注塑成型工艺缺陷分析解决方案
注塑电镀缺陷分析及处理
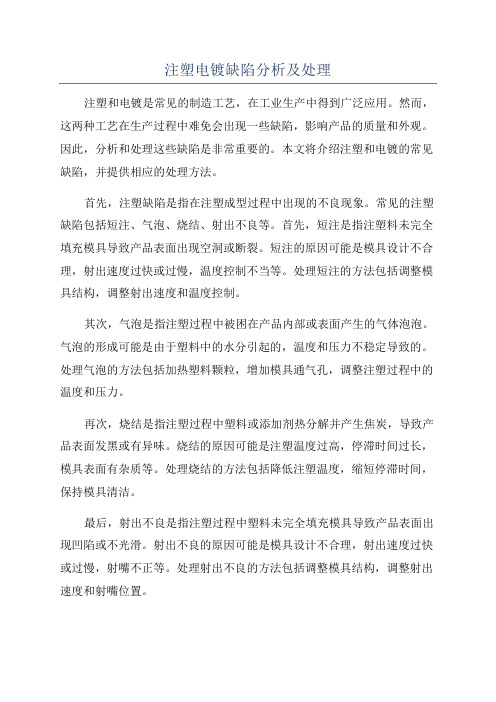
注塑电镀缺陷分析及处理注塑和电镀是常见的制造工艺,在工业生产中得到广泛应用。
然而,这两种工艺在生产过程中难免会出现一些缺陷,影响产品的质量和外观。
因此,分析和处理这些缺陷是非常重要的。
本文将介绍注塑和电镀的常见缺陷,并提供相应的处理方法。
首先,注塑缺陷是指在注塑成型过程中出现的不良现象。
常见的注塑缺陷包括短注、气泡、烧结、射出不良等。
首先,短注是指注塑料未完全填充模具导致产品表面出现空洞或断裂。
短注的原因可能是模具设计不合理,射出速度过快或过慢,温度控制不当等。
处理短注的方法包括调整模具结构,调整射出速度和温度控制。
其次,气泡是指注塑过程中被困在产品内部或表面产生的气体泡泡。
气泡的形成可能是由于塑料中的水分引起的,温度和压力不稳定导致的。
处理气泡的方法包括加热塑料颗粒,增加模具通气孔,调整注塑过程中的温度和压力。
再次,烧结是指注塑过程中塑料或添加剂热分解并产生焦炭,导致产品表面发黑或有异味。
烧结的原因可能是注塑温度过高,停滞时间过长,模具表面有杂质等。
处理烧结的方法包括降低注塑温度,缩短停滞时间,保持模具清洁。
最后,射出不良是指注塑过程中塑料未完全填充模具导致产品表面出现凹陷或不光滑。
射出不良的原因可能是模具设计不合理,射出速度过快或过慢,射嘴不正等。
处理射出不良的方法包括调整模具结构,调整射出速度和射嘴位置。
除了注塑缺陷,电镀缺陷也是制造过程中常见的问题。
常见的电镀缺陷包括气泡、孔洞、颜色不均匀和剥落等。
首先,气泡是指电镀过程中,被电解液困住的气体形成气泡。
气泡的形成可能是由于电解液中含有水分,电镀时间过长或温度不稳定。
处理气泡的方法包括预处理金属表面,控制电解液的成分和温度。
其次,孔洞是指电镀过程中金属表面出现小孔的问题。
孔洞的原因可能是金属表面存在杂质或油污,电镀液配比不当等。
处理孔洞的方法包括清洁金属表面,优化电镀液配比。
再次,颜色不均匀是指电镀后金属表面出现色差或斑点。
颜色不均匀的原因可能是电解液的浓度不一致,电镀时间不稳定或金属表面存在杂质。
注塑缺陷原因分析与解决方案
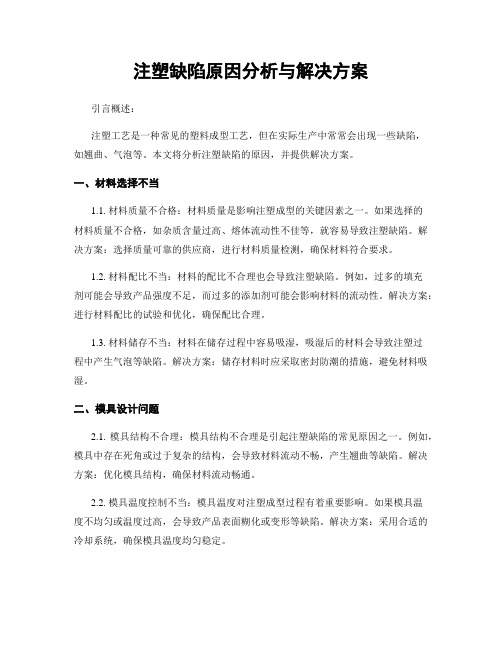
注塑缺陷原因分析与解决方案引言概述:注塑工艺是一种常见的塑料成型工艺,但在实际生产中常常会出现一些缺陷,如翘曲、气泡等。
本文将分析注塑缺陷的原因,并提供解决方案。
一、材料选择不当1.1. 材料质量不合格:材料质量是影响注塑成型的关键因素之一。
如果选择的材料质量不合格,如杂质含量过高、熔体流动性不佳等,就容易导致注塑缺陷。
解决方案:选择质量可靠的供应商,进行材料质量检测,确保材料符合要求。
1.2. 材料配比不当:材料的配比不合理也会导致注塑缺陷。
