车用轻量化材料分析
乘用车典型零部件轻量化系数计算方法

乘用车典型零部件轻量化系数计算方法在当今的汽车行业中,轻量化技术已经成为了发展的重要趋势。
轻量化不仅可以提高汽车的燃油经济性,减少尾气排放,同时也可以提高汽车的性能和安全性能。
乘用车典型零部件轻量化系数计算方法是一个关键的环节,它可以帮助汽车制造商评估和优化零部件的轻量化设计。
在本文中,我们将探讨乘用车典型零部件轻量化系数的计算方法,并结合个人观点和理解进行深入讨论。
1. 轻量化系数的定义在深入探讨乘用车典型零部件轻量化系数的计算方法之前,首先需要了解轻量化系数的定义。
轻量化系数是衡量某个零部件轻量化程度的参数,一般表示为百分比。
具体地说,轻量化系数可以通过计算零部件的质量减少量与原始质量的比值来得到。
如果一个零部件的原始质量为100kg,经过轻量化设计后减少到90kg,那么这个零部件的轻量化系数就为10%。
通过轻量化系数,可以直观地了解到零部件的轻量化效果,进而辅助制定轻量化设计策略。
2. 轻量化系数的计算方法乘用车典型零部件轻量化系数的计算方法并不是一成不变的,它会根据不同的零部件和轻量化设计策略而有所不同。
一般来说,轻量化系数的计算方法可以分为以下几种常见的形式:2.1 质量分配法质量分配法是一种常用的轻量化系数计算方法,它通过将零部件的总质量按比例分配到各个组成部分上,然后根据设计变化情况计算轻量化系数。
具体计算公式为:轻量化系数= ∑(原部件质量 - 新部件质量) / 原部件质量× 100%2.2 材料替代法材料替代法是指通过使用密度更小、强度更高的新材料替代原有材料,从而实现零部件的轻量化。
计算轻量化系数的方法为:轻量化系数 = (原部件质量 - 新部件质量) / 原部件质量× 100%2.3 结构优化法结构优化法是通过对零部件的结构进行优化设计,从而减少材料用量,实现零部件的轻量化。
计算轻量化系数的方法为:轻量化系数 = (原部件质量 - 新部件质量) / 原部件质量× 100%3. 个人观点和理解在我看来,乘用车典型零部件轻量化系数的计算方法是非常重要的。
面向汽车轻量化设计的材料测试与应用技术研究1
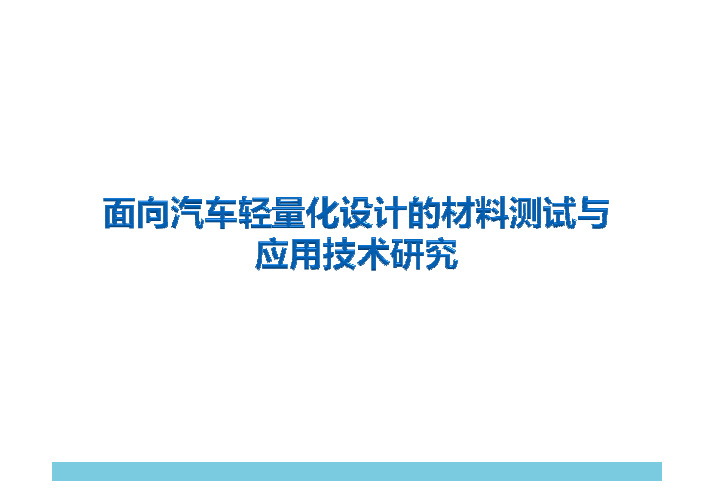
3
碳纤维材料仿真建模:以 Ls-Dyna中MAT54/55基础, 建立复合材料层合板模型
Source:2018车用材料性能测试与应用技术研讨会 21
非金属材料力学特性与仿真模型
不同非金属材料之间力学性能及细观结构差异较大,其变形过程涉及其内部分子键 断裂或大分子运动。充分考虑其曲线形式差异、各向异性特点、应变率效应等力学特性 ,塑料最终选定MAT187材料卡片。
1、概要 2、金属材料性能评价与仿真模型开发 3、非金属材料性能评价与仿真模型开发 4、接头力学性能评价与仿真模型开发 5、多材料混合车身轻量化技术特点概述
20
非金属材料力学特性与仿真模型
1
塑料材料仿真建模:以LsDyna中MAT187材料卡片为 基础,增加断裂失效模型
2
泡沫材料仿真建模:以 MAT57/83材料卡片为基础, 针对座椅及前保吸能泡沫
15
典型金属材料断裂失效行为的试验测试技术
d
d
d
1
1
5
5
0
Source:2018车用材料性能测试与应用技术研讨会 16
