多片钢板弹簧预应力计算
钢板弹簧模拟分析技术-一汽

钢板弹簧模拟分析技术潘淑华(中国第一汽车集团公司技术中心基础研究部吉林长春 130011)摘要:本文主要针对变截面钢板弹簧,进行强度及刚度分析。
考虑螺栓预紧而产生的预应力及满载、过载应力,及相应的刚度曲线变化情况。
探索少片变截面钢板弹簧的计算分析方法。
关键词:钢板弹簧预应力应力强度刚度1、概述钢板弹簧是汽车系统主要承载件之一,其性能的好坏直接影响整车的各种性能。
如何设计性能合理的钢板弹簧,对整车承载能力的提高有着极大的影响。
合理的钢板弹簧设计依赖对其各种性能的分析研究。
钢板弹簧是一种非线性大变形的结构,各片之间都存在着接触、摩擦,并且其总成在工作过程中始终存在螺栓夹紧预应力。
合理的模拟各片之间的接触、摩擦及螺栓预紧而产生的预应力,是钢板弹簧强度及刚度分析的关键。
2、计算对象国内某车的变节截面少片钢板弹簧(见图一),国外某车主副簧一体的变节截面少片钢板弹簧,(见图二)。
图一:国内某车的板簧模型图图二:国外某车的板簧模型图3、计算方法利用ABAQUS的STANDARD求解器3.1板弹簧模型的建立用非线性技术进行有限元分析时,单元模型类型及单元尺寸的选取直接影响计算的精度。
本计算应用减缩积分单元可以避免剪切自锁。
片间采用主从接触单元。
3.2计算过程的模拟1、螺栓预紧过程通过加螺栓预紧位移实现预应力的过程。
2、钢板弹簧满载工作过程根据设计要求,给出满载载荷。
3、钢板弹簧过载工作过程根据设计要求,给出过载载荷。
4、钢板弹簧卸载工作过程根据试验或设计要求进行卸载4、计算结果通过计算过程的准确模拟可以得到比较合理的应力计算结果。
每一步的应力结果都包括预应力在内。
应力结果完全可以评价板簧的强度情况。
计算可提供应力分布图及刚度曲线。
4.1强度结果以下是两种板簧的应力计算结果。
1、国内某钢板弹簧的计算应力分布情况图三:是第一片下预应力结果66.33(MPa)图四:第二片上下预应力结果14.97(MPa)图五:是第三片上预应力结果75.15 (MPa)图六:总成预应力75.15(MPa)发生在第三片上图七:满载应力:591.2 (MPa)图八:超载应力:1107MPa2、国外某钢板弹簧的计算应力分布情况图九:第一片预应力结果105.4MPa 图十:第二片预应力结果:58.3MPa图十一:第三片预应力结果:172MPa 图十二:第四片预应力结果:64MPa图十三:预应力状态最大应力:172MPa 图十四:总成达到要求位移状态时的应力:812 MPa 卸载的应力分布跟加载的相似,不再给出应力分布图。
钢板弹簧设计说明书
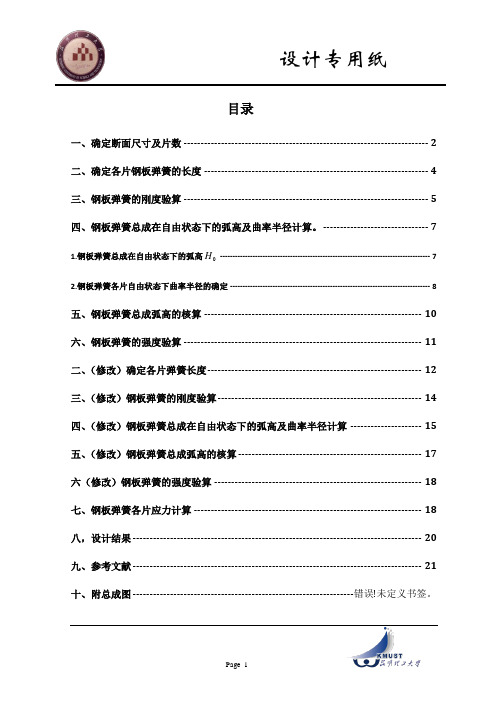
目录一、确定断面尺寸及片数 ------------------------------------------------------------------------ 2二、确定各片钢板弹簧的长度 ------------------------------------------------------------------ 4三、钢板弹簧的刚度验算 ------------------------------------------------------------------------ 5四、钢板弹簧总成在自由状态下的弧高及曲率半径计算。
------------------------------- 7H ------------------------------------------------------------------------------------ 71.钢板弹簧总成在自由状态下的弧高02.