高速线材在轧制过程中产生堆钢的原因及处理
高速线材在轧制过程中产生堆钢问题的分析及处理
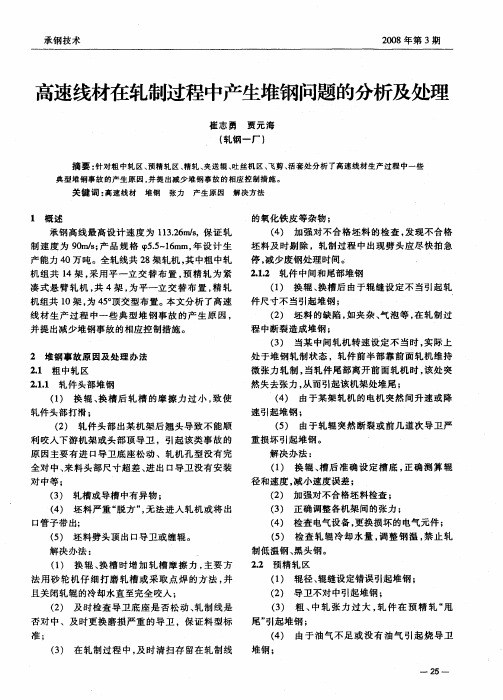
() 辊径、 1 辊缝设 定 错误 引起 堆 钢 ; () 导 卫不 对 中引起 堆钢 ; 2 () 粗 、 轧张力 过大 , 件 在预 精轧 “ 3 中 轧 甩
尾” 引起 堆 钢 ;
( ) 由 于 油 气 不 足 或 没 有 油 气 引 起 烧 导 卫 4 堆钢 ;
一
() 换 辊 、 1 换槽 后 由 于辊 缝设 定 不 当 引起 轧
件 尺 寸不 当引起 堆钢 ;
机 组共 1 0架 , 4 。 为 5顶交 型 布置 。本 文 分析 了高 速
线 材 生 产 过 程 中一 些 典 型 堆 钢 事 故 的产 生 原 因 , 并 提 出减 少堆 钢事 故 的相应 控 制措 施 。
解决办 法 :
() 由于 吐丝 管 磨损 严 重 , 丝 管将 要 磨穿 2 吐
时 表现 为 吐丝 线环 混乱 不 规则 ,严 重 时钢 的 头部 卡在 吐丝 管 中 ;
() 换 辊 时准确 设 定 辊 缝 , 确测 算 辊 径 和 1 正
速度 2 认 真检 查调 整 , 导 卫对 中 ; ) 使 3 规范料 型 , ) 消除粗 中轧张 力过 大现象 ;
速引 起堆 钢 ;
21 粗 中轧 区 . 211 轧 件头 部堆 钢 .. ( ) 换 辊 、 槽 后 轧 槽 的 摩 擦 力 过 小 , 使 1 换 致 轧件 头部 打滑 ;
( ) 轧 件 头部 出某 机 架 后 翘 头 导致 不 能 顺 2
利 咬入 下 游机 架 或 头 部顶 导 卫 ,引 起该 类 事 故 的 原 因 主要 有 进 口导 卫 底 座松 动 、轧 机 孔 型没 有 完 全对 中 、 料 头 部 尺寸 超 差 、 出 口导 卫 没有 安 装 来 进 对 中等 ; ( ) 轧 槽或 导槽 中有 异 物 ; 3
高速线材在轧制过程中堆钢的原因分析
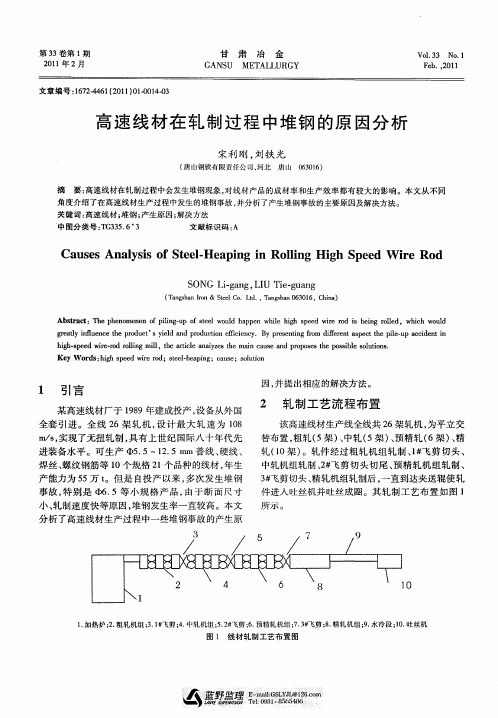
() 1由于 紧凑式 轧 机 生 产 时 钢料 量 取 困 难 , 出 易
现上 道次 轧件 尺寸 过大 , 以致 轧件进 入 下一道 次时 , 挤在 人 口夹板 内造 成堆 钢 。
3 3 精轧机 机 组堆钢 .
