注塑零件翘曲变形机理
塑料制品的翘曲变形

塑料制品的翘曲变形一. 翘曲变形是指注塑制品的形状偏离了模具型腔的形状,它是塑料制品常见的缺陷之一。
出现翘曲变形的原因很多,单靠工艺参数解决往往力不从心。
结合相关资料和实际工作经验,下面对影响注塑制品翘曲变形的因素作简要分析。
二、模具的结构对注塑制品翘曲变形的影响。
在模具方面,影响塑件变形的因素主要有浇注系统、冷却系统与顶出系统等。
1.浇注系统注塑模具浇口的位置、形式和浇口的数量将影响塑料在模具型腔内的填充状态,从而导致塑件产生变形。
流动距离越长,由冻结层与中心流动层之间流动和补缩引起的内应力越大;反之,流动距离越短,从浇口到制件流动末端的流动时间越短,充模时冻结层厚度减薄,内应力降低,翘曲变形也会因此大为减少。
一些平板形塑件,如果只使用一个中心浇口,因直径方向上的收缩率大于圆周方向上的收缩率,成型后的塑件会产生扭曲变形;若改用多个点浇口或薄膜型浇口,则可有效地防止翘曲变形。
当采用点浇口进行成型时,同样由于塑料收缩的异向性,浇口的位置、数量都对塑件的变形程度有很大的影响。
另外,多浇口的使用还能使塑料的流动比(L/t)缩短,从而使模腔内熔体密度更趋均匀,收缩更均匀。
同时,整个塑件能在较小的注塑压力下充满。
而较小的注射压力可减少塑料的分子取向倾向,降低其2.冷却系统在注射过程中,塑件冷却速度的不均匀也将形成塑件收缩的不均匀,这种收缩差别导致弯曲力矩的产生而使塑件发生翘曲。
如果在注射成型平板形塑件(如手机电池壳)时所用的模具型腔、型芯的温度相差过大,由于贴近冷模腔面的熔体很快冷却下来,而贴近热模腔面的料层则会继续收缩,收缩的不均匀将使塑件翘曲。
因此,注塑模的冷却应当注意型腔、型芯的温度趋于平衡,两者的温差不能太大(此时可考虑使用两个模温机). 除了考虑塑件内外表的温度趋于平衡外,还应考虑塑件各侧的温度一致,即模具冷却时要尽量保持型腔、型芯各处温度均匀一致,使塑件各处的冷却速度均衡,从而使各处的收缩更趋均匀,有效地防止变形的产生。
注塑制品翘曲变形原因分析

注塑制品翘曲变形原因分析注塑制品翘曲变形是指注塑制品的形状偏离了模具型腔的形状,它是塑料制品常见的缺陷之一。
随着塑料工业的发展,人们对塑料制品的外观和使用性能要求越来越高,翘曲变形程度作为评定产品质量的重要指标之一也越来越多地受到模具设计者的关注与重视。
模具设计者希望在设计阶段预测出塑料件可能产生翘曲的原因,以便加以优化设计,从而提高注塑生产的效率和质量,缩短模具设计周期,降低成本。
本文主要对在注塑模具设计过程中影响注塑制品翘曲变形的因素加以分析。
●模具的结构对注塑制品翘曲变形的影响在模具设计方面,影响塑件变形的因素主要有浇注系统、冷却系统与顶出系统等。
1.浇注系统的设计注塑模具浇口的位置、形式和浇口的数量将影响塑料在模具型腔内的填充状态,从而导致塑件产生变形。
流动距离越长,由冻结层与中心流动层之间流动和补缩引起的内应力越大;反之,流动距离越短,从浇口到制件流动末端的流动时间越短,充模时冻结层厚度减薄,内应力降低,翘曲变形也会因此大为减少。
图1为大型平板形塑件,如果只使用一个中心浇口(如图1a所示)或一个侧浇口(如图1b所示),因直径方向上的收缩率大于圆周方向上的收缩率,成型后的塑件会产生扭曲变形;若改用多个点浇口或薄膜型浇口,则可有效地防止翘曲变形。
a) 中心浇口b) 侧浇口c)多点浇口d) 薄膜型浇口当采用点浇进行成型时,同样由于塑料收缩的异向性,浇口的位置、数量都对塑件的变形程度有很大的影响。
a)直浇口b)10个点浇口c)8个点浇口d)4个点浇口e) 6个点浇口f) 4个点浇口由于采用的是30%玻璃纤维增强PA6,而得到的是重量为4.95kg的大型注塑件,因此沿四周壁流动方向上设有许多加强肋,这样,对各个浇口都能获得充分的平衡。
实验结果表明,按图f设置浇口具有较好的效果。
但并非浇口数目越多越好。
实验证明,按图c设计的浇口比图a的直浇口还差。
另外,多浇口的使用还能使塑料的流动比(L/t)缩短,从而使模腔内物料密度更趋均匀,收缩更均匀。
注塑模具制品的翘曲、变形原因及解决方法

注塑模具制品的翘曲、变形原因及解决方法
注塑成型是批量生产某些形状复杂部件时用到的一种加工方法。
具体指将受热融化的材料由高压射入模腔,经冷却固化后,得到成形品。
出现的翘曲、变形问题主要应从注塑模具设计方面解决,而成型条件的调整效果则是很有限的。
东莞恒圣塑胶实业有限公司专业为您介绍以下是翘曲、变形的原因及解决方法:
一、由成型条件引起残余应力造成变形时,可通过降低注射压力、提高注塑模具温度,并使注塑模具温度均匀,及提高树脂温度或采用退火方法予以消除应力。
二、脱模不良引起应力变形时,可通过增加推杆数量或面积、设置脱模斜度等方法加以解决。
