材料表面处理技术概论
表面处理技术概论-第4章 转化膜技术

⑶铝及铝合金阳极氧化膜的特点
①功能性:可以通过封孔处理以提高其保护性,也可在孔隙 中沉积特殊性能的物质而获得某些特殊功能,从而形成多 种多样的功能性膜层。
②吸附性:由于氧化膜呈现多孔结构,且微孔的活性较高, 有很好的吸附性。氧化膜对各种染料、盐类、润滑剂、石 蜡、干性油、树脂等均表现出很高的吸附能力。
4.1.4 表面转化膜用途
⑴提高材料的耐蚀性 ;氧化或磷化 ⑵提高材料的减摩耐磨性;磷化 ⑶提高材料的装饰性 ;钝化 ;着色 ⑷用作涂装底层;磷化膜 ⑸绝缘;磷化膜 ⑹防爆;瓦斯,粉尘,铝及铝合金与不锈钢
碰撞易通过铝热反应发生火花引爆。
• 4.2 阳极氧化
• 4.2.1 铝及铝合金的阳极氧化 • 4.2.2 铝阳极氧化膜的着色和封闭 • 4.2.3 镁合金阳极氧化
• 铝及铝合金进行阳极氧化时,由于电解质 是强酸性的,阳极电位较高,因此阳极反 应首先是水的电解,产生初生态的[O],氧 原子立即对铝发生氧化反应,生成氧化铝, 即薄而致密的阳极氧化膜。阳极发生的反 应如下:
H2O-2e-→[O]+2H+
2Al+3[O]→A12O3
阴极只是起导电作用和析氢反应:
4.1 转化膜技术简介
• 转化膜是指由金属的外层原子和选配的介质的阴 离ne
镁合金摩托车端盖磷酸盐转化膜
它的生成必须有基底金属的 直接参与,也就是说,它是 处在表层的基底金属直接同 选定介质中的阴离子反应, 使之达成自身转化的产物 (MmAn)。
易实现机械化或自动化作业,生产效 率高,转化处理周期短、成本低,但 设备投资大
无需专用处理设备,投资最省、工艺 灵活简便。但生产效率低、转化膜性 能差、膜层质量不易保证
适用范围
表面处理技术概论-绪论

因为,没有抗高温 涂层技术,载人飞船不 可能穿过大气层安全还 航;没有抗辐射薄膜技 术,太阳能电池不可能 在太空正常工作。
可见,从古代文明到现代文明,人 类离不开表面工程。
一、表面工程学的产生背景
20世纪80年代,电子、信息、 海洋、航天、先进制造等高科技的 急剧发展和对传统工业改造的迫切 需要,英国抢先提出表面工程概念。
表面工程技术日益得到重视的主要原因:
1) 社会生产、生活的需要 2) 通过表面处理大幅度提高产品质量 3) 节约贵重材料 4) 实现材料表面复合化,解决单一材料 无法解决的问题 5) 良好的节能、节材效果 6) 促进了新兴工业的发展
1983年英国伯明翰大学成立国际上的第 一个表面工程研究所—沃尔森表面工程研究 所; 1985年国际刊物《表面工程》发行;同 年召开第一次国际表面工程会议; 1986年国际热处理联合会改名为国际热 处理与表面工程联合会。
世界各发达国家均对表面工程 高度重视:
如美国工程科学院早在几年前为美 国国会提供的2000年前集中力量加 强发展的9项新科学技术中,有关材 料方面的仅有材料表面科学与表面 技术的研究。
三、使用表面技术的目的
(1) 提高材料抵御环境作用能力。 (2) 赋予材料表面某种功能特性。包括 光、电、磁、热、声、吸附、分离等等 各种物理和化学性能。
Modern Surface Engineering and Technology
教学目的
通过本课程学习
系统地掌握现代表面处理技术的基本原理; 能合理选择表面工程技术; 解决材料表面硬度、强度、耐磨性与心部强韧性之 间的矛盾; 充分发挥材料性能的潜力; 延长产品使用寿命和提高产品质量。
