各种回收氨方法比较
弗萨姆法回收氨的基本原理

弗萨姆法回收氨的基本原理
弗萨姆法是一种回收氨的方法,其基本原理是通过将废水中的氨与硫酸反应生成硫酸铵沉淀,从而实现氨的回收。
具体步骤如下:
1. 将废水中的氨与硫酸进行反应,生成铵离子(NH4+)和硫酸根离子(SO4^-2)。
2NH3 + H2SO4 →(NH4)2SO4
2. 硫酸铵是一种沉淀,可以通过沉淀法进行固液分离。
将产生的硫酸铵沉淀从废水中分离出来。
3. 硫酸铵沉淀可以进一步经过热解、结晶等工艺步骤进行后续处理,从而得到高纯度的氨。
通过弗萨姆法回收氨的优点是操作简便、成本较低,能够高效地回收废水中的氨并得到可再利用的硫酸铵产品。
这种方法在废水处理和化工生产过程中得到了广泛应用。
氨液回收应急处置方案

氨液回收应急处置方案背景说明氨液是一种常见的化学品,具有强烈的刺激性和腐蚀性。
在氨液的生产、运输和使用过程中,若发生泄漏事故,将会对环境和人体健康造成严重威胁。
因此,建立有效的氨液泄漏应急处置方案至关重要。
泄漏应急处置步骤以下是氨液泄漏应急处置的步骤:1.第一时间向氨液泄漏区域内的所有人员发出警报信号,让人员立即撤离现场。
2.立即启动氨液泄漏应急预案,并通知应急救援队伍赶到现场进行处置。
3.应急救援队伍在到达现场后,应首先做好防护措施,穿戴好防护设备。
同时,进行初步的现场评估,确定氨液泄漏的范围和情况。
4.针对不同的泄漏情况,进行相应的处置措施。
若是气体泄漏,则应设置隔离带,并采取措施将泄漏气体转移,避免进入周围环境。
若是液体泄漏,则应立即清除泄漏物,并封锁泄漏源头,避免泄漏扩散。
5.处置完毕后,应进行全面的现场检查,以确保已经清除干净,不存在危险的可能。
6.对已经处置的废气、废液等污染物进行正确的处理,避免对周围环境造成二次污染。
氨液回收的方法氨液回收是避免氨液泄漏对环境造成污染的有效方法。
以下是常见的氨液回收方法:1.吸收法:采用酸、碱溶液等吸收剂,将氨气吸收成液体。
常用的吸收剂有硫酸、氢氧化钠等。
吸收法回收的氨液还可以再利用。
2.冷凝法:将氨气冷却至低温后,形成液体。
通常可以通过制冷机等设备降低温度。
3.膜法:利用半透膜将氨气割离,并将其转化为液态氨。
常见的膜材有聚酰胺、硅酸盐等。
安全注意事项在氨液泄漏应急处置的过程中,需要注意以下安全事项:1.切记不要在未穿戴防护设备时进入泄漏现场。
2.多采取远离氨气的策略,并保持空气流通。
3.切勿直接接触氨液,以免发生皮肤腐蚀。
4.应在专业人员的指导下进行处置过程。
总结氨液是一种危险品,必须要有应急预案来应对可能的泄漏事件。
事前制定应急处置方案,涵盖了泄露的预防和处置的全面考虑,相信在未来的工作中,我们可以更加有效地防范和处置化学品泄漏事故的发生。
氨回收分离工艺简介
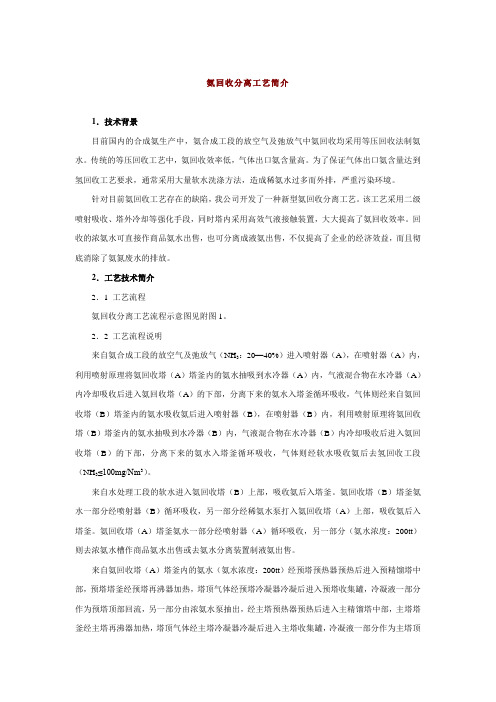
氨回收分离工艺简介1.技术背景目前国内的合成氨生产中,氨合成工段的放空气及弛放气中氨回收均采用等压回收法制氨水。
传统的等压回收工艺中,氨回收效率低,气体出口氨含量高。
为了保证气体出口氨含量达到氢回收工艺要求,通常采用大量软水洗涤方法,造成稀氨水过多而外排,严重污染环境。
针对目前氨回收工艺存在的缺陷,我公司开发了一种新型氨回收分离工艺。
