惠炼延迟焦化焦炭塔顺控系统的调试与运行
延迟焦化焦炭塔冲塔处理措施的探讨
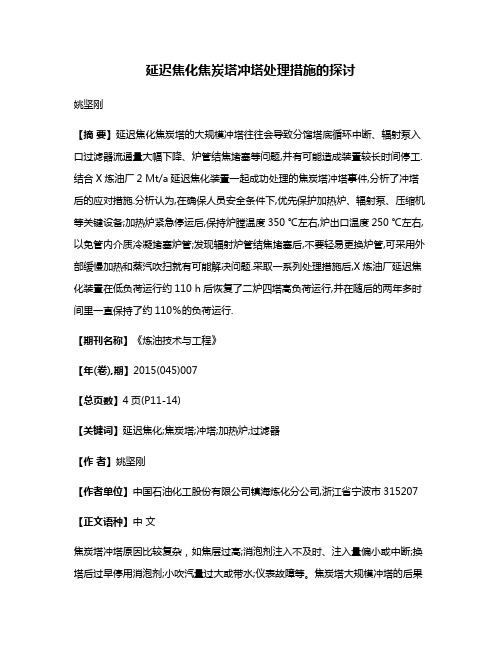
延迟焦化焦炭塔冲塔处理措施的探讨姚坚刚【摘要】延迟焦化焦炭塔的大规模冲塔往往会导致分馏塔底循环中断、辐射泵入口过滤器流通量大幅下降、炉管结焦堵塞等问题,并有可能造成装置较长时间停工.结合X炼油厂2 Mt/a延迟焦化装置一起成功处理的焦炭塔冲塔事件,分析了冲塔后的应对措施.分析认为,在确保人员安全条件下,优先保护加热炉、辐射泵、压缩机等关键设备;加热炉紧急停运后,保持炉膛温度350 ℃左右,炉出口温度250 ℃左右,以免管内介质冷凝堵塞炉管;发现辐射炉管结焦堵塞后,不要轻易更换炉管,可采用外部缓慢加热和蒸汽吹扫就有可能解决问题.采取一系列处理措施后,X炼油厂延迟焦化装置在低负荷运行约110 h后恢复了二炉四塔高负荷运行,并在随后的两年多时间里一直保持了约110%的负荷运行.【期刊名称】《炼油技术与工程》【年(卷),期】2015(045)007【总页数】4页(P11-14)【关键词】延迟焦化;焦炭塔;冲塔;加热炉;过滤器【作者】姚坚刚【作者单位】中国石油化工股份有限公司镇海炼化分公司,浙江省宁波市315207【正文语种】中文焦炭塔冲塔原因比较复杂,如焦层过高;消泡剂注入不及时、注入量偏小或中断;换塔后过早停用消泡剂;小吹汽量过大或带水;仪表故障等。
焦炭塔大规模冲塔的后果一般都比较严重,特别是在生焦末期或小吹汽初期,大量焦粉(泡沫焦)在短时间内进入分馏塔,导致分馏塔底循环中断、辐射泵入口过滤器流通量大幅下降、炉管结焦堵塞等,严重的还会使装置较长时间停工。
如某石化公司2014年5月发生了一起焦炭塔冲塔事件,导致该装置非计划停工,紧急抢修10日后才恢复正常生产。
以X炼油厂一套由二炉四塔组成的设计规模为2 Mt/a延迟焦化装置(Ⅱ焦化)为例,对其成功处理冲塔事件的措施进行了总结。
焦炭塔的冲塔往往都是突发性的,因而及时有效的应急措施就显得非常重要。
2012年8月Ⅱ焦化焦炭塔(T1101/2)小吹汽时,因塔内焦层过高、消泡剂注入中断等原因,发生了一起较为严重的冲塔事件,短时间内大量焦粉进入分馏塔。
延迟焦化装置除焦控制系统改造分1

延迟焦化装置除焦控制系统改造分析中国石化股份有限公司天津分公司炼油部焦化装置1997年投产,采用两炉四塔、两泵、一阀的模式,两台高压水泵一开一备,各用一套油站,以渣油为原料,加热到高温475~505C,迅速转移到焦炭塔中进行深度热裂化和缩合反应,即把焦化反应延迟到焦炭塔中进行,减轻炉管结焦程度,延长装置运行周期。
水力除焦系统的作用是使焦炭塔中的焦炭在高压水作用下脱落至储焦池后形成焦炭。
高压水经泵出口三位控制阀、高压水管线至78m除焦塔顶,通过隔断阀、高压绞管、水龙头、钻杆、水涡轮,最后从水力钻孔切焦器喷嘴喷射到塔内的焦层上。
操作钻杆通过绞车进入焦炭塔,利用高压水射流的轴心动压力和总打击力,分别进行钻孔和切焦作业,使焦炭塔内焦层破碎、脱落。