五、表面技术的分类
表面处理技术概述
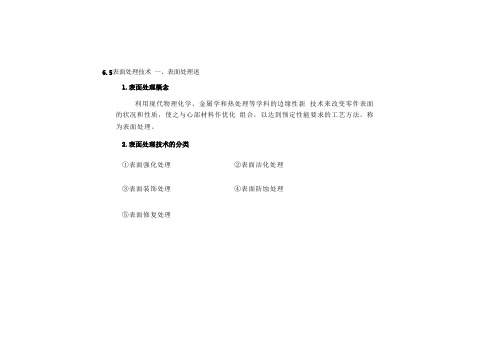
6.5表面处理技术一、表面处理述1.表面处理概念利用现代物理化学、金属学和热处理等学科的边缘性新技术来改变零件表面的状况和性质,使之与心部材料作优化组合,以达到预定性能要求的工艺方法,称为表面处理。
2.表面处理技术的分类①表面强化处理②表面洁化处理③表面装饰处理④表面防蚀处理⑤表面修复处理常用表面处理方法①热喷涂、喷丸、表面滚压②表面胀光、离子镀③激光表面强化、抛光④普通电镀、特种电镀⑤钢铁发蓝、钢铁憐化⑥铝阳极氧化及着色处理⑦喷漆与喷塑等、热喷涂氡一乙炔琨合气道粉末一火焰喷涂示意图喷涂粉末燃烧火焰送粉气道喷哺1.热喷涂原理IZ52?热喷涂是将金属或非金属材 料加热熔化,靠压缩气体连续吹 喷到制件表面上,形成与基体牢 固结合的涂层,从制件表层获得 所需要的物理化学性能。
基体、涂层Z 二 Z送丝机构二二C :二\\\\L\\\W\\\\V//,\\\~电弧喷涂原理图基体N前松体涂层、二二二一等离子喷涂原理图②喷涂材料可为金属、合金、金属氧化物和碳化物、陶瓷和塑料等,材料形态可为线材、棒料或粉末。
③喷涂的基体可为金属、陶瓷、玻璃、塑料、石膏、木材、布、纸等固体材料。
④喷涂的涂层厚度为几十微米至数毫米。
①工艺灵活,适用范围广。
热喷涂施工对象可大可小,小的可到小10mm内孔(线爆喷涂),2.热喷涂的特点大的可到桥梁、铁塔(火焰线材喷涂或电孤喷涂),可在室内喷涂,也可在野外现场作业;可整体喷涂,也可以局部喷涂。
②基体及喷涂材料广泛。
可通过喷涂不同材料,使工件表面获得所需的各种物理化学性能。
③工件应力变形小。
基体可保持较低的温度,工件产生的应力变形很小。
④生产效率高。
每小时喷涂材料重量从几千克到几十千克,沉积效率很高。
①防腐蚀:主要用于大型水闸钢闸门、造纸机烘缸、煤矿井下钢结构、高压输电铁塔、电视台天线、大型钢桥梁、化工厂大罐和管道的防腐喷涂。
3.热喷涂的应用②防磨损:通过喷涂修复已磨损的零件,或在零件易磨损部位预先喷涂上耐磨材料,如风机主轴、高炉风口、汽车曲轴、机床主轴、机床导轨、柴油机缸套、油田钻杆、农用机械刀片等。
材料表面处理技术及其应用
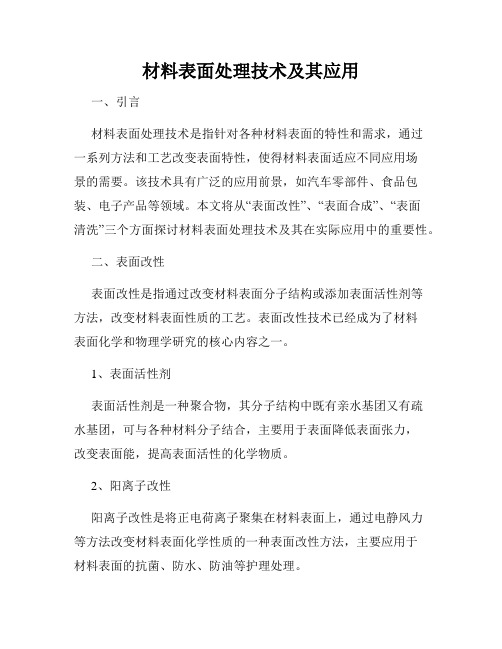
材料表面处理技术及其应用一、引言材料表面处理技术是指针对各种材料表面的特性和需求,通过一系列方法和工艺改变表面特性,使得材料表面适应不同应用场景的需要。
该技术具有广泛的应用前景,如汽车零部件、食品包装、电子产品等领域。
本文将从“表面改性”、“表面合成”、“表面清洗”三个方面探讨材料表面处理技术及其在实际应用中的重要性。
二、表面改性表面改性是指通过改变材料表面分子结构或添加表面活性剂等方法,改变材料表面性质的工艺。
表面改性技术已经成为了材料表面化学和物理学研究的核心内容之一。
1、表面活性剂表面活性剂是一种聚合物,其分子结构中既有亲水基团又有疏水基团,可与各种材料分子结合,主要用于表面降低表面张力,改变表面能,提高表面活性的化学物质。
2、阳离子改性阳离子改性是将正电荷离子聚集在材料表面上,通过电静风力等方法改变材料表面化学性质的一种表面改性方法,主要应用于材料表面的抗菌、防水、防油等护理处理。
