精益生产经典案例
非常好的精益生产案例值得借鉴

总结各案例的优点和不足
案例1:优点是 提高了生产效 率,降低了成 本;不足是忽 视了员工培训 和团队建设。
案例2:优点是 实现了精益生产, 提高了产品质量; 不足是忽视了客 户需求和市场变
化。
案例3:优点是 优化了生产流程, 提高了生产效率; 不足是忽视了员 工满意度和员工
流失率。
案例4:优点是 实现了精益生产, 提高了产品质量; 不足是忽视了供 应链管理和供应
商关系。
对其他企业的借鉴意义
精益生产可以提高生产效率,降低 成本
精益生产可以优化生产流程,提高 生产灵活性
添加标题
添加标题
添加标题
添加标题
精益生产可以减少浪费,提高产品 质量
精益生产可以提升员工素质,提高 员工满意度
对未来精益生产的展望
持续改进:不断优化生产流程,提 高生产效率
绿色生产:注重环保和可持续发展, 降低生产对环境的影响
解决方案:加强质量管理,提高员工技能,确保产品质量
问题:库存积压,资金周转困难 解决方案:实施JIT(准时生 产),减少库存,提高资金周转率
解决方案:实施JIT(准时生产),减少库存,提高资金周转 率
问题:员工士气低落,离职率高 解决方案:加强企业文化建设, 提高员工满意度,降低离职率
解决方案:加强企业文化建设,提高员工满意度,降低离职 率
精益生产的核心思想
消除浪费:通过 持续改进,消除 生产过程中的浪 费,提高生产效 率
持续改进:不断 追求更好的生产 方式,持续改进 生产流程
准时生产:根据 市场需求,准时 生产出所需的产 品,减少库存积 压
质量至上:注重 产品质量,追求 零缺陷,提高客 户满意度
精益生产的应用范围
精益生产在中国成功的经典案例
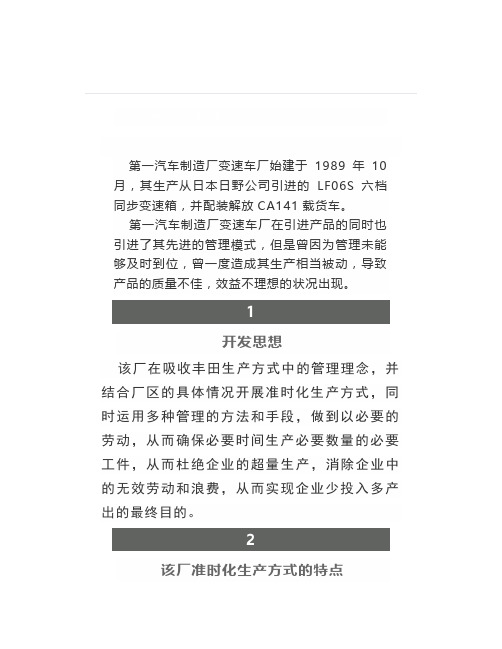
第一汽车制造厂变速车厂始建于1989年10月,其生产从日本日野公司引进的LF06S六档同步变速箱,并配装解放CA141载货车。
第一汽车制造厂变速车厂在引进产品的同时也引进了其先进的管理模式,但是曾因为管理未能够及时到位,曾一度造成其生产相当被动,导致产品的质量不佳,效益不理想的状况出现。
1开发思想该厂在吸收丰田生产方式中的管理理念,并结合厂区的具体情况开展准时化生产方式,同时运用多种管理的方法和手段,做到以必要的劳动,从而确保必要时间生产必要数量的必要工件,从而杜绝企业的超量生产,消除企业中的无效劳动和浪费,从而实现企业少投入多产出的最终目的。
2该厂准时化生产方式的特点01.目标明确,系统性强。
围绕提高产品质量,降低成本,满足市场需求的目标,进行“配套设计,同步实施”的开发与建议方式02.采用“拉动式”生产组织方式。
变“推动式”生产为“拉动式”生产组织方式,以市场需求为目标组织生产03.向工序间在制品为“0”进军。
04.实行“一人多机”操作。
实行U形生产设备布置,“一人多机”操作,大大提高劳动生产率05.工具定置集配,精度刀具强制换刀与跟踪管理。
06.“三为”现场管理。
强调观念更新,以生产现场为中心,生产工人为主体,车间主任为首的“三为”管理体制。
一切后方部门围绕准时化生产服务,使生产不停地创造附加价值07.生产现场实行“5S”活动——整顿、整理、清扫、清洁和素质。
08.实行“三自一控”、“创合格”、“深化工艺”、“五不流”和“产品创优”的“五位一体”的管理体系。
3实施效果经过1年多的实践,准时化生产方式使工厂面貌产生巨大变化。
1、生产能力大幅度提高,实现均衡生产原设计能力 6.8万台/年,92年实施准时化生产后实现8000台/月生产水平。