例如,过多的填充剂可能会导致产品强度不足,而过多的添加剂可能会影响材料的流动性。
解决方案:进行材料配比的试验和优化,确保配比合理。
1.3. 材料储存不当:材料在储存过程中容易吸湿,吸湿后的材料会导致注塑过程中产生气泡等缺陷。
解决方案:储存材料时应采取密封防潮的措施,避免材料吸湿。
二、模具设计问题2.1. 模具结构不合理:模具结构不合理是引起注塑缺陷的常见原因之一。
例如,模具中存在死角或过于复杂的结构,会导致材料流动不畅,产生翘曲等缺陷。
解决方案:优化模具结构,确保材料流动畅通。
2.2. 模具温度控制不当:模具温度对注塑成型过程有着重要影响。
如果模具温度不均匀或温度过高,会导致产品表面糊化或变形等缺陷。
解决方案:采用合适的冷却系统,确保模具温度均匀稳定。
2.3. 模具磨损严重:模具长时间使用后会出现磨损,磨损严重的模具会导致产品尺寸不准确或表面粗糙等缺陷。
解决方案:定期检查和维护模具,及时更换磨损严重的模具部件。
三、注塑工艺参数设置不当3.1. 注射压力过高或过低:注射压力是影响注塑成型的关键参数之一。
如果注射压力过高,会导致产品变形或开裂,而注射压力过低则会导致产品表面光洁度不高。
解决方案:根据产品要求和材料特性,合理设置注射压力。
3.2. 注射速度不合理:注射速度对产品的充填和冷却过程有着重要影响。
如果注射速度过快,会导致产品内部产生气泡或短射,而注射速度过慢则会导致产品表面瑕疵。
常见注塑缺陷及解决方案
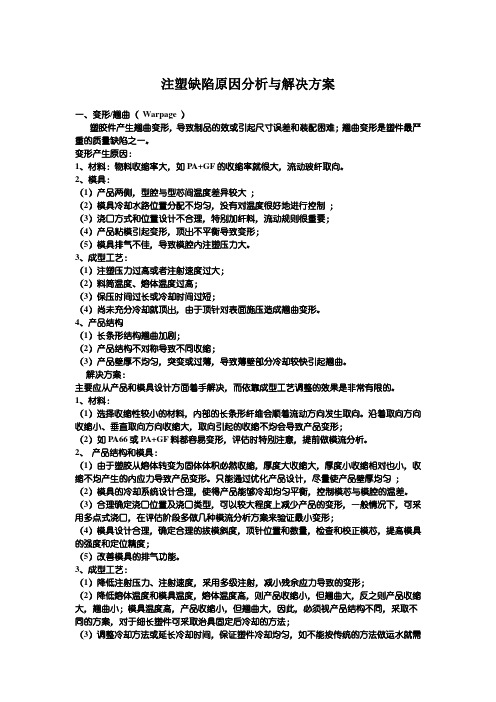
注塑缺陷原因分析与解决方案一、变形/翘曲(Warpage )塑胶件产生翘曲变形,导致制品的效或引起尺寸误差和装配困难;翘曲变形是塑件最严重的质量缺陷之一。
变形产生原因:1、材料:物料收缩率大,如PA+GF的收缩率就很大,流动玻纤取向。
2、模具:(1)产品两侧,型腔与型芯间温度差异较大;(2)模具冷却水路位置分配不均匀,没有对温度很好地进行控制;(3)浇口方式和位置设计不合理,特别加纤料,流动规则很重要;(4)产品粘模引起变形,顶出不平衡导致变形;(5)模具排气不佳,导致模腔内注塑压力大。
3、成型工艺:(1)注塑压力过高或者注射速度过大;(2)料筒温度、熔体温度过高;(3)保压时间过长或冷却时间过短;(4)尚未充分冷却就顶出,由于顶针对表面施压造成翘曲变形。
4、产品结构(1)长条形结构翘曲加剧;(2)产品结构不对称导致不同收缩;(3)产品壁厚不均匀,突变或过薄,导致薄壁部分冷却较快引起翘曲。
解决方案:主要应从产品和模具设计方面着手解决,而依靠成型工艺调整的效果是非常有限的。
1、材料:(1)选择收缩性较小的材料,内部的长条形纤维会顺着流动方向发生取向。
沿着取向方向收缩小、垂直取向方向收缩大,取向引起的收缩不均会导致产品变形;(2)如PA66或PA+GF料都容易变形,评估时特别注意,提前做模流分析。
