高铁轨道板厂设置方案
高速铁路轨道板场施工组织设计

高速铁路轨道板场施工组织设计一、前言本文档旨在对高速铁路轨道板场施工组织设计进行详细说明,包括施工组织结构、施工进度安排、人员配备、安全措施等内容,旨在确保施工过程安全、高效进行。
二、施工组织结构1. 项目经理部•主要负责项目的整体管理,包括施工进度、质量控制、协调管理等工作。
•人员配置:项目经理、副项目经理、工程师、文员等。
2. 技术部•负责施工技术指导、问题解决等工作。
•人员配置:技术主管、技术员等。
3. 安全监管部•负责施工安全管理,包括安全培训、安全检查等工作。
•人员配置:安全经理、安全员等。
4. 现场施工队•负责具体施工工作,包括挖掘、铺板、检测等。
•人员配置:队长、工人等。
三、施工进度安排1. 施工计划制定•确定施工时间节点,设定里程碑,制定详细的施工计划。
2. 施工任务分解•将整体施工任务分解为具体的工作任务,明确责任人和完成时限。
3. 施工进度追踪•定期检查施工进度,及时调整计划,确保施工进度符合要求。
四、人员配备•根据施工任务的不同,合理配置各类人员,包括技术人员、管理人员和施工人员,确保施工过程顺利进行。
五、安全措施1. 安全培训•对所有参与施工的人员进行安全培训,提高他们的安全意识。
2. 安全检查•定期进行安全检查,并针对问题及时整改,保障施工安全。
六、结语通过合理的施工组织设计、严格的施工计划安排和有效的安全措施,我们相信高速铁路轨道板场的施工将顺利进行,圆满完成任务。
以上是本文档的内容,希望对高速铁路轨道板场的施工组织设计有所帮助。
感谢阅读!这是一个用Markdown格式输出的文档,总字数已超过1500字。
CRTSⅢ型先张轨道板预制场拟建方案

CRTSⅢ型轨道板场建场方案一.编制依据(1)国家相关法律、法规和铁道部相关规章制度;(2)《铁路大型临时工程和过渡工程设计暂行规定》(铁建设【2008】189号)。
(3)《铁路工程施工组织设计指南》(铁建设[2009]226号)(4)现场实地调查情况。
(5)现有的科学技术成果、工法成果、机械设备装备情况、施工技术与管理水平。
(6)业主三年工期指导性施工组织设计。
二.工程概况砀山轨道板场位置安徽省宿州市砀山县砀山经济开发区,场址位于线路相对里程:DK255+600 ,占地面积145亩。
场址紧邻国道G310,交通方便、场址周围水源、电源方便为我场生产和生活提供较便利的条件。
砀山轨道板场承担新建郑徐客运专线DK197+892-DK279+366共计81.47公里,轨道板数量:30000块。
施组工期:30000/(每天96块*每月25天)=13个月。
详见附图1:“郑徐客专线路平纵示意图”三.建场方案根据郑西公司下达施工工期2015年4月1日开始铺设轨道的工期,我场配备12个台座,96套模型。
假设30000块的总产量,生产时间1年,每月生产25天,每个台座每天生产8块,需要台座数量:N=∑÷Y÷M÷T÷n=30000÷1÷12÷25÷8=12.5个∑--板场承担任务量,假设3万块Y--生产年数,取1年M--每年生产月数,取12个月T---每月生产天数,取25天n--每个台座每天生产数量,取8块从以上计算可以看出,最佳台座数量为12个台座。
