国内外高速线材轧制技术发展
国内外线材生产的兴起与发展

国内外线材⽣产的兴起与发展⽂献综述:⾼速线材⽣产⼯艺综述1 概述1.1 国内外线材⽣产的兴起与发展线材制品的品种与质量,不仅决定于其本⾝的⽣产⼯艺技术与装备⽔平,⽽且在很⼤程度上更有赖于其原料——线材的冶炼与轧制技术。
也就是说,线材品种质量的提⾼,将⼤⼤促进线材制品⾏业的发展与进步,否则线材制品⾏业的发展将受到制约,甚⾄处于落后状态。
这是100多年来线材制品⾏业发展历史所证实的.因此线材与其制品的关系是密不可分的。
线材⼀般是指直径为5——16mm的热轧圆钢或相当该断⾯的异型钢,因以盘卷状态交货,统称为线材或盘条。
国外线材规格已扩⼤到约6.50mm。
常见线材多为圆断⾯,异型断⾯线材有椭圆形、⽅形及螺纹形等,但⽣产数都很少。
线材在国民经济中的作⽤与地位是⾮常重要的,⾸先,线材产量占钢材总产量的⽐例很⼤、⼀般国家线树产量占钢材总产量的8%——10%,⽽我国却占20%以上;其次,线材⽤途⼗⼴泛,除直接⽤作建筑钢材外,线材的深加⼯产品⽤途更为⼴泛和重要。
例如各类商品钢丝及专⽤弹簧钢丝、焊丝、冷缴钢丝、镀锌钢丝、通讯线、轮胎钢丝及钢帘线、⾼强度钢丝及钢纱线舶承钢丝、模具钢丝、不锈钢丝、各种钢丝绳、钢钉、标谁件等等,可以说遍布国民经济各个部门,是不可或缺的重要品种。
国外先进⼯业国家线材加⼯⽐在70%左右,我国为30%左右。
线材⽣产的兴起与发展是随着科技进步、国民经济的发展⽽发展起来的。
线材轧机的开发与创新是线材⽣产发展的⾸要条件。
据记载,世界上第⼀台线材轧机在16世纪已经问世.当时是⽤锻坯轧制线材⽽⽐较正规的线材轧机在18世纪中期才出现,由粗轧及精轧两列横列式轧机组成。
因为采⽤反围盘及⼈⼯喂钢轧制,其轧速度超过8m/s,同时受头尾温差⼤的影响,线材存在着尺⼨精度差、盘重⼩、性能不稳定等致命缺点,限制了横列式轧机的发展。
为了保证产品质量并提⾼产量,同时也为了降低⽣产成本,必须提⾼轧制速度,所以20世纪初开发了半连续式轧机。
国际轧制技术发展
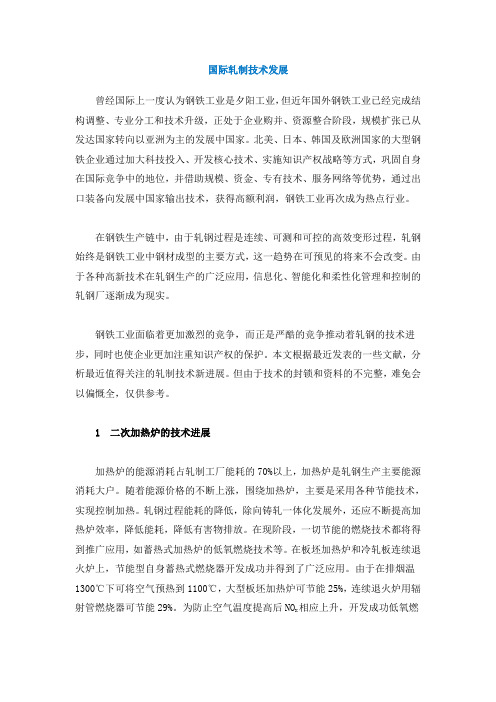
国际轧制技术发展曾经国际上一度认为钢铁工业是夕阳工业,但近年国外钢铁工业已经完成结构调整、专业分工和技术升级,正处于企业购并、资源整合阶段,规模扩张已从发达国家转向以亚洲为主的发展中国家。
北美、日本、韩国及欧洲国家的大型钢铁企业通过加大科技投入、开发核心技术、实施知识产权战略等方式,巩固自身在国际竞争中的地位,并借助规模、资金、专有技术、服务网络等优势,通过出口装备向发展中国家输出技术,获得高额利润,钢铁工业再次成为热点行业。
在钢铁生产链中,由于轧钢过程是连续、可测和可控的高效变形过程,轧钢始终是钢铁工业中钢材成型的主要方式,这一趋势在可预见的将来不会改变。
由于各种高新技术在轧钢生产的广泛应用,信息化、智能化和柔性化管理和控制的轧钢厂逐渐成为现实。
钢铁工业面临着更加激烈的竞争,而正是严酷的竞争推动着轧钢的技术进步,同时也使企业更加注重知识产权的保护。
本文根据最近发表的一些文献,分析最近值得关注的轧制技术新进展。
但由于技术的封锁和资料的不完整,难免会以偏慨全,仅供参考。
1 二次加热炉的技术进展加热炉的能源消耗占轧制工厂能耗的70%以上,加热炉是轧钢生产主要能源消耗大户。
随着能源价格的不断上涨,围绕加热炉,主要是采用各种节能技术,实现控制加热。
