2.车削知识
车工基本知识

车工基本知识一.车削的基本概念:1.切削运动:在切削加工中,为了切去多余的金属,必须使工件和刀具做相对的切削运动。
按照在切削过程中的作用,切削运动分主运动和进给运动。
⑴.主运动:切除工件上的切削层,使之转变为切屑,以形成工件新表面的运动。
⑵.进给运动:使新的切削层不断投入切削的运动。
车削时,工件的旋转是主运动。
通常,主运动的速度较高,消耗的切削功率较大。
车刀沿着所要形成的工件表面的纵向或横向移动是进给运动也叫走刀运动。
2.切削时工件上的三个表面:车刀在切削工件时,使工件上形成已加工表面,加工表面和待加工表面。
⑴.已加工表面:已经切去多余金属而形成的新表面。
⑵.待加工表面:即将被切去金属层的表面。
⑶.加工表面:车刀刀刃正在切削的表面。
如下图所示:二.车刀的工作面和角度1. 车刀的工作面:⑴.前刀面:(前面)切屑沿着它排出的刀面。
⑵.后刀面:(后面)后刀面分为:主后刀面和付后刀面。
与工件上加工表面相对着的是主后刀面;与工件上已加工表面相对着的是付后刀面。
⑶.主刀刃:(主切削刃)前刀面和主后刀面的相交部位,它担负主要的切削工作。
⑷.付刀刃:(付切削刃)前刀面和付后刀面的相交部位,它配合主刀刃完成切削工作。
⑸.刀尖:主刀刃和付刀刃的交点。
为了提高刀尖强度和延长刀具寿命,很多刀具都在刀尖处磨出圆弧型或直线型过渡刃。
圆弧型过渡刃也称为刀尖圆弧。
一般硬质合金车刀的刀尖圆弧半径为r =0.5-1mm⑹.修光刃:付刀刃近刀尖处一小段平直的刀刃。
如下图:任何车刀都由上述组成部分,但数量不完全相同。
如:典型的外圆车刀有3个刀面,2条刀刃和1个刀尖。
而割刀(切断刀)就有4个刀面(2个付后刀面)3条刀刃和2个刀尖。
此外刀刃可以是直线的,也可以是曲线的。
如车成型面的成型车刀的刀刃就是曲线。
2.车刀的辅助平面为了确定和测量车刀的角度,需要假设以下3个辅助平面作为基准:⑴.切削平面(P): 通过刀刃上某一选定点,切于工件加工表面的平面,即为该点的切削平面。
2车削的基础知识

1)粗车时,以提高生产效率为主,应尽快把多余材料去切除, ap
→f →v。 2)精车时,以保证加工质量为主,并兼顾生产率和刀具寿命。 ap
=0.1~0.8,f取小一些, 硬质合金车刀:v>80m/min;高速钢车
刀v<5m/min。
信息资讯
四、切削液
在车削过程中产生大量的热量,因此必须加注切削液。
楔角βo ------在主剖面内,前刀面与主后刀面之间的夹角。
主偏角κ r ------主切削刃在基面上的投影与进给方向的夹角,如图1-8所示。 副偏角κ r′ ------副切削刃在基面上的投影与进给方向的夹角,如图1-8所示。
刀尖角ε r ------主切削刃与副切削刃在基面上的投影之间的夹角。
刃倾角λ s------主切削刃与基面间的夹角(当主切削刃下倾,即刀尖为主切 削刃上的最高点时,刃倾角为正,反之为负,如图1-9所示)。
信息资讯
图1-7 车刀上的前角与后角
1—工件 2—切削平面
3—基面
图1-9 刃倾角的正负
车刀的刃磨视频
图1-8 外圆车刀的主偏角与副偏角
信息资讯
三、车削运动和切削用量
写的汉语拼音字母表示,车床的类代号是“C”,读作“车”。
信息资讯
机床的通用特性代号
机床的组、系代号
将每类机床划分为10 个组, 每个组又划分为10个系(系 列)。 机床的组用一位阿拉伯数字表示,位于类代号或通用特性代 号、结构特性代号之后。 机床的系用一位阿拉伯数字表示,位于组代号之后。
信息资讯
例:车削直径为100mm的铸铁带轮外圆,若选择的切削速度为60m/min, 要求一次把直径车削到95mm,试求车床主轴的转速和背吃刀量?