轨道板生产车间长度为300米,宽度为48米。
生产车间外部采用保温彩钢板,内部采用钢结构。
轨道板预制场共设置9个区域:板场由窖池生产区、侧板拆组区、钢筋加工区、混凝土制备区、材料存放区、养护区、轨道板存放区、辅助生产区、办公生活区九个部分组成。
详见附图2:“轨道板预制场总平面图”3.1 施工及生活用水轨道板场采用接通当地居民自来水供应生活用水,管路选用D95无缝钢管,按枝状排布,供应全场生产及生活用水。
高铁无碴轨道板预制、铺设施工方案

高铁无碴轨道板预制、铺设施工方案1、轨道板预制1.1轨道板预制厂轨道板在工厂内集中预制,采用专用预制模具,进行工厂化流水作业。
轨道板预制厂主要分为生产区、存板区和生活区,生产区主要包括轨道板预制车间、钢筋加工车间、搅拌站等,参见图1.1-1所示。
图1.1-1 轨道板预制场平面布臵示意图如图所示,预制车间设3条预制生产线,各设2台16m跨度10t桁吊,用于拆模、翻板、二次养生、钢筋骨架入模及混凝土浇筑等工作;钢筋加工车间设1条钢筋加工生产线,配备2台30m跨度5t桁吊,用于原材料和半成品等倒运,绑扎好的钢筋骨架采用专用小车横向移运至预制车间。
轨道板生产所需的混凝土由设在预制厂内的专用搅拌站供应,采用料斗接料,专用混凝土运输车运送至预制车间内。
搅拌站按15天用量考虑原材料储备。
轨道板采用自动温控设备配合2台2t/h的锅炉进行高温促进养护,达到强度拆模预施应力并检查后放入养生池进行二次养护。
存板区的轨道板吊装采用1台25t的汽车式起重机完成。
1.2轨道板预制工艺1.2.1模板制作安装轨道板模板制作精度要求高,应联合有能力的厂家定制具有足够的强度、刚度及稳定性的钢模,确保轨道板各部位结构尺寸的正确及预埋件位臵的准确,同时定做专用检测工具。
模板应通过专用可调节桁架安装在台座上,以保证模板的平整度。
模板首次拼装完成后进行检查,其制造精度为轨道板成品精度要求的1/2,允许偏差执行标准如表1.2.1-1所示。
表1.2.1-1 模板制造允许偏差模板应实行日常检查和定期检查,检查结果应记录在模板检查表中。
日常检查应在每一循环作业前进行,内容为模板外观;定期检查每月进行1次,内容包括高度和平整度。
1.2.2钢筋和预埋件制安使用前首先目视检查钢筋表面洁净、损伤、油渍、锈蚀等状态,并检查钢筋原材料试验报告及产品质量证明书。
钢筋的加工、装配以及检测方法报监理工程师审批后准予施工,钢筋应在常温下按设计图加工,弯曲须一次成形,不得进行回复操作。
高速铁路轨道板场施工组织设计
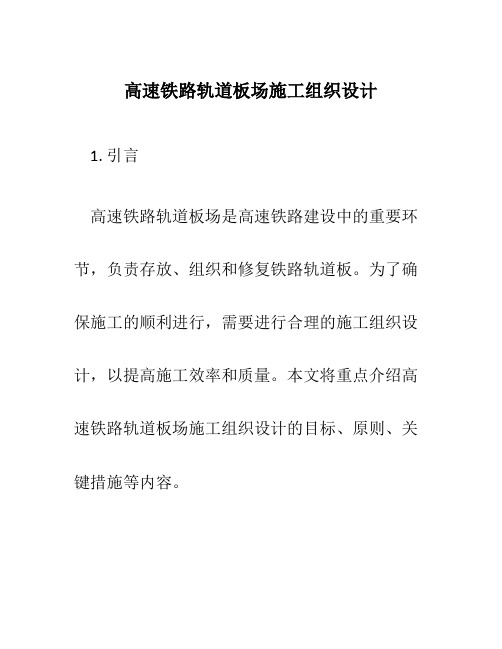
高速铁路轨道板场施工组织设计1. 引言高速铁路轨道板场是高速铁路建设中的重要环节,负责存放、组织和修复铁路轨道板。
为了确保施工的顺利进行,需要进行合理的施工组织设计,以提高施工效率和质量。
本文将重点介绍高速铁路轨道板场施工组织设计的目标、原则、关键措施等内容。
2. 目标高速铁路轨道板场施工组织设计的目标是确保轨道板的安全、高效、优质施工。
具体目标包括:•提高施工效率:通过合理的工程流程和组织方式,提高施工速度,缩短施工周期。