2、产品结构和模具:(1)由于塑胶从熔体转变为固体体积必然收缩,厚度大收缩大,厚度小收缩相对也小,收缩不均产生的内应力导致产品变形。
只能通过优化产品设计,尽量使产品壁厚均匀;(2)模具的冷却系统设计合理,使得产品能够冷却均匀平衡,控制模芯与模腔的温差。
(3)合理确定浇口位置及浇口类型,可以较大程度上减少产品的变形,一般情况下,可采用多点式浇口,在评估阶段多做几种模流分析方案来验证最小变形;(4)模具设计合理,确定合理的拔模斜度,顶针位置和数量,检查和校正模芯,提高模具的强度和定位精度;(5)改善模具的排气功能。
注塑成型常见不良现象及处理措施

注塑成型常见不良现象及处理措施注塑成型常见的不良现象有以下几种:
1. 短射:指注塑料进模型中未充满模腔,导致产品缺陷。
处理措施:增加注射
压力、延长注射时间、增加料缸温度、增加模具温度、增加模具出料口直径等。
2. 气泡:指产品表面或者内部浮现气泡,影响产品质量。
处理措施:增加注射
压力、延长注射时间、增加模具温度、增加料缸温度、增加模具出料口直径、增加模具排气孔等。
3. 热熔线:指产品表面浮现细小的线状缺陷,通常是由于注射速度过快导致的。
处理措施:减小注射速度、增加模具温度、增加模具出料口直径等。
4. 毛刺:指产品表面浮现细小的凸起,通常是由于模具设计不合理或者模具磨
损导致的。
处理措施:修复模具、修改模具设计、增加模具温度、增加模具出料口直径等。
5. 缩水:指产品尺寸缩小,通常是由于注射压力不足或者冷却时间不足导致的。
处理措施:增加注射压力、延长冷却时间、增加模具温度等。
6. 毛洞:指产品表面或者内部浮现凹陷,通常是由于注射速度过快或者模具设
计不合理导致的。
处理措施:减小注射速度、修改模具设计、增加模具温度等。
处理不良现象的关键是找到问题的根源,然后针对性地采取相应的处理措施。
同时,注塑成型过程中的参数控制和模具维护也是关键的因素,需要进行定期检查和调整。
精华---注塑件常见缺陷分析(王梦庆)

(2)空气如 果气泡粒 极为细微 而密集, 主要分布 在制品浇 口周围, 形成光芒 状纹或扇 形纹,这 多半是空 气引起的 。空气来 源为:
料内夹带 空气。当 浇口料较 多,且颗 粒大小相 差悬殊 时,易夹 带空气。 所以使用 浇口料 时,最好 把粉料筛 选出来。 若熔融时 背压太 低,螺杆 转速又太 高,使螺 杆回退过 快,空气 易随料一 起推向机 筒前端, 故一般提 倡在冷却 时间内尽 量延长熔 融时间, 这对提高 塑化质量 是很有帮
(2)设备方 面由于PC 熔体粘度 高,流动 性差,需 要的注塑 压力大, 与金相接 合力强, 分解物对 金属有强 腐蚀性, 所以在选 择加工设 备时,要 求选用小 型的或特 殊设计的 、镀铬的 螺杆,而 且塑化系 统不允许 有死角、 呆料、缺 口、裂缝 等情况出 现。一般 说来,如 果工艺条 件没问 题,而对