2轴类零件车削(普车实训操作+图解)
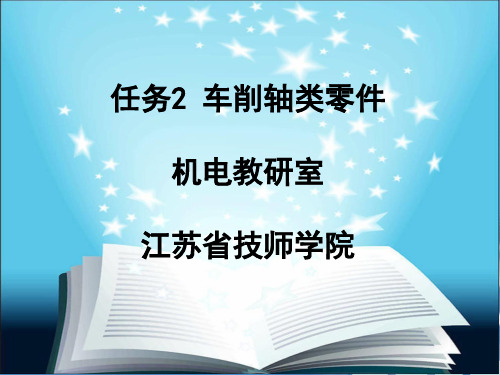
×
至所需位置30
2)机动进给转手动。当纵向车削将至所需
刻度时,应转为手动进给车削至尺寸,然
后退刀,停车检验。 3)横向二倍关系。半径和直径的关系。
10
4、主轴变速,必须先停车!
手柄变速:主轴转速s和进给量f。 参考:
主轴转速s=570r/min,
进给量f=0.05-0.11mm/r。
11
5.粗车和精车
a)开车对刀,使车刀 和工件表面轻微接触;
b) 向右退出车刀, 中滑板不变;
c)按要求横向进刀ap1;
d) 试切1~3毫米
e) 向右退出,停车,测量
f)调整切深至ap2后,机动进给车外圆
8
3. 注意事项 (1)消除机械间隙。
40 30 30
c)正确:反转 b) 错误: a)手柄摇过:要求 转至30,但转到40; 直接退至30; 约一周,再转
20
a)摇动床鞍、中滑板, 移动刀架;
b)使车刀距离工件端 面3mm左右处;
0
c)转动小滑板,使刀 尖轻微接触工件端面;
d)中滑板退刀(床鞍和 小滑板不动);
d)床鞍刻度盘调零 (注意消除机械间隙)。
2、质量分析
1)台阶长度不正确、不垂直。
2)表面粗糙度差。车刀不锋利,手动不
均匀或太快,切削用量不当。
3)倒角:防伤手;便于装配。
4
一、轴类零件:长度超过直径三倍以上。 1、组成:平面、外圆、倒角等。
5
一、轴类零件:长度超过直径三倍以上。 1、组成:平面、外圆、倒角等。
6
一、车外圆 1、车刀选择: 90°车刀、 45°弯头车 刀、尖刀(粗车外圆)。
a)90°车刀
b)45°车刀
车削加工基本内容

标题:车削加工那些事儿- 基础知识篇嘿,伙计们,今天咱们来侃侃这个车削加工的基本内容。
别看我这儿说得轻松,其实车削这活儿可讲究了,得有那么点手艺人才干得好。
不过别怕,咱们一点点来,不着急。
首先啊,咱得知道车削是啥。
简单来说,就是用个旋转的刀具去切一个转动的工件,就像你在家切菜似的,只不过咱们的工具和工件都是金属的,而且精度高得多。
咱们先说说车削加工的分类。
基本上,车削可以分为两大类:粗车和精车。
粗车嘛,就是为了快速去掉多余的材料,不太在乎表面光不光滑;精车呢,就是为了把工件加工到精确的尺寸和形状,表面得光滑得像婴儿的屁股一样。
再说说车削加工的设备。
最主要的设备就是车床,还有刀具、夹具这些。
车床有很多种,什么数控车床、普通车床等等,根据不同的需要来选。
刀具也得选对,不同的材料、不同的加工要求,用的刀都不一样。
夹具呢,就是用来固定工件的,保证它不会乱动。
接下来咱们看看车削加工的流程。
首先是准备工作,包括选材料、选刀具、装夹具这些。
然后是车削操作,这个时候要注意控制好切削速度、进给量这些参数。
最后是清理和检查,把工件表面的切屑清理干净,检查加工质量。
在车削过程中,还得注意几点:一是刀具得锋利,不然切不动;二是冷却液得够用,不然刀具和工件摩擦生热,会影响精度;三是测量要准确,不然加工出来的东西可能不合格。
当然啦,车削加工也不是万能的,有些材料太硬或者太粘,可能就不适合车削。
所以咱们得根据实际情况来选择合适的加工方法。
对了,还有一点很重要,就是安全。