该工艺采用二级喷射吸收、塔外冷却等强化手段,同时塔内采用高效气液接触装置,大大提高了氨回收效率。
回收的浓氨水可直接作商品氨水出售,也可分离成液氨出售,不仅提高了企业的经济效益,而且彻底消除了氨氮废水的排放。
2.工艺技术简介2.1 工艺流程氨回收分离工艺流程示意图见附图1。
2.2 工艺流程说明来自氨合成工段的放空气及弛放气(NH3:20—40%)进入喷射器(A),在喷射器(A)内,利用喷射原理将氨回收塔(A)塔釜内的氨水抽吸到水冷器(A)内,气液混合物在水冷器(A)内冷却吸收后进入氨回收塔(A)的下部,分离下来的氨水入塔釜循环吸收,气体则经来自氨回收塔(B)塔釜内的氨水吸收氨后进入喷射器(B),在喷射器(B)内,利用喷射原理将氨回收塔(B)塔釜内的氨水抽吸到水冷器(B)内,气液混合物在水冷器(B)内冷却吸收后进入氨回收塔(B)的下部,分离下来的氨水入塔釜循环吸收,气体则经软水吸收氨后去氢回收工段(NH3≤100mg/Nm3)。
来自水处理工段的软水进入氨回收塔(B)上部,吸收氨后入塔釜。
氨回收塔(B)塔釜氨水一部分经喷射器(B)循环吸收,另一部分经稀氨水泵打入氨回收塔(A)上部,吸收氨后入塔釜。
氨回收塔(A)塔釜氨水一部分经喷射器(A)循环吸收,另一部分(氨水浓度:200tt)则去浓氨水槽作商品氨水出售或去氨水分离装置制液氨出售。
来自氨回收塔(A)塔釜内的氨水(氨水浓度:200tt)经预塔预热器预热后进入预精馏塔中部,预塔塔釜经预塔再沸器加热,塔顶气体经预塔冷凝器冷凝后进入预塔收集罐,冷凝液一部分作为预塔顶部回流,另一部分由浓氨水泵抽出,经主塔预热器预热后进入主精馏塔中部,主塔塔釜经主塔再沸器加热,塔顶气体经主塔冷凝器冷凝后进入主塔收集罐,冷凝液一部分作为主塔顶部回流,另一部分则去液氨贮槽作商品液氨出售。
氨气的回收
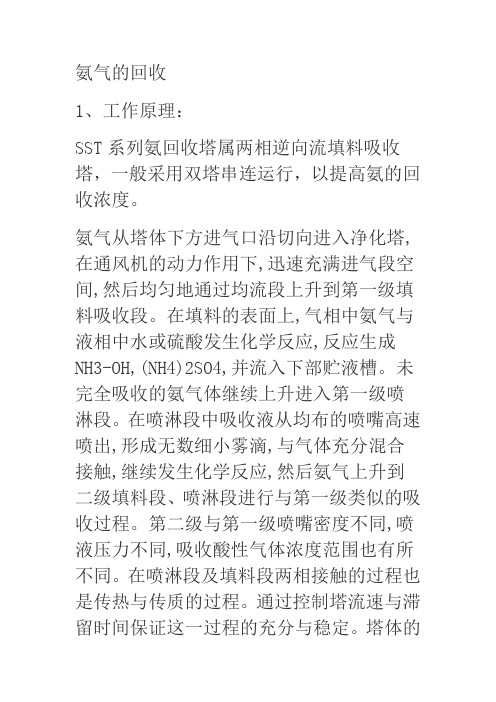
氨气的回收1、工作原理:SST系列氨回收塔属两相逆向流填料吸收塔,一般采用双塔串连运行,以提高氨的回收浓度。
氨气从塔体下方进气口沿切向进入净化塔,在通风机的动力作用下,迅速充满进气段空间,然后均匀地通过均流段上升到第一级填料吸收段。
在填料的表面上,气相中氨气与液相中水或硫酸发生化学反应,反应生成NH3-OH,(NH4)2SO4,并流入下部贮液槽。
未完全吸收的氨气体继续上升进入第一级喷淋段。
在喷淋段中吸收液从均布的喷嘴高速喷出,形成无数细小雾滴,与气体充分混合接触,继续发生化学反应,然后氨气上升到二级填料段、喷淋段进行与第一级类似的吸收过程。
第二级与第一级喷嘴密度不同,喷液压力不同,吸收酸性气体浓度范围也有所不同。
在喷淋段及填料段两相接触的过程也是传热与传质的过程。
通过控制塔流速与滞留时间保证这一过程的充分与稳定。
塔体的最上部是除雾段,气体中所夹的吸收液雾滴在这里被清除下来,经过处理后的洁净空气从净化塔上端排气管排入大气。
经过水或硫酸吸收的NH3-OH,(NH4)2SO4,可用于锅炉脱硫或作农肥。
2、性能特点:(1)净化率高SST系列氨回收塔采用二级逆向喷淋,填料比表面积大,由试验研究确定的气液比保证了性能稳定,对氨气的吸收效率可达到85%~95%。