三、由于冷却方法不合适,使冷却不均匀或冷却时间不足时,可调整冷却方法及延长冷却时间等。
四、对于成型收缩所引起的变形,就必须修正注塑模具的设计。
最重要的是应注意使制品壁厚一致。
关键词:模具加工,大型模具加工,大型注塑产品,注塑机产品。
塑料翘曲、弯曲和扭曲原因
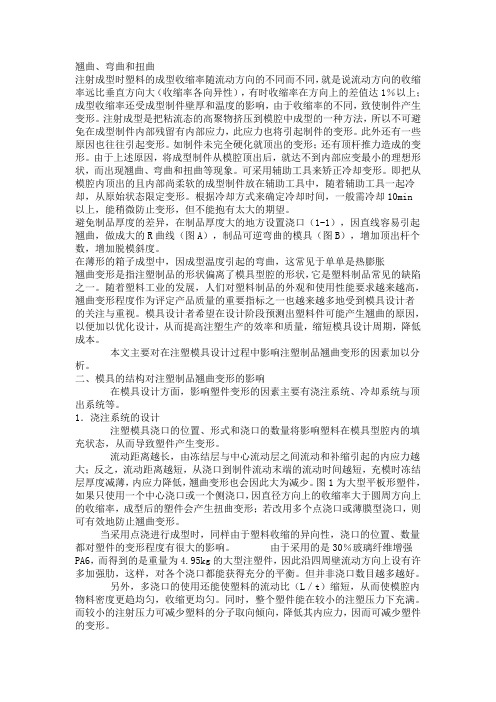
翘曲、弯曲和扭曲注射成型时塑料的成型收缩率随流动方向的不同而不同,就是说流动方向的收缩率远比垂直方向大(收缩率各向异性),有时收缩率在方向上的差值达1%以上;成型收缩率还受成型制件壁厚和温度的影响,由于收缩率的不同,致使制件产生变形。
注射成型是把粘流态的高聚物挤压到模腔中成型的一种方法,所以不可避免在成型制件内部残留有内部应力,此应力也将引起制件的变形。
此外还有一些原因也往往引起变形。
如制件未完全硬化就顶出的变形;还有顶杆推力造成的变形。
由于上述原因,将成型制件从模腔顶出后,就达不到内部应变最小的理想形状,而出现翘曲、弯曲和扭曲等现象。
可采用辅助工具来矫正冷却变形。
即把从模腔内顶出的且内部尚柔软的成型制件放在辅助工具中,随着辅助工具一起冷却,从原始状态限定变形。
根据冷却方式来确定冷却时间,一般需冷却10min以上,能稍微防止变形,但不能抱有太大的期望。
避免制品厚度的差异,在制品厚度大的地方设置浇口(1-1),因直线容易引起翘曲,做成大的R曲线(图A),制品可逆弯曲的模具(图B),增加顶出杆个数,增加脱模斜度。
在薄形的箱子成型中,因成型温度引起的弯曲,这常见于单单是热膨胀翘曲变形是指注塑制品的形状偏离了模具型腔的形状,它是塑料制品常见的缺陷之一。
随着塑料工业的发展,人们对塑料制品的外观和使用性能要求越来越高,翘曲变形程度作为评定产品质量的重要指标之一也越来越多地受到模具设计者的关注与重视。
模具设计者希望在设计阶段预测出塑料件可能产生翘曲的原因,以便加以优化设计,从而提高注塑生产的效率和质量,缩短模具设计周期,降低成本。
本文主要对在注塑模具设计过程中影响注塑制品翘曲变形的因素加以分析。
二、模具的结构对注塑制品翘曲变形的影响在模具设计方面,影响塑件变形的因素主要有浇注系统、冷却系统与顶出系统等。
1.浇注系统的设计注塑模具浇口的位置、形式和浇口的数量将影响塑料在模具型腔内的填充状态,从而导致塑件产生变形。
塑料翘曲变形的原因
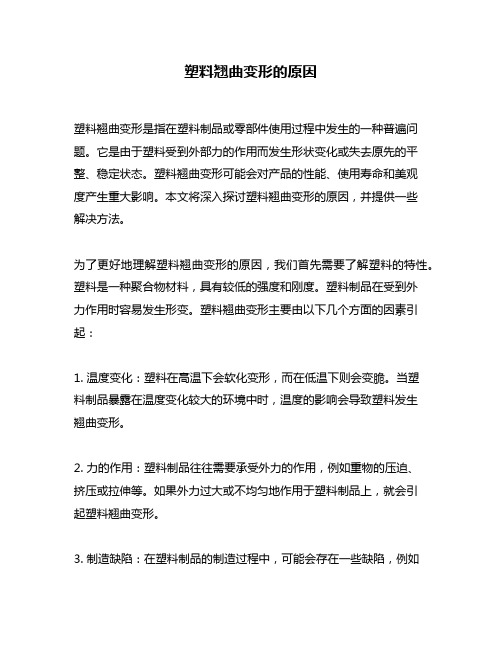
塑料翘曲变形的原因塑料翘曲变形是指在塑料制品或零部件使用过程中发生的一种普遍问题。
它是由于塑料受到外部力的作用而发生形状变化或失去原先的平整、稳定状态。
塑料翘曲变形可能会对产品的性能、使用寿命和美观度产生重大影响。
本文将深入探讨塑料翘曲变形的原因,并提供一些解决方法。
为了更好地理解塑料翘曲变形的原因,我们首先需要了解塑料的特性。
塑料是一种聚合物材料,具有较低的强度和刚度。
塑料制品在受到外力作用时容易发生形变。
塑料翘曲变形主要由以下几个方面的因素引起:1. 温度变化:塑料在高温下会软化变形,而在低温下则会变脆。
当塑料制品暴露在温度变化较大的环境中时,温度的影响会导致塑料发生翘曲变形。
2. 力的作用:塑料制品往往需要承受外力的作用,例如重物的压迫、挤压或拉伸等。
如果外力过大或不均匀地作用于塑料制品上,就会引起塑料翘曲变形。
3. 制造缺陷:在塑料制品的制造过程中,可能会存在一些缺陷,例如气泡、疏松区域或不均匀的厚度等。
这些制造缺陷会导致塑料制品在使用过程中容易发生翘曲变形。
4. 冷却不均匀:在塑料制品的加工过程中,冷却是一个重要的环节。
如果冷却不均匀或过快,就会导致塑料材料产生内部应力,从而引起翘曲变形。
那么,如何解决塑料翘曲变形问题呢?以下是一些建议:1. 选择合适的塑料材料:不同的塑料材料具有不同的特性,如强度、刚度和耐温性等。
在设计和选择塑料制品时,需要考虑到使用环境的要求,并选择合适的塑料材料来减少翘曲变形的可能性。
2. 改善制造工艺:优化塑料制品的制造工艺,确保塑料材料均匀冷却和充分固化。
这有助于减少内部应力和制造缺陷,从而降低翘曲变形的风险。
3. 增加支撑结构:对于长而细的塑料制品,在设计时可以增加合适的支撑结构,以增强整体的强度和稳定性,减少翘曲变形的可能性。
4. 控制使用环境:在使用塑料制品时,需要控制使用环境的温度和湿度。
避免过高或过低的温度对塑料造成不利影响,同时注意湿度对塑料的吸湿性。
制件翘起的知识
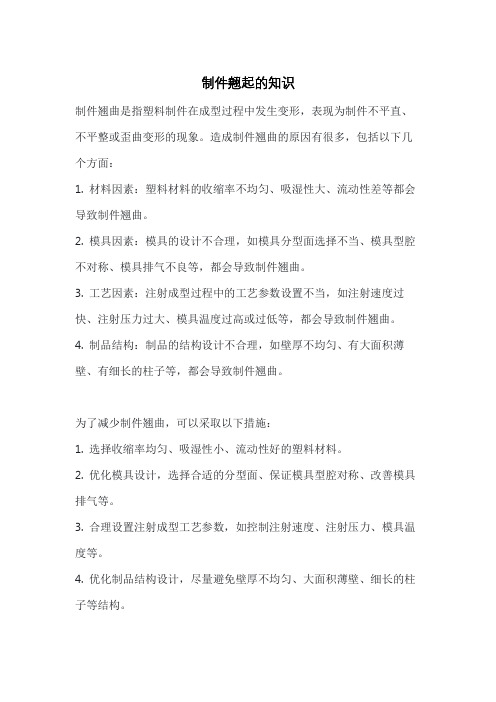
制件翹起的知识
制件翘曲是指塑料制件在成型过程中发生变形,表现为制件不平直、不平整或歪曲变形的现象。
造成制件翘曲的原因有很多,包括以下几个方面:
1. 材料因素:塑料材料的收缩率不均匀、吸湿性大、流动性差等都会导致制件翘曲。
2. 模具因素:模具的设计不合理,如模具分型面选择不当、模具型腔不对称、模具排气不良等,都会导致制件翘曲。
3. 工艺因素:注射成型过程中的工艺参数设置不当,如注射速度过快、注射压力过大、模具温度过高或过低等,都会导致制件翘曲。
4. 制品结构:制品的结构设计不合理,如壁厚不均匀、有大面积薄壁、有细长的柱子等,都会导致制件翘曲。
为了减少制件翘曲,可以采取以下措施:
1. 选择收缩率均匀、吸湿性小、流动性好的塑料材料。
2. 优化模具设计,选择合适的分型面、保证模具型腔对称、改善模具排气等。
3. 合理设置注射成型工艺参数,如控制注射速度、注射压力、模具温度等。
4. 优化制品结构设计,尽量避免壁厚不均匀、大面积薄壁、细长的柱子等结构。
总之,制件翘曲是塑料成型过程中常见的问题,需要从材料、模具、工艺和制品结构等方面综合考虑,采取相应的措施来减少或避免。
塑料制品的翘曲变形的原因分析和解决方法图文稿
塑料制品的翘曲变形的原因分析和解决方法集团文件版本号:(M928-T898-M248-WU2669-I2896-DQ586-M1988)塑料制品的翘曲变形的原因分析和解决方法一、前言翘曲变形是指注塑制品的形状偏离了模具型腔的形状,它是塑料制品常见的缺陷之一。
出现翘曲变形的原因很多,单靠工艺参数解决往往力不从心。
结合相关资料和实际工作经验,下面对影响注塑制品翘曲变形的因素作简要分析。
二、模具的结构对注塑制品翘曲变形的影响。
在模具方面,影响塑件变形的因素主要有浇注系统、冷却系统与顶出系统等。
1.浇注系统注塑模具浇口的位置、形式和浇口的数量将影响塑料在模具型腔内的填充状态,从而导致塑件产生变形。
流动距离越长,由冻结层与中心流动层之间流动和补缩引起的内应力越大;反之,流动距离越短,从浇口到制件流动末端的流动时间越短,充模时冻结层厚度减薄,内应力降低,翘曲变形也会因此大为减少。
一些平板形塑件,如果只使用一个中心浇口,因直径方向上的收缩率大于圆周方向上的收缩率,成型后的塑件会产生扭曲变形;若改用多个点浇口或薄膜型浇口,则可有效地防止翘曲变形。
当采用点浇口进行成型时,同样由于塑料收缩的异向性,浇口的位置、数量都对塑件的变形程度有很大的影响。
另外,多浇口的使用还能使塑料的流动比(L/t)缩短,从而使模腔内熔体密度更趋均匀,收缩更均匀。
同时,整个塑件能在较小的注塑压力下充满。
而较小的注射压力可减少塑料的分子取向倾向,降低其内应力,因而可减少塑件的变形。
2. 冷却系统在注射过程中,塑件冷却速度的不均匀也将形成塑件收缩的不均匀,这种收缩差别导致弯曲力矩的产生而使塑件发生翘曲。
如果在注射成型平板形塑件(如手机电池壳)时所用的模具型腔、型芯的温度相差过大,由于贴近冷模腔面的熔体很快冷却下来,而贴近热模腔面的料层则会继续收缩,收缩的不均匀将使塑件翘曲。
因此,注塑模的冷却应当注意型腔、型芯的温度趋于平衡,两者的温差不能太大(此时可考虑使用两个模温机)。
翘曲变形原因
翘曲变形原因统计第一种说法:注塑件的翘曲、变形是很棘手的问题,主要应从模具的设计方面着手解决,而成型条件的调整效果则是很有限的,翘曲变形的原因及解决方法可以参照以下各项;1)由成型条件引起残余应力造成变形时,可通过降低注射压力,提高模具温度并使模具温度均匀及提高树脂温度或采用退火方法予以消除应力。
2)脱模不良引起应力时,可通过增加推杆数量或面积、设置脱模斜度等方法加以解决。
3)由于冷却方法不合适,使冷却不均匀或冷却时间不足时,可调整冷却方法及延长冷却时间等。
例如,尽可能地在贴近变形的地方设置冷却回路。
4)对于成型收缩引起的变形,就必须修正模具的设计了,其中,最重要的是应注意使制品的壁厚一致。
有时,再不得已的情况下,只好测量制品的变形,按相反的方向修正模具,加以校正。
一般结晶性树脂(POM/PA/PP/PET等)比非结晶性树脂(如PMMA,PVC,PS,ABS,AS)的变形大。
另外,由于玻璃纤维增强树脂具有纤维配向性,变形也大。
第二种说法:一模具方面:(1)浇口位置不当或数量不足。
(2)顶出位置不当或制品受力不均匀。
二工艺方面:(1)模具、机筒温度太高。
(2)注射压力太高或注射速度太快。
(3)保压时间太长或冷却时间太短。
三原料方面:酞氰系颜料会影响聚乙烯的结晶度而导致制品变形。
四制品设计方面:(1)壁厚不均,变化突然或壁厚过小。
(2)制品结构造型不当。
第三种说法:肉厚不均、冷却不均。
塑胶的冷却速度不一样,冷却快的地方收缩小,冷却慢的地方收缩大,从而发生变形。
☐料温高,收缩大,从而变形大。
☐分子排向差异;侧壁的内弯曲。
☐制品脱模时的内部应力所致的变形,是制品未充分冷却固化前从模具顶出所致。