典型金属材料断裂失效行为的仿真分析
ε f 2,0
1,8 1,6
Element size 1mm
1,4
1,2
1,0
0,8
0,6
0,4
0,2
0,0
-0,1
0,0
0,1
0,2
0,3
0,4
1、概要 2、金属材料性能评价与仿真模型开发 3、非金属材料性能评价与仿真模型开发 4、接头力学性能评价与仿真模型开发 5、多材料混合车身轻量化技术特点概述
2
1、概要 2、金属材料性能评价与仿真模型开发 3、非金属材料性能评价与仿真模型开发 4、接头力学性能评价与仿真模型开发 5、多材料混合车身轻量化技术特点概述
汽车方面的毕业论文范文

汽车方面的毕业论文题目:汽车轻量化材料的应用与性能研究摘要随着全球能源危机和环保要求的不断提升,汽车轻量化已成为汽车工业的重要发展方向。
本研究深入探讨了多种轻量化材料在汽车制造中的应用及其性能表现,重点分析了铝合金、镁合金、高强度钢及碳纤维复合材料等主流材料的性能特点、制备工艺及实际应用效果。
研究结果表明,轻量化材料的应用显著降低了汽车整备质量,提高了燃油经济性,并改善了车辆操控性和行驶安全性。
此外,本研究构建了全面的轻量化材料性能评价体系,提出了包括合金化、热处理、表面处理及制备工艺改进等在内的性能优化策略,并通过实验验证了这些策略的有效性。
实验表明,优化后的轻量化材料在强度、韧性及耐腐蚀性等方面均得到了显著提升,为汽车轻量化技术的发展提供了有力支持。
然而,研究也存在一定局限性,如研究范围有限、实验设计需进一步精细化等。
未来研究应关注新兴轻量化材料,加强实验设计的科学性和严谨性,并密切关注行业动态和技术发展趋势,以推动轻量化材料在汽车工业中的创新应用,助力汽车工业可持续发展。
关键词:汽车轻量化材料;性能研究;铝合金;镁合金;碳纤维复合材料;性能优化策略目录摘要 (1)第一章引言 (3)1.1 研究背景与意义 (3)1.2 国内外研究现状 (4)1.3 研究方法与创新点 (5)第二章汽车轻量化材料概述 (7)2.1 轻量化材料分类 (7)2.2 材料性能特点 (8)2.3 制备工艺与技术 (9)第三章轻量化材料在汽车制造中的应用 (10)3.1 车身结构应用 (10)3.2 引擎与底盘部件应用 (11)3.3 内外饰件应用 (11)第四章轻量化材料性能评价与优化 (13)4.1 材料性能评价体系 (13)4.2 性能优化策略 (13)4.3 优化实验与结果分析 (14)第五章结论与展望 (16)5.1 研究结论 (16)5.2 研究局限性与未来方向 (16)第一章引言1.1 研究背景与意义在全球范围内,能源危机和环境问题日益严重,在此背景下,汽车工业轻量化已成为当务之急。
汽车轻量化材料及制造工艺研究现状

汽车轻量化材料及制造工艺研究现状摘要:近年来,我国汽车产业快速发展,产业规模不断提升。
消费者对于汽车质量的标准和要求也越来越高。
汽车轻量化发展是汽车产业发展的重要方向,如何通过轻量化发展提升汽车的性能和质量已经成为汽车企业关注的重点。
本文结合汽车轻量化材料的特点,分析汽车轻量化制造工艺,为企业汽车轻量化发展水平的不断提升提供借鉴和参考。
关键词:汽车材料;轻量化发展;制造工艺汽车产业的进步为促进经济社会发展、提升人民生活水平等发挥着重要的重要。