(2)设备阻力低在保证足够气液接触面积基础上,SST系列吸收塔选用空气动力特性最佳的填料品种及结构形式,使设备阻力在额定风量下不超过40毫米水柱,是国内各种填料吸收塔中阻力最低的一种。
这对于配用耐腐蚀低压通风极为有利。
(3)占地面积小SST系列氨回收塔将塔体、吸收液槽、循环泵、吸收液管道系统组合成一套完整的设备,结构紧凑,便于现场安装及操作管理。
各种回收氨方法比较
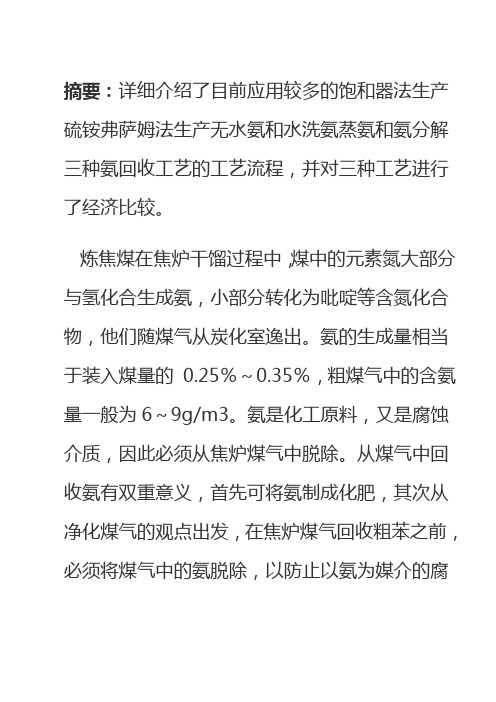
摘要:详细介绍了目前应用较多的饱和器法生产硫铵弗萨姆法生产无水氨和水洗氨蒸氨和氨分解三种氨回收工艺的工艺流程,并对三种工艺进行了经济比较。
炼焦煤在焦炉干馏过程中,煤中的元素氮大部分与氢化合生成氨,小部分转化为吡啶等含氮化合物,他们随煤气从炭化室逸出。
氨的生成量相当于装入煤量的 0.25%~0.35%,粗煤气中的含氨量一般为6~9g/m3。
氨是化工原料,又是腐蚀介质,因此必须从焦炉煤气中脱除。
从煤气中回收氨有双重意义,首先可将氨制成化肥,其次从净化煤气的观点出发,在焦炉煤气回收粗苯之前,必须将煤气中的氨脱除,以防止以氨为媒介的腐蚀性介质进入粗苯回收系统而造成设备的严重腐蚀。
对于氨的脱除,目前我国广泛采用的有三种不同类型的工艺,即生产硫铵、无水氨和氨分解等工艺。
硫铵工艺所得硫酸铵的国家标准见下表。
硫酸铵的国家标准名称指标一级品二级品三级品氮含量(以干基计),%≮21 ≮20.8≮20.6水分,%≯0.1≯1.0≯2.0游离酸(H2S4O) ,%≯0.05≯0.2≯0.3粒度(60目筛余量),%≮75 --颜色白色或微带颜色的结晶生产无水氨工艺所得的无水氨主要用于制造氮肥和复合肥料,还可用于制造硝酸、各种含氮无机盐及有机物中间体、磺胺药、聚氨酯、聚酰胺纤维和丁腈橡胶等。
此外,还常用作制冷剂。
氨分解工艺所产生的废气送入鼓风机前的吸煤气管道,但该工艺装臵无产品回收。
1 硫铵生产工艺生产硫铵是焦炉煤气净化工艺流程中回收氨的传统方法。
我国20世纪60年代以前建成的大中型焦化厂均采用半直接法鼓泡型饱和器生产硫铵,该工艺的主要缺点是设备腐蚀严重,硫铵质量差,煤气系统阻力大。
在宝钢一期工程的建设中,我们引进了酸洗法生产硫铵工艺,它是由酸洗、真空蒸发结晶以及硫铵离心、干燥、包装等三部分组成。
与饱和器法相比,由于实现了氨的吸收与硫铵结晶分离的操作,以获得优质大颗粒硫铵结晶。
酸洗塔结构为空喷塔,煤气系统阻力仅为饱和器的1/4,煤气鼓风机的电耗可大幅度下降。
氨逃逸的处理工艺

氨逃逸的处理工艺全文共四篇示例,供读者参考第一篇示例:氨是一种无色气体,常用于工业生产中的各种用途,但如果氨气从工厂中逃逸,可能会对环境和工人的健康造成严重危害。
必须采取适当的处理工艺来控制和处理氨气的逃逸。
需要正确识别氨气的来源和逃逸路径。
氨气主要来自于化肥、农药、合成纤维、皮革、食品和医药等工业生产过程中的废气排放。
逃逸的途径主要包括气体泄漏、废气排放口未经处理和设备密封不严等。
针对不同的逃逸来源和途径,可采取多种处理工艺来控制和处理氨气的逃逸。
常见的氨气处理工艺包括氨气回收、氨气吸附、氨气催化氧化和氨气冷凝等。
氨气回收是一种有效的处理工艺,通过使用吸附剂或膜分离等技术,将氨气从废气中分离出来,并将其重新利用于生产过程中。