车削加工的时候,一定要遵守安全规程,眼睛不能离工件太近,穿戴好防护装备,避免发生事故。
最后咱们聊聊车削加工的技巧。
这个就需要点经验了。
比如,你要是想提高加工效率,就得合理选择切削参数;要是想提高加工精度,就得仔细调整机床和夹具。
这些都是需要时间积累的。
好了,说了这么多,咱们这个车削加工基本内容就差不多了。
当然啦,这里面还有很多细节和技术要点,咱们以后可以慢慢聊。
2车削工艺与技能训练《工件的装夹》1
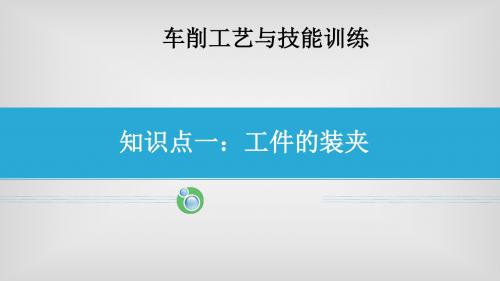
图1-1 三爪自定心卡盘 1-方孔 2-小锥齿轮 3-大锥齿轮 4-平面螺纹 5-卡爪
8
车削工艺与技能训练
一.钻中心孔
三爪自定心卡盘的卡爪可以装成正爪,实现由外向内夹紧;也可以装成反爪,实现由内向外夹紧, 即撑夹(反夹)。正爪夹持工件时,直径不能太大,卡爪伸出卡盘外圆的长度不应超过卡爪长度的三分之 一,以免发生事故。反爪可以夹持直径较大的工件。
三爪卡盘能自动定心,装夹方便,但是定心精度不高。若因三爪卡盘使用太长时间,而失去了应有的 精度,在加工高精度的工件时,也需要找正。三爪卡盘适于装夹截面为圆形、三角形、六方形的轴类和中 小型盘类零件。
图1-2 用三爪卡盘安装工件的方法 (a)正爪装夹圆柱面 (b)正爪装夹内圆柱面 (c)反爪装夹
9
车削工艺与技能训练
11
车削工艺与技能训练
一.钻中心孔
4.中心孔的加工方法
12
车削工艺与技能训练
二.用三爪卡盘、四爪卡盘装夹工件
1.用划针校正
13
车削工艺与技能训练
二.用三爪卡盘、四爪卡盘装夹工件
2.用百分表校正
14
车削工艺与技能训练
二.用三爪卡盘、四爪卡盘装夹工件
图1-9 用鸡心夹头装夹工件
7
车削工艺与技能训练
一.钻中心孔
3.轴类工件常用的装夹方法
车削加工时,工件必须先在车床夹具上进行找正、夹紧。由于工件的形状、大小和加工数量的 不同,必须采用不同的安装方法。 3.1 用三爪卡盘安装工件 三爪卡盘的结构如图1-1所示,安装工件如图1-2所示。安装时,将扳手方榫插入小锥齿轮2的方孔 1中转动,小锥齿轮2就带动大锥齿轮3转动。大锥齿轮3的背面是一平面螺纹4,三个卡爪5背面的螺 纹与平面螺纹啮合,因此当平面螺纹转动时,就带动三个卡爪同时作向心或离心移动,当三个卡爪的 张开度足以容纳工件时,将工件装上,再用板手锁紧。
项目二车削的基本知识

Vc=60 ~ 100m/min(硬质合金车刀切铸铁)
任务二 车刀
教师
唐华伟
一、认识常用车刀
1.车刀的种类和用途
一、认识常用车刀
“两刃”包括如下内容: (1)主切削刃 主切削刃是前刀面和主后刀面的相交部位,它担负着主要 的切削工作 (2)副切削刃 副切削刃是前刀面和副后刀面的相交部位,它配合主切削 刃完成少量的切削工作。
一、认识常用车刀
“一尖”是指刀尖。 刀尖是主切削刃和副切削刃的连接部位。为了提高刀
尖的强度和车刀的耐用度,通常磨成一小段圆弧形或直线 型过渡刃。
加工余量不大,且较均匀,因此选择精车的切削用 量时,应着重考虑如何保证加工质量,并在此基础 上提高生产率。
二、切削用量的基本概念
首选根据粗加工后的余量确定背吃刀量ap;其次 根据已加工表面粗糙度要求,选取较小的进给量f; 最后在保证刀具耐用度的前提下,确定一个尽可能 大的切削速度Vc.