消费者对于汽车的质量要求越来越高,汽车产业面临着能耗、安全、环保等方面的问题。
在这种情况下,轻量化发展更加符合企业发展的需要。
汽车轻量化在污染、能耗等方面的优势,有助于汽车企业不断提升经济效益和社会效益,实现汽车产业的稳定可持续发展。
1汽车轻量化材料实现汽车轻量化能够有效提升企业的安全、节能、环保等方面的性能,汽车轻量化材料是实现汽车轻量化的基础,目前常用的汽车轻量化材料主要包括以下几种:一是纤维增强材料,其中主要包括玻璃纤维、碳纤维等。
它们是通过复杂工艺形成的复合型材料,具有强度高、耐磨性强等方面的优势。
纤维增强材料主要应用于汽车底盘、支架等部位的制造,在保护汽车稳定、安全等方面发挥重要的作用,同时通过提到传统汽车材料实现汽车轻量化的目标。
二是低密度PP材料。
这种材料的拉伸强度和刚度等方面具备性能优势,同时经过加工强化后能够满足汽车制造很多方面的应用,且它具备明显的成本优势,能够有效降低汽车制造成本。
低密度PP材料主要应用于汽车保险杠、门板等部件的制造,经过应用能够实现非常好的汽车轻量化效果。
三是工程塑料。
这种材料质量轻且抗腐蚀性强,能够有效地应用于多种汽车零部件制造,进而实现汽车轻量化的目标。
目前工程塑料在汽车制造中应用更加广泛。
借助工程塑料的应用能够有效降低汽车制造中铁的应用,从而实现汽车轻量化。
四是低VOC绿色环保材料。
低VOC绿色环保材料是通过一些添加剂来降低挥发性的材料,主要应用于汽车内部部件。
新能源汽车内饰轻量化分析
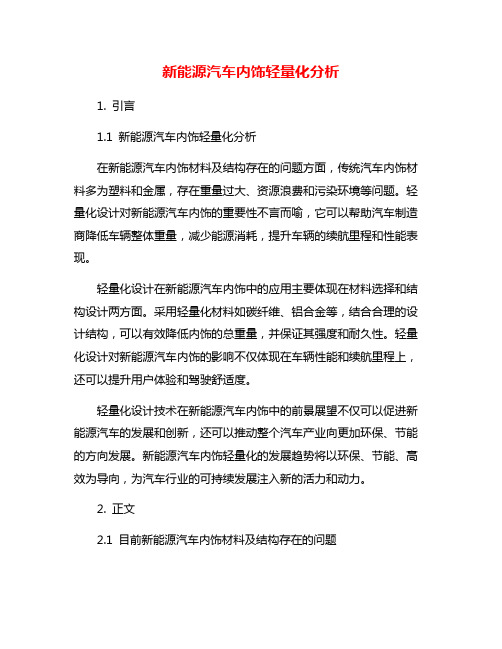
新能源汽车内饰轻量化分析1. 引言1.1 新能源汽车内饰轻量化分析在新能源汽车内饰材料及结构存在的问题方面,传统汽车内饰材料多为塑料和金属,存在重量过大、资源浪费和污染环境等问题。
轻量化设计对新能源汽车内饰的重要性不言而喻,它可以帮助汽车制造商降低车辆整体重量,减少能源消耗,提升车辆的续航里程和性能表现。
轻量化设计在新能源汽车内饰中的应用主要体现在材料选择和结构设计两方面。
采用轻量化材料如碳纤维、铝合金等,结合合理的设计结构,可以有效降低内饰的总重量,并保证其强度和耐久性。
轻量化设计对新能源汽车内饰的影响不仅体现在车辆性能和续航里程上,还可以提升用户体验和驾驶舒适度。
轻量化设计技术在新能源汽车内饰中的前景展望不仅可以促进新能源汽车的发展和创新,还可以推动整个汽车产业向更加环保、节能的方向发展。
新能源汽车内饰轻量化的发展趋势将以环保、节能、高效为导向,为汽车行业的可持续发展注入新的活力和动力。
2. 正文2.1 目前新能源汽车内饰材料及结构存在的问题目前新能源汽车内饰材料多样性不足,大多采用传统材料如塑料和皮革,缺乏创新性和环保性。
这些材料在生产过程中会产生大量的废弃物,对环境造成污染。
新能源汽车内饰结构设计不够轻量化,导致车辆整体重量增加,影响了车辆的能源效率和续航里程。
过重的内饰结构也会增加车辆的制动距离和加速能力,影响驾驶体验和安全性。
由于新能源汽车电池容量较大,需要更多的空间来放置电池组件,使得内饰空间受限,设计空间变得局促。
这对内饰设计带来了挑战,需要在保证电池组件安全和便捷性的前提下,尽可能减少内饰结构的占用空间。