钢板弹簧各片自由状态下曲率半径的确定 -------------------------------------------------------------------------------- 8五、钢板弹簧总成弧高的核算 ---------------------------------------------------------------- 10六、钢板弹簧的强度验算 ---------------------------------------------------------------------- 11二、(修改)确定各片弹簧长度--------------------------------------------------------------- 12三、(修改)钢板弹簧的刚度验算 ------------------------------------------------------------ 14四、(修改)钢板弹簧总成在自由状态下的弧高及曲率半径计算 --------------------- 15五、(修改)钢板弹簧总成弧高的核算 ------------------------------------------------------ 17六(修改)钢板弹簧的强度验算 ------------------------------------------------------------- 18七、钢板弹簧各片应力计算 ------------------------------------------------------------------- 18八,设计结果 ------------------------------------------------------------------------------------- 20九、参考文献 ------------------------------------------------------------------------------------- 21十、附总成图 ----------------------------------------------------------------- 错误!未定义书签。
汽车多片簧的设计计算及软件开发
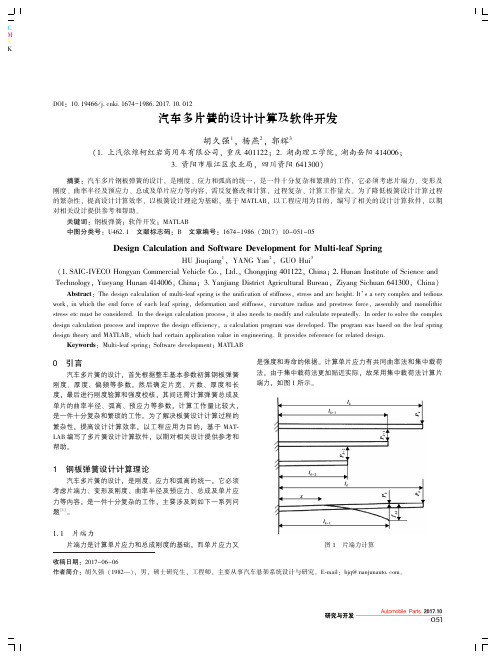
收稿日期:2017-06-06作者简介:胡久强(1982 ),男,硕士研究生,工程师,主要从事汽车悬架系统设计与研究㊂E⁃mail:hjq@nanjunauto com㊂DOI:10 19466/j cnki 1674-1986 2017 10 012汽车多片簧的设计计算及软件开发胡久强1,杨燕2,郭辉3(1 上汽依维柯红岩商用车有限公司,重庆401122;2 湖南理工学院,湖南岳阳414006;3 资阳市雁江区农业局,四川资阳641300)摘要:汽车多片钢板弹簧的设计,是刚度㊁应力和弧高的统一,是一件十分复杂和繁琐的工作,它必须考虑片端力㊁变形及刚度㊁曲率半径及预应力㊁总成及单片应力等内容,需反复修改和计算,过程复杂㊁计算工作量大㊂为了降低板簧设计计算过程的繁杂性,提高设计计算效率,以板簧设计理论为基础,基于MATLAB,以工程应用为目的,编写了相关的设计计算软件,以期对相关设计提供参考和帮助㊂关键词:钢板弹簧;软件开发;MATLAB中图分类号:U462 1㊀文献标志码:B㊀文章编号:1674-1986(2017)10-051-05DesignCalculationandSoftwareDevelopmentforMulti⁃leafSpringHUJiuqiang1,YANGYan2,GUOHui3(1 SAIC⁃IVECOHongyanCommercialVehicleCo.,Ltd.,Chongqing401122,China;2 HunanInstituteofScienceandTechnology,YueyangHunan414006,China;3 