粗 轧机 组 由一 架二 辊 闭 口开 坯机 和一组 紧凑 式 轧 机组成 。粗 轧机 组 平 时 堆 钢 次数 较 少 , 生 原 因 产 主 要为 :
精 轧 机 组 为 德 马 克 侧 交 1 。7 。 轧 机 , 生 5/ 5 型 产 堆钢 的原 因可能是 : () 粘钢 。 1导卫
图 1 线材 轧 制 工 艺 布 置 图
萋舞
第 1 期
宋利刚, 高速线材在轧制过程中堆钢的原因分析 等:
l 5
3 产 生 堆钢 原 因及 解 决方 法
3I . 粗轧 机 组堆钢
( 上下轧辊磨损不均匀可换轧槽或换辊 , 动 5 ) 传 部件 问 隙大可更 换磨损 严重 的传 动 部件 。侧 弯可 以 调整上一道的人 口导板位置与轧制线重合 。
产能 力 为 5 5万 t 。但 是 自投 产 以来 , 多次 发 生堆 钢 事故 , 别 是 6 5等 小 规 格 产 品 , 特 . 由于 断 面 尺 寸
小、 轧制速度快等原因, 堆钢发生率一直较高。本文
分析 了高速线 材生 产过 程 中一些堆 钢事 故 的产 生原
0
1加热炉 ;. . 2 粗轧机组 ;.} 3 1f 飞剪 ;. 4 中轧机组 ;.} 52} 飞剪;. 6 预精轧机组 ; .} 7 3f 飞剪 ;. 轧机组 ;. 8精 9 水冷段 ;O 吐丝机 l.
宋利 刚 , 刘铁 光
( 山 钢铁 有 限责 任 公 司 , 北 唐 河 唐 山 031) 6 06
棒线材轧制常见堆钢事故及处理措施

棒线材轧制常见堆钢事故及处理措施一、粗中轧区事故原因分析及对策1、轧件咬入后机架间堆钢故障原因:(1)轧制速度、轧辊直径设定不正确;换辊(槽)后张力设定过小。
(2)钢温波动太大。
(3)轧辊突然断裂。
(4)由于电控系统原因引起某架轧机的电机突然升速或降速。
处理措施:(1)准确设定轧制速度、辊径和张力。
(2)保温待轧,通知加热炉看火工。
(3)更换断辊。
(4)检查电气系统。
2、轧件头部在机架咬入时堆钢故障原因:(1)轧件尺寸不符合要求。
(2)轧槽中有异物或打滑。
(3)导卫安装不良、磨损严重或导卫中夹有氧化铁皮等异物。
(4)坯料内部存在分层、夹杂或冶废等缺陷引起的轧件“劈头”。
(5)上、下辊径不同、磨损不均匀或不同步造成的轧件头部弯曲。
(6)头部钢温过低造成的咬入困难或头部开裂。
(7)轧机机架刚性不好,轧制过程中存在跑偏现象。
(8)坯料“脱方”严重。
(9)轧件出粗轧机架后翘头导致不能顺利咬入下架次或头部冲导卫,简单来说就是翘头。
处理措施:(1)对轧机辊缝作适当调整。
(2)检查、清理或打磨轧槽。
(3)检查、清理、调整或更换导卫。
(4)认真检查坯料。
(5)检查传动部件间隙或更换轧辊。
(6)改善出钢条件。
(7)对轧机机架进行加固;检查锁紧缸的工作状态。
(8)杜绝不合格钢坯入炉。