产品品种由原来1个基本型发展为18个改型产品。
2、产品质量稳步提高 91年废品率下降35%,一次装配合格率由80%提高到92%,市场占有率大幅度提高。
3、推行看板管理,在制品大幅度下降在制品流动资金占用从91年初的700万下降到年底的350万,下降了50%,92年月产量增加了25%,而流动资金下降到300万。
化工企业精益生产案例
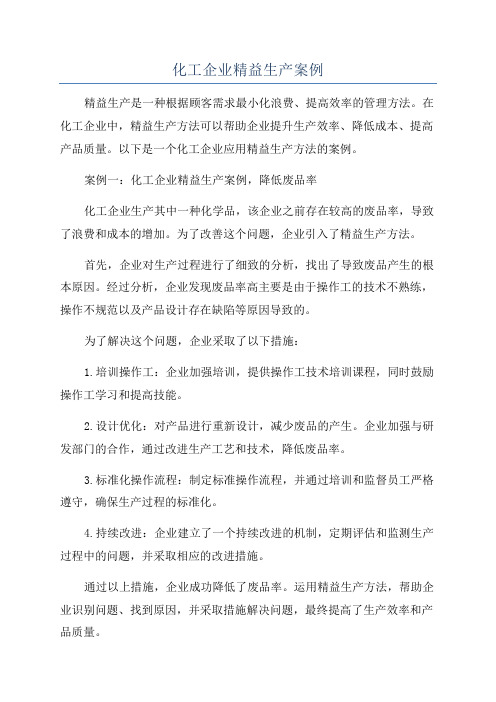
化工企业精益生产案例精益生产是一种根据顾客需求最小化浪费、提高效率的管理方法。
在化工企业中,精益生产方法可以帮助企业提升生产效率、降低成本、提高产品质量。
以下是一个化工企业应用精益生产方法的案例。
案例一:化工企业精益生产案例,降低废品率化工企业生产其中一种化学品,该企业之前存在较高的废品率,导致了浪费和成本的增加。
为了改善这个问题,企业引入了精益生产方法。
首先,企业对生产过程进行了细致的分析,找出了导致废品产生的根本原因。
经过分析,企业发现废品率高主要是由于操作工的技术不熟练,操作不规范以及产品设计存在缺陷等原因导致的。
为了解决这个问题,企业采取了以下措施:1.培训操作工:企业加强培训,提供操作工技术培训课程,同时鼓励操作工学习和提高技能。
2.设计优化:对产品进行重新设计,减少废品的产生。
企业加强与研发部门的合作,通过改进生产工艺和技术,降低废品率。
3.标准化操作流程:制定标准操作流程,并通过培训和监督员工严格遵守,确保生产过程的标准化。
4.持续改进:企业建立了一个持续改进的机制,定期评估和监测生产过程中的问题,并采取相应的改进措施。
通过以上措施,企业成功降低了废品率。
运用精益生产方法,帮助企业识别问题、找到原因,并采取措施解决问题,最终提高了生产效率和产品质量。
案例二:化工企业精益生产案例,提高设备利用率化工企业发现,其生产线的设备利用率较低,导致生产效率不高。
为了提高设备利用率,企业采用了精益生产方法。
首先,企业通过对生产线进行分析,找出导致设备利用率低的原因。
经过分析,企业发现设备故障率高、设备停机时间长以及设备维护不到位等原因导致了设备利用率低的问题。
为了解决这个问题,企业采取了以下措施:1.设备维护:企业加强设备的维护工作,定期检查和保养设备,防止故障的发生。
2.培训操作员:加强员工对设备操作的培训,提高操作员对设备使用和维护的技能。
3.优化生产计划:根据设备的特点和生产需求,优化生产计划,减少设备闲置时间。
精益生产案例总结借鉴经验

精益生产案例总结借鉴经验精益生产是一项以提高生产效率和质量为目标的管理方法,它在过去的几十年间在许多行业中得到了广泛应用。
以下是几个精益生产案例的总结,从中我们可以借鉴一些经验。
第一个案例是丰田汽车公司。
丰田公司是精益生产的创始者之一,他们的达成了在数量庞大的生产线中实现高效率和高质量的目标。
他们采用了一系列的流程改进措施,以降低生产过程中的浪费,并将线路进行优化。
此外,丰田还通过在员工培训方面投入大量资源,使员工具备了应对问题和改善生产过程的技能。
通过这种方式,丰田成功地提高了生产效率和质量,成为了全球汽车行业的领导者之一第二个案例是麦当劳。
麦当劳是精益生产方法在快餐业中的成功应用者。
麦当劳通过统一的流程和标准化操作来简化操作,减少浪费,并提高工作效率。
他们还利用精益生产的思想来进行菜单设计和供应链管理,以确保食品的质量和服务的一致性。
通过这些措施,麦当劳能够快速地为客户提供高质量的食品和满意的服务。
第三个案例是斯图亚特·麦迪逊酒店。
这家酒店以提供尽可能高效和舒适的服务而闻名。