目前新能源汽车内饰材料和结构存在的问题主要包括材料缺乏多样性和环保性、结构设计不够轻量化、内饰空间受限等方面。
为了推动新能源汽车内饰的发展,需要在材料和结构设计上进行创新,实现轻量化和环保化的目标。
2.2 轻量化设计对新能源汽车内饰的重要性轻量化设计对新能源汽车内饰的重要性是不可忽视的。
《汽车材料及轻量化趋势》报告总结

《汽车材料及轻量化趋势》报告总结汽车材料及轻量化趋势报告总结随着环境保护和能源消耗的日益严重,汽车行业对节能减排和轻量化技术的需求越来越高。
本报告对当前汽车材料及轻量化趋势进行了研究和总结,以下为报告总结的主要内容。
首先,报告对目前汽车材料的使用情况进行了分析。
目前,汽车主要采用的材料包括钢铁、铝合金、塑料和复合材料等。
钢铁是汽车材料中使用最广泛的材料,其优点是强度高、价格低廉,但密度较大,不利于车辆的轻量化。
铝合金具有重量轻、强度高的特点,但价格相对较高。
塑料和复合材料具有重量轻、强度高、耐腐蚀等优点,但在成本和可回收性方面仍存在一定的挑战。
其次,报告对轻量化技术的发展趋势进行了探讨。
随着材料科学和工程技术的不断进步,新型材料的研发和应用也得到了广泛关注。
其中,碳纤维复合材料、镁合金和高强度钢等被认为是未来汽车轻量化的重要方向。
碳纤维复合材料具有高强度、高刚度和低密度的特点,可以显著减轻车辆重量,但制造成本较高。
镁合金具有重量轻、强度高和良好的可塑性,但存在易燃、易腐蚀和价格高等问题。
高强度钢通过优化合金设计和热处理工艺,可以在保证强度的前提下减轻材料的重量,但成本较高。
最后,报告对轻量化技术的市场前景进行了展望。
随着政府对环境保护和能源消耗的要求越来越严格,汽车行业对轻量化技术的需求将持续增加。
轻量化技术除了能够减少燃料消耗和排放,还能提高汽车的性能和安全性。
因此,未来几年内,轻量化技术有望在汽车行业取得广泛应用。
特别是碳纤维复合材料和高强度钢等新型材料的研发和应用将成为汽车轻量化的重要方向。
综上所述,汽车材料及轻量化趋势报告指出当前汽车材料的使用情况,并对轻量化技术的发展趋势进行了分析和总结。
报告认为,未来汽车行业对轻量化技术的需求将持续增加,并展望了轻量化技术的市场前景。
希望该报告可以为相关企业和研究机构提供有价值的参考和指导,推动汽车轻量化技术的研发和应用。
2023年车用塑料形势分析

2022年车用塑料形势分析塑料以其重量轻、设计空间大、制造成本低、性能优异、功能广泛,能使汽车在轻量化、平安性和制造成本等几方面获得更多的突破,从而成为了21世纪汽车工业最好的材料选择。
作为汽车轻质材料,塑料及其复合材料不仅可减轻零部件约40%的质量,而且还可使选购成本大幅降低,所以近年来塑料在汽车中的用量快速上升。
今年第四季度的车市还将连续近几个月来的旺销势头。
一是汽车刺激政策效果具有可持续性;二是中西部城市有浩大的人口基础,虽然从目前的乘用车肯定占比不高,但从趋势看显现出份额逐年攀升的态势;三是中西部地区,受金融危机的影响小,区域经济政策上受益更大,经济增速相对较高。
因此,2022年中国汽车销量达到1200万辆的目标完全能实现,中国将成为全球的第一大市场,销量将超过美国而成为世界第一。
平安舒适、节能环保是汽车塑化的推动力汽车轻量化已经成为降低汽车排放、提高燃烧效率的有效措施。