这样不仅可以减少氨气的排放量,还可以减少生产成本,提高资源利用率。
氨气吸附是一种通过吸附剂吸附氨气的技术,常用的吸附剂包括活性碳、分子筛等。
吸附后的氨气可以通过再生处理,将其提取出来或转化成其他有用的化合物。
这种处理工艺可以有效去除废气中的氨气,减少对环境的污染。
氨气催化氧化是利用氧化剂(如过氧化氢、臭氧等)将氨气氧化成无害的气体(如氮氧化物和水蒸气)的技术。
这种处理工艺具有高效、环保、节能的优点,可以有效减少氨气的排放量。
氨气冷凝是一种通过降低废气温度,使氨气在废气中凝结成液态,然后进行收集和处理的技术。
这种处理工艺适用于高温高浓度的氨气废气,可以有效减少氨气的排放量,同时也可以回收氨气以降低成本。
针对氨气的逃逸问题,我们可以采取适当的处理工艺来控制和处理。
通过氨气回收、氨气吸附、氨气催化氧化和氨气冷凝等处理工艺的结合应用,可以有效减少氨气的排放量,保护环境,确保工人健康,并且提高资源利用效率。
希望各生产企业重视氨气排放问题,积极采取相应的处理措施,共同建设清洁美丽的环境。
【字数:443】第二篇示例:氨气是一种常见的气体,在工业生产、化工加工、农业施肥等过程中会不可避免地产生。
制冷系统氨液回收方案
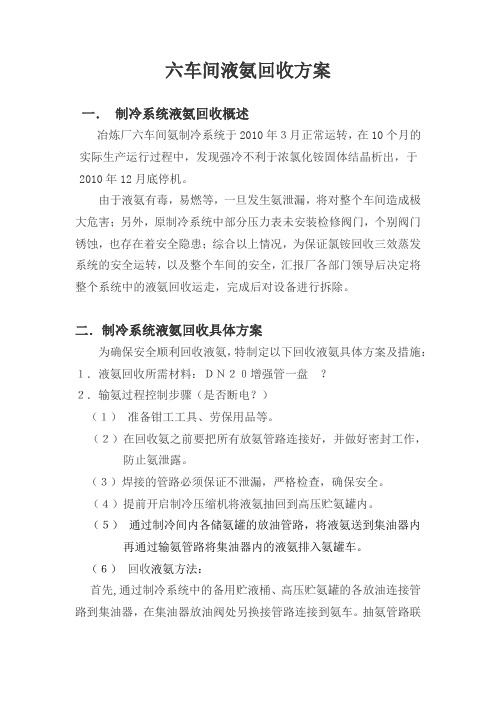
六车间液氨回收方案一.制冷系统液氨回收概述冶炼厂六车间氨制冷系统于2010年3月正常运转,在10个月的实际生产运行过程中,发现强冷不利于浓氯化铵固体结晶析出,于2010年12月底停机。
由于液氨有毒,易燃等,一旦发生氨泄漏,将对整个车间造成极大危害;另外,原制冷系统中部分压力表未安装检修阀门,个别阀门锈蚀,也存在着安全隐患;综合以上情况,为保证氯铵回收三效蒸发系统的安全运转,以及整个车间的安全,汇报厂各部门领导后决定将整个系统中的液氨回收运走,完成后对设备进行拆除。
二.制冷系统液氨回收具体方案为确保安全顺利回收液氨,特制定以下回收液氨具体方案及措施:1.液氨回收所需材料:DN20增强管一盘?2.输氨过程控制步骤(是否断电?)(1)准备钳工工具、劳保用品等。
(2)在回收氨之前要把所有放氨管路连接好,并做好密封工作,防止氨泄露。
(3)焊接的管路必须保证不泄漏,严格检查,确保安全。
(4)提前开启制冷压缩机将液氨抽回到高压贮氨罐内。
(5)通过制冷间内各储氨罐的放油管路,将液氨送到集油器内再通过输氨管路将集油器内的液氨排入氨罐车。
(6)回收液氨方法:首先,通过制冷系统中的备用贮液桶、高压贮氨罐的各放油连接管路到集油器,在集油器放油阀处另换接管路连接到氨车。
抽氨管路联接好之后打开各相应的阀门开始放氨。
(虹吸罐剩余、压缩机油冷却器中的液氨可从各自的放油阀处另设单独管路抽取,设软接头,或另行办法解决。
制冷机中的少量液氨通过集油器放出,如果放不出,可让其自然蒸发)。
其次,两贮氨罐中的液氨抽去完毕之后,开启小活塞压缩机继续抽空,将抽出的少量剩余氨气体冷却之后通过蒸发冷冷却成液氨之后,放入备用高压贮液桶。
最后,系统剩余少量氨气,可通过原配置的活塞压缩机,经加氨站,把加氨站两排气阀打开,关闭其余两个加氨阀门,同时将小型活塞压缩机的冷凝器冷却水进出口连接进出水管路并注入循环冷却水,用来冷却氨气体。
并将压缩机排气阀关闭,通过小型压缩机将系统中的气体吸出并冷却,放出液氨。