他们利用精益思维来优化客户服务流程,通过减少等待时间和提高响应速度来提高客户满意度。
酒店还通过减少不必要的库存和降低员工失误率来降低成本。
通过这些改进,斯图亚特·麦迪逊酒店实现了更高的客户满意度和更好的经济效益。
从这些案例中,我们可以总结出一些精益生产的经验。
首先,流程和操作的标准化是关键,这样可以简化操作,减少浪费并提高效率。
其次,员工培训和参与是至关重要的,员工需要具备改进生产过程的技能和意识。
第三,持续改进是一项重要的工作,公司需要不断地寻找和解决问题,以进一步提高生产效率和质量。
最后,客户需求应始终放在首位,公司需要根据客户需求进行产品和服务的设计和提供。
在实践中,每个组织都可以根据自己的需求和情况进行精益生产的应用。
通过借鉴成功案例的经验并灵活运用其核心原则,可以帮助组织实现更高的效益和更好的竞争力。
精益生产改善案例

精益生产改善案例精益生产是一种持续改进的管理方法,旨在消除浪费、提高效率和质量。
下面我们将介绍一个精益生产改善案例,以便更好地理解这一管理方法的应用。
某汽车零部件生产企业在生产过程中遇到了一些问题,比如生产效率低下、库存积压、质量不稳定等。
为了解决这些问题,企业决定引入精益生产理念进行改善。
首先,企业对生产流程进行了价值流分析,发现在生产过程中存在着许多不必要的环节和浪费。
比如,生产线上的物料运输距离过长,工人需要来回奔波,浪费了大量的时间和精力。
因此,企业决定重新布局生产线,将相关的工序和设备安排在一起,缩短物料运输距离,减少不必要的等待时间,提高生产效率。
其次,企业加强了对员工的培训和激励,鼓励员工提出改进建议,并给予相应的奖励。
通过员工的参与和建议,企业发现了一些隐藏的问题和改进的空间,比如设备维护不到位、工艺参数不合理等。
企业立即采取了相应的措施,加强设备维护保养,优化工艺参数,提高了生产效率和产品质量。
最后,企业建立了一套全面的质量管理体系,包括从原材料采购到成品出厂的全过程控制和监督。
通过引入精益生产的质量管理工具,比如5S、KAIZEN等,企业不断改进和优化质量管理流程,提高了产品的一致性和稳定性。
经过一段时间的努力,企业取得了显著的成效。
生产效率得到了提升,库存积压问题得到了缓解,产品质量得到了提高,客户满意度也有了明显的提升。
精益生产的改善案例为企业带来了实实在在的经济效益和社会效益。
通过这个案例,我们可以看到精益生产的改善方法是多方面的,不仅仅局限于生产流程的优化,还包括员工的参与和质量管理的全面提升。
精益生产不仅仅是一种管理方法,更是一种企业文化和理念,需要企业全体员工的共同努力和持续改进。
总之,精益生产是一种不断改进的管理方法,通过消除浪费、提高效率和质量,帮助企业实现持续增长和发展。
希望这个案例能够给大家带来一些启发,也希望更多的企业能够积极引入精益生产理念,不断改进和提高自身的竞争力。
精益生产改善案例

精益生产改善案例在一个制造业公司中,生产线上的某个环节出现了严重的问题。
这个环节的效率低下,导致了产品的生产速度慢,生产线的停工时间增多,生产成本增加,产品质量也难以得到保证。
为了解决这个问题,公司决定采用精益生产的方法来进行改善。
首先,公司组建了一个跨职能的改善小组,包括了生产部门的一些工人和管理人员,以及质量部门的相关人员。
他们共同分析了存在问题的环节,并列出了一系列可能的改进措施。
经过多次头脑风暴和讨论,小组决定首先进行5S的改善。
他们认为,通过清除现场的垃圾和无用物品,对工作区进行规划和标识,可以提高工作效率并减少错误发生的可能性。