各国对汽车的轻量化、燃油消耗指标都作出了明确的规定,减轻汽车质量已经成为世界汽车行业的重要讨论课题。
据美国平均燃料经济性(CAFE)估算,轿车平均质量要削减8%才能达到标准规定的6.7L/100km。
依据最新资料,国外汽车自身质量同过去相比已经减轻了20%。
将来的10年内,轿车自身质量还将连续减轻20%。
铝合金、镁合金、工程塑料、复合材料和高强度钢、超高强度钢等轻量化材料的开发与应用在汽车的轻量化中将发挥重大作用。
目前,高性能工程塑料用量的多少已成为现代汽车工业进展水平的重要标志之一。
据专家介绍,假如现有欧洲路面上跑的汽车都采纳PC材料替代车侧窗和后窗的玻璃,使车身轻量化,仅此一项每年则将节约约21亿L燃油,相当于24亿欧元。
另外,由于使用了塑料,汽车的整体重量减轻,由此欧洲每年可削减1000万t的CO2的排放。
目前在发达国家车用塑料现已占塑料总消耗量的7%以上,估计不久将会达到10%~11%。
国外汽车的内饰件如今已基本实现塑料化。
汽车制造中的轻量化材料与工艺创新

汽车制造中的轻量化材料与工艺创新随着环境保护意识的增强和能源危机的日益严重,汽车工业正迫切寻求一种更加环保、高效的解决方案。
轻量化是一个不可忽视的趋势,汽车制造中的轻量化材料与工艺创新正扮演着重要的角色。
本文将探讨汽车制造中的轻量化材料与工艺创新,并分析其对汽车工业的影响与发展。
一、轻量化材料在汽车制造中的应用随着技术的进步,新型轻量化材料被广泛应用于汽车制造中。
其中,铝合金、镁合金和碳纤维等材料具有重量轻、强度高的优势,逐渐取代传统材料的地位。
与传统钢铁相比,铝合金具有优异的耐腐蚀性和可塑性,可以实现更好的造型设计和外观效果。
镁合金具有更高的特殊强度和刚性,可以有效减轻汽车的整体重量。
碳纤维作为一种新型的复合材料,具有优异的强度和刚性,同时重量轻,被广泛应用于高端汽车制造。
二、轻量化材料对汽车性能的影响轻量化材料的应用不仅可以有效减轻汽车的总重量,还可以提高汽车的燃油经济性和性能表现。
首先,减轻汽车自身重量可以降低能源消耗,提高燃油效率,减少尾气排放。
其次,轻量化材料具有更好的刚性和强度,能够提高车辆的操控性和安全性能。
此外,减轻汽车总重量还可以降低车辆的传动系统和制动系统的负荷,延长部件的使用寿命,减少维修保养成本。
三、轻量化工艺创新与汽车制造轻量化材料的应用不仅需要材料本身的创新,还需要在汽车制造工艺方面进行创新。
制造商需要采用先进的焊接技术、粘接技术和成型技术,以确保新材料的安全可靠性。
例如,与传统焊接相比,激光焊接是一种更加灵活高效的工艺,可以减少焊接热影响区域,提高焊接强度和质量。
同时,粘接技术也成为轻量化制造中的重要工艺,其具有良好的密封性和减震性能,可以提供更好的承载能力和车身刚性。
此外,先进的成型技术,如热成型、压缩成型和注塑成型等,可以实现复杂的车身构造和形状设计,提高整体车身的强度和轻量化效果。
四、轻量化材料与工艺创新对汽车工业的影响与发展汽车工业的持续发展离不开轻量化材料与工艺的创新。
- 1、下载文档前请自行甄别文档内容的完整性,平台不提供额外的编辑、内容补充、找答案等附加服务。
- 2、"仅部分预览"的文档,不可在线预览部分如存在完整性等问题,可反馈申请退款(可完整预览的文档不适用该条件!)。