二、切削用量的基本概念
ap= d待-d已 2
二、切削用量的基本概念
4.切削用量的选择 切削用量的合理选择,对于能否充分发挥机床
潜力与刀具切削性能,并实现优质、高产、低成本 和安全操作都有很重要的作用。
二、切削用量的基本概念
4.切削用量的选择 (1)粗加工时切削用量的选择 粗加工时,着重考虑考虑以提高生产效率为主,兼顾刀具耐用性。 首先选取尽可能大的ap;其次选择尽可能大的f;最后选择一个合适 的切削速度Vc 增大被吃刀量ap可以使走刀次数减少,增大进给量f有利于断屑
项目三外圆、端面、台阶的车削资料要点

机械工程系实习讲义首页教学过程及教学内容[课前组织]1.检查学生出勤情况,填写教学日志。
2.检查学生装束是否整齐3.讲述要求:纪律、卫生、学习方法、如何作笔记4.宣布本项目的学习任务与目的要求:[设备工量具准备]任务一车削基础知识(1)了解车削加工时切削用量的选择原则。
(2)了解金属车削的过程。
(3)基本掌握车削过程中表面质量的控制方法。
(4)了解车刀切削时磨损的原因与刀具寿命的含义。
任务二外圆、端面、台阶的车削(1)掌握试切法与试测法控制外圆尺寸的方法。
(2)熟练掌握工件找正和安装方法。
(3)掌握零件尺寸的测量方法和对质量进行简单分析。
任务三切外沟槽、切断(1)了解切断刀和车槽刀的种类和用途。
(2)了解切断刀和车槽刀的组成部分和角度要求。
(3)掌握掌握切断刀和车槽刀的刃磨方法。
(4)掌握外沟槽的车削方法和测量方法。
(5)了解车沟槽时产生的问题和防止方法。
(6)掌握直进法和左右车削法切断工件。
[入门指导]任务一车削的基础知识导语:在车削加工时,合理选择切削用量对提高劳动生产率,延长刀具的使用寿命,保证加工质量,降低生产成本有着重要的意义。
一、车削加工时切削用量的选择1.合理选择切削用量的含义衡量切削用量是否合理的标准:①能否保证加工零件的质量要求(主要是加工精度和表面质量)②在加工系统刚性许可的条件下,是否充分利用了车床功率。
③在保证加工质量和刀具寿命的条件下,是否充分发挥了刀具的切削性能。
2.选择切削用量的原则(1)切削深度的选择(2)进给量的选择(3)切削速度的选择•选择切削速度的一般原则如下1)车刀材料使用硬质合金车刀可比高速工具钢车刀的切削速度快。
2)工件材料切削强度和硬度较高的工件时,因为产生的热量和切削力都比较大,车刀容易磨损,所以切削速度应选得低些。
脆性材料如铸铁工件,虽然强度不高,但车削时形成崩碎切屑,热量集中在切削刃附近,不易传散。
因此,切削速度也应取得低一些。
3)表面粗糙度要求表面粗糙度值小的工件,如用硬质合金车刀车削,切削速度应取得高些;如用高速工具钢车刀车削,切削速度应取得低些。
普车的基础知识
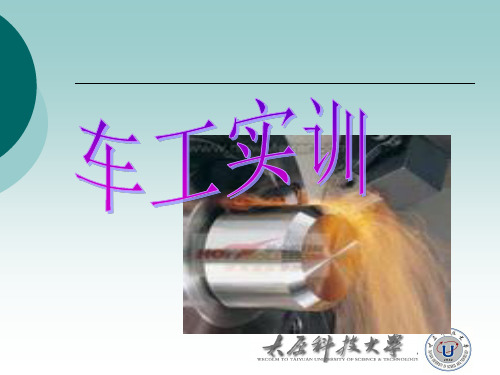
车削加工的基本知识
作横向移动。故刀架可作纵向或横向直线进给运动。当接 通丝杠并闭合开合螺母时可车削螺纹。溜板箱内设有互锁 机构,使光杠、丝杠两者不能同时使用。 光杠与丝杠 : 将进给箱的运动传至溜板箱光杠用于 一般车削,丝杆用于车螺纹。 尾 座: 它用于安装后顶尖,以支持较长工件进行加 工,或安装钻头、铰刀等刀具进行孔加工。偏移尾架 可以车出长工件的锥体。