于是,小组成员将现场进行了清扫和整理,制定了工具的放置位置,并贴上了标识。
清理过程中,他们发现了一些不必要的材料和设备,这些都被清理出现场。
然后,小组开始进行价值流分析,以了解整个生产线上的价值流,查找潜在的浪费和瓶颈。
他们使用了看板来跟踪和控制生产进度,并制定了一些指标来评估生产效率和质量。
通过价值流分析,他们发现在工艺流程中的某个关键环节存在操作不一致的问题,这导致了产品的质量不稳定和生产速度的下降。
小组成员决定在这个环节上进行标准化工作的改进。
他们参考了最佳操作的方法,并通过培训和激励措施,促使工人们按照标准进行操作。
他们还使用了一些帮助工人准确操作的工具,如工装夹具和指导书。
最后,小组对整个生产线进行了持续改进的追踪和监控。
他们设立了一个改进看板,记录并跟踪改进措施的实施和效果。
每周,小组会召开例会,评估改进措施的成效,并对存在的问题进行讨论和解决。
经过几个月的努力,公司开始看到改善的成果。
生产线上的效率明显提高,生产成本减少,产品质量稳定提升。
员工的工作积极性和满意度也得到了明显的提升。
通过精益生产方法的应用,这个制造业公司成功解决了生产线上存在的严重问题。
这个案例展示了精益生产的潜力和价值,证明了通过精益生产的改进方法,可以提高生产效率,降低成本,提升产品质量,增强公司的竞争力。
精益生产经典案例
精益生产经典事例2016-02-16 精益生产促使中心自动化与防呆防错一个小改良的大成效零缺点最大的诀窍:经过挖掘人的智慧,找到了傻瓜都能做对的方法,减少质量对人的依靠。
有一家电子生产型公司,他们在组装设施时因为需要装置的螺丝数目多,操作工常常会有忘记,致使不良。
以后,公司就从精益生产的角度进行考虑,降低人的要素。
他们特意设计了一种机械手,机械手尾端有磁铁。
假如这个部位需要装 5 颗螺丝,机械手就自动抓起 5 颗螺丝,假如需要装 16 颗螺丝,机械手就自动抓起 16 颗螺丝。
操作工只需看下机械手上有没有节余的螺丝就能够了。
这样就减少了质量不良的发生。
还有一家生产复印机的工厂,他们的复印机里面有一个小电扇,这个小电扇特别重要,一旦装反了,就会致使机械破坏。
但因为是流水线作业,操作工在装置时,因为疲惫、忘记等多种原由,可能会犯错。
主管就要求操作工装好后要进行检查,用手摸一下,试下风向。
可是每日生产数千台复印机,操作工人可能就会产生错觉,有风没风不高兴了,走神了,仍是会产生装反的现象。
以后,就经过挖掘员工潜能,在复印机旁边装一个小风车,假如装置正确就会有风,风车会转,所以只需风车会转,装置就是完满的,不然,就是错误的。
这样这家公司复印机的合格率就大大提升了。
怎样加强管理目视化的改良某公司有一个开放式的大办公室,有 200 人在一同办公。
因为管理不到位,常常发生办公室的灯、空调没相关的现象。
近来,公司高层也知道了此事,指示行政部一定加强管理,赶快解决此问题。
于是行政部想了很多方法,如:出台制度、人走灯灭、保安检查、领导值班检查、进行处分、通告等。
一开始还可以起到必定作用,但时间一长,因为监察不到位,老问题仍是持续发生,制度落实不好。
其实,制度诚然重要,但不可以迷信制度。
这属于无心识犯错,无心识犯错是不可以够用制度来拘束的。
管理很重要,但职工的自主管理更重要。
某酒店想出了一个好方法:他们在每位客人的房间钥匙上都有一个卡,这个卡插进去,经过感觉电源才能开通,只需一锁门,钥匙一取出来,就自动断电了,灯也就灭了。
精益生产改善案例
精益生产改善案例精益生产是一种持续改善的管理方法,旨在消除浪费、提高效率和质量。