轧钢过程能耗的降低,除向铸轧一体化发展外,还应不断提高加热炉效率,降低能耗,降低有害物排放。
在现阶段,一切节能的燃烧技术都将得到推广应用,如蓄热式加热炉的低氧燃烧技术等。
在板坯加热炉和冷轧板连续退火炉上,节能型自身蓄热式燃烧器开发成功并得到了广泛应用。
由于在排烟温1300℃下可将空气预热到1100℃,大型板坯加热炉可节能25%,连续退火炉用辐射管燃烧器可节能29%。
为防止空气温度提高后NO相应上升,开发成功低氧燃X烧技术,即在空气预热温1150℃下,将氧浓度由15%降到2%后仍可稳定燃烧,NO由750ppm降到40ppm。
X在线数学模型在其中起到关键作用。
加拿大IPSCO汽车公司Alabama分厂自2001年起便致力于卷、板材的生产。
高速线材轧制工艺提升与优化

高速线材轧制工艺提升与优化【摘要】高速线材轧制工艺在现有的工程实践中存在诸多问题,如生产效率低、能耗高等。
为此,本文从优化关键技术、提升工艺方法等方面进行了深入研究和探讨。
针对目前存在的问题,提出了一些改进方案,并对高速线材轧制工艺的发展趋势进行了分析和展望。
结合工艺的应用领域,探讨了其在行业中的重要性和价值。
未来,可以通过进一步提升工艺,加强研究与创新,来实现高速线材轧制工艺的进一步提升和优化。
总结了本文的研究成果,提出了未来研究方向,展望了高速线材轧制工艺的未来发展方向。
【关键词】高速线材轧制工艺、优化、提升、关键技术、方法、发展趋势、应用领域、进一步提升、未来研究方向、总结、研究背景、研究意义、研究方法。
1. 引言1.1 研究背景高速线材轧制是金属加工领域的重要工艺之一,具有广泛的应用前景。
随着社会经济的不断发展,对高速线材的需求量也在不断增加,因此如何提升和优化高速线材轧制工艺显得尤为重要。
在过去的研究中发现,现有的高速线材轧制工艺存在一些问题,如产能低、质量波动大、能耗高等。
这些问题不仅影响了生产效率,还影响了产品质量,降低了企业的竞争力。
有必要对高速线材轧制工艺进行进一步的提升和优化,以适应市场需求的变化。
通过对高速线材轧制工艺进行研究,可以找到关键的技术点,从而实现对工艺的优化。
而研究方法的选择则直接影响着研究成果的可靠性和实用性,因此需要合理选择研究方法,以确保研究的科学性和有效性。
的探讨将有助于更好地理解高速线材轧制工艺的现状及存在的问题,为后续的研究奠定基础。
1.2 研究意义高速线材轧制工艺的优化与提升具有重要的研究意义。
随着社会经济的快速发展,高速线材在建筑、交通、机械制造等领域的应用日益广泛,对高速线材的质量和性能要求也越来越高。
优化和提升高速线材轧制工艺,可以有效改善产品质量,提高生产效率,降低生产成本,提升企业的竞争力。
随着科技的不断进步和创新,高速线材轧制工艺也面临着新的挑战和机遇。
高速线材轧制工艺提升与优化

高速线材轧制工艺提升与优化随着社会发展和科技进步,高速线材轧制工艺必须不断优化和提升,以适应市场需求和环保要求,提高产品质量和生产效率。
本文从工艺改进、设备升级和人才培养三个方面探讨高速线材轧制工艺的提升与优化。
一、工艺改进1、模具优化设计模具是高速线材轧制过程中最重要的组成部分。
优化模具设计可以提高生产效率和产品质量,降低能耗和成本。
在模具设计中,需要考虑材料、几何形状、表面质量和润滑条件等因素,以确保产品达到预期质量要求,并尽可能减少材料浪费和能量消耗。
2、润滑技术改进润滑是高速线材轧制过程中必要的关键技术。