YanjiangDistrictAgriculturalBureau,ZiyangSichuan641300,China)Abstract:Thedesigncalculationofmulti⁃leafspringistheunificationofstiffness,stressandarcheight.It saverycomplexandtediouswork,inwhichtheendforceofeachleafspring,deformationandstiffness,curvatureradiusandprestressforce,assemblyandmonolithicstressetcmustbeconsidered.Inthedesigncalculationprocess,italsoneedstomodifyandcalculaterepeatedly.Inordertosolvethecomplexdesigncalculationprocessandimprovethedesignefficiency,acalculationprogramwasdeveloped.TheprogramwasbasedontheleafspringdesigntheoryandMATLAB,whichhadcertainapplicationvalueinengineering.Itprovidesreferenceforrelateddesign.Keywords:Multi⁃leafspring;Softwaredevelopment;MATLAB0㊀引言汽车多片簧的设计,首先根据整车基本参数初算钢板弹簧刚度㊁厚度㊁偏频等参数,然后确定片宽㊁片数㊁厚度和长度,最后进行刚度验算和强度校核,其间还需计算弹簧总成及单片的曲率半径㊁弧高㊁预应力等参数,计算工作量比较大,是一件十分复杂和繁琐的工作㊂为了解决板簧设计计算过程的繁杂性,提高设计计算效率,以工程应用为目的,基于MAT⁃LAB编写了多片簧设计计算软件,以期对相关设计提供参考和帮助㊂1㊀钢板弹簧设计计算理论汽车多片簧的设计,是刚度㊁应力和弧高的统一,它必须考虑片端力㊁变形及刚度㊁曲率半径及预应力㊁总成及单片应力等内容,是一件十分复杂的工作,主要涉及到如下一系列问题[1]㊂1 1㊀片端力片端力是计算单片应力和总成刚度的基础,而单片应力又是强度和寿命的依据㊂计算单片应力有共同曲率法和集中载荷法,由于集中载荷法更加贴近实际,故采用集中载荷法计算片端力,如图1所示㊂图1㊀片端力计算㊀㊀计算时,根据相邻片之间接触点变形相等的条件,可以建立整副板簧的平衡方程组,如公式(1)所示:fAk-fBk=fCk-fDkPkl3k2EIkηAk-Pk+1l3k+13EIkηBk=Pk+1l3k+13EIk+1ηCk-Pk+2l3k+23EIk+1ηDk{(1)式中:fAk为力作用于lk片端部,中部某断面的变形;fBk为力作用于lk片中部,相应断面的变形;fCk为力作用于lk+1片端部,端部处的变形;fDk为力作用于lk+1片中部,端部处变形;Pk为第k片的片端力;l为二分之一片长;E为材料的弹性模量;η为计算系数,分别为公式(2)所示:ηAk=12(lk+1/lk)2[3-(lk+1/lk)]ηBk=ηCk=1ηDk=12[3(lk+1/lk+2)-1]ìîíïïïïï(2)1 2㊀变形及刚度弹簧总成端部的变形,对于对称弹簧来说,就是弹簧总成的变形[2]㊂有了弹簧在非夹紧状态下的总成变形,就可计算出弹簧总成的自由刚度和夹紧刚度㊂图2为推求整副板簧在满载载荷P的作用下端部变形示意图㊂图2㊀弹簧总成变形根据莫尔定理,弹簧端部在力P作用下的变形为:f=ʏl10M0MEIxdx=ʏa2a1+ʏa3a2+ʏanan-1=ðnk=1ʏak+1akPa3k+13EIk-Pa3k3EIkéëêùûú㊀a1=0(3)由此,则整副板簧的自由刚度和夹紧刚度为:c0=2Pf=6Eα/ðnk=1a3k+1-a3kIkæèçöø÷cJ=c0(0 95+2S/L){(4)式中:α为修正系数,可取0 9 0 92;参数ak=l1-lk,an+1=l1;Ik为惯性矩;S为夹紧长度;L为主片伸直长度㊂1 