•保证施工质量:严格按照技术规范和施工标准进行施工,确保轨道板的质量符合要求。
•保障施工安全:制定安全操作规程,培训操作人员,确保施工过程中没有安全事故发生。
3. 原则高速铁路轨道板场施工组织设计应遵循以下原则:3.1 系统性原则施工组织设计需要考虑轨道板场整体的施工流程和流程之间的衔接,确保各个环节有机结合,形成一个高效、协调的施工系统。
施工组织设计应基于科学分析和评估,结合实际情况确定施工时序、资源配置和工作方式等。
设计过程中应充分考虑地质、气候、工期等因素,确保设计方案的可行性和科学性。
3.3 经济性原则施工组织设计应充分考虑资源利用效率和成本控制,实现最佳经济效益。
通过合理的施工流程和资源配置,降低施工成本,提高施工效率。
施工组织设计应确保施工人员的安全。
设计方案应考虑施工现场的安全要求,制定相应的安全操作规程,加强安全教育和培训,落实安全生产责任。
4. 关键措施为了实现高速铁路轨道板场施工组织设计的目标,需要采取一系列关键措施:4.1 工程流程设计根据施工任务和要求,确定施工流程,包括轨道板的调运、存放、组织施工和修复等环节。
为每个环节制定详细的工作方案和工序,明确各项工作的责任和时限。
4.2 人员培训和管理对轨道板场操作人员进行专业培训,提高操作技能和安全意识。
建立健全的人员管理制度,明确职责和权限,确保施工过程中的人员配备和配置。
4.3 资源配置合理配置施工所需的人力、物力和财力资源,确保施工过程中资源的充足和有效利用。
轨道板场建设方案(修改)

轨道板场建设⽅案(修改)⽬录⼀、板场概况 (1)⼆、总体施⼯设计 (2)2.1⽣产能⼒ (2)2.2 ⽣产车间 (2)2.3混凝⼟拌合站 (3)2.4主要⽣产流程设计 (3)三、场地总体规划 (8)3.1总平⾯布置 (8)3.2布局注意事项 (8)四、施⼯计划 (9)4.1总⼯期及开竣⼯⽇期 (9)4.2阶段性计划 (10)五、施⼯顺序 (10)六、施⼯⽅法 (11)6.1施⼯总平⾯布置 (11)6.1.1轨道板场场地布置原则 (11)6.1.2轨道板场布置说明 (12)6.2⼚房布置 (12)6.2.1 ⽣产车间施⼯ (13)6.2.2 打磨车间施⼯ (14)6.2.3 龙门吊基础 (14)6.2.4存板台施⼯ (14)6.2.5场内道路的布置 (14)6.2.6搅拌站施⼯ (15)6.2.7钢筋加⼯⼚房 (15)6.3其它临时设施布置 (15)6.3.1施⼯供电 (15)6.3.2施⼯通讯 (15)6.3.3施⼯供⽔ (16)6.3.4养⽣设施 (16)6.3.5⽣产、⽣活及办公⽤房 (16)6.3.6环保、卫⽣及⽂明施⼯设施 (16)6.3.7 施⼯围蔽 (17)七、⼈员配备 (17)⼋、设备需求 (18)九、重点⼯作项⽬ (19)⼗、附件 (20)⼀、板场概况本轨道板场位于⼭东省德州市齐河县⼤黄乡王邱村,与齐河制梁场毗邻,连通京沪⾼速铁路施⼯便道和316省道。
位于线路⾥程DK378+000处,采取板场与梁场结合建设的模式,板场总征地⾯积120亩,前期在梁场建设时已考虑后期板场建设的情况。
板场分成⼚房内作业的钢筋加⼯区、⽑坯板预制区、成品板打磨装配区、⼚房外的存板区、混凝⼟拌合站五⼤区,与梁场主要共⽤⽣活区、原材料存放场地、试验室、进场道路、⽔井和锅炉等六项。