优化润滑技术可以降低摩擦阻力、延长模具寿命、提高产品表面质量和消耗能量。
目前,常用的润滑方式有干润滑、湿润滑和辅助润滑等。
可以根据不同类型的高速线材轧制工艺和产品要求来选择不同的润滑技术,以最大程度地提高生产效率和产品质量。
3、自动化控制自动化技术在高速线材轧制工艺中的应用越来越普遍。
自动化控制可以大大提高工艺稳定性、降低人工误差、节省能耗和减少环境污染。
例如,采用先进的测量和控制系统可以实时监测生产过程中的各个参数,从而调整和优化生产过程。
通过自动化控制,可以更加精确地控制高速线材轧制工艺,提高生产效率和产品质量。
二、设备升级机器设备是高速线材轧制工艺的核心部分。
随着生产工艺的不断发展和变化,机器设备也需要不断升级,以适应新的技术和产品要求。
例如,采用更加先进的设备可以提高生产效率和产品质量。
同时,考虑到环境保护和资源利用的要求,新型设备也应具有更高的能源效率和降低环境污染的能力。
2、生产线改造生产线改造可以提高生产过程的自动化程度,降低生产成本和能耗,提高产品的质量和产量。
例如,可以采用智能化的生产线控制系统,实现生产线上的实时监控和操作,从而快速响应生产过程中的变化,准确控制生产线的各个环节。
此外,合理布置生产线的设备和工艺流程,也可以优化生产过程。
三、人才培养1、培养专业技能高速线材轧制工艺需要高度的专业技能,如机器设备操作、模具更换、润滑技术等。
中国钢铁轧制技术的进步与发展趋势

中国钢铁轧制技术的进步与发展趋势随着我国经济的快速发展,钢铁材料产量的需求呈现出爆发式增长。
为满足市场需求,钢铁轧制技术也在不断发展和进步。
本文将从技术层面探讨我国钢铁轧制技术的进步与发展趋势。
一、高端钢铁材料的需求趋势我国的钢铁产业从存量革命到优质化引领,经历了快速发展。
当前,我国产量已经达到了全球领先地位。
然而,仍然需要满足更高端的需求,例如重要工程和高端用途的钢铁材料。
这些钢铁材料需要较高的机械性能、化学成分和微观组织,才能满足设计和使用要求。
在这种情况下,提高钢铁材料的热加工技术是至关重要的。
因为钢材的热加工过程会改变其物理性能和微观结构。
例如,精确控制钢材的温度和时间可以影响钢材的硬度、强度、韧性和延展性。
所以,钢铁轧制技术的研究和发展变得尤为重要。
我国的钢铁轧制技术从20世纪初开始逐步完善。
最初,轧制主要依赖于人工劳动和手工车间。
20世纪60年代,我国引进外国轧机和轧制技术,开始实施全面改造和技术革新。
此后,新的轧机、轧制好工艺和工具被引入,使得我国的钢铁轧制产量和质量得到了提高。
目前,我国正处于钢铁产业优化升级的时期。
技术创新和成果转化为我国钢铁产业的发展带来了广阔的空间。
作为最具代表性的热加工工艺,钢铁轧制技术的发展已经成为制约或推动我国钢铁产业进一步发展的关键因素之一。
1. 轧制工艺自动控制和模型预测钢铁轧制工艺自动控制和模型预测是未来发展的应用方向之一。
在轧制过程中,自动控制技术可以实现较高精度的温度和厚度控制,提高轧制效率和质量。
预测模型可以辅助操作员及时调整工艺参数、解决工艺失控问题,并且通过基于数据的思考和分析,推动轧制技术的进步。
2. 智能轧机系统智能轧机系统是未来发展的另一个应用方向,在轧制过程中可以监测并控制轧机参数,提高管控能力和监测效果。
通过大数据和机器学习算法的支撑,这种系统能够对钢铁轧制遇到的各种问题进行预警或自动修复,提升生产工艺的智能化和自动化程度。