☐一般为防止制品变形,可在顶出后,用夹具对制品定型,矫正变形或防止进一步的变形,但制品在使用中若再次碰到高温时又会复原,对此点需特别加以注意。
第四种说法:如果制件的收缩均匀,那么成型件不会发生变形或翘曲,只是单纯地变小了。
翘曲变形原因
翘曲变形原因统计第一种说法:注塑件的翘曲、变形是很棘手的问题,主要应从模具的设计方面着手解决,而成型条件的调整效果则是很有限的,翘曲变形的原因及解决方法可以参照以下各项;1)由成型条件引起残余应力造成变形时,可通过降低注射压力,提高模具温度并使模具温度均匀及提高树脂温度或采用退火方法予以消除应力。
2)脱模不良引起应力时,可通过增加推杆数量或面积、设置脱模斜度等方法加以解决。
3)由于冷却方法不合适,使冷却不均匀或冷却时间不足时,可调整冷却方法及延长冷却时间等。
例如,尽可能地在贴近变形的地方设置冷却回路。
4)对于成型收缩引起的变形,就必须修正模具的设计了,其中,最重要的是应注意使制品的壁厚一致。
有时,再不得已的情况下,只好测量制品的变形,按相反的方向修正模具,加以校正。
一般结晶性树脂(POM/PA/PP/PET等)比非结晶性树脂(如PMMA,PVC,PS,ABS,AS)的变形大。
另外,由于玻璃纤维增强树脂具有纤维配向性,变形也大。
第二种说法:一模具方面:(1)浇口位置不当或数量不足。
(2)顶出位置不当或制品受力不均匀。
二工艺方面:(1)模具、机筒温度太高。
(2)注射压力太高或注射速度太快。
(3)保压时间太长或冷却时间太短。
三原料方面:酞氰系颜料会影响聚乙烯的结晶度而导致制品变形。
四制品设计方面:(1)壁厚不均,变化突然或壁厚过小。
(2)制品结构造型不当。
第三种说法:肉厚不均、冷却不均。
塑胶的冷却速度不一样,冷却快的地方收缩小,冷却慢的地方收缩大,从而发生变形。
☐料温高,收缩大,从而变形大。
☐分子排向差异;侧壁的内弯曲。
☐制品脱模时的内部应力所致的变形,是制品未充分冷却固化前从模具顶出所致。
☐一般为防止制品变形,可在顶出后,用夹具对制品定型,矫正变形或防止进一步的变形,但制品在使用中若再次碰到高温时又会复原,对此点需特别加以注意。
第四种说法:如果制件的收缩均匀,那么成型件不会发生变形或翘曲,只是单纯地变小了。
(完整版)塑料制品的翘曲变形的原因分析和解决方法
塑料制品的翘曲变形的原由剖析和解决方法一、序言翘曲变形是指注塑制品的形状偏离了模具型腔的形状,它是塑料制品常有的缺点之一。
出现翘曲变形的原由好多,单靠工艺参数解决常常力所不及。
联合有关资料和实质工作经验,下边对影响注塑制品翘曲变形的要素作简要剖析。
二、模具的构造对注塑制品翘曲变形的影响。
在模具方面,影响塑件变形的要素主要有浇注系统、冷却系统与顶出系统等。
1.浇注系统注塑模具浇口的地点、形式和浇口的数目将影响塑料在模具型腔内的填补状态,从而以致塑件产生变形。
流动距离越长,由冻结层与中心流动层之间流动和补缩惹起的内应力越大;反之,流动距离越短,从浇口到制件流动尾端的流动时间越短,充模时冻结层厚度减薄,内应力降低,翘曲变形也会所以大为减少。
一些平板形塑件,假如只使用一其中心浇口,因直径方向上的缩短率大于圆周方向上的缩短率,成型后的塑件会产生歪曲变形;若改用多个点浇口或薄膜型浇口,则可有效地防备翘曲变形。
当采纳点浇口进行成型时,相同因为塑料缩短的异向性,浇口的地点、数目都对塑件的变形程度有很大的影响。
L/t )缩短,从而使模腔内熔体密度更趋平均,缩短此外,多浇口的使用还可以使塑料的流动比(更平均。
同时,整个塑件能在较小的注塑压力下充满。
而较小的注射压力可减少塑料的分子取向偏向,降低其内应力,因此可减少塑件的变形。
2.冷却系统在注射过程中,塑件冷却速度的不平均也将形成塑件缩短的不平均,这类缩短差异以致曲折力矩的产生而使塑件发生翘曲。
假如在注射成型平板形塑件(如手机电池壳)时所用的模具型腔、型芯的温度相差过大,因为切近冷模腔面的熔体很快冷却下来,而切近热模腔面的料层则会持续缩短,缩短的不平均将使塑件翘曲。
所以,注塑模的冷却应该注意型腔、型芯的温度趋于均衡,二者的温差不可以太大(此时可考虑使用两个模温机)。
除了考虑塑件内表面的温度趋于均衡外,还应试虑塑件各侧的温度一致,即模具冷却时要尽量保持型腔、型芯各处温度平均一致,使塑件各处的冷却速度均衡,从而使各处的缩短更趋平均,有效地防备变形的产生。
- 1、下载文档前请自行甄别文档内容的完整性,平台不提供额外的编辑、内容补充、找答案等附加服务。
- 2、"仅部分预览"的文档,不可在线预览部分如存在完整性等问题,可反馈申请退款(可完整预览的文档不适用该条件!)。
- 3、如文档侵犯您的权益,请联系客服反馈,我们会尽快为您处理(人工客服工作时间:9:00-18:30)。