3、等离子体改性等离子体改性是一种电离气体处理技术,通过高能等离子体将氧气、氮气等气体中的离子与材料表面化学物质相互反应,形成氧化或硝化的工艺。
应用于材料的氧化、活化等方面。
三、表面合成表面合成技术是指通过材料表面类型等自组装作用或表面化学反应,形成一层或多层超薄分子膜的工艺。
1、自组装法自组装法是在水溶液或有机溶液中通过静电相互作用、范德瓦尔斯力等物理作用,通过分子态材料自动排列形成分子层膜或超薄分子膜等工艺,并且降低表面自由能、增加表面特性、提高比表面积等特性。
其在电子产品、食品包装等领域的应用十分广泛。
2、凝胶法凝胶法是采用化学反应或聚合物合成等方法,将溶液中的单体或预聚物聚合成大分子组成的凝胶层,在材料表面,形成层层生长的聚合物薄膜。
应用于材料的吸附、分离等方面。
3、光敏化学反应光敏化学反应是一种在光照激励下,物质发生化学反应的表面反应技术。
特点是光化学反应瞬间发生,速度快,可以制备具有很高复杂度、定向性的化学修饰材料。
自然科学知识:材料和工程的表面处理技术
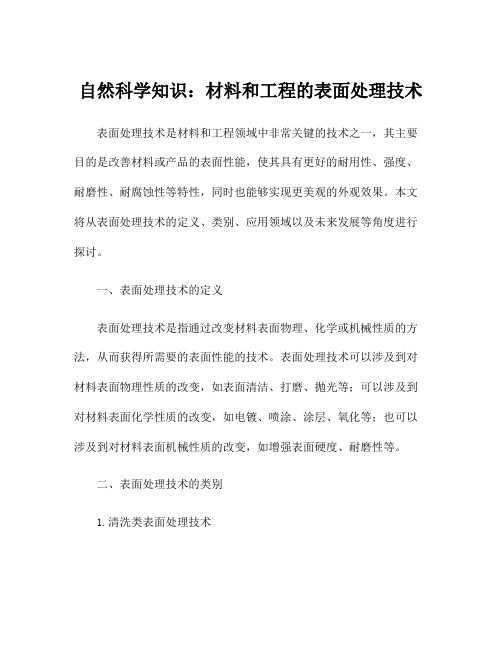
自然科学知识:材料和工程的表面处理技术表面处理技术是材料和工程领域中非常关键的技术之一,其主要目的是改善材料或产品的表面性能,使其具有更好的耐用性、强度、耐磨性、耐腐蚀性等特性,同时也能够实现更美观的外观效果。
本文将从表面处理技术的定义、类别、应用领域以及未来发展等角度进行探讨。
一、表面处理技术的定义表面处理技术是指通过改变材料表面物理、化学或机械性质的方法,从而获得所需要的表面性能的技术。
表面处理技术可以涉及到对材料表面物理性质的改变,如表面清洁、打磨、抛光等;可以涉及到对材料表面化学性质的改变,如电镀、喷涂、涂层、氧化等;也可以涉及到对材料表面机械性质的改变,如增强表面硬度、耐磨性等。
二、表面处理技术的类别1.清洗类表面处理技术清洗类表面处理技术是指利用各种清洗剂或机械力量清除材料表面附着物的方法。
这种技术广泛应用于半导体、电子、汽车等行业,能够减少表面缺陷,提高材料表面的可靠性和稳定性。
2.表面涂层类表面处理技术表面涂层类表面处理技术是指利用各种化学或物理涂层方法在材料表面形成一定厚度和特定性质的薄层。
涂层材料可以是金属、非金属、光敏物质等。
这种技术广泛应用于航空航天、汽车、机械等行业,能够显著提高材料表面的耐磨、耐腐蚀等性能。
3.表面改性类表面处理技术表面改性类表面处理技术是指在材料表面产生一定的化学物理变化,从而改变材料原有的性质。
本类技术主要包括注塑、电镀、氧化、阳极化等技术,其主要应用于汽车、电子、半导体等行业,能够大大提高材料的表面硬度、抗腐蚀性、机械强度等性质。
三、表面处理技术的应用领域表面处理技术广泛应用于各种领域,具有很高的经济效益和社会效益。
下面列举了一些典型的应用领域。
1.电子行业电子行业中的芯片、集成电路、显示屏等产品,表面处理技术是不可或缺的关键环节。
通过表面清洗、氧化、电镀等技术的应用,能够提高产品稳定性和可靠性。
2.汽车行业汽车构成多种材料,如铝、钢、玻璃等,通过表面处理技术能够提高车身外观效果,同时也是提高汽车耐用性和安全性的重要手段。
材料表面处理技术研究综述
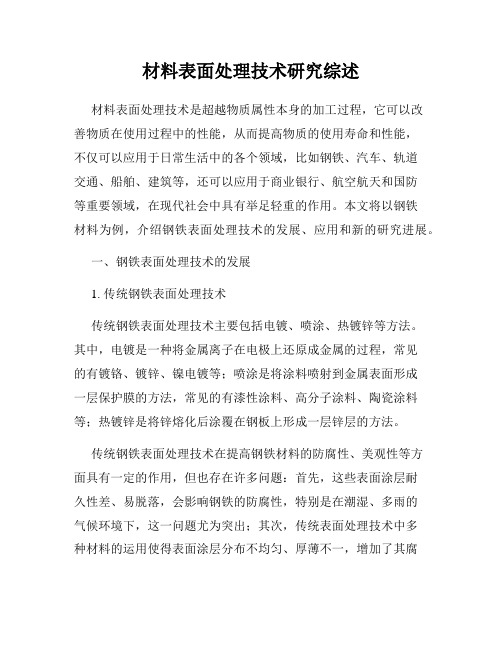