第八章----氨的蒸馏与回收
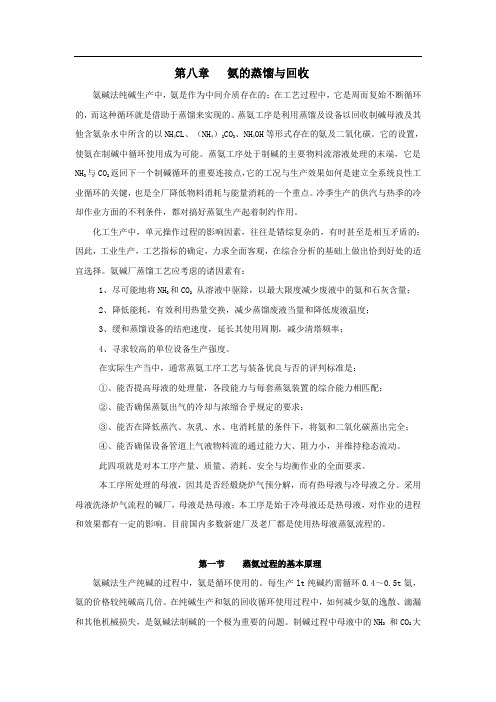
第八章氨的蒸馏与回收氨碱法纯碱生产中,氨是作为中间介质存在的;在工艺过程中,它是周而复始不断循环的,而这种循环就是借助于蒸馏来实现的。
蒸氨工序是利用蒸馏及设备以回收制碱母液及其他含氨杂水中所含的以NH4CL、(NH4)2CO3、NH4OH等形式存在的氨及二氧化碳。
它的设置,使氨在制碱中循环使用成为可能。
蒸氨工序处于制碱的主要物料流溶液处理的末端,它是NH3与CO2返回下一个制碱循环的重要连接点,它的工况与生产效果如何是建立全系统良性工业循环的关键,也是全厂降低物料消耗与能量消耗的一个重点。
冷季生产的供汽与热季的冷却作业方面的不利条件,都对搞好蒸氨生产起着制约作用。
化工生产中,单元操作过程的影响因素,往往是错综复杂的,有时甚至是相互矛盾的;因此,工业生产,工艺指标的确定,力求全面客观,在综合分析的基础上做出恰到好处的适宜选择。
氨碱厂蒸馏工艺应考虑的诸因素有:1、尽可能地将NH3和CO2从溶液中驱除,以最大限度减少废液中的氨和石灰含量;2、降低能耗,有效利用热量交换,减少蒸馏废液当量和降低废液温度;3、缓和蒸馏设备的结疤速度,延长其使用周期,减少清塔频率;4、寻求较高的单位设备生产强度。
在实际生产当中,通常蒸氨工序工艺与装备优良与否的评判标准是:①、能否提高母液的处理量,各段能力与每套蒸氨装置的综合能力相匹配;②、能否确保蒸氨出气的冷却与浓缩合乎规定的要求;③、能否在降低蒸汽、灰乳、水、电消耗量的条件下,将氨和二氧化碳蒸出完全;④、能否确保设备管道上气液物料流的通过能力大、阻力小,并维持稳态流动。
此四项就是对本工序产量、质量、消耗、安全与均衡作业的全面要求。
本工序所处理的母液,因其是否经煅烧炉气预分解,而有热母液与冷母液之分。
采用母液洗涤炉气流程的碱厂,母液是热母液;本工序是始于冷母液还是热母液,对作业的进程和效果都有一定的影响。
目前国内多数新建厂及老厂都是使用热母液蒸氨流程的。
第一节蒸氨过程的基本原理氨碱法生产纯碱的过程中,氨是循环使用的。
- 1、下载文档前请自行甄别文档内容的完整性,平台不提供额外的编辑、内容补充、找答案等附加服务。
- 2、"仅部分预览"的文档,不可在线预览部分如存在完整性等问题,可反馈申请退款(可完整预览的文档不适用该条件!)。
- 3、如文档侵犯您的权益,请联系客服反馈,我们会尽快为您处理(人工客服工作时间:9:00-18:30)。
摘要:详细介绍了目前应用较多的饱和器法生产硫铵弗萨姆法生产无水氨和水洗氨蒸氨和氨分解三种氨回收工艺的工艺流程,并对三种工艺进行了经济比较。
炼焦煤在焦炉干馏过程中,煤中的元素氮大部分与氢化合生成氨,小部分转化为吡啶等含氮化合物,他们随煤气从炭化室逸出。
氨的生成量相当于装入煤量的 0.25%~0.35%,粗煤气中的含氨量一般为6~9g/m3。
氨是化工原料,又是腐蚀介质,因此必须从焦炉煤气中脱除。
从煤气中回收氨有双重意义,首先可将氨制成化肥,其次从净化煤气的观点出发,在焦炉煤气回收粗苯之前,必须将煤气中的氨脱除,以防止以氨为媒介的腐蚀性介质进入粗苯回收系统而造成设备的严重腐蚀。
对于氨的脱除,目前我国广泛采用的有三种不同类型的工艺,即生产硫铵、无水氨和氨分解等工艺。