(9)认真检查前一架次进口导卫是否松动,导卫松动使轧件咬入箱型孔后受到进口导卫的压力,使轧件下部受压较大,导致下部延伸变大而造成翘头,最终未能顺利咬入轧机而堆钢。
3、轧件卡在机架内造成堆钢故障原因:(1)由于钢温过低或轧制速度过高而引起电机过载跳闸。
(2)发生设备或安全事故时紧急停车。
处理措施:应根据具体情况分析处理。
二、预精轧区事故原因分析及对策1、机架间堆钢故障原因:(1)辊径、辊缝设定错误。
(2)导卫安装不准确,导卫被堵塞或被冲掉。
(3)粗、中轧张力过大,轧件在预精轧“甩尾”。
(4)轧机或辊箱轴承烧,导致次架次料型变化。
(5)压下装置自锁性能坏,在轧制时因振动,料型产生变化。
高速线材常见事故处理
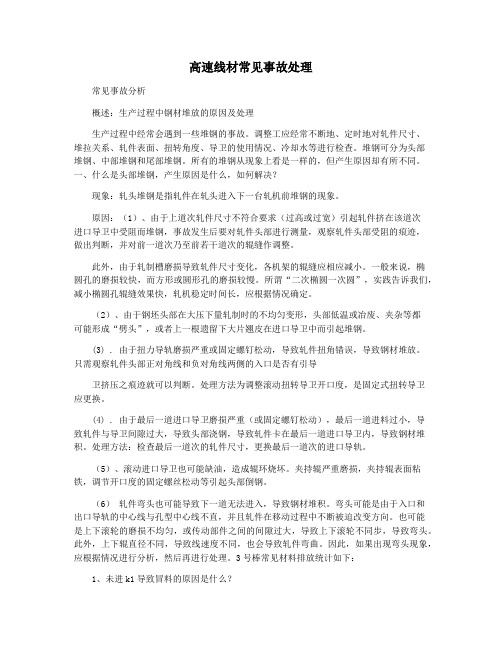
高速线材常见事故处理常见事故分析概述:生产过程中钢材堆放的原因及处理生产过程中经常会遇到一些堆钢的事故。
调整工应经常不断地、定时地对轧件尺寸、堆拉关系、轧件表面、扭转角度、导卫的使用情况、冷却水等进行检查。
堆钢可分为头部堆钢、中部堆钢和尾部堆钢。
所有的堆钢从现象上看是一样的,但产生原因却有所不同。
一、什么是头部堆钢,产生原因是什么,如何解决?现象:轧头堆钢是指轧件在轧头进入下一台轧机前堆钢的现象。
原因:(1)、由于上道次轧件尺寸不符合要求(过高或过宽)引起轧件挤在该道次进口导卫中受阻而堆钢,事故发生后要对轧件头部进行测量,观察轧件头部受阻的痕迹,做出判断,并对前一道次乃至前若干道次的辊缝作调整。
此外,由于轧制槽磨损导致轧件尺寸变化,各机架的辊缝应相应减小。
一般来说,椭圆孔的磨损较快,而方形或圆形孔的磨损较慢。
所谓“二次椭圆一次圆”,实践告诉我们,减小椭圆孔辊缝效果快,轧机稳定时间长,应根据情况确定。
(2)、由于钢坯头部在大压下量轧制时的不均匀变形,头部低温或冶废、夹杂等都可能形成“劈头”,或者上一根遗留下大片翘皮在进口导卫中而引起堆钢。
(3) . 由于扭力导轨磨损严重或固定螺钉松动,导致轧件扭角错误,导致钢材堆放。
只需观察轧件头部正对角线和负对角线两侧的入口是否有引导卫挤压之痕迹就可以判断。
处理方法为调整滚动扭转导卫开口度,是固定式扭转导卫应更换。
(4) . 由于最后一道进口导卫磨损严重(或固定螺钉松动),最后一道进料过小,导致轧件与导卫间隙过大,导致头部浇钢,导致轧件卡在最后一道进口导卫内,导致钢材堆积。
处理方法:检查最后一道次的轧件尺寸,更换最后一道次的进口导轨。
(5)、滚动进口导卫也可能缺油,造成辊环烧坏。
夹持辊严重磨损,夹持辊表面粘铁,调节开口度的固定螺丝松动等引起头部倒钢。
(6)轧件弯头也可能导致下一道无法进入,导致钢材堆积。
弯头可能是由于入口和出口导轨的中心线与孔型中心线不直,并且轧件在移动过程中不断被迫改变方向。
新高线精轧机组常见堆钢事故的原因分析及预防