材料表面处理技术研究综述材料表面处理技术是超越物质属性本身的加工过程,它可以改善物质在使用过程中的性能,从而提高物质的使用寿命和性能,不仅可以应用于日常生活中的各个领域,比如钢铁、汽车、轨道交通、船舶、建筑等,还可以应用于商业银行、航空航天和国防等重要领域,在现代社会中具有举足轻重的作用。
本文将以钢铁材料为例,介绍钢铁表面处理技术的发展、应用和新的研究进展。
一、钢铁表面处理技术的发展1. 传统钢铁表面处理技术传统钢铁表面处理技术主要包括电镀、喷涂、热镀锌等方法。
其中,电镀是一种将金属离子在电极上还原成金属的过程,常见的有镀铬、镀锌、镍电镀等;喷涂是将涂料喷射到金属表面形成一层保护膜的方法,常见的有漆性涂料、高分子涂料、陶瓷涂料等;热镀锌是将锌熔化后涂覆在钢板上形成一层锌层的方法。
传统钢铁表面处理技术在提高钢铁材料的防腐性、美观性等方面具有一定的作用,但也存在许多问题:首先,这些表面涂层耐久性差、易脱落,会影响钢铁的防腐性,特别是在潮湿、多雨的气候环境下,这一问题尤为突出;其次,传统表面处理技术中多种材料的运用使得表面涂层分布不均匀、厚薄不一,增加了其腐蚀风险;最后,涂层生产过程中环保问题尤为关键,表面涂层生产的废水和废气会对环境造成严重的污染。
2. 新型钢铁表面处理技术随着科学技术的不断进步,钢铁表面处理技术逐渐转向新型技术。
这些新型技术采用的新材料具有性能稳定、防腐性能好、环保等特点,对钢铁表面的涂层腐蚀性、光泽度等性质都有很大的提升。
主要的新型表面处理技术包括化学镀、电化学沉积、物理气相沉积等。
化学镀是一种通过化学反应将金属离子还原到基体表面形成涂层的过程。
化学镀法比传统的电镀法更加环保,而且涂层具有一定的耐蚀性、塑性和良好的外观效果。
电化学沉积是一种将金属沉积到基体表面的方法,最常见的应用是金属膜的制备。
这种方法不仅简便,而且具有高效、高质量的特点;物理气相沉积是一种利用物理气相或者化学反应沉积材料到基体表面形成涂层的方法,该技术主要应用于高精度元件、光学材料和微电子等领域。
表面处理技术概论低维材料
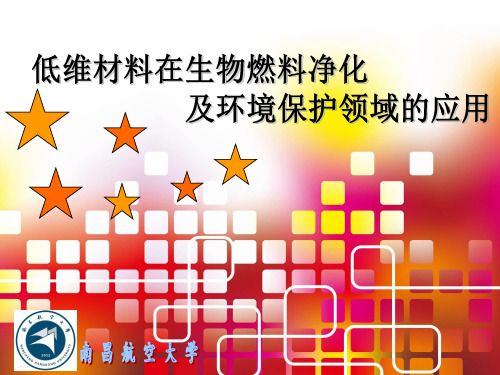
一、基本概念解释(1)、低维材料(2)、纳米材料(3)、生物燃料(4)、生物燃料净化1、维数比三小的叫低维材料,具体来说是二维、一维和零维材料。
2、二维材料,包括两种材料的界面,或附着在基片上的薄膜.界面的深或膜层的厚度在纳米量级。
半导体量子阱属二维材料。
3、一维材料,或称量子线,线的粗细为纳米量级.4、零维材料,或称量子点,它由少数原子或分子堆积而成,微粒的大小为纳米量级.半导体和金属的原子簇(cluster)是典型的零维材料.1、纳米材料是指在三维空间中至少有一维处于纳米尺度范围(1-100nm)或由它们作为基本单元构成的材料,这大约相当于10~100个原子紧密排列在一起的尺度。
2 、纳米材料大致可分为纳米粉末、纳米纤维、纳米膜、纳米块体等四类。
纳米纤维:指直径为纳米尺度而长度较大的线状材料。
可用于:微导线、微光纤(未来量子计算机与光子计算机的重要元件)材料;新型激光或发光二极管材料等。
静电纺丝法是制备无机物纳米纤维的一种简单易行的方法。
纳米膜:纳米膜分为颗粒膜与致密膜。
颗粒膜是纳米颗粒粘在一起,中间有极为细小的间隙的薄膜。
致密膜指膜层致密但晶粒尺寸为纳米级的薄膜。
可用于:气体催化(如汽车尾气处理)材料;过滤器材料;高密度磁记录材料;光敏材料;平面显示器材料;超导材料等。
3、低维材料大多是纳米材料,低维材料范围较小,我们将主要介绍二维材料。