在实践中,精益生产可以应用于各种行业和组织,带来显著的改善效果。
下面我们将介绍一个关于精益生产改善的案例,以便更好地理解其实际应用。
这个案例发生在一家汽车零部件制造公司。
在过去,该公司的生产线存在着许多浪费,如过多的库存、不必要的运输、瑕疵品的产生等。
这些问题导致了生产效率低下和成本的增加,因此公司决定引入精益生产来改善现状。
首先,公司对生产线进行价值流分析,找出了造成浪费的根本原因。
他们发现,生产线上存在着不必要的等待时间、过多的库存积压和瑕疵品的频繁出现。
为了解决这些问题,公司采取了一系列措施。
首先,他们优化了生产线的布局,将工作站重新排列,减少了物料运输的距离,缩短了等待时间。
其次,他们实施了定期保养和设备维护计划,以确保设备的正常运转,减少了停机时间。
同时,他们加强了对员工的培训,提高了生产线的灵活性和适应性,减少了瑕疵品的产生。
经过这些改进措施的实施,公司取得了显著的成效。
生产效率得到了提高,库存周转率大幅增加,瑕疵品率显著下降。
同时,员工的工作积极性和满意度也得到了提升。
通过这个案例,我们可以看到精益生产在实际应用中的巨大潜力。
只要公司能够深入分析问题,找出根本原因,并采取有效的改进措施,就能够取得显著的改善效果。
因此,我们鼓励更多的企业和组织引入精益生产,不断优化自身的生产流程,提高竞争力。
总之,精益生产改善案例向我们展示了一种持续改善的管理方法,它能够帮助企业发现和消除各种形式的浪费,提高效率和质量,实现持续增长。
希望这个案例能够对大家有所启发,促使更多的企业关注精益生产,实现更好的发展。
精益生产案例分享
精益生产案例分享:丰田汽车1. 背景丰田汽车公司是世界上最大的汽车制造商之一,以其高效的生产方式和卓越的质量管理而闻名。
丰田在20世纪50年代引入了精益生产方法,这一方法通过减少浪费、提高效率和质量来优化生产流程。
下面将以丰田汽车为例,介绍其在生产过程中应用精益生产的具体案例。
2. 过程2.1 TPS(丰田生产系统)丰田生产系统(Toyota Production System,简称TPS)是精益生产方法的核心。
其主要原则包括“消除浪费”、“建立流程”和“实现标准化”。
TPS通过以下几个关键元素来实现这些原则:2.1.1 精确计划在TPS中,每个工作站都有一个明确的计划,并按照计划进行操作。
这样可以避免不必要的等待时间和浪费。
2.1.2 拉动式生产TPS采用拉动式生产模式,即根据需求进行生产,而不是按照预定计划进行推动式生产。
这样可以减少库存和过剩生产。
2.1.3 Jidoka(自动停线)丰田引入了Jidoka概念,即在生产过程中发现问题时立即停线,确保问题不会进一步传递。
这有助于提高质量和避免缺陷。
2.2 案例:丰田生产线改进丰田在其汽车生产线上应用精益生产方法,不断改进生产效率和质量。
下面是一个具体案例:2.2.1 背景在某条汽车装配线上,存在着许多浪费和效率低下的问题。
工人需要花费大量时间等待零部件供应、处理缺陷和调整机器。
这导致了生产周期长、质量不稳定和成本增加。
2.2.2 过程改进丰田采取了以下措施来改善这条装配线的效率:2.2.2.1 流程优化首先,丰田分析了装配线上的每个工序,并找出了其中的浪费和瓶颈。
他们通过重组工序、优化布局和消除不必要的动作来简化流程,并减少等待时间。
2.2.2.2 JIT(准时生产)丰田实施了JIT生产模式,即按需生产。
他们与供应商建立了紧密的合作关系,确保零部件能够准时到达装配线。
这样可以减少库存和等待时间。
2.2.2.3 自动化和标准化丰田引入了更多的自动化设备和机器人来替代繁重的人工劳动。