3. 信息化和数字化技术信息化和数字化技术可以改变轧制过程中的人工操作和决策过程,提高操作及决策的准确率和精度。
高速轧机线材生产

1、线材生产的主要工艺装备手段:全连轧高速无扭线材轧机和控制冷却技术。
2、高速线材轧机:美国摩根公司的侧交45度;英国阿希洛公司的顶交45度;德国德马克公司的侧交15度/75度;意大利达涅利公司的平立交替高速线材轧机。
高速线材轧机的发展1.1线材轧机的发展与高速线材轧机的诞生A、横列式、半连续式、连续式、高速轧机B、二战结束时具有代表性的连续轧机:美国摩根公司为代表研制的精轧机组集体传动的二辊水平式轧机,德国施罗曼公司为代表研制的精轧机组单独驱动的平立交替式轧机,前者进行多线轧制时,椭圆轧件进入下一道必须扭转翻钢,最初为6架次,轧制速度为25.5m/s,当进一步提高速度是,首先受到进入精轧机活套的速度限制,当活套出口速度太高时甩尾、打结的故障频繁,后来改为8架次,速度提高到35m/s,活套入口速度则有14.1m/s降到13.8m/s,并且活套轧件的断面增大了,降低活套事故。
后者避免了扭转而且实现了单线轧制,但电机传动的速度精度低,不能控制在1%以内,达不到齿轮传动时相临轧机速比绝对不变的水平,结构高大,轧机高速运转震动大,速度不如前者,设备费用较前者贵近一倍,产品尺寸精度提高了20%,速度基本相同。
C、线材断面尺寸精度达到正负0.3mm时,若再提高精度对于低碳钢丝的拉拔就毫无意义了。
D、张力是造成线材同条尺寸差的主要原因之一。
轧件在未进入下一架之前,和后尾脱开前一架之后,头尾都建立不了张力,与中间有张力段比较头尾尺寸大。
理想的办法是无张力轧制,但在高速轧制的情况下,细小轧件的活套控制很难。
如采用微张力轧制再尽可能缩短轧机间距,则能将张力的危害减到最小。
实现微张力轧制必须提高传动精度,只有机组集体传动能达到这种要求。
1.2高速线材轧机的发展1.2.1高速线材轧机机型高速轧机:一般是最大轧制速度高于40m/s的轧机。
特点:高速、单线、无扭、微张力、组合结构、碳化钨辊环和自动化,产品特点是盘重大、精度高、质量好。
高速线材生产技术的发展趋势
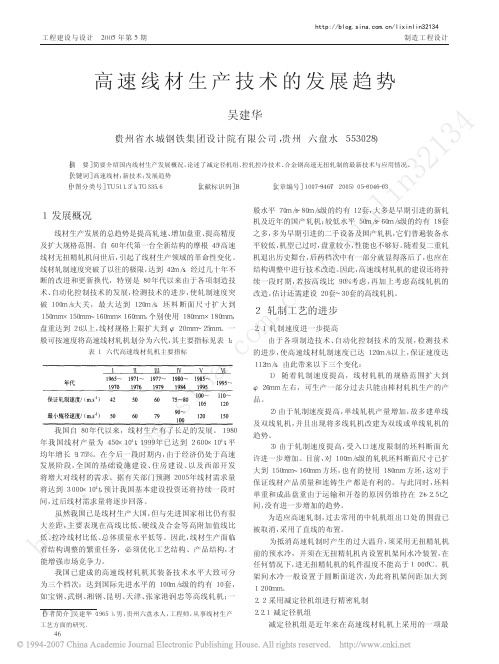
¡ ¡ ¡ ¡ ¡ ¡¡¢1965¡1970 1971¡1976 1977¡1979 1980¡1984 1985¡19951995¡ ¡¢£¤¥¦/¡m.s -1¡42 50 60 75¡80 100¡105 110¡120¡¢£¤¥¦/¡m.s -1¡ 5060 79 90¡100120 1501发展概况线材生产发展的总趋势是提高轧速、增加盘重、提高精度及扩大规格范围。
自60年代第一台全新结构的摩根45!高速线材无扭精轧机问世后,引起了线材生产领域的革命性变化。
线材轧制速度突破了以往的极限,达到42m/s。
经过几十年不断的改进和更新换代,特别是80年代以来由于各项制造技术、自动化控制技术的发展,检测技术的进步,使轧制速度突破100m/s大关,最大达到120m/s。
坯料断面尺寸扩大到150mm"150mm#160mm"160mm,个别使用180mm"180mm,盘重达到2t以上,线材规格上限扩大到!20mm#25mm。
一般可按速度将高速线材轧机划分为六代,其主要指标见表1:表1六代高速线材轧机主要指标我国自80年代以来,线材生产有了长足的发展。