4、在材料学中,厚度为纳米量级的晶体薄膜通常被视作二维的,即只有长宽,厚度可忽略不计,称为二维纳米材料。
*低维材料*纳米材料(3)、生物燃料•生物燃料(biofuel)泛指由生物质组成或萃取的固体、液体或气体燃料。
•可以替代由石油制取的汽油和柴油,是可再生能源开发利用的重要方向。
所谓的生物质是指利用大气、水、土地等通过光合作用而产生的各种有机体,即一切有生命的可以生长的有机物质。
它包括、动物和微生物。
不同于石油、煤炭、核能等传统燃料,这新兴的燃料是可再生燃料。
材料表面处理技术综述

材料表面处理技术综述第一章绪论材料表面处理是一种改善材料表面特性、提高其性能的工艺。
表面处理技术在现代工业中得到了广泛应用,具有较高的研究和实用价值。
本文就材料表面处理技术进行了综述,包括表面处理的研究意义、研究现状、表面处理方法以及应用前景等。
第二章表面处理的研究意义表面处理技术是在材料科学领域中的一个非常重要的研究方向。
材料的表面性质是保证其机械、物理和化学性质的关键,通过表面处理能够改善材料的表面性能,提高材料的性能指标。
同时,表面处理技术还可以应用于材料的加工、制造和使用等环节。
例如,在制造航空航天器和高速列车等领域中,表面处理技术能够提高材料的耐腐蚀性、耐磨性和耐疲劳性,保证设备的持久稳定运行。
在环保领域中,表面处理技术可以降低污染物的排放,保护环境。
第三章表面处理技术的研究现状表面处理技术主要分为机械处理、物理处理和化学处理三类。
机械处理方法包括打磨和喷砂磨砂等;物理处理方法主要包括电子束辐照、电弧表面熔化和等离子体喷涂等;化学处理方法包括酸洗、电解处理等。
其中,等离子体喷涂技术目前被广泛应用于表面处理领域。
它采用气体放电等离子体技术,在低压下将金属粉末、陶瓷粉末或材料薄膜等喷涂到材料表面,形成一层覆盖层,以改善材料表面性能。
等离子体喷涂具有喷涂速度快、覆盖率高、成像度好、表面光滑等优点。
同时,该技术也应用于冶金、环保等领域。
第四章表面处理技术的方法1. 预处理预处理在表面处理技术中非常重要,它可以清洗掉材料表面的污垢和氧化层,为接下来的处理工作做好准备。
不同的物质需要不同的预处理方法,常见的方法包括酸洗、碱洗和电解处理等。
2. 机械处理机械处理是通过物理力量改变材料表面的形貌以及物理结构,从而达到改善表面性能的目的。
这种方法可以钝化表面,防止其腐蚀,同时也能增加表面粗糙度,提高表面附着力。
3. 热处理热处理是通过改变材料温度来改善表面性能的一种方法。
在高温下,材料表面的化学反应速度加快,可以增加材料附着力,同时也可以改善材料的耐磨性和耐腐蚀性。
- 1、下载文档前请自行甄别文档内容的完整性,平台不提供额外的编辑、内容补充、找答案等附加服务。
- 2、"仅部分预览"的文档,不可在线预览部分如存在完整性等问题,可反馈申请退款(可完整预览的文档不适用该条件!)。
- 3、如文档侵犯您的权益,请联系客服反馈,我们会尽快为您处理(人工客服工作时间:9:00-18:30)。
材料表面处理技术概论摘要:本文简要介绍了材料表面处理技术的概念,研究背景,发展历程,和应用现状等方面。
关键词:表面处理技术、历史、现状表面处理在基体材料表面上形成一层与基体的机械、物理和化学性能不同的表层的工艺方法。
表面处理的目的是满足产品的耐蚀性、耐磨性、装饰或其他特种功能要求。