新高线精轧机组常见堆钢事故的原因分析及预防推荐单位:股份轧钢厂棒线分厂所在岗位:轧钢工徒弟姓名:指导老师:新高线精轧机组常见堆钢事故的原因分析及预防股份轧钢厂棒线分厂摘要:高速线材精轧机组发生的堆钢事故按照轧件的轧制过程分,可分为头部堆钢、中部堆钢及尾部堆钢。
而按照事故原因分则可细分为很多类别。
本文就是对新高线精轧机组曾出现过的堆钢事故进行分析和总结,找出产生堆钢事故的原因,并探讨预防措施,以期对实际生产有一定的指导作用,能够降低生产成本,提高作业率。
关键词:高速线材精轧机;堆钢;预防一、前言宝钢集团新疆八一钢铁有限公司股份轧钢厂棒线分厂新高线精轧机组采用的是摩根式顶角交替45°悬臂式轧机。
其中,前5架为φ230辊大辊径轧机,后5架为φ170辊小辊径轧机。
精轧机组作为高速线材轧制的最后一道工序,对于成品的尺寸及质量有着至关重要的作用。
同时,精轧机组也是轧线事故发生频率最高的机组,因此,研究精轧机组的事故原因并加以预防,对于降低生产成本,提高作业率有着很强的积极意义。
二、事故分析及预防i.3#飞剪余条堆钢正常轧制过程中,造成3#飞剪处余条的原因主要有两个:一是钢温不均匀;二是粗中轧堆钢轧制,使得红条中间大,头尾小。
当红条轧至中间时,可能会造成余条,降速不及时会造成堆钢。
预防方法:1. 钢温尽量加热均匀,避免同一支钢坯各段出现较大的温差;2. 合理调节各机架的张力。
粗中轧最好处于微张力轧制状态,这样既能保证成品尺寸,也能防止余条堆钢,同时,由于新高线的活套未启用,因此,18#要处于拉钢轧制状态。
ii.辊环爆裂堆钢辊环爆裂的原因主要有两个:1. 辊环材质不合格;2. 辊环冷却不到位。
预防措施:点检轧机时检查各架轧机的冷却水管接头是否完好,冷却水管是否正对轧槽,冷却水管是否固定牢。
iii.锥套碎堆钢锥套碎裂的原因主要有三个:1. 锥套未安装到位;2. 来料尺寸过大;3. 辊缝设置过小。
其中,后两点都会使得锥套的受力过大而使锥套碎裂。
高速线材生产堆钢问题浅析
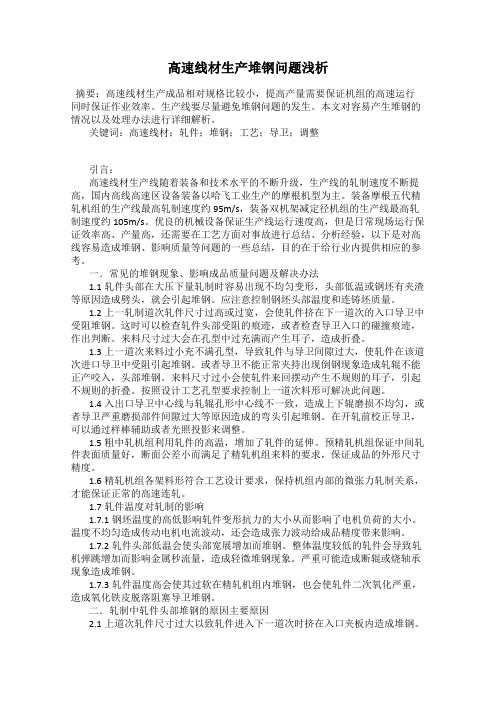
高速线材生产堆钢问题浅析摘要:高速线材生产成品相对规格比较小,提高产量需要保证机组的高速运行同时保证作业效率。
生产线要尽量避免堆钢问题的发生。
本文对容易产生堆钢的情况以及处理办法进行详细解析。
关键词:高速线材;轧件;堆钢;工艺;导卫;调整引言:高速线材生产线随着装备和技术水平的不断升级,生产线的轧制速度不断提高,国内高线高速区设备装备以哈飞工业生产的摩根机型为主。
装备摩根五代精轧机组的生产线最高轧制速度约95m/s,装备双机架减定径机组的生产线最高轧制速度约105m/s。
优良的机械设备保证生产线运行速度高,但是日常现场运行保证效率高、产量高,还需要在工艺方面对事故进行总结、分析经验,以下是对高线容易造成堆钢、影响质量等问题的一些总结,目的在于给行业内提供相应的参考。