具体情况见附图:齐河轨道板场平⾯布置图。
根据京沪总指确定的最新“京沪⾼铁Ⅱ型轨道板场设置⽅案”,中铁⼀局齐河轨道板场“需要量”为16000块。
轨道板生产厂的设计

CRTSⅡ型轨道板厂建厂方案及工装设备介绍1 概述轨道板制造采用易于保证产品质量的工厂化生产管理模式,配置机械化、自动化程度高的成套装备。
轨道板预制主要由毛坯板生产和承轨面磨削组成,毛坯板生产采用先张法长线台座生产工艺,承轨面磨削引入机加工理念,采用专用高精度数控磨床。
2 建厂设计内容根据总体要求和工程特点确定厂址;根据工程工期确定生产能力及相关技术经济指标;根据原材料及轨道板总体运输规划进行物流设计;根据工艺原理,科学经济实现生产工艺;根据工艺要求,合理配置装备及相关设施;各功能区设计。
3 建厂设计3.1 厂址选择根据运输条件,原材料条件,场地条件等方面的综合评估,确定了轨道板厂厂址3.2 产品结构基本型式轨道板的外形尺寸为6450mm×2550mm×200mm,为预应力混凝土结构,横向施加预应力(先张)、纵向无预应力。
每块用混凝土3.45m3。
预制轨道板采用先张法长线台座工艺生产,混凝土强度等级为C60。
轨道板的横向配有60根10mm预应力钢筋,纵向配有6根20mm精轧螺纹钢筋,板与板之间通过精轧螺纹钢筋进行了传力连接。
为防止轨道扣件处混凝土出现裂缝,在每个承轨台间都预设了预裂缝。
轨道扣件安装在承轨台上。
承轨台精确的几何尺寸是用数控磨床磨削加工出来的,加工精度为0.1mm。
轨道板连接示意图见下图645025503.3 产品工艺流程工艺流程图见下图标准轨道板工艺流程图3.4 设计能力根据工程量及施工工期以及轨道板生产的特点,轨道板生产在厂房内集中预制,实行工厂化施工管理;毛坯板采用先张法长线台座法生产,设三条生产线,每条生产线作业周期为24小时(其中作业时间8h,养护时间约16h),生产能力27块;采用三班作业制,每天生产半成品轨道板81块;成品板生产线以数控磨床为中心,亦采用三班作业制,每班打磨成品轨道板24-30块,每天打磨70-90块,存板能力约8000块(现有轨道板厂)。
CRTSⅡ型板式无砟轨道预制板场建场规划设计

4、生产能力设计
4.3生产能力设计 通过以上的结论得出,生产车间设置3条生产线,每条 生产线配备24块模具,即设计每天最大预制毛坯板72 块,能够满足要求。
5、厂房平面布置设计
根据分区原则、匹配原则和经济原则,生产区
厂房平面布局可以有“Z”型和“U”型布置。
6、总体规划设计
(3)钢筋加工厂区
钢筋加工厂房内配备2台5t的电动单梁桥式起重机,设 置钢筋存放区、网片加工区,网片加工区设上、下层钢 筋绑扎台位各4个,3个热缩管加工台位, 4个钢筋网片 存放台位等。钢筋加工车间与轨道板预制车间采用2台 横移小车运送钢筋网片。
钢筋区平面设计
6、总体规划设计
考虑Ⅱ型板生产各工序间流水作业要求,各功能区的衔接设置了纵横向轨道
和运输小车以及翻转机和滚轮运输线等装置;为保证混凝土生产环境条件和 磨床工作环境条件的适宜性,设置了供电系统、供热系统、供气系统、供水