一般国内所说的表面处理有两种解释,一种是狭义的表面处理,即只包括喷砂、喷丸等在内的即常说的前处理部分;另一种是广义的表面处理,即包括前处理、电镀、涂装、化学氧化、热喷涂等众多物理化学方法在内的工艺方法。
我们所说的主要是广义的表面处理,即表面工程技术。
一、发展背景磨损、腐蚀和断裂是机械零部件、工程构件的三大主要破坏形式,它们所导致的经济损失十分巨大,其中由于磨损、腐蚀导致的机件失效与相应的经济损失占非常大的比重。
在美国国家材料政策委员会向美国国会提出一份报告中指出:由于摩擦磨损引起的损失,使美国经济每年支付1000亿美元的巨额资金,这项损失中材料部分约为200亿美元;在1983年前联邦德国的一次调查中指出:由于摩擦磨损造成的总随时估计为387亿马克;在英国,由于摩擦磨损造成的经济损失每年至少为51500万英镑以上。
1986年我国对摩擦磨损造成的损失惊醒了全面彻底的调查分析,指出:此项损失至少占国民总产值的1.8%。
许多国家政府对腐蚀造成的经济损失也进行了调查分析,美国Battelle 实验室和国家标准总局1978年共同进行调查表明:1975年美国的腐蚀一年损失达820亿美元,占国民总产值的4.9%,1995年4月Battelle和SSINA发表报告指出:现在美国因为腐蚀一年的损失达3000亿美元;1983年我国曾做过腐蚀调查,当时的结论为我国因腐蚀造成的损失至少在400亿元人民币以上。
众所周知,摩擦和腐蚀均是发生于机件表面的材料流失过程,而且其它形式的机件失效是从表面开始,采用表面防护措施延缓和控制表面的破坏,称为解决上述问题的有效方法,在解决问题的同时,促进了表面工程科学和表面技术的形成与发展。
二、发展历史人们使用表面技术已有悠久的历史。
我国早在战国时代已进行了钢的淬火,使钢的表面坚硬。
欧洲使用类似的技术也有很久的历史。
但是表面技术的迅速发展史从19世纪工业革命开始的,尤其是近30年发展更为迅速。
1983年,表面工程的概念首次被提出,同年英国伯明翰大学沃福森表面工程研究所建立和1985年《表面工程》国际刊物发行,1986年国际热处理联合会也改名为国际热处理及表面工程联合会,这些都是表面工程技术在国际上迅速发展的重要标志。
同样,在国内表面工程技术也得到了迅速发展,其标志为1987年中国机械工程学会建立的表面工程研究所(学会性质)、1988年出版的《表面工程》期刊(经国家科委正式批准1997年更名为《中国表面工程》)。
现在表面工程已经发展成为横跨材料学、摩擦学、物理学、化学界面力学和表面力学材料失效与防护金属热处理学、焊接学、腐蚀与防护学、光电子学等学科的边缘性综合性复合型学科。
表面技术的应用已经十分广泛,可以用于防腐、耐磨、修复、强化、装饰等,也可以是光、电磁、声、热、、化学、生物等方面的应用。
表面技术所涉及的基材不仅是金属材料、有机高分子子材料及复合材料。
我国自“六五”计划以来,通过在设备维修领域和制造领域推广应用表面工程技术已取得了几百亿元的经济效益。
在国家的节能、节材“九五”规划中建议将发展表面工程作为重大措施之一,并列为节能、节材示范项目。
国计委已决定建立国家表面工程研究中心。
材料表面改性作为传统材料性能优化的基础研究也被列入国家自然科学基金“九五”优先资助领域。
一些国内外知名专家预言,表面工程将成为21世纪工业发展的关键技术之一。
三、发展现状表面工程有多种技术方法,包括电镀、电刷镀、化学镀、涂装、粘结、热喷涂、热浸镀、化学气相沉积、表面热处理、表面激光改性、离子注入等。