水力除焦控制系统包括高压水泵、泵阀、塔阀、钻机绞车等控制,要求控制系统须具有高可靠性及安全性,因此选用了Siemens冗余PLCS7400H控制系统,将原AB系统IlOV控制电压改为24V,将高压水泵轴系监控BENTLY仪表信号送入控制系统,实现操作站实时监测。
一、改造后除焦控制系统构成改造后l#泵除焦控制系统采用Siemens冗余PLC、非接触式接近开关、BENTLY在线检测系统,构成了一套设计合理、安全联锁、功能齐全、操作方便、工作效率高的控制系统。
1.Siemens S7-400控制系统结构此次改造后系统硬件组态图如图l所示,采用UR2-H冗余控制器机架,控制器选用414-4H冗余CPU,I/O机架型号为IM153 -2共四套,通过冗余PROFIBUS 总线与系统进行通信,共采用11块16通道DI开关量输入模块,七块16通道DO开关量输出模块,九块八通道AI模拟量输入模块,其中三块为RTD温度输入模块,一块四通道AO模拟量输出模块。
上位通信通过两块C P443—1工业以太网通信模块及Siemens交换机与工作站进行通信,实现整个除焦过程的在线实时监测。
另外,38m平台上设操作台两套,操作台上设有报警、显示仪表、操作按钮,通过该操作台对除焦过程进行操控。
延迟焦化装置焦炭塔顺控系统的应用与运行

28中海沥青股份有限公司1.0Mt/a延迟焦化装置由镇海石化工程公司设计,于2016年5月15日一次开车成功。
装置采用一炉两塔工艺,设计生焦周期为24h。
焦炭塔是两塔频繁切换操作,一个塔在进料生焦,另一个塔则在小吹汽、大吹汽、小给水、大给水、溢流、放水、卸盖、除焦、上盖、赶空气、蒸汽试压、脱水、油气预热等操作[1],每个周期(36~48 h)切换一次,每次有31个阀门需要操作,其中约20多个阀门开关错误会导致火灾等安全事故[2]。
为避免发生人为误操作事故,保障人员和设备安全,装置投用了一套焦炭塔顺序控制系统。
1 焦炭塔工艺联锁特点①顺控共有27只电动阀、2只自动底盖机和2台自动顶盖机。
大油气背压环阀和油气平衡阀不参加顺控过程,其中大油气背压环阀在DCS中具有远程调节的功能。
②系统只能发出指定设备和阀门的联锁或解锁信号,不能发出联锁设备的开关操作信号,相关指定操作由外操现场完成。
在所有顺控相关设备、电动阀门现场附近分别设置操作完成现场确认按钮(需按2s以上),在所需顺控步骤的设备、电动阀门操作完成后,阀位状态信号与该阀或设备的现场确认信号共同回讯至DCS联锁系统。
每个大步骤必须按“开始”按钮,才能开始执行本步的顺控操作;步骤必须从第一步开始执行,否则无法继续执行。
③须将源程序独立备份,运行程序须具有记忆跟踪功能,程序能在故障停车后恢复并入运行,能自动识辨在线运行的联锁操作阶段及进程,并经由内操引导确认后,投入运行。
④逻辑框图中每个过程及之中的人工确认、DCS选塔信号都是独立的、能与其它DCS信号相互区分的DCS联锁信号,以免运行程序发生混乱。
DCS选塔信号为各母程序相互交替操作运行的关键信号,程序系统设置了不受干扰的且独一无二可靠的指令信号。