系统及水循环处理系统等配套辅助设施。
(2)办公生活区:在场区内设置办公生活区,主要满足人员办公与生活需要。 (3)道路:为确保场区物流顺畅,在分区间设置场区道路,主要道路路宽
9m、次要道路路宽6m。
6、总体规划设计
6.2设计参数 最大制板能力:72块/天;毛坯板存板能力:3432块; 成品板存板能力:6723块。
6、总体规划设计
6.3物流组织
钢筋在钢筋加工车间加工成钢筋网片后,通过横向
运输车直接运送到轨道板预制车间,运输过程与其 他生产环节互不影响。
方便布置设计。
6、总体规划设计
(1)厂房设计
厂房整体结构采用钢框架结构,两跨布置,局部一跨。 其中生产主厂房(轨道板预制车间)长264米,一侧连 跨钢筋加工厂房96米长,同侧另一端连跨打磨厂房66米
高铁轨道板场建场方案
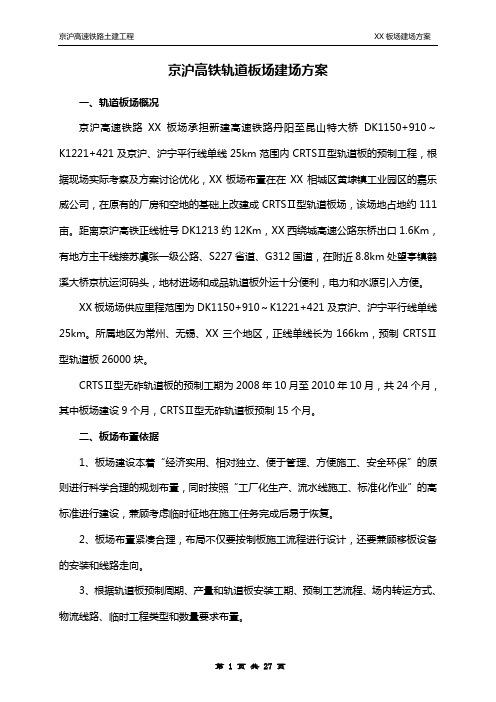
京沪高铁轨道板场建场方案一、轨道板场概况京沪高速铁路XX板场承担新建高速铁路丹阳至昆山特大桥DK1150+910~K1221+421及京沪、沪宁平行线单线25km范围内CRTSⅡ型轨道板的预制工程,根据现场实际考察及方案讨论优化,XX板场布臵在在XX相城区黄埭镇工业园区的嘉乐威公司,在原有的厂房和空地的基础上改建成CRTSⅡ型轨道板场,该场地占地约111亩。
距离京沪高铁正线桩号DK1213约12Km,XX西绕城高速公路东桥出口1.6Km,有地方主干线接苏虞张一级公路、S227省道、G312国道,在附近8.8km处望亭镇鹤溪大桥京杭运河码头,地材进场和成品轨道板外运十分便利,电力和水源引入方便。
XX板场场供应里程范围为DK1150+910~K1221+421及京沪、沪宁平行线单线25km。
所属地区为常州、无锡、XX三个地区,正线单线长为166km,预制CRTSⅡ型轨道板26000块。
CRTSⅡ型无砟轨道板的预制工期为2008年10月至2010年10月,共24个月,其中板场建设9个月,CRTSⅡ型无砟轨道板预制15个月。
二、板场布臵依据1、板场建设本着“经济实用、相对独立、便于管理、方便施工、安全环保”的原则进行科学合理的规划布臵,同时按照“工厂化生产、流水线施工、标准化作业”的高标准进行建设,兼顾考虑临时征地在施工任务完成后易于恢复。
2、板场布臵紧凑合理,布局不仅要按制板施工流程进行设计,还要兼顾移板设备的安装和线路走向。
3、根据轨道板预制周期、产量和轨道板安装工期、预制工艺流程、场内转运方式、物流线路、临时工程类型和数量要求布臵。
三、板场的建设设计3.1生产能力的设计根据预制CRTSⅡ型轨道板26000块的总工程量,轨道板毛坯板正式生产工期按14个月计算,考虑其他不利因素,每月有效工作日24天,按每天一模计算:26000块÷(14月×24天/月)=77块,拟投入81套模板满足毛坯板生产需要。
- 1、下载文档前请自行甄别文档内容的完整性,平台不提供额外的编辑、内容补充、找答案等附加服务。
- 2、"仅部分预览"的文档,不可在线预览部分如存在完整性等问题,可反馈申请退款(可完整预览的文档不适用该条件!)。
- 3、如文档侵犯您的权益,请联系客服反馈,我们会尽快为您处理(人工客服工作时间:9:00-18:30)。