本文选择几种作为介绍。
1、气相沉积技术气相沉积是利用气相中发生的物理、化学过程,在工件表面形成具有特殊性能的金属或化合物涂层。
按照过程的性质可将其分为化学气相沉积和物理气相沉积两大类。
化学气相沉积是利用气态物质在固态工件表面进行化学反应,生成固态沉积物的过程。
通常处理是将低温下气化的金属盐与加热到高温的基体接触,通过与碳氢化合物和氢气或氮气进行气相反应,在基体表面上沉积所要求的金属或金属间化合物。
化学气相反应室应抽真空并加热到900一1000℃,生成物沉积在工件表面。
钢件经沉积镀覆后,还需进行热处理,可在同一反应室内进行由于加热温度较高、所用钢种皆系合金钢,故升温时要采用预热处理,沉积处理后随炉冷至200℃以下,取出空冷,再进行淬火和回火处理。
碳素工具钢、渗碳钢、轴承钢、高速钢、铸铁及硬质合金等多种材料都可进行气相沉积。
物理气相沉积(PVD)是通过蒸发、电离或溅射等过程,产生金属粒子沉积在工件表面,形成金属涂层或与反应气反应形成化合物涂层。
物理气相沉积的重要特点是沉积温度低于600℃,沉积速度比CVD 快。
PVD法可适用于黑色金属高速钢、碳素工具钢等有色金属、陶瓷、高聚物、玻璃等各种材料。
PVD法有真空蒸镀、真空溅射、离子镀三大类.2、离子注入表面强化处理离子注人是根据被处理表面材料所需要的离子注人是根据被处理表面材料所需要的性能来选择适当种类的原子,使其在真空电场中离子化,并在高电压作用下加速注人工件表层的技术。
离子注入设备真空中将注入的原子电离成离子,用聚束系统形成离子束流,用加速系统以必要的能量加速。
由于加速的离子束也可能含有不需要的离子,需要利用质量分析器进行质量分离,只让必要的离子从狭缝通过。
由于通过狭缝的离子束的断面的不均匀,为使离子束有良好的均匀性,应对离子束作电扫描。
离子注人技术在工业上应用广泛。
在材料工业中用于金属材料表面合金化,可以提高工程材料的表面性能。
例如,利用N、C、B等非金属元素注入到钢、铁、有色金属及各种合金中,当注人剂量的离子大于时,将产生明显的表面硬化作用,一般提高10%--100%,甚至更高。
离子注入能改变金属表面的摩擦系数,又由于它提高了硬度,耐磨性增强。
当离子注入Ce、Y、Hf、Th、Zr、Nb、Ti或其它能稳定氧化物的活性元素于钢中,可大大提高钢的耐腐蚀能力。
3、熔盐浸镀处理TMD处理是熔盐浸镀法、电解法及粉末法进行扩散表面硬化处理技术的总称。
TD处理是Toyota Diffusion的简称,系日本丰田中央研究所于七十年代所发展的材料表面改性技术,在日本已有超过二十年的实际工业应用历史。
TD处理是将欲处理的工件置于含有碳化物形成元素如钒、妮、铬高温盐浴中,温度保持在871一1037℃,处理时间为1一8h。
此时底材中所含的碳会往外扩散至表面,与盐浴中的碳化物形成元素结合为碳化物,例如碳化钒、碳化铌与碳化铬。
前二者有优异耐磨性与耐剥离强度,而后者碳化铬虽然有较低的耐磨性,但是却有高的抗氧化性。
此碳化物非常细致内部没有疏松组织,与底材系以金属键结方式紧密结合,在碳化物与底材之间存在一层薄的扩散层约2一20微米。
由于碳化物形成所需的碳均由底材供应,因此适合TD作处理的底材必须为含碳量至少在0.3%以上的含碳材料,如钢铁\镍合金、钻合金及超硬合金。
处理前,工件均须作预热以防加热过速产生变形,然后在各种工件材料的A化温度下进行TD处理。
