量每批要一致,否则也会出现颜色深浅不同的现象。
二.片剂随着中国几千年历史的发展,尤其是近年来中药及其制剂的广泛使用中药已成为独具特色的治病良药。
但是,中药片剂在生产中也存在着不少问题,现对这些问题及其解决方法作一综述。
1 生产工艺糖衣片的常规打光方法是在闷锅结束后,打蜡粉加入片子中(每万片用量3~5g),开动糖衣锅打光,一般需15min完成。
但生产时,常因一些因素掌握不好而导致打光困难,甚至被迫停止。
报道可改用“布袋-糖衣锅”法打光,该法只需5~10min,且应用广泛。
生产复方冬凌草含片,老工艺是将冬凌草提取液经减压浓缩到稠膏状后,直接与其他浸膏混合置烘箱中高温烘干,新工艺将提取液经减压浓缩至稠膏状后,溶解在乙醇中,制粒前喷入干粉中,制粒后在鼓风机中低温烘干。
通过对比发现,采用新工艺制得的含片中冬凌草甲素含量比老工艺制得者高,临床疗效更显著。
2 崩解片剂崩解迟缓是影响片剂质量的主要因素之一。
据报道片剂崩解迟缓主要是受主药!赋形剂和生产过程的影响[3]"最佳解决办法是:加入崩解作用较强的崩解剂,如2%~5%羟甲基淀粉钠;在保证片剂成品质量的前提下,可按一定比例与崩解良好的颗粒混合均匀压片;先加入一定量的崩解剂,然后再与崩解良好的颗粒混合"另外,改进制粒方法也可改善片剂的崩解性能,如紫花杜鹃片(浸膏在颗粒中占80%)分别用混合机与喷雾制粒,两种片剂的崩解时限分别为60,20~30min;感冒清片(浸膏在颗粒中占40%)用上述两方法制粒,两种片剂的崩解时限分别为55,23min。
结果表明,改用喷雾制粒压片,崩解时限明显缩短,产品质量提高。
3 包衣在气温较高的条件下,片芯易失水,且由于受热膨胀,导致片子的爆裂。
一般认为,糖衣片所发生的龟裂砚象主要是包衣层中搪层和有色搪层水份挥发引起的,然面过份干燥还会析出糖的结晶,而形成龟裂,所以当羞片水份在30%-50%时,包衣温度在50℃以下干操,不会导致片芯的膨胀,低温放置也不会龟裂。
由于包衣时衣层的厚度、颜色不均匀等原因造成片面花斑、片面高低不平、光亮度差异等外观质量问题也很常见。
处理方法是将返工片去蜡后包上一层薄粉层,然后上糖层、色层,再打光(此法对片重为0.25g以下的合适);或者将要处理的药片置包衣锅内吹热使之升温,然后用加热的无色浆液滚动摩擦数分钟后,吹热风进行干燥,如此4~6次即可将蜡遮盖,使颜色变浅,片面更平,再上若干遍色浆,即可打光。
包糖衣时素片要压得好,且压好的素片也不能直接包糖衣,一定要全部放入石灰缸(或干燥器)中吸潮,24h后再行包衣。
中药片剂在包糖衣过程中经常出现烂片现象。
解决的办法是用倍量浓度的明胶包隔离层,待片子表面均匀润湿后,立即加足量滑石粉,使片子表面完全覆盖并吸收多余水分,然后重复1次,在低温下(75℃左右)将片子烘干,这样制得的素片在包衣时不会出现烂片。
一些富含油性及纤维性较强的全粉末或半粉末中药片剂,常因硬度不够在包糖衣过程中,特别是在包第一层时碎裂。
解决的办法:用小型糖衣锅包,并且用50%~55%的糖浆包第一层粉层,当第一层粉层包好后,后面的操作就不会发生碎裂。
4 辅料有的片剂中含生药较多,用提取浸膏与15%的淀粉浆制粒、压片,但片剂硬度不够,包衣过程中常出现掉硅、裂片、脱帽等现象。
实验表明,用3%的羟丙基甲基纤维素(HPMC)乙醇溶液代替15%的淀粉浆,制粒、压片,使素片质量得到明显提高。
新型药用辅料粉末状纤维素同目前常用的玉米淀粉及微晶纤维素等相比,具有性能优良,性质稳定,应用广泛,使用安全等特点,尤其对于不同类型中药片剂均有较好的改善崩解及溶出作用。
实验表明,葛根浸膏片随着羟甲基淀粉钠用量的增加,崩解时间缩短,葛根素的溶出加快,药物吸收好,提高了生物利用度。
对甲壳素在中药片剂中的崩解性能考察表明,以甲壳素为崩解剂制备肝炎宁和穿心莲浸膏片,并与以淀粉!CMC-Na、L-HPC及微晶纤维素为崩解剂的片剂进行比较,甲壳素的崩解性能最好。
聚羧乙烯具有良好的可压性和粘合性,可解决某些中药片剂的松片!裂片等问题,如在丹参浸膏粉中添加聚羧乙烯制片,片剂硬度随聚羧乙烯用量增加而增大,素片包衣成膜性明显改善,使原本难以进行薄膜包衣的中药浸膏片能够进行薄膜包衣。
5 溶出近年来,许多报道反映,不同厂家生产的同一品种中药片剂,甚至同一厂家生产的不同批号的中药片剂的溶出速率存在极显著差异。
改进中药片剂溶出速率方面的措施,如添加促进崩解,有助溶、增溶作用的辅料。