(1)水汽一 般说来, 如果气泡 不规则地 分散在制 品表面, 大都是由 水汽所引 起的。 PC 的热 熔料对水 分非常敏 感,要求 含水量在 0. 02%以 下。所以 要控制水 分的含 量,就要 对料进行 充分的干 燥。一般 PC料的干 燥温度在 120℃左 右,干燥 时间4h左 右,时间 不能太 长,如超 过lOh, 物料易变 质,特别 是加入了 阻燃剂的 料更不宜 干燥时间 过长;而干 燥方式则 以除湿干
(6).检查止 逆阀是否 裂开或无 法运作。
(7).应根据 塑料的特 性改善干 燥条件, 让塑料彻 底干燥。
(8).适当降 低螺杆转 速和增大 背压,或 降低注射 速度。
注塑件弯 曲
1.注塑件 缺陷的特 征
注塑件形 状与模腔 相似但却 是模腔形 状的扭曲 版本。
2.可能出 现问题的 原因
(1).弯曲是 因为注塑 件内有过 多内部应 力。
注塑缺陷描述及解决方案

注塑缺陷描述及解决方案注塑是一种常用的塑料加工方法,通过将熔融的塑料材料注入模具中,然后冷却成型,最终得到所需的产品。
然而,在注塑过程中,可能会出现一些缺陷,如气泡、短射、毛刺等,这些缺陷会降低产品质量,影响生产效率。
因此,及时发现并解决注塑缺陷是非常重要的。
首先,气泡是注塑中常见的缺陷之一、气泡通常由以下原因引起:塑料材料中含有水分、注塑机压力不稳定、模具排气不畅等。
为解决气泡缺陷,可以采取以下措施:在使用塑料材料之前对其进行干燥处理,确保材料中不含水分;调整注塑机的压力和速度,保持稳定的注塑过程;对模具进行排气孔设计,确保顺畅排气。
其次,短射是另一种常见的注塑缺陷。
短射通常是由于塑料材料流动性不好、充型不足或注塑机压力不足等原因引起的。
为解决短射问题,可以采取以下措施:选用流动性好的塑料材料,例如增加流动助剂;优化模具的设计,确保充型顺畅;调整注塑机的压力和速度,保证充型充分。
此外,毛刺也是一种常见的注塑缺陷。
毛刺通常是由于模具接缝不严、射出速度过快、注塑机压力过高等原因引起的。
为解决毛刺问题,可以采取以下措施:检查和调整模具接缝,确保接缝紧密;调整射出速度和注塑机压力,控制流动状态,减少毛刺的产生。
此外,还可能出现其他一些注塑缺陷,如烧焦、变色等。
对于这些缺陷,可以通过调整注塑工艺参数、改进模具设计、使用优质的塑料材料等方法加以解决。
总之,注塑缺陷的解决需要综合考虑塑料材料的选择、注塑机的调整以及模具设计等因素。
通过合理的工艺控制和改进,可以有效降低注塑缺陷的发生,提高产品质量和生产效率。
同时,及时发现和解决注塑缺陷也需要经验丰富的操作人员进行实时监控和调整。
注塑件常见缺陷分析