⑤程序接收到开关状态信号和现场确认信号后完成了指定操作工序,在规定允许的延迟时间后自动发出该完成操作工序联锁阀门的锁定指令,将该阀门或设备锁定。
⑥程序设有每个具有联锁功能的阀门和设备的软旁路系统,满足所处工序的相关设备、阀门因故障时,可将错误的检测信号切出;⑦程序设有各工序的程序人工牵引功能,可将程序引导至上一级操作工序。
延迟焦化工艺参数优化及操作控制

化气,并使汽油的蒸汽压合格;柴油需要加氢精
制;蜡油可作为催化裂化原料或燃料油。
二、主要工艺参数
焦化装置的工艺参数包括加热炉、焦炭塔温度、压力、循 环比以及分馏、吸收、放空系统操作温度、压力等。 主要控制指标是加热炉、焦炭塔温度与压力及循环比。
1.操作温度
焦化装置操作温度一般指加热炉出口温度或焦炭塔温度,一般控 制在493-502℃。
0.105-0.141MPa或更低,循环比降到0.05,焦化液体收率
可提高3%,焦炭产率降低2%。 福斯特-惠勒公司典型焦化装置的设计压力为0.103MPa, Lummus公司典型低压焦化装置焦炭塔压力亦为0.103MPa,
Kellog公司典型设计压力为0.1-0.141MPa.
④加工高沥青质渣油时,为了减少弹丸焦(shot-coke)的 生成;
⑤加热炉燃烧工况不佳,需增加循环比,减缓炉管结焦。
降低循环比的影响:
①单程(零循环比)或低循环比焦化,液体收率高,焦炭收率低; ②单程或低循环比使焦化蜡油变重、质量变差,残炭与重金属含
量增加,其残炭可高达1.9%,会影响下游催化裂化及加氢裂化 装置。
(3) 可高循环比方案
通过循环油泵抽出分馏塔底含焦粉的循环油,以一定比例混入 加热炉进料缓冲罐。
特点:
①采用分馏塔底循环油代替新鲜原料渣油成分馏塔底与焦炭塔高温油气 换热,由于循环油中胶质、沥青质含量低,其结焦倾向降低,用于提 高蒸发段温度的低循环比操作。 ②该方案中的循环油既可使用分馏塔换热、洗涤段冷凝下来的循环油, 也可用蜡油或柴油馏分,实现选择性馏分油循环。 ③塔底循环油经塔外换热器循环回流,可控制塔底温度,减缓塔底结焦
(2) 大陆-菲利浦斯公司低循环比+馏分油循环方案
焦炭塔的操作方法
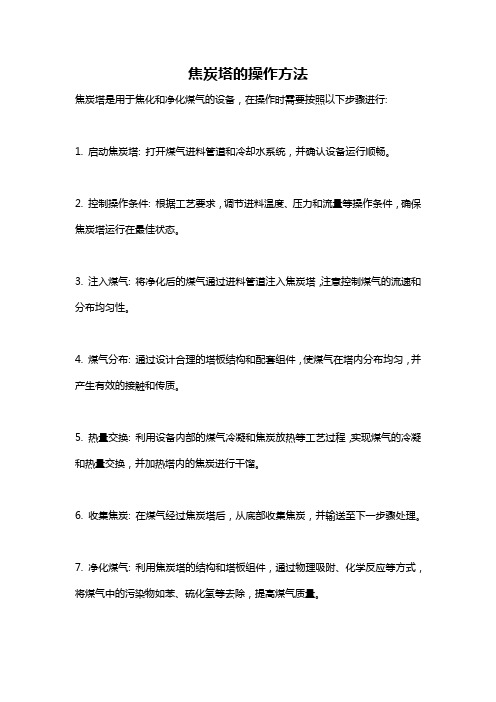
焦炭塔的操作方法
焦炭塔是用于焦化和净化煤气的设备,在操作时需要按照以下步骤进行:
1. 启动焦炭塔: 打开煤气进料管道和冷却水系统,并确认设备运行顺畅。
2. 控制操作条件: 根据工艺要求,调节进料温度、压力和流量等操作条件,确保焦炭塔运行在最佳状态。
3. 注入煤气: 将净化后的煤气通过进料管道注入焦炭塔,注意控制煤气的流速和分布均匀性。
4. 煤气分布: 通过设计合理的塔板结构和配套组件,使煤气在塔内分布均匀,并产生有效的接触和传质。
5. 热量交换: 利用设备内部的煤气冷凝和焦炭放热等工艺过程,实现煤气的冷凝和热量交换,并加热塔内的焦炭进行干馏。
6. 收集焦炭: 在煤气经过焦炭塔后,从底部收集焦炭,并输送至下一步骤处理。
7. 净化煤气: 利用焦炭塔的结构和塔板组件,通过物理吸附、化学反应等方式,将煤气中的污染物如苯、硫化氢等去除,提高煤气质量。