WarpageWARPAGEWarpage can be defined as a dimensional distortion in a molded product after itis ejected from the mold at the end of the injection molding process. Warpage issometimes called ``potato-chipping'' because the part tends to appear wavy. MachineInadequate Injection Pressure or TimeExplanation: If too little injection pressure is used the plastic material will tend to cool and solidify before the mold is packed out. If no packing is achieved the individual molecules are not held tightly together and have space to move while the part is cooling. Also, if the injection hold time is not long enough, the packing process is minimized and the molecules can relax before full solidification occurs. In either case, as the part cools it is uncontrolled and the plastic is allowed to move because it is not being constrained. Each area of the part cools at a different rate and warpage will occur due to the differences.Solution: Increase the injection pressure or time applied. This will ensure the total part is cooling while constrained and the tendency for warpage will be minimized.Inadequate Residence TimeExplanation: Residence time is the amount of time a material must spend being exposed to heat in the barrel. The time is determined by the ability of the specific resin to absorb heat enough to be properly processed. Inadequate residence time will result in under-heated material, which causes the material to be stiff. It will cool off before the mold is packed and individual molecules will be unconstrained while they solidify. Molecules that are not constrained during cooling will shrink at differing rates throughout the part and warpage will occur. Solution: Increase the residence time by adding time to the cooling portion of the cycle. While increased cycle time may add cost to the final product, each material requires a specific minimum amount of time to absorb heat in the barrel, and if the time is not long enough warped parts will occur.Barrel Temperature Too LowExplanation: When barrel temperatures are too low, the material will not have a chance to heat to the proper flow temperature. The cold material gets pushed into the mold but solidifies before the molecules are packed and constrained. This results in warpage as the molecules shrink at varying rates.Solution: Increase the barrel temperature. This will allow the material to come to proper heat and it will fill the mold before solidification takes place. The molecules will be packed and constrained as they cool, thus shrinking at uniform rates, minimizing the chance of warpage.Nozzle Temperature Too LowExplanation: The nozzle, being the final transfer point between the heated barrel and the mold, is a critical area and must be scrutinized whenever splay patterns occur. If the nozzle is too cold, the plastic material may slow down as it travels through the area and the molecules will not get packed under constraint. They will shrink at varying rates and cause warpage.Solution: Increase the nozzle temperature 10 degrees F at a time until the warpage disappears. If splay still appears, reduce the temperature of the nozzle, and make sure the nozzle being used is of the proper design for the material being molded. There are many different nozzle designs and some may interfere with proper flow if they are not designed for the material in use.Excessive Stress BuildupExplanation: The injection molding process tends to build up physical stress in a molded part due to the stretching and squeezing action that takes place on the individual plastic molecules as they are heated, expanded, cooled and contracted. They must be allowed to relax and recover in a constrained position before they solidify or the stress will be locked in. It will then be released as the part cools after being ejected from the mold and warpage will occur. Solution: Increase the barrel temperature and decrease injection pressure until the stress is minimized. It can never be eliminated but lower pressure will result in lower stress. And, higher