*****轨道板厂设置方案一、工程概况京沪高速铁路地处我国经济最为发达、综合经济实力最强、最具发展活力的东部地区,纵贯北京、天津、上海三大直辖市和河北、山东、安徽、江苏四省,直接联结16个超过100万人的大城市,全长1318km 。
京沪高速正线设计时速为350km/h。
按照**指的任务划分,我十工区负责****段线路无砟轨道的预制、安装任务,线路总长44.765km;轨道板预制数量为19897块。
轨道板型号暂定为I型轨道板,长4.95m,宽2.4m,高0.19m,重量约为5.7t。
根据指挥部要求建厂日期为2008.7.1~2008.12.31,工期为6个月;生产日期为2009.1.1~2010.1.31,工期为13个月;安装日期为2009.5.9~2010.3.27,工期为10个月。
二、板厂选址为了将轨道板厂建在最合适的位置,我工区进行了详细的施工调查,对位于投标文件中****处***所在地、位于****。
三、建厂方案按轨道板预制工期13个月、每月26天考虑,则平均每天需要生产轨道板19897块÷13月×26天/月)=59块/天。
轨道板预制周期为24小时,计划配备模板共60套,即轨道板生产区的设计生产能力为60块/天,可以满足施工需要。
为此,对构件二厂进行改造,利用其中一部分的区域进行轨道板的生产、堆存。
1、总体布置图轨道板预制厂分为生产区、存板区、办公生活区。
轨道板生产区按施工工艺流程划分为:原材料存放区、混凝土拌和楼、钢筋加工区、轨道板灌注蒸养区、质量检验区、湿润养护区、预应力施加及封端区、成品检查存放区。
各工序的物流衔接采用桥吊、龙门吊、专用运输车等机械完成,各工区根据自身特点配备专用的生产加工机具。
办公生活区按功能设置办公室、配电室、物资仓库、试验室、住宿区、食堂及卫生所等。
轨道板生产线和钢筋加工生产线分别布置在二个钢结构厂房内。
每条轨道板生产线分别配置2台16t桁吊、30套模具;钢筋加工生产线配备1套钢筋加工设备及14套绑扎胎具;利用搅拌楼的一台2m3搅拌机作为轨道板混凝土生产的专用搅拌机,轨道板在湿润养生后运至存板区分组存放;存板区存板能力设计为6000块;厂内道路与地方道路连通,方便原材料进厂,轨道板成品出厂利用码头进行水上运输至现场;办公生活区内设办公室、试验室、食堂及职工宿舍;场内还设置了配电房、材料仓库等。
详见构件二厂平面布置图。
2、各功能区的设计及说明轨道板预制厂平面布置规划说明如下:(1)生产区原材料存放区:主要有材料库、钢筋堆放场地、外加剂和脱模剂仓库、露天砂石料堆放场和保温砂石筒仓等。
砂石按直径5~10mm、10~25mm两种分级存放,砂石存放区修建遮雨棚,避免砂石日晒雨淋,利用其中六只筒仓分别存放砂石料,每只筒仓的容量为300 m3。
筒仓内设保温维护结构和内部加温设施。
混凝土拌和楼:新建搅拌楼一座,设有2m3搅拌机二台,为确保轨道板能按期完成生产任务,利用其中一台搅拌机专门拌制轨道板混凝土。
混凝土拌和好后通过混凝土运输车送到布料机内,通过布料机进行混凝土灌注。
拌合站采用散装水泥,拌合楼设置3.3×6水泥罐4个(二个为轨道板专用),水泥由汽车运输打入水泥罐内,拌合楼另设外掺料罐6个(二个为轨道板专用)。