硫铵工艺所得硫酸铵的国家标准见下表。
硫酸铵的国家标准名称指标一级品二级品三级品氮含量(以干基计),%≮21 ≮20.8≮20.6水分,%≯0.1≯1.0≯2.0游离酸(H2S4O) ,%≯0.05≯0.2≯0.3粒度(60目筛余量),%≮75 --颜色白色或微带颜色的结晶生产无水氨工艺所得的无水氨主要用于制造氮肥和复合肥料,还可用于制造硝酸、各种含氮无机盐及有机物中间体、磺胺药、聚氨酯、聚酰胺纤维和丁腈橡胶等。
此外,还常用作制冷剂。
氨分解工艺所产生的废气送入鼓风机前的吸煤气管道,但该工艺装臵无产品回收。
1 硫铵生产工艺生产硫铵是焦炉煤气净化工艺流程中回收氨的传统方法。
我国20世纪60年代以前建成的大中型焦化厂均采用半直接法鼓泡型饱和器生产硫铵,该工艺的主要缺点是设备腐蚀严重,硫铵质量差,煤气系统阻力大。
在宝钢一期工程的建设中,我们引进了酸洗法生产硫铵工艺,它是由酸洗、真空蒸发结晶以及硫铵离心、干燥、包装等三部分组成。
与饱和器法相比,由于实现了氨的吸收与硫铵结晶分离的操作,以获得优质大颗粒硫铵结晶。
酸洗塔结构为空喷塔,煤气系统阻力仅为饱和器的1/4,煤气鼓风机的电耗可大幅度下降。
采用干燥冷却机将干燥后的硫铵进一步冷却,防止结块,有利于自动包装。
鞍山焦耐院将此工艺经改进后用于天津煤气二厂,装臵投产后已通过了技术鉴定。
在宣钢和北焦的建设中,我们引进了间接法饱和器生产硫铵工艺,该工艺是从酸性气体中回收氨,其硫铵的质量比饱和器法好,但因在较高温度(100℃左右)下操作,对设备和管道材质的要求高,加之饱和器尺寸并不比半直接法小,因此投资高于半直接法。
在杭钢焦化厂,我们将此工艺用于蒸氨塔后氨汽生产硫铵,并已正常投产。
除上述方法外,鞍钢二回收从法国引进的二手设备喷淋式饱和器,以代替半直接法的鼓泡型饱和器。
喷淋式饱和器的特点是煤气系统阻力较小,设备尺寸可相对减小,硫铵质量有所提高。
国内已有不少厂家用其代替老式的鼓泡型饱和器。
但是,不管采用那种生产硫铵的工艺,从经济观点分析,其共同的致命缺点是硫铵的收入远远不够支付其生产费用。
下面重点介绍一下酸洗法和喷淋式饱和器生产硫铵的工艺。
(1)酸洗法生产硫铵工艺。
酸洗法硫铵生产工艺由氨的回收、蒸发结晶与分离干燥等3部分组成。
其工艺流程见图1.如图1 所示,煤气自下而上经过酸洗塔,在酸洗塔分上下两段,均用含游离酸2%~3%的硫铵母液进行喷洒,煤气中的氨即与硫酸结合生成硫铵,从酸洗塔顶逸出煤气经除酸器分离出酸雾后送入煤气总管。
用泵将母液循环槽中的硫铵母液抽送至结晶槽,结晶槽的母液用循环泵抽出,经母液加热器加热后送入真空蒸发器,蒸发器在(绝压)11kPa压力和48℃下工作,母液因真空蒸发而浓缩,浓缩后的过饱和溶液经中心管自流至结晶槽底部。
含有小颗粒结晶的母液在结晶槽中部经循环泵抽出大量循环,使结晶不断长大,几乎不含结晶的母液在结晶槽上部溢流至满流槽,再用泵送回母液循环槽。
大颗粒结晶沉积在结晶槽底部用浆液泵送往供料槽。
蒸发器的真空是用二级蒸汽喷射造成的,蒸汽喷射器使用0.7MPa的中压蒸汽。
从蒸发器上部出来的汽体经第一凝缩器与第二凝缩器冷凝后排往热井。
含有大颗粒结晶的硫铵母液在供料槽内进行沉降分离,上部清液溢流回结晶槽,底部含有50%结晶的母液进入离心机,滤液经滤液槽后再返回结晶槽。