处理后的冷却方式则有多种选择,视材料而定,可采用空冷、油冷、水冷、盐浴冷却、氮气冷却,使底材获得硬化,再行回火。
当钢材A化温度大于TD处理温度上限时,处理后的钢材必须放在真空热处理炉或具保护性的盐浴炉中加热至A化温度并作冷却,以完成底材的硬化。
实际应用最广的是用熔盐浸镀法在工件表面涂覆VC、NBC、Cr-C 等碳化物镀层。
TD处理有直接加热与间接加热形式两种。
熔盐浸镀法的原理是将放入耐热坩埚中的硼砂(至少占70%-90%)熔融后,欲涂覆哪种碳化物即向硼砂中相应的加入哪种能形成碳化物的物质。
例如涂覆VC时加入Fe-V的合金粉末或V205粉末,将含碳的钢件浸入保持在800—1200℃的盐浴中,保温1—10h,即可得到由碳化物构成的表面涂层。
4、激光表面处理技术激光表面处理激光是1960年才出现的一种新光源。
激光具有高亮度、高单色性、高相干性、强方向性等特征,由于这些特点决定了它在许多领域中都有重大的应用。
激光表面处理是一种高能量密度的表面热处理,下面介绍有关几种新型的激光表面处理工艺。
激光表面融处理(LSM)是用能量密度较大的激光照射工作表面,使材料表面层熔化,停止照射后靠基体热传导快冷却凝固技术。
在激光熔融处理时,当冷却速度为106℃/S以上时,足以抑制正常晶粒的形成,而在表面层 1一10微米内产生亚稳结构这类亚结构通常是超细的枝晶,甚至是非晶态,这主要取决于金属或合金的本质和冷却速度,这种处理方法相当于激光上釉,其特点是表面具有高硬度、高耐磨和高耐蚀性。
另一种常用于铸铁或高碳钢的处理工艺是通过激光束照射铸铁表面,使表面熔融,而片状石墨均匀地熔于奥氏体基体中,在随后的自冷却过程中过饱和的碳以渗碳体形式析出在表面层,形成莱氏体组织;这种表层硬度约为1000HV,大幅度地提高耐磨性,此工艺已用于汽车凸轮轴生产中。
激光合金化是用激光束把基体材料表层和涂敷到表面上的合金化物质一起熔化后迅速凝固,从而达到改变表层化学成分、提高金属的耐磨性、抗蚀性及高温抗氧化性的一种表面改性处理方法。
激光合金化能量密度一般为104一106W/cm2。
,合金化熔池深度为0.5一2mm,基体材料为碳钢或铸铁,有时亦选用有色金属Al、Ti、Ni为基体合金。
合金化的材料可以是粉末、薄片、线材或棒材,可预先加人或同时加人,预先加入的方式有沉积、电镀、离子注人、刷涂、喷涂等。
这种工艺可使零件有高硬度、高耐磨性、优良的耐蚀性,已在工业上广泛应用。
5、低温等离子材料表面改性等离子体物理在天文学和受控核聚中有极重大的应用。
近四十年来,低温等离子体技术发展得很快,在机械工业中亦得到广泛应用。
低温等离子体改善材料表面性能的机理粗略认为在低温等离子体反应室内,低压工作气体中的电子在电场加速作用下,由于电子碰撞及派生离子、原子的碰撞使气体电离,从而产生低温等离子体低温等离子体中存在大量的离子、电子以及亚稳态、激发态、游离态粒子,这些粒子具有几个电子伏至十几个电子伏能量伴随着等离子体产生将出现各种能量的光辐射,这些具有一定能量活性粒子和各种能量光辐射可直接引起材料表面发生某些物理变化和化学变化,活性离子和光辐射又可在低温下(低于400℃)分解反应气体使反应气体的生成物沉积到材料表面从而改变材料表面的物理化学性。
此外,有的高能离子会注人到基体材料表层,引起碰撞、散射、激发、溅射、重排、异构、裂解等,也可使材料表面组成、成分及结构发生变化,从而实现材料表面的改性。