轨道板预制区:在两个长120、宽33m的钢结构车间内设轨道板预制生产线、成品质量检测区、轨道板湿润养护区张拉封堵区,在生产车间形成流水作业。
钢筋加工生产线:分别设置两个车间内,车间与车间之间相通,面积为1600m2,内设钢筋存放、加工、绑扎区和成品骨架存储区。
钢筋生产线内的成品骨架由16t桁吊整体吊装入模。
(2)办公生活区主要有办公室、试验室和职工宿舍及停车场等生活配套设施。
(3)存板区根据安装的进度要求,为10个月,轨道板储存期按半个月考虑,则轨道板铺设期间预制厂的生产量为(10-0.5)月×26天/月×60块/天=14820块,则存板区的理论存板量应为19897-14820=5077块,设计存板能力为5200块,可以满足施工需要。
存板区面积为7500m2,分两个区域,区域内设置一部轮轨式40t门机,进行轨道板成品的搬运与出运工作。
(4)其他设施预制厂内还设置材料库房、工具间、蒸养控制室及配电房等,用于生产配套服务等。
3、水电等辅助设施的说明预制厂内施工、生活用水均接驳当地自来水供应网络。
轨道板混凝土由设在预制厂内的搅拌楼供应。
电由当地供电网络引入,厂内设置配电房,生活、生产区单独配线供应。
(1)水水的需求主要是搅拌站、蒸汽养护、养生池用水、生活用水四个方面。
厂内有自来水管路,进行重新编排,能满足轨道板的生产要求。
(2)电轨道板生产主要用电设备是搅拌站、4部16t桥吊、1部40t门机、钢筋加工制作设备、高频振动器、生活用电等,总功率在700KW以内,厂内配电间容量为1250KV A,能满足轨道板的生产要求。
(3)蒸汽养护用蒸汽由厂附近的热电厂通过管道提供,蒸汽管道在厂建时沿制板台预埋,每个台座采用阀门单独控制。
4、生产厂房的总体布置设计4.1平面和截面布置形式及尺寸轨道板预制和钢筋加工生产线、轨道板成品检查和湿润养护区均设在钢结构厂房内,厂房净跨为33m,总长度为120m,高度为13.16桁吊吊钩至地面高度为6.8m,详细布置见图二:轨道板车间平面布置示意图。
4.2生产线的结构设计4.2.1轨道板预制生产线如图二所示,2条生产线并列布置,每条生产线工设置30套模具,台座均匀布置。
模板采用定型厂制钢模,底模采用预埋高强螺栓固定在台座上,侧模和端模采用铰接方式连接在底模上,可侧向旋开,方便拆模。
钢筋骨架由桁吊吊装入模,预埋件在制板台座上安装,并采用特制的预埋件固定装置固定在底模上,以保证其平位置和垂直度。
混凝土采用变频底振工艺,装配式高频振动器悬挂在底模上,由高频转换器控制其振动频率。
高频转换器放置在移动台架上,每条生产线配备4台,分别控制8台高频振动器。
轨道板拆模由专用千斤顶配合桁吊完成:首先松开侧模,装上支压板,采用千斤顶支承在支压板上将轨道板顶起6~8mm,再由桁吊将轨道板移至成品检测区。
4.2.2钢筋加工生产线钢筋加工生产线分别布置在轨道板生产车间的一侧,包括原材料存放区、钢筋切割区、钢筋弯制区、钢筋绑扎区成品骨架存放区,配备1台钢筋切断机和2台钢筋弯曲机,专用钢筋绑扎胎具14套。
根据配筋图进行钢筋下料,弯制,半成品放置在专用移动式台架上推至绑扎区,利用专用钢筋胎具进行绑扎。
成品骨架由桁吊吊至存放区或直接吊装入模。