1980年我国线材产量为450"104t,1999年已达到2600"104t,平均年增长9.75%。
在今后一段时期内,由于经济仍处于高速发展阶段,全国的基础设施建设、住房建设、以及西部开发将增大对线材的需求。
据有关部门预测2005年线材需求量将达到3000"104t,预计我国基本建设投资还将持续一段时间,过后线材需求量将逐步回落。
国内外先进热轧技术综述b
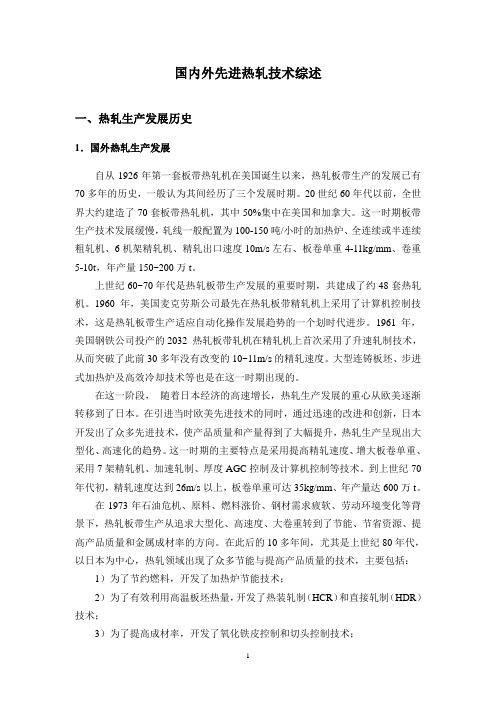
国内外先进热轧技术综述一、热轧生产发展历史1.国外热轧生产发展自从1926年第一套板带热轧机在美国诞生以来,热轧板带生产的发展已有70多年的历史,一般认为其间经历了三个发展时期。
20世纪60年代以前,全世界大约建造了70套板带热轧机,其中50%集中在美国和加拿大。
这一时期板带生产技术发展缓慢,轧线一般配置为100-150吨/小时的加热炉、全连续或半连续粗轧机、6机架精轧机、精轧出口速度10m/s左右、板卷单重4-11kg/mm、卷重5-10t,年产量150~200万t。
上世纪60~70年代是热轧板带生产发展的重要时期,共建成了约48套热轧机。
1960年,美国麦克劳斯公司最先在热轧板带精轧机上采用了计算机控制技术,这是热轧板带生产适应自动化操作发展趋势的一个划时代进步。
1961年,美国钢铁公司投产的2032 热轧板带轧机在精轧机上首次采用了升速轧制技术,从而突破了此前30多年没有改变的10~11m/s的精轧速度。
大型连铸板坯、步进式加热炉及高效冷却技术等也是在这一时期出现的。
在这一阶段,随着日本经济的高速增长,热轧生产发展的重心从欧美逐渐转移到了日本。
在引进当时欧美先进技术的同时,通过迅速的改进和创新,日本开发出了众多先进技术,使产品质量和产量得到了大幅提升,热轧生产呈现出大型化、高速化的趋势。
这一时期的主要特点是采用提高精轧速度、增大板卷单重、采用7架精轧机、加速轧制、厚度AGC控制及计算机控制等技术。
到上世纪70年代初,精轧速度达到26m/s以上,板卷单重可达35kg/mm、年产量达600万t。
在1973年石油危机、原料、燃料涨价、钢材需求疲软、劳动环境变化等背景下,热轧板带生产从追求大型化、高速度、大卷重转到了节能、节省资源、提高产品质量和金属成材率的方向。
在此后的10多年间,尤其是上世纪80年代,以日本为中心,热轧领域出现了众多节能与提高产品质量的技术,主要包括:1)为了节约燃料,开发了加热炉节能技术;2)为了有效利用高温板坯热量,开发了热装轧制(HCR)和直接轧制(HDR)技术;3)为了提高成材率,开发了氧化铁皮控制和切头控制技术;4)为了提高产品质量,开发了板厚、板宽、板凸度高精度控制技术。
- 1、下载文档前请自行甄别文档内容的完整性,平台不提供额外的编辑、内容补充、找答案等附加服务。
- 2、"仅部分预览"的文档,不可在线预览部分如存在完整性等问题,可反馈申请退款(可完整预览的文档不适用该条件!)。
- 3、如文档侵犯您的权益,请联系客服反馈,我们会尽快为您处理(人工客服工作时间:9:00-18:30)。
国内外高速线材轧制技术发展1 国内外高速线材轧制技术发展及现状1.1 70年代前后高速线材轧机简况(简单介绍)自1966年8月第一套高速无扭轧机在加拿大钢铁公司投产,直至70年代末,精轧机设计速度为50~70m/s,钢坯断面为80~130mm方,盘重800~2000kg。