3㊀单片曲率半径计算及预应力分配钢板弹簧设计的重要环节和内容就是:在已知总成曲率半径R0㊁各片厚度hk㊁宽度b㊁长度Lk的情况下,确定各片预应力σ0k和曲率半径Rk㊂1 3 1㊀各片预应力的确定预应力σ0k的确定,实则为弯矩Mk的确定,推荐采用弯矩曲线图法来确定各片弯矩和预应力[3]㊂图3中纵坐标代表弯矩Mk,横坐标表示各片的序号k㊂当在横坐标上取适当长度代表总片数n,并将n等分,那么各等分点1㊁2㊁ ㊁k㊁ ㊁n便表示各片的位置,aᶄ表示a的整数部分,相应的纵坐标就代表各片预应力的弯矩㊂图3㊀弯矩曲线图图中M1㊁a㊁θ㊁Ma+2是待求参数,当确定了这些参数,弯矩图曲线就确定了㊂有了弯矩曲线图,就可以方便地计算出各片的弯矩和预应力,待求参数由计算公式(5)确定:M1=(3000-σ静)W1a=n/2-1tanθ= EIaᶄ+2δaᶄ+2R0+ðaᶄ+2i=1hi-1()2Maᶄ+2=AM1-Btanθìîíïïïïïï(5)式中:厚度h1为主片厚度;L1为主片长度;fc为满载静挠度;δ为挠度增大系数; 为非单一圆弧系数,各片等厚时取 =1 06,不等厚时取 =1 2;其余各计算参数由公式(6)计算确定:A=aᶄ[1-(aᶄ-1)/(n-4)]n-[aᶄ+1 5+2/(2aᶄ+6-n)]B=(n-aᶄ-4)(n-aᶄ-2)2{n-[aᶄ+1 5+2/(2aᶄ+6-n)]}σ静=6Eh1fc/[δ(L1-kS)2]ìîíïïïïï(6)1 3 2㊀各片曲率半径的确定在已知各片厚度hk㊁预应力σ0k以及总成曲率半径R0的情况下,可确定各片曲率半径Rk:1Rk=2σ0kEhk+ /(R0+ðki=1hi-1)(7)其中,非单一圆弧系数 为:∂=1-2Eðnk=1(IkLkσ0k)/hk(R0+ðnk=1hi-1)2[]{}ðnk=1IkLk()/(R0+ðnk=1hi-1)3[]{}(8)1 4㊀总成曲率半径计算及预应力校核钢板弹簧总成在自由状态下的曲率半径是指主片上的曲率半径,所谓总成曲率半径只不过是总成自由弧高H0的换算半径,如图4所示㊂在已知各片长度Lk㊁厚度hk㊁宽度b以及曲率半径Rk的情况下,计算总成在自由状态下的曲率半径R0,同时校核各片预应力σ0k,这是对已有板簧的验算[3]㊂图4㊀总成曲率构成依据郭孔辉院士提出的 郭氏U法 计算总成曲率半径,该方法依据最小势能原理,计算结果比较可靠,而且接近实际情况,在考虑片厚影响的条件下,总成曲率半径为:R0=ðnk=1AkCk/Bk()/ðnk=1Ak/Bk()(9)其中,参数Ak㊁Bk㊁Ck㊁Rᶄ0分别为:Ak=IkLk/RkBk=(1+ðki=1hi+1/Rᶄ0)3Ck=Rk+ðki=1hi-1Rᶄ0=1nðki=1Rkìîíïïïïïïïï(10)在计算和校核预应力前,需确定非单一圆弧系数,虽然它对曲率半径的影响较小,但对预应力的影响是不可忽视的,因此需确定非单一圆弧系数 :=ðnk=1IkLkðnk=1Ik/Rkðnk=1IkLk/Rkðnk=1Ik(11)有了非单一圆弧系数就可以根据下式计算和校核弯矩和预应力:Mk=EIk1Rk- /(Rk+ðki=1hi-1)[]σ0k=Ehk21R- /(Rk+ðki=1hi-1)[]ìîíïïïï(12)1 5㊀总成及单片应力对于总成根部静应力的计算,建议直接采用集中载荷法的各片根部应力平均值来代替总成根部静应力㊂σA=0 06nbðnk=1[(Pklk-Pk+1lk+1)/h2k](13)单片弯矩和应力的计算,各单片任意截面的应力σkx按下式计算:σkx=Mkx/100Wk(14)其中:Mkx为各片任意截面处的弯矩;Wk为各片断面系数㊂2 钢板弹簧设计计算过程钢板弹簧的设计是以整车技术参数作为输入条件,首先需确定设计载荷㊁板簧长度㊁偏颇要求㊁悬架静挠度㊁动挠度㊁满载弧高以及整车布置要求,然后根据设计理论和计算公式进行计算㊁选择和匹配㊂钢板弹簧设计简图如图5所示[4-5]㊂图5㊀钢板弹簧简图2 