- 3、如文档侵犯您的权益,请联系客服反馈,我们会尽快为您处理(人工客服工作时间:9:00-18:30)。
ULSAC
ULSAC项目试制车门的结构及装配过程
高强度钢
ULSAB-AVC
ULSAB-AVC项目中采用的材料强度和加工工艺
ULSAB-AVC项目中采用的各种高强度钢板
高强度钢
屈服强度小于210MPa的 钢为软钢 210-550MPa的为高强度 钢(HSS) 高于550MPa的为超高强 度钢(UHSS)。
ULSAB
重量/kg 扭转刚度/N·m/kg 弯曲刚度/N·m/kg 一次固有振动数/Hz
部件个数
对比车平均值 271 11531 11902 38 195
ULSAB目标 <200 <13000 <12200 <40
ULSAB试制 203 20800 18100 60 158
与对比车相比 -68 9269 6198 22 -37
-
布氏硬度/HB 70 65 60 60 63 60
24
22
13
10
31
28
11
10
6061-0
45
6061-T4
197
冷轧钢板
181
125
30
25
271
24
20
298
46
23
主要铝合金板的机械性能
硬度HV 52 80 26 91
64 45
n值
r值
0.32
0.74
0.13
1.05
0.31
0.61
0.13
0.75
0.28
0.66
0.20
0.74
0.21
TRT在NSB项目中的 应用
2020/10/18
2.1 高强度钢
TRT在Scalight项目中 的应用
2.2 2.3 2.4
高强度钢
车身用高强钢的结构与性能
铝合金
铝合金的发展历史
“空间框架结构”车身
实现了全铝车身设计制造
“壳式支撑结构”车身
带加强筋钢结构的一种替代品
“四门两盖”阶段
比较昂贵的权宜之计,对车身承 载性影响不大
汽车用钢屈服强度和伸长率的关系
钢
YP/MPa
TS/MPa
EI /%
λ-值
厚度/mm
热轧
开发钢
470
610
35
90%
2.3
传统钢
530
610
24
60%
冷轧
开发钢
390
600
37
60%
1.4
传统钢
பைடு நூலகம்
420
600
25
60%
590MPa级残留奥氏体热、冷轧钢板的机械性能
高强度钢
材料结构方式
变截面技术 对于车辆的轻 量化、安全性 和其结构本身 的承载适应性 都有显著提高
•变形铝合金 ——是经熔炼铸成铸锭后,在经过热 挤压加工形成各种型材、棒材、管材 和板材。
制造保险杠、发动机罩、车门 行李箱等车身面板、车轮的轮 辐、轮罩、轮外饰罩等结构件 仪表板等装饰件。
铝合金
密度低 耐蚀性好
是钢的1/3 不易生锈
柔性…的强度设计
在常温下的强度不低于铸铁
高的导热性能
约比铝高三倍
铝合金
铝合金在车身中应用车型
• 奥迪A8 第一代铝合金ASF车身
奥迪 A2第二代铝合金ASF车身 新奥迪A8第二代铝合金ASF车身
铝合金
车身用铝合金的特点
•铸造铝合金 ——直接用铸造方法浇注或压铸成零件 或毛坯的铝合金。
变速箱壳体等壳体类零件; 电动机部件; 保险杠、轮辋、制动钳等非发动 机结构件。
TRB的应用实例
2.1高强度钢
高强钢拼焊应用于车身
2020/10/18
2.1 高强度钢 2.2 2.3 2.4