5个案例,秒懂精益生产精髓
Mindset & Innovation40网印工业Screen Printing Industry2020.05理念与新知精益生产,创造性地解决了适应市场多品种、少批量产品需求带来的切换和浪费问题,被称为是当前工业界最佳的一种生产组织体系和方式。
在疫情突发与经济下滑的形势下,印刷企业更应该向管理要效益,组织精益生产,提高劳动利用率,达到降低成本、缩短生产周期和改善产品质量的目的。
精益生产的优势体现在日常工作中的点点滴滴,下面分享5个经典案例,希望能给大家带来启示。
自动化与防呆防错 一个小改善的大效果有一家生产复印机的工厂,他们的复印机里面有一个小风扇,这个小风扇非常重要,一旦装反了,就会导致机械损坏。
但由于是流水线作业,操作工在装配时,由于疲劳、遗忘等多种原因,可能会出错。
主管就要求操作工装好后要进行检查,用手摸一下,试下风向。
但是每天生产数千台复印机,操作工人可能就会产生错觉,有风?没风?不开心了,走神了,总之还是会产生装反的现象。
后来,在复印机旁边装了一个小风车,如果装配正确就会有风,风车会转,因此只要风车会转,装配就是完好的,否则,就是错误的。
因此,这家公司复印机的生产合格率就大大提高了。
强化管理之——目视化的改善某企业有一个开放式的大办公室,有200人在一起办公。
由于管理不到位,经常发生办公室的灯、空调没有关的现象。
最近,公司高层也知道了此事,指示行政部必须强化管理,尽快解决此问题。
于是行政部想了许多办法,如:出台制度、人走灯灭、保安检查、领导值班检查、进行处罚、公告等。
一开始还能起到一定作用,但时间一长,由于监督不到位,老问题还是继续发生,制度落实不好。
其实,制度固然重要,但不能迷信制度。
这属于无意识犯错,无意识犯错是不可以用制度来约束的。
管理很重要,但员工的自主管理更重要。
5个案例,秒懂精益生产精髓Mindset & Innovation 41网印工业Screen Printing Industry2020.05理念与新知一个公司通过努力也想出了好办法:他们在公司的门上设计了一个卡通画,只要一锁门,就会有一个卡通画跳出来,问“你关灯了吗?”通过这种人性化的管理和提醒,忘记关灯和空调的现象终于杜绝了。
- 1、下载文档前请自行甄别文档内容的完整性,平台不提供额外的编辑、内容补充、找答案等附加服务。
- 2、"仅部分预览"的文档,不可在线预览部分如存在完整性等问题,可反馈申请退款(可完整预览的文档不适用该条件!)。
- 3、如文档侵犯您的权益,请联系客服反馈,我们会尽快为您处理(人工客服工作时间:9:00-18:30)。
精益生产经典案例
2016-02-16精益生产促进中心
自动化与防呆防错一个小改善的大效果
零缺陷最大的窍门:通过发掘人的智慧,找到了傻瓜都能做对的办法,减少品质对人的依赖。
有一家电子生产型企业,他们在组装设备时由于需要装配的螺丝数量多,操作工经常会有遗忘,导致不良。
后来,公司就从精益生产的角度进行考虑,降低人的因素。
他们专门设计了一种机械手,机械手末端有磁铁。
如果这个部位需要装5颗螺丝,机械手就自动抓起5颗螺丝,如果需要装16颗螺丝,机械手就自动抓起16颗螺丝。
操作工只要看下机械手上有没有剩余的螺丝就可以了。
这样就减少了品质不良的发生。
还有一家生产复印机的工厂,他们的复印机里面有一个小风扇,这个小风扇非常重要,一旦装反了,就会导致机械损坏。
但由于是流水线作业,操作工在装配时,由于疲劳、遗忘等多种原因,可能会出错。
主管就要求操作工装好后要进行检查,用手摸一下,试下风向。