8. 排放尾气: 经过净化处理的煤气通过顶部排气管道排放到大气中,同时确保排放符合环保要求。
9. 监控和调节: 在整个操作过程中,需要进行实时监控焦炭塔的运行情况,并根据生产要求及时调节操作条件和生产参数。
10. 停机和维护: 在完成焦化和净化生产任务后,关闭煤气和冷却水管道,进行设备的检查、维护和保养工作,确保设备的正常运行和安全性。
焦炭塔操作指导延迟焦化装置技术培训PPT 45页

延迟焦化装置提负荷操作指导意见---------焦炭塔部分
2、焦炭塔系统的生焦操作
2.3 实际生产中空塔气速的计算 将所有物料按照操作条件下焦炭塔温度、压力等 条件还原为实际体积,得到焦炭塔的气速,具体 计算方法如下:
1)急冷油不计算在内;加工损失计算在焦炭中; 2)T-焦炭塔平均温度=(T1塔顶+T2塔底)/2;℃ 3)P--焦炭塔压力=10*(塔顶实测压力P1+0.1);
19
延迟焦化装置提负荷操作指导意见---------焦炭塔部分
2、焦炭塔系统的生焦操作
2.7 缩短生焦时间对生焦操作的影响 焦炭塔的材质应选用14CrMo,裙座连接处应采用整体型,
已检测到焦炭塔裙座焊缝开裂,筒体鼓包、开裂、倾斜等存在 明显缺陷的装置尽量不缩短生焦时间.
塔体材质比较
材料 许用应力475℃ MPa 高温屈服强度475℃ MPa
18
延迟焦化装置提负荷操作指导意见---------焦炭塔部分
2、焦炭塔系统的生焦操作
2.7 缩短生焦时间对生焦操作的影响 缩短生焦时间提高处理量,焦炭塔进料和出料的
管道及阀门操作更加频繁,其可靠程度应提高。焦炭 塔进料阀、四通阀、甩油阀和塔顶油气隔断阀等特阀 应采用可靠度高的防结焦动力球阀,上述阀门和除焦 操作的给汽阀、给水阀、放水阀、放空阀相结合,采 用安全联锁及顺序自动控制,可降低劳动强度,保证 操作安全。进料管线及塔顶大油气管线的震动也应引 起重视,应全面进行应力计算,改变配管结构防止震 动,保证安全操作。
其中塔内焦炭堆密度和原料性质及操作条件有关,在设计时 通常采用热态的堆密度。
14
延迟焦化装置提负荷操作指导意见---------焦炭塔部分
2、焦炭塔系统的生焦操作
延迟焦化装置焦炭塔周期性切换操作波动的原因及对策

一、焦炭塔切换周期内操作波动的原因分析1.换塔前新塔预热温度偏低焦炭塔的预热过程为:新塔赶空气、试压合格后,关闭脱水隔断阀,缓慢打开新塔瓦斯阀,将老塔油气引入新塔,待新塔压力与老塔压力接近平稳之后,全开新塔瓦斯阀,将底部甩油改去放空,待底部温度上升至170℃以后,再关底部放空阀,全开甩油去甩油罐阀,再逐渐关小瓦斯总阀,建立瓦斯循环,甩油罐甩油去原料罐或分馏塔回炼,在换塔前,新塔底部温度,要求达到330℃以上,塔壁温度在280℃以上。
但是有时预热一段时间后,温度很难升上去,主要是预热的时间不够,新塔不能得到有效的预热循环,造成温度偏低;进料线有焦,焦炭塔的油不能放下来,多数因除焦不净,新塔预热后焦块掉下来堵住进料热偶引起,造成油气循环量小,温度不能上涨;过滤器堵,也会造成焦炭塔预热不畅,焦炭塔底部的油不能放到甩油罐,油气无法进一步的循环,焦炭塔的温度得不到提高。