一.常见的堆钢现象、影响成品质量问题及解决办法1.1轧件头部在大压下量轧制时容易出现不均匀变形,头部低温或钢坯有夹渣等原因造成劈头,就会引起堆钢。
应注意控制钢坯头部温度和连铸坯质量。
1.2上一轧制道次轧件尺寸过高或过宽,会使轧件挤在下一道次的入口导卫中受阻堆钢。
这时可以检查轧件头部受阻的痕迹,或者检查导卫入口的碰撞痕迹,作出判断。
来料尺寸过大会在孔型中过充满而产生耳子,造成折叠。
1.3上一道次来料过小充不满孔型,导致轧件与导卫间隙过大,使轧件在该道次进口导卫中受阻引起堆钢。
或者导卫不能正常夹持出现倒钢现象造成轧辊不能正产咬入,头部堆钢。
来料尺寸过小会使轧件来回摆动产生不规则的耳子,引起不规则的折叠。
按照设计工艺孔型要求控制上一道次料形可解决此问题。
1.4入出口导卫中心线与轧辊孔形中心线不一致,造成上下辊磨损不均匀,或者导卫严重磨损部件间隙过大等原因造成的弯头引起堆钢。
在开轧前校正导卫,可以通过样棒辅助或者光照投影来调整。
1.5粗中轧机组利用轧件的高温,增加了轧件的延伸。
预精轧机组保证中间轧件表面质量好,断面公差小而满足了精轧机组来料的要求,保证成品的外形尺寸精度。
轧钢棒材堆钢

线材在粗、中轧时会出现堆钢现象,分为轧件头部、中部和尾部堆钢,具体原因及解决方法如下:
1轧件头部堆钢
1)换辊、换槽后轧槽的摩擦力过小,致使轧件头部打滑;
2)轧件头部出机架后翘头导致不能顺利咬入下游机架或头部顶导位;
3)轧槽或导槽有异物;
4)坯料严重脱方,无法进入轧机或将出口管子带出;
5)坯料劈头顶出导卫或缠辊。
解决办法:
1)换辊、换槽时增加轧槽摩擦力,用砂轮机打磨轧槽或采用点焊方法,并且关闭轧辊的冷却水直至完全咬入;
2)及时检查导卫底座是否松动,轧制线是否对中,及时更换旧的导卫。
3)轧制过程,及时清理氧化铁皮;
4)轧制过程,及时清除不合格坯料,出现劈头,应尽快拍急停,减少废钢处理时间。
2轧件中部和尾部堆钢
1)由于辊缝设定不当引起轧件尺寸不当造成堆钢;
2)坯料的缺陷,如夹杂、气泡等,在轧制过程中断裂造成堆钢;
3)轧机转速设计不当,处于堆钢轧制状态,当轧件前半部靠前面轧机维持微张力轧制,当轧件尾部离开前面轧机时,该处突然失去张力,从而引起该机架处堆尾;
4)机架电机突然升速或降速引起堆钢;
5)轧辊突然断裂或前几道次导卫严重损坏引起堆钢。
解决方法:
1)换辊、槽后,准确设定槽底,正确测算辊径和速度,减小速度误差;
2)加强对不合格坯料检查;
3)正确调整各机架间的张力;
4)检查电气设备,更换损坏的电气元件;
5)检查轧辊冷却水量,调整钢温,禁止轧制低温钢、黑头钢。
高速线材轧机轧制产生堆钢问题的分析
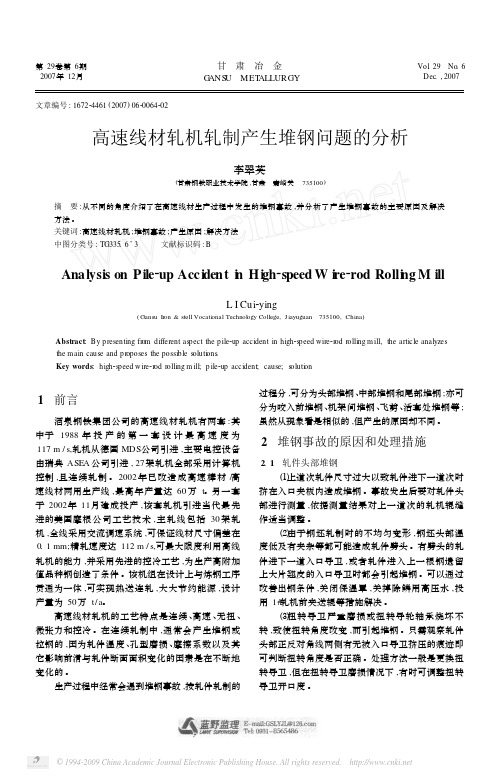