1㊀板簧刚度初算及总惯性矩的确定首先根据整车布置需要确定板簧设计所需基本参数:钢板弹簧簧上载荷Fw㊁钢板弹簧伸直长度L㊁钢板弹簧悬架静挠度fc㊁钢板弹簧悬架动挠度fd㊁钢板弹簧满载弧高fa,由此可计算板簧刚度:C=Fw/fc(15)有关钢板弹簧的刚度㊁强度等,可在引入修正系数δ后按等截面简支梁的计算公式计算,根据修正后的简支梁公式计算钢板弹簧所需的总惯性矩J0,对于对称式钢板弹簧:J0=(L-Cs)3ktδ48E(16)式中:s为U形螺栓中心距;k为考虑U形螺栓夹紧处钢板弹簧后的无效长度系数;δ为挠度增大系数;E为材料的弹性模量㊂2 2㊀板簧断面尺寸及片数确定钢板弹簧总截面系数W0按公式(17)确定:W0=(L-Cs)F/4[σw](17)式中:[σw]为许用应力㊂由此可计算钢板弹簧平均厚度hp:hp=2J0W0=(L-Cs)2δ[σw]F6Ef0(18)有了平均厚度hp后,就可以对钢板弹簧的叶片宽度b进行设计选择㊂增大叶片宽,能增加卷耳强度,但车身受侧向力的作用倾斜时板簧的扭应力会增大㊂而且前悬架用宽的板簧,会影响转向轮的最大转角㊂减小叶片宽度,则会增加片数,从而增加片间摩擦和弹簧总成厚度㊂故推荐比值在b/hp在6 10之间㊂由此可确定片宽㊁片厚和片数,这三者是一个权衡协调的过程,而且还需要根据板簧标准选择相应的材料规格㊂b=hprn=12J0/bh3p{(19)2 3㊀各叶片长度与总成刚度计算钢板弹簧各叶片长度是基于各叶片展开图接近梯形梁的这一原则来确定的,所以选用作图法来确定钢板弹簧的各片长度㊂首先确定钢板弹簧第一片长度l1,第i片的一半长度为li:l1=L/2li=[l1-(l1-s/2)](i-1)n{(20)在所有参数确定后,需要对总成刚度进行验算㊂在此之前,有关挠度增大系数δ㊁惯性矩J0㊁片长和叶片端部形状等的确定都不够准确,所以有必要验算刚度,这里采用共同曲率法计算刚度㊂总成自由刚度和夹紧刚度按公式(4)计算㊂2 4㊀总成自由弧高和曲率半径钢板弹簧各片装配后,在预压缩和U形螺栓夹紧前,其主片上表面与两端连线间的最大高度差称为钢板弹簧总成在自由状态下的弧高H0,钢板弹簧总成在自由状态下的曲率半径R0按照公式(9)计算㊂2 5㊀各片自由状态下的曲率半径和预应力分配因钢板弹簧各片在自由状态下和装配后的曲率半径不同,装配后各片产生预应力,其值决定了自由状态下的曲率半径R0㊂其曲率半径和预应力分别按照公式(7)和公式(12)计算㊂2 6㊀总成装配后的曲率半径和预应力由于钢板弹簧各片在自由状态下的曲率半径Ri是根据静预应力σ0i计算而得,受其影响,装配后钢板弹簧总成与自由状态下的弧高计算结果会不同㊂因此,需要核算钢板弹簧总成的弧高和总成曲率半径,分别按照公式(13)和公式(14)计算㊂2 7㊀强度校核对于总成根部应力,建议采用集中载荷法的平均值来计算,按照公式(12)计算㊂3 设计软件开发及计算实例为了降低板簧设计计算过程的繁杂性,提高设计计算效率,利用MATLAB/GUI编写了设计计算程序,这使得设计更加方便快捷,这在工程应用上具有十分重要的意义㊂该设计软件能计算片端力㊁变形及刚度㊁曲率半径及预应力㊁总成及单片应力,完成了多片簧的设计计算流程,同时还能进行主副簧的设计计算以及悬架参数计算㊂程序流程图及软件界面分别如图6㊁图7所示㊂某车型前悬架钢板弹簧设计计算实例:根据某车型载荷㊁性能参数及安装布置要求,所设计的普通多片钢板弹簧需满足如下要求:板簧负荷,空载17500N,满足48000N;刚度420N/mm;自由弧高130mm;主片伸直长度1650mm;总成应力小于450MPa㊂利用设计计算程序,根据以上参数,可得相关计算结果如表1所示㊂图6㊀程序结构及设计流程图图7㊀主界面表1㊀板簧设计结果mm片序1234567891011121314片宽9090909090909090909090909090片厚1614141414141414141414141010片长1650165015201400126011201010880750610500370240240㊀㊀将所设计的板簧进行刚度试验,总成理论计算自由刚度为426 4N/mm,试验结果为440 3N/mm,与理论计算结果一致㊂4㊀结论综上所述,利用MATLAB软件,以工程应用的方式,根据整车载荷㊁性能参数及安装布置要求,完成了普通多片簧,包括主副簧的设计计算,并进行了刚度验算和强度校核,其间还计算了弹簧总成及单片的曲率半径㊁弧高㊁预应力等参数㊂基本解决了板簧设计计算过程的繁杂性,提高了设计计算效率,具有一定的工程应用价值㊂参考文献:[1]彭莫,刁增祥.