2.预热速度过快有时受到除焦系统的影响,预热的时间不够,为了抢时间,加快了预热的速度,预热时间从正常时5小时减少到4小时左右,预热时间缩短了近1小时,由于预热不充分,从而导致热量的不均衡,操作的紊乱。
同时速度的加快,油气量变化太快,将影响去分馏塔的油气负荷,蒸发段温度下降较多,上部回流控制阀必须关小才能保证蒸发段温度,由于上部回流量减少与进料的换热少,分馏塔底温度过低,原料进加热炉温度下降,大大加剧了加热炉的热负荷,操作的调整难度加大。
3.油气线结焦,预热油气量不够有时因急冷油注入问题或油气线速过高、焦高太高,引起油气循环线结焦或堵塞,有新塔顶温度上不去的现象。
在新塔预热油,顶温升不高,影响到焦炭塔预热速度,焦炭塔顶压力也超高。
二、优化焦炭塔切换周期内操作的对策1.吹扫彻底,确保预热流程通畅在除焦班进行除焦时,外操现场开汽吹扫进料短管,并检查短管内无焦粒、焦粉方停汽,这样保证了预热时进料短管内无焦堵。
在除焦班除完焦后,要求除焦人员扫尽焦炭塔内壁的焦粉,铲除清理焦炭塔塔底盖焦粉后方可上短管,以保证在预热时无焦粉落入塔底堵塞进料线。
延迟焦化装置运行参数设置和计算

1、延迟焦化工艺特点--通过调节温度、压力 和循环比等参数增加操 作弹性
• 炉出口温度增加5~6℃,瓦斯油收率增加1.0~1.2% • 循环比降低到0.05~0.15,可较大提高液收,但务必注意
加热炉管结焦和分馏塔蒸发段超温问题
• 馏份油循环,液收可增加2.0~2.5m%,焦炭收率下降
为轻质化加工手段
• 普通高稠原油可按照“稀释→换热→深度电脱盐脱水→加热→闪馏→
或初馏→焦化”流程进行加工
• 塔河油常渣、辽河稠油渣油、沙轻减渣、伊朗油和科威特油减渣等高
沥青质含量、高残炭、低热稳定性的焦化料,建议不要采用超低循环 比操作条件,避免在加热炉管及主分馏塔底结焦;选用具有在线清焦 技术的双面辐射炉型;在工艺设计中考虑选择性瓦斯油外循环流程, 以增加产品方案灵活性和延长焦化炉运行周期,并且可以避免弹丸焦 的生成
焦炭收率之间最佳平衡和经济的操作点
• 加工重质劣质“四高”原料量,一般采用低压、高温和低循环比操作
条件,以实现最大馏份油收率,但务必注意弹丸焦生成问题。
• 调整循环比,在达到最大馏份油收率和处理量时,应满足对蜡油
(HCGO)质量要求
• 在采用低压操作时,务必考虑到焦炭塔内气速以及造成的设备、管线
及系统压降,从而对气压机产生的影响
• 延迟焦化工艺的发展趋势是降低操作压力,以提高液体产品的收率 • 我国焦化装置的操作压力在0.15~0.20 MPa之间
▪ 以前,典型焦化装置的设计压力为0.25 MPa左右 ▪ 新设计的焦化装置操作压力为0.1 Mpa, ▪ 低压操作设计应注意焦化部份的系统压力平衡,在老装置改造时会
受一定限制。
操作温度
• 操作温度是指焦化加热炉出口温度或焦炭塔温度 • 在压力和循环比一定时,焦化温度每增加5.5℃,瓦斯油收率增 加