barrel temperatures allow the use of lower injection pressures.MOLDSmall GatesExplanation: Gates that are too small will cause excessive restriction to the flow of the molten plastic as it passes through. This restriction may cause additional physical stress to the plastic molecules as they are stretched and squeezed again going through the gate area. The stress gets released after ejection and the parts will warp.Solution: Optimize gate size and shape. The material supplier can provide data on proper sizing and shape, or use a computer finite element analysis program to help make the determination.Mold Temperature Too LowExplanation: Generally, a hot mold will allow a material to stay molten longer than a cold mold and cause the molecules to stay fluid longer before they cool and solidify. If the mold is too coldthe molecules will solidify before they are packed and will shrink at differing, uncontrolled rates. This is a prime cause of warpage.Solution: Increase the mold temperature to the point at which the material has the proper flow and packs out the mold with maximum fill. Start with the material suppliers recommendations and adjust accordingly. Allow 10 cycles for every 10-degree change for the process to re-stabilize.Uneven Mold TemperaturesExplanation: The plastic molecules must cool and shrink evenly to resist warpage. If the mold is not cooling the plastic in a uniform manner the molecules will have varying cooling and shrinking characteristics and this will cause warpage.Solution: Check the surfaces of the mold that are in contact with the molten plastic. Use a fast-acting pyrometer to determine if there is more than a 10 degree F difference between any two points, even between the two mold halves. A difference greater than 10 degrees F will cause too great a difference in shrink rates and warpage will occur.Non-Uniform EjectionExplanation: It is possible that either the ejection system of the mold or the press will not be operating properly. If the part is