基本车削工作
车外圆: 在车削加工中,外圆车削是一个基础,几乎绝大部分的 工件都少不了外圆车削这道工序,车外圆时常见的方法 有下列几种. ⑴用直头车刀车外圆:这种车刀强度较好,常用于粗车外 圆。 ⑵用45°弯头车刀车外圆:适用车削不带台阶的光滑轴。 ⑶用主偏角为90°的偏刀车外圆:适于加工细长工件的 外圆。
d n
1000
式中: Vc——切削速度(m/s或m/min) ; d——工件待加工表面的最大直径(mm); n——工件每分钟的转数(r/min)。
车削加工的基本知识
2.进给量 ƒ 它是指在主运动一个循环(或单位时间)内,车刀与工件之 间沿进给运动方向上的相对位移量,又称走刀量,其单位为
mm/r。即工件转一转,车刀所移动的距离。
车刀的角度的主要作用
(1)前角(γ 0) 前刀面和基面的夹角。影响刃口的锋利和强度, 切削变形和切削力。大,锋利、减少切削变形、切削省力,切屑 顺利排出。负(小),增加切削刃强度,耐冲击。 (2)后角(α0) 后刀面和切削平面的夹角。在主截面内的是主后角 ( α0 ),在副截面内的是副后角(α0 ′)。主要减少车刀后刀面与 工件的摩擦。 (3)主偏角(Kr) 主切削刃在基面上的投影与进给运动方向间的夹 角。改变主切削刃和刀头的受力和散热。 (4)副偏角(Kr′) 副切削刃在基面上的投影与背离进给运动方向 间的夹角。减少副切削刃与工件已加工表面的摩擦。 在切削平面内测量的角度: (5)刃倾角(λs) 主切削刃与基面的夹角。控制排屑方向,负值时, 增加刀头强度和保护刀尖。
- 1、下载文档前请自行甄别文档内容的完整性,平台不提供额外的编辑、内容补充、找答案等附加服务。
- 2、"仅部分预览"的文档,不可在线预览部分如存在完整性等问题,可反馈申请退款(可完整预览的文档不适用该条件!)。
- 3、如文档侵犯您的权益,请联系客服反馈,我们会尽快为您处理(人工客服工作时间:9:00-18:30)。
普通车床的组成和传动一、车床的型号机床均用汉拼音字母和数字,按一定规律组合进行编号,以表示机床的类型和主要规格。
车床型号C6132的含义如下:C——车床类;6——普通车床组;1——普通车床型;32——最大加工直径为320mm。
老型号C616的含义如下:C——车床;6——普通车床;16——主轴中心到床面距离的1/10,即中心高为160mm。
二、车削运动和车床的用途为了使车刀能够从毛坯上切下多余的金属,车削加工时,车床的主轴带动工件作旋转运动,称主运动;车床的刀架带动车刀作纵向、横向或斜向的直线移动,称进给运动。
通过车刀和工件的相对运动,使毛坏被切削成一定的几何形状、尺寸和表面质量的零件,以达到图纸上所规定的要求。
在机械加工车间中,车床约占机床总数的一半左右。
车床的加工范围很广,主要加工各种回转表面,其中包括端面、外圆、内圆、锥面、螺纹、回转沟槽、回转成形面和滚花等。
普通车床加工尺寸精度一般为IT10~IT8,表面粗糙度值Ra=6.3~1.6μm。