第29卷第6期2007年12月甘 肃 冶 金G ANS U MET ALLURGYVol.29 No.6Dec.,2007文章编号:167224461(2007)0620064202高速线材轧机轧制产生堆钢问题的分析李翠英(甘肃钢铁职业技术学院,甘肃 嘉峪关 735100)摘 要:从不同的角度介绍了在高速线材生产过程中发生的堆钢事故,并分析了产生堆钢事故的主要原因及解决方法。
关键词:高速线材轧机;堆钢事故;产生原因;解决方法中图分类号:TG335.6+3 文献标识码:BAnalysis on Pile2up Acci dent i n Hi gh2speed W i re2rod Rolli n g M illL I Cui2ying(Gansu Ir on&stell Vocati onal Technol ogy College,J iayuguan 735100,China)Abstract:By p resenting fr om different as pect the p ile2up accident in high2s peed wire2r od r olling m ill,the article analyzes the main cause and p r oposes the possible s oluti ons.Key words:high2s peed wire2r od r olling m ill;p ile2up accident;cause;s oluti on1 前言酒泉钢铁集团公司的高速线材轧机有两套:其中于1988年投产的第一套设计最高速度为117m/s,轧机从德国MDS公司引进,主要电控设备由瑞典ASEA公司引进,27架轧机全部采用计算机控制,且连续轧制。
2002年已改造成高速棒材/高速线材两用生产线,最高年产量达60万t。
另一套于2002年11月建成投产,该套轧机引进当代最先进的美国摩根公司工艺技术,主轧线包括30架轧机,全线采用交流调速系统,可保证线材尺寸偏差在0.1mm;精轧速度达112m/s,可最大限度利用高线轧机的能力,并采用先进的控冷工艺,为生产高附加值品种钢创造了条件。
- 1、下载文档前请自行甄别文档内容的完整性,平台不提供额外的编辑、内容补充、找答案等附加服务。
- 2、"仅部分预览"的文档,不可在线预览部分如存在完整性等问题,可反馈申请退款(可完整预览的文档不适用该条件!)。
- 3、如文档侵犯您的权益,请联系客服反馈,我们会尽快为您处理(人工客服工作时间:9:00-18:30)。
高速线材堆钢的原因分析及处理
摘要:高速线材在轧制过程中有时会产生堆钢现象,本文介绍了一些常见的堆钢事故,并结合职工操作、工艺、设备等方面对这些堆钢事故产生的原因进行分析和总结,同时针对存在的问题提出了相应的措施。
关键词:高速线材;堆钢;产生原因;措施
1前言