注塑件常见缺陷分析1.毛边:项目原因分析及解决方式1)射出机合模力不足,或单向受力填充时射出压力大于合模力,造成溢胶调整射出条件2)射出压力,射出量太大过分饱和填充调整射出条件3)模具合模不紧密,或有杂物模具制造偏差间隙太大重新合模4)模具分模面有下陷或塌角异物压制或磨损补焊或降面5)滑块或斜梢未完全回位顶出系统卡死,回不到底,压异物实配活动部位,清除异物,更换弹簧6)塑胶温度过高调机不当降低加热温度至合适温度7)模板变形弯曲模具强度不够;超过使用寿命校正,研磨,更换模板2.缩水:项目原因分析及解决方式1)射出压力不足,产品填充不足调机不当调整射出条件2)产品肉厚不均设计不当,内应力产生尽量按设计原则更改设计3)产品肉太厚设计不当,难于泠却,则更改设计,辅助射出成型4)模具泠却不均,模具水路分布不均,水路调节不均或接错,则更改设计,按水路图运水3.气泡项目原因分析及解决方式1)原料含水份,溶剂或易挥发物塑胶未充分干燥烘干充分2)塑料温度太高或变热时间太长,已降聚或分解调机不当降温,保温3)注射压力太小调机不当适当加压4)注射柱塞退回太早调机不当保压5)模具温度太低塑胶温度降太快模具加到合适温度6)注射速度太快调机不当温度,速度,压力三要素调整7)在料筒加料端混入空气熔胶中混入空气余料射空,下料均匀4.凹痕项目原因分析及解决方式1)流道浇口太小料流速度太快浇口适当加大2)塑件太厚或厚薄县殊收缩后产品产生内应力更改设计3)浇口位置不适当料流不顺畅移到肉厚适当处4)注射及保压时间太短调机不当调整射出条件5)加料量不够调机不当调整射出条件6)料筒温度太高调机不当调整射出条件7)注射压力太小调机不当调整射出条件8)注射速度太慢调机不当调整射出条件9)模面受损外力受伤修模整理5.溶接痕项目原因分析及解决方式1)塑料温度太低调机不当调整射出条件2)浇口太多模具设计不当取消部分浇口,或移位3)脱模剂过量作业不当加强模具抛光,尽量不用脱模剂4)注射速度太慢调机不当调整射出条件5)模具温度太低调机不当模具加温至适当温度6)注射压力太小调机不当适当加压7)模具排气不良模具加工不良在适当位置加开排气槽6.脱皮分层项目原因分析及解决方式1)不同塑料混杂来料不良用料纯正2)同一塑料不同级别查相混来料不良杜绝混料3)塑化不均调机不当螺竿转速,温度调整4)混入异物来料不良用料纯正7.表面波绞项目原因分析及解决方式1)料筒温度太低。
注塑成型件的缺陷和解决方法

成型件的缺陷和解决方法1引言新制成的注射模都是需要进行试模的,用以检验模具是否是合格?但是,判断模具合格的因素很多。
有产品结构设计和造型的因素;有模具设计和制造的因素;有塑件材料的因素;有机床设备选择的因素;有成型工艺参数选择的因素;还有塑件材料前、后处理的因素。
若要在诸多的因素中找准影响试模问题件的缺陷,通过问题件外表面和内部成型痕迹的辩别和分析,才能找到缺陷所产生真正的原因。
最后可以够找到整治的措施,缺陷便可以迎刃而解。
因为,塑件在成形的过程中所造成缺陷的因素,总是会塑件上遗留下相应的痕迹。
这些成型痕迹就是我们分析和解决问题件缺陷的最好依据。
2 案例一:根据成型件使用状况和痕迹来确定塑料的材料及填充料的成份2.1 成型件的资料成型件的名称与组成:转换开关组件,由大件1和小件2粘接成一体,大件1上安装有三个嵌件3,如图(1)所示。