三、C6132(或C616)车床的组成部分及其功用C6132车床由床身、床头箱、变速箱、进给箱、光杆、丝杆、溜板箱、刀架、床腿和尾架等部分组成。
1.床身:是车床的基础零件,用来支承和安装车床的各部件,保证其相对位置,如床头箱、进给箱、溜板箱等。
床身具有足够的刚度和强度,床身表面精度很高,以保证各部件之间有正确的相对位置。
床身上有四条平行的导轨,供大拖板(刀架)和尾架相对于床头箱进行正确的移动,为了保持床身表面精度,在操作车床中应注意维护保养。
2.床头箱(主轴箱):用以支承主轴并使之旋转。
主轴为空心结构。
其前端外锥面安装三爪卡盘等附件来夹持工件,前端内锥面用来安装顶尖,细长孔可穿入长棒料。
C6132车床主轴箱内只有一级变速,其主轴变速机构安放在远离主轴的单独变速箱中,以减小变速箱中的传动件产生的振动和热量对主轴的影响。
3.变速箱:由电动机带动变速箱内的齿轮轴转动,通过改变变速箱内的齿轮搭配(啮合)位置,得到不同的转速,然后通过皮带轮传动把运动传给主轴。
4.进给箱又称走刀箱,内装进给运动的变速齿轮,可调整进给量和螺距,并将运动传至光杆或丝杆。
5.光杆、丝杆:将进给箱的运动传给溜板箱。
光杆用于一般车削的自动进给,不能用于车削螺纹。
丝杆用于车削螺纹。
6.溜板箱:又称拖板箱,与刀架相联,是车床进给运动的操纵箱。
它可将光杆传来的旋转运动变为车刀的纵向或横向的直线进给运动;可将丝杆传来的旋转运动,通过“对开螺母”直接变为车刀的纵向移动,用以车削螺纹。
7.刀架:用来夹持车刀并使其作纵向、横向或斜向进给运动。
它包括以下各部分。
(1)大拖板(大刀架、纵溜板)与溜板箱连接,带动车刀沿床身导轨纵向移动,其上面有横向导轨。
(2)中溜板(横刀架、横溜板)它可沿大拖板上的导轨横向移动,用于横向车削工件及控制切削深度。
(3)转盘它与中溜板用螺钉紧固,松开螺钉,便可在水平面上旋转任意角度,其上有小刀架的导轨。
(4)小刀架(小拖板、小溜板)它控制长度方向的微量切削,可沿转盘上面的导轨作短距离移动,将转盘偏转若干角度后,小刀架作斜向进给,可以车削圆锥体。
(5)方刀架它固定在小刀架上,可同时安装四把车刀,松开手柄即可转动方刀架,把所需要的车刀转到工作位置上。
8.尾架:安装在床身导轨上。
在尾架的套筒内安装顶尖,支承工件;也可安装钻头、铰刀等刀具,在工件上进行孔加工;将尾架偏移,还可用来车削圆锥体,使用尾架时注意:1)用顶尖装夹工件时,必须将固定位置的长手柄扳紧,尾架套筒锁紧。
2)尾架套筒伸出长,一般不超过100mm。
3)一般情况下尾架的位置与床身端部平齐,在摇动拖板时严防尾架从床身上落下,造成事故。
四、C6132(或C616)车床各部分的调整及其手柄的使用C6132车床采用操纵杆式开关,在光杆下面有一主轴启闭和变向手柄当手柄向上为反转,向下为正转,中间为停止位置。
1.主轴转速的调整主轴的不同转速是靠床头箱上变速手轮与变速箱上的长、短手柄配合使用得到的。
变速手传输线有低速I和高速II两个位置,长手柄有左、右两个位置,短手柄有左、中、右三个位置,它们相互配合使用,可使主轴获得28.5~1430r/min 12种不同的转速(详见床头箱上的主轴转速表)。