汽车悬架构件设计的计算[M].北京:机械工业出版社,2012.[2]彭莫.渐变刚度钢板弹簧的计算方法[J].汽车工程,1993(6):350-358.PENGM.DesignandCalculationofLeafSpringwithVaryingStiffness[J].AutomotiveEngineering,1993(6):350-358.[3]袁涌,蔡静.Matlab/GUI在钢板弹簧悬架设计中的应用[J].湖北汽车工业学院学报,2011,25(2):16-19.YUANY,CAIJ.ApplicationofMatlab/GUIinLeafSpringSuspensionDesign[J].JournalofHubeiAutomotiveIndustriesInstitute,2011,25(2):16-19.[4]佟刚,张国忠,任飞.具有等厚主片变截面钢板弹簧优化设计[J].机械设计与制造,2001(2):9-10.TONGG,ZHANGGZ,RENF.ResearchonOptimizationofTaper⁃leafSpringwiththeMainLeafofEqualThickness[J].MachineryDesign&Manufacture,2001(2):9-10.[5]江浩斌,周孔亢.农用运输车钢板弹簧选型与计算机辅助参数设计[J].江苏理工大学学报(自然科学版),2000,21(1):19-23.JIANGHB,ZHOUKK.TypeSelectingandComputerAidedParameterDesignofLeafSpringsforAgriculturalTransporters[J].JournalofJiangsuUniversityofScienceandTechology(NaturalScience),2000,21(1):19-23.。
预应力的计算公式

预应力的计算公式在工程领域中,预应力技术的应用十分广泛,而准确计算预应力的大小对于确保结构的安全性和稳定性至关重要。
预应力的计算并非是一个简单的过程,它涉及到多个因素和复杂的公式。
接下来,咱们就来详细探讨一下预应力的计算公式。
首先,我们需要明确什么是预应力。
简单来说,预应力就是在结构承受荷载之前,预先对其施加的压力,目的是改善结构的性能,提高其承载能力和抗裂性。
预应力的计算通常基于材料力学和结构力学的原理。
在常见的预应力混凝土结构中,预应力的大小主要取决于以下几个关键因素:预应力钢筋的面积、预应力钢筋的张拉控制应力、预应力钢筋与混凝土之间的粘结性能以及结构的几何形状和尺寸等。
对于直线预应力钢筋,其预应力的计算公式可以表示为:P =σcon × Ap其中,P 表示预应力的大小,σcon 表示预应力钢筋的张拉控制应力,Ap 表示预应力钢筋的截面面积。
这里的张拉控制应力σcon 是一个重要的参数,它的取值需要考虑多种因素,如钢筋的种类、强度等级、施工工艺等。
一般来说,σcon不能超过钢筋的强度标准值,以保证钢筋在使用过程中的安全性。
在实际工程中,由于预应力钢筋并非完全直线布置,可能存在曲线或者折线的情况,此时需要考虑预应力钢筋的摩擦损失。
摩擦损失会导致预应力在传递过程中逐渐减小,其计算公式通常较为复杂,与钢筋的弯曲半径、摩擦系数以及预应力的传递长度等有关。
另外,还有锚具变形和钢筋回缩引起的预应力损失。
这种损失通常可以通过实验或者经验公式来确定。