1976年以后,出现了原西得得马克型,意大利达涅利型,得英财团的阿希洛型等高速轧机,单摩根侧交45°轧机占有绝对优势,在1966~1979年世界各国已建成投产的137套机组中占80%。
高速无扭精轧机组是高线生产的关键设备,它集中了当代线材生产工艺和设备的新成就。
该阶段的高速无扭轧机实现了高速、单线、连续无扭和微张轧制,采用∅150~∅210mm碳化钨辊环,采用了快速换辊和换导卫装置。
高速无扭轧机机架数量的选择和工艺布置特点如下:(1) 本阶段的轧制速度一般为60m/s,最大为75m/s。
为提高生产能力,一般采用粗、中轧机组多线轧制,精轧机组分线布置的方式。
在1978年前建成或改造的66家高线轧机中,24家为4线轧制,6家为3线轧制,二者约占总量的45%。
(2) 机架数随钢坯断面和成品尺寸不同而有所不同,但基本模式是粗轧7架、中轧8架、精轧10架布置方式,全线25架轧机,仅在精轧入口前有一活套,成品尺寸精度受连轧张力影响较大。
1.280年代高速线材轧制技术的发展(重点讲)80年代后,由于以连铸坯作为坯料的比例增加,连铸坯的断面尺寸趋于增大,及用户对小规格、大盘重线材需求量的日益增加,因而线材尺寸范围已扩大到∅5~∅25mm,精度要求也越来越高。
为适应这一发展,线材终轧速度已达到100m/s,设计速度达到120m/s,相应的钢坯断面尺寸均在∅130~∅160mm。
其技术进步表现在以下方面:(1)为实现无扭精轧机增速,原侧交45°轧机改为顶交45°V型轧机,向下旋转90°,设备重心下降,两根传动轴接近底面基础,机组重量较轻,倾动力矩减小。
同时轧线标高下降450mm,使设备重心下降,因而具有刚性增大,振动减小,运行稳定,噪音低,视野开阔,换辊检修方便等优点[1]。
1981~1990年摩根公司提供精轧速度超过100m/s(包括90m/s保证速度)的高速精轧机28套,其中1986年以后提供的100m/s 10套无扭精轧机均为V型结构。
其中较为典型的使1990年8月投产的巴西贝尔戈厂高速线材轧机,该套轧机共28道次,使用150mm×150mm ×12800mm坯料、轧制∅5.5mm线材时,终轧速度120m/s,单线年设计产量达60万t[2]。
与此同时,德马克由原侧交45°改为75°/15°,向下旋转30°,如酒钢、唐钢高线轧机;克虏伯公司将原侧交45°改为平-立交替,向下旋转45°,均向原阿希洛、达涅利公司的低重心方向发展。
(2) 为实现控温轧制和生产高硬度合金钢产品,轧机承载能力逐步提高,超重型轧机(VHD)被应用。
此时的摩根V型轧机除有重心降低的优点外,还将同架次的轧辊中心距增加(∅200mm机架增14mm,∅150mm机架增6.4mm),从而增加了轴颈尺寸,辊轴抗弯强度提高25%,减少了辊跳和断轴次数,轧机向重型化发展,新型超重型轧机的承受能力时普通型的1.8倍。
(3) 为提高线材的综合力学性能,除日益完善轧后控冷外,开始采用控温轧制技术,一是降低开轧温度,二是精轧前强迫水冷,降低轧件进入精轧机温度。
对于高、低碳钢,粗轧开轧温度分别为900、850℃,精轧机入口温度分别为925、870℃,出口轧件温度分别为900、850℃。
为降低精轧机开轧温度,国外新建轧机分别在中轧机组前后增设水冷箱,以保证精轧温度为900℃;在无扭精轧机架之间设水冷导管,以使线材终轧温度为800℃,超重型轧机可以满足700~750℃的轧制要求。