首钢股份公司第一线材厂生产线设备仿摩根五代轧机设计,国内厂家生产,该生产线最大稳定轧制速度为88m/s。
全线由28架轧机组成,粗、中轧共14架,预精轧4架,为平立交替布置,精轧机10架为顶交45°布置,精轧机后无减定径机组,直接是夹送辊及吐丝机。
产品规格φ5.5—φ16mm,规格跨度较大,同时生产的品种较广。
从目前的生产状况来看,φ6.5mm(包含6.5mm)以下的小规格线材产品因轧制速度快,断面尺寸小等原因,其堆钢事故率远超于其他规格。
本文按照不同轧区分类,介绍了其产生的原因及解决办法。
2导致堆钢的原因分析及措施
2.1 粗中轧区域(1-14架)
2.1.1 轧件不能顺利咬入下一架次造成堆钢
造成此类事故的原因主要有:①轧件前头从上一架次出来后翘头;②上一支的后尾倒钢将出口导卫拉高;③进口导卫开口度调整不合适;④导卫与孔型不对中(轧制线不正);⑤槽孔打滑;⑥轧件尺寸不符合工艺要求;⑦因坯料原因造成的前头劈裂。
处理措施:①针对轧件翘头需要检查上下辊径及磨损情况、传动部件连接处的间隙、进出口导卫高低的一致性;②合理的调整进口导卫开口度及与轧辊之间的距离;③新换槽孔辊缝设定过小,对轧机辊缝做适当调整或重新打磨槽孔;④对轧机辊缝做适当调整;⑤认真检查坯料,加长1#剪剪切前头长度。
2.1.2轧件咬入后机架之间堆钢
主要原因:①人为原因造成轧制速度、轧辊直径等参数设定不正确;②换辊或槽孔后堆拉关系调整不合适;③钢坯温度波动太大;④因电控原因造成的某架轧机突然升速或降速;⑤主控台操作工在调整轧机转速时调错转数或架次;
处理措施:①正确的设定轧制速度、辊径、合理的调整轧机间堆拉关系。
做好两人之间的确认工作;②通知加热炉调火工,同时保温待轧;③电气专业检查,倒备用柜。
2.1.3轧件后尾堆钢
主要原因是由于在上游机架处,轧件拉钢造成后尾脱离上游机架时,在下游机架堆钢。
处理措施:合理的调整堆拉关系及轧机尺寸。
2.2 预精轧区域(15-18架)
2.2.1 机架之间堆钢
主要原因:①辊缝、辊径、轧速等参数设定错误;②导卫安装不合适;③导卫打铁;④粗中轧拉钢造成轧件在预精轧甩后尾;⑤因电控原因造成某架轧机转速异常。
处理措施:①重新核对设定参数;②检查更换或调整进出口导卫;③调整预精轧内活套高度及加强巡检;④合理的调整连轧机的堆拉关系;⑤电气专业检查同时倒备用柜。
2.2.2预精轧某一架次跳车
主要原因:①预精轧冷却水压及润滑系统故障;②电机跳闸;③事故检测系统作用。
处理措施:①检查冷却水压力、机旁控制水阀;②设备专业检查润滑系统;③检查预精轧鱼线吊坠是否系紧,同时检查其接近开关。
2.3高速区域(精轧机至吐丝机)
2.3.1精轧机内机架间堆钢
主要原因:①导卫轮不转或轴承烧;②轧件劈头;③导卫或辊环装错;④辊缝设定不当或来料尺寸不合适;⑤辊环碎;⑥鱼线断导致轧线自动碎断。