欧洲激光拼焊板历年使用量
激光拼焊板,采用激光焊接技术把 不同厚度、不同表面镀层甚至不同 原材料的金属薄板焊接在一起,然 后再进行冲压。
高强度钢
空心变截面钢管技术,实现进一步 的轻量化,而且与传统的矩形截面 相比,具有同样的抗拉压和突出的 抗扭力学性能。
北美轿车高强度钢的应用趋势
高强度钢
高强度钢在车身上应用的示例
•车身结构减重 •抗扭抗弯提高 •造价降低 •90%高强钢板
•减重32%
•减重约30%
•五星碰撞标准
•无框架车门结构 •制造成本降低
•生产成本被接受
•高强钢车门外板 •成本低于铝材30% •油耗降低
•超高强钢车门杆件
•钢铁高回收性
高强度钢
高强度钢
高强度钢的发展历史
CP 钢 TMS 钢 TRIP 钢 各向同性钢 高强度 IF 钢 烘烤硬化钢 双相钢 磷合金钢 微合金钢 1975 1980 1985 1990 1995 2000
汽车用高强度钢板的开发进程
高强度钢
高强度钢在车身轻量化发展中的地位和作用
价格低,经济性好; 性能优越,能保证大零件 的刚性; 利用现有的汽车生产线, 节约设备投资。
轻量化材料
1.高强度钢
与国际先进水平差距大; 可生产低级别的双相钢; 冷轧超高强度钢可生产一部分; 先进的高强度钢板在研发阶段。
3.镁合金
镁合金的时代已经到来; 我国是镁资源大国; 目前国内用量很少。
2.铝合金
资源丰富,体系完善 ; 我国汽车用铝与国际水平差距较大 ; 使用潜力大。
4.复合材料
已经起步,逐年上升; 多元化发展; 品种较少,与国外差距大 。
2020/10/18
等厚度板 TWB 减重20% TRB 减重40% TRT减重55%
各种结构板料的减重效果比较
高强度钢
各种结 构板料 的机械 性质比 较
综合新方案
连续变截面板技术,轧制过程中, 轧辊的间距可以实时地调整变化, 从而使轧制出的薄板沿轧制方向上 具有预先定制的变截面形状。
高强度钢
运用TRB技术的宝马后横梁
2.00
奥迪铝车身空间框架结构中的材料
镁合金
镁合金在车身上应用的示例
近年来世界汽车用镁合金压铸件统计表
镁合金
镁合金在车身上应用的出发点
按化学成分分类 按是否含变质剂锆分类
按成型工艺分类
铸造镁合金多用于压铸工艺生产。生产效率高、精度高、铸件表面质量好 、铸态组织优良、可生产薄壁及形状复杂的构件。
变形镁合金可用挤压、轧制、锻造和冲压等塑性成形方法加工。具有更高 的强度、更好的塑性和更多的样式规格。
表面美观
无色透明的氧化膜
铸造性好
…
切削性好 耐磨性好
溶化温度低,易成复杂形状
...
是铸铁的4-5倍,工具磨损小
铝合金
种类 5052-0 5052-H24 5182-0 5182-H24
屈服极限(N/mm2) 107 212 125 273
拉伸强度(N/mm2) 213 269 264 350
延伸率(%) 平均延伸率(%)
镁合金
牌号 AZ91D AM60B AM50A AS41A AS21 AE42
抗拉强度/MPa 240 225 210 215 172 230
屈服强度/MPa 160 130 125 140 110 145
镁合金的力学性能
延伸率/% 疲劳强度/MPa
3
50~70
8
50~70
10
-
6
50~70
4
-
10