warm enough and the ejection force is not even and exactly perpendicular to the part, stresses will be set up in the part as it tries to resist the ejection activity. These stresses will cause warpage of the part as it cools after being ejected.Solution: Inspect and adjust the ejection system(s) as required. Make sure all adjusting devices are locked down to eliminate slipping, and that all components are properly lubricated. It may be necessary to use a guided ejection system that utilizes leader pins and bushings to keep the system in line and even.MATERIALImproper Flow RateExplanation: Resin manufacturers supply specific formulations in a range of standard flow rates. Thin-walled products may require an easy flow material while thick-walled products can use a material that is stiffer. It is better to use as stiff a flow as possible because that improves physical properties of the molded part. But the stiff material will be more difficult to push and this may result in the material solidifying before full packing takes place. The molecules will be left to shrink at different rates and warpage will occur.Solution: Utilize a material that has the stiffest flow possible without causing warpage. Contact the material supplier for help in deciding which flow rate should be used for a specific application.OPERATORInconsistent Process CycleExplanation: The machine operator may be opening the gate too soon, thereby effectively shortening the overall cycle time. This would cause the part to be ejected before the skin has formed properly and excessive, uncontrolled shrinkage may occur. The varying shrinkage ratesformed properly and excessive, uncontrolled shrinkage may occur. The varying shrinkage rates will cause warpage.Solution: If possible, run the machine on the automatic cycle, using the operator only to interrupt the cycle if an emergency occurs. Use a robot if an ``operator'' is necessary. In addition, instruct all employees on the importance of maintaining consistent cycles.发送稍后发送。