硫铵结晶采用带冷风的干燥冷却器进行干燥、冷却。
酸洗法硫铵与老式饱和器硫铵工艺相比,有以下优点:酸洗法工艺采用空喷塔,煤气系统阻力小,约为饱和器法的1/4~1/5,使风机电耗可以大大降低;酸洗法工艺在酸洗塔内母液始终控制在不饱和状态,结晶颗粒是在真空蒸发结晶系统内形成,由于采用了大流量的母液循环,控制了晶核的形式,并使结晶有足够的成长时间,因而,可以获得大颗粒的优质硫铵结晶。
酸洗法硫铵的设备与管道均采用了超低碳不锈钢(OOCrl7Nil4Mo2),较好地解决了稀硫酸的腐蚀问题,酸洗塔可不设备品,大大减少了设备的维修工作量。
我国自行设计的酸洗法硫铵生产装臵,将酸洗塔由一台两段改为二台各一段的空喷塔,这样,两台可以互为备用,便于连续、稳定生产。
(2) 喷淋式饱和器法硫铵工艺。
喷淋式饱和器硫铵生产工艺与鼓泡式饱和器流程基本一样,只是将喷淋式饱和器代替鼓泡式饱和器。
喷淋式饱和器是将饱和器和结晶器连为一体,流程更为简化。
在此流程中采用母液加热器,从结晶槽顶部一部分母液通过加热器加热,再循环返回饱和器喷淋。
在饱和器底部控制一定的母液液位,母液从满流管流入满流槽。
在满流槽中除去焦油的母液流入母液贮槽。
母液循环泵从结晶槽上部抽出母液,送到喷淋室的环形分配箱进行喷洒,母液循环量为15L/m3。
吸收氨后的母液通过中心降液管向下流到结晶槽底部。
饱和器内母液酸度控制20%~30%,结晶段的结晶体积百分比上限为35%~40%,下限为4%。
晶比达到25%时,启动结晶泵抽取结晶,送往结晶槽提取硫铵。
在保证饱和器水平衡的条件下,一般饱和器母液温度保持在50~55℃,煤气出口温度44~48℃。
喷淋式饱和器的阻力一般为1000~2000Pa,为旧式鼓泡型饱和器的1/5~1/4。
饱和器后的煤气含氨可达到30~50mg/m3。
其流程见图2。
图2 喷淋式饱和器法生产硫铵工艺喷淋式饱和器的结构有如下特点:①喷淋室由本体、外套筒和内套筒组成,煤气进入本体后向下在本体与外套筒的环形室内流动,然后由上出喷淋室,再沿切线方向进入外套筒与内套筒间旋转向下进入内套筒,由顶部出去。
外套筒与内套筒间形成旋风分离作用,以除去煤气夹带的液滴,起到除酸器的作用。
②在喷淋室的下部设臵母液满流管,控制喷淋室下部的液面,促使煤气由入口向出口在环形室内流动。
③在煤气入口和煤气出口间分隔成两个弧形分配箱,在弧形分配箱配臵多组喷嘴,喷嘴方向朝向煤气流,形成良好的气液接触面。
④喷淋室的下部为结晶槽,用降液管与结晶槽连通,循环母液通过降液管从结晶槽的底部向上返,不断生成的硫铵晶核,穿过向上运动的悬浮硫铵母液,促使晶体长大,并引起颗粒分级,小颗粒升向顶部,从上部出口接到循环泵,结晶从下部抽出。
⑤在煤气出口配臵有母液喷洒装臵。
煤气入口和出口均设有温水喷洒装臵,可以较彻底清洗喷淋室。
⑥饱和器材质,国外引进的设备其材质均采用耐酸不锈钢制造,所用材料牌号为URANUS 50(法国牌号);我国引进的酸洗法酸洗塔材质为SUS316L,目前国内采用的喷淋式饱和器和母液加热器均采用SUS316L,它可使用于接触介质硫酸酸度在10%以下的设备。
喷淋式饱和器结构见图3。
喷淋式饱和器结构见图3。