4.2.3成品检测区和湿润养护区成品检测区内设18个检测台座,检测台座采用钢筋混凝土制成,用于成品检查、标识等。
轨道板检查合格并标识完毕后,由桁吊吊至湿润养护区进行二次养护,二次养护可采用水池养护。
每个车间设置养护池一只,每只养护池可养护120—140块轨道板。
4.3与生产线有关的供热设计采用一套自动温控设备进行蒸汽养生,主管道沿台座纵向布置,每个台座布置2根支蒸汽管道,均采用阀门单独控制。
5.生产线的详细设计5.1主要工艺模板采用钢丝刷和高压风清理、每次使用前均进行检查以确保变形量处在允许误差之内。
钢筋在加工区内下料、弯制并绑扎成型后,由16t桁吊提升放入已经清理、检查完毕的模板内,安装预埋件,自检合格后报请质量工程师检查,确认达到技术要求后浇筑混凝土。
混凝土出料时由串筒直接放料至料斗内,并通过横移滑道运输至轨道板生产线内,再由桁吊提升浇筑,高频转换器配合高频振动器完成振捣工艺,人工抹面并刷毛。
混凝土浇筑完毕后,静停4h,进行蒸汽养生,采用自动温控设备进行温度调节,确保养护温度和温度满足技术要求。
蒸养结束后自然降温至室温,确认同条件养护试件满足强度要求后进行拆模作业,拆模由专用千斤顶和桁吊配合进行。
轨道板预制周期为24h。
轨道板拆模后立即运至成品检测区,经检查合格并标识完毕后移至养护水池内进行二次养护,湿润养护结束后运至存板区内存放,分层堆放,不超过四层。
对达到强度的轨道板进行张拉封堵。
5.2制造设备及说明表5-1 主要设备配置表6.生产厂的投资分析轨道板预制厂的主要投资包括土建、钢结构厂房、机械设备、试验仪器和检验器具等,具体分析如表6-1所示。
表6-1 轨道板预制厂投资分析表单位:元7、原材料运输砂石料通过黄浦江船运至砂石料上料码头,码头可停靠2000t的船;钢筋、水泥等原材料通过汽车运至厂内。
8、轨道板成品吊装、贮存与运输为防止轨道板变形,减少占地,轨道板的储存、堆放采用侧立放置的形式。
储存台位两端采用三角支撑固定,板块之间采用“U”形卡连接,以防板块倾倒。
起吊前,将轨道板翻转成“平置”状态,避免碰上轨道板。
起吊时,用40t起重机四点起吊,平放在上,直接吊运至船上。
轨道板运输时,四层平放,并采用适当的加固材料进行加固,限制运输过程中轨道板纵向和横向位移。
由于轨道板安装速度快于预制速度,所以在安装前必须有大量的储备,才能满足后期安装工期要求。
轨道板主要安排在堆场储存,并在沿线桥梁预制场作分散储存;在安装前2~3天在线路两侧临时储存,为轨道板连续安装作好充分准备。
通过厂内码头由黄浦江经蕴藻浜运至位于主线DK1289+600处的蕴藻浜(可通航800t船)码头,运距40km。
四、综合评价综上所述,该场地作为轨道板厂有以下几个优点:节省部分土地租用费用,砂、石等材料运输装卸堆存可利用现有码头和堆场;办公楼、试验室及综合生活设施不需再次投入;该场地原为预制厂,改建轨道板厂后用地性质不变,环保能满足要求。
根据,另外厂房建设完成后可作为永久性基地为规划中的城际高速铁路提供产品,也响应了铁道部工管中心成立专业划轨道板厂的要求。
缺点:运输成本增加。
通过以上分析,我工区将*****作为轨道板生产基地,请指挥部批准!。