在盐酸黄连素片中分别加入羧甲基淀粉钠、低取代羟丙基纤维素,结果两种片剂的溶出度参数间差异极显著,羧甲基淀粉钠明显优于低取代羟丙基纤维素。
6 松片松片是片剂生产过程中常见的实际问题,因中药品种繁多,成分复杂,且各品种的特性各异,松片问题则更为突出,现将其克服方法简述如下:6.1提高药材的粉碎度,使原生药粉末的粒度在100目至120目之间,这样就可较好地克服生药原粉的弹性,解决松片的问题。
6.2适当调整生药粉末与浸膏的比例6.3选用粘合力较强的粘合剂,选用粘合力较强的枯合剂,如淀粉明胶浆、炼蜜等,并在不影响崩解度的情况下,适当增加粘合剂的用量。
6.4中药制粒后,颗粒中细粉不可太多,当细粉超过30%时,即出现松片和裂片,因为压片时细粉阻碍了颗粒中气体的逸出,留在片内,一旦压力消失,气体膨胀,即产生松片和裂片。
此时,补救的办法是用80目筛筛取部分细粉,重新制粒压片。
6.5增加颗粒的流动性,一些中药片剂,由于颗粒疏松,流动性不好,填充于模孔中的颗粒量不足而引起松片,此时,可增加润滑剂的用量或几种润滑剂配合使用,以增加颗粒的流动性,或加人少量氢氧化铝和微粉硅胶等助流剂克服松片。
三、胶囊剂胶囊剂由于具有可掩盖药物的苦味、臭味及美观、易服、崩解快、溶出度高、吸收好、生物利用度高、可定时定量释放药物与可多种途径给药等优点,已经越来越受到医家的推崇和患者的喜爱。
随着用途的广泛,用量的增大,其质量问题也越来越受到人们的关注。
1生产过程中可能出现的质量问题及其对策1.1水分升高水分升高的原因是生产场所的空气湿度太大或保管不当而使物料或胶囊受潮引起。
其对策为:1.1.1控制操作室的温度在25℃左右,相对湿度在30%~45%的范围内。
1.1.2对吸湿性强的药物加入适宜的抗潮剂。
1.1.3将配好的物料或填充好的胶囊密封保管好。
1.2胶囊瘪头或锁口不到位:胶囊填充机的压力太大易引起胶囊瘪头,压力太小则会使锁口不到位。
对策为调整胶囊填充机的压力,使其符合生产要求。
1.3错位太多1.3.1按贮存条件保管好胶囊壳,以防止其变形。
1.3.2检查胶囊填充机的顶针是否垂直,如不垂直,应予调正。
1.3.3检查胶囊盘(半自动机)或冲模(全自动机)是否磨损;如过于残旧,则应更换胶囊盘或冲模。
1.4装量差异不合格1.4.1检查胶囊填充机运作是否正常,如出现故障,应及时排除。
1.4.2检查胶囊填充机的落料位置是否处于最佳位置;否则,调整之。
1.4.3检查胶囊填充机的转速是否处于生产该品种的最佳状态;否则,调整之。
1.4.4检查胶囊填充机的螺杆或冲杆是否磨损;如磨损,更换之。
1.4.5生产中应及时定量加料,以保证装量的稳定性。
1.4.6检查粉末(颗粒)的粒度是否符合工艺要求,如不符合,重新按规定整粒、过筛、混匀。
1.4.7检测粉末(颗粒)是否受潮;如受潮,重新按工艺要求烘干。
1.4.8检查配料工序是否严格按处方投料、按工艺要求生产;否则,采取适当的补救措施。
1.4.9调整处方或工艺,使其符合生产要求。
1.5崩解时限或溶出度不合格1.5.1选用符合药用要求的胶囊壳。
1.5.2了解原料本身的溶出度或崩解情况,以更好地进行处方配伍。
1.5.3检查配料工序是否按处方和工艺要求生产。
1.5.4调整处方或工艺。
1.6交叉污染1.6.1更换品种时,彻底清洗生产场所、机械、生产用具。
1.6.2对进入操作室的人和物要进行净化处理。
1.6.3为防止生产原料的污染,必须贮存在与其它物料明显分开的地方。
1.6.4操作室与邻室及外界的静压差应符合GMP的要求。
1.7微生物污染在生产过程中一经发现药物半成品或成品受微生物污染并造成药物卫生学不合格时,应立即停止该品种、批次的生产,并杜绝进入下一工序。
对该生产场所必须进行消毒灭菌,经再验证符合生产要求后方可继续使用。
对仅受霉菌污染且微量超标的少量粉末(颗粒),可用加10%左右乙醇闷透的方法进行灭菌。
对受霉菌污染程度大、或受细菌或其它杂菌污染超标的半成品或成品,可用60Co辐照的方式进行灭菌。
为防止药物在生产过程中受微生物污染,可采取以下措施进行预防:1.7.1所用原辅料、胶囊壳卫生学必须符合规定。
1.7.2使用的工具、容器应清洁无异物。
1.7.3定期进行室内消毒灭菌操作。
1.7.4对进入操作室的人和物必须进行净化处理。
1.7.5操作人员应按规定穿戴好工作服、帽、卫生手套,不得用手直接接触药物。