该产品是某生产流水线上机械手上的转换开关,与气源相通,工作压力为3个大气压,需要完成两个26°角的转向运动。
是国产化出口类型的产品,国产化后还须与进口件能够具有进行互换的性能。
2.2 成型件的技术要求大件有1-φ14H8 mm、3-φ6G7 mm和3-φ4H8 mm的共七个孔,小件有1-φ14H8 mm 和3-φ6G7 mm 四个孔。
孔的精度高,锥度和椭圆度均不能大于0.01 mm ,否则转换开关易产生漏气而不能保持3个大气压,机械手便无法正常工作。
大小两件粘接后七孔应保持同轴度的一致,接缝处不能漏气,粘接面间的三个φ1.8 mm的通气孔不能有串气和堵气现象,并且具有一定的强度。
制品表面为亚光,光滑而细腻。
2.3 成型件的材质情况因不清楚进口件的材质,厂家先采用了聚四氟乙烯进行试模,出现了很多的问题。
2.4 问题件的状况聚四氟乙烯,收缩率为:3.1~7.7%。
缩痕大而多,翘曲和变形严重,粘接面的不平度超过0.4 mm ,两件贴合后缝隙达0.7~0.8mm,七个孔的椭圆度和锥度也很大,完全不能满足使用要求。
- 1、下载文档前请自行甄别文档内容的完整性,平台不提供额外的编辑、内容补充、找答案等附加服务。
- 2、"仅部分预览"的文档,不可在线预览部分如存在完整性等问题,可反馈申请退款(可完整预览的文档不适用该条件!)。
- 3、如文档侵犯您的权益,请联系客服反馈,我们会尽快为您处理(人工客服工作时间:9:00-18:30)。
文件编号QR/THSY-751/05 发布实施2014/5/8
注塑成型工艺缺陷分析解决方案
版本A/0 页次
1.产品跑披风
分析:刚开机,温度低,模温越做越高。
解决方案:降低温度,模温,压力,速度及保压时间。
2.产品缺料
分析:射出位置不够,压力及速度过低,模温低,射出时间不足。
解决方案:提高料管温度,加大注塑压力及速度时间,提升模温,调整射出位置。
3.产品脆裂
分析:使用水口和二次料过多,造成产品易脆裂,料在料管内停留时间过长,造成胶料老化,使产品易脆裂。
解决方案:增加新料比例,减少水口料回收使用次数,一般不能超过三次,避免原料在料管内长时间停留。
4.产品缺胶,水口边缩水
分析:模具排气不良,射胶速度慢,保压压力和时间不够。
解决方案:增大模具排气,适当提高射胶速度,增加保压压力和时间。
5.产品有内应力,产品爆裂
分析:由于产品内残存应力,放置一段时间后由于应力的作用,产品爆裂。
解决方案:提高注塑时的模具温度,降低射出压力和保压时间。
编制:审核:会签:批准:
注塑成型工艺缺陷分析解决方案
文件编号QR/THSY-751/05 发布实施2014/5/8 版本A/0 页次
6.产品色纹,水波纹
分析:背压低,注塑压力小,速度慢,温度低。
解决方案:适当增加机台背压,提高注塑压力及速度,提高模具温度和料管温度。
编制:审核:会签:批准:。