除了上述因素,混凝土的收缩和徐变也会导致预应力的损失。
混凝土在硬化过程中会发生体积收缩,在长期荷载作用下会产生徐变,这些都会使预应力逐渐减小。
计算混凝土收缩和徐变引起的预应力损失需要考虑混凝土的配合比、养护条件、环境湿度以及结构的使用年限等众多因素。
在计算预应力时,还需要考虑预应力的有效预应力。
有效预应力是指扣除各种损失后,实际作用在结构上的预应力。
有效预应力的大小直接影响着结构的性能和安全性。
预应力的计算公式

预应力的计算公式
预应力的计算公式:
F=PS
F-张拉力kN,P-压力MPa,S-活塞面积mm2。
根据这个公式转换就行。
通俗些,我给你举个例子,你就明白了。
假设预制板中铺设有10条10.7的钢筋(该规格的钢筋横截面积为90mm2,标准抗拉强度为1420MPa),按照一般标准规定,取张拉系数0.7,即每条钢筋的张拉应力为1420*0.7=994MPa。
张垃机的油缸活塞面积为400cm2,则张拉时,压力表值P2计算为。
由于在张拉过程中,钢筋受拉力F1与张拉机的张拉力
F2大小是相等的,所以有F1=F2。
即,P1*S1=P2*S2,所以P2=P1*S1/S2
=1条钢筋张拉应力*1条钢筋横截面积*钢筋条数/张拉机活塞面积=994*90*10/400*100=22.365MPa
平均张拉力计算校核
Pp=P×[1-e-(kx+μθ)]/(kx+μθ)
PP-------预应力筋平均张拉力(N)
P -------预应力筋张拉端的张拉力(N)
L-------从张拉端至计算截面的孔道长度(m)
θ-------从张拉端至计算截面曲线孔道部分切线的夹角之和(rad)k -------孔道每米局部偏差对摩擦的影响系数。
μ-------预应力筋与孔道壁的摩擦系数。
理论伸长值:△L=Pp×L÷AP÷EP。
汽车钢板弹簧的设计
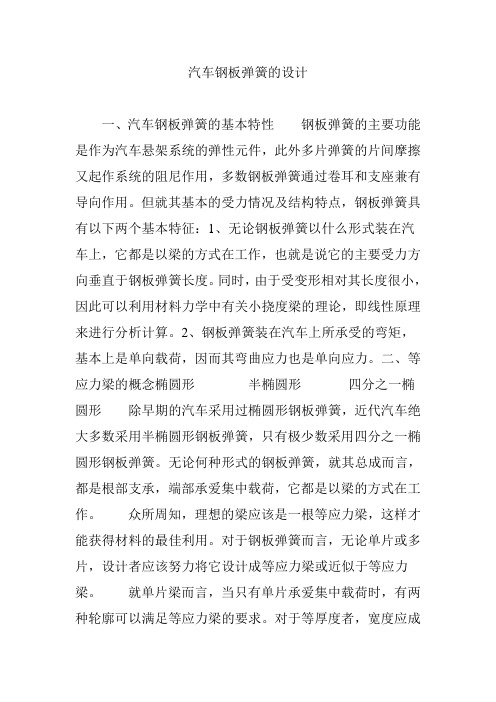
汽车钢板弹簧的设计一、汽车钢板弹簧的基本特性钢板弹簧的主要功能是作为汽车悬架系统的弹性元件,此外多片弹簧的片间摩擦又起作系统的阻尼作用,多数钢板弹簧通过卷耳和支座兼有导向作用。
但就其基本的受力情况及结构特点,钢板弹簧具有以下两个基本特征:1、无论钢板弹簧以什么形式装在汽车上,它都是以梁的方式在工作,也就是说它的主要受力方向垂直于钢板弹簧长度。
同时,由于受变形相对其长度很小,因此可以利用材料力学中有关小挠度梁的理论,即线性原理来进行分析计算。
2、钢板弹簧装在汽车上所承受的弯矩,基本上是单向载荷,因而其弯曲应力也是单向应力。
二、等应力梁的概念椭圆形半椭圆形四分之一椭圆形除早期的汽车采用过椭圆形钢板弹簧,近代汽车绝大多数采用半椭圆形钢板弹簧,只有极少数采用四分之一椭圆形钢板弹簧。
无论何种形式的钢板弹簧,就其总成而言,都是根部支承,端部承爱集中载荷,它都是以梁的方式在工作。
众所周知,理想的梁应该是一根等应力梁,这样才能获得材料的最佳利用。
对于钢板弹簧而言,无论单片或多片,设计者应该努力将它设计成等应力梁或近似于等应力梁。
就单片梁而言,当只有单片承爱集中载荷时,有两种轮廓可以满足等应力梁的要求。
对于等厚度者,宽度应成三角形,对于等宽度者,厚度为抛物线形状。
当然,从理论上讲,只要截面系数沿片长方向与弯矩成比例变化,都可以成为等应力梁。
然而汽车上几乎没有采用同时变厚又变宽的弹簧。
上述轮廓线只是对弯曲应力而言,实际上钢板弹簧端部受剪切强度的要求以及卷耳的存在,第一种轮廓只能是在三角形端部加上等宽的矩形或整个宽度成为梯形,而第二种轮廓只能是抛物线端部接上一段等厚度的矩形或厚度按梯形变化的梁。
为了简化轧制工艺,对于等宽度者,可用梯形代替抛物线。
此外,根部也设计成为平直的,便于与支承座贴合,也就是说,或者由梯形和根部、端部为矩形的三段直线构成。
所以,在实际应用上,只能把弹簧设计成为近似的等应力梁。
由于结构上的原因,没有人在汽车上采用等厚度变宽度的单片钢板弹簧,但等宽度变厚度的单片钢板弹簧早就得到实际的应用。