操作和使用时应注意:1)必须停车变速,以免打坏齿轮。
2)当手柄或手轮板不到正常位置时,要用手扳转卡盘。
3)为了安全操作,转速不高于360r/min。
2.进给量的调整进给量的大小是靠变换配换齿轮及改变进给箱上两个手传输线的位置得到的。
其中一手轮有5个位置。
另一手轮有4个位置。
当配换齿轮一定时,这两个手轮配合使用,可以获得20 种进给量。
更换不同的配换齿轮。
可获得多种进给量(详见进给箱上的进给量表)。
离合手柄是控制光杆和丝杆转动的,一般车削走刀时,使用光杆,离合手柄向外拉;车螺纹时,使用丝杆、离合手柄向里推。
3.手动手柄的使用顺时针摇动纵向手动手柄,刀架向右移动;逆时针摇动,刀架向左移动。
顺时针摇动横向手动手柄,刀架向前移动;逆时针摇动,刀架向后移动。
4.自动手柄的使用使用光杆时,当换向手轮处于“正向”(-)位置时,抬起纵向自动手柄,刀架自动向左进给;抬起横向自动手柄,刀架自动向前进给。
使用丝杆时,向下按开合螺母手柄,向左自动走刀车削右旋螺纹。
当换向手柄处玩弄“反向”(-)位置时,上述情况正好相反。
当换向手柄处于“空档”(O)位置时,纵、横向自动进给机构失效。
5.其它手柄的使用,当需要刀具短距离移动时,可使用小刀架手柄。
装刀和卸刀时,需要使用方刀架锁紧手柄。
注意:装刀、卸刀和切削时,方刀架均需锁紧,此外,尾架手轮用于移动尾架套筒,手柄用于锁紧尾架套筒。
五、普通车床的传动系统车切基本知识一、车刀材料在切削过程中,刀具的切削部分要承受很大的压力、摩擦、冲击和很高的温度。
因此,刀具材料必须具备高硬度、高耐磨性、足够的强度和韧性,还需具有高的耐热性(红硬性),即在高温下仍能保持足够硬度的性能。
常用车刀材料主要有高速钢和硬质合金。
1.高速钢高速钢又称锋钢、是以钨、铬、钒、钼为主要合金元素的高合金工具钢。
高速钢淬火后的硬度为HRC63~67,其红硬温度550℃~600℃,允许的切削速度为25~30m/min。
高速钢有较高的抗弯强度和冲击韧性,可以进行铸造、锻造、焊接、热处理和切削加工,有良好的磨削性能,刃磨质量较高,故多用来制造形状复杂的刀具,如钻头、铰刀、铣刀等,亦常用作低速精加工车刀和成形车刀。
常用的高速钢牌号为W18Cr4V和W6Mo5Cr4V2两种。
2.硬质合金硬质合金是用高耐磨性和高耐热性的WC(碳化钨)、TiC(碳化钛)和Co(钴)的粉末经高压成形后再进行高温烧结而制成的,其中Co起粘结作用,硬质合金的硬度为HRA89~94(约相当于HRC74~82),有很高的红硬温度。
在800~1000℃的高温下仍能保持切削所需的硬度,硬质合金刀具切削一般钢件的切削速度可达100~300m/min,可用这种刀具进行高速切削,其缺点是韧性较差,较脆,不耐冲击,硬质合金一般制成各种形状的刀片,焊接或夹固在刀体上使用。
常用的硬质合金有钨钴和钨钛钴两大类:(1)钨钴类(YG)由碳化钨和钴组成,适用于加工铸铁、青铜等脆性材料。
常用牌号有YG3、YG6、YG8等,后面的数字表示含钴量的百分比,含钴量愈高,其承受冲击的性能就愈好。
因此,YG8常用于粗加工,YG6和YG3常用于半精加工和精加工。