国外较为典型的控冷生产线为日本君津厂、巴西贝尔戈厂和韩国浦项线材厂。
为实现无扭机架之间水冷,摩根轧机间距由710/630mm逐步改为800/750mM,V型轧机有的增至1200/820mm,摩根机组总长分别为5895、6850和10100mm,这与超重型精轧机结构的改进是一致的。
(4) 随着轧制速度的提高和单线生产能力的增大,不仅新建长淘汰了多线轧制方案,而且一些多线生产厂家,也改为双线或单线方式,以获取更好的产品质量和效益。
例如,1991年乌克兰Maeewka冶金公司建成了双线、年产120万t的高线厂;澳大利亚BHP公司,与1988年将1975年建成的4线50m/s轧机,改为双线100m/s轧机,钢坯断面由90mm×90mm 方增加到120mm×120mm方,最高机时产量达140t/h;“七五”期间,我国首钢第二线材厂、鞍钢股份有限公司引进的4线轧机,也分别改成双线和3线轧机。
(5) 为减小连轧张力对成品尺寸精度的影响,减少精轧工艺故障,出现了单线悬臂式平-立交替的4架活套轧制的预精轧机组,使全线的活套数量由1个增至5个,实现了无扭无张轧制;为减少预精轧占地,90年代摩根公司又将精轧顶交无扭轧制技术用于预精轧机,以取代平-立交替轧机。
该技术特别适用于现有高线轧机改造(鞍钢已应用了该技术)。
(6) 为使双线轧制的粗中轧机组生产高碳合金钢产品时,也实现无扭轧制,摩根公司为浦项3#轧机设计了平-立可转换机架,即生产普通产品时,全部水平机架双线轧制;生产合金钢产品时,采用平-立全无扭单线轧制,增加了生产的灵活性。
此外,为提高成品精度,粗中轧机组张力的闭环调节、成品热定径机和测径仪等技术也被应用于线材生产线中。
1.3 90年代高线轧制新技术(重点)1.3.1双机架台克森高精度轧机为满足老式摩根轧机现代化改造的要求,近年摩根公司推出双机架台克森(Tekisun)高精度轧机,该轧机安装在无扭精轧机和夹送辊之间,与现有无扭轧机配合使用。
可将轧制速度有70m/s增加到100m/s,同时成品尺寸公差可达到±0.1mm。
该技术已于1991年在西班牙和日本大同钢厂应用并获成功。
我国天津高线厂、首钢三线材厂筹建,鞍钢高线厂改造时,都曾考虑过采用该技术;张家港、湘潭高线厂预留了安装此轧机的位置。
1.3.2 双模块靠素精轧机组为进一步提高轧机利用率,降低金属消耗,简化操作,实现以最低成本生产出高质量的产品,达涅利公司最新推出了双模块高速精轧机组,将高速线材生产技术推向新阶段。
七主要设计思想为:(1) 工艺布置:160mm×160mm方坯→粗中轧机组12架→预精轧机组5架,其中后3架为大压下定径轧机→8+4双模块精轧机组(T.M.B)→夹送辊吐丝机→控冷线。
(2) 3架大压下定径轧机的压下量,变化范围大,可以通过调整辊缝(±5mm)和快速换机架(约4min)来实现,以满足“T.M.B”机组前导孔型所需要的变形量,使1#~14#轧机仅用1套孔型。
(3)“T.M.B”机组由2个相续的模块组成,第一模块由8架组成,共有3个孔型系统;第二模块由4架组成,共有5个套孔型,覆盖了∅5~∅20mm成品所有规格。
(4) 可将双模块分开布置,如将第二模块设在水冷段后,可达到下列效果:①第一模块轧出的轧件均大于∅8mm,可实现水冷箱常开操作,消除轧件头部无水冷带来的缺陷。
②在双模块机组之间配备高速切头尾飞剪,可取消盘卷人工切头切尾。