汽车钢板弹簧的性能、计算和试验

汽车钢板弹簧的性能、计算和试验东风汽车公司技术中心陈耀明1983 年3 月初稿2005 年1 月再稿目录前言(2)一.钢板弹簧的基本功能和特性(3)1. 汽车振动系统的组成(3)2. 悬架系统的组成和各元件的功能(6)3. 钢板弹簧的弹性特性(7)4. 钢板弹簧的阻尼特性(12)5. 钢板弹簧的导向特性(14)二.钢板弹簧的设计计算方法(17)1. 单片和少片变断面弹簧的计算方法(17)2. 多片钢板弹簧的刚度和工作应力计算(24)3. 多片弹簧各单片长度的确定(32)4. 多片弹簧的弧高计算(36)5. 钢板弹簧计算中的几个具体问题(43)三.钢板弹簧的试验(46)1. 钢板弹簧的静刚度测定(46)2. 钢板弹簧的动刚度测定(50)3. 钢板弹簧的应力测定(52)4. 钢板弹簧单片疲劳试验(53)5. 钢板弹簧总成疲劳试验(54)前言本文是为汽车工程学会悬架专业学组所办的“减振器短训班”撰写的讲义,目的是让汽车减振器的专业人员对钢板弹簧拥有一些基本知识,以利于本身的工作。
内容分为三部分:钢板弹簧的基本功能和特性,设计计算方法,以及试验等。
因为这部分内容非本次短训班的重点,所以要求尽量简单扼要,也许有许多不全面的地方,只供学习者参考。
有关钢板弹簧较详细的论述,可参考本学组所编的“汽车悬架资料”。
钢板弹簧的基本功能和特性1. 汽车振动系统的组成汽车在道路上行驶,由于路面存在不平度以及其它各种原因,必然引起车体产生振动。
从动态系统的观点来看,汽车是一个多自由度的振动系统。
其振源主要来自路面不平度的随机性质的激振,此外还有发动机、传动系统以及空气流动所引起的振动等等。
为改善汽车的平顺性,也就是为减小汽车的振动,关键的问题是研究如何对路面不平度的振源采取隔振措施,这就是设计悬架系统的根本目的。
换言之,就是在一定的道路不平度输入情况下,通过悬架系统的传递特性,使车体的振动输出达到最小。
当研究对象仅限于悬架系统时,人们往往把车体当为一个刚体来看待。
汽车钢板弹簧设计计算

1.1单个钢板弹簧的载荷已知汽车满载静止时汽车前轴荷G1=3000kg,非簧载质量Gu1=285kg,则据此可计算出单个钢板弹簧的载荷:Fw1=(G1-Gu1)/2=1357.5 kg (1)进而得到:Pw1=Fw1×9.8=13303.5 N (2)1.2钢板弹簧的静挠度钢板弹簧的静挠度即静载荷下钢板弹簧的变形。
前后弹簧的静挠度都直接影响到汽车的行驶性能[1]。
为了防止汽车在行驶过程中产生剧烈的颠簸(纵向角振动),应力求使前后弹簧的静挠度比值接近于1。
此外,适当地增大静挠度也可减低汽车的振动频率,以提高汽车的舒适性。
但静挠度不能无限地增加(一般不超过240 mm),因为挠度过大,即频率过低,也同样会使人感到不舒适,产生晕车的感觉。
此外,在前轮为非独立悬挂的情况下,挠度过大还会使汽车的操纵性变坏。
一般汽车弹簧的静挠度值通常如表1[2]所列范围内。
本方案中选取fc1=80 mm。
1.3钢板弹簧的满载弧高满载弧高指钢板弹簧装到车轴上,汽车满载时钢板弹簧主片上表面与两端(不包括卷耳孔半径)连线间的最大高度差[3]。
当H0=0时,钢板弹簧在对称位置上工作。
考虑到使用期间钢板弹簧塑性变形的影响和为了在车架高度已限定时能得到足够的动挠度值,常取H0∈10-20mm。
本方案中H01初步定为18mm。
1.4钢板弹簧的断面形状板弹簧断面通常采用矩形断面,宜于加工,成本低。
但矩形断面也存在一些不足。
矩形断面钢板弹簧的中性轴,在钢板断面的对称位置上。
工作时,一面受拉应力,一面受压应力作用,而且上、下表面的名义拉应力和压应力的绝对值相等。
因材料的抗拉性能低于抗压性能,所以在受拉应力作用的一面首先产生疲劳断裂。
除矩形断面以外的其它断面形状的叶片,其中性轴均上移,使受拉应力的一面的拉应力绝对值减小,而受压应力作用的一面的压应力绝对值增大,从而改善了应力在断面上的分布情况,提高了钢板弹簧的疲劳强度并节约了近10%的材料。