综上所述,喷淋式饱和器工艺综合了旧式饱和器法流程简单,酸洗法有大流量母液循环搅拌,结晶颗粒大的优点,又解决了旧式饱和器法煤气系统阻力大,酸洗法工艺流程长,设备多的缺点。
其工艺流程和操作条件与现有的鼓泡型饱和器相接近,易于掌握,设备材料国内能够解决。
不但可以在新建厂采用,而且更适于老厂的大修改造。
2 生产无水氨的工艺另一种可供选择的脱氨方法是弗萨姆法生产无水氨。
弗萨姆工艺是由美钢联开发的,它可以从焦炉煤气中吸收氨(半直接法),也可以从酸性气中吸收氨(间接法)。
宝钢二期工程从美国U.S.S公司引进了一套从焦炉煤气中吸收氨的弗萨姆装臵,焦炉煤气导入吸收塔与磷酸铵溶液直接接触,吸收煤气中的氨,然后经解析、精馏制取产品无水氨。
该工艺的特点是利用磷酸二氢铵具有选择性吸收的特点,从煤气中回收氨精馏制得高纯度的无水氨(纯度可达99.98%)。
但由于介质具有一定的腐蚀性,且解吸、精馏要求在较高的压力下操作,故对设备材质要求较高。
除此之外,该工艺具有一定的经济规模限制,规模过小既不经济也不好操作。
攀钢焦化厂在引进AS法脱硫的同时引进了一套间接法弗萨姆无水氨装臵,它是将脱酸塔顶的酸性气体引出送入间接法弗萨姆装臵的吸收塔,用磷酸溶液吸收酸性气中的氨。
由于该工艺不与煤气直接接触,几乎不产生酸焦油,与半直接法相比,酸焦油分离和处理设施可大为简化。
弗萨姆装臵生产出的无水氨纯度高,产值较高,经济效益较好。
由于是液体产品储运不方便。
弗萨姆法吸收氨的原理是用磷酸的一铵盐和二铵盐的水溶液从焦炉煤气中选择性吸收氨,吸收了氨的磷铵母液在再生工序的压力下用蒸汽汽提,得到含氨约20%的氨汽,再生后的磷铵母液返回吸收部分循环使用。
含氨20%的氨汽经精馏得到99.98%的无水氨。
这种方法由吸收、解析、精馏三个部分组成其工艺流程见图4, 吸收和再生的代表性化学反应式为:1)氨的吸收。
焦炉煤气从吸收塔底进入,吸收塔为上下两段空喷塔,吸收液与煤气逆流接触,分上下两段单独循环喷洒吸收液,上段吸收液NH3/H3PO4分子数比为1.25,在自身循环过程中吸收了煤气中的氨 ,循环液的分子数比上升为1.35,上段循环液的一部分从塔内溢流到下段作为下段吸收液的补充。
下段吸收液循环吸收氨以后,分子数比达到1.85,抽出循环量的3%送往再生工序。
塔的操作温度为55℃,塔后煤气含氨可达0. lg/m3。
吸收塔的阻力为1.0~1.5kPa。
塔的材质为SUS304L。
2)磷铵母液的再生。
吸收了氨的磷铵母液进入解析塔,先要经过预处理除油,再与解析塔底贫液换热至104℃后进入接触器。
富液除油的方式采用泡沫浮选除焦油器。
由于磷铵母液在吸收氨的过程中吸收了微量酸性气体(H2S, HCN, CO2等)与吸收液中的氨反应生成的铵盐,易在后工序精馏塔内造成堆积而堵塔,所以酸性气体就必须从吸收液中蒸出,这就是接触器的目的。
104℃的富液在接触器中靠精馏工序来的废蒸汽加热至沸点,将溶解在吸收液中的酸性气体蒸出,这些含氨的酸性气体由接触器排出返回吸收塔,接触器材质为SUS316L。
富液经接触器后用泵经气液换热器与解析塔顶的浓氨汽换热,然后再经加热器加热至187℃后进入解析塔顶部,塔底通入直接蒸汽,塔的操作压力约为1. 4MPa。
含氨气体以184℃离开塔顶,经过换热、冷却调节至131℃后进入接受槽作为精馏塔的原料。