(5) 借助大压下定径机组,“T.M.B”机组可采用小压下量(约12%~16%),成品精度达到±(0.08~0.10)mm。
双模块高速精轧机组的出现,给优质特殊刚线材生产带来巨大效益,具体表现在:(1)产品规格大,尺寸精度高,产品通常范围为∅5.5~∅20mm,使∅4.5~∅5.0mm和∅24~∅25mm的成品生产成为可能。
(2) 精轧速度高达120m/s,可提高小规格机时产量,单线达规格机时产量可达120t。
(3) 轧机利用系数≥90%,成材率≥97%,分别比传统轧机提高5%和0.5%。
(4) 全部产品可实现低温轧制,产品性能好,并可节能降耗。
2 国内高速线材生产技术的发展及现状(全面了解)2.1 国内高速线材轧机的研制及使用情况自70年代开始,我国即开展了45°无扭精轧机组的研制工作。
到目前,我国已有沈阳线材厂、齐齐哈尔特殊钢厂、攀钢、宜昌八一钢厂、苏州钢厂、南宁钢厂、通钢公司、泰州轧钢厂、三明钢铁厂、太原钢铁公司、无锡玉东钢厂、新余钢厂等12套国产高速线材轧机,除沈线、攀钢为双线外,其余均为单线,轧制速度为36~65m/s,总设计能力为170万t。
最近,北京钢铁设计研究总院研制出顶交45°新型精轧机。
其基本性能:轧速90m/s(设计为1085m/s),产品规格∅5.5~∅20mm,精轧机架规格∅200×5+∅165×5,机组总延伸系数9.5,年生产能力30万t。
2.2 引进国外高线轧机概况(1)“七五”期间我国先后有11个厂家,从国外10家引进16条高速线材生产线,年生产能力达340万t。
引进的轧机种类繁多,性能各异,综合评价具有下列特点:①在装备上,有马钢、酒钢、唐钢的新设备,也有以首钢为代表的半新半旧设备和马尾中钢、青岛钢厂的旧设备。
②从制造厂家和轧机类型上,有摩根公司的45°侧交,德马克公司的75°/15°侧交,阿希洛公司45°顶交和达涅利公司的平-立交替式,兼容了世界各主要厂商制造的典型设备。
③轧制线数以单线、双线为主,也有3线、4线轧制,成品保证速度为50~90m/s。
在引进设备中,综合技术水平较高的有马钢、唐钢、酒钢,其后为首钢。
在达产速度上,首钢居于榜首,1995年首钢两厂实际年产175万t,是全国引进高线轧机设计总量的27%。
(2)为配合实施“八五”期间硬线达到120万t的发展规划,昆明、湘潭、天津高速线材厂又相继建成投产。
1996年又有张家港、包头和武港高线厂投产。
新投产的6家生产线(除武港双线外)均为单线。
为满足硬线生产要求,全线无扭轧制,精轧机选用先进的超重型“V”型轧机,设计速度在120m/s以上,保证速度超过100m/s,具有国外90年代技术水平。
见表1。
表1. “八五”及1996年投产的高线厂序号厂名简介线数保证速度/m∙s设计能力/万t坯料断面mm⨯mm盘重/t粗\中架机架数预精轧机架数投产日期年\月1 昆钢 1 105 35 150⨯150 2.0 6+6 6 1995.12 湘钢 1 105 38 150⨯150 2.0 6+8 4 1995.123 天钢 1 105 35 135⨯135 2.0 6+64 1995.54 包钢 1 105 35 150⨯150 2.0 6+18 4 1995.125 张钢 1 105 63 130⨯130 2.0 6+6 4 19966 武钢 2 105 70 200⨯200 1.8 6+10 4 1996.10双线平平到1996年末,全国引进高线轧机的厂家约为18家,设计能力为720万t。