但是每天生产数千台复印机,操作工人可能就会产生错觉,有风没风不开心了,走神了,还是会产生装反的现象。
后来,就通过发掘员工潜能,在复印机旁边装一个小风车,如果装配正确就会有风,风车会转,因此只要风车会转,装配就是完好的,否则,就是错误的。
这样这家公司复印机的合格率就大大提高了。
如何强化管理目视化的改善
某企业有一个开放式的大办公室,有200人在一起办公。
由于管理不到位,经常发生办公室的灯、空调没有关的现象。
最近,公司高层也知道了此事,指示行政部必须强化管理,尽快解决此问题。
于是行政部想了许多办法,如:出台制度、人走灯灭、保安检查、领导值班检查、进行处罚、公告等。
一开始还能起到一定作用,但时间一长,由于监督不到位,老问题还是继续发生,制度落实不好。
其实,制度固然重要,但不能迷信制度。
这属于无意识犯错,无意识犯错是不可以用制度来约束的。
管理很重要,但员工的自主管理更重要。
某酒店想出了一个好方法:他们在每位客人的房间钥匙上都有一个卡,这个卡插进去,通过感应电源才能开通,只要一锁门,钥匙一拿出来,就自动断电了,灯也就灭了。
一个公司通过努力也想出了好办法:他们在公司的门上设计了一个卡通画,只要一锁门,就会有一个卡通画跳出来,问“你关灯了吗”。
通过这种人性化的管理和提醒,忘记关灯和空调的现象终于杜绝了。
美国西南航空学丰田标准化与简单化
日本产品曾经是低劣产品的代名词,美国人曾经看不起日本企业。
但二十世纪头十年,美国先生发生了恐怖袭击、全球金融危机,于是美国人也放下身段向日本人学习。
美国西南航空学习日本丰田公司,推行精益生产。
他们所有的机型就只有一种,就是737客机。
这样设备操作简单化,机师维护简单化,设备配件也简单化,他们是空姐负责飞机的清扫飞机卫生,这样降低了成本,飞机的中转时间也大大缩短了。
另外,还有一个好处,就是这里的飞行员、机师、空姐等非常稳定,为什么因这他们就只熟悉737机型,到其他航空公司不好找工作。
关于洗手间的改善小智慧,大改善
在提倡TPM—工厂全面改善的过程中,小小的洗手间也是一个大有作为的地方,可以创造出你意想不到的价值。
1、利用马桶节约用水。
为了节约用水,某公司员工想出一个办法。
经过多次试验,他在马桶内加上二块砖,里面装的水就少了,这样即能保证冲洗干净,也能节约用水。
2、小便池前滴漏。
由于男生在小便时离便池远,导致小便池前滴漏。
解决这种问题用行政命令显然不行,于是他们想出了一个好主意。
他们在小便前帖了一些幽默小故事,标题很大,但内容字体很小,须走近才能看得清楚。
于是这一困惑管理的难题较好的解决了。
但是在实际中千万不能搞反了,如果内容字体很大,他们就会离得远才看的清楚。
3、水龙头忘记关。
可以采用延时开关。
4、电灯忘记关。
可以用声音感应开关。
5、厕纸浪费。
一开始他们把纸放在洗手间便池隔间里,但是这样用的很快。
经过观察他们发现,是许多员工浪费,甚至装在自己口袋里带走了。
后来,他们就把纸放在隔间外面,这样由于洗手间人来人往,有了监督,大家就不好意思浪费,更不好意思私自带走了。
简单做管理,需要大智慧。
看理光、丰田如何做管理日本公司留人的故事
有一家日本公司,他们的总经理是一位65岁的老人,他是退休后又被公司返聘的。
他说,留人的关键是真正爱员工,全神贯注地考虑员工需求,去满足他们。
他有一个好习惯是每周陪员工工作2小时,了解他们的辛苦。
我始终为一线员工说话,让每一个弱势群体感觉到有一个为他们撑腰的人。
为了员工成长,他们身体力行,全力付出。
同时要善待每一位离开的员工。
让他们想念、怀念这个曾经的家园!。