(2)钨钛钴类(YT)由碳化钨、碳化钛和钴组成,加入碳化钛可以增加合金的耐磨性,可以提高合金与塑性材料的粘结温度,减少刀具磨损,也可以提高硬度;但韧性差,更脆、承受冲击的性能也较差,一般用来加工塑性材料,如各种钢材。
常用牌号有YT5、YT15、YT30等,后面数字是碳化钛含量的百分数,碳化钛的含量愈高,红硬性愈好;但钴的含量相应愈低,韧性愈差,愈不耐冲击,所以YT5常用于粗加工,YT15和YT30常用于半精加工和精加工。
二、车刀的组成及结构形式1.车刀的组成车刀由刀头和刀体两部分组成。
刀头用于切削,刀体用于安装。
刀头一般由三面,两刃、一尖组成。
前刀面是切屑流经过的表面。
主后刀面是与工件切削表面相对的表面。
副后刀面是与工件已加工表面相对的表面。
主切削刃是前刀面与主后刀面的交线,担负主要的切削工作。
副切削刃是前刀面与副后刀面的交线,担负少量的切削工作,起一定的修光作用。
刀尖是主切削刃与副切削刃的相交部分,一般为一小段过渡圆弧。
2.车刀的结构形式最常用的车刀结构形式有以下两种:(1)整体车刀刀头的切削部分是靠刃磨得到的,整体车刀的材料多用高速钢制成,一般用于低速切削。
(2)焊接车刀将硬质合金刀片焊在刀头部位,不同种类的车刀可使用不同形状的刀片。
焊接的硬质合金车刀,可用于高速切削。
三、车刀的主要角度及其作用车刀的主要角度有前角(γ0)、后角(α0)、主编角(Kr)、副偏角(Kr’)和刃倾角(λs)。
为了确定车刀的角度,要建立三个坐标平面:切削平面、基面和主剖面。
对车削而言,如果不考虑车刀安装和切削运动的影响,切削平面可以认为是铅垂面;基面是水平面;当主切削刃水平时,垂直于主切削刃所作的剖面为主剖面。
(1)前角γ0在主剖面中测量,是前刀面与基面之间的夹角。
其作用是使刀刃锋利,便于切削。
但前角不能太大,否则会削弱刀刃的强度,容易磨损甚至崩坏。
加工塑性材料时,前角可选大些,如用硬质合金车刀切削钢件可取γ0=10~20,加工脆性材料,车刀的前角γ0应比粗加工大,以利于刀刃锋利,工件的粗糙度小。
(2)后角α0在主剖面中测量,是主后面与切削平面之间的夹角。
其作用是减小车削时主后面与工件的摩擦,一般取α0=6~12°,粗车时取小值,精车时取大值。
(3)主偏角Kr在基面中测量,它是主切削刃在基面的投影与进给方向的夹角。
其作用是:1)可改变主切削刃参加切削的长度,影响刀具寿命。
2)影响径向切削力的大小。
小的主偏角可增加主切削刃参加切削的长度,因而散热较好,对延长刀具使用寿命有利。
但在加工细长轴时,工件刚度不足,小的主偏角会使刀具作用在工件上的径向力增大,易产生弯曲和振动,因此,主偏角应选大些。
车刀常用的主偏角有45°、60°、75°、90°等几种,其中45°多。
(4)副偏角Kr’在基面中测量,是副切削刃在基面上的投影与进给反方向的夹角。
其主要作用是减小副切削刃与已加工表面之间的摩擦,以改善已加工表面的精糙度。
在切削深度a p、进给量f、主偏角Kr相等的条件下,减小副偏角Kr’,可减小车削后的残留面积,从而减小表面粗糙度,一般选取Kr′=5~15°。
(5)刃倾角入λs 在切削平面中测量,是主切削刃与基面的夹角。