处理措施:①更换导卫,同时加强导卫安装的正确性;②加强坯料检查及加长切头长度;③重新核对及调整辊缝;④更换辊环,同时检查冷却水管。
⑤检查鱼线吊坠处的接近开关、检查精轧机内导卫处是否有废钢,若有则说明是前一支后尾在精轧机内堆钢,重新设定精轧机内辊缝。
2.3.2精轧机废钢箱处堆钢
分为两种情况,一是未吐丝而堆钢,二是吐丝若干圈后堆钢。
主要原因有:①水冷段的冷却水不能正常关闭或开启过早;②水冷段内有异物;③水冷导槽安装错位;④精轧机后首段水冷箱水阀开启过大或水压过大;⑤精轧机、夹送辊、吐丝机之间的速度匹配不好;
处理措施:①电控专业检查水阀控制系统并手动试水,主控台调整开启延时;②检查水冷喷嘴及导槽安装是否正确,有无松动,同时检查其中是否有异物,并用一根φ13mm的圆钢穿水冷段;
③检查核对三者之间的速度匹配;④可将水冷喷嘴及导槽的使用规格放大,如将φ12mm更换为φ16mm规格。
2.3.3夹送辊吐丝机处的堆钢
主要原因:①夹送辊进出口导管安装不正确、磨损严重或导管内有异物;②夹送辊前检测信号失灵,使夹送辊不能按时张开/闭合;③吐丝管磨损严重;④夹尾延时设定过短,造成丢后尾;⑤精轧机、吐丝机之间的速度不匹配;⑥线材内部质量缺陷(冶炼缺陷)或轧制缺陷(严重折叠或耳子)造成堆钢。
处理措施:①检查、更换进出口导管;②电气专业检查检测信号;③更换吐丝管;④将夹尾延时加长;⑤合理设定精轧机、吐丝机之间的速度匹配;
2.4飞剪处堆钢
主要原因:①飞剪剪切速度与上游轧机速度不匹配,切前头后有弯造成堆钢;②飞剪切后尾长度过短,造成后尾未完全切断,带入下一道轧机;③剪刃、转辙器磨损严重造成剪切位置不正确;
④中途飞剪误动作,剪切失控。
处理措施:①重新设定飞剪的超前系数;②调整切头尾长度;③检查剪刃和飞剪的前头导槽;
④检查光电管、热检信号。
2.5活套处堆钢
主要原因:①活套延时设定不正确;②活套高度设定不合适;③活套的起套辊、导向辊或导向板磨损严重;④活套扫描器故障;⑤前面的热检信号被挡;⑥水雾过大或阳光照射影响检查效果。
处理措施:①重新设定或调整参数;②更换工艺备件,或对导向板补焊;③更换活套扫描器并重新调整零位;④在水雾大处加吹雾风机,针对阳光照射在合适角度加遮挡板。
3 结束语
在生产过程中,发生堆钢事故时,由于受到时间及指标的限制,需要快速而准确的找到原因,这就需要对发生的事故进行综合考虑,多方面寻找原因,这样才能缩短处理时间避免重复性事故发生。
更要求现场操作人员在日常生产中不断地、定时地对轧件尺寸、轧机堆拉关系、导卫情况等方面进行检查,这样才能更好的减少事故发生的频率。
作者简介:史昌,助理工程师,出生于1983年,2006年毕业于西安建筑科技大学(原西安冶金建筑学院)材料成型与控制工程专业,北京科技大学材料工程领域在读工程硕士。
2006年7月到北京首钢股份公司第一线材厂工作,目前为高速线材车间工艺主管师。